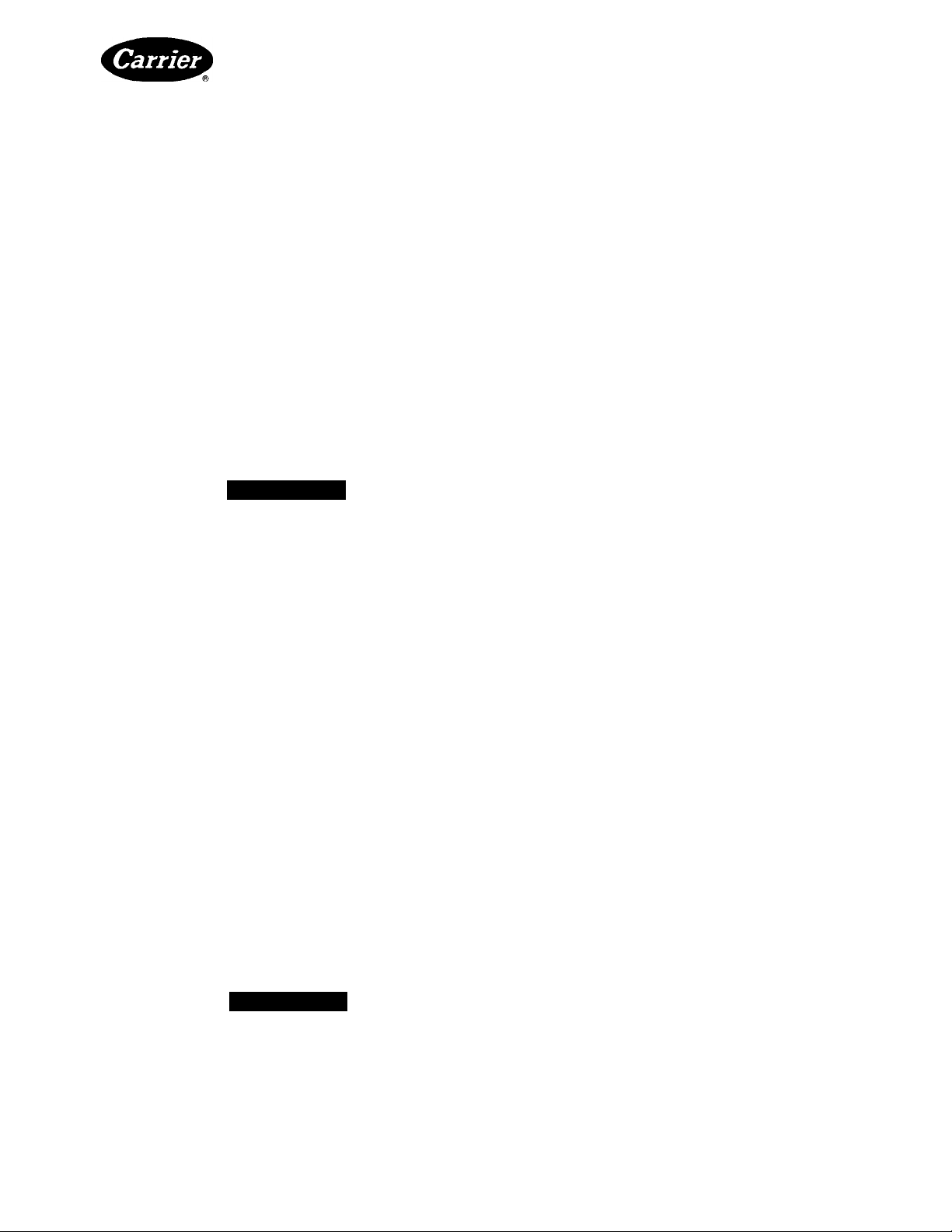
HEATING & COOLING
, ^pAH024-060
Ì-ÌOnzCintal Indoor Single-Package Cooling Units
Installation, Start-Up and Service Instructions
SAFETY CONSIDERATIONS
Installing and servicing air conditioning equipment
can be hazardous due to system pressure and electrical
components. Only trained and qualified service personnel
should install, repair or service air conditioning
equipment.
Untrained personnel can perform basic maintenance
functions such as cleaning coils and filters and replacing
filters. All other operations should be performed by
trained service personnel. When working on air condi
tioning equipment, observe precautions in the literature
and on tags and labels attached to unit.
Follow all safety codes. Wear safety glasses and work
gloves. Use quenching cloth for unbrazing operations.
Have fire extinguisher available.
A WARNING
Before performing service or maintenance opera
tions on unit, turn off main power switch to unit.
Electrical shock can cause personal injury.
INTRODUCTION
The 50AH024,036,048 and 060 units are single
package, indoor ceiling-mounted air conditioners of 2, 3,
4 and 5 tons capacity respectively.
These units can be mounted as factory-shipped single
package units or can be separated and mounted as a
split system. If unit is split, the condenser section can be
mounted horizontally.
All units are designed to be ducted on both the con
denser and evaporator sides. Centrifugal blowers are
used to insure quiet air delivery in the conditioned space.
Sound level requirements should be determined before
final unit installation site is chosen.
Unit servicing is relatively simple as access to the
condenser and evaporator motors, blowers, belt and
pulley is gained through removable swing doors located
on bottom of unit. These doors may also be used for
cleaning of condenser coils. Unit side panels provicfe
access to control box and pressure switches.
Refrigeration cycle components (e.g., compressor,
filter drier, etc.) can be serviced upon removal of the base
unit from the space.
INSTALLATION
A WARNING
Determine building alterations required to run
piping, wiring and ductwork. Follow dimensional
drawings carefully for ductwork, piping locations,
electrical wiring and overall unit dimensions. Read
booklet before starting installation.
Step 1 — Receive and Inspect Unit — Unpack
and check unit against shipping order. Inspect carefully
for concealed shipping damage. If unit is damaged or
incomplete, file claim with transportation company and
advise Carrier immediately.
Step 2 — Protect Unit from Damage — To main
tain warranty, unit must be protected against theft and
vandalism and stored indoors at all times.
Step 3 — Provide Unit Support — Refer to Fig. 1
and 2 for unit dimensions and component locations.
Refer to Table 1 — Physical Data for unit sizes and
weights.
Each unit requires the following:
• 4 threaded suspension rods (3/8-in. - 16 SAE Grade 1
minimum)
• washers and locknuts
Install the 4 field-supplied rods by suspending from a
suitable ceiling support. Locate rods to mate with 4
outside corner rigging holes shown in Fig. 1.
The ceiling and ceiling supports of existing buildings
may require reinforcements; follow all applicable codes.
Step 4 — Rig and Place Unit — Move and store
unit in horizontal position. Provide space around unit for
service, filter access, ductwork and overhead clearance
as indicated in Fig. 1.
Using suitable hydraulic lift source, raise unit up to
meet bottom of the 4 threaded rods suspended from
ceiling. Center unit so that the 4 threaded rods can be
easily inserted into the factory-drilled holes at each end.
Refer to Fig. 3 for rigging details.
Apply washers and locknuts on ends of each of the
4 rods.
Tighten locknuts sufficiently so that unit weight is
supported entirely by the 4 rods. Level unit within the
space by adjusting locknuts.
IMPORTANT: Unit must be level to operate
properly.
NOTE: The 2 factory-drilled holes in the middle of unit
can be used for support if a split system application is
desired. If required, an accessory vibration isolator pack
age is available for use to dampen vibration that may be
transmitted to building structure.
Step 5 — Make Piping Connections — Two
3/4-m. pipe thread condensate drain connections are pro
vided below the evaporator coil. One 3/4-in. pipe thread
connection is provided for condenser coil washdown.
One of the evaporator drains is plugged at factory and
plug must be removed when making field connections.
The condenser washdown pan is plugged at factory. This
drain is to be used only when condenser coil is being
cleaned and plug must be replaced when cleaning is
completed.
Manufacturer reserves the right to discontinue, or change at any time, specifications or designs without notice and without incurring obligations.
Book|1 |4 PC111 Catalog No 565-040 PrintedinUSA Form60AH-2SI . Pg1 6-87 Replaces: 50AH-1SI
Tab l2a|7b
For replacement items use Carrier Specified Parts
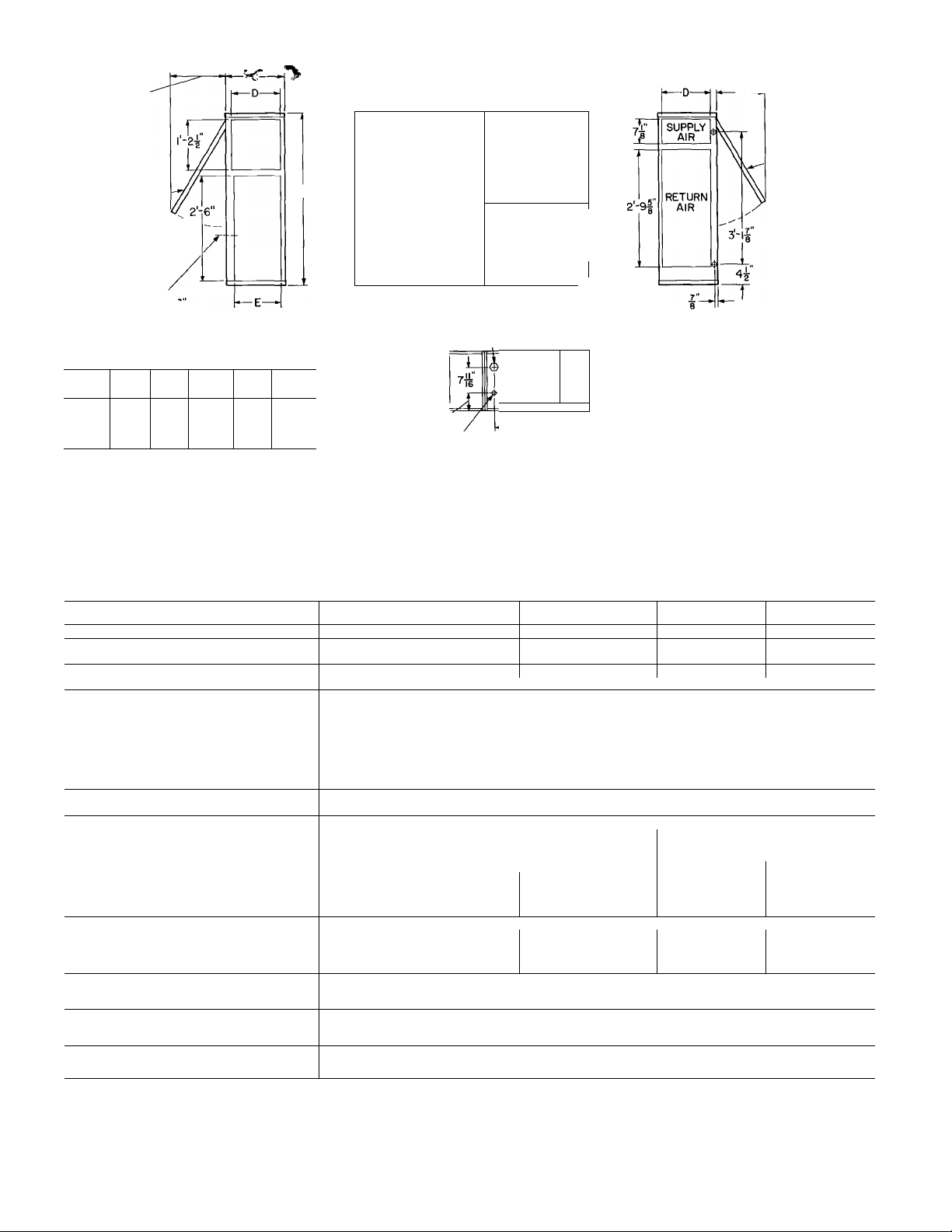
r-5 MIN FOR
REMOVAL OF
PANEL
BOTTOM ACCESS'
PANEL (COND FAN
MOTOR a
BLOWER, COND
COIL WASHDOWN)
CONDENSER COIL
WASHDOWN DRAIN 5
DIMENSIONS (ft-in.)
UNIT
50AH
024
2-5
2-4%
036
048 2-5
2-4%
060
A
2-1% 1- 4%
2-2% 1-11%
FPT
C D E
B
2-2 1- 4% 1-2 1-1
1-11% 1-8% 1-7%
2-3
1-2 1-1
1-8% 1-7%
CORNER D
4'-o"
o
CORNER C
0'-4"-
TgDIA (TYP 8 PLACES)
RIGGING HOLES
I I
I I
I I
I I
1
> \
1
_ _ _
1
°
-2-4"-
COND SECT.
ACCESS PANEL
I "DIA HOLE FIELD
CONTROL WIRING
Fig. 1 — Dimensions
CONTROL BOX
FIELD POWER SUPPLY
JUNCTION BOX
0'-5"
r - i -
1
i r -
i i i
1 1 1
" " i
_ _ _ _
j i
/-~>COMPR !
{ '
1- —,
1
2- 1
o r~j--1
CONTROLS
coMPR a
ACCESS
PANEL
--
CORNERA
^EVAP
r 'COIL
■CORNER B
—0'-4"
EVAP COIL
ACCESS PANEL
FILTER
CONDENSATE DRAINS (2)
0'-3"MIN FOR P-TRAP
r-5" MIN FOR REMOVAL
\
___
, OF PANEL
BOTTOM ACCESS
PANEL(EVAR
■FAN MOTOR a
BLOWER, EVAR
COIL a
CONDENSATE
PAN)
FPT
- Center of Gravity
- Direction of Airflow
Table 1 — Physical Data
UNIT 50AH
SHIPPING WEIGHT (lbs) (Note 1) 600
OPERATING WEIGHT (lbs)
Base Unit
OPERATING CHARGE (lbs) (Note 2) 56
Refrigerant
COMPRESSOR — TYPE Hermetic
Quantlty...Model
Oil (oz)
HPS Setting (psig)
Cutout
Reset
LPS Setting (psig)
Cutout
Reset
CONDENSATE CONNECTION
Condensate Drain %...FPT
CONDENSER FAN
Nominal Cfm
Maximum Rpm
Blower Size On.)
Pulley Pitch Diameter (in.)
Blower None
Motor (Variable)
Motor Hp
Motor Rpm
EVAPORATOR FAN Centrifugal — Direct-Drive
Nominal Cfm
Maximum Rpm
Blower Size (in.)
Motor Hp
CONDENSER COIL Copper Tubes — Aluminum Fins
Size (L X H) (in.)
Number of Rows...Fins/in.
EVAPORATOR COIL
Size (L X H) (in.)
Number of Rows...Fins/in.
INDOOR AIR FILTERS
Number...Size (in.)
Centrifugal — Direct-Drive Centrifugal — Belt Drive
024 036 048
480 500 580
(1) AB5524H (1). AV5535H* (1).. P46
32 32 76
1350
1100
12 X 6
None 2 4-3 4
%
825 1725
800
1100
10 X 5 10 X 6
Vs
40 X 15 40 X 22
Copper Tubes — Aluminum Fins
34 X 15
Factory-Supplied Cleanable Type
620 700
5.5 80
R-22
426 ± 7
320 ± 20
27 ± 4
67 ± 7
Size (in.)...Type
60 60
% 1 0
1200
1150
Vi
4...13.6
4...14.4
(1) .1
060
710
590
76
(1)...P60
76
2250 2450
1 9-2 9 2 4-3 4
1725 1725
1600 2000
1050
10 X 8 10 X 8
1500
12 X 9
60
1 5
1050
%
34 X 22
%
CFM — Cubic Feet per Minute
FPT — Female Pipe Thread
PSIG — Pounds per Square Inch Gage
RPM — Revolutions per Minute
'Three-phase units use (1) AV5535E compressor
NOTES:
1 Shipping weights include base unit plus packaging
2. If components are to be split, additional refrigerant will be needed Refer to charging
charts found on page 5 and 6
3 If components are to be split, the maximum length of refrigerant tubing to be used is
75 ft, assuming components will be installed in same horizontal plane If components
are not to be installed in same horizonal plane, contact Carrier, Syracuse for more
information For additional piping information, refer to Carrier System Design Manual,
Part 3