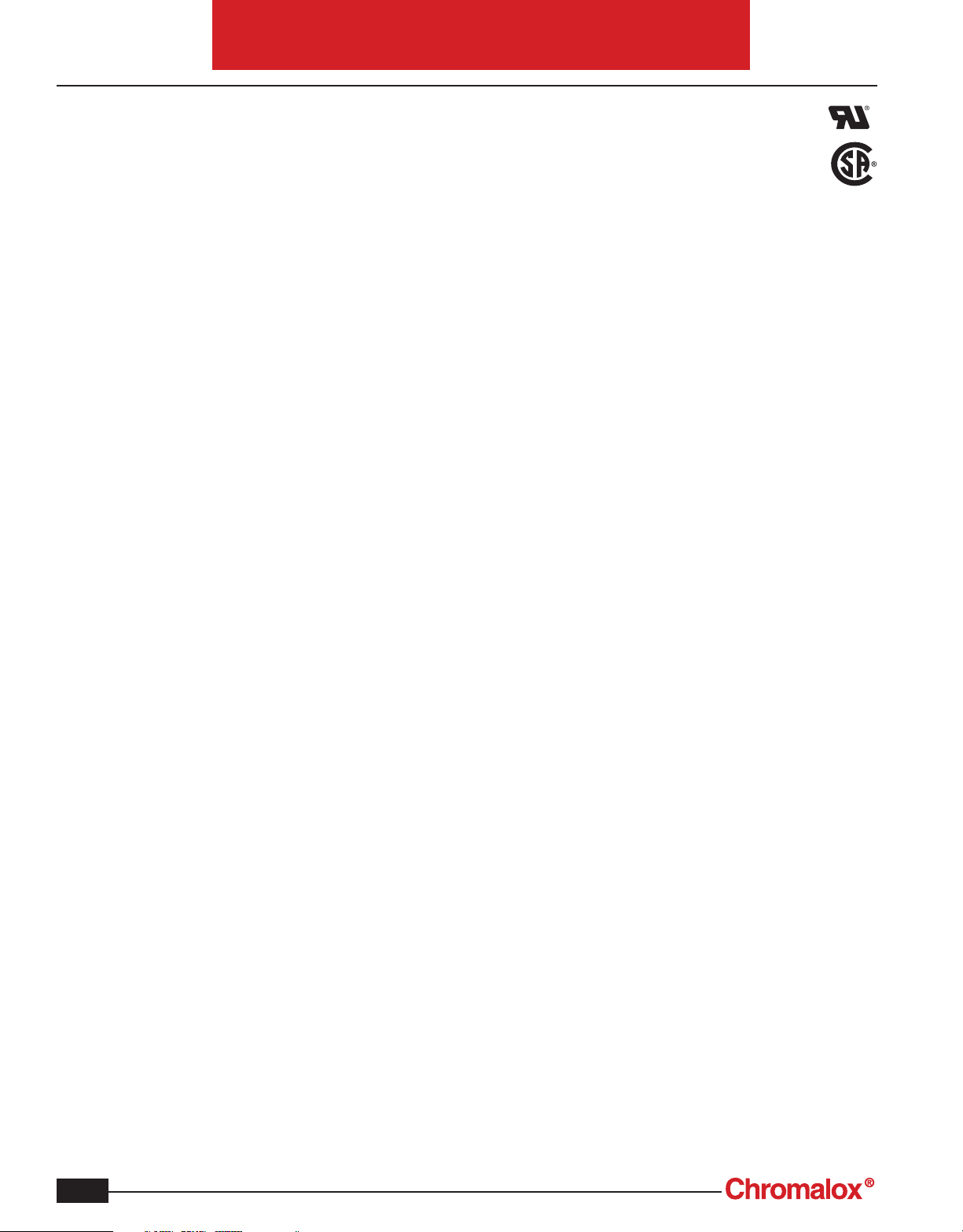
Cartridge Heaters
Application & Installation
Recommendations
Applications
Application at High Watt Densities —
Type CIR cartridge heaters are designed
and manufactured to provide watt density
capabilities second to none. To obtain best life
at the highest watt densities allowed per Curve
G-235 in the Application Guidelines, close attention to application details is suggested.
A. For closest fit and best heat transfer, holes
should be drilled and reamed, rather than
just drilled to final diameter with a general purpose drill.
B. The sensor for the temperature control
should be placed between the working
surface of the part and the heaters. The
temperature of the part approximately 1/2"
away from the heaters is used in selecting
maximum allowable watt density from the
graph.
C. Control of power is an important consider ation in high watt density applications.
On/Off control is frequently utilized, but it
can cause wide excursions in the
temperature of the heater and working
parts. SCR power controls are valuable in
extending the life of high watt density
heaters, since they effectively eliminate
on-off cycling.
Application at Medium Watt Densities
— Curve G-235 in the Application Guidelines
shows maximum allowable watt density for
various fits and operating temperatures. The
vast majority of applications do not require
maximum W/In
only as high as you need. Take advantage of
the safety margin provided by using ratings
less than the maximum allowed. Select and
space heaters for most even heat pattern
rather than for highest possible wattage per
heater.
At medium watt densities, general purpose
drills are usually adequate for drilling holes.
Typically, these result in holes 0.003 to 0.008"
over the normal size of the drill, resulting in
fits of 0.01 to 0.015". Of course, the tightest
fit is desirable from a heat transfer standpoint,
but somewhat looser fits aid in installing and
removing cartridge heaters, especially long
ones. Holes drilled completely through the
part are recommended to facilitate removal of
the heater. After drilling, clean or degrease the
part to remove cutting lubricants.
Operation in Vacuum — When heaters are
operated in a block which is in a vacuum, the
inside of the holes should be pre-oxidized to
2
, however. Use a watt density
Components
improve emissivity. Substantial reductions in
maximum allowable watt density are usually necessary for vacuum operation. Where
possible, the installation should be designed
so that the lead end of the heater is outside
the vacuum. When the lead end of the heater
is inside the vacuum, a voltage of 120 volts or
less is recommended. On an unsealed heater,
outgassing may be expected.
Operation in Square Grooves — Round
type CIR cartridge heaters may be installed
in square or v-shaped grooves if this proves
convenient. The inside of the groove should be
treated to improve its emissivity (by oxidizing
or anodizing). Allowable W/In
mated by using the 0.05" fit line in the graph,
providing that the square is approximately the
same width as the nominal diameter of the
heater.
Operation on 480V — Chromalox type CIR
cartridge heaters 5/8" diameter and larger can
be operated on 480 volts. One approach is to
take two stock 240 volt heaters and connect
them in series on 480 volts. Another is to order specially rated 480 volt cartridge heaters.
Check with your Local Chromalox Sales office
for recommendations.
Because of higher voltage stresses inside the
heater, lower maximum watt densities are
allowable in 480 volt applications, either with
two 240 volt heaters in series or with specially
rated 480 volt units. To determine maximum
allowable watt density at 480 volts, enter
Curve G-235 with an operating temperature
value which is 200°F higher than the actual
operating temperature. A maximum operating
temperature of 1000°F is suggested.
Testing Recommendations
Testing Recommendations — Testing under
simulated operating conditions is suggested
when equipment manufacturers design new
products. Cartridge heaters of the appropriate
physical size are operated on a variable transformer until the heat output is at the proper
level. Then, voltage and current measurements
are taken and required wattage rating is calculated. Heaters of the correct wattage rating are
then ordered for the designed product.
Installation Recommendations
1. On moving machinery, anchor the leads
securely. As little movement as possible
should be allowed close to where the leads
emerge from the heater. A loop in the lead
2
can be esti-
wire will frequently extend lead life. If
application conditions result in continual
lead flexing, terminate the cartridge heater
leads at a terminal block which moves with
the heated assembly. Flexing is transferred
to the extension leads which can be
economically replaced.
2. For rapidly vibrating equipment, employ
the terminal block described above. Keep
leads from heater to block short and well
supported to prevent lead movement due
to vibration.
3. Protect leads from spray, oil and abrasion.
Contaminating liquids and vapors can
enter unsealed cartridge heaters and cause
insulation breakdown.
4. Avoid tape on leads where they emerge
from the cartridge heater. The adhesive on
some tapes can enter the heater and turn
to carbon which is electrically conductive.
Where glass tape cannot be avoided, a
tape with a silicone based adhesive is
suggested.
5. Design the installation so that the leads are
in an ambient temperature which doesn't
exceed the rating on the lead insulation
(842°F for standard leads). Where
temperatures require it, use nickel or
nickel-plated copper wire with
fluoropolymer insulation, silicone
impregnated Fiberglas
insulation to extend leads.
6. Graphite and other lubricants to help
insert the cartridge heater into the hole
are generally not recommended. These are
electrically conductive and can get on the
lead end of the heater unless extra care is
taken. Use Chromalox heat transfer and
release coating.
7. As operating temperatures rise, thermal
insulation on the heated part becomes
more desirable to conserve heat. Thermal
insulation results in lower wattage
requirements and therefore lower watt
density on the heaters. Other benefits are
more even work temperatures and greater
operator safety and comfort.
8. Leads must not extend into the hole
containing the cartridge heater. Generally,
the lead end of the heater sheath should be
flush with the surface of hole or extended
by 1/16 inch.
®
or Rockbestos®
A-94