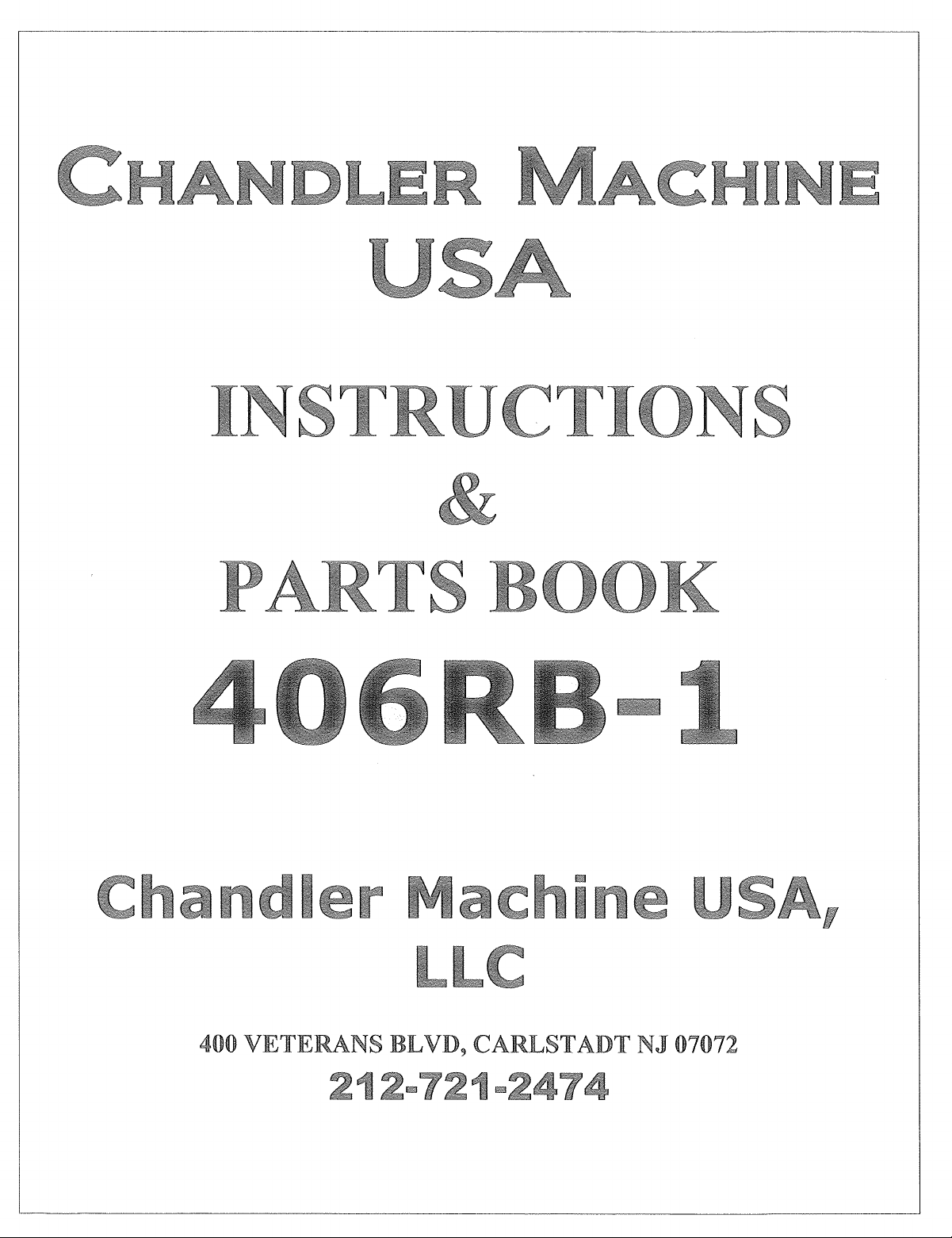
I
400 VETERANS BLVD, CARLSTADT
NJ
07072
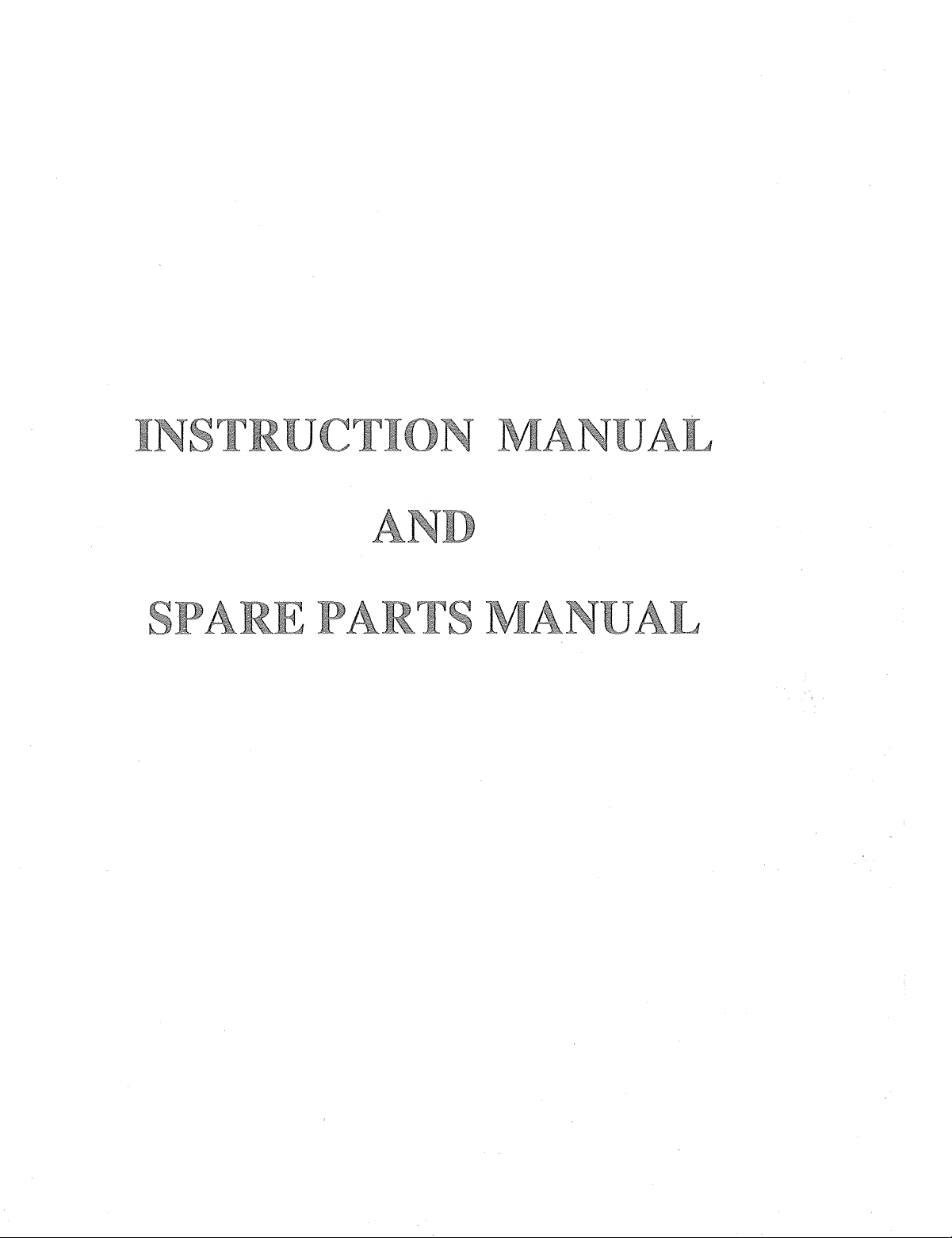
u
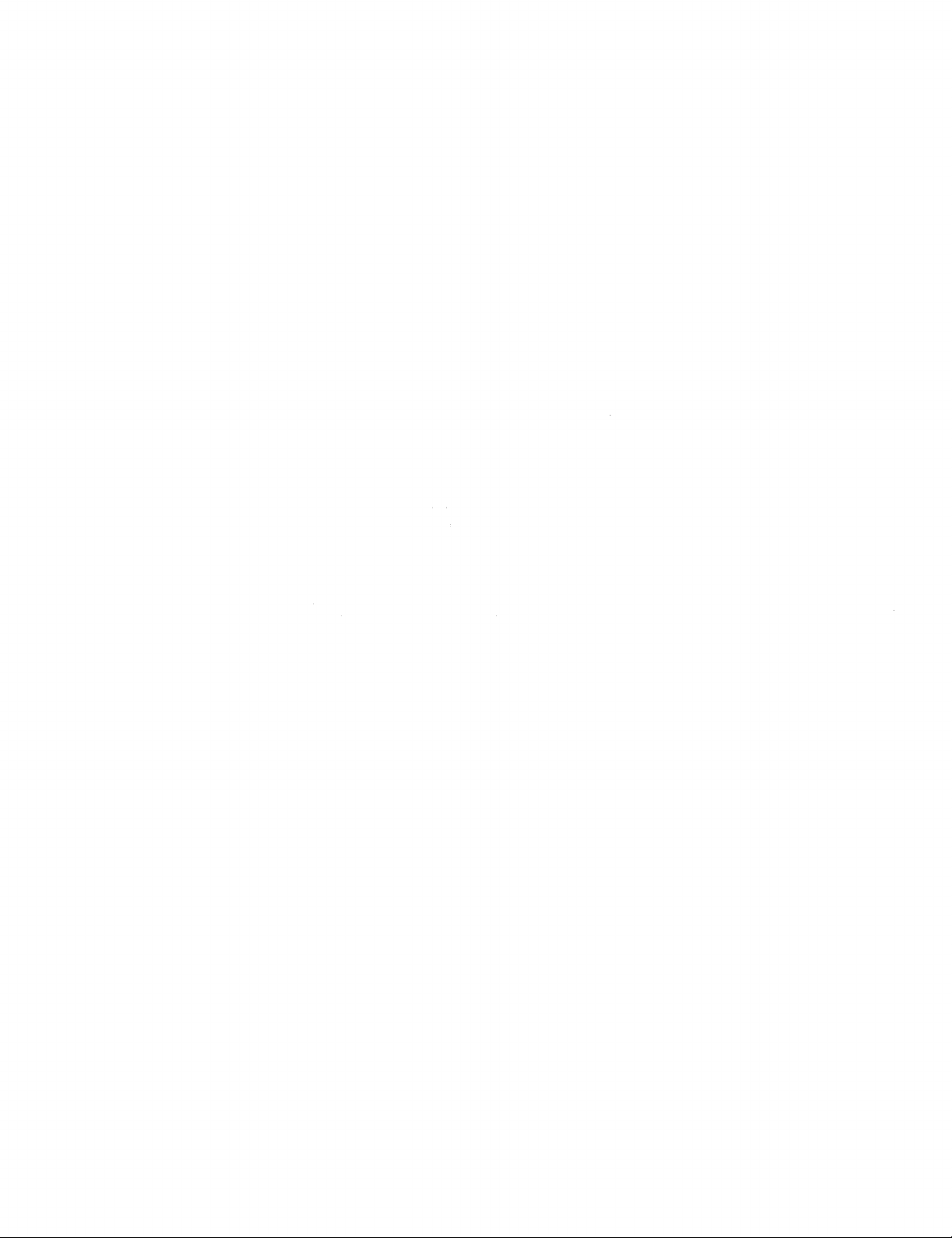
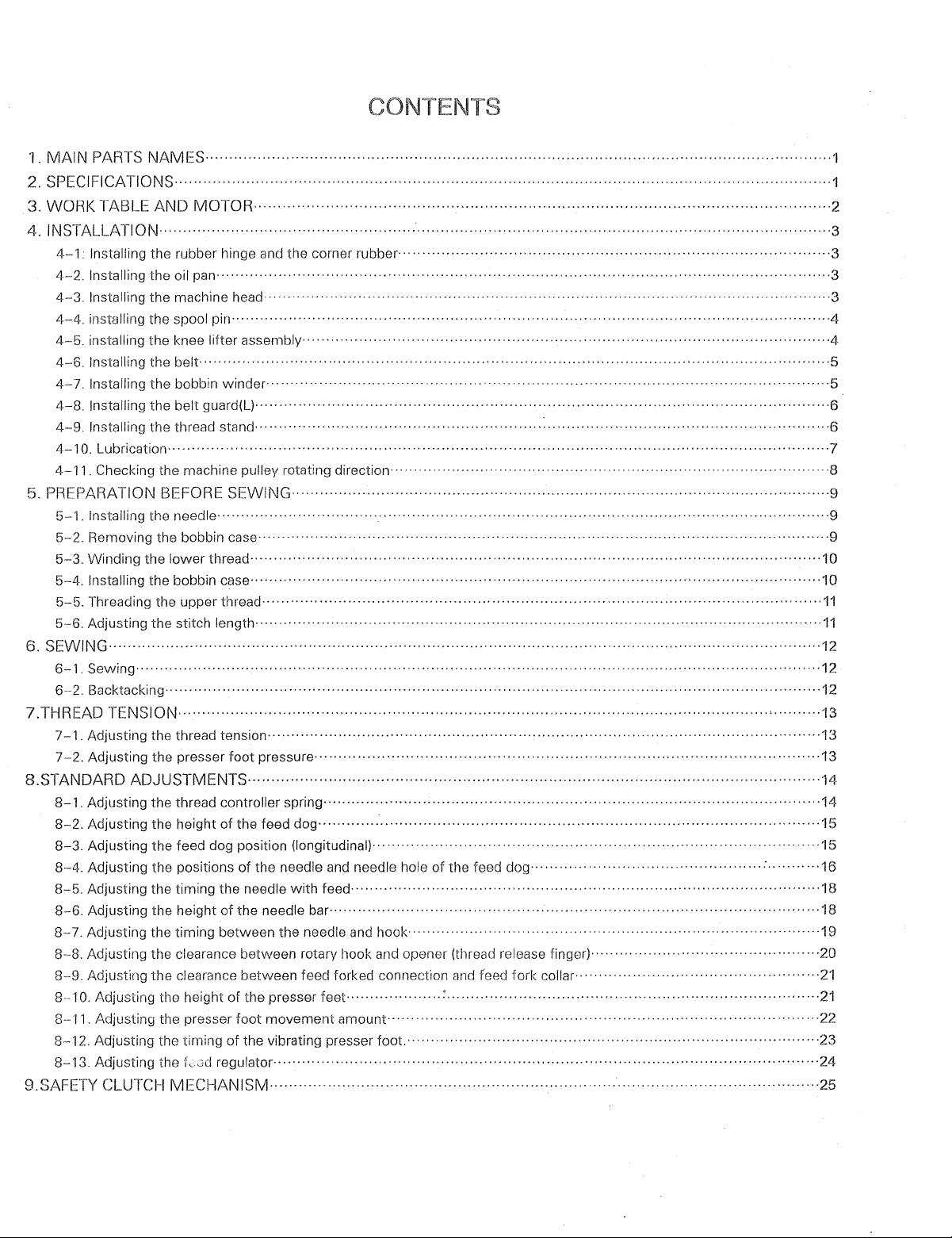
CONTENTS
1.
MAIN
PARTS
2. SPECIFICATIONS··········································································································································1
3. WORK TABLE AND MOTOR ........................................................................................................................ 2
4.
INSTALLATION·············································································································································3
4-1:
Installing the rubber hinge and the corner rubber····
4-2.
Installing the oil pan··· ...... · ...
4--3. Installing
4-4.
installing the spool pin ... ······· .... ···· ... · .....
4-5.
installing the knee lifter
4-6.
Installing the belt······
4-7.
Installing the bobbin winder
4-8.
Installing the belt guard{L)· · · · · · · · · · · · · · · · · · · · · · · · · · · · · · · · · · · · · · · · · · · · · · · · · · · · · · · · · · · · · · · · · · · · · · · · · · · · · · · · · · · · · · · · · · · · · · · · · · · · · · · · · · · · · · · · · · · · · · · ·6
4-9.
Installing the thread
4-1
0.
Lubrication···················································
4-11.
Checking the machine pulley rotating direction··
5. PREPARATION BEFORE SEWING .................................................................................................................. g
5-1.
Installing the needle····
5-2.
Removing the bobbin case············
5-3.
Winding the
5-4.
Installing the bobbin case· .. · ..
5-5.
Threading the upper
5-6.
Adjusting the stitch
6. SEWING······················································································································································12
6-1.
Sewing················································································································································12
6--2.
Backtacking·························································-·······
7 .THREAD TENSION···································· ........ ·········· ...... ··········································································
7-1.
Adjusting the thread tension·· .....
7-2.
Adjusting the presser foot
8.STANDARD ADJUSTMENTS········································
8-1.
Adjusting the thread controller
8-2.
Adjusting the height
8-3.
Adjusting the feed dog position (longitudinal)···· ..
8-4.
Adjusting the positions
8-5.
Adjusting the timing the needle
8-6.
Adjusting the height
8-7.
Adjusting the timing between the needle and hook
8-8.
Adjusting the clearance between rotary hook and opener (thread release
Adjusting the clearance between feed forked connection
8--9.
8--10. Adjusting the height
s-·11. Adjusting the presser foot
8-12.
Adjusting the timing
8-13.
Adjusting the
9.SAFETY CLUTCH MECHANISM···· .............................................................................................................. 25
NAMES································································· ..................................................................
........
the machine
lower
thread················-
length·································
L0d
regulator···········································-··············
···········
··
..
······
....
·········
.....
··············
head···············
assembly··············································································································
..
····
..
···
..
..
···················
stand············
..
··
..
··
..
········
········································
thread·············································
pressure·····················
spring···················
of
the feed dog· .....
of
the needle
of
the needle
of
the presser
movement
of
the vibrating presser foot ...
... ······
..
·················
···················
··············
················
with
bar·····································································································
..
················
.. · ..
··············································
..
·············
.... ·
........
.......................................................................................................
and
feed
feet····················:···························
..
················
..
..
··
..
···
..
··· ...... ···· ......
·················
.........
·········
......
···········································································
needle hole
...................................................................................................
amount·······························································
..
···· ... ···
.. ·
..
· · · · · · · · · · · · · · · · · · · · · · · · · · · · · · · · · · · · · · · · · · · · · · · · · · · · · · · · · · · · · · · · · · · · · · · · · · · · · · · · · · · · · · · 7
···············
..
·····························
..
········································
··········
.....................
..
··············································································14
..
································
······························
of
the feed
......................................................................................
and
·······
..
····
....
··
..
·····
..
··· ..
················
..... ···
..
···················
.. · ..
······················
..
···
..
··············
·····················
..
··········
..
··
... ·
..
·······
....
···········
..................
.........................................................................
.....
···························································
····························································
dog··················
feed fork
..
·····································································
..
..
·····
..
···
..
··············
..
····
..
···· ...... ···
..
···············
················································
...
finger)···············································
collar··················································
........................................................
...... ·
..
··
..
···
..... ·····
··
..
················································
..
·····································
······················
..
······ ...... ···
..
···· .... ·· ...... ····
....
·······································
..
·······································
···························
..
···············································
·········
...
····································
...
···············
.....
···········································
..
..
· .... ···
··· ...
..
······
.... · ..
..
··
....
··············
..
················
..
··
..
··················
···············
..
··········
..
···················
..
...
·········:.·
...............
·······
... ·
..
.. · .. · ..
..
··········
..
··
..
················11
..... ····· ·13
···· ..
......
···
·········22
..
·· .... ·· ·3
·········
···· ·3
....
..
·········
.... ···· ·9
······11
···13
..
···15
······15
··
···21
··· ·5
..
·1
·13
·14
·16
·18
-19
·20
·21
·23
-4
·5
·6
·8
·9
10
12
18
24
-1
·3
-4
0
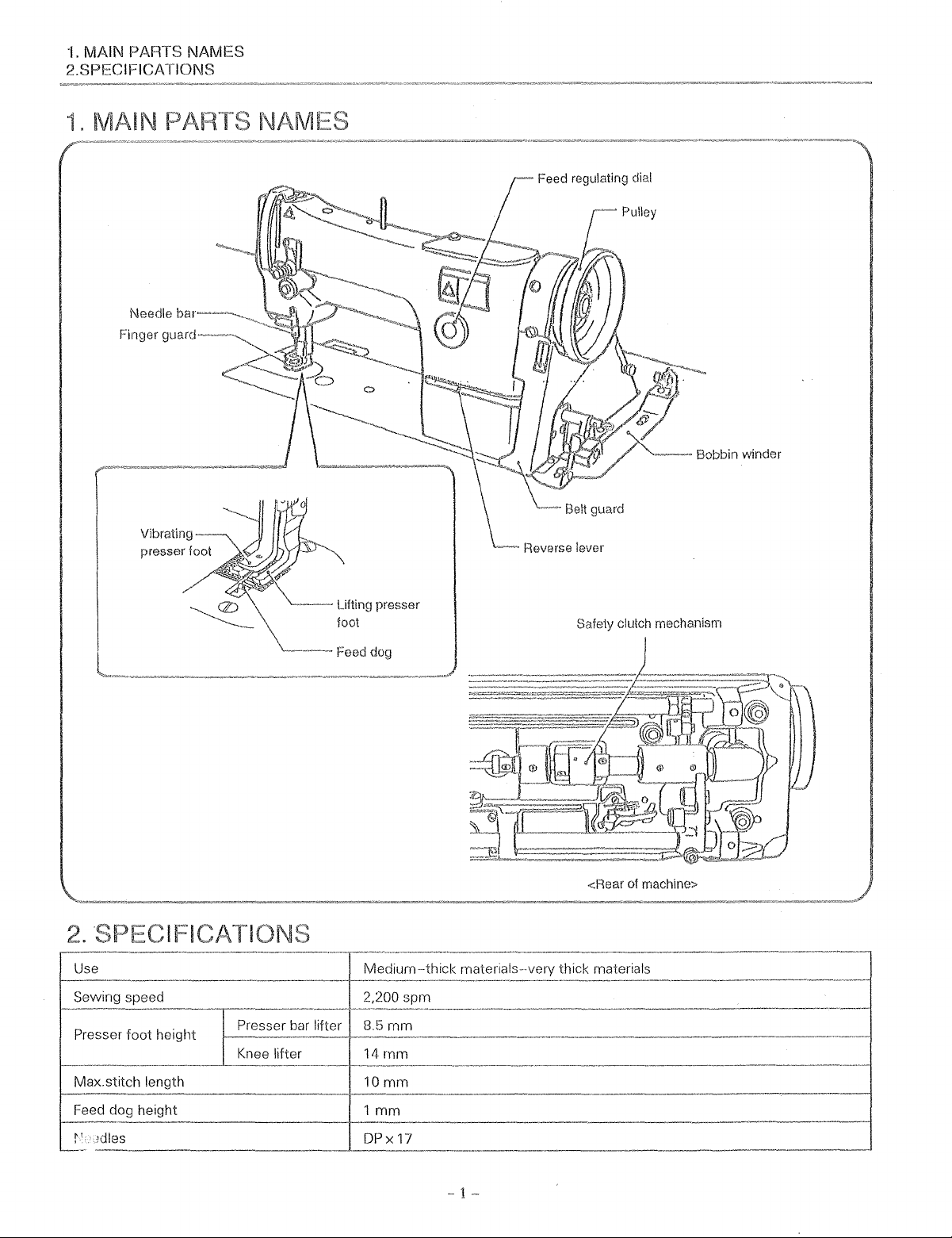
1.
MAIN PARTS NAMES
2.SPECIFICATIONS
1"
MAIN
Feed regulating dial
Vibrating
presser foot
~-
lifting presser
foot
-~Feed
dog
Safety clutch mechanism
of
<Rear
materials--very thick materials
machine>
-
1-
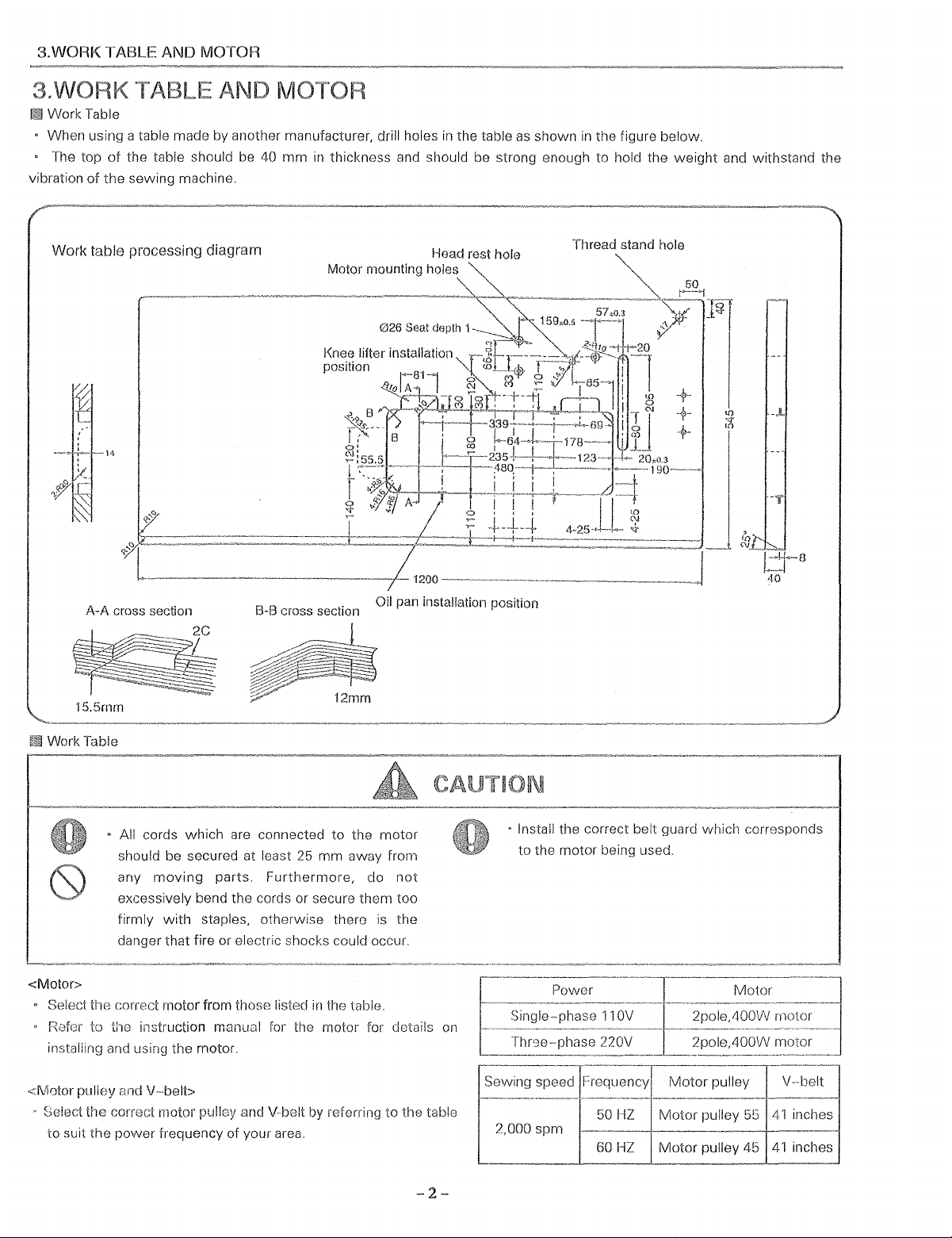
3.WORK TABLE AND MOTOR
3.WORK TABLE AND MOTOR
Work Table
• When using a table made by another manufacturer, drill holes
• The top
vibration
of
the table should be 40
of
the sewing machine.
mm
in
thickness and should be strong enough to hold the
in
the table
as
shown
in
the figure below.
weight
and withstand the
Work
table
processing
14
A-A
cross section
diagram
B-B
cross section
Motor mounting holes
!<:nee
lifter installation
position
Oil pan installation position
Head
Thread stand hole
15.5mm
Work Table
• All cords which are connected to the
should be secured at least 25
moving
any
excessively bend the cords or secure them too
with
firmly
danger that fire or electric shocks could occur.
<Motor>
• Sek;ct
<M0tor pulley and
UiG
correct motor from those listecl
f{,:Jfor
to
the instruction manual for the motor for details on
installing and using the motor.
V-belt>
Select the correct motor pulley and V-belt by referring to the table
to
suit
the
power frequency of your area.
parts.
staples, otherwise them
Furthermore,
mm
in
the table.
motor
away from
do
not
is
the
• Install the correct belt guard which
to the motor being used.
Power
50
HZ
Motor
pulley 55
2,000 spm
60HZ
Motor
pulley 45
Motor
motor
41
inches
41
inches
-2-
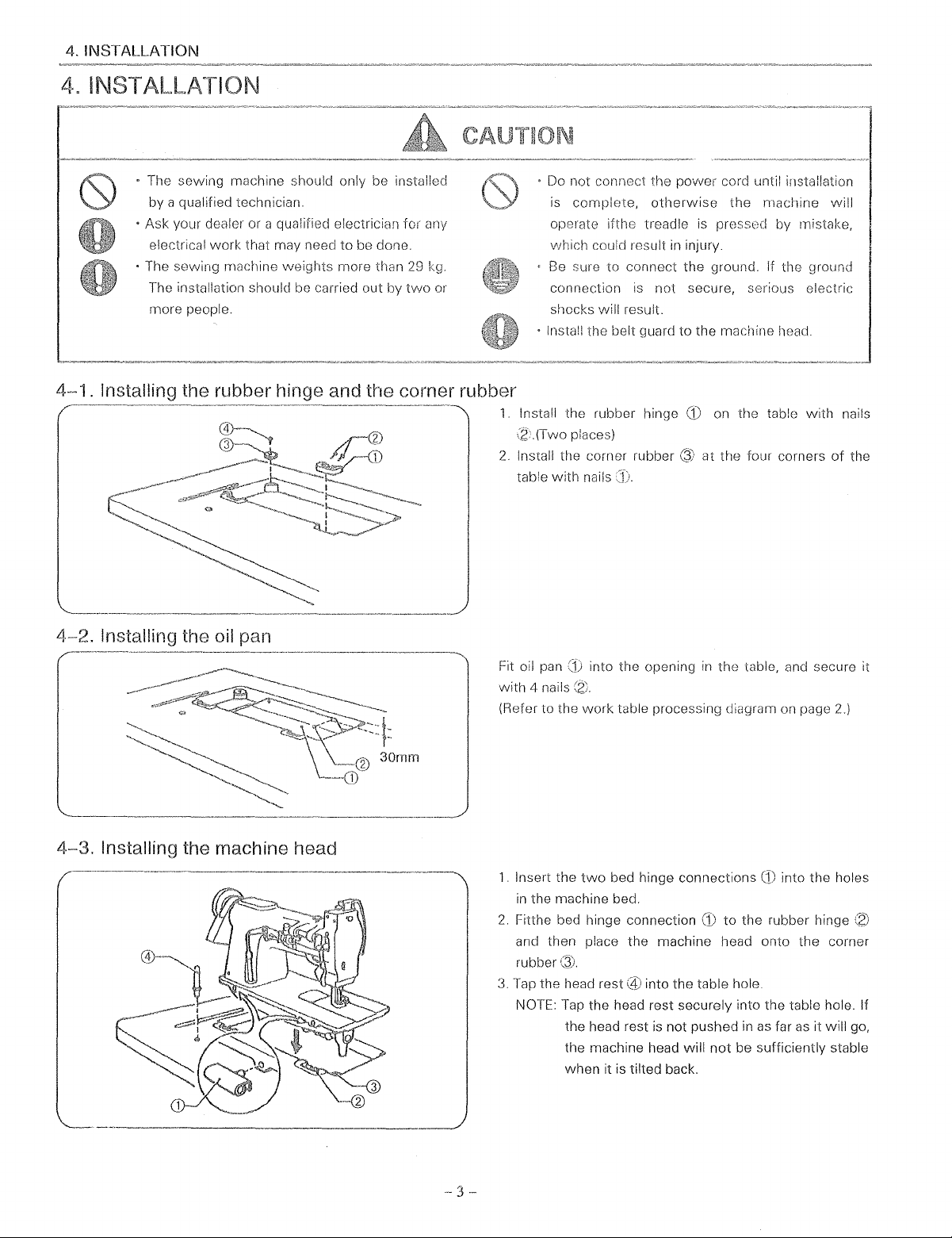
4.
INSTALLATION
4.
INSTALLATION
o The sewing machine should only be installed
by a qualified technician.
• Ask your dealer or a qualified electrician for any
electrical
· The sewing machine
The installation should be
more people.
4-1.
Installing the rubber hinge and the corner rubber
4~2.
Installing the oil pan
work
that may need to be done.
weights
carried out by
more than 29 kg.
two
or
o Do not connect the
is
complete,
oper8te ifthe treadle is
v;hich could result in injury.
Be
sure to connect the ground. If the ground
connection is not secure, serious electric
shocks will result.
• Install the belt guard to the machine head.
1.
Install the rubber hinge
(2
(Two places)
2.
Install the corner rubber Q) at the four corners
table
with
nails
power
otherwise
(1)
cord until installation
the
m8chine
prEJSSt)cl
on the table
by mistake,
with
will
nails
of
the
4-3.
Installing the machine head
Fit oil pan
with
4 nails
(Refer to the
1.
Insert the
in
the machine bed.
2.
Fitthe bed hinge connection to the rubber hinge
and then place the machine head onto the corner
rubber
3.
Tap the head rest into the table hole.
NOTE:
into the opening
work
table processing diagram on page
two
bed hinge connections
Tap
the head rest securely into the table hole. If
the head rest
the machine head will
when
it is tilted back.
is
in
the table, and secure it
not pushed in
not
be sufficiently stable
CD
into the holes
as
far
as
it will go,
2.)
--
3
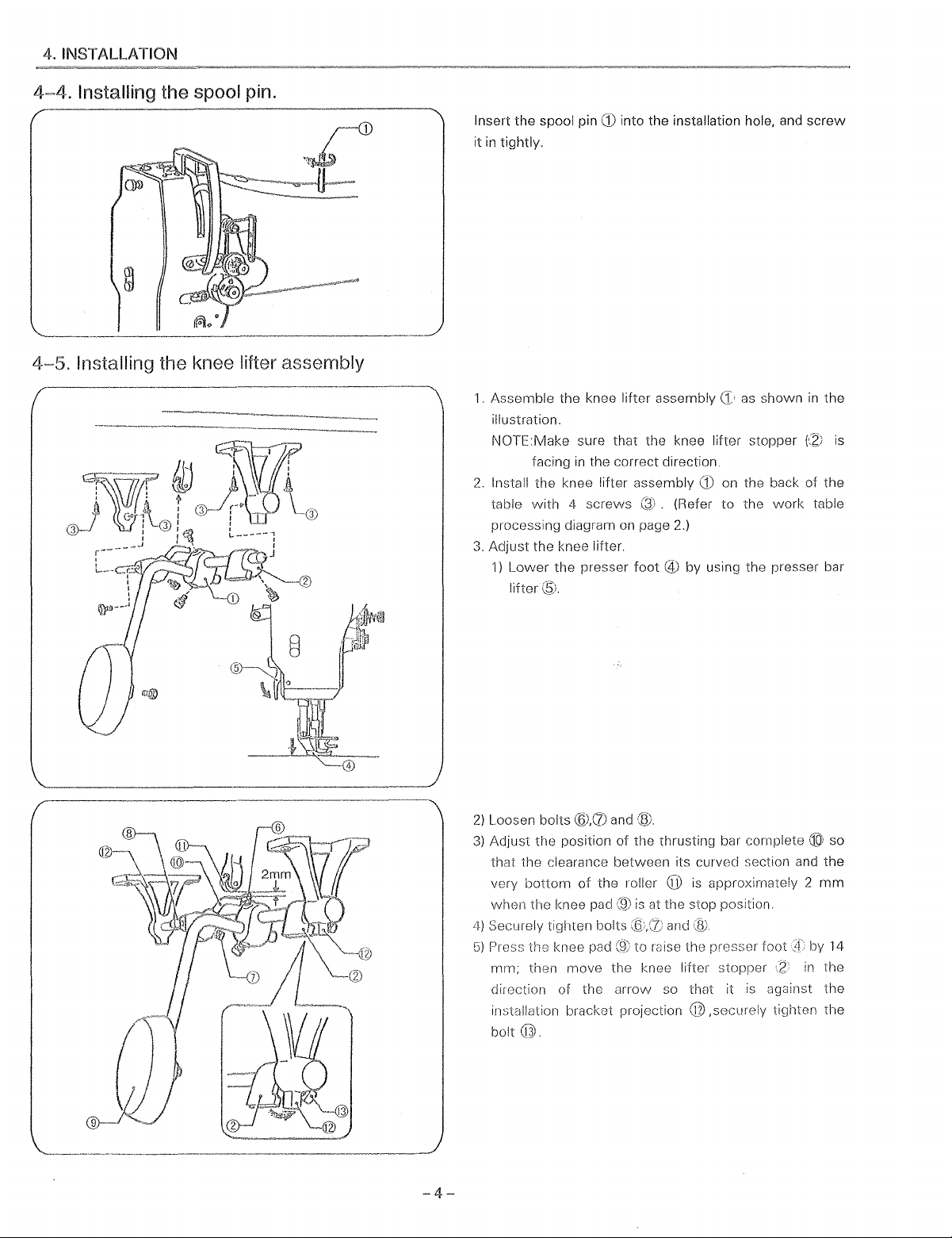
4.
INSTALLATION
4~4.
Installing the spool pin.
4-5.
Installing the knee lifter assembly
Insert
the
spool pin
it
in
tightly.
1.
Assemble
illustration.
NOTE:Make sure that the knee lifter stopper
facing
2.
Install
the
table
with 4 screws
processing diagram on page 2.)
3.
Adjust
the knee lifter.
1)
Lower
lifter®.
CD
into the installation hole, and
the
knee lifter assembly
in
the correct direction.
knee lifter assembly
the
presser
foot @ by
as shown
CD
on the back of
(Refer
to
the
using the presser bar
work
screw
in
the
fZ:;
is
the
table
2)
Loosen bolts
3)
Adjust
the
position
that
the
clearance
very
bottom
when
the
knee pad
4)
Securely tighten bolts and
G)
Press the knee pad
mm;
then
move
direction of the
installation bracket projection
bolt@.
-4-
@.(1)
and
(til
of
the thrusting bar complete ® so
between
of
the
roller @ is approximately 2
(9)
the knee lifter stopper
arrow
its curved section and
is
at the stop position.
to
mise the presser
so that it
is
@,securely
foot
!f
:z
against
tighten
the
mm
by 14
in
the
the
the
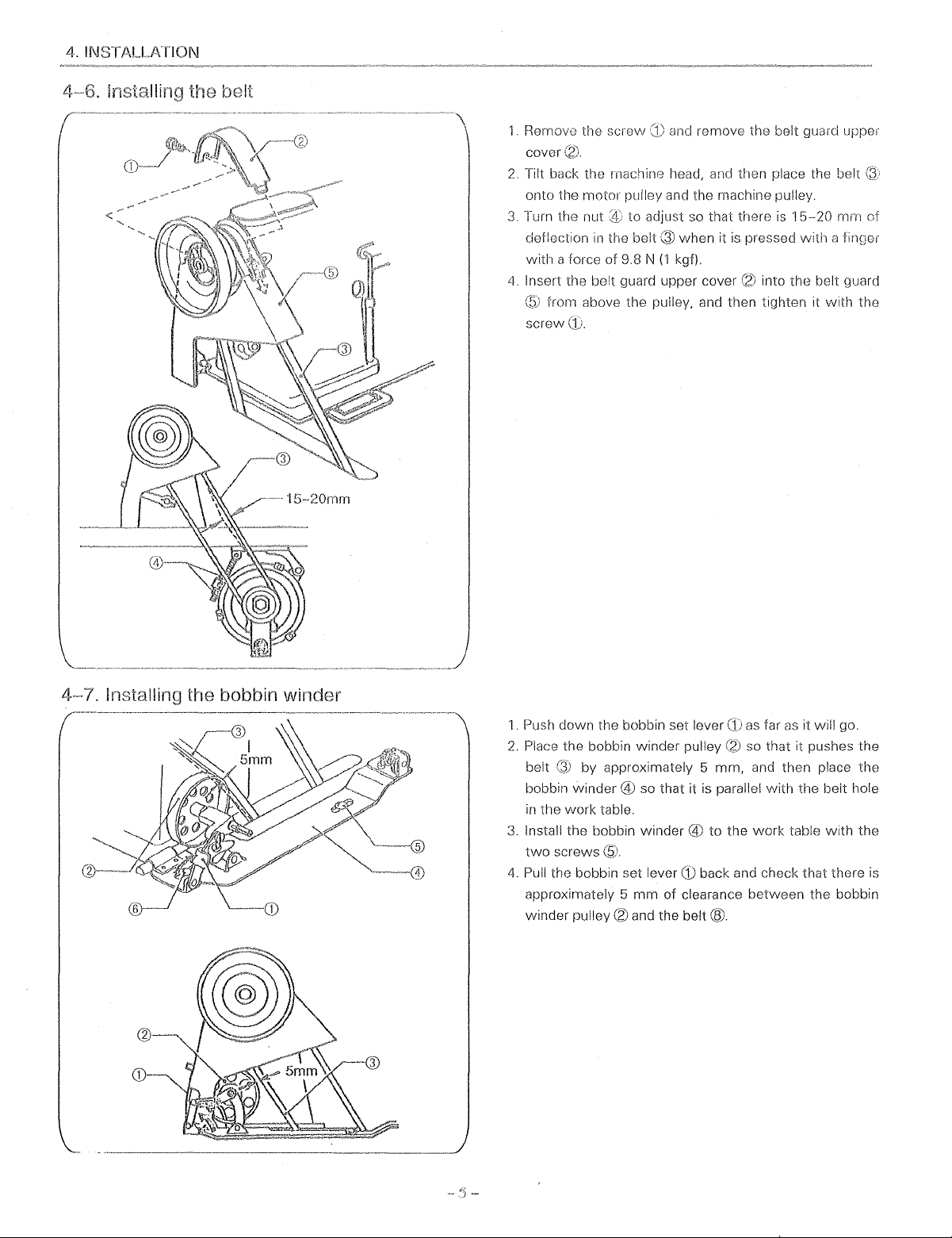
4.
INSTALLATION
ling thH belt
1.
Remove the screw
cover
2.
Tilt back the rnachine head, and then place the belt
onto the
3.
Turn the nut to adjust so that there
deflection
with
4.
Insert the belt guard upper cover into the belt guard
screw
motor
in
a force of 9.8 N
from above the
(1)
and
romove the belt guard upper
pulley and the machine pulley.
is
the belt Q)
when
it
is
pressed
(1
kgf).
pulley, and then tighten it vvith the
15-20
with
a finQer
mm
of
4-7.
Installing the bobbin winder
1.
Push down the bobbin set lever
2.
Place the bobbin winder pulley so that it pushes the
belt by approximately 5 mrn, and then place the
bobbin winder
in
the work table.
3.
Install the bobbin
two
screws
4.
Pull the bobbin set lever
approximately 5
winder pulley
@ so that it is parallel
winder@
@.
GJ
mm
of clearance between the bobbin
(2)
and the
belt®.
as
tar
as
it will go.
with
the belt hole
to the
work
table
with
back and check that there
the
is
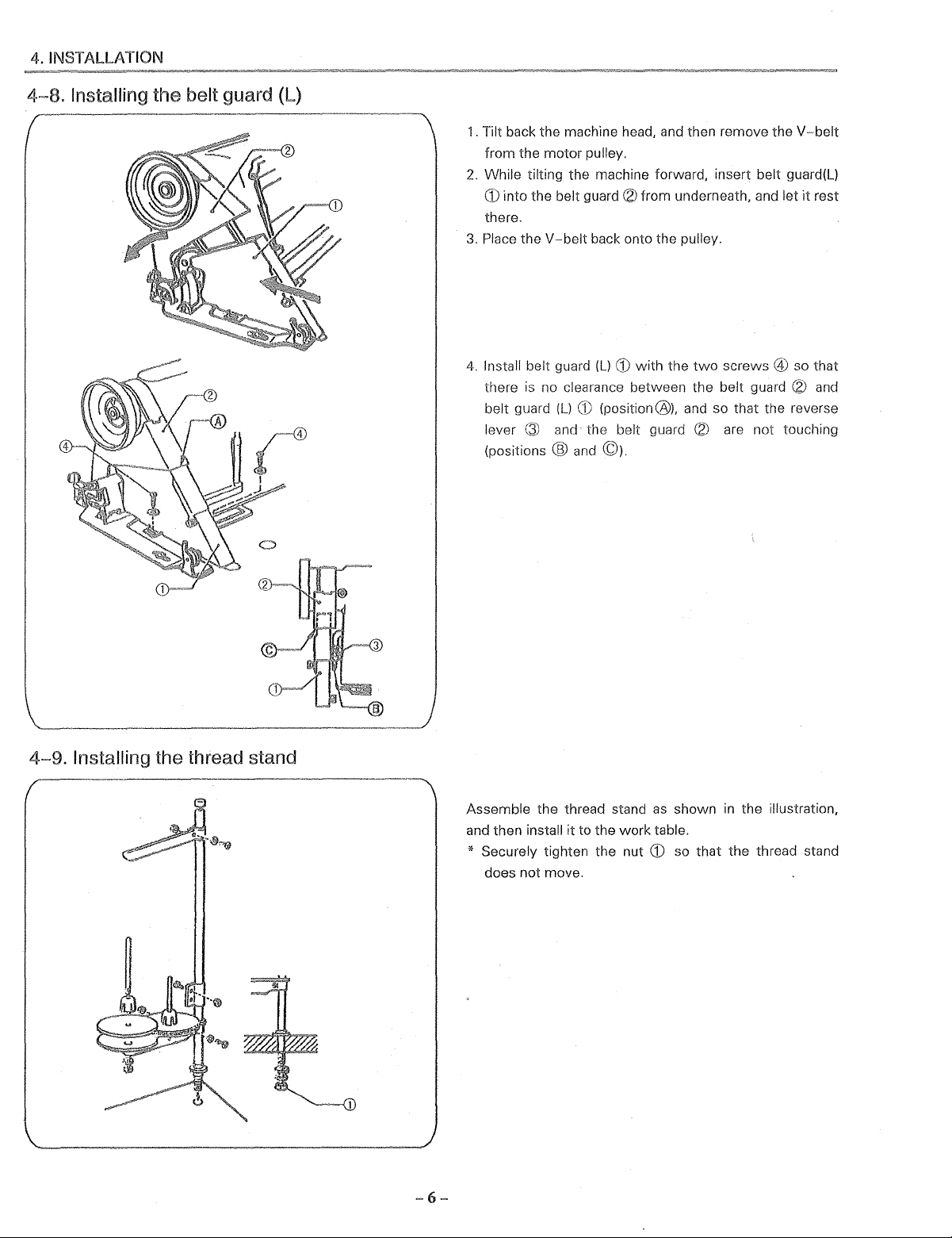
4. INSTALLATION
4~8.
Installing the belt guard (L)
1.
Tilt back the machine head, and then remove the
from the
2.
While tilting the machine forward, insert belt guard(L)
G) into the belt guard
there.
3.
Place the
4.
Install belt guard (L) G)
there is no clearance between the
belt guard (L)
lever @ and the belt guard
(positions
motor
pulley.
V-belt
back onto the pulley.
G)
(position@), and so that the reverse
@ and ©).
(2)
from underneath, and let
with
the
two
screws @ so that
belt guard
(2)
are
not
(2)
touching
V-belt
it
rest
and
4-9.
Installing the thread stand
Assemble the thread stand
it
to the
and then install
work
* Securely tighten the nut
does not move.
as
table.
CD
shown
so
that
in
the illustration,
the thread stand
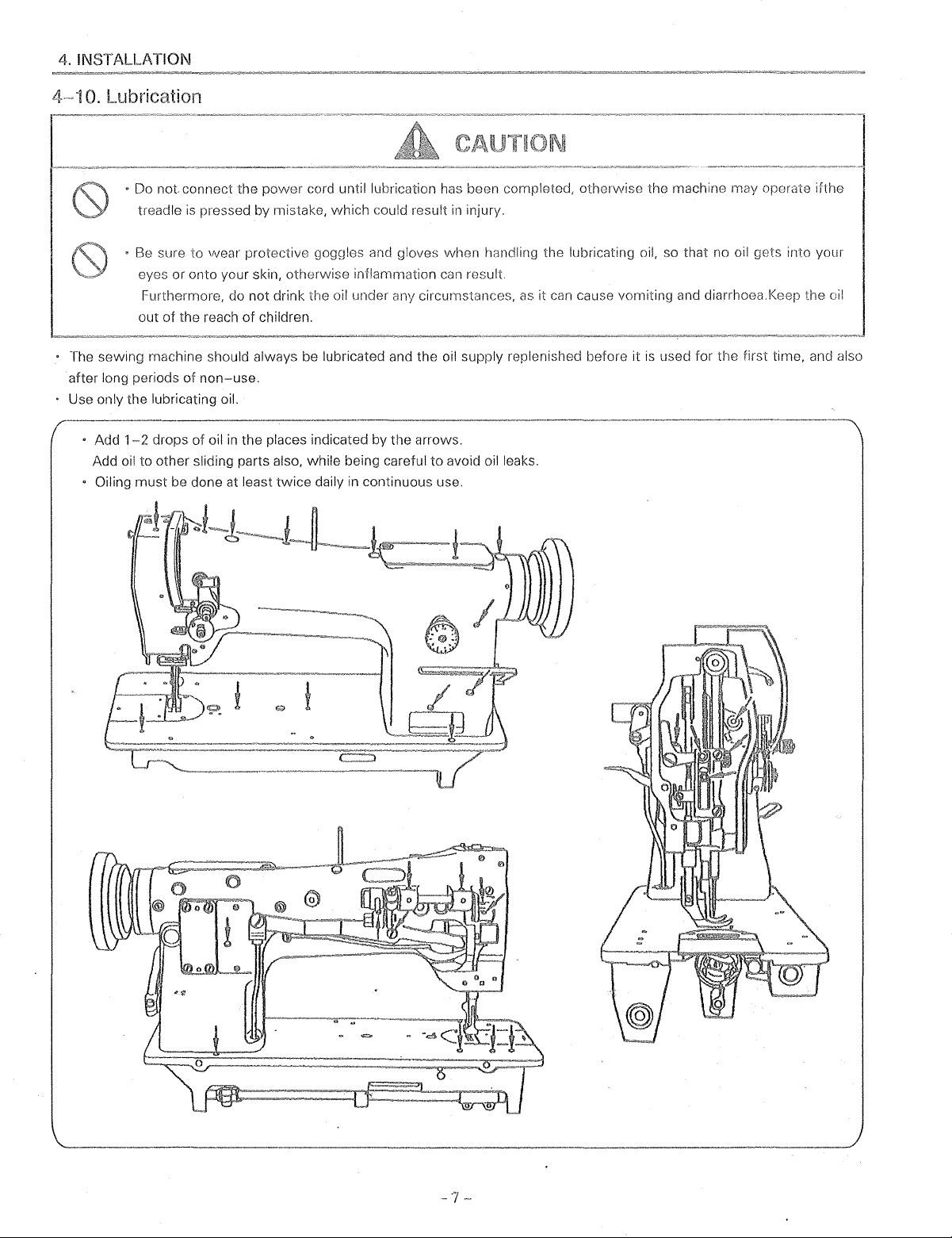
4. INSTALLATION
4-" 10. Lubrication
•
Do
not
connect the
treadle
•
Be
eyes or onto your skin, otherwise inflammation can
out
is
sure
to
Furthermore, do not drink the oil under any circumstances,
of
the reach
power
cord until lubrication has been completed, otherwise the machine may operate ifthe
pressed by mistake, which could result
vvear protective goggles
of
children.
and
gloves when handling the lubricating oil, so that no oil gets into your
in
injury.
result
as
it can cause vomiting and diarrhoea. Keep the oil
The sewing machine should always be lubricated and the oil supply replenished before it
after long periods
Use only the lubricating oil.
•
Add
1-2
Add oil to other sliding parts also, while being careful to avoid oil leaks.
Oiling
must
of
non-use.
drops
of
oil
in
be done at least
the places indicated by the arrows.
twice
daily
in
continuous use.
is
used for the first time, and also
-7-
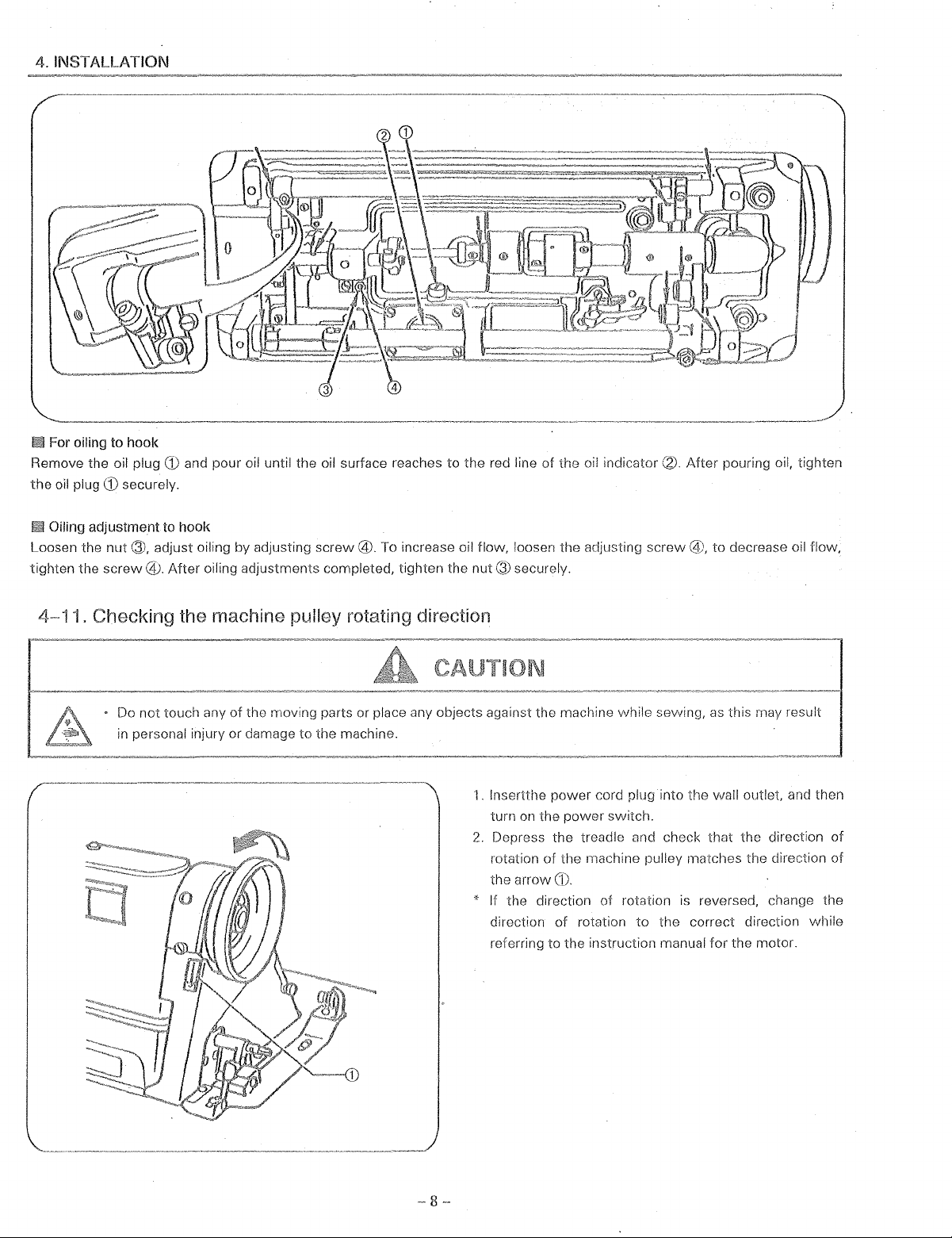
4. INSTALLATION
II
For oiling to hook
Remove the
the
oil plug
oil plug
CD
securely.
CD
and pour oil until the oil surface reaches to the red line of the oil indicator
\2).
After pouring oil, tighten
Oiling adjustment to hook
Loosen the
tighten the
4~
nut®.
adjust oiling by adjusting
screw@.
After
oiling adjustments completed, tighten the
screw@.
To increase oil flow, loosen the adjusting
11. Checking the machine pulley rotating direction
Do
not
touch any
in
personal injury or damage
of
the moving parts or place any objects against the machine while sewing,
to
the machine.
screw@,
nut®
securely.
1.
lnsertthe
turn
2.
Depress the treadle and check that the direction
rotation
the arrow
* If the direction
direction
referring to the instruction manual for the motor.
power
cord plug into the wall
on
the
power
switch.
of
the machine pulley matches the direction
CD.
of
rotation
of
rotation
to
the correct direction while
to
decrease oil flow,
as
this may result
outlet
is
reversed, change the
and then
of
of
-8--
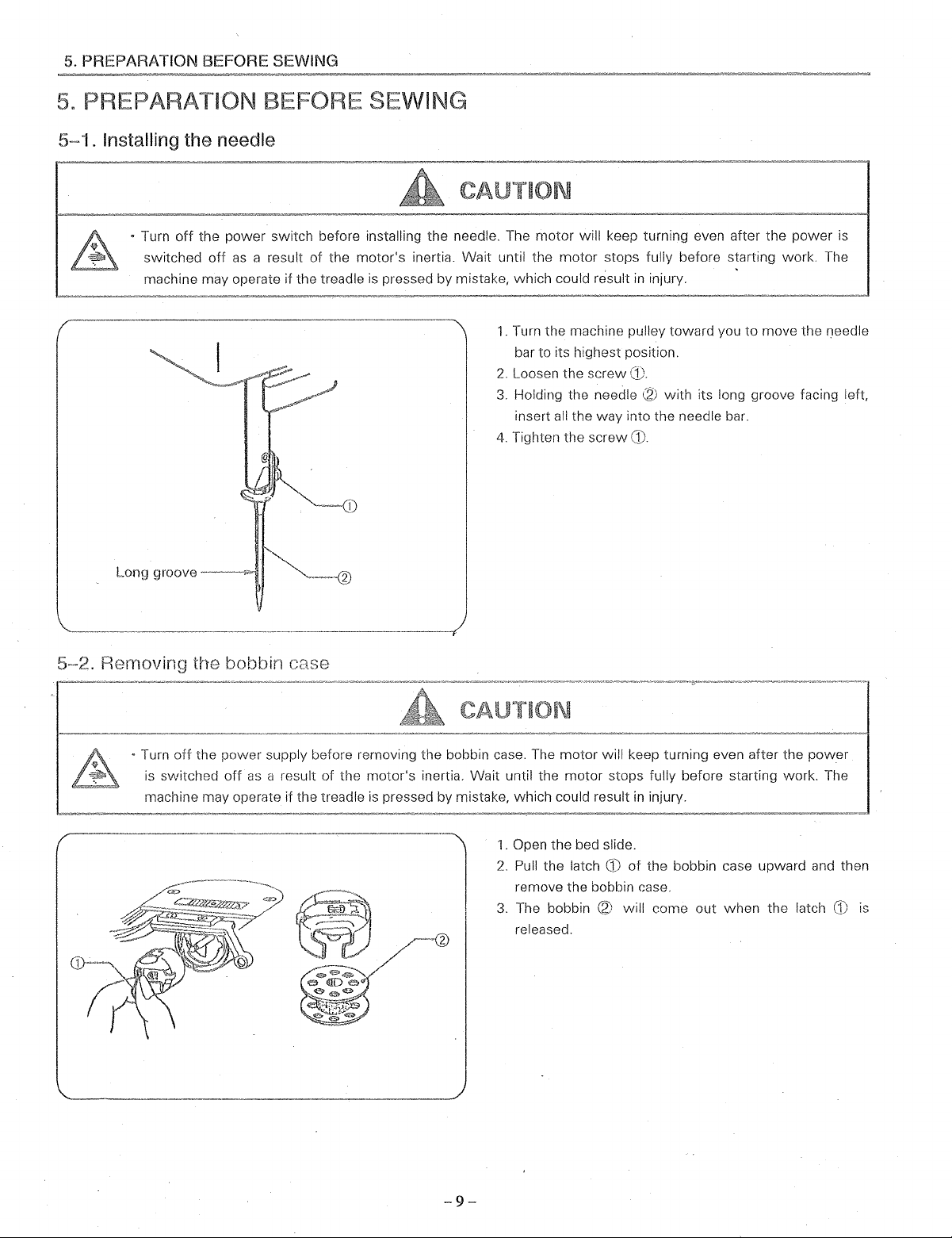
5.
PREPARATION BEFORE SEWING
5.
PR
5-1
PARATION BEFOR SEWING
. Installing the needle
• Turn
off
the
power
switch before installing the needle. The
off
as
switched
machine may operate if the treadle
a result
of
the
motor
motor's
inertia. Wait until the
is
pressed by mistake, which could result
1.
Turn the machine pulley toward you to move the needle
2.
Loosen the
3.
4.
Tighten the
motor
bar to its highest position.
Holding the needle
insert all the way into the needle bar.
will keep turning even after the
stops fully before starting
in
injury.
screw(!).
(2)
with
its long groove facing
screw
CD.
left
Long
5-2.
R£~moving
groove-
~
the bobbin case
• Turn
off
the power supply before removing the bobbin case. The motor will keep turning even after the
is
switched
machine may operate if the treadle
off
as
a result of the motor's inertia. Wait until the
motor
is
pressed by mistake, which could result
1.
Open the bed slide.
2.
Pull the latch
remove the bobbin case.
3.
The bobbin
2
released.
power
stops fully before starting work. The
in
injury.
CD
of
the bobbin case upward and then
(2)
will come
out
when
the latch
CD
is
-9-
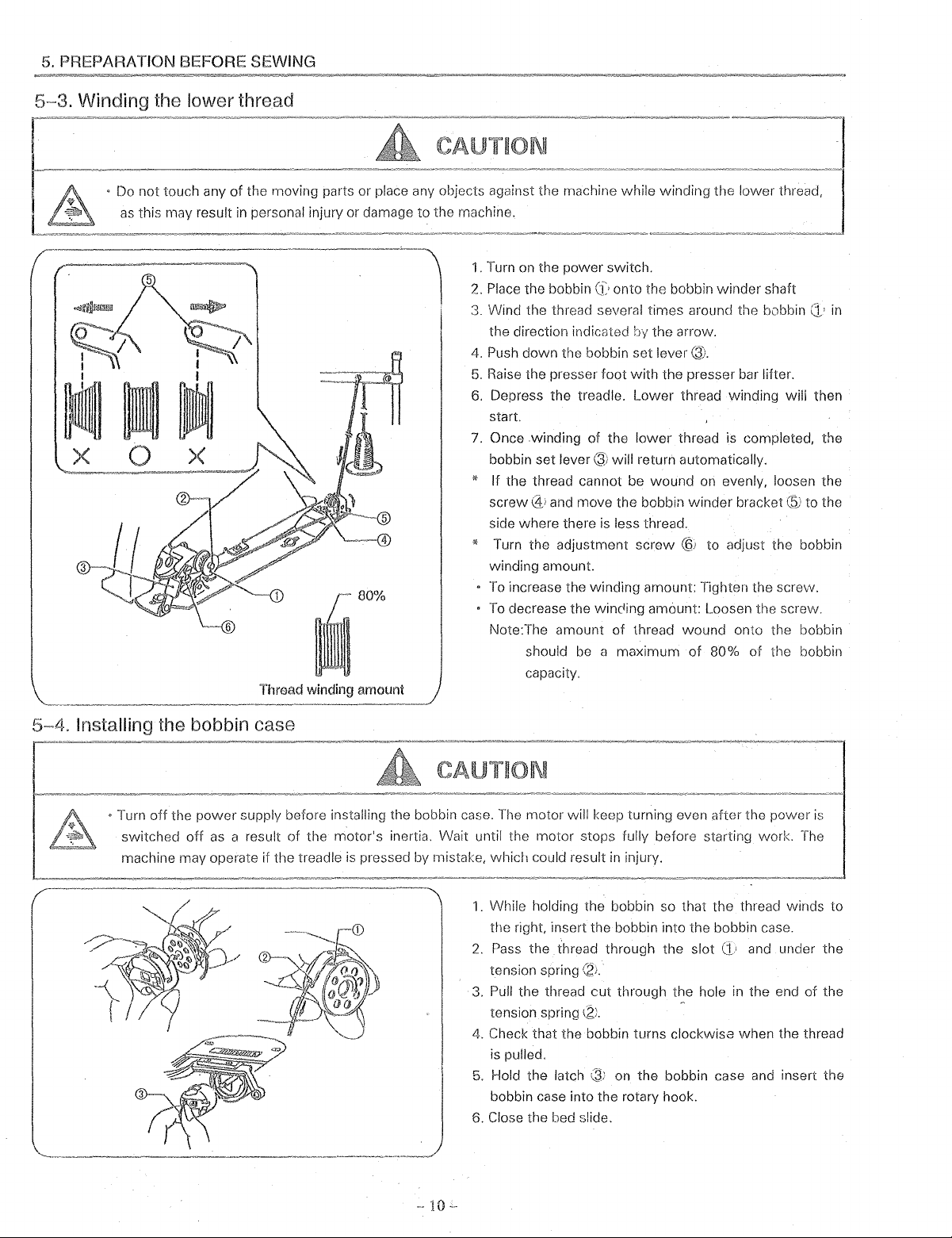
5.
PREPARATION BEFORE SEWING
5~3.
Winding the lower thread
• Do not touch any
as
this may result
of
the moving parts or place any objects against the machine while winding the lower
in
personal injury or damage to the machine.
1.
Turn
on
the power switch.
2.
Place the bobbinG:· onto the bobbin winder shaft
3. Wind the thread several times around the bobbin
the direction indicated the arrow.
4.
Push down the bobbin set lever Q).
5.
Raise
Thread winding amount
the presser foot
6.
Depress the treadle. Lower thread winding will then
start.
7.
Once .winding of the
bobbin set
lever®
* If the thread cannot be wound
screw@_~
side where there
* Turn the adjustment screw
winding amount.
To
To
Note:The amount of thread wound onto the bobbin
and move the bobbin winder bracket to the
increase the winding amount: Tighten the screw.
decrease the wincing amount: Loosen the screw.
should
capacity.
be
with
the presser bar lifter.
lower
thread is completed, the
will return automatically.
on
evenly, loosen the
is
less thread.
@j
to adjust the bobbin
a maximum
of
80% of the bobbin
<1·
in
5~4.
Installing the bobbin case
• Turn
off
the
power
switched
machine may operate if the treadle
off
supply before installing the bobbin case.
as
a result of the motor's inertia. Wait until the motor stops fully before starting work. The
is
pressed by mistake, which could result
The
motor will keep turning even after the power
in
injury.
1.
While holding the bobbin so that the thread winds to
the right, insert the bobbin into the bobbin case.
2.
Pass
the thread through the slot
tension spring
3.
Pull the thread
tension spring
4.
Check that the bobbin turns clockwise when the thread
is
pulled.
5.
Hold the latch
bobbin case into the rotary hook.
6.
Close the bed slide.
\21.
cut
through the hole
(2:.
;.3;
on the bobbin case
and
in
the end of the
and
is
under the
insert the