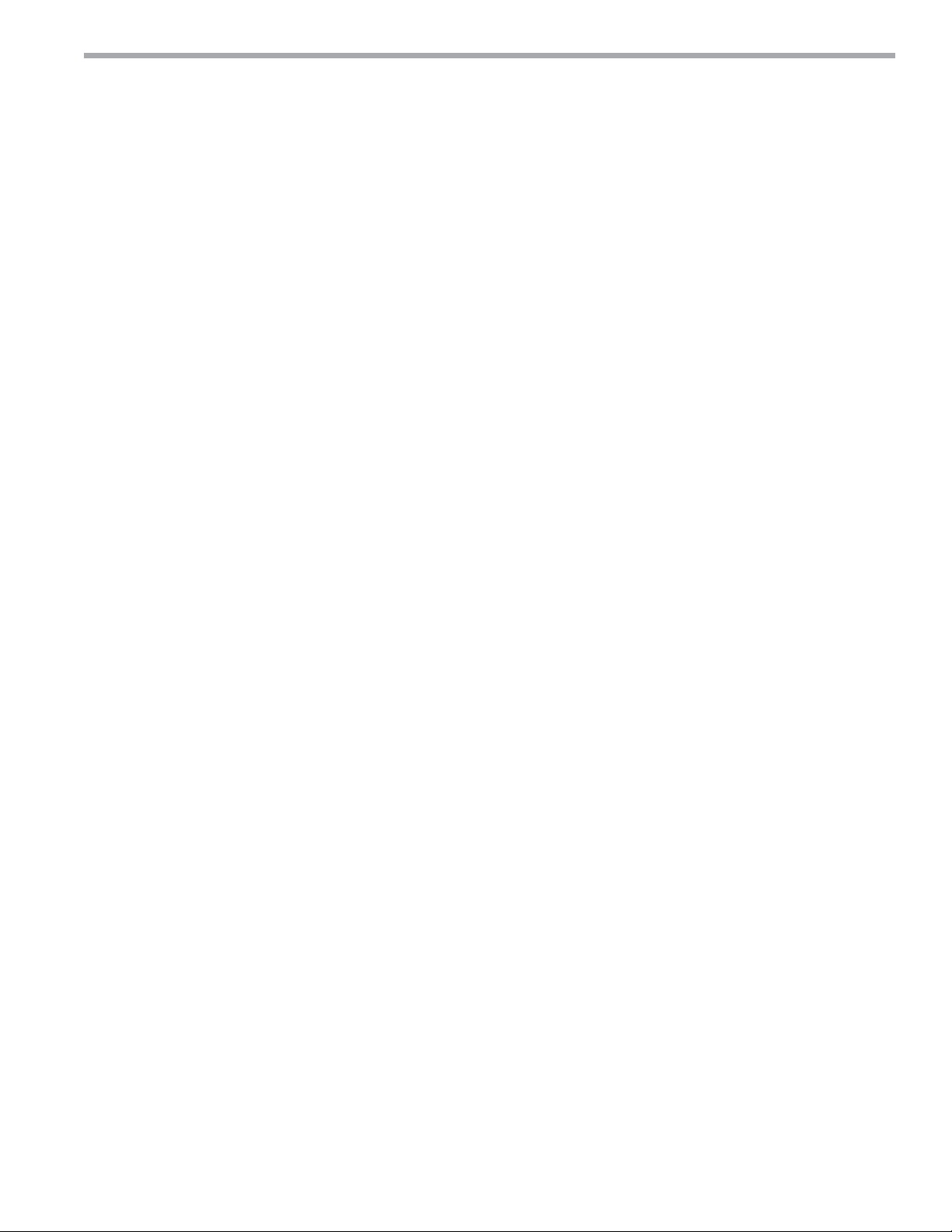
THE SMART SOLUTION FOR ENERGY EFFICIENCY
Water Coil Maintenance - (Direct ground water
applications only) If the system is installed in an area with
a known high mineral content (125 P.P.M. or greater) in
the water, it is best to establish a periodic maintenance
schedule with the owner so the coil can be checked
regularly. Consult the well water applications section
of this manual for a more detailed water coil material
selection. Should periodic coil cleaning be necessary, use
standard coil cleaning procedures, which are compatible
with the heat exchanger material and copper water
lines. Generally, the more water fl owing through the unit,
the less chance for scaling. Therefore, 1.5 gpm per ton
[1.6 l/m per kW] is recommended as a minimum fl ow.
Minimum fl ow rate for entering water temperatures
below 50°F [10°C] is 2.0 gpm per ton [2.2 l/m per kW].
Water Coil Maintenance - (All other water loop
applications) Generally water coil maintenance is not
needed for closed loop systems. However, if the piping
is known to have high dirt or debris content, it is best
to establish a periodic maintenance schedule with the
owner so the water coil can be checked regularly. Dirty
installations are typically the result of deterioration of iron
or galvanized piping or components in the system. Open
cooling towers requiring heavy chemical treatment and
mineral buildup through water use can also contribute
to higher maintenance. Should periodic coil cleaning be
necessary, use standard coil cleaning procedures, which
are compatible with both the heat exchanger material
and copper water lines. Generally, the more water fl owing
through the unit, the less chance for scaling. However,
fl ow rates over 3 gpm per ton (3.9 l/m per kW) can
produce water (or debris) velocities that can erode the
heat exchanger wall and ultimately produce leaks.
Hot Water Generator Coils - See water coil
maintenance for ground water units. If the potable
water is hard or not chemically softened, the high
temperatures of the desuperheater will tend to scale
even quicker than the water coil and may need more
frequent inspections. In areas with extremely hard water,
a HWG is not recommended.
Filters - Filters must be clean to obtain maximum
performance. Filters should be inspected every month
under normal operating conditions and be replaced
when necessary. Units should never be operated without
a fi lter.
Washable, high effi ciency, electrostatic fi lters, when dirty,
can exhibit a very high pressure drop for the fan motor
and reduce air fl ow, resulting in poor performance. It is
especially important to provide consistent washing of
climatemaster.com
Tranquility
®
30 Digital (TE)
Rev.: January 30, 2019
Preventive Maintenance
these fi lters (in the opposite direction of the normal air
fl ow) once per month using a high pressure wash similar
to those found at self-serve car washes.
Condensate Drain - In areas where airborne bacteria
may produce a “slimy” substance in the drain pan, it may
be necessary to treat the drain pan chemically with an
algaecide approximately every three months to minimize
the problem. The condensate pan may also need to be
cleaned periodically to ensure indoor air quality. The
condensate drain can pick up lint and dirt, especially with
dirty fi lters. Inspect the drain twice a year to avoid the
possibility of plugging and eventual overfl ow.
Compressor - Conduct annual amperage checks to
ensure that amp draw is no more than 10% greater than
indicated on the serial plate data.
Fan Motors - All units have lubricated fan motors. Fan
motors should never be lubricated unless obvious, dry
operation is suspected. Periodic maintenance oiling is
not recommended, as it will result in dirt accumulating in
the excess oil and cause eventual motor failure. Conduct
annual dry operation check and amperage check to
ensure amp draw is no more than 10% greater than
indicated on serial plate data.
Air Coil - The air coil must be clean to obtain maximum
performance. Check once a year under normal operating
conditions and, if dirty, brush or vacuum clean. Care
must be taken not to damage the aluminum fi ns while
cleaning. When the heat pump has experienced less
than 100 operational hours and the coil has not had
suffi cient time to be “seasoned”, it is necessary to clean
the coil with a mild surfactant such as Calgon to remove
the oils left by manufacturing processes and enable the
condensate to properly “sheet” off of the coil.
CAUTION: Fin edges are sharp.
Cabinet - Do not allow water to stay in contact with the
cabinet for long periods of time to prevent corrosion of
the cabinet sheet metal. Generally, vertical cabinets are
set up from the fl oor a few inches [7 - 8 cm] to prevent
water from entering the cabinet. The cabinet can be
cleaned using a mild detergent.
Refrigerant System - To maintain sealed circuit integrity,
do not install service gauges unless unit operation
appears abnormal. Reference the operating charts for
pressures and temperatures. Verify that air and water
fl ow rates are at proper levels before servicing the
refrigerant circuit.
53
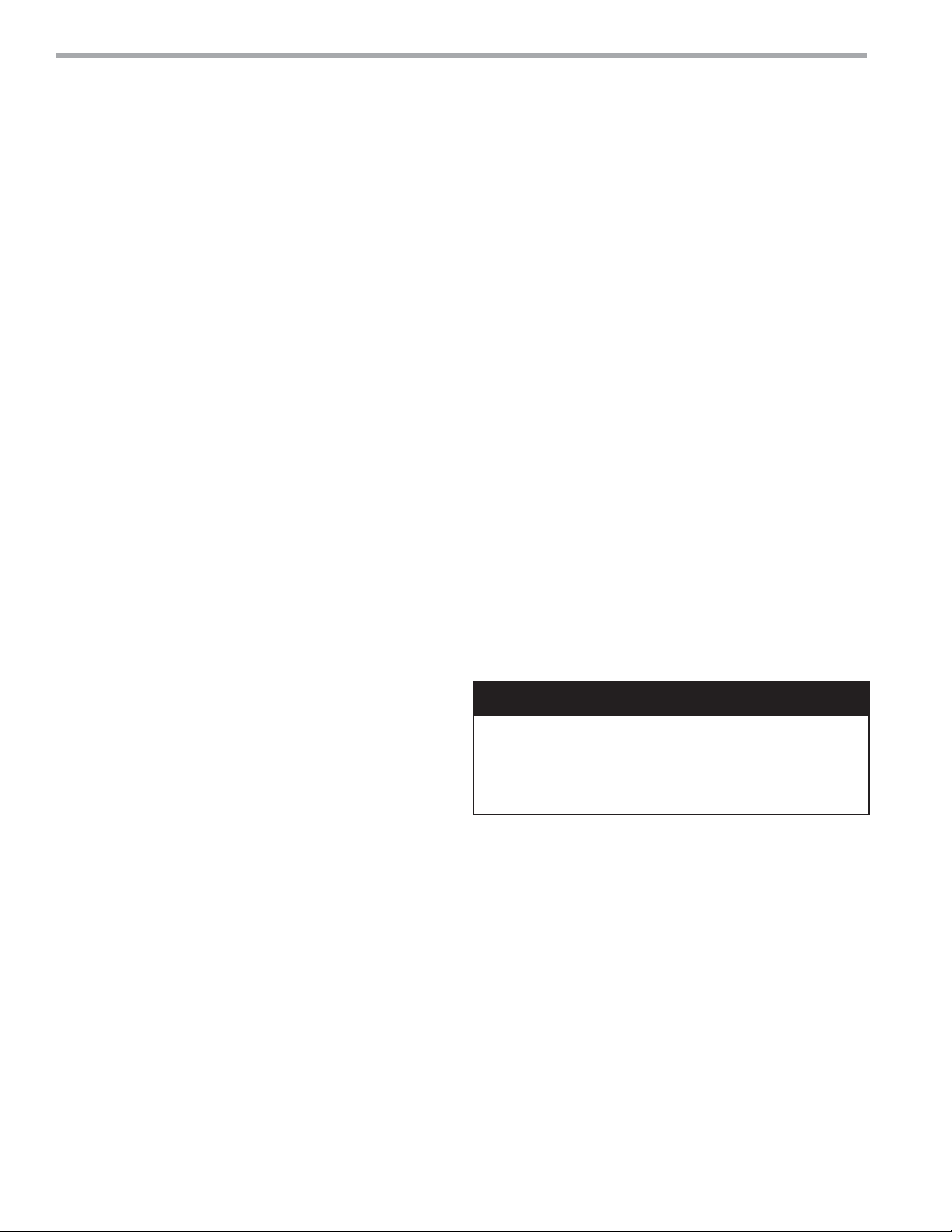
CLIMATEMASTER WATER-SOURCE HEAT PUMPS
Tranquility
Rev.: January 30, 2019
®
30 Digital (TE)
Troubleshooting
General
If operational diffi culties are encountered, perform
the preliminary checks below before referring to the
troubleshooting charts.
• Verify that the unit is receiving electrical supply power.
• Make sure the fuses in the fused disconnect switches
are intact.
After completing the preliminary checks described
above, inspect for other obvious problems such as
leaking connections, broken or disconnected wires, etc.
If everything appears to be in order, but the unit still fails
to operate properly, refer to the “DXM2 Troubleshooting
Process Flowchart” or “Functional Troubleshooting
Chart.”
DXM2 Board
DXM2 board troubleshooting in general is best
summarized as verifying inputs and outputs. After inputs
and outputs have been verifi ed, board operation is
confi rmed and the problem must be elsewhere. Below
are some general guidelines for troubleshooting the
DXM2 control.
Field Inputs
Conventional thermostat inputs are 24VAC from the
thermostat and can be verifi ed using a voltmeter
between C and Y1, Y2, W, O, G. 24VAC will be present at
the terminal (for example, between “Y1” and “C”) if the
thermostat is sending an input to the DXM2 board.
Proper communications with a thermostat can be verifi ed
using the Fault LED on the DXM2. If the control is NOT
in the Test mode and is NOT currently locked out or
in a retry delay, the Fault LED on the DXM2 will fl ash
very slowly (1 second on, 5 seconds off), if the DXM2 is
properly communicating with the thermostat.
Outputs
The compressor and reversing valve relays are 24VAC
and can be verifi ed using a voltmeter. For units with
ECM blower motors, the DXM2 controls the motor using
serial communications, and troubleshooting should be
done with a communicating thermostat or diagnostic
tool. The alarm relay can either be 24VAC as shipped or
dry contacts for use with DDC controls by clipping the
JW1 jumper. Electric heat outputs are 24VDC “ground
sinking” and require a voltmeter set for DC to verify
operation. The terminal marked “24VDC” is the 24VDC
supply to the electric heat board; terminal “EH1” is stage
1 electric heat; terminal “EH2” is stage 2 electric heat.
When electric heat is energized (thermostat is sending a
“W” input to the DXM2 controller), there will be 24VDC
between terminal “24VDC” and “EH1” (stage 1 electric
heat) and/or “EH2” (stage 2 electric heat). A reading
of 0VDC between “24VDC” and “EH1” or “EH2” will
indicate that the DXM2 board is NOT sending an output
signal to the electric heat board.
Test Mode
Test mode can be entered for 20 minutes by pressing the
Test pushbutton. The DXM2 board will automatically exit
test mode after 20 minutes.
WARNING!
WARNING! HAZARDOUS VOLTAGE! DISCONNECT ALL
ELECTRIC POWER INCLUDING REMOTE DISCONNECTS
BEFORE SERVICING.
Failure to disconnect power before servicing can cause
severe personal injury or death.
Sensor Inputs
All sensor inputs are ‘paired wires’ connecting each
component to the board. Therefore, continuity on
pressure switches, for example can be checked at the
board connector. The thermistor resistance should be
measured with the connector removed so that only the
impedance of the thermistor is measured. If desired, this
reading can be compared to the thermistor resistance
chart shown in Table 8. An ice bath can be used to check
the calibration of the thermistor.
54
ClimateMaster Water-Source Heat Pumps
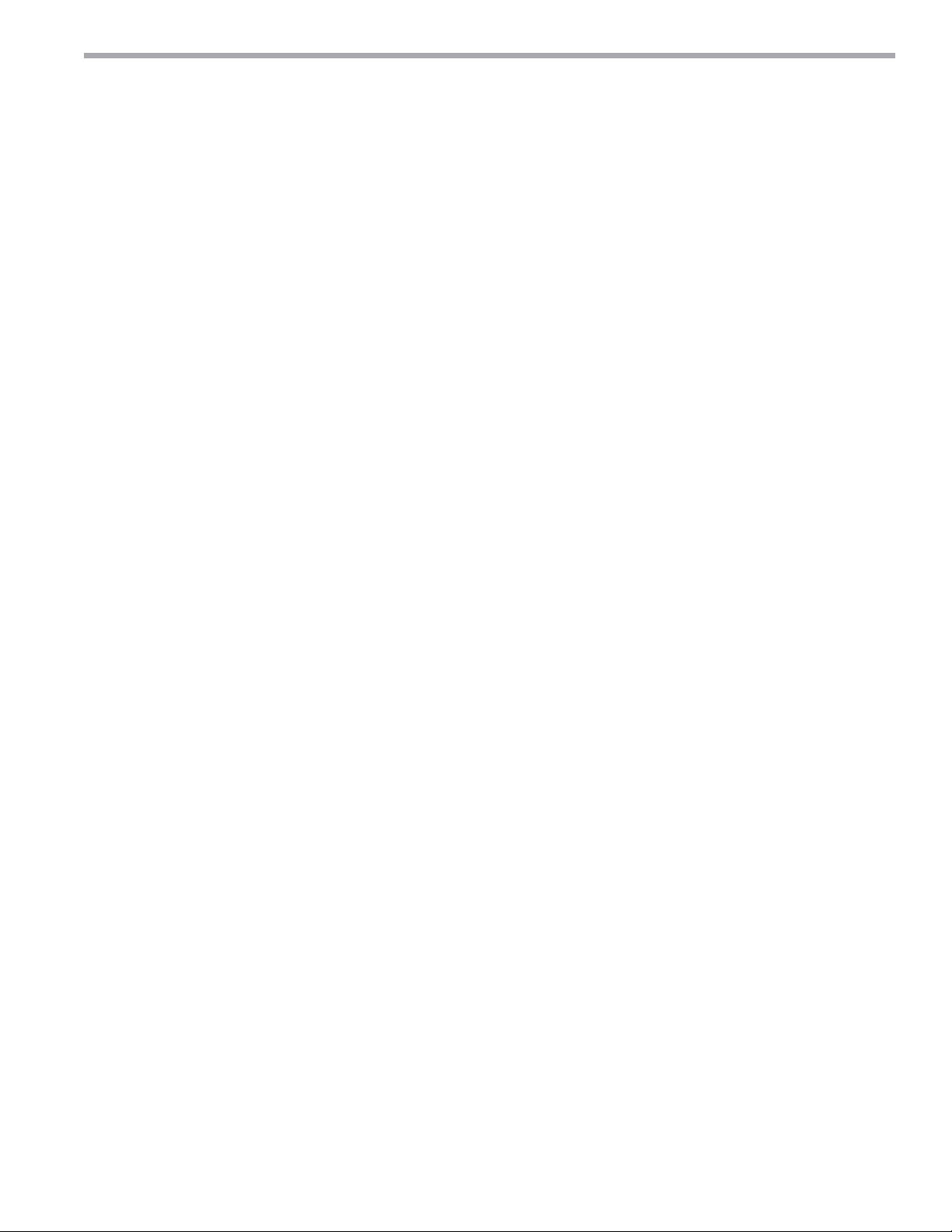
THE SMART SOLUTION FOR ENERGY EFFICIENCY
Advanced Diagnostics
If a communicating thermostat or diagnostic tool
(ACDU) is connected to the DXM2, additional diagnostic
information and troubleshooting capabilities are
available. The current status of all DXM2 inputs can be
verifi ed, including the current temperature readings of all
temperature inputs. With a communicating thermostat
the current status of the inputs can be accessed from
the Service Information menu. In the manual operating
mode, most DXM2 outputs can be directly controlled
for system troubleshooting. With a communicating
thermostat the manual operating mode can be accessed
from the Installer menu. For more detailed information
on the advanced diagnostics of the DXM2, see the
DXM2 Application, Operation and Maintenance (AOM)
manual (part #97B0003N15).
DXM2 Troubleshooting Process Flowchart/Functional
Troubleshooting Chart
The “DXM2 Functional Troubleshooting Process
Flowchart” is a quick overview of how to start diagnosing
a suspected problem, using the fault recognition features
of the DXM2 board. The “Functional Troubleshooting
Chart” on the following page is a more comprehensive
method for identifying a number of malfunctions that
may occur, and is not limited to just the DXM2 controls.
Within the chart are fi ve columns:
• The “Fault” column describes the symptoms.
• Columns 2 and 3 identify in which mode the fault is
likely to occur, heating or cooling.
• The “Possible Cause column” identifies the most likely
sources of the problem.
• The “Solution” column describes what should be done to
correct the problem.
Tranquility
®
30 Digital (TE)
Rev.: January 30, 2019
Troubleshooting (Continued)
climatemaster.com
55