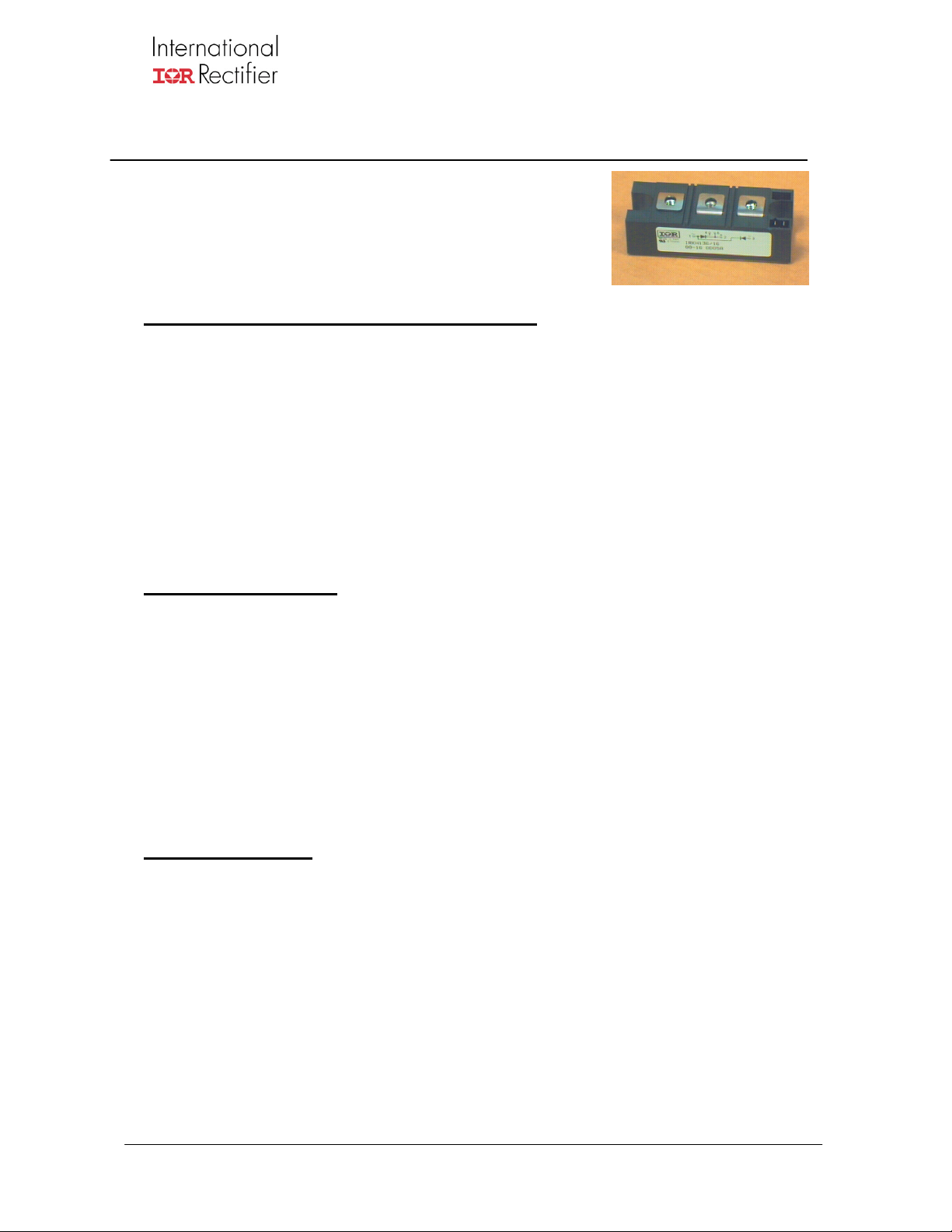
Assembly of INT-a-PAK Modules
Important heatsink mounting instruction
In order to guarantee good thermal contact and keep the contact thermal resistance
value specified in data sheets we recommend to use flat heatsink with tolerances
< 0.03mm (1.18mils) and a levelling depth of < 0.02mm (0.79mils) according to DIN
ISO1302.
In general a milled or machined surface is satisfactory if prepared with tools in good
working conditions.
The heatsink mounting surface must be clean, with no dirt, corrosion or surface
oxides. It is very important to keep the mounting surface free from particles
exceeding in thickness 0.05mm (2mils) provided thermal compound.
Thermal Compound
Coat uniformly the heatsink surface and the power module baseplate with a good
quality thermal compound.
Apply uniform pressure on the package to force the compound to spread over the
entire contact area.
The purpose of thermal grease is to fill gaps at baseplate-heatsink interface. The
suggested thermal grease is the Dow Corning 340.
Screen printing or rubber rolling are the preferred methods to apply the grease.
A final thickness of grease layer in the range of 80 – 100 µm is considered suitable
for most of applications.
Module fastening
Bolt the module to the heatsink using two M6 screws. The recommended torque is
4-6 Nm (35-53 Lbf*inch) +- 10%.
An even amount of torque should be applied for each individual mounting screw.
A torque calibrate wrench, accurate in the specified range, must be used in mounting
the module, in order to achieve optimum results. The mounting screw must be
tightened in sequence.
After a period of about three hours, recheck the torque with a final tightening in
opposite sequence to allow the spread of the compound.
1
by International Rectifier Corp. Italy –