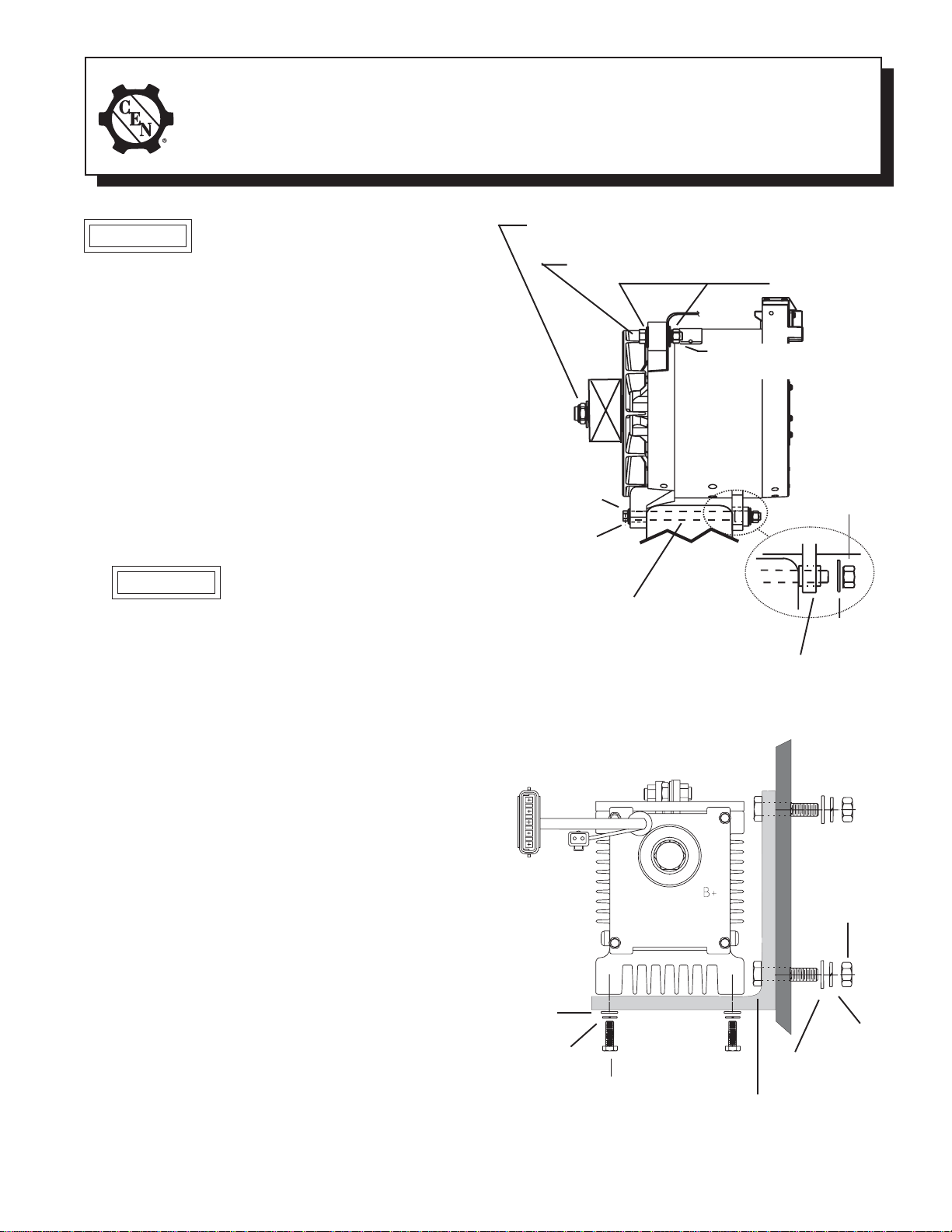
C. E. Niehoff & Co
BRUSHLESS ALTERNATORS
C616 Alternator
with Regulator
and External Rectifier
Installation Instructions
CAUTION
This symbol is used to indicate
presence of hazards that can cause
minor property damage.
C616 Alternator
1. Mounting lug width on alternator complies with
SAE J180 (May 1987) standards.
2. Units are shipped with shaft collar, hardened
washer and locknut. Remove and discard shaft
collar. Install pulley and furnished hardened
washer. Torque locknut to 163 Nm/ 120 lb. ft.
3. Use hardened washers between aluminum
surfaces and bolt heads and nuts. Torque
mounting bolts to 88 Nm/65 lb. ft.
CAUTION
Slip bushing in lower rear
mounting lug must be securely
tightened against mounting
bracket on engine. Failure
to do so can result in
broken mounting lugs
or broken upper
mounting bracket.
0.625-18 Locknut and hardened washer—
torque to 163 Nm/120 lb.ft.
12mm/0.50 in. Mounting bolt
Hardened washers
TT
T
TT
TT
T
TT
T
TT
TT
TT
TT
T
12mm/0.50 Locknut –
torque to 88 Nm/65 lb. ft.
TT
T
TT
12mm/0.50 in.
Mounting bolt
(full length)
TT
T
T
TT
TT
TT
TT
T
Hardened
washer
Alternator mounting
bracket on engine
Slip bushing must be tightened against bracket —
see “CAUTION” at left
TT
Bracket
on engine
Figure 1 - C616 Alternator Inst allation
12mm/0.50
Locknut –
torque to
88 Nm/65 lb. ft.
TT
T
TT
TT
T
TT
TT
T
TT
Hardened
washer
A8-205 External Rectifier and A4-501 Bracket
1. Mounting location of rectifier and bracket
should provide proper cooling and protect
rectifier from direct water, road debris, or
chemicals.
2. Using the standard A9-463 wiring harness,
rectifier can be mounted up to 6 feet away
from alternator.
3. Use hardened washers between aluminum
surfaces and bolt heads and nuts. Bracket
mounting bolts must have minimum .50 in.
thread engagement. See Figure 2 for torque
values.
®
4. Use a suitable adhesive such as Loctite
or equivalent on screws. Follow manufacturer’s
instructions.
222
Flat
T
TT
washer
Lockwasher
.3750-16 UNC-2B Mounting bolt
grade 5 or better–
torque to 27 Nm/20 lb.ft.
TT
TT
TT
T
TT
T
TT
Figure 2 - Rectifier and Bracket Installation
54 Nm/40 lb.ft.
TT
T
TT
TT
T
TT
Flat washer
11mm/0.44 in.
Mounting bolt -
grade 5 or better
Locknut
(4 places) –
torque to
TT
T
TT
TT
T
TT
TT
T
TT
Lockwasher
II0099APage 1 of 2
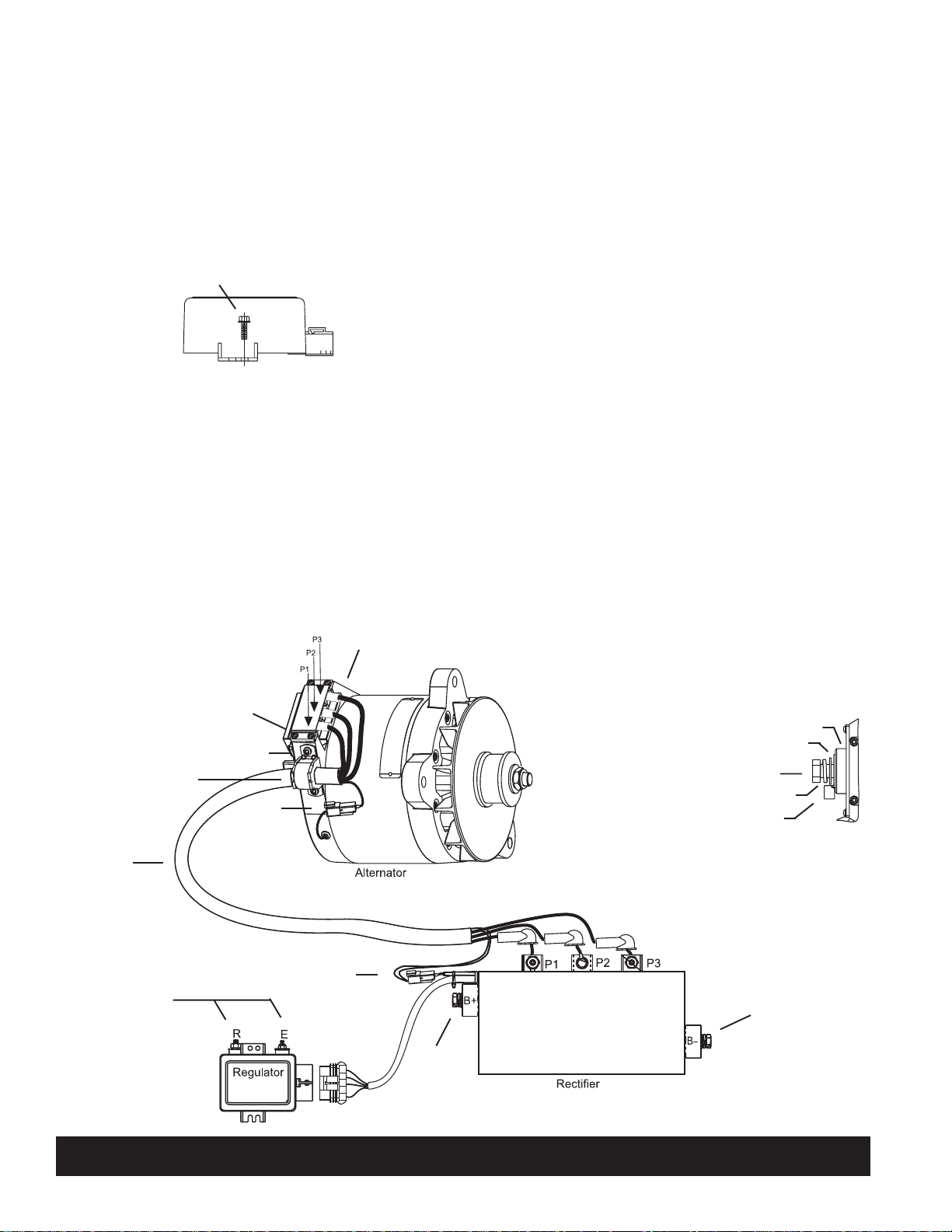
A2-136 Regulator
1. Mounting location of regulator must provide
protection from water, road debris, or
chemicals.
Regulator can be located up to 18 inches
away from the rectifier. If extension harness
CEN A9-448 is added, the regulator can be
moved an additional 43 in. away.
2. See Figure 3 for torque values.
#10-32 x .62 flange lock screw (4 places) -
torque to 8.5 Nm/75 lb. in.
TT
T
TT
Figure 3 - Regulator Installation
Wiring Connections
1. Alternator phase cable:
a. Remove and save terminal cover screws and
terminal cover.
b. Connect phase cable into terminal block on top
of alternator either through anti-drive end (as
shown in Figure 4) or through drive end:
1) Run phase cable through cable bracket
mounted in one of two locations (LOC. A
or LOC. B). See Figure 4.
Phase terminal bolts (3 places) –
torque to 9 Nm/80 lb. in.
Terminal cover screws –
torque to 3.9 Nm/35 lb. in.
Screws –
torque to 6.7 Nm/60 lb. in.
Cable bracket
Phase
cable
LOC. A
TT
TT
T
Field
inline
connection
TT
T
TT
TT
TT
T
TT
TT
T
Cable bracket
TT
T
TT
TT
TT
T
LOC. B
2) Use torque values shown to fasten cables
to terminal block.
3) Coat terminals with Dow Corning® 1-2577
Low VOC RTV coating or equivalent. Do not
use coating containing acetic acid (vinegar
smell) on electrical components.
c. Replace terminal cover on terminal block. If
phase cable was routed through the anti-drive
end, the terminal cover must be rotated 180º
before re-installing. Use torque value shown to
fasten screws in terminal cover.
2. Connect remaining harnesses between components
as shown in Figure 4. Use torque values shown.
3. Choose wire gauge for B+ and B– cables capable of
handling maximum alternator output with minimum
voltage drop.
4. Connect E terminal on regulator to ignition source
through oil pressure switch, using #10 ring
terminal. Torque #10-24 terminal nut to 3.4 Nm/30
lb. in.
5. If required, connect R terminal to tachometer or
relay, using 1/4 in. ring terminal. Torque terminal
nut to 3.4 Nm/30 lb.in.
Sealing Wiring Connections
1. On ALL metallic electrical connections to rectifier
(including B+ and B– connections), alternator,
regulator, and their harness connectors, apply Dow
Corning® 1-2577 Low VOC RTV coating or equivalent. Do not use coating containing acetic acid
(vinegar smell) on electrical components.
2. At regulator harness connections, apply coating as
described in step 1, then wrap connection in
electrical tape from sleeve to sleeve.
Insulator
B+ terminal bolt –
Washer
torque to 30 Nm/22 lb. ft.
Lockwasher
Battery output cable terminal
B+ Terminal Connection
TT
TT
T
TT
TT
T
TT
T
TT
TT
T
TT
TT
T
TT
Phase terminal bolts (3 places) –
torque to 8 Nm/70 lb. in.
R and E
terminal nuts –
torque to
3.4 Nm/30 lb. in.
Field inline connection
TT
T
TT
T
TT
TT
TT
TT
T
B+
(see
inset above)
TT
T
TT
B– terminal bolt –
torque to 30 Nm/22 lb. ft.
T
TT
TT
Figure 4 - Electrical Connections
C. E. Niehoff & Co. • 2021 Lee Street • Evanston, IL 60202 Tech Services Hotline 800-643-4633
II0099APage 2 of 2