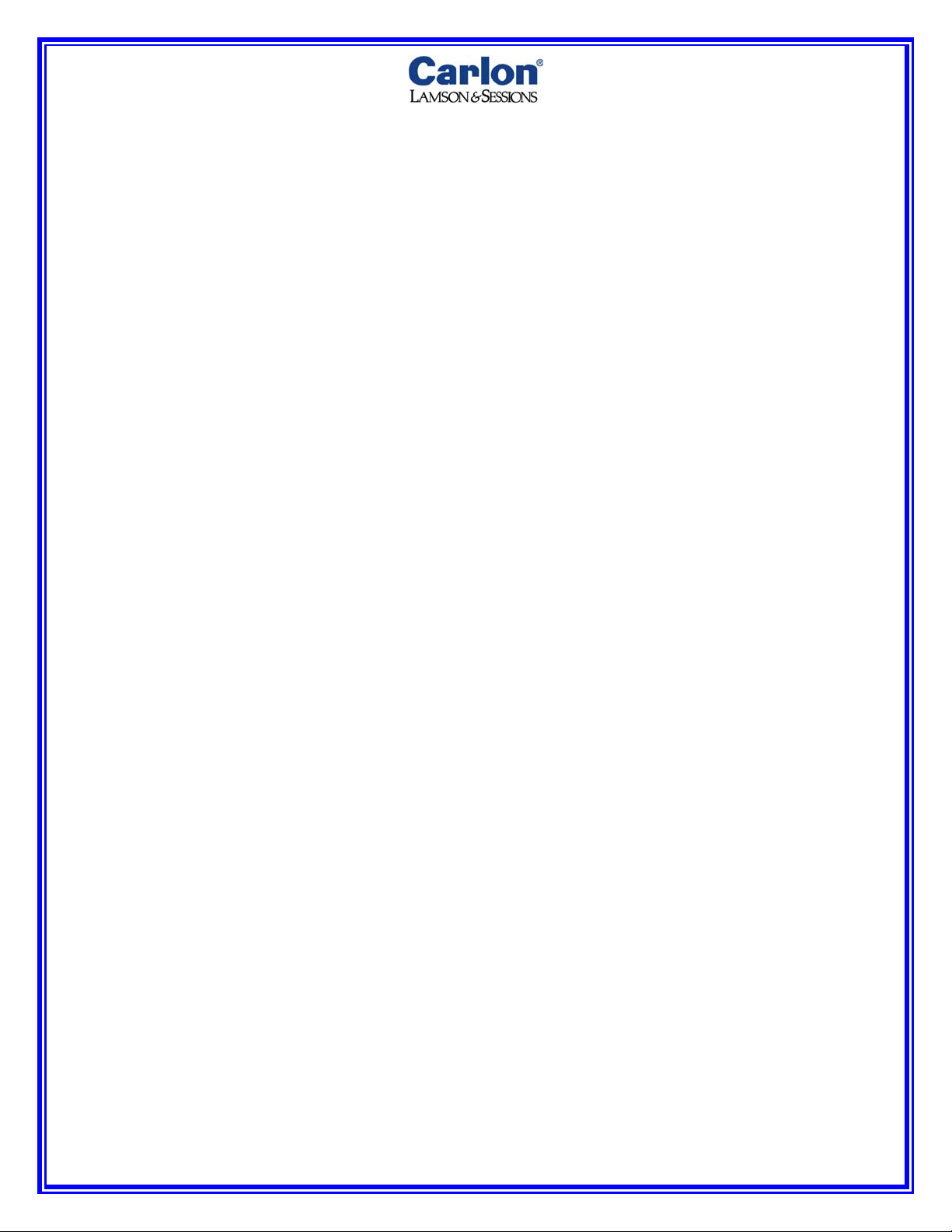
DUCT PROOFING AND CABLE INSTALLATION
Gross Automation (877) 268-3700 · www.carlonsales.com · sales@grossautomation.com
Duct Proofing for Cable Pulling
Use 175 or 250 CFM Compressor for maximum line blowing potential. Choose
pull line based on length of pull and tension expected.
1. Remove all plugs in terminator at exit end and only the plug being shot
into on the entrance end.
2. Turn threaded nozzle into terminator until tight, without pull line or missiles
to blow any debris or water which might have collected.
3. Open gate on nozzle to apply air to innerduct. Close gate after any debris
or water has been blown out.
4. Unscrew nozzle and thread pull line through eyelet in nozzle and tie to line
blowing missile. Place pull line reel on stand for feeding.
5. Place line blowing missile into open innerduct and carefully open gate on
nozzle.
6. Feed pull line off reel and keep slight tension to avoid rope packing in
innerduct.
7. When using flat tape as pull line, use twisted blow line (RP142) to blow in
and retrieve flat tape.
Proofing for Jetting Cable
Use 375 CFM compressor for best results
1. Attach polyethylene feed tube (1'' SDR 13.5 for 4 way and 1 3/4'' SDR
13.5 for 3 way) with coupling recommended for high speed air blowing
systems to empty innerduct extension on jet through terminator.
2. Assemble coupling according to high speed blowing system
manufacturers recommended instructions.
3. Attach opposite end of polyethylene feed to high speed air speed
machine.
4. Plug all unused holes in the Multi-Gard terminator at entry point and
remove all plugs at exit terminator. Apply 100 -110 PSI to the Multi-Gard
innerduct. Close the air output valve and stop compressor. The innerduct
is acceptable if a loss of 20 PSI or less happens within 2 minutes of
pressurization. WARNING: NO PERSONNEL IN MANHOLES DURING
PRESSURE TEST.
www.carlonsales.com
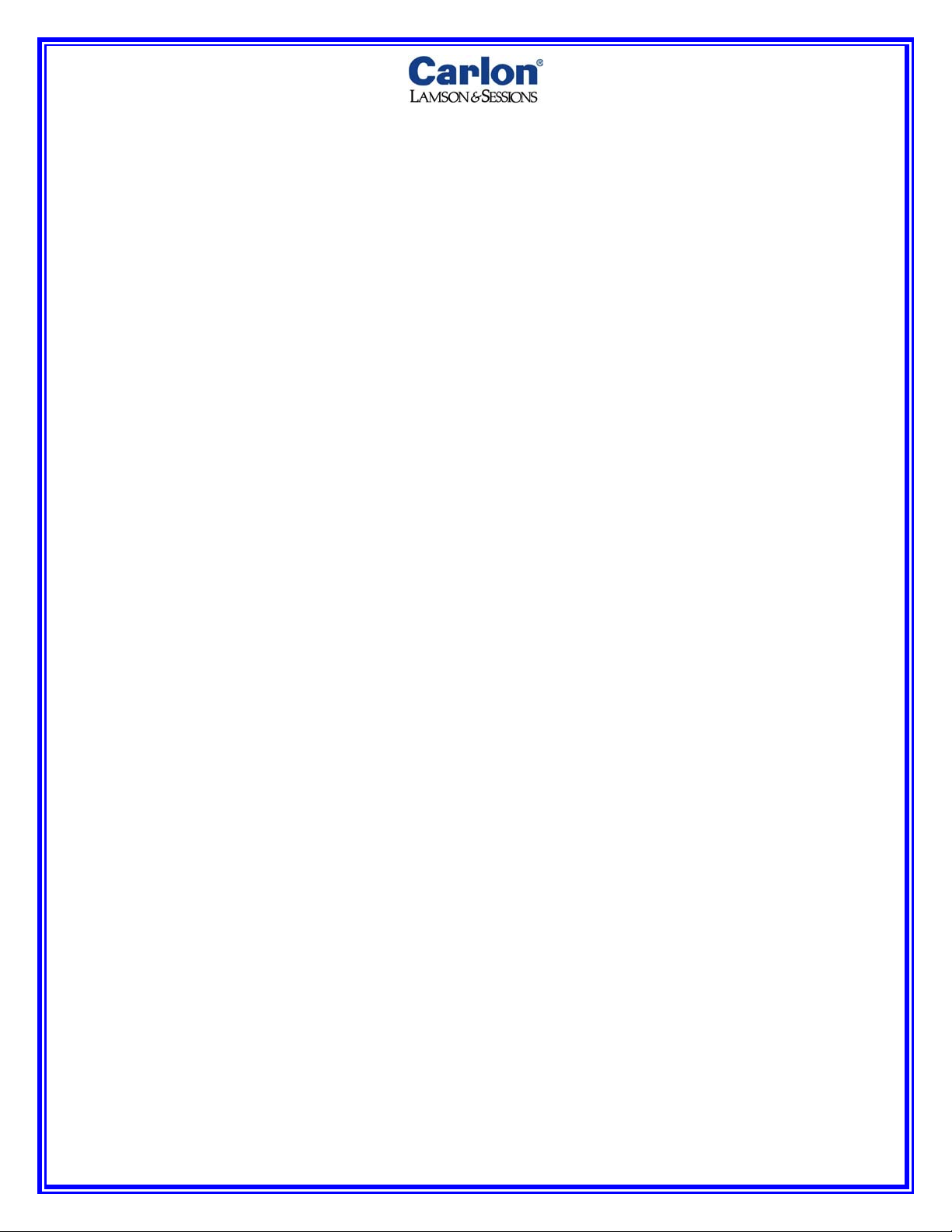
DUCT PROOFING AND CABLE INSTALLATION
Gross Automation (877) 268-3700 · www.carlonsales.com · sales@grossautomation.com
Cable Installation Using Pulling Equipment
The low co efficient of friction of pre lubricated PVC will allow pulls in excess of
4000' for Multi-Gard unless abrupt changes are in the route. Pull speeds of 100
200 ft. per minute are acceptable.
Cable pulling operations:
1. Multi-Gard innerducts are pre lubricated. Additional Polywater lubricant
may be used for longer pulls.
2. Align the pull blocks or sheaves so the pull line passes directly and freely
from the innerduct entrance. Cable should be fed from the top of the reel.
3. Choose swivel with load rating at or below maximum pull limit. Attach
swivel between pull line and cable pulling eye or basket grlp.
4. Maintain constant pulling tension to avoid stop/start. A monitoring device
should be used to avoid over tensioning the cable. Most outside plant
cables are rated for 600 Ibs. Check with cable manufacturer for specific
pulling tension.
5. Leave slack in each handhole where racking will be needed.
Innerduct Racking Using Pulling Equipment
The racking operation should be done after the cable has been pulled through
the Multi-Gard.
1. Place PVC corrugated split innerduct over slack cable.
2. Secure cable in innerduct against handhole/manhole wall out of way.
Cable Installation Using Jetting Equipment
Multi-Gard with the new Air Gard™ gasket and pre lubed PVC innerduct is ideal
for jetting cable.
Jetting cable operations:
1. Set up jetting equipment for easy accessibility to PE innerduct secured to
Multi-Gard.
2. Blow foam carriers through innerduct until clean and dry.
3. Multi-Gard is now ready for jetting according to high speed air blowing
system manufacturer's instructions.
4. Leave slack in each handhole where racking will be needed.
www.carlonsales.com