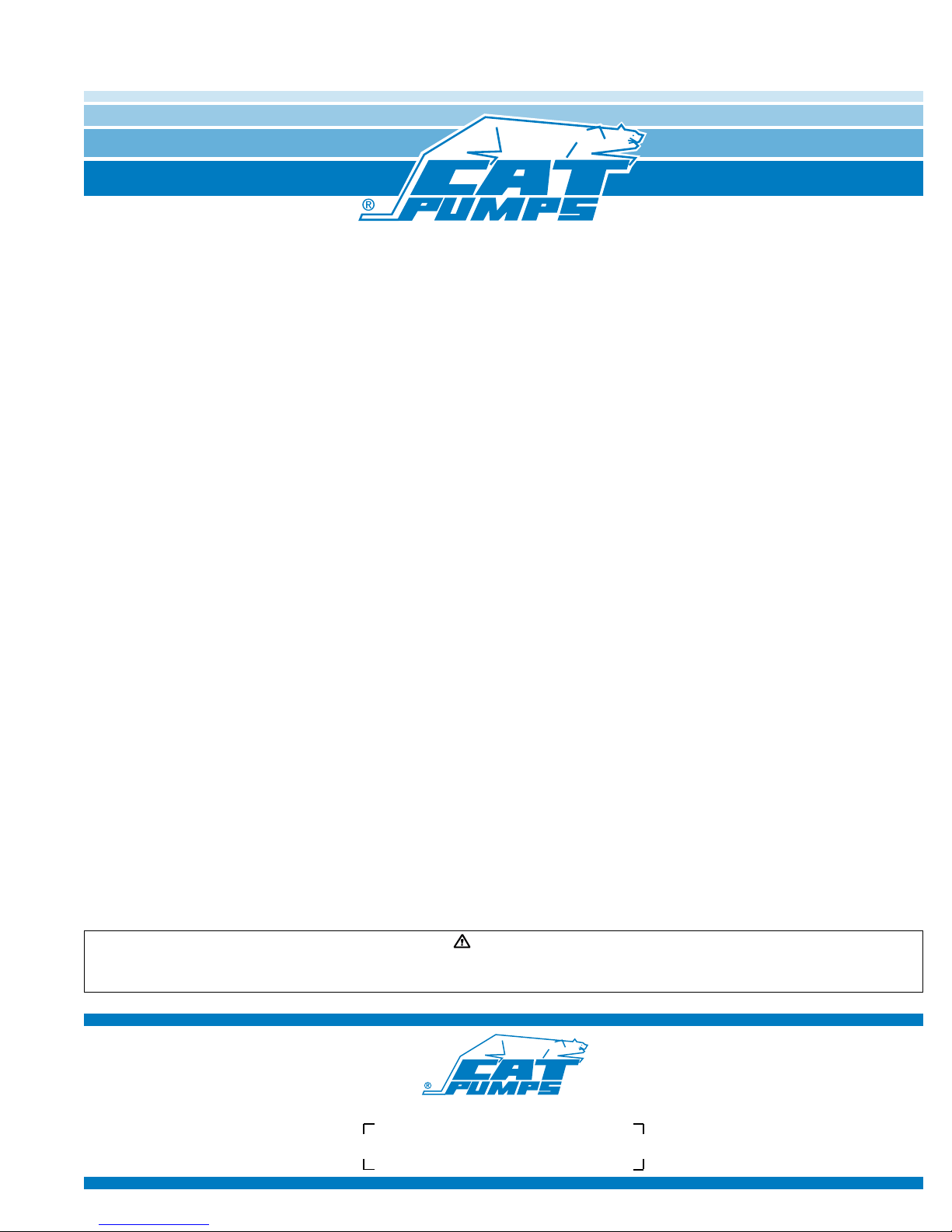
PISTON PUMP SERVICE MANUAL
3 FRAME: 280,281,290,291 10 FRAME: 621,623,820,821,825,1010,1011,1015
4 FRAME: 331,333,335,430,431,435 25 FRAME: 1520,1521,1525,2520,2521,2525,2520C
4406,1406,0406,4206,1206,0206 :EMARF 06093,323 :EMARF 5
INSTALLATION AND START-UP INFORMATION
Optimum performance of the pump is dependent upon the entire liquid system and will be obtained only with
the proper selection, installation of plumbing, and operation of the pump and accessories.
SPECIFICATIONS: Maximum specifications refer to individual attributes. It is not
implied that all maximums can be performed simultaneously. If more than one
maximum is considered, check with your CAT PUMPS supplier to confirm the
proper performance and pump selection. Refer to individual pump Data Sheet for
complete specifications, parts list and exploded view.
LUBRICATION: Fill crankcase with special CAT PUMP oil per pump specifications
[3FR-10 oz., 4FR-21 oz., 5FR-21 oz.,10FR-40 oz., 25FR-84 oz., 60FR-10 Qts.]. DO
NOT RUN PUMP WITHOUT OIL IN CRANKCASE. Change initial fill after 50 hours
running period. Thereafter, change oil every 3 months or 500 hour intervals.
[25FR, 60FR] Oiler adjustment is vertical to start feed, horizontal to stop feed, 45°
to drain reservoir. Additional lubrication may be required with increased hours of
operation and temperature.
PUMP ROTATION: Pump was designed for forward rotation to allow optimum
lubrication of the
level is increased slightly above center dot to assure adequate lubrication.
PULLEY SELECTION: Select size of motor pulley required to deliver the desired
flow from Horsepower Requirement and Pulley Selection Chart (refer to Tech
Bulletin 003).
DRIVE SELECTION: The motor or engine driving the pump must be of adequate
horsepower to maintain full RPM when the pump is under load. Select the electric
motor from the Horsepower Requirement Chart according to required pump
discharge flow, maximum pressure at the pump and drive losses of approximately
3-5%. Consult the manufacturer of gas or diesel engine for selection of the proper
engine size.
MOUNTING: Mount the pump on a rigid, horizontal surface in a manner to permit
drainage of crankcase oil. An uneven mounting surface will cause extensive
damage to the pump base. To minimize piping stress, use appropriate flexible
hose to inlet and discharge ports. Use the correct belt; make sure pulleys are
aligned. Excessive belt tension may be harmful to the bearings. Hand rotate pump
before starting to be certain shaft and bearings are free moving.
LOCATION: If the pump is used in extremely dirty or humid conditions, it is
recommended pump be enclosed. Do not store or operate in excessively high
temperature areas or without proper ventilation.
INLET CONDITIONS: Refer to complete Inlet Condition Check-List in this manual
before starting system. DO NOT STARVE THE PUMP
Temperatures above 130°F are permissible. Add 1/2 PSI inlet pressure per each
degree F over 130°F. Elastomer or RPM changes may be required. See Tech
Bulletin 002 or call CAT PUMPS for recommendations.
C.A.T.: Installation of a C.A.T. (Captive Acceleration Tube) is recommended in
applications with stressful inlet conditions such as high temperatures, booster pump
feed, long inlet lines or quick closing valves.
crosshead area.
Reverse rotation is acceptable if the crankcase oil
OR R
UN DRY.
DISCHARGE CONDITIONS: OPEN ALL VALVES BEFORE STARTING SYSTEM to
avoid deadhead overpressure condition and severe damage to the pump or system.
Install a Pulsation Dampening device onto the discharge head or in the discharge
line. Be certain the pulsation dampener (Prrrrr-o-lator) is properly precharged for the
system pressure (refer to individual Data Sheet).
A reliable Pressure Gauge should be installed near the discharge outlet of the high
pressure manifold. This is extremely important for adjusting pressure regulating
devices and also for proper sizing of the nozzle or restricting orifice. The pump is
rated for a maximum pressure; this is the pressure which would be read at the
discharge manifold of the pump, NOT AT THE GUN OR NOZZLE.
Use PTFE thread tape or pipe thread sealant (sparingly) to connect accessories or
plumbing. Exercise caution not to wrap tape beyond the last thread to avoid tape from
becoming lodg
the pump or system.
PRESSURE REGULATION: All systems require both a primary pressure regulating
device (i.e., regulator, unloader) and a secondary pressure safety relief device (i.e.,
pop-off valve, safety valve). The primary pressure device must be installed on the
discharge side of the pump. The function of the primary pressure regulating device
is to protect the pump from over pressurization, which can be caused by a plugged
or closed off discharge line. Over pressurization can severely damage the pump,
other system components and can cause bodily harm. The secondary safety relief
device must be installed in-line between the primary device and pump on the
discharge side of the manifold. This will ensure pressure relief of the system if the
primary regulating device fails. Failure to install such a safely device will void the
warranty on the pump.
If a large portion of the pumped liquid is by-passed (not used) when the high
pressure system is running,
sized, baffled supply tank or to drain. If routed to the pump inlet, the by-pass liquid
can quickly develop excessive heat and result in damage to the pump. A
temperature control device to shut the system down within the pump limits or multiple
THERMO VALVES must be installed in the by-pass line to protect the pump.
NOZZLES: A worn nozzle will result in loss of pressure. Do not adjust pressure
regulating device to compensate. Replace nozzle and reset regulating device to
system pressure.
PUMPED LIQUIDS: Some liquids may require a flush between operations or
before storing. For pumping liquids other than water, contact your CAT PUMPS
supplier.
STORING: For extended storing or between use in cold climates, drain all pumped
liquids from pump and flush with antifreeze solution to prevent freezing and
damage to the pump. DO NOT RUN PUMP WITH FROZEN LIQUID (refer to Tech
Bulletin 083).
ed in the p
ump or accessories. This condition will cause a malfunction of
th
is by-pass liquid should be routed to an adequately
All systems require both a primary pressure regulating device (i.e., regulator, unloader) and a secondary pressure safety relief device (i.e., pop-off valve, safety valve).
Failure to install such relief devices could result in personal injury or damage to the pump or to system components. CAT PUMPS does not assume any liability or responsibility
for the operation of a customer’s high pressure system.
World Headquarters
CAT PUMPS
1681- 94th Lane N.E. Minneapolis, MN 55449-4324
Phone (763) 780-5440 — FAX (763) 780-2958
e-mail:techsupport@catpumps.com
www.catpumps.com
International Inquiries
FAX (763) 785-4329
e-mail:intlsales@catpumps.com
WARNING
The Pumps with Nine Lives
CAT PUMPS (U.K.) LTD.
1 Fleet Business Park, Sandy Lane, Church Crookham, Fleet
N.V. CAT PUMPS INTERNATIONAL S.A.
CAT PUMPS DEUTSCHLAND GmbH
Hampshire GU52 8BF, England
Phone Fleet 44 1252-622031 — Fax 44 1252-626655
e-mail: sales@catpumps.co.uk
Heiveldekens 6A, 2550 Kontich, Belgium
Phone 32-3-450.71.50 — Fax 32-3-450.71.51
e-mail: cpi@catpumps.be www.catpumps.be
Buchwiese 2, D-65510 Idstein, Germany
Phone 49 6126-9303 0 — Fax 49 6126-9303 33
e-mail: catpumps@t-online.de www.catpumps.de
PN 30001 Rev G 6481
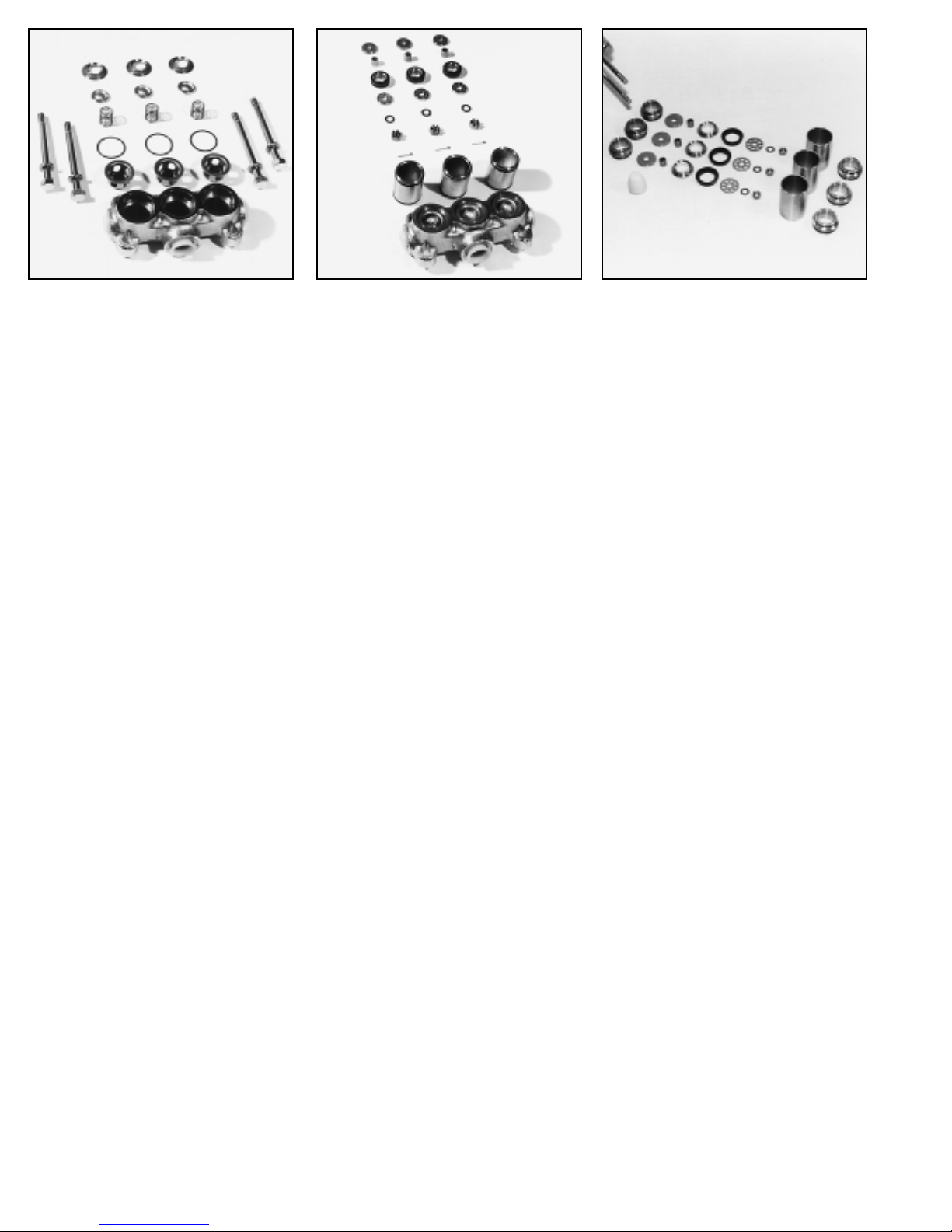
CAUTION: Before commencing with service, shut off drive (electric motor, gas or diesel engine) and turn off water supply to
pump. Relieve all discharge line pressure by triggering gun or opening valve in discharge line.
After servicing is completed, turn on water supply to pump, start drive, reset pressure regulating device and secondary valve, read
system pressure on the gauge at the pump head. Check for any leaks, vibration or pressure fluctuations and resume operation.
SERVICING THE VALVE ASSEMBLIES
Disassembly
1. Remove the two (2), four (4) or eight (8) Hex Flange
Nuts securing the Discharge Manifold to the crankcase
of the pump.
2. Support the Discharge Manifold and tap from the
backside with soft mallet. Gradually work free from
Cylinders.
3. Valve assemblies will remain in the Manifold. Pump
models with the o-ring groove on the outside of the
valve seat require the assistance of a Reverse Pliers
Tool to remove the valve seat. The Valve, Spring and
Retainer will then fall out when the Manifold is inverted.
Pump models without the o-ring groove on the outside
of the Valve Seat permit the Seat, Valve, Spring and
Retainer all to fall out when Manifold is inverted.
Reassembly
1. Examine Retainer for wear and replace as needed.
Place Retainer in manifold chamber with nylon tab
down.
2. Examine Spring for fatigue and replace as needed.
Insert Spring into center of Retainer.
3. Inspect the Valves for wear, ridges or pitting and
replace as needed.
NOTE: Seating side of Flat Valves may be lapped on
flat surface using 240 grit paper. Quiet Valves due
to their shape must be replaced. Insert Valve over
Spring with dimpled side up.
NOTE: Do not mix Quiet Valve and Flat Valve
Assemblies.
5. Examine O-Rings and Back-up-Rings on the Valve
Seat if used and replace if worn. Always lubricate
O-Rings for ease of installation and to avoid damage.
NOTE: First install O-Ring in groove on seat
towards seating surface, then Back-up-Ring.
NOTE: Models without outer groove on seat require
the O-Ring to be placed on lip of retainer.
NOTE: On Model 390, examine O-Rings on
Discharge Valve Adapter and replace if cut or worn.
Lubricate O.D. of Adapter O-Rings and press
Adapter into Discharge Manifold.
6. Install O-Ring, then Back-up-Ring on exposed Cylinder.
Back-up-Rings go to low pressure side of the
O-Rings. Lubricate O-Rings and Back-up-Rings on
exposed Cylinder. Exercise caution when slipping
Manifold over Cylinders to avoid damaging Cylinder
O-Rings. Completely press Manifold over Cylinders.
NOTE: On Model 390, Discharge Valve Adapter will
press into Cylinders when Manifold is reassembled
to crankcase.
7. Replace two (2), four (4) or eight (8) Hex Flange Nuts
and torque per chart.
NOTE: Replace all original Shims if used. When
new manifold is used reshim pump. When starting
the pump, check to see that there is no Cylinder
motion as this will cause premature failure of the
cylinder O-Rings. Center Cylinder motion indicates
improper shimming. Refer to Tech Bulletin 017 for
more information.
4. Examine Valve Seats for wear, pitting or grooves. Lap
the Flat Valve Seats with 240 grit paper or replace if
evidence of excessive wear. Quiet Valve Seats must
be replaced if worn. Install Seats with dishside down.
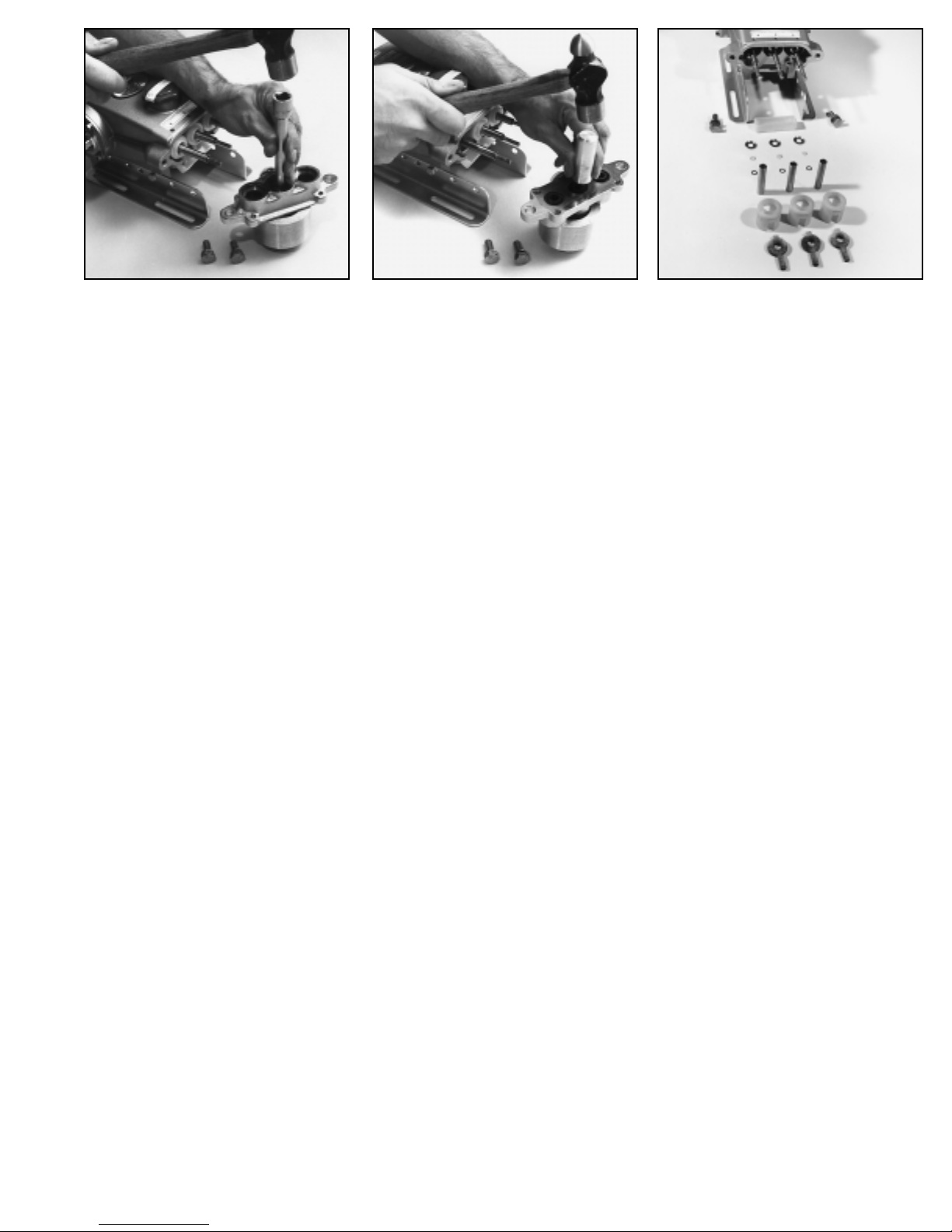
SERVICING THE PUMPING SECTION
■ Standard Piston Pump
Disassembly
1. Remove the Discharge Manifold as described in
Servicing the Valve Assemblies section.
2. Grasp Cylinders by hand and with an up and down
motion, pull Cylinders from Inlet Manifold.
(Model 390) When removing the Discharge Manifold to
service the Piston Assemblies, the Discharge Adapters
will generally remain in the discharge ports of the
manifold. They can be easily removed with a pliers.
Examine the adapter O-Rings and replace if worn or
cut. Lubricate the O-Rings and outer surface of the
adapters for ease of installation. Install the smaller
diameter, long extension of the adapter into the
discharge manifold ports.
3. Remove Cotterpin, Nut and Washer from Piston Rod.
4. Remove Retainer, Spacer, Piston-Cup Assembly and
Inlet Valve.
(Model 390) After removing the Inlet Valve, the Inlet
Adapters will be visible in the inlet manifold ports.
Remove the Adapters with a pliers. Examine the
O-Rings and replace if worn or cut. Lubricate the
O-Rings and outer surface of the adapter for ease of
installation. Install the smaller diameter, long
extension of the adapter into the inlet manifold ports.
3. Examine Cup for wear, cracking, tearing or separation
from the Piston. If worn replace and lubricate before
installing on Piston.
Note cup installation: Wipe cup inserter with oil. Slip
bac-cup Ring (when used) onto piston. Push Cup over
inserter and square with all surfaces. Faulty Cup
installation causes premature Cup failure. Some
models use a one-piece Piston Assembly.The Cup
does not separate from the Piston. Replace entire
assembly. Lubricate Piston Assembly and slip PistonCup assembly onto Piston Rod with lip facing
discharge.
4. Replace Piston Spacer and Retainer on Rod.
5. Replace Washer, thread on Nut and torque per chart.
NOTE: Always replace with new stainless steel
Cotterpin and turn ends under.
6. Examine Cylinder walls for scoring or etching which
causes premature wear of Cups and replace as
needed.
7. Lubricate Cylinder and replace O-Rings and/or
Back-up-Rings if worn or damaged. Back-up-Rings go
to low pressure side of the o-rings. Carefully slip
Cylinder over Rod Ends and push into Inlet Manifold
with Back-up-Rings facing the discharge manifold.
Reassembly
1. Examine Inlet Valve surface for pitting, scale or
grooves. Reverse Valve and sand inlet side of Valve
using 240 grit paper for clean surface or replace if
evidence of excessive wear. Slip onto Rod.
2. Examine Piston seating surface and lightly sand on flat
surface using 240 grit paper. If extreme pitting or sharp
edges are present, replace Piston.
8. Position Discharge Manifold onto pump as described,
replace fasteners and torque per chart.