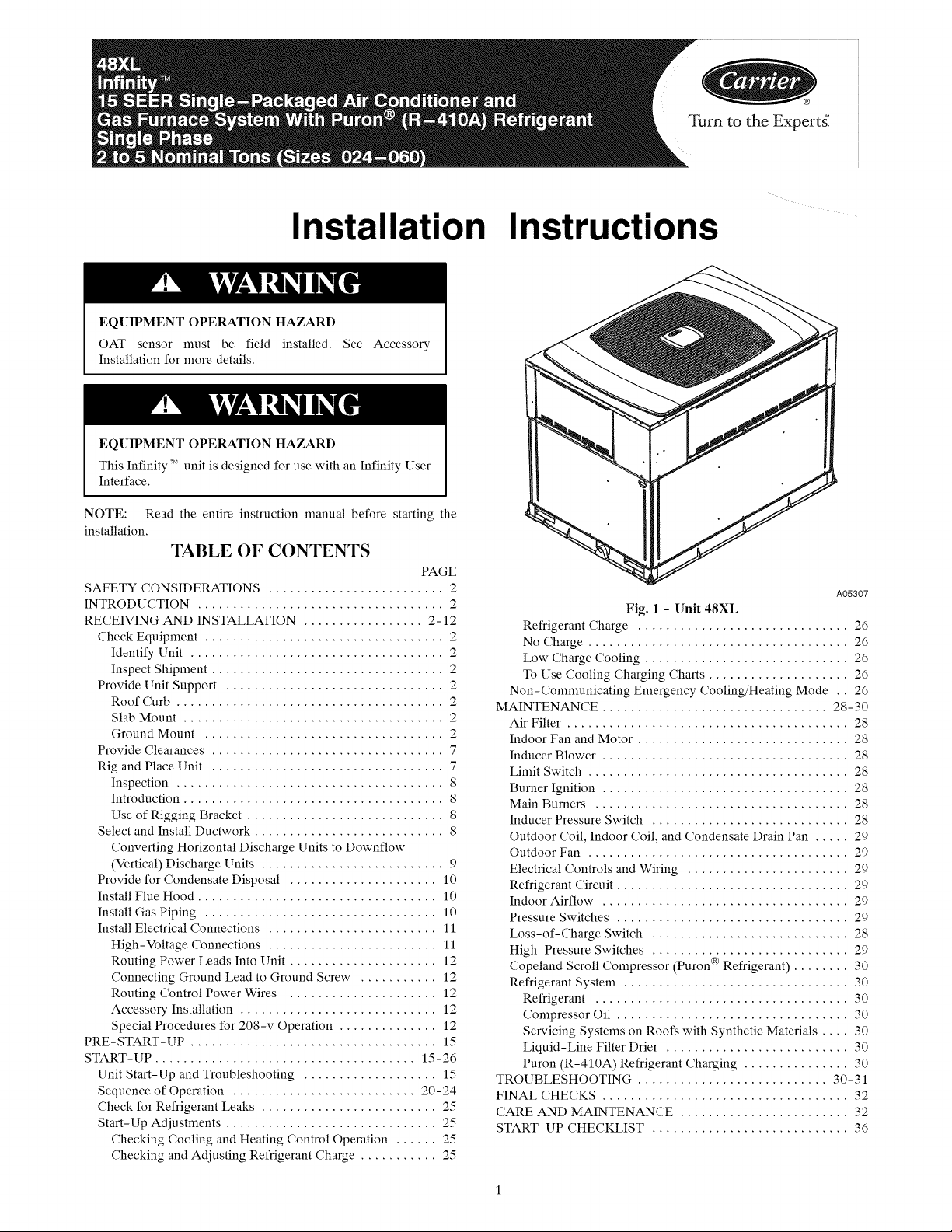
Installation Instructions
EQUIPMENT OPERATION HAZARD
OAT sensor must be field installed. See Accessory
Installation for more details.
EQUIPMENT OPERATION HAZARD
This Infinity TM unit is designed for use with an Infinity User
Interface.
NOTE: Read the entire instruction manual before starting the
installation.
TABLE OF CONTENTS
PAGE
SAFETY CONSIDERATIONS ......................... 2
INTRODUCTION ................................... 2
RECEIVING AND INSTALLATION ................. 2-12
Check Equipment .................................. 2
Identify Unit .................................... 2
Inspect Shipment ................................. 2
Provide Unit Support ............................... 2
Roof Curb ...................................... 2
Slab Mount ..................................... 2
Ground Mount .................................. 2
Provide Clearances ................................. 7
Rig and Place Unit ................................. 7
Inspection ...................................... 8
Introduction ..................................... 8
Use of Rigging Bracket ............................ 8
Select and Install Ductwork ........................... 8
Converting Horizontal Discharge Units to Downflow
(Vertical) Discharge Units .......................... 9
Provide for Condensate Disposal ..................... 10
Install Flue Hood .................................. 10
Install Gas Piping ................................. 10
Install Electrical Connections ........................ 11
High-Voltage Connections ........................ 11
Routing Power Leads Into Unit ..................... 12
Connecting Ground Lead to Ground Screw ........... 12
Routing Control Power Wires ..................... 12
Accessory Installation ............................ 12
Special Procedures for 208-v Operation .............. 12
PRE-START-UP ................................... 15
START-UP ..................................... 15-26
Unit Start-Up and Troubleshooting ................... 15
Sequence of Operation .......................... 20-24
Check for Refrigerant Leaks ......................... 25
Start-Up Adjustments .............................. 25
Checking Cooling and Heating Control Operation ...... 25
Checking and Adjusting Refrigerant Charge ........... 25
®
Turn to the Expertg
A05307
Fig. 1 - Unit 48XL
Refrigerant Charge .............................. 26
No Charge ..................................... 26
Low Charge Cooling ............................. 26
To Use Cooling Charging Charts .................... 26
Non-Communicating Emergency Cooling/Heating Mode .. 26
MAINTENANCE ................................ 28-30
Air Filter ........................................ 28
Indoor Fan and Motor .............................. 28
Inducer Blower ................................... 28
Limit Switch ..................................... 28
Burner Ignition ................................... 28
Main Burners .................................... 28
Inducer Pressure Switch ............................ 28
Outdoor Coil, Indoor Coil, and Condensate Drain Pan ..... 29
Outdoor Fan ..................................... 29
Electrical Controls and Wiring ....................... 29
Refrigerant Circuit ................................. 29
Indoor Airflow ................................... 29
Pressure Switches ................................. 29
Loss-of-Charge Switch ............................ 28
High-Pressure Switches ............................ 29
Copeland Scroll Compressor (Puron cR)Refrigerant) ........ 30
Refrigerant System ................................ 30
Refrigerant .................................... 30
Compressor Oil ................................. 30
Servicing Systems on Roofs with Synthetic Materials .... 30
Liquid-Line Filter Drier .......................... 30
Puron (R-410A) Refrigerant Charging ............... 30
TROUBLESHOOTING ........................... 30-31
FINAL CHECKS ................................... 32
CARE AND MAINTENANCE ........................ 32
START-UP CHECKLIST ............................ 36
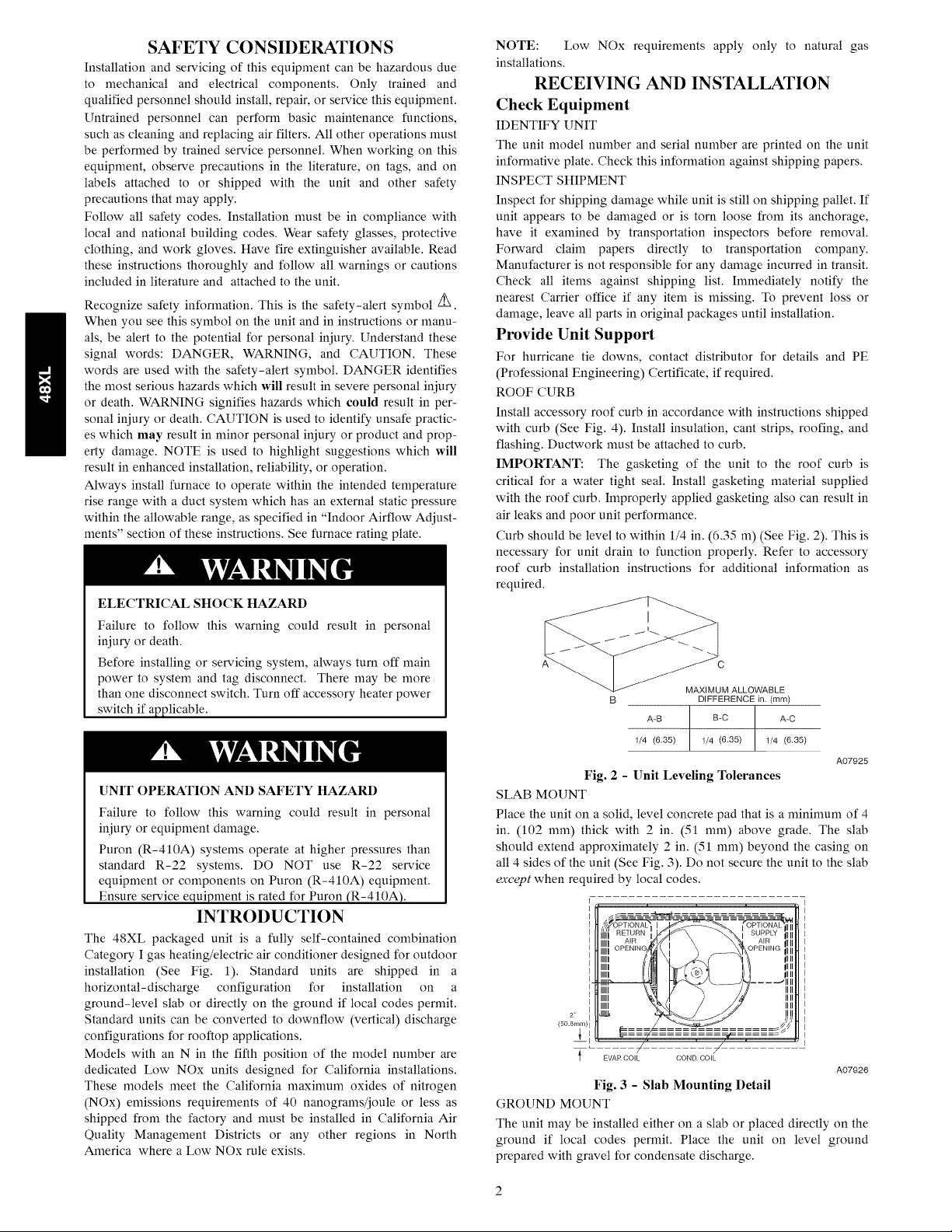
SAFETY CONSIDERATIONS
Installation and servicing of this equipment can be hazardous due
to mechanical and electrical components. Only trained and
qualified personnel should install, repair, or service this equipment.
Untrained personnel can perform basic maintenance flmctions,
such as cleaning and replacing air filters. All other operations must
be performed by trained service personnel. When working on this
equipment, observe precautions in the literature, on tags, and on
labels attached to or shipped with the unit and other safety
precautions that may apply.
Follow all safety codes. Installation must be in compliance with
local and national building codes. Wear safety glasses, protective
clothing, and work gloves. Have fire extinguisher available. Read
these instructions thoroughly and follow all warnings or cautions
included in literature and attached to the unit.
Recognize safety information. This is the safety-alert symbol /_.
When you see this symbol on the unit and in instructions or manu-
als, be alert to the potential for personal iniury. Understand these
signal words: DANGER, WARNING, and CAUTION. These
words are used with the safety-alert symbol. DANGER identifies
the most serious hazards which will result in severe personal iniury
or death. WARNING signifies hazards which could result in per-
sonal iniury or death. CAUTION is used to identify unsafe practic-
es which may result in minor personal injury or product and prop-
erty damage. NOTE is used to highlight suggestions which will
result in enhanced installation, reliability, or operation.
Always install furnace to operate within the intended temperature
rise range with a duct system which has an external static pressure
within the allowable range, as specified in "Indoor Airflow Adjust-
ments" section of these instructions. See furnace rating plate.
ELECTRICALSHOCK HAZARD
Failure to follow this warning could result in personal
iniury or death.
Before installing or servicing system, always turn off main
power to system and tag disconnect. There may be more
than one disconnect switch. Turn off accessory heater power
switch if applicable.
UNIT OPERATION AND SAFETY HAZARD
Failure to follow this warning could result in personal
iniury or equipment damage.
Puron (R-410A) systems operate at higher pressures than
standard R-22 systems. DO NOT use R-22 service
equipment or components on Puron (R-410A) equipment.
Ensure service equipment is rated for Puron (R-410A).
INTRODUCTION
The 48XL packaged unit is a fully self-contained combination
Category I gas heating/electric air conditioner designed for outdoor
installation (See Fig. 1). Standard units are shipped in a
horizontal-discharge configuration for installation on a
ground-level slab or directly on the ground if local codes permit.
Standard units can be converted to downflow (vertical) discharge
configurations for rooftop applications.
Models with an N in the fifth position of the model number are
dedicated Low NOx units designed for California installations.
These models meet the California maximum oxides of nitrogen
(NOx) emissions requirements of 40 nanograms/joule or less as
shipped from the factory and must be installed in California Air
Quality Management Districts or any other regions in North
America where a Low NOx rule exists.
NOTE: Low NOx requirements apply only to natural gas
installations.
RECEIVING AND INSTALLATION
Check Equipment
IDENTIFY UNIT
The unit model number and serial number are printed on the unit
informative plate. Check this information against shipping papers.
INSPECT SHIPMENT
Inspect for shipping damage while unit is still on shipping pallet. If
unit appears to be damaged or is torn loose from its anchorage,
have it examined by transportation inspectors before removal.
Forward claim papers directly to transportation company.
Manufacturer is not responsible for any damage incurred in transit.
Check all items against shipping list. Immediately notify the
nearest Carrier office if any item is missing. To prevent loss or
damage, leave all parts in original packages until installation.
Provide Unit Support
For hurricane tie downs, contact distributor for details and PE
(Professional Engineering) Certificate, if required.
ROOF CURB
Install accessory roof curt) in accordance with instructions shipped
with curt) (See Fig. 4). Install insulation, cant strips, roofing, and
flashing. Ductwork must be attached to curb.
IMPORTANT: The gasketing of the unit to the roof curt) is
critical for a water tight seal. Install gasketing material supplied
with the roof curt). Improperly applied gasketing also can result in
air leaks and poor unit performance.
Curb should be level to within 1/4 in. (6.35 m) (See Fig. 2). This is
necessary for unit drain to function properly. Refer to accessory
roof curt) installation instructions for additional information as
required.
MAXIMUM ALLOWABLE
DIFFERENCE in. (ram)
A-B
1/4 (6.35)
Fig. 2 - Unit Leveling Tolerances
SLAB MOUNT
Place the unit on a solid, level concrete pad that is a minimum of 4
in. (102 mm) thick with 2 in. (51 mm) above grade. The slat)
should extend approximately 2 in. (51 mm) beyond the casing on
all 4 sides of the unit (See Fig. 3). Do not secure the unit to the slat)
except when required by local codes.
RETURr SUPPLY
lUll .,_ lY/i_ \ \'\1 .,_ dill
m_ _E_ dlII
III1|OPENIN,_ i _, f--_OPENING 1111
IIII| tlil _ _z_ ( 't [ _III
IIIII Ill[ I_J'/_ _ _II jlII
IIIII Ill| IIll _<s'_ I!,I tlii
_ Hiv-'_ \ -- JbJ/.... illl
IIIII N I/ "_ //I IIII
IIIII _'_ A' ) /_ IIII
IIIII N?',.q / // IIII
2" _
(50.Smm)
#-- -2=_--__-----_/
/
EVAR COIL COND. COIL
Fig. 3 - Slab Mounting Detail
GROUND MOUNT
The unit may be installed either on a slab or placed directly on the
ground if local codes permit. Place the unit on level ground
prepared with gravel for condensate discharge.
B-C A-C
1/4 (6.35) 1/4 (6.35)
. j, .
/
A07925
A07926
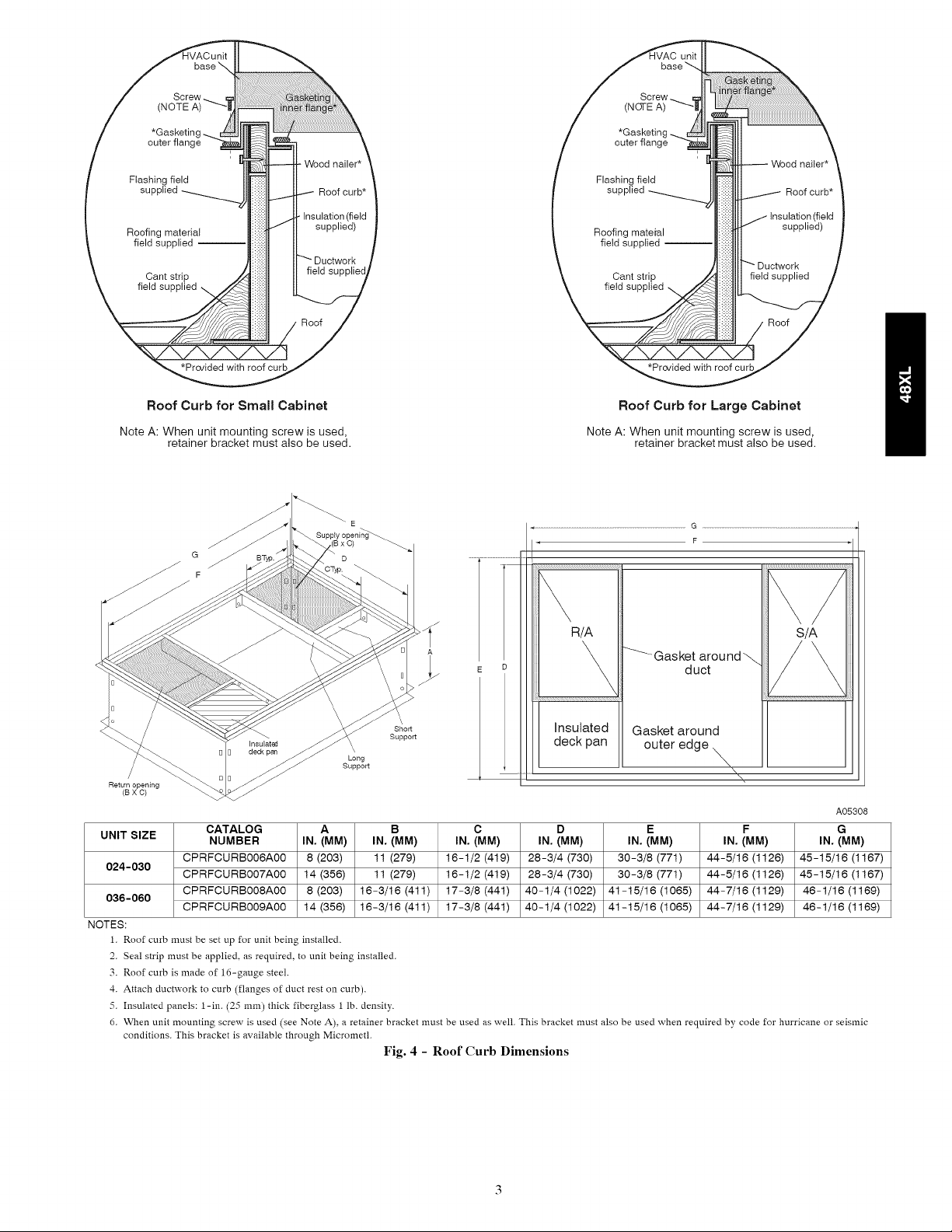
ase
/ ,,Screw.__._
/ (NOTE A) -_'l
/ *Gasketing .._ r_ j
/ \
Flashing field Ill_l II
I supplied _ JJU_ilt"_ Ro°f curb*
Roofing material U_ I[ supphed)
fieldsupplied-- ll_ii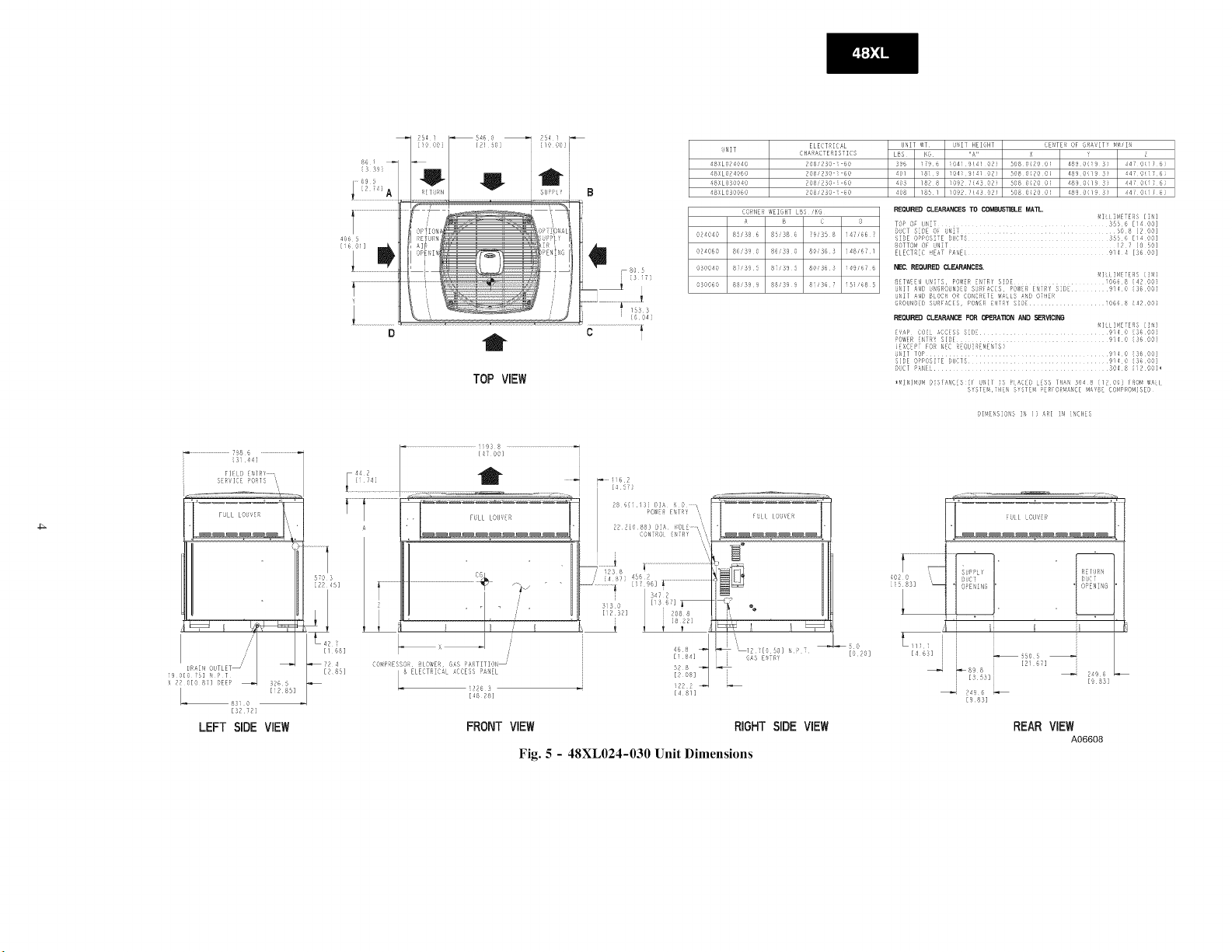
..............................798 6 ......................
:3:44]
FII{L:} _TR_ ¸ _
8ER,qSE PORIS _,
.......i]
TOP VIEW
INIT
48XL024¢140
,SXLO2,1G#I
_SXLU30040
48XL03_060
CORNER_EIEHT LBS KG
O24040 85/58 6 85,38 955 8 4b(6
0_4060 86¸¸¸¸390 86¸¸¸39 e 8O¸¸¸¸36¸5 i_8,0_/
0300,!O 8_395 8;',53 _, 8O¸¸¸¸36¸5 I_9/C_ 6
638,060 88¸¸¸¸39¸9 88/39 9 81/36 7 15i¸¸¸68 5
4 Hi C )
ELEGTRIG_L
CHARACTERISTICS
208'230 ] 60
208,230 i 60
2GS,P30 _0
UNIT U_IT HEIGHT ,3ENTEROF GRAVlT{ M_,_/I_
LSS "_" X '
396 _U4:_14_ 02; ¸ 8080(800_ 489 0(:_ 5)
@l i81¸9 1641_(43 ¢2) 5,USO{28UJ 489G,:19 3) 4,170_176}
405 /8_ 8 I_9_ _(43 0_;' 5O8 O(20 i_) 489 Oil9 3) 4,1,' 6(i}' 6}
4O8 /8_/ 09? ', 5 '? 5G80{_00_ 489¸O i95 44_G_ii _}
REOUIREDCLEARANCESTO COMBUS_BLE MAlL
TO_ OE U_iT ..... 585¸6 [14 00]
_CT SinE OF u_il .............. S08 [2 00]
SIDE OPPOSi_E DUCTS 555 6 [/4 00]
80TTO_ OF gNIT /2 7 [0 _0]
ELECT_iC HEA_ PANEL 9i4 4 [36 O0]
NEC. REQUIREDCLEARANCES,
8ET_EN VN:TS, POWERENTRY S]SE • • I066 8:4_ OOI
U_l[ AND UNGI_OUr,I_i)SU:_i_¢IS PO_'I_ I'/:RY S:I)i ...... 914¸0 _3_ 00]
U_i[ AN_¸ 8LOG4 OR 80r_CREIE _A_LS _ 0iHEI_
6_OUNSE8 SURF_ClS, PO_E!RENTRY S_ ........... i06_ 8:42 ,UO]
REQUIRE_CLEARANCEFOR OPERATIONAND _RVlCINO
Ev_l_ CO:L AGCiSS S:I)E .............. 914 0 3_ GO]
POWERENTR_¸ SlOE 914 0 (36 O0
(i:XC_R:¸ FO_ Ii{¢ R_OU_Ri_ENTG)
U_ll top .......................................... 9i,1¸0:3_ GO]
SIDE OPPOSITE DUCTS.............................. 9i4 0 {36 GOI
O_C[ P_r,_LL.................... 3,34 8 _12 GO]_
_MJU]KU O]S _C S [ tlHil IS [{&C [} L GS IUAN 904 8 1 00} [ROB _4i
S_'SII_,:_IE_ G_Sri_ PER[ %_A_CE _4448ECO_IfRO_IISE_
Vii LOil,]
#41Ui_IETER8 [iN]
vl ilk T( 8 [ _]
,<ILL]tdETERS [I]
ER_IN OUTLET--"
_851 O
//'/
[52 72]
LEFT SIDE VIEW
[i2 85]
[I 68]
]' ,I
[285]
FRONTVIEW RIGHTSIDEVIEW
Fig. 5 - 48XL024-030 Unit Dimensions
[4 6_]
.....1 i
ii I i_
_5505
[953]j
2496
[985]
REAR VIEW
A06608
2498
[983]
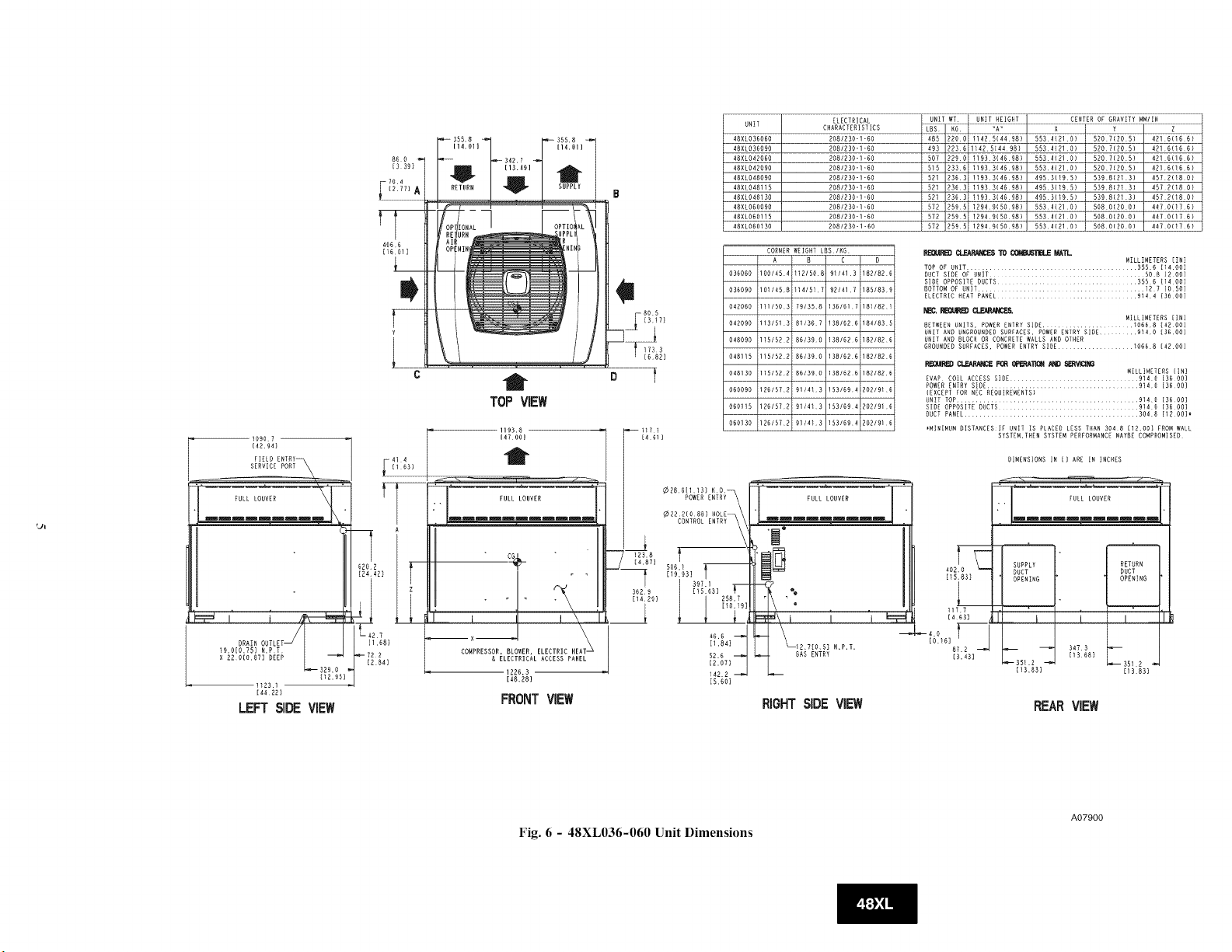
'.yl
$090 7
(42941
SERVICE PORT
FULL LOUVER
t
TOP VIEW
G;%_!
t
FULL LOUVER
mmm _ mm mm _ mm mm mm mm mmm
_H? 1
[4 611
286{113)
POWER ENTRY
¢ 22210881
CONTROL ENTRY
UNIT ELECTRICAL
48XLOS6060 2081230-I-60
48XL036090 20B/230-1-00
48XLO42060 20B1230-I-60
4BXL042090 2O81R3O-l-GO
48XLO4809U 2081230"1=60
48XL048115 20B1230-1-60
48XL048130 2081230-I"60
48XLOUOORO 2081230-I-60
48XLOROH5 2O81D3O'l'6O
48XLODOlSO 2081230-I-60
CORNER WEIGHT LBSIND
A B C 0
CHARACTERISTICS
036060 1001454 1121508 911413 1821826
036090 1011458 _14/517 92/417 185/839
042060 1111503 79135,0 1361617 1811821
042090 1131513 81/36T 13B1620i1841835
O4BORO 115152 D B6/390 IBB/62EilBD/B26
O48115 115/522 861390 13B/620 1821826
048130 1151522 861390 13B/6261IBRIB26
000090 1261572 911413 153/694 2021916
060115 1261572 911415 153/694 _OD/916
060130 1261572 911413 1531694iROD/916
UNIT WT UNIT NEIGNT CENTER OF GRAVITY MMIIN
LBS KG "A" X Y 2
485 2200 11425(449B) 5534(210) 5DOT(DO5) 4216(166)
493 2236 I142514498) 5534(210) 520T(DOD) 4215(166)
507 2290 11933(4698) 5534(210) 5207(205) 4216(166)
515 '336 1193314098) 5534(210) 5207(205) 4210(166)
521 2363 11933(4098) 4953(195) 5398(213) 4572(180)
521 2363 11933(469B) 4953(195) 5398(213) 4572(180)
521 2363 11933(4698) 4953(195} 5398(213) 4572(180)
572 2595 12949(5098) 5534(210) 508 0(200) 4470(176)
572 259 5 12949(509B) 5534(21 O) 508 0(200) 4470(17 D)
572 2595 12949(5098) 5534(210) 5OBO{2OO) 4470(176)
TOP OF UNIT ............................................. 355.6 [14.00]
DUCT SIDE OF UNIT ......................... 508 [DO0]
SIDE OPPOSITE DUCTS ............... 3SS 6 [14 ON)
BOTTOM OR UNIT ................... 12 T [O 50]
ELECTRIC NEAT PANEL .............. 9_4 4 [36 OR]
BETWEEN UNITS, POWER ENTRY SIDE ............... 1066B [42 ON]
UNIT AND UNGROUNDED SURFACES, POWER ENTRY SIDE ...... 9_40 [3600]
UNIT AND BLOCK OR CONCRETE WALLS AND OTHER
GROUNDED SURFACES, POWER ENTRY SIDE ................... 10068 [4200]
RB_JIBED ¢f_.A,e,N_CE_ 8P_,P,A'IIONA._B 8_RVIa_
IVAP COIL ACCESS SIDE ........................... 9140 [36 ON)
POWER ENTRY SIDE ....................................... 9140 [3600]
(EXCEPT FOR NEC REOUIREMENTS)
UNIT TOP ................................................ R14O [3600]
SIDE OPPOSITE DUCTS ..................................... 9140 [3600]
DUCT PANEL .............................................. 3048 [IDOO]_
_MINIMUM DISTANCESIE UNIT IS PLACED LESS THAN 304 B [ID,O0} FROM WALL
SYSTEM,THEN SYSTEM PERFORMANCE MAYBE COMPROMISED
MILLIMETERS [IN]
MILLIMETERS [[N]
MILLIMETERS TIN)
DIMENSIONS IN [] ARE IN INCHES
FULL LOUVER
DRAIN
19,010,75] N,PT
X 220[O.BT] DEEP
1_23.I
144221
LEFTSIDEVIEW
£12.951
[1.681
722
C284)
I II i \
COMPRESSOR, BLOWER, ELECTRIC HEAT _
RICAL ACCESS PAN
]2263
[48,28]
FRONT VIEW
Fig. 6 - 48XL036-060 Unit Dimensions
362,9
[14,29}
5O6
397.1
115.G31
[1.B4]
52.0
46.6
[2.07]
142.2
[5.00]
BAS ENTRY
N,P.T.
402,0
115,831
H77
I4N3I
[0.16] _-
TC
87.2
[B.43]
RIOHTSIDE VIEW
SUPPLY RETURN
DUCT DUCT
OPENING " ' "
_ 3473
_35_.2 _ _351.2 _4
[13.B31 E13831
[13681
REARVIEW
A07900

UNIT SIZE
NOMINAL COOLING CAPACITY (ton)
NOMINAL HEATING CAPACITY (Btu)
OPERATING WEIGHT (Ib)
COMPRESSORS
Quantity
REFRIGERANT: PURON (R-410A)
Quantity (Ib)
REFRIGERANT METERING DEVICE
OUTDOOR COIL
OUTDOOR FAN
INDOOR COIL
INDOOR FAN
Nominal Airflow (Cfm)
Comfort
Efficiency
Max
Furnace (gas ht.) airflow-Low Stage
Furnace (gas ht.) airflow-High Stage
Size (in.)
Motor HP (RPM)
FURNACE SECTION*
Burner Orifice No. (Qty._Drill Size)
HIGH-PRESSURE SWITCH (peig)
Cut-out
HIGH-PRESSURE SWITCH 2 (psig)
LOSS-OF-CHARGE /
LOW- PRESSURE SWITCH
RETURN-AIR FILTERS Throwaway
(in.)€
(mm)
Continued next page.
(kg)
Size
Part Number
Rows...Fins/in,
Face Area (sq ft)
Nominal Cfm
Diameter (in.)
(ram)
Motor Hp (Rpm)
Rows...Fins/in,
Face Area (sq ft)
(ram)
Natural Gas
Reset (Auto)
(Compressor Solenoid)
Cut-out
Reset (Auto)
(Liquid Line) (psig)
Cut-out
Reset (auto)
(kg)
Table I - Physical Data - Unit 48XL
024040 024060 030040 036090 042060 042090
2 2 2-1/2 3 3-1/2 3-1/2
40,000 60,000 40,000 90,000 60,000 90,000
396 401 403 493 507 515
180 182 183 224 230 234
10.1 10.1 11.3 11.3 9.5 9.5 13.8 13.8
4.6 4.6 5.1 5.1 4.3 4.3 6.3 6.3
2 Ton 2 Ton 3 Ton 3 Ton 3 Ton 3 Ton 4 Ton 4 Ton
EA36YD129 EA36YD129 EA36YD139 EA36YD139 EA36YD139 EA36YD139 EA36YD149 EA36YD149
2...21 2...21 2...21 2...21 2...21 2...21 2...21 2...21
13.6 13.6 15.3 15.3 17.5 17.5 19.4 19.4
2700 2700 2700 2700 2800 2800 2800 2800
22 22 22 22 22 22 22 22
559 559 559 559 559 559 559 559
1/8 (825) 1/8 (825) 1/8 (825) 1/8 (825) 1/8 (825) 1/8 (825) 1/8 (825) 1/8 (825)
3...17 3...17 3...17 3...17 3...17 3...17 3...17 3...17
3.7 3.7 3.7 3.7 4.7 4.7 4.7 4.7
Variable based on Comfort Rollback(see Userlnter_ceinstructionsfor moreinformation).
7OO
8OO
475
844
10x10
254x254
1/2
2...44 3...44 2...44 3...44 3...44 3...38 3...44 3...38
700 875 875 1050 1050 1225
800 1000 1000 1200 1200 1400
727
1120
10x10
254x254
1/2
20x24x1 24x30x1 24x36x1
508x610x25 610x762x25 610x914x25
475
844
10x10
254x254
1/2
030060 036060
2-1/2 3
60,000 60,000
408 485
185 220
2-Stage Scroll
1
TXV
727
1120
10x10
254x254
1/2
670 ±10
470 ± 25
565 ± 15
455 ± 15
745
1120
11x10
279x254
3/4
23 ± 5
55 ± 5
875
1410
11x10
279x254
3/4
745
1120
11x10
279x254
3/4
1225
1400
875
1410
11x10
279x254
3/4
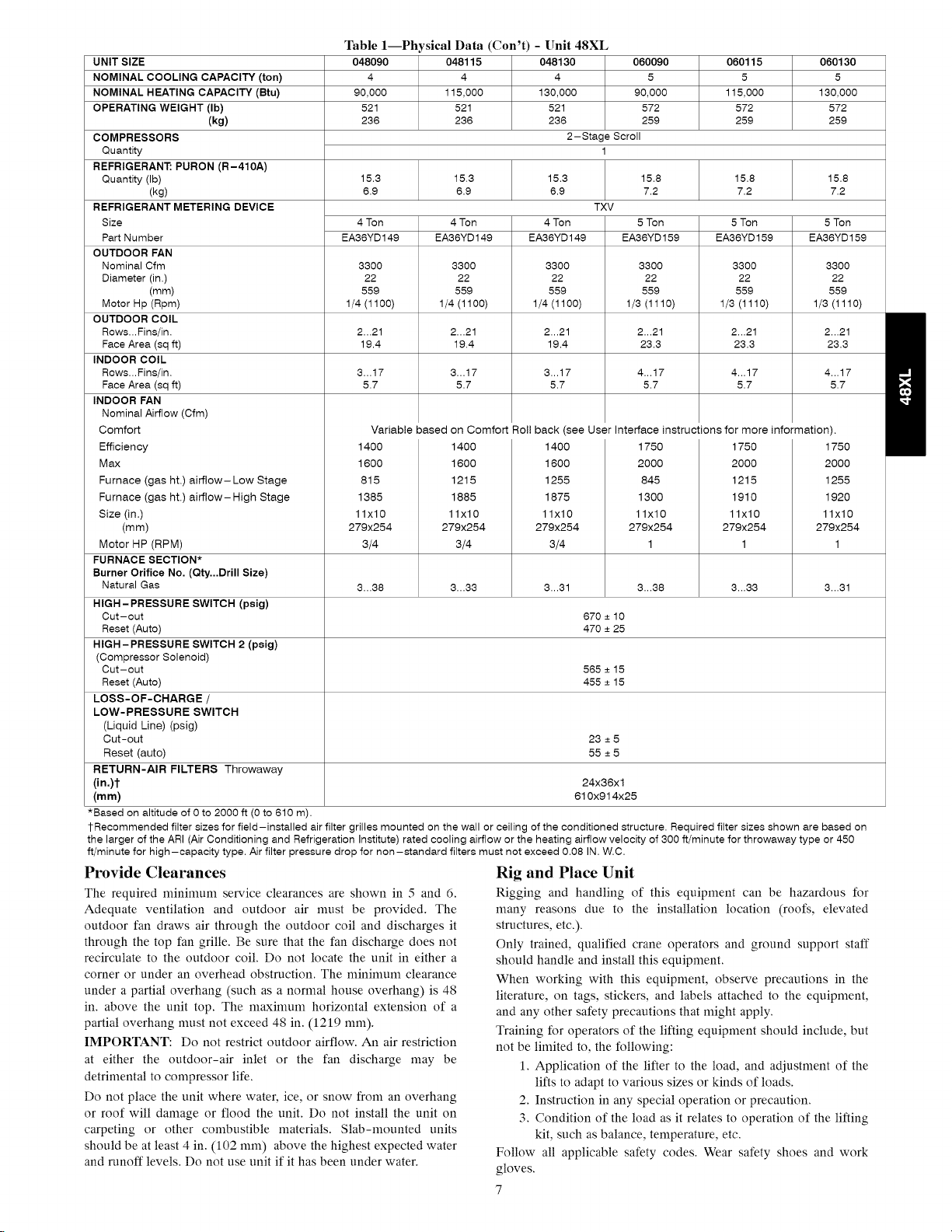
UNITSIZE
NOMINAL COOLING CAPACITY (ton)
NOMINAL HEATING CAPACITY (Btu)
OPERATING WEIGHT (Ib)
COMPRESSORS
Quantity
REFRIGERANT: PURON (R-410A)
Quantity (Ib)
REFRIGERANT METERING DEVICE
Size
Part Number
OUTDOOR FAN
Nominal Cfm
Diameter (in.)
Motor Hp (Rpm)
OUTDOOR COIL
Rows...Fins/in,
INDOOR COIL
Rows...Fins/in,
INDOOR FAN
Nominal Airflow (Cfm)
Comfort
Efficiency
Max
Furnace (gas ht.) airflow-Low Stage
Furnace (gas ht.) airflow-High Stage
Size (in.)
Motor HP (RPM)
FURNACE SECTION*
Burner Orifice No. (Qty._Drill Size)
Natural Gas
HIGH-PRESSURE SWITCH (peig)
Cut-out
Reset (Auto)
HIGH-PRESSURE SWITCH 2 (peig)
(Compressor Solenoid)
Cut-out
Reset (Auto)
LOSS-OF-CHARGE /
LOW-PRESSURE SWITCH
RETURN-AIR FILTERS Throwaway
(in.)1-
(ram)
*Based on altitude of 0 to 2000 ft (0 to 610 m).
1-Recommended filter sizes for field-installed air filter grilles mounted on the wall or ceiling of the conditioned structure. Required filter sizes shown are based on
the larger of the ARI (Air Conditioning and Refrigeration Institute) rated cooling airflow or the heating airflow velocity of 300 ft/minute for throwaway type or 450
ft/minute for high-capacity type. Air filter pressure drop for non-standard filters must not exceed 0.08 IN. W.C.
(kg)
(mm)
Face Area (sq ft)
Face Area (sq ft)
(ram)
(Liquid Line) (psig)
Cut-out
Reset (auto)
Provide Clearances
The required minimum service clearances are shown in 5 and 6.
Adequate ventilation and outdoor air must be provided. The
outdoor fan draws air through the outdoor coil and discharges it
through the top fan grille. Be sure that the fan discharge does not
recirculate to the outdoor coil. Do not locate the unit in either a
corner or under an overhead obstruction. The minimum clearance
under a partial overhang (such as a normal house overhang) is 48
in. above the unit top. The maximum horizontal extension of a
partial overhang must not exceed 48 in. (1219 mm).
IMPORTANT: Do not restrict outdoor airflow. An air restriction
at either the outdoor-air inlet or the fan discharge may be
detrimental to compressor life.
Do not place the unit where water, ice, or snow from an overhang
or roof will damage or flood the unit. Do not install the unit on
carpeting or other combustible materials. Slab-mounted units
should be at least 4 in. (102 mm) above the highest expected water
and runoff levels. Do not use unit if it has been under water.
(kg)
048090 048115 060115 060130
4 4 5 5
90,000 115,000 115,000 130,000
521 521 572 572
236 236 259 259
15.3 15.3 15.3 15.8 15.8 15.8
6.9 6.9 6.9 7.2 7.2 7.2
4Ton 4Ton 4Ton 5Ton 5Ton 5Ton
EA36YD 149 EA36YD 149 EA36YD 149 EA36YD 159 EA36YD 159 EA36YD 159
3300 3300 3300 3300 3300 3300
22 22 22 22 22 22
559 559 559 559 559 559
1/4 (1100) 1/4 (1100) 1/4 (1100) 1/3 (1110) 1/3 (1110) 1/3 (1110)
2...21 2...21 2...21 2...21 2...21 2...21
19.4 19.4 19.4 23.3 23.3 23.3
3...17 3...17 3...17 4...17 4...17 4...17
5.7 5.7 5.7 5.7 5.7 5.7
Variable based on Comfort Rollback(see Userlnterfaceinstructionsfor moreinformation).
1400 1400 1400 1750 1750
1600 1600 1600 2000 2000
815
1385
11x10
279x254
3/4
3...38 3...33 3...31 3...38 3...33 3...31
1215
1885
11x10
279x254
3/4
048130 060090
4 5
130,000 90,000
521 572
236 259
2-Stage Scroll
1
TXV
1255
1875
11x10
279x254
3/4
670 ± 10
470 ± 25
565 ± 15
455 ± 15
23 ± 5
55 ± 5
24x36xl
610x914x25
845
1300
11x10
279x254
1750
2000
1215
1910
11x10
279x254
1
1
1255
1920
11x10
279x254
1
Rig and Place Unit
Rigging and handling of this equipment can be hazardous for
many reasons due to the installation location (roofs, elevated
structures, etc.).
Only trained, qualified crane operators and ground support staff
should handle and install this equipment.
When working with this equipment, observe precautions in the
literature, on tags, stickers, and labels attached to the equipment,
and any other safety precautions that might apply.
Training for operators of the lifting equipment should include, but
not be limited to, the following:
1. Application of the lifter to the load, and adjustment of the
lifts to adapt to various sizes or kinds of loads.
2. Instruction in any special operation or precaution.
3. Condition of the load as it relates to operation of the lifting
kit, such as balance, temperature, etc.
Follow all applicable safety codes. Wear safety shoes and work
gloves.
7
Table 1--Physical Data (Con't) - Unit 48XL
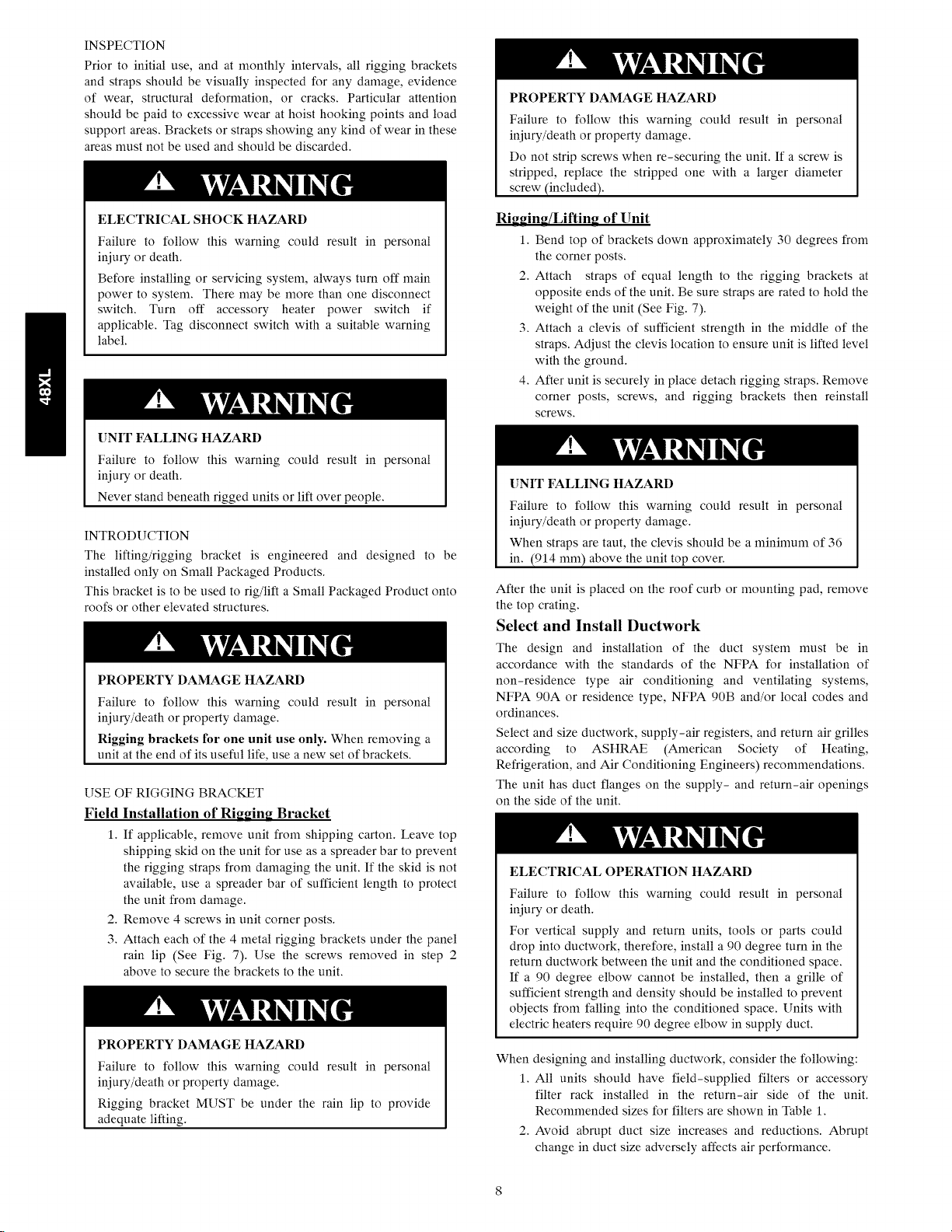
INSPECTION
Prior to initial use, and at monthly intervals, all rigging brackets
and straps should be visually inspected for any damage, evidence
of wear, structural deformation, or cracks. Particular attention
should be paid to excessive wear at hoist hooking points and load
support areas. Brackets or straps showing any kind of wear in these
areas must not be used and should be discarded.
PROPERTY DAMAGE HAZARD
Failure to follow this warning could result in personal
iniury/death or property damage.
Do not strip screws when re-securing the unit. If a screw is
stripped, replace the stripped one with a larger diameter
screw (included).
ELECTRICALSHOCK HAZARD
Failure to follow this warning could result in personal
iniury or death.
Before installing or servicing system, always turn off main
power to system. There may be more than one disconnect
switch. Turn off accessory heater power switch if
applicable. Tag disconnect switch with a suitable warning
label.
UNIT FALLING HAZARD
Failure to follow this warning could result in personal
iniury or death.
Never stand beneath rigged units or lift over people.
INTRODUCTION
The lifting/rigging bracket is engineered and designed to be
installed only on Small Packaged Products.
This bracket is to be used to rig/lift a Small Packaged Product onto
roofs or other elevated structures.
PROPERTY DAMAGE HAZARD
Failure to follow this warning could result in personal
iniury/death or property damage.
Rigging brackets for one unit use only. When removing a
unit at the end of its useful life, use a new set of brackets.
USE OF RIGGING BRACKET
Field Installation of Ri_in_ Bracket
1. If applicable, remove unit from shipping carton. Leave top
shipping skid on the unit for use as a spreader bar to prevent
the rigging straps from damaging the unit. If the skid is not
available, use a spreader bar of sufficient length to protect
the unit from damage.
2. Remove 4 screws in unit corner posts.
3. Attach each of the 4 metal rigging brackets under the panel
rain lip (See Fig. 7). Use the screws removed in step 2
above to secure the brackets to the unit.
PROPERTY DAMAGE HAZARD
Failure to follow this warning could result in personal
iniury/death or property damage.
Rigging bracket MUST be under the rain lip to provide
adequate lifting.
Riu_inu/Liftinu of Unit
1. Bend top of brackets down approximately 30 degrees from
the corner posts.
2. Attach straps of equal length to the rigging brackets at
opposite ends of the unit. Be sure straps are rated to hold the
weight of the unit (See Fig. 7).
3. Attach a clevis of sufficient strength in the middle of the
straps. Adjust the clevis location to ensure unit is lifted level
with the ground.
4. After unit is securely in place detach rigging straps. Remove
corner posts, screws, and rigging brackets then reinstall
screws.
UNIT FALLING HAZARD
Failure to follow this warning could result in personal
iniury/death or property damage.
When straps are taut, the clevis should be a minimum of 36
in. (914 mm) above the unit top cover.
After the unit is placed on the roof curb or mounting pad, remove
the top crating.
Select and Install Ductwork
The design and installation of the duct system must be in
accordance with the standards of the NFPA for installation of
non-residence type air conditioning and ventilating systems,
NFPA 90A or residence type, NFPA 90B and/or local codes and
ordinances.
Select and size ductwork, supply-air registers, and return air grilles
according to ASHRAE (American Society of Heating,
Refrigeration, and Air Conditioning Engineers) recommendations.
The unit has duct flanges on the supply- and return-air openings
on the side of the unit.
ELECTRICAL OPERATION HAZARD
Failure to follow this warning could result in personal
iniury or death.
For vertical supply and return units, tools or parts could
drop into ductwork, therefore, install a 90 degree turn in the
return ductwork between the unit and the conditioned space.
If a 90 degree elbow cannot be installed, then a grille of
sufficient strength and density should be installed to prevent
objects from falling into the conditioned space. Units with
electric heaters require 90 degree elbow in supply duct.
When designing and installing ductwork, consider the following:
1. All units should have field-supplied filters or accessory
filter rack installed in the return-air side of the unit.
Recommended sizes for filters are shown in Table 1.
2. Avoid abrupt duct size increases and reductions. Abrupt
change in duct size adversely affects air performance.
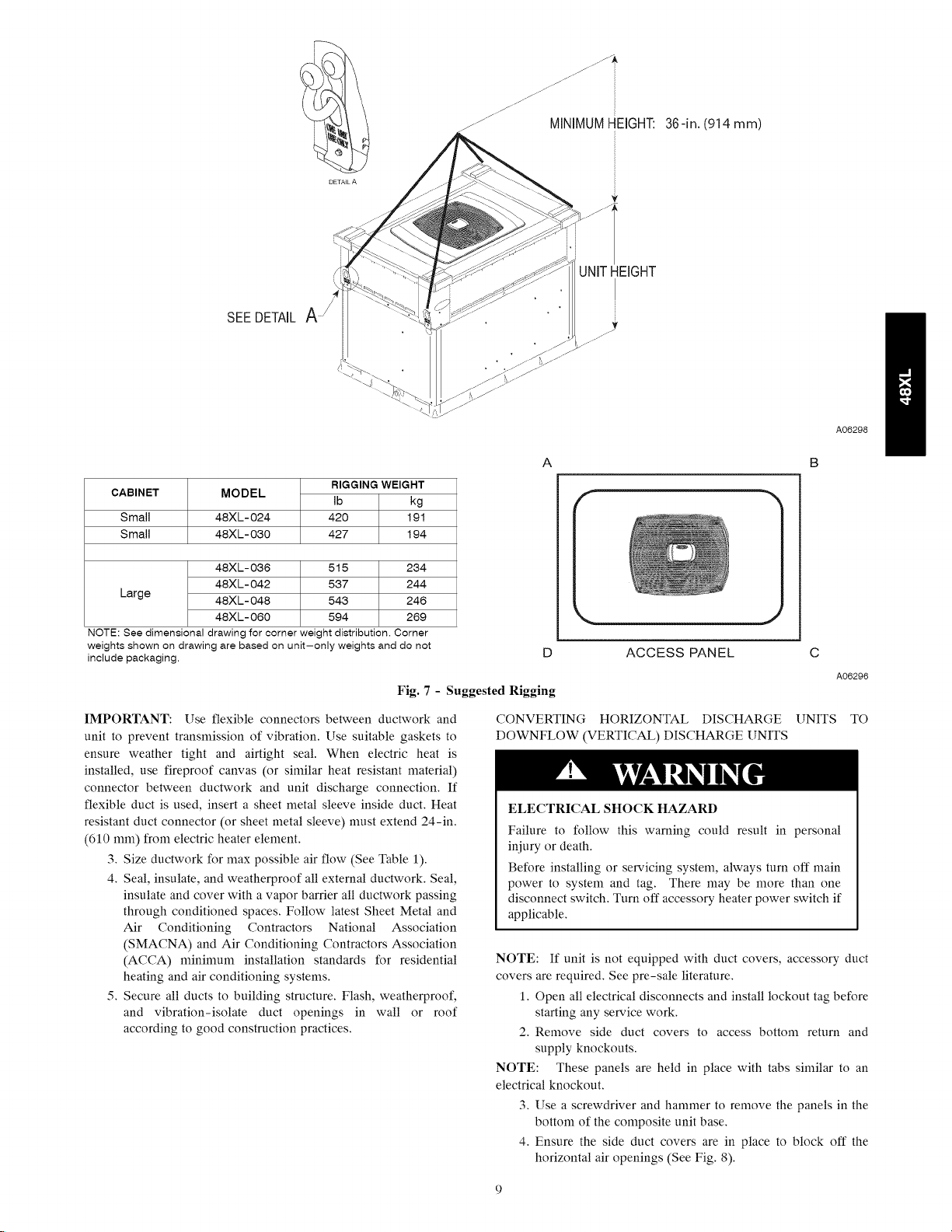
UNITHEIGHT
36-in. (914 mm)
SEE DETAIL
CABINET
Small
Small
Large 48XL-048 543 246
NOTE: See dimensional drawing for corner weight distribution. Corner
weights shown on drawing are based on unit-only weights and do not
include packaging.
MODEL
48XL-024
48XL-030
48XL-036 515 234
48XL-042 537 244
48XL-060 594 269
A /
RIGGING WEIGHT
Ib kg
420 191
427 194
Fig. 7 - Suggested Rigging
IMPORTANT: Use flexible connectors between ductwork and
unit to prevent transmission of vibration. Use suitable gaskets to
ensure weather tight and airtight seal. When electric heat is
installed, use fireproof canvas (or similar heat resistant material)
connector between ductwork and unit discharge connection. If
flexible duct is used, insert a sheet metal sleeve inside duct. Heat
resistant duct connector (or sheet metal sleeve) must extend 24-in.
(610 mm) from electric heater element.
3. Size ductwork for max possible air flow (See Table 1).
4. Seal, insulate, and weatherproof all external ductwork. Seal,
insulate and cover with a vapor barrier all ductwork passing
through conditioned spaces. Follow latest Sheet Metal and
Air Conditioning Contractors National Association
(SMACNA) and Air Conditioning Contractors Association
(ACCA) minimum installation standards for residential
heating and air conditioning systems.
5. Secure all ducts to building structure. Flash, weatherproof,
and vibration-isolate duct openings in wall or roof
according to good construction practices.
A06298
A
J
D
CONVERTING HORIZONTAL DISCHARGE UNITS TO
DOWNFLOW (VERTICAL) DISCHARGE UNITS
ELECTRICAL SHOCK HAZARD
Failure to follow this warning could result in personal
iniury or death.
Before installing or servicing system, always turn off main
power to system and tag. There may be more than one
disconnect switch. Turn off accessory heater power switch if
applicable.
NOTE: If unit is not equipped with duct covers, accessory duct
covers are required. See pre-sale literature.
1. Open all electrical disconnects and install lockout tag before
starting any service work.
2. Remove side duct covers to access bottom return and
supply knockouts.
NOTE: These panels are held in place with tabs similar to an
electrical knockout.
3. Use a screwdriver and hammer to remove the panels in the
bottom of the composite unit base.
4. Ensure the side duct covers are in place to block off the
horizontal air openings (See Fig. 8).
ACCESS PANEL C
A06296
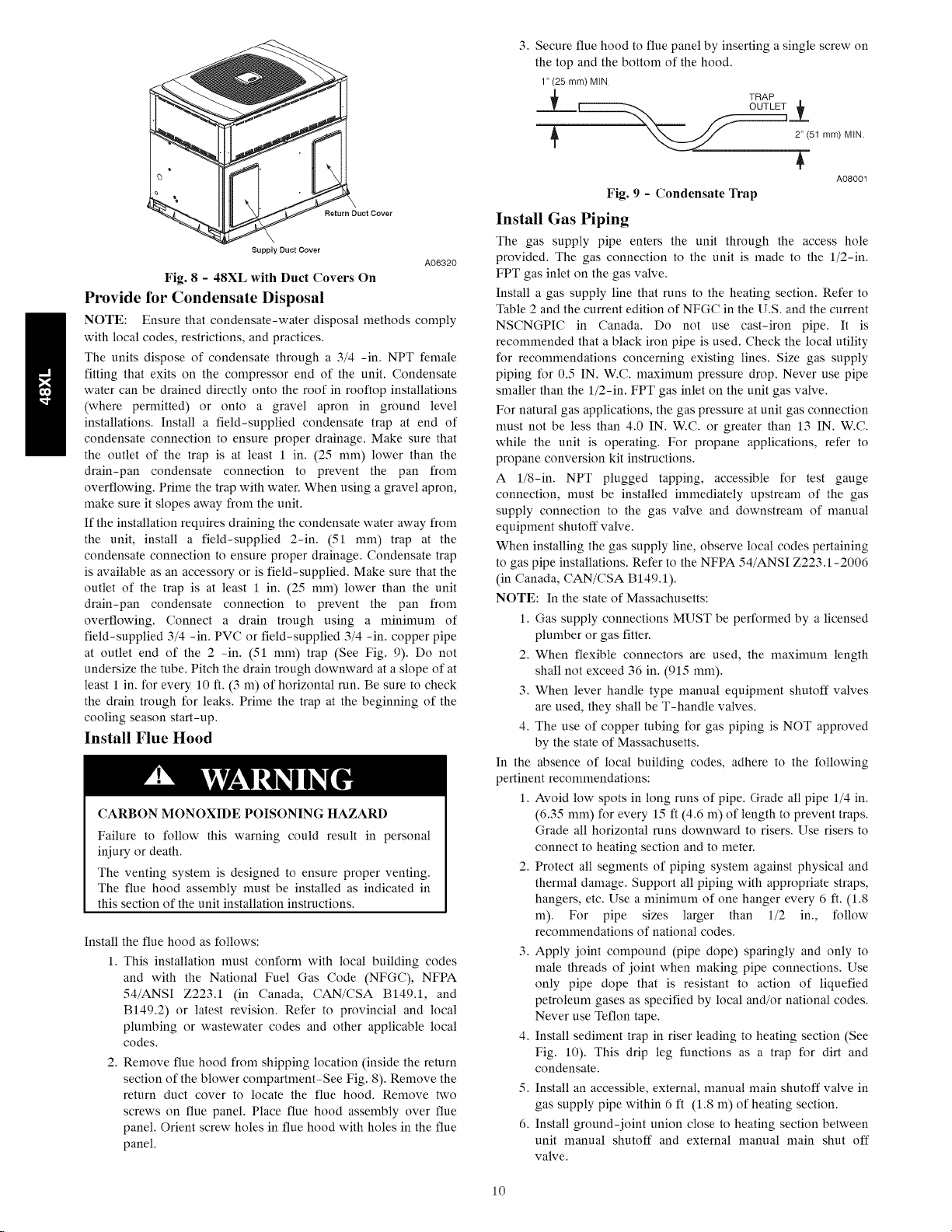
Supply Duct Cover
A06320
Fig. 8 - 48XL with Duct Covers On
Provide for Condensate Disposal
NOTE: Ensure that condensate-water disposal methods comply
with local codes, restrictions, and practices.
The units dispose of condensate through a 3/4 -in. NPT female
fitting that exits on the compressor end of the unit. Condensate
water can be drained directly onto the roof in rooftop installations
(where permitted) or onto a gravel apron in ground level
installations. Install a field-supplied condensate trap at end of
condensate connection to ensure proper drainage. Make sure that
the outlet of the trap is at least 1 in. (25 mm) lower than the
drain-pan condensate connection to prevent the pan from
overflowing. Prime the trap with water. When using a gravel apron,
make sure it slopes away from the unit.
If the installation requires draining the condensate water away from
the unit, install a field-supplied 2-in. (51 mm) trap at the
condensate connection to ensure proper drainage. Condensate trap
is available as an accessory or is field-supplied. Make sure that the
outlet of the trap is at least 1 in. (25 mm) lower than the unit
drain-pan condensate connection to prevent the pan from
overflowing. Connect a drain trough using a minimum of
field-supplied 3/4 -in. PVC or field-supplied 3/4 -in. copper pipe
at outlet end of the 2 -in. (51 mm) trap (See Fig. 9). Do not
undersize the tube. Pitch the drain trough downward at a slope of at
least 1 in. for every 10 ft. (3 m) of horizontal run. Be sure to check
the drain trough for leaks. Prime the trap at the beginning of the
cooling season start-up.
Install Flue Hood
CARBON MONOXIDE POISONING HAZARD
Failure to follow this warning could result in personal
injury or death.
The venting system is designed to ensure proper venting.
The flue hood assembly must be installed as indicated in
this section of the unit installation instructions.
Install the flue hood as follows:
1. This installation must conform with local building codes
and with the National Fuel Gas Code (NFGC), NFPA
54/ANSI Z223.1 (in Canada, CAN/CSA B149.1, and
B149.2) or latest revision. Refer to provincial and local
plumbing or wastewater codes and other @plicable local
codes.
2. Remove flue hood from shipping location (inside the return
section of the blower compartment-See Fig. 8). Remove the
return duct cover to locate the flue hood. Remove two
screws on flue panel. Place flue hood assembly over flue
panel. Orient screw holes in flue hood with holes in the flue
panel.
3. Secure flue hood to flue panel by inserting a single screw on
the top and the bottom of the hood.
1" (25 mm) MIN.
__ 2" (51 mm) MIN
A08001
Fig. 9 - Condensate Trap
Install Gas Piping
The gas supply pipe enters the unit through the access hole
provided. The gas connection to the unit is made to the l/2-in.
FPT gas inlet on the gas valve.
Install a gas supply line that runs to the heating section. Refer to
Table 2 and the current edition of NFOC in the U.S. and the current
NSCNGPIC in Canada. Do not use cast-iron pipe. It is
recommended that a black iron pipe is used. Check the local utility
for recommendations concerning existing lines. Size gas supply
piping for 0.5 IN. W.C. maximum pressure drop. Never use pipe
smaller than the l/2-in. FPT gas inlet on the unit gas valve.
For natural gas @plications, the gas pressure at unit gas connection
must not be less than 4.0 IN. W.C. or greater than 13 IN. W.C.
while the unit is operating. For propane @plications, refer to
propane conversion kit instructions.
A 1/8-in. NPT plugged t@ping, accessible for test gauge
connection, must be installed immediately upstream of the gas
supply connection to the gas valve and downstream of manual
equipment shutoff valve.
When installing the gas supply line, observe local codes pertaining
to gas pipe installations. Refer to the NFPA 54/ANSI Z223.1-2006
(in Canada, CAN/CSA B149.1).
NOTE: In the state of Massachusetts:
1. Gas supply connections MUST be performed by a licensed
plumber or gas fitter.
2. When flexible connectors are used, the maximum length
shall not exceed 36 in. (915 mm).
3. When lever handle type manual equipment shutoff valves
are used, they shall be T-handle valves.
4. The use of copper tubing for gas piping is NOT @proved
by the state of Massachusetts.
In the absence of local building codes, adhere to the following
pertinent recommendations:
1. Avoid low spots in long runs of pipe. Grade all pipe 1/4 in.
(6.35 mm) for every 15 ft (4.6 m) of length to prevent traps.
Orade all horizontal runs downward to risers. Use risers to
connect to heating section and to meter.
2. Protect all segments of piping system against physical and
thermal damage. Support all piping with @propriate straps,
hangers, etc. Use a minimum of one hanger every 6 ft. (1.8
m). For pipe sizes larger than 1/2 in., follow
recommendations of national codes.
3. Apply joint compound (pipe dope) sparingly and only to
male threads of joint when making pipe connections. Use
only pipe dope that is resistant to action of liquefied
petroleum gases as specified by local and/or national codes.
Never use Teflon t@e.
4. Install sediment trap in riser leading to heating section (See
Fig. 10). This drip leg functions as a trap for dirt and
condensate.
5. Install an accessible, external, manual main shutoff valve in
gas supply pipe within 6 ft (1.8 m) of heating section.
6. Install ground-joint union close to heating section between
unit manual shutoff and external manual main shut off
valve.
10
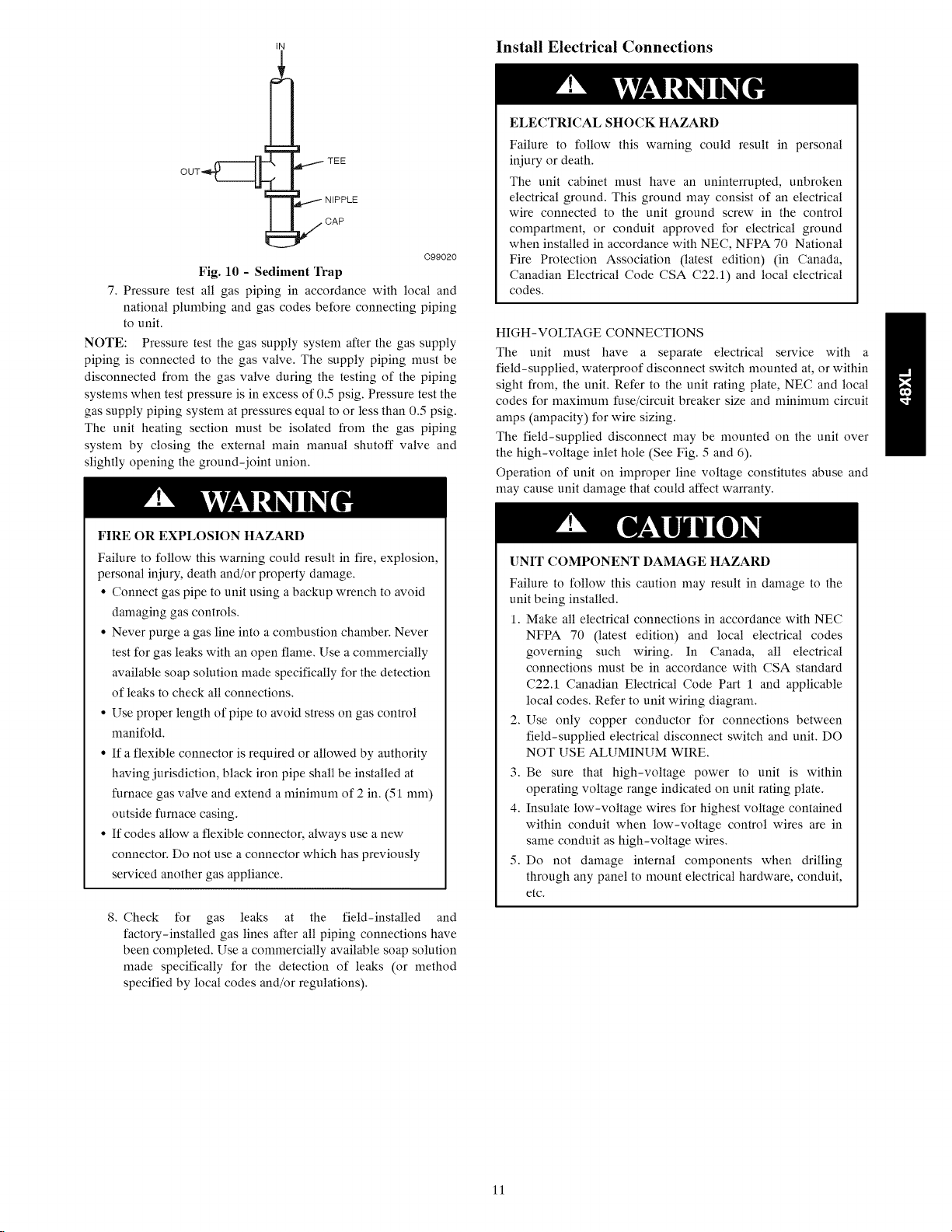
IN
TEE
_-_ NIPPLE
CAP
C99020
Fig. 10 - Sediment Trap
7. Pressure test all gas piping in accordance with local and
national plumbing and gas codes before connecting piping
to unit.
NOTE: Pressure test the gas supply system after the gas supply
piping is connected to the gas valve. The supply piping must be
disconnected from the gas valve during the testing of the piping
systems when test pressure is in excess of 0.5 psig. Pressure test the
gas supply piping system at pressures equal to or less than 0.5 psig.
The unit heating section must be isolated from the gas piping
system by closing the external main manual shutoff valve and
slightly opening the ground-joint union.
Install Electrical Connections
ELECTRICAL SHOCK HAZARD
Failure to follow this warning could result in personal
iniury or death.
The unit cabinet must have an uninterrupted, unbroken
electrical ground. This ground may consist of an electrical
wire connected to the unit ground screw in the control
compartment, or conduit approved for electrical ground
when installed in accordance with NEC, NFPA 70 National
Fire Protection Association (latest edition) (in Canada,
Canadian Electrical Code CSA C22.1) and local electrical
codes.
HIGH-VOLTAGE CONNECTIONS
The unit must have a separate electrical service with a
field-supplied, waterproof disconnect switch mounted at, or within
sight from, the unit. Refer to the unit rating plate, NEC and local
codes for maximum fuse/circuit breaker size and minimum circuit
amps (ampacity) for wire sizing.
The field-supplied disconnect may be mounted on the unit over
the high-voltage inlet hole (See Fig. 5 and 6).
Operation of unit on improper line voltage constitutes abuse and
may cause unit damage that could affect warranty.
FIRE OR EXPLOSION HAZARD
Failure to follow this warning could result in fire, explosion,
personal injury, death and/or property damage.
• Connect gas pipe to unit using abackup wrench to avoid
damaging gas controls.
• Never purge a gas line into a combustion chamber. Never
test for gas leaks with an open flame. Use a commercially
available soap solution made specifically for the detection
of leaks to check all connections.
• Use proper length of pipe to avoid stress on gas control
manifold.
• If a flexible connector is required or allowed by authority
having jurisdiction, black iron pipe shall be installed at
furnace gas valve and extend aminimum of 2 in. (51 mm)
outside furnace casing.
• If codes allow a flexible connector, always use anew
connector. Do not use a connector which has previously
serviced another gas appliance.
8. Check for gas leaks at the field-installed and
factory-installed gas lines after all piping connections have
been completed. Use a commercially available soap solution
made specifically for the detection of leaks (or method
specified by local codes and/or regulations).
UNIT COMPONENT DAMAGE HAZARD
Failure to follow this caution may result in damage to the
unit being installed.
1. Make all electrical connections in accordance with NEC
NFPA 70 (latest edition) and local electrical codes
governing such wiring. In Canada, all electrical
connections must be in accordance with CSA standard
C22.1 Canadian Electrical Code Part 1 and applicable
local codes. Refer to unit wiring diagram.
2. Use only copper conductor for connections between
field-supplied electrical disconnect switch and unit. DO
NOT USE ALUMINUM WIRE.
3. Be sure that high-voltage power to unit is within
operating voltage range indicated on unit rating plate.
4. Insulate low-voltage wires for highest voltage contained
within conduit when low-voltage control wires are in
same conduit as high-voltage wires.
5. Do not damage internal components when drilling
through any panel to mount electrical hardware, conduit,
etc.
11

Table2- MaximumGas Flow Capacity*
NOMINAL INTERNAL LENGTH OF PIPEft (m)'{"
IRON PIPE DIAMETER 10 20 30 40 50 60 70 80 90 100 125 150 175 200
SIZE (IN.) (IN.) (3.0) (6.1) (9.1) (12.1) (15.2) (18.3) (21.3) (24.4) (27.4) (30.5) (38.1) (45.7) (53.3) (61.0)
1/2 .622 175 120 97 82 73 66 61 57 53 50 44 40 -- --
3/4 .824 360 250 200 170 151 138 125 118 110 103 93 84 77 72
1 1.049 680 465 375 320 285 260 240 220 205 195 175 160 145 135
1- 1/4 1.380 1400 950 770 600 580 530 490 460 430 400 360 325 300 280
1- 1/2 1.610 2100 1460 1180 990 900 810 750 690 650 620 550 500 460 430
*Capacity of pipe in cu ft of gas per hr for gas pressure of 0.5 psig or less. Pressure drop of 0.5-IN. W.C. (based on a 0.60 specific gravity gas). Refer to Table,
NFPA 54/ANSI Z223,1.
1-This length includes an ordinary number of fittings.
ROUTING POWER LEADS INTO UNIT
Use only copper wire between disconnect and unit. The high
voltage leads should be in a conduit until they enter the duct panel;
conduit termination at the duct panel must be watertight. Run the
high-voltage leads through the power entry knockout on the
power entry side panel. See Fig. 5 and 6 for location and size. For
single-phase units, connect leads to the black and yellow wires.
CONNECTING GROUND LEAD TO GROUND SCREW
Connect the ground lead to the chassis using the ground screw on
the control plate near the inducer switch (See Fig. 13).
ROUTING CONTROL POWER WIRES
For detailed instruction on the low voltage connections to the User
Interface (UI), refer to the UI installation guide.
Form a drip-loop with the control leads before routing them into
the unit. Route the low voltage control leads through grommeted,
low-voltage hole provided into unit (See Fig. 5 and 6). Connect
user interface leads to unit control power leads as shown in Fig. 14.
The unit transformer supplies 24-v power for complete system
including accessory electrical heater. Transformer is factory wired
for 230-v operation. If supply voltage is 208-v, rewire transformer
primary as described in Special Procedures for 208-v Operation
section.
The furnace board is fused by a board-mounted automotive fuse
placed in series with transformer SEC1 and R circuit. The C circuit
of transformer circuit is referenced to chassis ground through a
printed circuit run at SEC2 and gas valve grounding wire. Check to
be sure control board is mounted securely using both
factory-installed screws.
ACCESSORY INSTALLATION
A. Outdoor Air Thermistor (OAT)
The OAT input is used to supply outdoor temperature data for
system level functions and for temperature display on User
Interface (UI). Using two wires of the field-supplied thermostat
wire cable, wire the ends of the two black OAT pigtails. Wire the
opposite ends of these two wires to the OAT provided with the UI.
There is no polarity to be observed.
NOTE: Mis-wiring OAT inputs will not cause damage to either
Infinity control or thermistor. If the thermistor is wired incorrectly,
no reading will appear at UI. Re-wire thermistor correctly for
normal operation.
B. Humidifier Connections
The furnace control board terminal marked HUM is provided for
low voltage (24-vac) control of a humidifier. No humidistat is
required as UI monitors indoor humidity.
When commanded to operate humidifier, the unit control will
energize the HUM output to turn humidifier on and de-energize
HUM output to turn humidifier off. Wire HUM and COM
terminals directly to humidifier as shown in Fig. 14.
C. Electronic Air Cleaner
Electronic Air Cleaner terminals are provided on the Infinity
Control Board (EAC-I and EAC-2). While these terminals can be
used to power a 230V EAC, it is recommended that any EAC be
installed per the EAC installation instructions and connected
separately to a standard II5V or 230V outlet with an airflow
sensor to control operation of the EAC.
SPECIAL PROCEDURES FOR 208-V OPERATION
Be sure unit disconnect switch is open.
Disconnect the black primary lead from the transformer. See unit
wiring label (See Fig. 16 and 17).
Connect the black primary lead to the transformer terminal labeled
208-v.
EQUIPMENT OPERATION HAZARD
The installation of an outdoor temperature sensor using the
Infinity control board OAT terminals is required. Many
Infinity features (auto humidity control, comfort rollback,
ETC.) will be lost if the OAT is not connected.
For detailed mounting instructions for the OAT sensor,
please refer to TSTATXXSEN01-B installation instructions
(catalog no. 63TS-TAI3): Procedures 1 through 3.
12

TOP COVER
FROM
GAS LINE
Fig. 11 - Typical Installation
GROUND
LEAD
USER
INTERFACE
*NEC - NATIONAL ELECTRICAL CODE
GROUND SCREW
(IN SPLICE BOX)
DISCONNECT
PER NEC*
A06091
SINGLE-PHASE L1
CONNECTIONS
TO DISCONNECT
PER NEC L2 ......
LEGEND
NOTE: Use copper wire only.
NEC - National Electrical Code
Field Wiring
_ Splice Connections
Fig. 12 - Line Power Connections
z_L_ BLKm
-- _YEL_
A06299
13

HP/AC
Board
Furnac6
Board
A06306
Fig. 13 - Control Plate
User
interface
| Factory Wiring
infinity Furnace
m
Board
infinity HP/AC
1
|
|
|
L
Fig. 14 - Control Voltage Wiring Connections
Board
Outdoor Air Thermistor
(Supplied with [U)
FIELD CONNECTION
REQUIRED
OAT
(BLACK WIRES)
OCT
a_Outdeor CoilThermistor
FACTORY CONNECTED
m
0
m
Y2
m
FACTORY WIRES PROVIDED
Y1
m
w1
m
C
FOR FIELD CONNECTION
OF UTiLiTY CURTAILMENT
R
A06301
14

PRE-START-UP
FIRE, EXPLOSION, ELECTRICAL SHOCK
HAZARD
Failure to follow this warning could result in personal
iniury or death and/or property damage.
1. Follow recognized safety practices and wear protective
goggles when checking or servicing refrigerant system.
2. Do not operate compressor or provide any electric power
to unit unless compressor ternfinal cover is in place and
secured.
3. Do not remove compressor ternfinal cover until all
electrical sources are disconnected and tagged.
4. Relieve and recover all refrigerant from system before
touching or disturbing anything inside ternfinal box if
refrigerant leak is suspected around compressor
ternfinals.
5. Never attempt to repair soldered connection while
refrigerant system is under pressure.
6. Do not use torch to remove any component. System
contains oil and refrigerant under pressure.
7. To remove a component, wear protective goggles and
proceed as follows:
a. Shut off gas supply to unit.
b. Shut off electrical power to unit and install
lockout tag.
c. Relieve and reclaim all refrigerant from system
using both high- and low-pressure ports.
d. Cut component connecting tubing with tubing
cutter and remove component from unit.
e. Carefully unsweat remaining tubing stubs when
necessary. Oil can ignite when exposed to flame.
Use the Start-Up Checklist supplied at the end of this book and
proceed as follows to inspect and prepare the unit for initial
start-up:
1. Remove all access panels.
2. Read and follow instructions on all DANGER, WARNING,
CAUTION, and INFORMATION labels attached to, or
shipped with unit.
3. Make the following inspections:
a. Inspect for shipping and handling damages, such as
broken lines, loose parts, disconnected wires, etc.
b. Inspect for oil at all refrigerant tubing connections and
on unit base. Detecting oil generally indicates a
refrigerant leak. Leak test all refrigerant tubing
connections using electronic leak detector, or
liquid-soap solution. If a refrigerant leak is detected, see
following Check for Refrigerant Leaks section.
c. Inspect all field- and factory-wiring connections. Be
sure that connections are completed and tight.
d. Ensure wires do not touch refrigerant tubing or sharp
sheet metal edges.
e. Inspect coil fins. If damaged during shipping and
handling, carefully straighten fins with a fin comb.
4. Verify the following conditions:
a. Make sure gas line is free of air. Before lighting the unit
for the first time, perform the following tasks with the
gas valve in the OFF position.
NOTE: If the gas supply pipe was not purged before connecting
the unit, it will be full of air. It is recommended that the ground
joint union be loosened, and the supply line be allowed to purge
until the odor of gas is detected. Never purge gas lines into a
combustion chamber. Immediately upon detection of gas odor,
retighten the union. Allow 5 nfinutes to elapse, then light unit.
b. Make sure that condenser-fan blade is correctly
positioned in fan orifice. Top 1/3 of condenser fan blade
should be within fan orifice venturi.
c. Ensure fan hub is positioned correctly with respect to
motor housing (See Fig. 24).
d. Make sure that air filter(s) is in place.
e. Make sure that condensate drain trap is filled with water
to ensure proper drainage.
f. Make sure that all tools and nfiscellaneous loose parts
have been removed.
5. Compressors are internally spring mounted. Do not loosen
or remove compressor holddown bolts.
6. Each unit system has two Schrader-type ports, one
low-side Schrader fitting located on the suction line, and
one high-side Schrader fitting located on the compressor
discharge line. Be sure that caps on the ports are tight.
START-UP
Unit Start-Up and Troubleshooting
NOTE: Always check high- and low-voltage supply to the unit
components. Check the integrity of the plug receptacle connections
and unit wiring harness prior to assunfing a component failure.
A. LED Description
LEDs built into Infinity control boards provide installer or service
person information concerning operation and/or fault condition of
the unit controls and ECM motor. This information is also
available at the system UI in text with basic troubleshooting
instructions. Careful use of information displayed will reduce the
need for extensive manual troubleshooting.
Both the furnace and heat pump (HP)/air conditioner (AC) boards
have an amber LED and a green LED. On the HP/AC board, these
are located near the System Conmmnications connector (ABCD)
(lower right corner of the HP/AC board as installed in the unit).
On the furnace board, these are located at the upper right side,
adjacent to the fuse, above the terminal block. The amber LED is
the System Status LED, labeled STATUS. The green LED, labeled
COMM, is used as an indicator of system communications status
(See Fig. 15 and 18).
Status Codes will be displayed on the STATUS LED using the
following protocol:
1. The number of short flashes indicates first digit of code.
2. The number of long flashes indicates second digit of code.
3. A short flash is 0.25 seconds on. A long flash is 1 second
Oil.
4. The time between flashes is 0.25 seconds.
5. The time between last short flash and first long flash is 1
second.
6. The LEDs will be off for 2.5 seconds before repeating code.
7. If multiple status codes are active concurrently, the highest
priority status code is displayed.
B. Control Start-Up and System Communications
Troubleshooting
On power up, green COMM LEDs will be turned off until
successful system conmmnications are established (this should
happen within 10 seconds). Once conmmnications with UI are
successful, both COMM LEDs will be lit and held on. At the same
time, amber STATUS LEDs will be lit and held continuously on
until a request for operating mode is received. The STATUS LED
will be on any time unit is in idle mode.
If, at any time, communications are not successful for a period
exceeding 2 nfinutes, the Infinity control will only allow
15

emergency heating or cooling operation using a common
thermostat and the terminal strip connections on the two control
boards (See Non-Communicating Emergency Cooling/Heating
Mode) and will display Status Code 16, System Communication
Fault, on amber STATUS LED. No further troubleshooting
information will be available at UI until communications are
re-established.
If either COMM LED does not light within proper time period and
status codes are not displayed;
1. Check system transformer high- and low-voltage to be sure
the system is powered.
2. Check ABCD connection on both boards.
3. Check fuse on furnace board to be sure it is not blown. If
fuse is open, check system wiring before replacing it to be
sure a short does not cause a failure of replacement fuse.
If COMM LED does not light within proper time period and status
code is displayed:
1. Check system wiring to be sure UI is powered and
connections are made A to A, B to B, etc. and wiring is not
shorted. Miswiring or shorting of the ABCD
communications wiring will not allow successful
communications.
NOTE: Shorting or miswiring low-voltage system wiring will
not cause damage to unit control or UI but may cause low voltage
fuse to open.
C. Indoor Fan Motor Troubleshooting
The indoor fan is driven by an ECM motor consisting of two parts:
the control module and the motor winding section. Do not assume
motor or module is defective if it will not start. Use the
designed-in LED information aids and follow troubleshooting
steps described below before replacing motor control module or
entire motor. Motor control module is available as a replacement
part.
VERIFY MOTOR WINDING SECTION
ELECTRICALSHOCK HAZARD
Failure to follow this warning could result in personal
iniury or death.
After disconnecting power from the ECM motor, wait at
least 5 minutes before removing the control section. Internal
capacitors require time to discharge.
as long as UI maintains a demand for airflow. The control will not
operate electric heaters while a fault condition exists. The control
communicates with the motor at least once every five seconds,
even when the motor is idle. If, during operation, the control does
not communicate with the motor for more than 25 seconds, the
motor will shut itself down and wait for communications to be
reestablished.
D. Furnace Control Troubleshooting
Furnace control faults indicated by flashing codes on the amber
system STATUS LED can be resolved using troubleshooting
information provided below. Codes are listed in order of their
priority, highest to lowest. Though multiple faults can exist at any
time, only the highest priority code will be displayed on STATUS
LED. Clearing the indicated fault when multiple faults exist will
cause the next highest priority Status Code to be flashed. All
existing faults, as well as a fault history, can be viewed at UI.
STATUS CODE CONTINUOUS OFF
Check for 230 VAC at L1 and L2, and 24 VAC at SEC-1 and
SEC-2.
STATUS CODE CONTINUOUS ON
Control has 24 VAC power.
STATUS CODE 11 - NO PREVIOUS CODE
Stored status codes are erased automatically after 72 hours.
STATUS CODE 12 - BLOWER ON AFTER POWER UP
(230 VAC or 24 VAC) Blower runs for 90 seconds if unit is
powered up during a call for heat (R-W/W1 closed) or (R-W/W1
opens) during blower on-delay period.
STATUS CODE 13 - LIMIT CIRCUIT LOCKOUT
Lockout occurs if a limit or flame rollout switch is open longer
than 3 minutes or 10 successive limit trips occurred during high
heat. Control will auto reset after three hours. Refer to status code
33.
STATUS CODE 14 - IGNITION LOCKOUT
Control will auto reset after three hours. Refer to status code 34.
STATUS CODE 15 - BLOWER MOTOR LOCKOUT
Indicates the blower failed to reach 250 RPM or the blower failed
to communicate within 30 seconds after being turned ON in two
successive heating cycles. Control will auto reset after 3 hours.
Refer to status code 41.
gqRNSA
Before proceeding to replace a motor control module:
1. Check motor winding section to be sure it is functional.
2. Remove motor control module section and unplug winding
plug. Motor shaft should turn freely, resistance between any
two motor leads should be similar and resistance between
any motor lead and unpainted motor end should exceed
100,000 ohms.
3. Failing any of these tests, entire ECM motor must be
replaced.
4. Passing all of the tests, motor control module alone can be
replaced.
MOTOR TURNS SLOWLY
1. Low static pressure loading of blower while access panel is
removed will cause blower to run slowly. Particularly at low
airflow requests. This is normal, do not assume a fault
exists.
2. Recheck airflow and system static pressure using UI service
screens with access panel in place.
NOTE: Blower motor faults will not cause a lockout of blower
operation. The fan coil control will attempt to run the blower motor
ojt
a>-
T°
r_VCZ] _ _O
RN4
D
Fig. 15 - Detail of Furnace Board
16
=
A06026

DANGER:
ELECTRICAL SHOCK HAZARD DISCONNECTPOWERBEFORE SERVICING
UNIT COMPONENTARRANGEMENT
SECTIO_
OUTDOORF_N []
CONNECTIONWIRING DIAGRAM
FIELD SUPPLY I _
208,_3o VAC _'I"M i,,,,_ -
60HZ,IPH
LADDER WIRING DIAGRAM
[]
I
_°
qf_
SAS TI
_°
?
_F[ELD SPLICE
• SPLICE
FACTORY WIRING
- FIEL@ COnTrOL _IRI_G
FIEL@ POWE_ WIRING
RSC REMOTE SPARKER CONTROL
CQNT CONTACTOR
CAP CAPACITOR
COMP COMPRESSOR MOTOR
CS COMPRESSOR SOLENO[D
CCH CRANK CASE HEATER
LEGEND
P
P
PLI 1(c)
TO BE WIRED iN ACCOROANC[ WITH NEC ANO
LOCAL CODES
8LOWER-O_ DELAY FOR GAS _EATING iS 3O SECONDS¸
_LOWER-OYF OELAY FOR GAS H[ATING IS 120 SECONOS
D_AULT WITH Fi[LD SELECTABLE D[LAYS OF gO, 120,
150, OR 180 SECONDS AVAILABLE
8LOWER-OFF OEL_Y _OR COOLING IS 9O SECONDS
IGNITION LOCKOUT OCCURS AFTER FOUR CONSECUTIVE,
UNSUCCESSFUL IGNITION ATTEMPTS CONTROL W_LL
AUTO R[S[T AFTER THREE HOURS¸
co_
COM _
DUSO0003 111_.
>
g
co
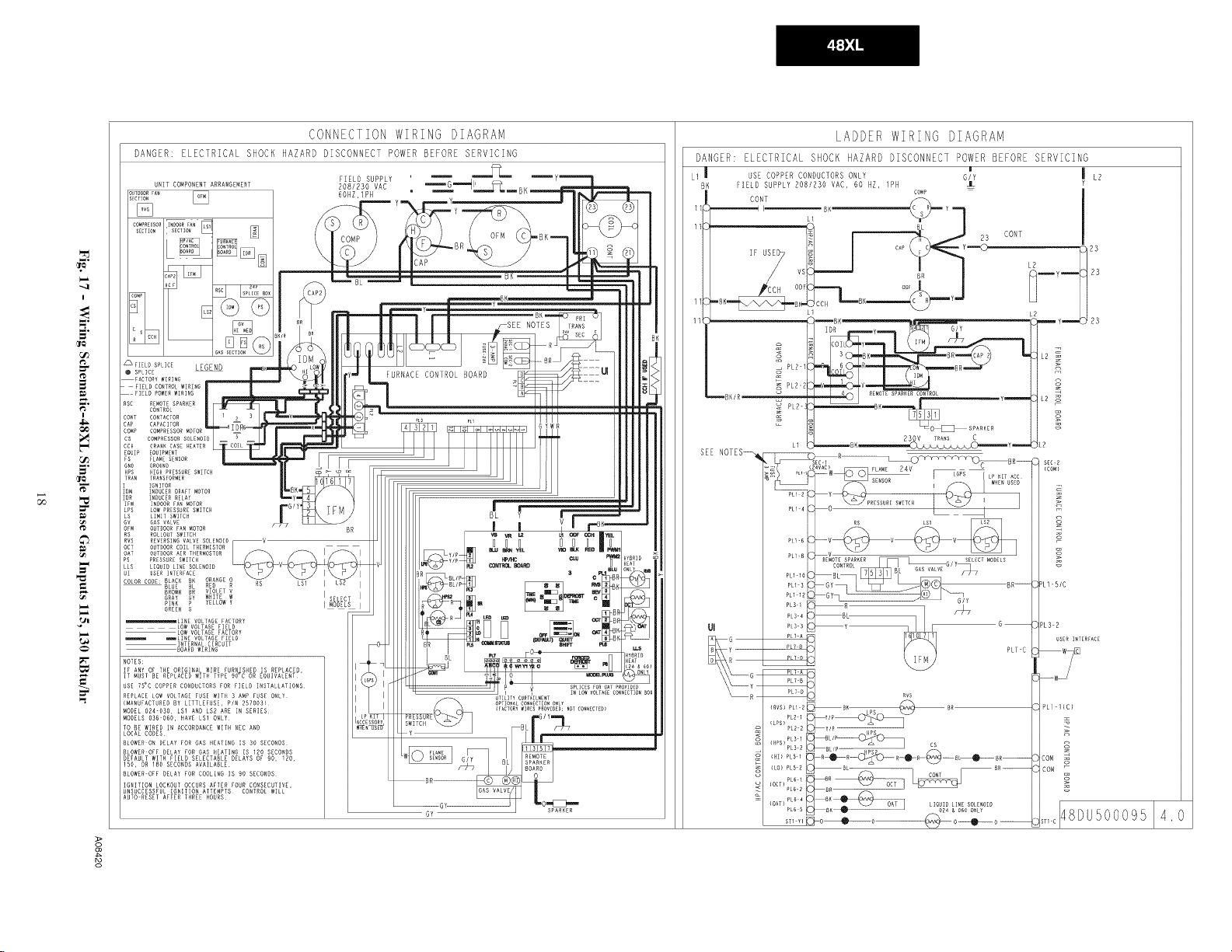
CONNECTION WIRING DIA6RAM
DANGER:
OUTDOORFA,, _ 60HE, 1PH _ _
SECTIO_
ELECTRICAL SHOCK HAZARD DISCONNECT POWERBEFORE SERVICING
UN]T COMPONENT ARRANGEMENT 208/230 VAC _''''_1_
FIELD SUPPLY ------_ ,.._' L_-- _,
LADDER WIRING DIAGRAM
DANGER:
L1 _ USE COPPER CONDUCTORS ONLY
ELECTRICAL SHOCK HAZARD DISCONNECT POWERBEFORE SERVICING
B_ IELD SUPPY 208/230 VAC, 60 mz, PH
Y
SECTION SECTIOn,
I
=.
q_
_o
?
-B,
r
q_
T
ICCH I GAS SECTIO_ @
_ FZELD SPL]CE LEGEND
0 SPL]CE
FACTORY WIRING
FIELD CONTROL WIRING
FIELD POWER WIRING
RSC REMOTE SPARKER
CONTROL
CONT CONTACTOR
CAP CAPACITOR
co_P COMPRESSOR
CS COMPRESSOR SOLENOID
CCH CRANK CASE HEATER
EQUIP EQUIPMENT
FS FLAME SENSOR
G_,D GROUND
HPS HIGH PRESSURE SWITCH
TRAN TRANSFORMER
I
11
SEE NOTES_
CONT I
23
L2
PL1-51C
NOTES;
IF ANY OE THE ORIGinAL WIRE FURNISHED iS REPLACED,
IT MUST BE REPLACED WFH TYPE 90 C OR EQUIVALENT
USE T_C COPPER CONDUCTORS FOR FIELD INSTALLATIONS
REPLACE LOW VOLTAGE FUSE WITH R AMP J:USE ONLY
(MANUFACTURED BY LITTLEFUSE, P/N 257003)
MODEL DR4-DSD, LSI AND LS2 ARE IN SERIES
MODELS D36 D6D, RAVE LSI ONLY
TO BE WIRED iN ACCORDANCE _ITN REC AND
LOCAL CODES
RLOWER-ON DELAY _OR GAS HEATING iS BD SECONDS
BLOWER OFF DELAY FOR GAS HEATING IS IDO SECONDS
DEFAUL_ _ITR EIELD DELECTABLE DELAYS OF DO, 120,
ISD, OR 180 SECONDS AVAILABLE
BLOWER OFF DELAY FOR COOLING IS 90 SECONDS
IGNITION LOCKOUT OCCURS AEPER FOUR CONSECUTIVE.
UNSUCCESSFUL [GNIHON ATTEMPTS CONTROL WILL
AUTO RESET AFTER THREE HOURS
PL>4
UI PL>_
I
I
IT I
PL3 I _!L
GI
PL3 2
PLi l(C)
GOM
CO_
SER INTERFACE
PLT C
DU500095
g
2
o_

o
©
D
O
OOO
°° {]
[
OO
[E]
UTILITY RELAY *
UTILITY SIGNAL
'_ OPEN RELAY
* SUPPLIED BY UTILITY PROVIDER
Fig. 18 - 2-Stage HP/AC Control Board
STATUS CODE 21 - GAS HEATING LOCKOUT
Control will NOT auto reset. Check for mis-wired gas valve or
defective control (valve relay).
STATUS CODE 22 ABNORMAL FLAME-PROVING
SIGNAL
Flame is proved while gas valve is de-energized. Inducer will run
until fault is cleared. Check for leaky gas valve or stuck-open gas
valve.
STATUS CODE 23 - PRESSURE SWITCH DID NOT OPEN
Check for obstructed pressure tubing or pressure switch stuck
closed.
STATUS CODE 24 - SECONDARY VOLTAGE FUSE IS OPEN
Check for short circuit in secondary voltage (24VAC) wiring.
STATUS CODE 25 - INVALID MODEL SELECTION OR
SETUP ERROR
Indicates either the model plug is missing or incorrect. If code
flashes 4 times on power-up, control is defaulting to model
selection stored in memory. Check for proper model plug number
and resistance values per wiring diagram.
STATUS CODE 31, 32 - PRESSURE SWITCH OR RELAY DID
NOT CLOSE OR REOPENED
Control relay may be defective. If open longer than five minutes,
inducer shuts off for 15 minutes before retry. If open during blower
on-delay period, blower will come on for the selected blower
off-delay. Check for excessive wind, restricted vent, defective
inducer motor, defective pressure switch, lower inducer voltage
(230VAC), inadequate combustion air supply, disconnected or
obstructed pressure tubing, or low inlet gas pressure (if LGPS
used).
STATUS CODE 33 - LIMIT CIRCUIT FAULT
Indicates a limit or flame rollout switch is open. Blower will run
for 4 minutes or until open switch remakes, whichever is longer. If
open longer than 3 minutes, code changes to lockout 13. If open
less than 3 minutes status code 33 continues to flash until blower
shuts off. Check for loose blower wheel, restricted vent, excessive
.a
O
•43ff]° O0
0
d]]O
oo
@ IRcD @
Lql_id Ilne So lellold
wind, dirty filter or restricted duct system, defective switch or
connections, or inadequate combustion air supply (flame roll-out
switch open).
STATUS CODE 34 - IGNITION PROVING FAILURE
Control will try three more times before lockout 14 occurs. If flame
signal lost during blower on-delay period, blower will come on for
the selected blower off-delay. Check for oxide buildup on flame
sensor (clean with fine steel wool), proper flame sense microamps
(.5 microamps D.C. min., 4.0-6.0 nominal), manual valve shutoff,
low inlet gas pressure, control ground continuity, gas valve
defective or turned off, flame sensor must not be grounded,
inadequate flame carryover or rough ignition, or green/yellow wire
must be connected to unit sheet metal.
STATUS CODE 41 - BLOWER MOTOR FAULT
Indicates the blower failed to reach 250 RPM or the blower failed
to communicate within the prescribed time limits. Thirty seconds
after being turned ON or ten seconds during steady-state
operation.
STATUS CODE 45 - CONTROL CIRCUITRY LOCKOUT
Auto reset after one hour lockout due to gas valve relay stuck open,
flame sense circuit failure, or software check error. Reset power to
clear lockout. Replace control if status code repeats.
E. HP/AC Control Troubleshooting
See Table 4 for HP/AC control board status codes and
troubleshooting information.
STATUS CODE 53, OUTDOOR AIR TEMPERATURE
SENSOR FAULT - DETAILED DESCRIPTION
If an OAT sensor is found at power-up, input is constantly checked
to be within a valid temperature range. If sensor is found to be
open or shorted at any time after initial validation, Status Code 53
will be displayed at amber STATUS LED.
Check for faults in wiring connecting sensor to OAT terminals.
Using an Ohm meter, check resistance of thermistor for a short or
open condition.
@
A05247
19

Ifthermistor is shorted or open, replace it to return the system to
normal operation. If fault is in the wiring connections, correcting
the fault will clear the code and return the system to normal
operation.
NOTE: If fault condition is an open thermistor or a wiring problem
that appears to be an open thermistor and the power to the unit is
cycled off, the fault code will be cleared on the next power-up but
the fault will remain and system operation will not be as expected.
This is because on power-up, the unit control cannot discern
the difference between an open sensor or if a sensor is not
installed.
Sequence of Operation
The 48XL packaged unit is designed for installation with a
communicating UI. This unit will not respond to commands
provided by a common thermostat except under certain emergency
situations described in Step l--Start-Up and Troubleshooting.
The UI uses temperature, humidity and other data supplied from
indoor and outdoor system components to control heating or
cooling system for optimum comfort. The unit will be commanded
by UI to supply airflow. The unit will operate the indoor blower at
requested airflow for most modes.
INDOOR AIRFLOW ADJUSTMENTS
The nominal requested airflow for air conditioner operations will
be 350 cfm per ton of nominal cooling capacity as defined by unit
size. Actual airflow request will be adjusted from nominal using
indoor and outdoor temperature and indoor humidity data to
optimize the system operation for occupant comfort and system
efficiency. Refer to UI literature for further system control details.
UNIT OPERATION HAZARD
Failure to follow this caution may result in unit damage.
For cooling operation, the recommended airflow is 350 to
450 cfm for each 12,000 Btuh of rated cooling capacity. For
heating operation, the airflow must produce a temperature
rise that falls within the range stamped on the unit rating
plate.
For gas heat operations, Table 3 shows the temperature rise in each
gas heating mode. Refer to these tables to determine the desired
heating airflow for the system being installed.
NOTE: Be sure that all supply-and return-air grilles are open,
free from obstructions, and adjusted properly. Airflow can be
changed using the UI. See UI installation instructions for more
detail.
NOTE: Once the compressor has started and then has stopped, it
should not be started again until 4 minutes have elapsed. The
cooling cycle remains :'on" until the room temperature drops to
point that is slightly below the cooling control setting of the UI.
AIR CONDITIONER SEQUENCE OF OPERATION
COOLING OPERATION
With a call for first stage cooling, the outdoor fan, and low stage
compressor are energized. If low-stage cannot satisfy cooling
demand, high-stage cooling is energized by the UI. After second
stage is satisfied, the unit returns to low-stage operation until first
stage is satisfied or until second stage is required again. When both
first stage and second stage cooling are satisfied, the compressor
will shut off.
NOTE: When two-stage unit is operating at low-stage, system
vapor (suction) pressure will be higher than a standard single-stage
system or high-stage operation.
NOTE: Outdoor fan motor will continue to operate for one
minute after compressor shuts off, when outdoor ambient is greater
than or equal to 100°F (38°C).
UTILITY INTERFACE WITH INFINITY CONTROL
The utility curtailment relay should be connected to factory
supplied pigtails (PINK, connected to R, VIOLET connected to Y2
on the control board) located in the low voltage splice box (See
Fig. 13, 14 and 16). This input allows a power utility device to
interrupt compressor operation during peak load periods. When the
utility sends a signal to shut the system down, the UI will display
"Curtailment Active".
COMPRESSOR OPERATION
When the compressor is operating in low stage, the modulating
ring is deactivated, allowing two internal bypass ports to close off
33% of the scroll compression area so the system operates at part
load capacity. The 24-volt solenoid coil is de-energized in
low-stage operation.
When the compressor is operating at high stage, the modulating
ring is activated, sealing the bypass ports, which allows the
compressor to operate at full load capacity. The 24-volt solenoid
coil is energized in high stage operation.
CRANKCASE HEATER OPERATION (IF APPLICABLE)
The crankcase heater is energized during off cycle below 65°F
(18 °C) outdoor air temperature.
OUTDOOR FAN MOTOR OPERATION
The outdoor unit control energizes the outdoor fan any time the
compressor is operating. The outdoor fan remains energized if a
pressure switch or compressor overload should open. Outdoor fan
motor will continue to operate for one minute after the compressor
shuts off when the outdoor ambient is greater than or equal to
100°F (38°C).
TIME DELAYS-AIR CONDITIONER OPERATIONS
The unit time delays include:
• Five minute time delay to start cooling operation when there is a
call from the thermostat or user interface. To bypass this feature,
momentarily short and release Forced Defrost pins.
• Five minute compressor recycle delay on return from a
brown-out condition.
• Two minute time delay to return to standby operation from last
valid communication (with Infinity only).
• One minute time delay of outdoor fan at termination of cooling
mode when outdoor ambient is greater than or equal to 100°F
(38°C).
• There is no time delay between air conditioner staging from low
to high and from high to low capacity; the compressor will change
from low to high and from high to low capacity as demand
dictates.
20

Table 3 - Air Delivery and Temperature Rise at Rated Heating Input
Unit
48XL(-,N)024040 35
48XL(-,N)030040 (19)
48XL(-,N)030060 25 - 55 25 - 55 40 50
48XL(-,N)036060 60,000 39,000
48XL(-,N)042060 (14-31) (14-31) (22) (28)
48XL(-,N)036090
48XL(-,N)042090 35 - 65 35 - 65 50 55
48XL(-,N)048090 90,000 58,500 (19-36) (19-36) (28) (31)
48XL(-,N)060090
48XL(-,N)048115 115,000 75,000 30 - 60 30 - 60 45 50
48XL(-,N)060115 (17-33) (17-33) (25) (28)
48XL(-,N)048130 130,000 84,500 35 - 65 35 - 65 50 55
48XL(-,N)060130 (19-36) (19-36) (28) (31)
Airflow delivery values for external static pressure values of up to 1IN. W.C.
OPERATION FAULT FLASH POSSIBLE CAUSE AND ACTION
Standby - no call for unit operation None flash Normal operation.
Emergency Mode mostat Control tinuous ity Control. Only high stage operation is available. This operating
Low Stage Cool/Heat Operation None 1, pause Normal operation.
High Stage Cool/Heat Operation None 2, pause Normal operation.
Rated Heating Input (Btu/hr) Heating Rise Range OF(°C) Heating Rise Either Stage, °F (°C)
High Stage Low Stage High Stage Low Stage
40,000 26,000
Table 4 - Heat Pump/Air Conditioner Board Status Codes
Standard Ther- Rapid, con- Unit being controlled by standard thermostat inputs instead of Infin-
System Commu- 16
nications Failure
Invalid Model Plug 25
High-Pressure 31 High-pressure switch trip. Check refrigerant charge, outdoor fan operation
Switch Open and coils for airflow restrictions.
Low-Pressure
Switch Open
Control Fault 45 Outdoor unit control board has failed. Control board needs to be replaced.
Brown Out (230 46 Line voltage < 187v for at least 4 seconds. Compressor and fan operation
v) not allowed until voltage>190v. Verify line voltage.
No 230v at Unit 47 heating demand exists. Verify the disconnect is closed and 230v wiring is
Outdoor Air Temp 53 Outdoor air sensor not reading or out of range. Ohm out sensor and check
Sensor Fault wiring.
Outdoor Coil Sen-
sor Fault
Thermistors Out of 56 Improper relationship between coil sensor and outdoor air sensor. Ohm out
Range sensors and check wiring.
Low Stage Ther- Compressor voltage sensed, then disappears while cooling or heating de-
mal Cutout 71 mand exists. Possible causes are internal compressor overload trip or start
High Stage Ther- Compressor voltage sensed, then disappears while cooling or heating de-
mal Cutout 72 mand exists. Possible causes are internal compressor overload trip or start
Contactor Shorted 73 Compressor voltage sensed when no demand for compressor operation
No 230V at Com- 74 Compressor voltage not sensed when compressor should be starting. Con-
pressor tactor may be stuck open or there is a wiring error.
Low Stage Ther- 81 Thermal cutout occurs in three consecutive low/high stage cycles. Low
mal Lockout stage locked out for 4 hours or until 24v power recycled.
High Stage Ther- 82 Thermal cutout occurs in three consecutive high/low stage cycles. High
mal Lockout stage locked out for 4 hours or until 24v power recycled.
Low-Pressure 83 Low-pressure switch trip has occurred during 3 consecutive cycles. Unit
Lockout operation locked out for 4 hours or until 24v power recycled.
High-Pressure 84 High-pressure switch trip has occurred during 3 consecutive cycles. Unit
Lockout operation locked out for 4 hours or until 24v power recycled.
20 - 50 15-45 35 30 40
(11-28) (8-25) (19) (17) (22)
AMBER LED
CODE
On solid, no
flashing mode should be used in emergency situations only.
Communication with UI lost. Check wiring to UI, indoor and outdoor units.
Control does not detect a model plug or detects an invalid model plug. Unit
will not operate without correct model plug.
32 Low-pressure switch trip. Check refrigerant charge and indoor air flow.
There is no 230v at the contactor when indoor unit ispowered and cooling/
connected to the unit.
55 Coil sensor not reading or out of range. Ohm out sensor and check wiring.
relay not releasing (if installed).
relay not releasing (if installed).
exists. Contactor may be stuck closed or there is a wiring error.
"Efficiency .... Comfort"
High Stage Low Stage High Stage
Low Stage
21

INFINITY CONTROLLED LOW AMBIENT COOLING
NOTE: When this unit is operating below 55°F (13°C) outdoor
temperature, provisions must be made for low ambient operation.
This unit is capable of low ambient cooling down to 0°F
(-18°C).ONLY when using the Infinity control. A low ambient kit
is not required, and the outdoor fan motor does not need to be
replaced for Infinity controlled low ambient operation. Low
ambient cooling must be enabled in the UI set-up. Fan may not
begin to cycle until about 40°F (4°C).OAT. Fan will cycle based
on coil and outdoor air temperature. Infinity controlled low
ambient mode operates as follows:
• In high stage, fan is off when outdoor coil temp is <outdoor air
temperature plus 3 ° F (1.7 ° C) or outdoor fan has been ON for 30
minutes. (Fan is turned off to allow refrigerant system to
stabilize.)
• In low stage, fan is off when outdoor coil temp is <outdoor air
temperature plus 1 °F (.6°C) or outdoor fan has been ON for 30
minutes. (Fan is turned off to allow refrigerant system to
stabilize.)
• In high stage and low stage, fan is on when outdoor coil temp >
outdoor air temperature plus 25 °F (13.8 °C) or outdoor coil temp
> 80°F (27°C) or if outdoor fan has been OFF for 30 minutes.
(Fan is turned on to allow refrigerant system to stabilize.)
• Low-pressure switch is ignored for first 3 minutes during low
ambient start up. After 3 minutes, if LPS trips, then outdoor fan
motor is turned off for 10 minutes with the compressor running. If
LPS closes within 10 minutes then cooling continues with the
outdoor fan cycling per the coil temperature routine listed above
for the remainder of the cooling cycle. If the LPS does not close
within 10 minutes, then the normal LPS trip response (shut down
cooling operation and generate LPS trip error) will occur.
DEHUMIDIFICATION MODE
This Infinity system can be used to dehumidify the living space.
See UI Installation Instructions for more details.
SEQUENCE OF OPERATION-GAS HEAT
NOTE: Infinity control must be grounded for proper operation or
control will lock out.
NOTE: If a power interruption occurs during a call for heat, the
control will start a 90-second blower only ON period two seconds
after power is restored, if the UI is still calling for gas heating. The
amber LED light will flash code 12 during the 90-second period,
after which the LED will be ON continuously, as long as no faults
are detected. After the 90-second period, the unit will respond to
the UI normally.
GAS HEAT MODE AND ADJUSTMENTS
When the UI calls for gas heat, the Infinity furnace board performs
a self-check, verifies the pressure switch is open, and starts the
inducer on high speed.
1. Inducer Pre-purge Period: When the inducer motor comes
up on high speed, the pressure switch closes, and the
Infinity ignition control on the furnace board begins a 15
second pre-purge period. If the pressure switch fails to
remain closed, the inducer will remain running. After the
pressure switch re-closes, the Infinity ignition control will
begin a 15 second pre-purge period.
2. Trial-For-Ignition Sequence: The spark igniter will spark
for 3 seconds. The main gas valve relay contact closes to
energize the gas valve on low stage. After 5 seconds, the
igniter is de-energized and a 2-second flame-proving
period begins. NOTE: The unit always lights on high
speed inducer and low stage gas valve operation.
3. Flame-Proving: When the burner flame is proved at the
flame-proving sensor, the furnace control determines what
heating stage to run based on feedback from the UI. If the
UI is asking for low stage gas heat, the ignition control will
change the inducer speed to low speed and keep the gas
valve energized on low stage. If the UI is asking for high
stage gas heat, the ignition control will maintain running the
inducer on high speed and energize the gas valve's high
stage relay to increase gas flow.
If the burner flame is not proved within 2 seconds, the control will
close the gas valve and repeat the ignition sequence up to 3 more
Trials-For-Ignition before going to Ignition-Lockout. Lockout
will reset automatically after 3 hours, by momentarily interrupting
230 VAC power, or by interrupting 24 VAC power at SEC1 or
SEC2 to the furnace board.
If flame is proved when there should be no flame present, control
will lock out of Gas-Heating mode and operate the inducer motor
until flame is no longer proved.
4. Blower-On Delay: If the burner flame is proven,
approximately 37 seconds after the gas valve is opened the
Indoor Blower is turned on to the appropriate speed for the
gas heating stage.
Simultaneously, the humidifier terminal HUM and electronic air
cleaner terminal EAC-I are energized throughout the heating
cycle.
NOTE: EAC-2 terminal is common with L2 and will have
ll5VAC-to-ground when unit is powered.
5. Blower-Off Delay: When the call for gas heat is satisfied,
the gas valve is de-energized, stopping the flow of gas to
the burners, and de-energizing the HUM terminal. The
inducer motor will remain on for a 4-second post-purge
period. The indoor blower and air cleaner terminal EAC-I
will remain energized for 90, 120, 150, or 180 seconds
(depending on selection of blower-off delay selected in the
UI). The factory-set default is 120-second blower-OFF
delay.
CHECK GAS INPUT (NATURAL GAS)
[]NIT DAMAGE HAZARD
Failure to follow this caution may result in component
damage.
Do not redrill an orifice. Improper drilling (burrs,
out-of-round holes, etc.) can cause excessive burner noise
and misdirection of burner flame. If orifice hole appears
damaged or it is suspected to have been redrilled, check
orifice hole with a numbered drill bit of correct size.
FIRE HAZARD
Failure to follow this warning could result in personal
iniury, death and/or property damage.
DO NOT bottom out gas valve regulator adjusting screws.
This can result in unregulated manifold pressure and result
in excess overfire and heat exchanger failures.
22

CARBONMONOXIDEPOISONINGHAZARD
Failureto follow this warning could result in personal
iniury and/or death.
If the manifold pressure and/or gas rate is not properly
adjusted on HI and LO stages, excess carbon monoxide can
be produced.
FIRE AND UNIT DAMAGE HAZARD
Failure to follow this warning could result in personal
iniury or death and/or property damage.
Unsafe operation of the unit may result if manifold pressure
is outside of the ranges listed in Table 6.
Gas input rates on rating plate are for installations at altitudes up to
2000 ft (610 m). Input rate must be within - 2% of rating plate
input.
1. Determine the correct gas input rate.
a. The rated gas inputs shown in Table 4 are for altitudes
from sea level to 2000 ft (610 m) above sea level.
These inputs are based on natural gas with a heating
value of 1050 Btu/ft3 at .65 specific gravity.
IN THE U.S.A.:
The input rating for altitudes above 2,000 ft (610 m) must be
reduced by 4 percent for each 1,000 ft (305 m) above sea level.
For installations below 2,000 ft, (610 m) refer to the unit rating
plate.
For installations above 2,000 ft, (610 m) multiply the input by on
the rating plate by the derate multiplier in Table 6 for the correct
input rate.
Table 5 - Altitude Derate Multiplier for U.S.A.
Altitude ft (m) Percent of Derate Factor*
0-2000
(0-610) 0 1.00
2001-3000
(610-914) 8-12 0.90
3001-4000
(915-1219) 12-16 0.86
4001-5000
(1220-1524) 16-20 0.82
5001-6000
(1524-1829) 20-24 0.78
6001-7000
(1829-2134) 24-28 0.74
7001-8000
(2134-2436) 28-32 0.70
8001-9000
(2139-2743) 32-36 0.66
9001-10,000 36-40 0.62
(2744-3048)
:'Derate multiplier factors are based on midpoint altitude for altitude range,
IN CANADA:
The input rating for altitudes from 2,000 (610 m) to 4,500 ft (1372
m) above sea level must be derated 10 percent by an authorized
Gas Conversion Station or Dealer.
EXAMPLE:
90,000 Btuh Input Furnace Installed at 4300 ft (1372 m).
Furnace Input Rate Derate Multiplier Furnace Input Rate
at Sea Level X Factor at Installation
Altitude
90,000 X 0.90 = 81,000
Derate Multiplier
b. When the gas supply being used has a different heating
value or specific gravity, refer to national and local
codes, or contact your distributor to determine the
required orifice size.
2. Adjust manifold pressure to obtain low stage input rate (See
Fig. 19).
a. Turn off gas supply to unit.
b. Remove pipe plug on manifold (See Fig. 20) and
connect manometer. Turn on gas supply to unit.
c. Turn gas valve switch to ON.
d. Set unit to run for 20 minutes in low-stage gas heat
operation using the "INSTALLER CHECKOUT" menu
on the User Interface.
e. Remove regulator adjustment cap from low stage gas
valve pressure regulator (See Fig. 19) and turn
low-stage adjusting screw (3/16 or smaller flat-tipped
screwdriver) counterclockwise (out) to decrease rate and
clockwise (in) to increase input rate.
1/2" NPT iNLET
1/2' NPT OUTLET J _ PDAE_'/FOLDE TAP
A04167
Fig. 19 - Redundant Automatic Gas Control Valve
NOTE: DO NOT set low stage manifold pressure less than 1.4
IN. W.C. or more than 2.0 IN. W.C. for natural gas. If manifold
pressure is outside this range, change main burner orifices.
f. Re-install low stage regulator adjustment cap.
g. Leave manometer connected.
NOTE: If orifice hole appears damaged or it is suspected to have
been re-drilled, check orifice hole with a numbered drill bit of the
correct size. Never re-drill an orifice. A burr-free and squarely
aligned orifice hole is essential for proper flame characteristics.
3. Verify natural gas low stage input rate.
a. Turn off all other gas appliances and pilots served by
the gas meter.
b. If unit is not running, set unit to run for 20 minutes in
low-stage gas heat operation using the "INSTALLER
CHECKOUT" menu on the UI.
c. Record number of seconds for gas meter to complete
one revolution.
d. Divide number of seconds in step c. into 3600 (number
of seconds in 1 hour).
e. Multiply result of step d. by the number of cubic feet
shown for one revolution of test dial to obtain cubic feet
of gas flow per hour.
f. Multiply result of step f. by Btu heating value of the gas
to obtain total measured input shown in Table 4.
(Consult the local gas supplier if the heating value of
gas is not known).
EXAMPLE: Assume a 90,000 high stage input unit is being
installed. Assume that the size of the dial is 2 cubic ft., one
revolution takes 129 sec., and the heating value of the gas is 1050
Btu/ft3. Proceed as follows:
23

a.129sec.to complete one revolution
b. 3600/129 = 27.9
c. 27.9 x 2 = 55.8 ft3 of gas flow/hr.
d. 55.8 x 1050 = 58,590 Btuh input.
In this example, the nonfinal input rate for low stage is 58,500
Btu/hr, so the low stage manifold pressure is correctly set.
If the measured low stage rate is too low, increase the manifold
pressure to increase rate. If the measured low stage rate is too high,
decrease the manifold pressure to decrease rate.
NOTE: Double-check that UI is running on low stage gas heat
while clocking the low stage firing rate.
4. Verify proper low stage gas heat temperature rise.
a. Furnace must operate within rise range listed on rating
plate.
b. Select "COMFORT" or "EFFICIENCY" mode on UI.
"COMFORT" mode will provide a warmer supply air
temperature, while "EFFICIENCY" will provide lower
gas consumption.
c. Make sure access panel is re-installed on the unit.
d. Measure supply and return temperatures as close to the
unit as possible. Subtract the return temperature from
the supply temperature to deternfine rise. Rise should
fall within the range specified on the rating plate.
5. Adjust manifold pressure to obtain high stage input rate
(See Fig. 19).
a. Set unit to run for 20 minutes in high-stage gas heat
operation using the "INSTALLER CHECKOUT" menu
on the UI.
b. Remove regulator adjustment cap from high stage gas
valve pressure regulator (See Fig. 19) and turn
high-stage adjusting screw (3/16 or smaller flat-tipped
screwdriver) counterclockwise (out) to decrease rate and
clockwise (in) to increase input rate.
NOTE: DO NOT set high stage manifold pressure less than 3.2
IN.W.C. or more than 3.8 IN. W.C. for natural gas. If manifold
pressure is outside this range, change main burner orifices.
c. Re-install high stage regulator adjustment cap.
d. Leave manometer connected.
6. Verify natural gas high stage input rate.
a. Turn off all other gas appliances and pilots served by
the gas meter.
b. If unit is not running, set unit to run for 20 minutes in
high stage gas heat operation using the "INSTALLER
CHECKOUT" menu on the UI.
c. Record number of seconds for gas meter to complete 1
revolution.
d. Divide number of seconds in step c. into 3600 (number
of seconds in 1 hour).
e. Multiply result of step d. by the number of cubic feet
shown for one revolution of test dial to obtain cubic feet
of gas flow per hour.
f. Multiply result of step f. by Btu heating value of the gas
to obtain total measured input shown in Table 4.
(Consult the local gas supplier if the heating value of
gas is not known).
EXAMPLE: Assume a 90,000 high stage input unit is being
installed. Assume that the size of the dial is 2 cubic ft., one
revolution takes 84 sec., and the heating value of the gas is 1050
Btu/ft3. Proceed as follows:
a. 84 sec. to complete one revolution
b. 3600/84 = 42.9
c. 42.9 x 2 = 85.8 ft3 of gas flow/hr.
d. 85.8 x 1050 = 90,090 Btuh input.
In this example, the nonfinal input rate for high stage is 90,000
Btu/hr, so the high stage manifold pressure is correctly set.
If the measured high stage rate is too low, increase the manifold
pressure to increase rate. If the measured high stage rate is too
high, decrease the manifold pressure to decrease rate.
NOTE: Double-check that User Interface is running on high stage
gas heat while clocking the low stage firing rate.
7. Verify proper high stage gas heat temperature rise.
a. Furnace must operate within rise range listed on rating
plate.
b. Make sure access panel is re-installed on the unit.
c. Measure supply and return temperatures as close to the
unit as possible. Subtract the return temperature from
the supply temperature to deternfine rise. Rise should
fall within the range specified on the rating plate.
NOTE: If the temperature rise is outside the rating plate range,
first check:
a. Gas input for low and high stage gas heat operation.
b. Derate for altitude, if applicable.
c. Return and supply ducts for excessive restrictions
causing static pressures in excess of .5 IN. W.C.
d. Make sure model plug is installed.
8. Final Check
a. Turn off gas to unit
b. Remove manometer from pressure tap.
c. Replace pipe plug on manifold (See Fig. 20).
d. Turn on gas to unit.
e. Check for leaks.
CHECK GAS INPUT (PROPANE GAS)
Refer to propane kit installation instructions for properly checking
gas input.
NOTE: For installations below 2,000 ft (610 m), refer to the unit
rating plate for proper propane conversion kit. For installations
above 2,000 ft (610 m), contact your distributor for proper propane
conversion kit.
CHECK BURNER FLAME
With burner access panel removed, observe the unit heating
operation. Watch the burner flames to see if they are light blue and
soft in appearance, and that the flames are approximately the same
for each burner. Propane will have blue flame (See Fig. 21). Refer
to the Maintenance section for information on burner removal.
MANIFOLD PIPE PLUG
099019
Fig. 20 - Burner Assembly
24

BURNERFLAME
BURNER
MANIFOLD
C99021
Fig. 21 - Monoport Burner
LIMIT SWITCHES
Normally closed limit switch (LS) completes the control circuit.
Should the leaving-air temperature rise above the maximum
allowable temperature, the limit switch opens and the control
circuit "breaks." Any interruption in the control circuit instantly
closes the gas valve and stops gas flow to the burners and pilot.
The blower motor continues to run until LS resets. The furnace
board STATUS LED will display STATUS CODE 33.
When the air temperature at the limit switch drops to the
low-temperature setting of the limit switch, the switch closes and
completes the control circuit. The direct-spark ignition system
cycles and the unit returns to normal heating operation.
ROLLOUT SWITCH
The function of the rollout switch is to close the main gas valve in
the event of flame rollout. The switch is located above the main
burners. When the temperature at the rollout switch reaches the
maximum allowable temperature, the control circuit trips, closing
the gas valve and stopping gas flow to the burners. The indoor fan
motor (IFM) continues to run until switch is reset. The furnace
board STATUS LED will display STATUS CODE 33.
CONTINUOUS FAN MODE
When continuous fan operation is requested by the UI indoor fan
motor will operate at continuous blower airflow. Continuous fan
operation is programmable. See the UI Owner's Manual for
detailed instructions. Terminal EAC-I is energized as long as the
indoor fan motor is energized.
During a call for gas heat, the Infinity control will transition the
indoor fan motor to continuous blower airflow or gas heat airflow,
whichever is lowest. The indoor fan motor will remain ON until
the burners ignite, then shut OFF and remain OFF for the
blower-ON delay allowing the heat exchangers to heat up more
quickly, then restarts at the end of the blower-ON delay period.
The indoor fan motor will revert to continuous-blower airflow
after the gas heating cycle is completed.
When the UI "calls for cooling", the indoor fan motor will switch
to operate at cooling airflow. When the call for cooling is satisfied,
the indoor fan motor will operate an additional 90 seconds at
cooling airflow before transitioning back to continuous-blower
airflow.
When the call for continuous fan is removed, the indoor blower
will continue operating for an additional 5 seconds before shutting
down, if no other function requires blower motor operation.
COMPONENT TEST
The Infinity Furnace Board features a gas component test system to
help diagnose a system problem in the case of a gas component
failure. To initiate the component test procedure, ensure that there
are no UI inputs to the control (the ABCD connector can be
removed from the Infinity control board for this operation) and all
time delays have expired. Turn on setup switch SWl-6.
NOTE: The component test feature will not operate if the control
is receiving any UI signals or until all time delays have expired.
The component test sequence is as follows:
1. The control turns the inducer motor ON and keeps it ON
through step 3.
2. After waiting 10 seconds, the control turns the igniter ON
for 15 seconds, then OFF.
3. The control then turns the indoor fan motor on for 15
seconds, then OFF.
4. After shutting the blower motor OFF, the control runs the
inducer for 10 seconds, then turns it OFF.
NOTE: The EAC terminals are energized when the blower is
operating.
After the component test is completed, one or more status codes
(11, 25, or 41) will flash. See component test section or Status
Code Label for explanation of status codes.
NOTE: To repeat component test, turn setup switch SWl-6 to
OFF and then back ON.
Check for Refrigerant Leaks
Locate and repair refrigerant leaks and charge the unit as follows:
1. Use both high- and low-pressure ports to relieve system
pressure and reclaim remaining refrigerant.
2. Repair leak following accepted practices.
NOTE: Install a filter drier whenever the system has been opened
for repair.
3. Check system for leaks using an approved method.
4. Evacuate refrigerant system and reclaim refrigerant if no
additional leaks are found.
5. Charge unit with Puron (R-410A) refrigerant, using a
volumetric-charging cylinder or accurate scale. Refer to
unit rating plate for required charge.
Start-Up Adjustments
Complete the required procedures given in the Pre-Start-Up
section before starting the unit. Do not jumper any safety devices
when operating the unit. Do not operate the unit in cooling mode
when the outdoor temperature is below 40°F (4°C) (unless
low-ambient operation is enabled in the UI). Do not rapid cycle
the compressor. Allow 5 min. between "on" cycles to prevent
compressor damage.
CHECKING COOLING AND HEATING CONTROL
OPERATION
See UI Installation Instructions for detailed system CHECKOUT.
CHECKING AND ADJUSTING REFRIGERANT CHARGE
The refrigerant system is fully charged with Puron (R-410A)
refrigerant and is tested and factory sealed.
NOTE: Any adjustment to refrigerant charge must be done with
unit operating in HIGH stage.
NOTE: Adjustment of the refrigerant charge is not required
unless the unit is suspected of not having the proper R-410A
charge. The charging label and the tables shown refer to system
temperatures and pressures in cooling mode only. A refrigerant
charging label is attached to the outside of the unit.
25

Table 6 - Heating Inputs
HEATING INPUT(BTU/HR)*
High Stage Min Max Low Stage
40,000 4.0 13.0 1.4 - 2.0
60,000 4.0 13.0 1.4 - 2.0
90,000 4.0 13.0 1.4 _ 2.0
115,000 4.0 13.0 1.4 _ 2.0
130,000 4.0 13.0 1.4 _ 2.0
*Cubic ft of natural gas per hour for gas pressures of .5 psig (14 IN. W.C.) or less and a pressure drop of .5 IN. W.C. (based on a .60 specific gravity gas). Ref:
Table 6.2 (b) NPFA 54 / ANSI Z223.1.
UNIT STANDARD CFM (SCFM)
SIZE 600 1100 1200 1300 1700 1800 1900 2100
024 0.005
030
036
042
O48
060
Low Stage
26,000
39,000
58,500
75,000
84,500
700 800
0.007 0.010
0.007 0.010
NUMBER OF
ORIFICES
900 1000
0.012 0.015
0.012 0.015
0.019 0.023
0.014
2
3
3
3
3
Table 7 - ECM Wet Coil Pressure Drop (IN. W.C.)
0.018 0.021 0.024
0.027 0.032 0.037
0.017 0.020 0.024
GAS SUPPLY PRESSURE (IN. W.C.)
0.027 0.032
Natural
1400 1500 1600 2000
0.042 0.047
0.027 0.031 0.035 0.039 0.043
0.036 0.041 0.046 0.052 0.057 0.063 0.068
0.029 0.032 0.036 0.040 0.045 0.049 0.053
MANIFOLD PRESSURE (IN. W.C.)
Natural
High Stage
3.2-3.8
3.2-3.8
3.2-3.8
3.2-3.8
3.2-3.8
Table 8 - Filter Pressure Drop Table (IN. W.C.)
FILTERSIZE CFM
in.(mm) 500 600 700 800 900 1000 1100 1200 1300 1400 1500 1600 1700 1800 1900 2000 2100 2200 2300
20X20X1
(508x508x25)
24X30X1
(610x762x25)
24X36X1
(610x914x25)
0.05 0.07 0.08 0.1 0.12 0.13 0.14 0.15 ...........
.... 0.05 0.6 0.07 0.07 0.08 0.09 0.1 ........
....... 0.06 0.07 0.07 0.08 0.09 0.09 0.10 0.11 0.12 0.13 0.14 0.14
IMPORTANT: When evaluating the refrigerant charge, an
indicated adjustment to the specified factory charge must always be
very minimal. If a substantial adjustment is indicated, an abnormal
condition exists somewhere in the cooling system, such as
insufficient airflow across either coil or both coils.
REFRIGERANT CHARGE
The amount of refrigerant charge is listed on the unit rating plate
and/or the physical data table. Refer to the Refrigeration Service
Techniques Manual, Refrigerants Section.
NO CHARGE
Check for leak. Use standard evacuating techniques. After
evacuating system, weigh in the specified amount of refrigerant
(refer to system rating plate).
LOW CHARGE COOLING
Use Cooling Charging Chart (Fig. 23). Vary refrigerant until the
conditions of the chart are met. Note that charging charts are
different from type normally used. Charts are based on charging
the units to correct subcooling for the various operating conditions.
Accurate pressure gauge and temperature sensing devices are
required. Connect the pressure gauge to the service port on the
suction line. Mount the temperature sensing device on the suction
line and insulate it so that the outdoor ambient does not affect the
reading. Indoor air CFM must be within the normal operating
range of the unit.
TO USE COOLING CHARGING CHARTS
Take the liquid line temperature and read the manifold pressure
gauges.
Refer to the chart to determine what the liquid line temperature
should be.
NOTE: If the problem causing the inaccurate readings is a
refrigerant leak, refer to Check for Refrigerant Leaks section.
NON-COMMUNICATING EMERGENCY COOLING /
HEATING MODE: 4-WIRE THERMOSTAT
This mode of operation is provided only in the case where the UI
has failed or is otherwise unavailable. If communications cannot be
established with the UI, the Infinity furnace board will enable the
standard thermostat input terminals to allow simple thermostatic
control of the 48XL unit.
For control with a standard thermostat, disconnect the ABCD
connectors from both control boards and using No. 18 AWG
color-coded, insulated type 90°C minimum or equivalent wire,
make the connections between the standard thermostat, the furnace
board, and the HP/AC board per Fig. 22. Recommend the use of
interconnecting wire with 105C, 600V, 2/64" insulation.
The Infinity control will respond to cooling and heating demands
with the maximum safe airflow based on gas furnace output and
unit cooling capacity.
26

infinity Furnace infinityHP/AC
Board Board
OutdoorAirThermistor
(SuppliedwithIU)
FIELDCONNECTION
REQUIRED
(BLACKWIRES)
Standard
4=Wire
Thermostat
OutdoorCoil Thermistor
FACTORYCONNECTED
_'m m
FACTORYWIRESPROVIDED
FOR FIELDCONNECTION
OFUTiLiTY CURTAILMENT
Fig. 22 - Non-Communicating Emergency Cooling/Heating Wiring Connections
Required Subcooling °F (°C) Required Liquid LineTemperaturefor a SpecificSubcooling (R-410A)
ModelSize Pressure Pressure
Outdoor Ambient Temperature Required Subeoolin9(°F) Required Subcooling (°C)
AO6302
024 15.5(8.6) 15.6(8.7)15.7(8.7)15.8(8.8)15.9(8.9) 174 56 5I 46 36 1200 13 I1 8 2
030 16.8(93) 16,4(9.I) I6.2(9) 156(8,7) 15(8,3) I81 59 54 49 39 1248 15 I2 9 4
036 14(7.7) 13.9(7.7) 13.9(7.7) 13.8(7.7) 13.7(7.6) 188 61 56 51 41 1296 16 13 10 5
042 19.2( 10.7 ) 19.1 ( 10.6 ) 19.1( 10.6 ) 18.9 ( 10.5) 18.7( 10.4 ) 195 63 58 53 43 1344 17 14 12 6
048 21(11.6) 20.8(11.5) 20,7(11.5) 20,4(11,3) 20.2(11.2) 202 65 60 55 45 1393 18 16 13 7
oe° 16.2(9) 16.6(9.2) 16.8(9.3) 17.3(9.6) 17.8(9.9) 209 67 62 57 47 1441 20 17 14 9
216 69 64 59 49 1489 2I 18 15 10
223 71 66 61 51 1537 22 19 16 11
Char in Procedure 230 73 68 63 53 1586 23 20 17 12
1- MeasureDischargeline pressurebyattachinga gaugeto theservice port. 237 75 70 65 55 I834 24 21 I9 I3
2- Measurethe Liquidlinetemperatureby attachingatemperaturesensingdevice toit, 244 77 72 67 57 1882 25 22 20 14
3- insulatethe temperaturesensingdeviceso that theOutdoorAmbient doesn'taffect
the reading, 259 81 76 71 61 1786 27 24 22 16
4- Refertothe required Subcooiingin thetable basedon the model size andthe 267 83 78 73 63 1841 28 26 23 17
275 85 80 75 65 1896 29 27 24 18
OutdoorAmbient temperature. 283 87 82 77 67 1951 31 28 25 19
5- Interpolateif theOutdoortemperaturelies in betweenthetable values, Extrapolateif 291 89 84 79 69 2008 32 29 28 20
the temperatureliesbeyondthe tablerange. 299 91 86 81 71 2061 33 30 27 22
6- Findthe PressureValue correspondingto the themeasured Pressureon the 308 93 88 83 73 2123 34 31 28 23
CompressorDischargeline.
7- Readacrossfrom the Pressurereadingto obtainthe Liquid linetemperaturefor a
requiredSubcooIing.
8-Add Charge if the measuredtemperatureis higherthan theliquidline temperature
valuein the table.
9-Add Charge usingthe serviceconnection on the Suctionline of the Compressor,
317 95 90 85 75 2185 35 32 29 24
326 97 92 87 77 2247 36 33 30 25
335 99 94 89 79 2309 37 34 31 26
344 101 96 9I 81 2372 38 35 33 27
353 102 97 92 82 2434 39 36 34 28
363 104 99 94 84 2503 40 37 35 29
373 106 101 96 86 2571 41 39 36 30
383 108 103 98 88 2640 42 40 37 31
393 110 105 100 90 2709 43 4I 38 32
403 112 107 102 92 2778 44 42 39 33
413 114 109 104 94 2847 45 43 40 34
423 116 111 106 96 2916 46 44 41 35
433 117 112 107 97 2985 47 45 42 36
443 119 114 109 99 3054 48 46 43 37
453 121 116 111 101 3123 49 47 44 38
463 I22 117 112 102 3192 50 47 45 39
473 124 119 114 104 3261 51 48 46 40
483 126 121 116 106 3330 52 49 47 41
493 127 122 117 107 3399 53 50 47 42
503 129 124 119 109 3468 54 51 48 43
513 130 125 120 110 3537 55 52 49 44
523 132 127 122 112 3606 56 53 50 44
533 133 128 123 113 3675 56 54 51 45
50DU500166- 2,0
AO8423
Fig. 23 - Cooling Charging Table-Subcooling
27

MAINTENANCE
To ensure continuing high performance, and to minimize the
possibility of premature equipment failure, periodic maintenance
must be performed on this equipment. This packaged unit should
be inspected at least once each year by a qualified service person.
To troubleshoot unit, refer to Table 10, Troubleshooting Chart.
NOTE TO EQUIPMENT OWNER: Consult your local dealer
about the availability of a maintenance contract.
PERSONAL INJURY AND UNIT DAMAGE
HAZARD
Failure to follow this warning could result in personal
injury or death and possible unit component damage.
The ability to properly perform maintenance on this
equipment requires certain expertise, mechanical skills,
tools and equipment. If you do not possess these, do not
attempt to perform any maintenance on this equipment,
other than those procedures recommended in the Owner's
Manual.
ELECTRICAL SHOCK HAZARD
Failure to follow these warnings could result in personal
injury or death:
1. Turn off electrical power to the unit before performing
any maintenance or service on this unit.
2. Use extreme caution when removing panels and parts.
3. Never place anything combustible either on or in contact
with the unit.
[]NIT OPERATION HAZARD
Failure to follow this caution may result in equipment
damage or improper operation.
Errors made when reconnecting wires may cause improper
and dangerous operation. Label all wires prior to
disconnecting when servicing.
The minimum maintenance requirements for this equipment are as
follows:
1. Inspect air filter(s) each month. Clean or replace when
necessary.
2. Inspect indoor coil, drain pan, and condensate drain each
cooling season for cleanliness. Clean when necessary.
3. Inspect indoor fan motor and wheel for cleanliness each
cooling season. Clean when necessary.
4. Check electrical connections for tightness and controls for
proper operation each cooling season. Service when
necessary.
5. Check for restrictions on inducer outlet. Clean flue hood.
6. Inspect burner compartment before each heating season for
rust, corrosion, soot or excessive dust.
7. Inspect all accessories. Perform any service or maintenance
to the accessories as recommended in the accessory
instructions.
Air Filter
IMPORTANT: Never operate the unit without a suitable air filter
in the return-air duct system. Always replace the filter with the
same dimensional size and type as originally installed. See Table 1
for recommended filter sizes.
Inspect air filter(s) at least once each month and replace
(throwaway-type) or clean (cleanable-type) at least twice during
each cooling season and twice during the heating season, or
whenever the filter becomes clogged with dust and lint.
Indoor Fan and Motor
NOTE: All motors are pre-lubricated. Do not attempt to lubricate
these motors.
For longer life, operating economy, and continuing efficiency,
clean accumulated dirt and grease from the blower wheel and
motor annually.
Inducer Blower
NOTE: All motors are pre-lubricated. Do not attempt to lubricate
these motors.
Clean periodically to assure proper airflow and heating efficiency.
Inspect blower wheel every fall and periodically during the heating
season. For the first heating season, inspect blower wheel
bi-monthly to determine proper cleaning frequency.
Limit Switch
Remove unit access panel to gain access to the limit switch. The
limit switch is located above the indoor blower housing.
NOTE: On small chassis units, a second limit switch is located
beside the indoor blower housing.
Burner Ignition
[]nit is equipped with a direct spark ignition 100 percent lockout
system. Ignition module is located in the control box. Refer to
additional information in the Start-Up & Troubleshooting section
for Status Code information.
Main Burners
At the beginning of each heating season, inspect for deterioration
or blockage due to corrosion or other causes. Observe the main
burner flames and adjust, if necessary.
EQUIPMENT DAMAGE HAZARD
Failure to follow this caution may result in equipment
damage or improper operation.
When servicing gas train, do not hit or plug orifice spuds.
Removal of Gas Train
To remove the gas train for servicing:
1. Shut off main gas valve.
2. Shut off power to unit.
3. Remove unit access panel.
4. Disconnect gas piping at unit gas valve.
5. Remove wires connected to gas valve. Mark each wire.
6. Remove ignitor and sensor wires at the ignitor module.
7. Remove the mounting screw that attaches the burner rack to
the unit base.
8. Slide the burner rack out of the unit.
9. To reinstall, reverse the procedure outlined above.
Inducer Pressure Switch
Inspect pressure switch connections. Inspect pressure switch tube
for cracks or restrictions. Replace if needed.
28

ELECTRICALSHOCKHAZARD
Failureto follow this warning could result in personal
injury or death.
Disconnect and tag electrical power to the unit before
cleaning and lubricating the blower motor and wheel.
Outdoor Coil, Indoor Coil, and Condensate
Drain Pan
Inspect the condenser coil, evaporator coil, and condensate drain
pan at least once each year.
The coils are easily cleaned when dry; therefore, inspect and clean
the coils either before or after each cooling season. Remove all
obstructions, including weeds and shrubs, that interfere with the
airflow through the condenser coil. Straighten bent fins with a fin
comb. If coated with dirt or lint, clean the coils with a vacuum
cleaner, using the soft brush attachment. Be careful not to bend the
fins. If coated with oil or grease, clean the coils with a mild
detergent and water solution. Rinse coils with clear water, using a
garden hose. Be careful not to splash water on motors, insulation,
wiring, or air filter(s). For best results, spray condenser coil fins
from inside to outside the unit. On units with an outer and inner
condenser coil, be sure to clean between the coils. Be sure to flush
all dirt and debris from the unit base.
Inspect the drain pan and condensate drain line when inspecting
the coils. Clean the drain pan and condensate drain by removing all
foreign matter from the pan. Flush the pan and drain trough with
clear water. Do not splash water on the insulation, motor, wiring, or
air filter(s). If the drain trough is restricted, clear it with a
"plumbers snake" or similar probe device.
Outdoor Fan
UNIT OPERATION HAZARD
Failure to follow this caution may result in damage to unit
components.
Keep the outdoor fan free from all obstructions to ensure
proper cooling operation, Never place articles on top of the
unit,
1. Remove 4 screws holding outdoor grille and motor to top
cover.
2. Turn motor/grille assembly upside down on top cover to
expose fan blade.
3. Inspect the fan blades for cracks or bends.
4. If fan needs to be removed, loosen setscrew and slide fan off
motor shaft.
5. When replacing fan blade, position blade according to the
table shown in Fig. 24.
6. Ensure that set screw engages the flat area on the motor
shaft when tightening.
7. Replace grille.
infinity Top
A06035
UNIT SIZE "A" DIM. IN. (MM)
024 1 (26)
030 1 (26)
036 1 (26)
042 1 (26)
048 11/32 (9)
060 9/16 (14)
Fig. 24 - Outdoor Fan Blade Clearance
Electrical Controls and Wiring
Inspect and check the electrical controls and wiring annually. Be
sure to turn off the electrical power to the unit.
Remove access panel to locate all the electrical controls and wiring.
Check all electrical connections for tightness. Tighten all screw
connections. If any smoky or burned connections are noticed,
disassemble the connection, clean all the parts, re-strip the wire
end and reassemble the connection properly and securely.
After inspecting the electrical controls and wiring, replace all the
panels. Start the unit, and observe at least one complete cooling
cycle to ensure proper operation. If discrepancies are observed in
operating cycle, or if a suspected malfunction has occurred, check
each electrical component with the proper electrical
instrumentation. Refer to the unit wiring label when making these
checks.
Refrigerant Circuit
Inspect all refrigerant tubing connections and the unit base for oil
accumulation annually. Detecting oil generally indicates a
refrigerant leak.
If oil is detected or if low performance is suspected, leak test all
refrigerant tubing using an electronic leak detector, or liquid-so@
solution. If a refrigerant leak is detected, refer to Check for
Refrigerant Leaks section.
If no refrigerant leaks are found and low performance is suspected,
refer to Checking and Adjusting Refrigerant Charge section.
Indoor Airflow
The heating and/or cooling airflow does not require checking
unless improper performance is suspected. If a problem exists, be
sure that all supply- and return-air grilles are open and free from
obstructions, and that the air filter is clean.
Pressure Switches - Refrigerant Circuit
Pressure switches are protective devices integrated into the control
circuit (low voltage). They shut off compressor if abnormally high
or low pressures are present in the refrigeration circuit. These
pressure switches are specifically designed to operate with Puron
(R-410A) systems. R-22 pressure switches must not be used as
replacements for the Puron (R-410A) system.
Loss-of-Chame (Low Pressure) Switch
This switch is located on the liquid line and protects against low
suction pressures caused by such events as loss of charge, low
airflow across indoor coil, dirty filters, etc. It opens if the system
pressure drops to about 20 psig. If system pressure is above this,
switch should be closed.
Hi_h-Pressure Switches (HPS & HPS2)
The high-pressure switches are located on the discharge line and
protects against excessive condenser coil pressure. HPS opens at
29

670 psig shutting down the compressor, while HPS2 opens at 565,
limiting the compressor to low-stage operation only.
High pressure may be caused by a dirty outdoor coil, failed fan
motor, or outdoor air recirculation.
To check switches:
1. Turn off all power to unit.
2. Disconnect leads on switch.
3. Apply ohm meter leads across switch. You should have
continuity on a good switch.
NOTE: Because these switches are attached to refrigeration
system under pressure, it is not advisable to remove this device for
troubleshooting unless you are reasonably certain that a problem
exists. If switch must be removed, remove and recover all system
charge so that pressure gauges read 0 psi. Never open system
without breaking vacuum with dry nitrogen.
Copeland Scroll Compressor (Puron Refrigerant)
The compressor used in this product is specifically designed to
operate with Puron (R-410A) refrigerant and cannot be
interchanged.
The compressor is an electrical, as well as mechanical, device.
Exercise extreme caution when working near compressors. Power
should be shut off, if possible, for most troubleshooting techniques.
Refrigerants present additional safety hazards.
EXPLOSION, FIRE HAZARD
Failure to follow this warning could result in personal
injury or death and/or property damage.
Wear safety glasses and gloves when handling refrigerants.
Keep torches and other ignition sources away from
refrigerants and oils.
The scroll compressor pumps refrigerant throughout the system by
the interaction of a stationary and an orbiting scroll. The scroll
compressor has no dynamic suction or discharge valves, and it is
more tolerant of stresses caused by debris, liquid slugging, and
flooded starts. The compressor is equipped with an anti-rotational
device and an internal pressure-relief port. The anti-rotational
device prevents the scroll from turning backwards and replaces the
need for a cycle protector. The pressure-relief port is a safety
device, designed to protect against extreme high pressure. The
relief port has an operating range between 550 and 625 psi
differential pressure.
The Copeland scroll compressor uses Mobil 3MA POE oil.
This is the only oil allowed for oil recharge.
Refrigerant System
This step covers the refrigerant system of the 48XL, including the
compressor oil needed, servicing systems on roofs containing
synthetic materials, the filter drier, and refrigerant charging.
REFRIGERANT
UNIT OPERATION AND SAFETY HAZARD
Failure to follow this warning could result in personal
iniury or equipment damage.
This system uses Puron (R-410A) refrigerant which has
higher operating pressures than R-22 and other refrigerants.
No other refrigerant may be used in this system. Gauge set,
hoses, and recovery system nmst be designed to handle
Puron. If you are unsure, consult the equipment
manufacturer.
COMPRESSOR OIL
The compressor in this system uses a polyolester (POE) oil, Mobil
3MA POE. This oil is extremely hygroscopic, meaning it absorbs
water readily. POE oils can absorb 15 times as much water as other
oils designed for HCFC and CFC refrigerants. Take all necessary
precautions to avoid exposure of the oil to the atmosphere.
SERVICING SYSTEMS ON ROOFS WITH SYNTHETIC
MATERIALS
POE (polyolester) compressor lubricants are known to cause long
term damage to some synthetic roofing materials.
Exposure, even if immediately cleaned up, may cause
embrittlement (leading to cracking) to occur in one year or more.
When performing any service that may risk exposure of
compressor oil to the roof, take appropriate precautions to protect
roofing. Procedures which risk oil leakage include, but are not
limited to, compressor replacement, repairing refrigerant leaks, and
replacing refrigerant components such as filter drier, pressure
switch, metering device, coil, accunmlator, or reversing valve.
Synthetic Roof Precautionary Procedure
1. Cover extended roof working area with an in,permeable
polyethylene (plastic) drip cloth or tarp. Cover an
approximate 10 X 10 ft (3x3 m) area.
2. Cover area in front of the unit service panel with a terry
cloth shop towel to absorb lubricant spills and prevent
run-offs, and protect drop cloth from tears caused by tools
or components.
3. Place terry cloth shop towel inside unit immediately under
component(s) to be serviced and prevent lubricant run-offs
through the louvered openings in the unit base.
4. Perform required service.
5. Remove and dispose of any oil-contaminated material per
local codes.
LIQUID-LINE FILTER DRIER
The filter drier is specifically designed to operate with Puron. Use
only factory-authorized components. Filter drier must be replaced
whenever the refrigerant system is opened. When removing a filter
drier, use a tubing cutter to cut the drier from the system. Do not
unsweat a filter drier from the system. Heat from unsweating will
release moisture and contaminants from drier into system.
PURON (R-410A) REFRIGERANT CHARGING
Refer to unit information plate and charging chart. Some R-410A
refrigerant cylinders contain a dip tube to allow liquid
refrigerant to flow from cylinder in upright position. For
cylinders equipped with a dip tube, charge Puron units with
cylinder in upright position and a commercial metering device in
manifold hose. Charge refrigerant into suction line.
TROUBLESHOOTING
LED DESCRIPTION
LEDs built into Infinity control boards provide installer or service
person information concerning operation and/or fault condition of
the unit controls and ECM motor. This information is also
available at the system UI in text with basic troubleshooting
instructions. Careful use of information displayed will reduce the
need for extensive manual troubleshooting. See section B in
Start-Up & Troubleshooting and Table 5, as well as the UI
instructions, for additional information. Additional
Troubleshooting information can be found in Table 10.
MAJOR COMPONENTS
2-STAGE HP/AC BOARD
The two-stage HP/AC control board controls the following
functions:
- Low- and high-stage compressor operation
- Outdoor fan motor operation
- Reversing valve operation
3O

- Defrost operation
- Low ambient cooling
- Crankcase heater operation
- Compressor external protection
- Pressure switch monitoring (refrigerant)
- Time delays
FURNACE BOARD
The furnace board controls the following functions:
- Indoor blower operation
- Gas valve
- Inducer motor
- Remote sparker module
- Pressure switch monitoring (gas)
SYSTEMS COMMUNICATION FAILURE
If communication with the Infinity Control is lost with the UI, the
controls will flash the appropriate fault codes. Check the wiring to
the UI, indoor and outdoor units.
MODEL PLUG
The HP/AC control board must have a valid model plug to operate.
If a valid model plug is not detected, it will not operate and the
control will flash the appropriate fault code, shown in Table 5.
PRESSURE SWITCH PROTECTION-REFRIGERANT
The unit is equipped with high- and low-pressure switches. If the
control senses the opening of a high- or low-pressure switch, it
will respond as follows:
1. De-energize the compressor contactor (HPS1 & LPS) or the
compressor solenoid contactor (HPS2).
2. Keep the outdoor fan operating for 15 minutes.
3. Display the appropriate fault codes.
4. After a 15 minute delay, if there is still a call for cooling and
the LPS or HPS is reset, the compressor contactor is
energized.
5. If LPS or HPS has not closed after a 15 minute delay, the
outdoor fan is turned off. If the open switch closes anytime
after the 15-minute delay, then resume operation with a call
for cooling.
6. If LPS or HPS trips 3 consecutive cycles, the unit operation
is locked out for 4 hours.
7. In the event of a high-pressure switch trip or high pressure
lockout, check the refrigerant charge, outdoor fan operation
and outdoor coil for airflow restrictions.
8. In the event of a low-pressure switch trip or low pressure
lockout, check the refrigerant charge and indoor airflow.
CONTROL FAULT
If the HP/AC control board has failed, the control will flash the
appropriate fault code (See TaMe 5). The control board should be
replaced.
BROWN OUT PROTECTION
If the line voltage is less than 187v for at least 4 seconds, the
appropriate compressor contactor and fan relay are de-energized.
Compressor and fan operation are not allowed until voltage is a
minimum of 190v. The control will flash the appropriate fault
code (See Table 5).
230V LINE (POWER DISCONNECT) DETECTION
If there is no 230v at the compressor contactor when the unit is
powered and cooling demand exists, the appropriate error code is
displayed. Verify that the disconnect is closed and 230v wiring is
connected to the unit.
COMPRESSOR VOLTAGE SENSING
The control board input terminals VS and L2 (See Fig. 18) are
used to detect compressor voltage status, and alert the user of
potential problems. The control continuously monitors the high
voltage on the run capacitor of the compressor motor. Voltage
should be present any time the compressor contactor is energized,
and voltage should not be present when the contactor is
de-energized.
CONTACTOR SHORTED DETECTION
If there is compressor voltage sensed when there is no demand for
compressor operation, the contactor may be stuck closed or there is
a wiring error. The control will flash the appropriate fault code.
COMPRESSOR THERMAL CUTOUT
If the control senses the compressor voltage after start-up, and is
then absent for 10 consecutive seconds while cooling demand
exists, the thermal protector is open. The control de-energizes the
compressor contactor for 15 minutes, but continues to operate the
outdoor fan. The control Status LED will flash the appropriate
code shown in Table 5. After 15 minutes, with a call for low or
high stage cooling, the compressor contactor is energized. If the
thermal protector has not re-set, the outdoor fan is turned off. If
the call for cooling continues, the control will energize the
compressor contactor every 15 minutes. If the thermal protector
closes (at the next 15 minute interval), check the unit will resume
operation.
If the thermal cutout trips for three consecutive cycles, then unit
operation is locked out for 4 hours and the appropriate fault code is
displayed.
NO 230V AT COMPRESSOR
If the compressor voltage is not sensed when the compressor
should be starting, the contactor may be stuck open or there is a
wiring error. The control will flash the appropriate fault code.
Check the contactor and control box wiring.
TROUBLESHOOTING UNIT FOR PROPER SWITCHING
BETWEEN LOW & HIGH STAGES
Check the suction pressures at the service valves. Suction pressure
should be reduced by 3-10% when switching from low to high
capacity.
NOTE: The liquid pressures are very similar between low and
high stage operation, so liquid pressure should not be used for
troubleshooting.
Compressor current should increase 20-45% when switching from
low to high stage. The compressor solenoid, when energized in
high stage, should measure 24vac.
COMPRESSOR INTERNAL RELIEF
The compressor is protected by an internal pressure relief (IPR)
which relieves discharge gas into compressor shell when
differential between suction and discharge pressures exceeds 550 -
625 psi. The compressor is also protected by an internal overload
attached to motor windings.
TEMPERATURE THERMISTORS
Thermistors are electronic devices which sense temperature. As the
temperature increases, the resistance decreases. Thermistors are
used to sense outdoor ambient (OAT) and coil temperature (OCT).
Refer to Fig. 25 for resistance values versus temperature. See Fig.
26 for OCT location.
If the outdoor ambient or coil thermistor should fail, the HP/AC
control will flash the appropriate fault code (See Table 5).
IMPORTANT: Coil thermistor is factory mounted. Check to
insure thermistor is mounted properly. Outdoor air thermistor
(OAT) is field mounted and connected. Verify that the OAT has
been properly installed.
31

THERMISTOR CURVE
9O I I I I
80-k----4------4-----_------4-------I....
\ i i i i i
7o- -'_-- q------ I----- _------ T------I ....
6o-__X__J._ _ _ .I__ _ __ _ _ J__ _ _I....
\i i i i i
50.... '_------ 1----- _------ 1-------I ....
40- - /_.__ l______/___l ....
30.... _----_'-Z_----_------I-------I....
20.... _ ______/'_._/__ ____/ ____--I....
lo.... H--- t---_--_--
o ..................I...................I...................I...................I...................I,,-,_
I\ I I I I
I I _ I I
0 20 40 60 80 100 120
TEMPERATURE (DEG. F)
"tub
A91431
Fig. 25 - Resistance Values Versus Temperature
THERMISTOR SENSOR COMPARISON
The control continuously monitors and compares the outdoor air
temperature sensor and outdoor coil temperature sensor to ensure
proper operating conditions. The comparison is:
• In cooling mode, if the outdoor air sensor indicates -> 10 °F
(-12°C) warmer than the coil sensor (or) the outdoor air sensor
indicates -> 20 °F cooler than the coil sensor, the sensors are out of
range.
• In heating if the outdoor air sensor indicates _ 35 F (_ C)
warmer than the coil sensor (or) the outdoor air sensor indicates
->10°F (-12°C) cooler than the coil sensor, the sensors are out
of range.
If the sensors are out of range, the control will flash the appropriate
fault code as shown in Table 5.
The thermistor comparison is not performed during low ambient
cooling operation.
FAILED THERMISTOR DEFAULT OPERATION
Factory defaults have been provided in the event of failure of
outdoor air thermistor and/or coil thermistor.
If the OAT sensor should fail, low ambient cooling will not be
allowed and the one-minute outdoor fan off delay will not occur.
Defrost will be initiated based on coil temperature and time.
If the OCT sensor should fail, low ambient cooling will not be
allowed. Defrost will occur at each time interval during heating
operation, but will terminate after 5 minutes.
If there is a thermistor out of range error, defrost will occur at each
time interval during heating operation, but will terminate after 5
minutes.
Refer to the Troubleshooting Chart (Table 10) for additional
troubleshooting information.
> o ,_o
\ J
_ tight on the liquid
g
Fig. 26 - Outdoor Coil Thermistor (OCT) Attachment
o
F
A06311
FINAL CHECKS
IMPORTANT: Before leaving job, be sure to do the following:
1. Ensure that all wiring is routed away from tubing and sheet
metal edges to prevent rub-through or wire pinching.
2. Ensure that all wiring and tubing is secure in unit before
adding panels and covers. Securely fasten all panels and
covers.
3. Tighten service valve stem caps to l/2-turn past finger
tight.
4. Leave Users Manual with owner. Explain system operation
and periodic maintenance requirements outlined in manual.
5. Fill out Start-Up Checklist located at the back of this
manual and place in customer file.
CARE AND MAINTENANCE
For continuing high performance and to minimize possible
equipment failure, periodic maintenance must be performed on this
equipment.
Frequency of maintenance may vary depending upon geographic
areas, such as coastal applications. See Users Manual for
information.
32

AIR CONDITIONER WITH PURON
REFRIGERATION SECTION QUICK-REFERENCE GUIDE
Puron refrigerant operates at 50-70 percent higher pressures than R-22. Be sure that servicing equipment and replacement components are
designed to operate with Puron. Puron refrigerant cylinders are rose colored.
• Puron refrigerant cylinders manufactured prior to March 1, 1999, have a dip tube that allows liquid to flow out of cylinder in upright
position. Cylinders manufactured March 1, 1999 and later DO NOT have a dip tube and MUST be positioned upside down to allow liquid
to flow.
• Recovery cylinder service pressure rating must be 400 psig. DOT 4BA400 or DOT BW400.
• Puron systems should be charged with liquid refrigerant. Use a commercial-type metering device in the manifold hose.
• Manifold sets should be 750 psig high side and 200 psig low side with 520 psig low side retard.
• Use hoses with 750 psig service pressure rating.
• Leak detectors should be designed to detect HFC refrigerant.
• Puron, as with other HFCs, is only compatible with POE oils.
• Vacuum pumps will not remove moisture from oil.
• Only use factory-specified liquid-line filter driers with rated working pressures no less than 600 psig.
• Do not install a suction-line filter drier in liquid line.
• POE oils absorb moisture rapidly. Do not expose oil to atmosphere.
• POE oils may cause damage to certain plastics and roofing materials.
• Wrap all filter driers and service valves with wet cloth when brazing.
• A Puron liquid-line filter drier is required on every unit.
• Do not use an R-22 TXV.
• Never open system to atmosphere while it is under a vacuum.
• When system must be opened for service, break vacuum with dry nitrogen and replace filter driers.
• Do not vent Puron into the atmosphere.
• Observe all warnings, cautions, and bold text.
• Do not leave Puron suction line driers in place for more than 72 hrs.
33

Table9- Troubleshooting Chart
SYMPTOM
Compressor and outdoor fan
will not start
Compressor will not start but condenser fan
runs
Compressor cycles (other than normally sat-
isfying) cooling/heating calls
Compressor operates continuously
Excessive head pressure
Head pressure too low
Excessive suction pressure
Suction pressure too low
IFM does not run
IFM operation is intermittent
CAUSE
Power failure
Fuse blown or circuit breaker tripped
Defective contactor, transformer, control relay, or high-
pressure, loss-of-charge or low-pressure switch
Insufficient line voltage
Incorrect or faulty wiring
UI setting too low/too high
Units have a 5-minute time delay
Faulty wiring or circuit
Loose connections in compressor
Compressor motor burned out, seized, or
internal overload open
Defective run capacitor, overload, or PTC (positive
temperature coefficient) thermistor
Low input voltage (20 percent low)
Refrigerant overcharge or undercharge
Defective compressor
Insufficient line voltage
Blocked outdoor coil
Defective run/start capacitor, overload or start relay
Faulty outdoor fan motor or capacitor
Restriction in refrigerant system
Dirty air filter
Unit undersized for load
UI temperature set too low
Low refrigerant charge
Air in system
Outdoor coil dirty or restricted
Dirty air filter
Dirty indoor or outdoor coil
Refrigerant overcharged
Air in system
Indoor or outdoor air restricted or air short-cycling
Low refrigerant charge
Restriction in liquid tube
High heat load
Reversing valve hung up or leaking internally
Refrigerant overcharged
Dirty air filter
Low refrigerant charge
Metering device or low side restricted
Insufficient coil airflow
Temperature too low in conditioned area
Outdoor ambient below 55°F (13°C)
Filter drier restricted
Blower wheel not secured to shaft
Insufficient voltage at motor
Power connectors not properly sealed
Water dripping into motor
Connectors not firmly sealed
REMEDY
Call power company
Replace fuse or reset circuit breaker
Replace component
Determine cause and correct
Check wiring diagram and rewire correctly
Reset UI setting
DO NOT bypass this compressor time
delay-wait for 5 minutes until time-delay
relay is de-energized
Check wiring and repair or replace
Determine cause
Replace compressor
Determine cause and replace
Determine cause and correct
Recover refrigerant, evacuate system, and re-
charge to capacities shown on rating plate
Replace and determine cause
Determine cause and correct
Determine cause and correct
Determine cause and replace
Replace
Locate restriction and remove
Replace filter
Decrease load or increase unit size
Reset UI setting
Locate leak, repair, and recharge
Recover refrigerant, evacuate system, and re-
charge
Clean coil or remove restriction
Replace filter
Clean coil
Recover excess refrigerant
Recover refrigerant, evacuate system, and re-
charge
Determine cause and correct
Check for leaks, repair and recharge
Remove restriction
Check for source and eliminate
Replace valve
Recover excess refrigerant
Replace filter
Check for leaks, repair and recharge
Remove source of restriction
Check filter-replace if necessary
Reset UI setting
Verify low-ambient cooling enabled in UI
Replace
Properly tighten blower wheel to shaft
Determine cause and correct
Connectors should snap easily; do not force
Verify proper drip loops in connector wires
Gently pull wires individually to be sure they are
crimped into the housing
34

SYMPTOM
Burners will not ignite
Inadequate heating
Poor flame characteristics
Table lO--Troubleshooting Chart Con't-Gas Furnace Operation
CAUSE REMEDY
Water in gas line Drain. Install drip leg.
No power to unit
No 24-v power supply to control circuit
Mis-wired or loose connections
Misaligned spark electrodes
No gas at main burners
Inducer pressure switch not closing
Dirty air filter
Gas input to unit too low
Unit undersized for application
Restricted airflow
Limit switch cycles main burners
Incomplete combustion results in: Aldehyde odors,
carbon monoxide, sooting flame, floating flame
Check power supply fuses, wiring or circuit
breaker.
Check transformer.
NOTE: Some transformers have internal over-
current protection that requires a cool-down peri-
od to reset.
Check all wiring and wire nut connections
Check flame ignition and sense electrode posi-
tioning.
Adjust as necessary.
1. Check gas line for air. Purge as necessary.
NOTE: After purging gas line of air, wait at least 5
minutes for any gas to dissipate before attempt-
ing to light unit.
2. Check gas valve.
1. Check pressure switch wires, connections,
and tubing. Repair or replace if necessary.
Clean or replace filter as necessary
Check gas pressure at manifold match with that
on unit nameplate
Replace with proper unit or add additional unit
Clean or replace filter. Remove any restriction.
Check rotation of blower, temperature rise of unit.
Adjust as necessary.
1. Tighten all screws around burner compartment
2. Cracked heat exchanger. Replace.
3. Unit over-fired. Reduce input (change orifices
or adjust gas line or manifold pressure).
4. Check burner alignment.
5. Inspect heat exchanger for blockage. Clean
as necessary.
35

START=UP CHECKLIST
(Remove and Store in Job File)
I. Preliminary information
MODEL NO.:
SERIAL NO.:
DATE:
TECHNICIAN:
II. PRE-START-UP (insert checkmark in box as each item is completed)
VERIFY THAT ALL PACKING MATERIALS HAVE BEEN REMOVED FROM UNIT
REMOVE ALL SHIPPING HOLD DOWN BOLTS AND BRACKETS PER INSTALLATION INSTRUCTIONS
CHECK ALL ELECTRICAL CONNECTIONS AND TERMINALS FOR TIGHTNESS
CHECK GAS PiPiNG FOR LEAKS (WHERE APPLICABLE)
CHECK THAT INDOOR (EVAPORATOR) AIR FILTER IS CLEAN AND IN PLACE
VERIFY THAT UNIT INSTALLATION IS LEVEL
CHECK FAN WHEEL, AND PROPELLER FOR LOCATION IN HOUSING/ORIFICE AND SETSCREW TIGHTNESS
ill. START-UP
ELECTRICAL
SUPPLY VOLTAGE
COMPRESSOR AMPS
INDOOR (EVAPORATOR) FAN AMPS
TEMPERATURES
OUTDOOR (CONDENSER) AIR TEMPERATURE
RETURN-AIR TEMPERATURE DB
COOLING SUPPLY AIR DB
WB
GAS HEAT SUPPLY AiR
PRESSURES
GAS INLET PRESSURE
GAS MANIFOLD PRESSURE
REFRIGERANT SUCTION
REFRIGERANT DISCHARGE
IN.WG
IN.WG
PSIG SUCTION LINE TEMP*
PSIG DISCHARGE TEMPI,
( ) VERIFY REFRIGERANT CHARGE USING CHARGING CHARTS
GAS HEAT TEMPERATURE RISE
TEMPERATURE RISE (See Literature) RANGE
MEASURED TEMPERATURE RISE
( ) VERIFY THAT CONDENSATE CONNECTION IS INSTALLED PROPERLY
( ) VERIFY THAT OUTDOOR AIR THERMISTOR (OAT) iS PROPERLY INSTALLED & CONNECTED
*Measured at suction inlet to compressor
1-Measured at liquid line leaving condenser.
DB
WB
Copyright 2008 Carrier Corp. • 7310 W. Morris St. • Indianapolis, IN 46231 Printed in U.S.A. Edition Date: 08/08
Manufacturer reserves the right to change, at any time, specifications and designs without notice and without obligations,
3d
Catalog No:48XL-O4Sl
Replaces: 48XL-3SI