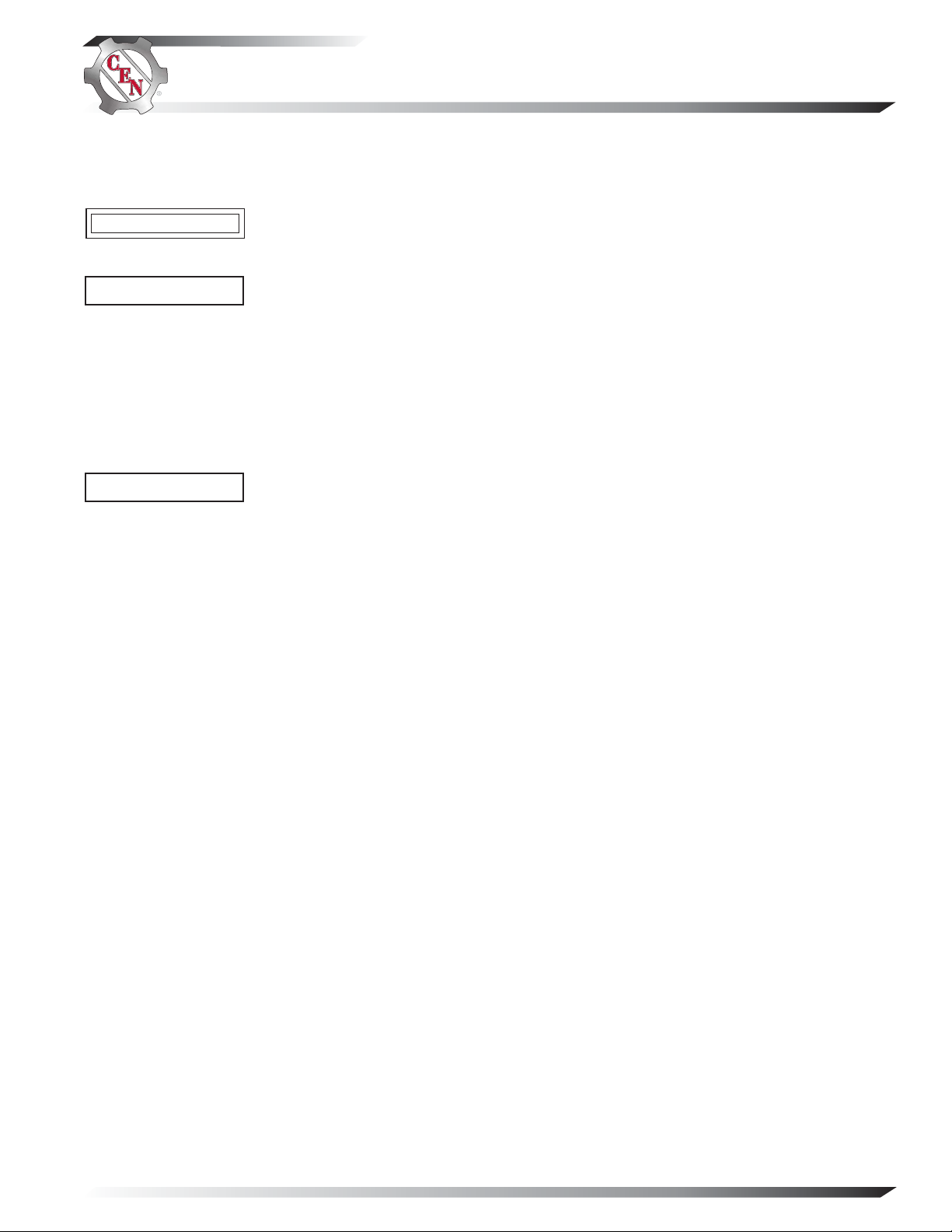
C.E. Niehoff & Co.
N1601, N1602, N1603, and N1604
Alternator Troubleshooting Guide
Hazard Definitions
These terms are used to bring attention to presence of hazard(s)
of various risk levels or to important information concerning
product life.
Indicates presence of hazard(s) that
CAUTION
will or can cause minor personal
injury or property damage.
Indicates special instructions on
NOTICE
installation, operation or mainte nance that are important but not
related to personal injury hazards.
Table of Contents
Section A: Wiring Diagrams ............................... 2 – 3
Section B: Basic Troubleshooting ............................4
Section C: Advanced Troubleshooting .............. 5 – 10
Battery Conditions
Until temperatures of electrical
NOTICE
system components stabilize, these
conditions may be observed during
cold-start voltage tests.
• Maintenance/Low Maintenance Battery
— Immediately after engine starts, system volts are
lower than regulator setpoint, amps are medium.
— 3–5 minutes into charge cycle, system volts
increase, amps decrease.
— 5–10 minutes into charge cycle, system volts
increase to, or near, regulator setpoint and amps
decrease to a minimum.
— Low maintenance battery has same characteristics
with slightly longer recharge times.
• Maintenance-free Battery
— Immediately after engine starts, system volts are
lower than regulator setpoint, low charging amps.
— Once charge cycle begins, low volts and low amps
are still present.
— After alternator energizes, voltage will increase
several tenths. Amps will increase gradually, then
quickly, to medium to high amps.
— F i n a l l y , v o l t s w i l l i n c r e a s e t o s e t p o i n t a n d a m p s w i l l
decrease.
The time it takes to reach optimum voltage and amperage will vary with engine speed, load, and ambient
temperature.
• High-cycle Maintenance-free Battery
These batteries respond better than standard maintenance-free. Charge acceptance of these batteries may
display characteristics similar to maintenance batteries.
• AGM (Absorbed Glass Mat) Maintenance-free Batter y
These dry-cell batteries respond better than standard
maintenance-free. If battery state of charge drops to
75% or less, batteries should be recharged to 95% or
higher separately from the engine’s charging system to
avoid damaging charging system components and to
provide best overall performance. Charge acceptance of
these batteries may display
maintenance batteries.
characteristics similar to
Battery Charge Volt and Amp Values
Volt and amp levels fluctuate depending on the battery
state of charge. If batteries are in a state of discharge—as
after extended cranking time to start the engine—system
volts will measure lower than the regulator setpoint after
the engine is restarted and system amps will measure
higher. This is a normal condition for the charging system;
the greater the battery discharge level, the lower the system
volts and the higher the system amps. The volt and amp
readings will change as batteries recover and become fully
charged: system volts will increase to regulator setpoint
and system amps will decrease to low level (depending on
other loads).
• Low Amps: Minimum or lowest charging system amp
value required to maintain battery state of charge,
obtained when testing the charging system with a fully
charged battery and no other loads applied. This value
will vary with battery type.
• Medium Amps: System amps value which can cause
the battery temperature to rise above adequate charging temperature within 4-8 hours of charge time. To
prevent battery damage, the charge amps should be
reduced when battery temperature rises. Check battery
manufacturer’s recommendations for proper charge
amp rates.
• High Amps: System amps value which can cause
the battery temperature to rise above adequate charging temperature within 2-3 hours of charge time. To
prevent battery damage, the charge amps should be
reduced when battery temperature rises. Check battery
manufacturer’s recommendations for proper charge
amp rates.
• Battery Voltage: Steady-state voltage value as mea-
sured with battery in open circuit with no battery load.
This value relates to battery state of charge.
• Charge Voltage: Voltage value obtained when the
charging system is operating. This value will be higher
than battery voltage and must never exceed the regulator voltage setpoint.
• B+ Voltage: Voltage value obtained when measuring
voltage at battery positive terminal or alternator B+
terminal.
• Surface Charge: Higher than normal battery voltage
occurring when the battery is disconnected from
battery charger. The surface charge must be removed
to determine true battery voltage and state of charge.
• Significant Magnetism: Change in strength or intensi-
ty of a magnetic field present in alternator rotor shaft
when the field coil is energized. The magnetic field
strength when the field coil is energized should feel
stronger than when the field is not energized.
• Voltage Droop or Sag: Normal condition occurring
when the load demand on alternator is greater than
rated alternator output at given rotor shaft RPM.
TG29D
Page 1
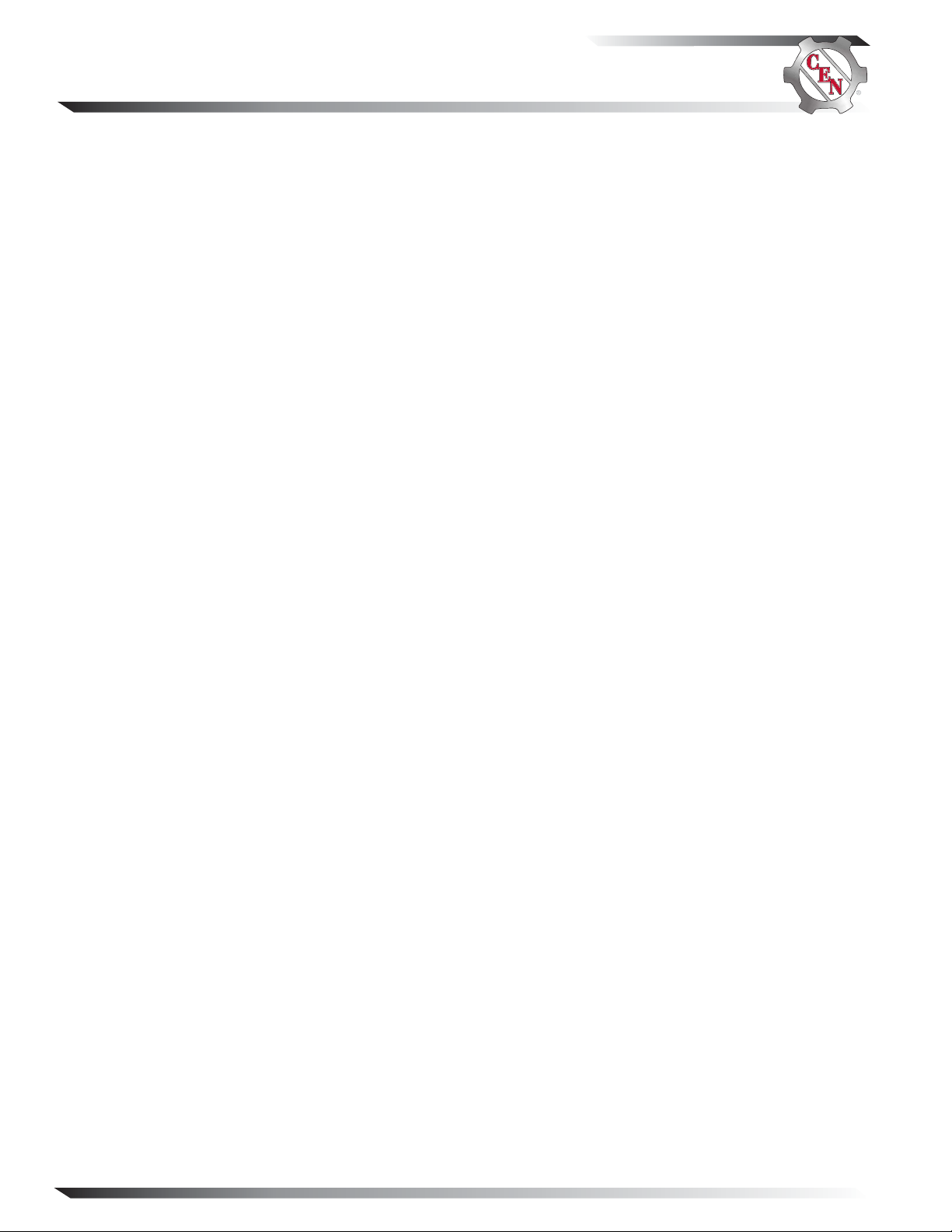
Section A: Wiring Diagrams
CEN N1601, N1602, N1603, N1604
Alternator and Regulator Description
and Operation
The alternators listed below are self-rectifying. All windings and current-transmitting components are nonmoving, so there are no brushes or slip rings to wear
out. Energize switch activates regulator. Field coil is
then energized.
• N1601 28 V 400 A
• N1602 28 V 400 A with optional 28 V/ 14 V
(50 A maximum on 14 V)
• N1603 28 V 450 A
• N1604 28 V 400 A
N3107 regulator used on some N1601, N1603, and
N1604 alternators maintains alternator output voltage
at regulated setting as vehicle electrical loads are
switched on and off. Alternator output current is selflimiting and will not exceed rated capacity of alternator.
The regulator has:
• an AC terminal to provide optional AC voltage
output tap.
• overvoltage cutout (OVCO). Regulators with OVCO
(overvoltage cutout) will trip at vehicle electrical
system voltages above 32 volts that exist longer than
3 seconds. OVCO feature detects high voltage and
reacts by signaling relay in field control circuit to
open. This turns off alternator. Restarting engine
resets OVCO circuit.
The following regulators receive energize signal after
engine is running:
• N3118—used on some N1602 alternators
• N3211—used on some N1601 and N1603 alternators
• N3223—used on some N1602 alternators
• N3236—used on some N1604 alternators
• N3237—used on some N1602 and N1603 alternators
• N3245—used on some N1602 and N1603 alternators
Regulator monitors alternator rotation and provides
field current only when it detects alternator shaft rotating at suitable speed. After regulator detects alternator
rotation, it gradually applies field current, preventing an
abrupt mechanical load on accessory drive system. The
soft start may take up to 10 seconds at full electrical
load. These regulators:
• are negative temperature compensated. Setpoints
are 28.0 ± 0.2 V (and on N3118 and N3223, 14.0 ±
0.2 V. See below.) at 75F. N3237 and N3245 regulators are negative temperature compensated according to switch-selected battery type. Customer selects
position per application.
• provide overvoltage cutout (OVCO). Regulator will
trip OVCO when system voltage rises above 32 V in
a 28 V system (16 V in a 14 V system) for longer than
3 seconds. OVCO feature detects high voltage and
signals the field circuit to open, turning off alternator. Restarting engine resets OVCO circuit.
• maintain alternator output voltage at regulated
settings as vehicle electrical loads are switched
on and off.
N3118 and N3223 regulators can be used in single
28 V or dual voltage applications. The regulators:
• allow single-voltage operation (28 V only). 14 V
single voltage application is not available with
these regulators.
• provide optional 28 V/14 V output only from the
regulator when phase cable from alternator is
connected to regulator.
Page 2
TG29D
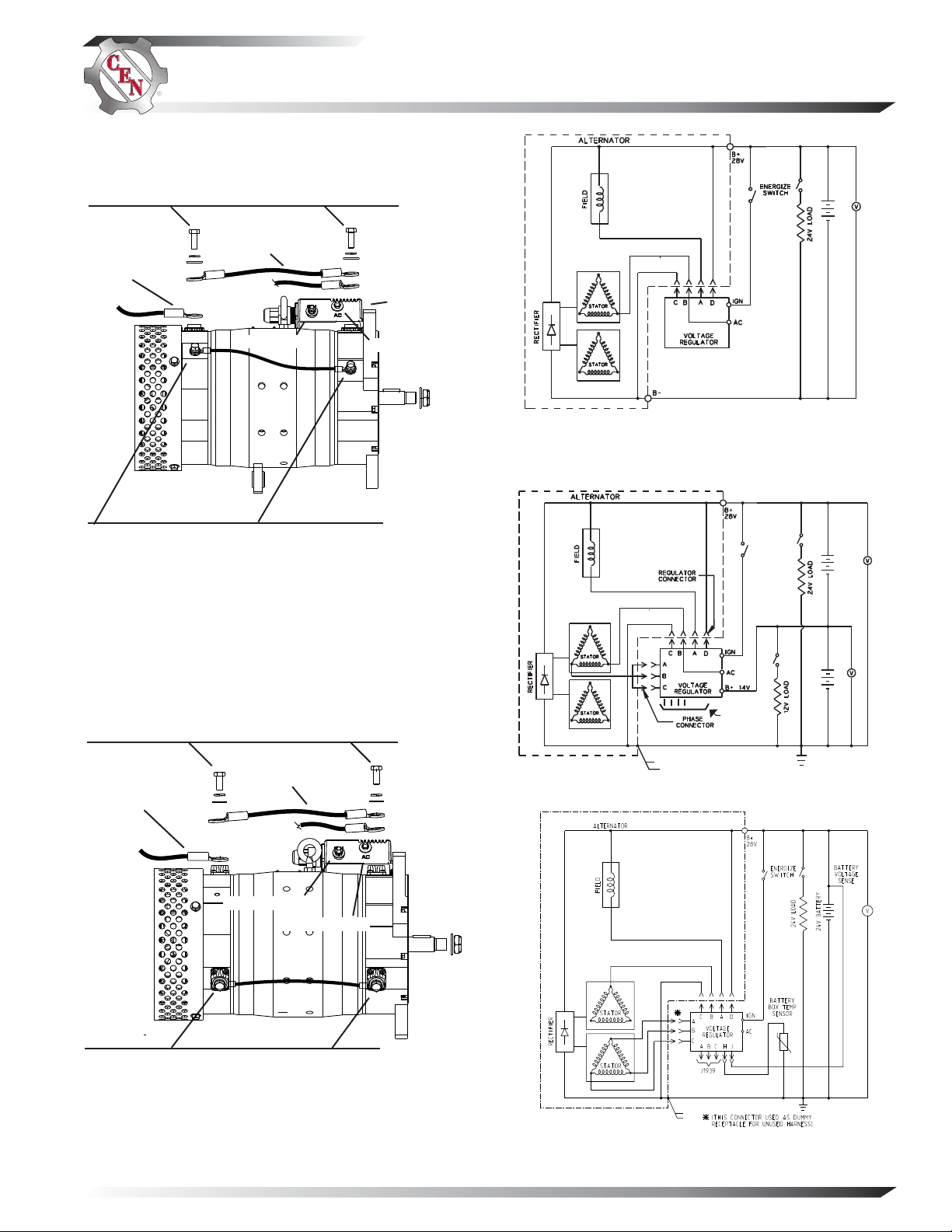
B+ connections on alternator
Both positive terminals must be connected together at battery positive
potential, using interconnect cable and cable of suitable size as part
of vehicle cabling, when alternator is installed in vehicle and during
operation.
Interconnect
Positive cables
from vehicle
cable
IGN terminal
14V B+
terminal
(N3118 and
N3223 only)
AC terminal
Section A: Wiring Diagrams (CONT’ D)
Case ground: N1601, N1603
Isolated ground: N1604
Figure 3 — N1601-1 thru -4, N1603-1/-2, and N1604-1/-2
Wiring Diagram
B– connections on alternator
Both B – terminals must be connected to the vehicle’s common ground,
using interconnect cable and cable of suitable size as part of vehicle
cabling, when alternator is installed in vehicle and during operation.
Figure 1 — N1601, N1602, and N1603
Alternator and Regulator Terminals
B+ connections on alternator
Both positive terminals must be connected together at battery positive
potential, using interconnect cable and cable of suitable size as part
of vehicle cabling, when alternator is installed in vehicle and during
operation.
Positive cables
from vehicle
Interconnect
cable
IGN terminal
AC terminal
•••
N3223 only —
J1939 connector
Figure 4 — N1602-1, -2, -4, -5, - 6 Wiring Diagram
B– connections on alternator
Both B – terminals must be connected to the vehicle’s common ground,
using interconnect cable and cable of suitable size as part of vehicle
cabling, when alternator is installed in vehicle and during operation.
Figure 2 — N1604
Alternator and Regulator Terminals
TG29D
Figure 5 — N1602-3/-7 and N1603-3 Wiring Diagram
Page 3