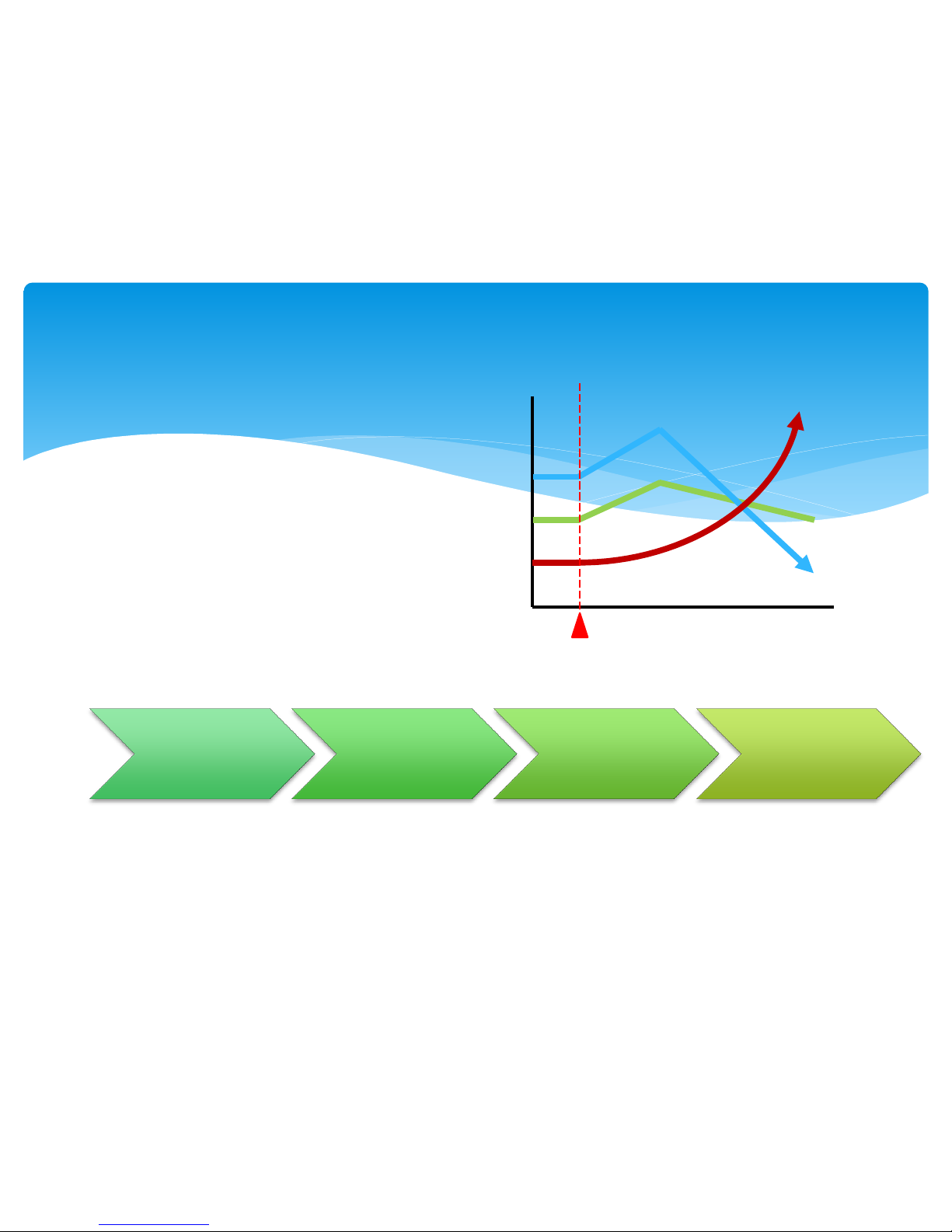
Pre-Visit
Serviced
History Check
Common
Process
(Before)
Maintenance
Process
Common
Process
(After)
Purpose
Increase the following items.
FCFR (First Call Fix Rate)
Uptime
MCBC (Mean Copies Between Calls)
Customer Satisfaction
How to use
This document was developed by Canon USA Engineering Services and Solutions to
perform consistent, effective and efficient maintenance on all Canon products.
FCFR, MCBV,
Uptime
Parts Cost
Visits, Labor
Implementation of the Preventative Maintenance Procedure
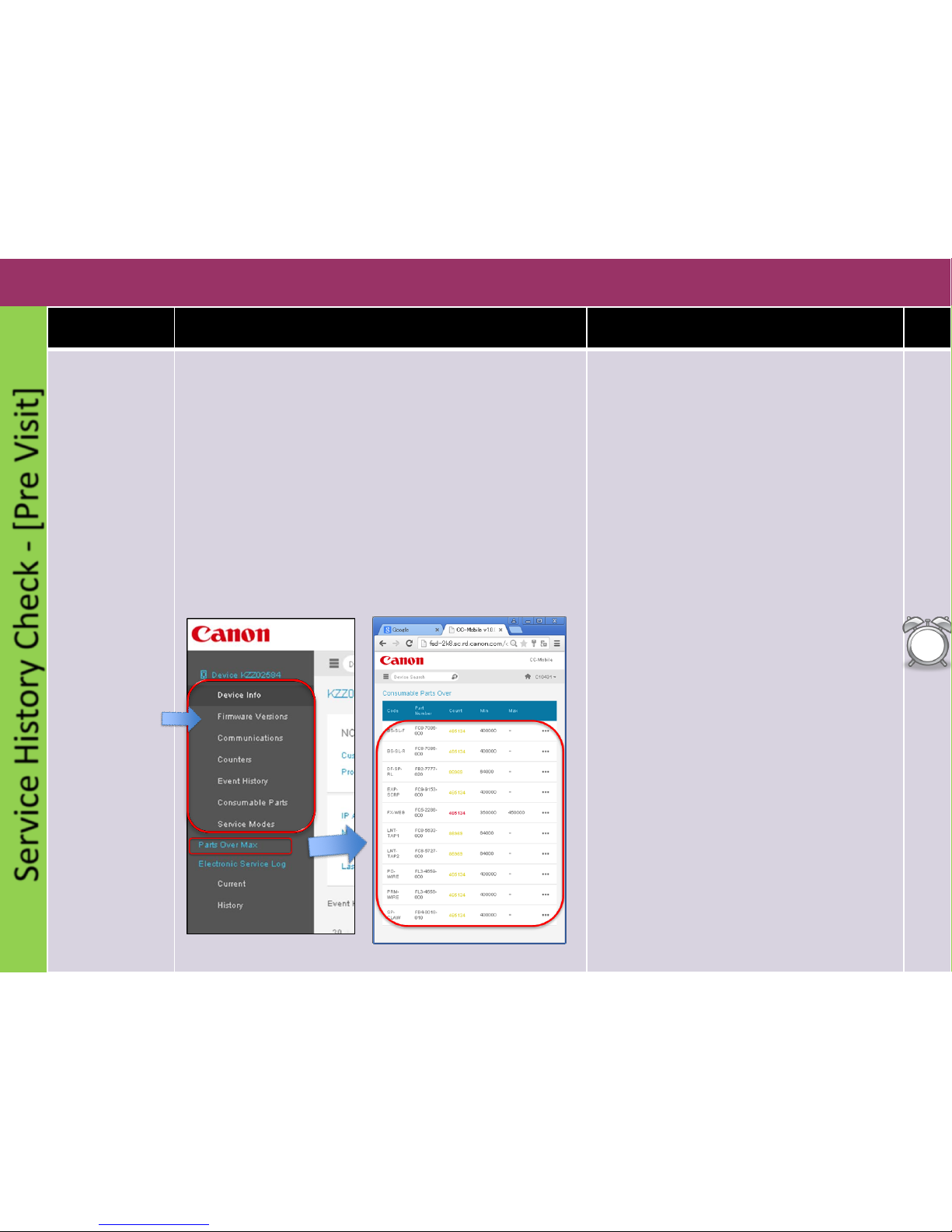
Service History Check - [Pre Visit]
Procedure Detail Note Time
Action Prior to
Customer Visit:
Whenever
possible,
Check Snapshot
for :
6
min
Check
1. Log into Snapshot :
• Enter the machine Serial Number to check the
following:
1. Firmware Version – Prepare Firmware if necessary
2. Communications
3. Counters – Machine Usage
4. Event History – Check History for Errors, Alarms
and Jams
5. Consumable Part Counters -
Prepare Consumable and Durable
Parts
• Firmware Version
• Event History
• Part Counters
• Service Mode Settings
iR ADV C255iF/ C355iF Advanced Maintenance Guide
1. Understand the machine's current condition
(jams and error, needed consumable parts) before
visiting EM call or PM-Call.
2. Prepare all consumable parts that exceeded
Target and replace them on a PM-call, replace any
parts that exceeded life you have now at the EM
call.
3. Take the necessary actions for the jamming and
errors.
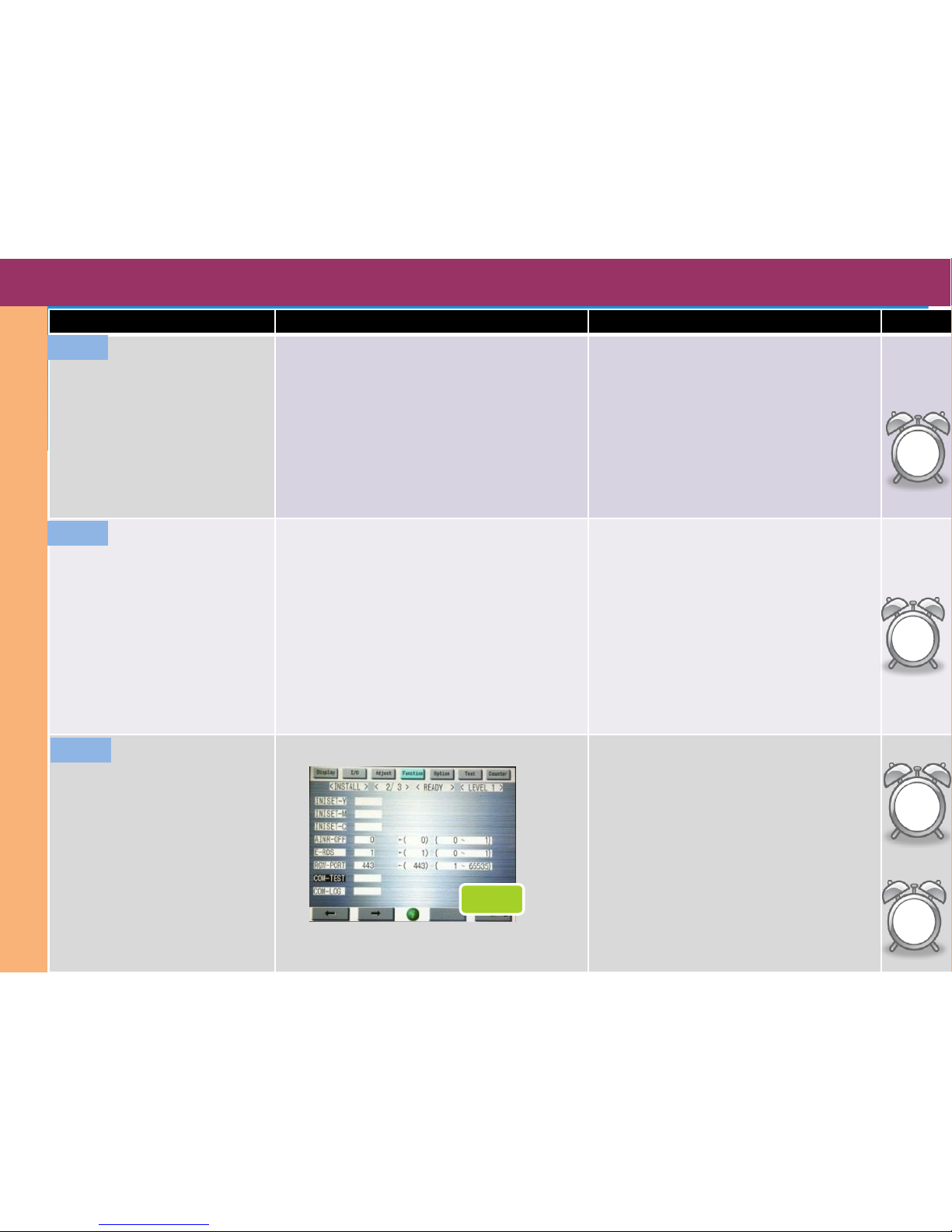
Procedure Detail Note Time
Verify Customers’
Concern
Ask the customer about the condition of the machine
and validate any issues they have.
Ask Questions to find out if there are any following
issues on the machine?
1.Copy Quality
2.Jamming
3.ERROR
4.Other issues (Copier Only)
5.No Problem
Point:
- To perform efficient maintenance, we need to
ask the customer about the machine condition.
Check the Serial
Number
Ensure the serial number on the machine matches the
serial number that you are dispatched to.
Point:
- If the serial number is incorrect and there is
more than one machine at the account that is
down please notify dispatch.
Perform COM-TEST
COPIER > Function > INSTALL>COM-TEST If COM-TEST is NG, fix this issue at first. If you can’t
fix this issue please insure the issue is resolved
prior to leaving the account.
Common Process (Before)
C1
1
min
Check
1
min
Scan
1
min
Check
1
min
COM TEST
C2
C3
iR ADV C255iF/ C355iF Advanced Maintenance Guide
COM TEST
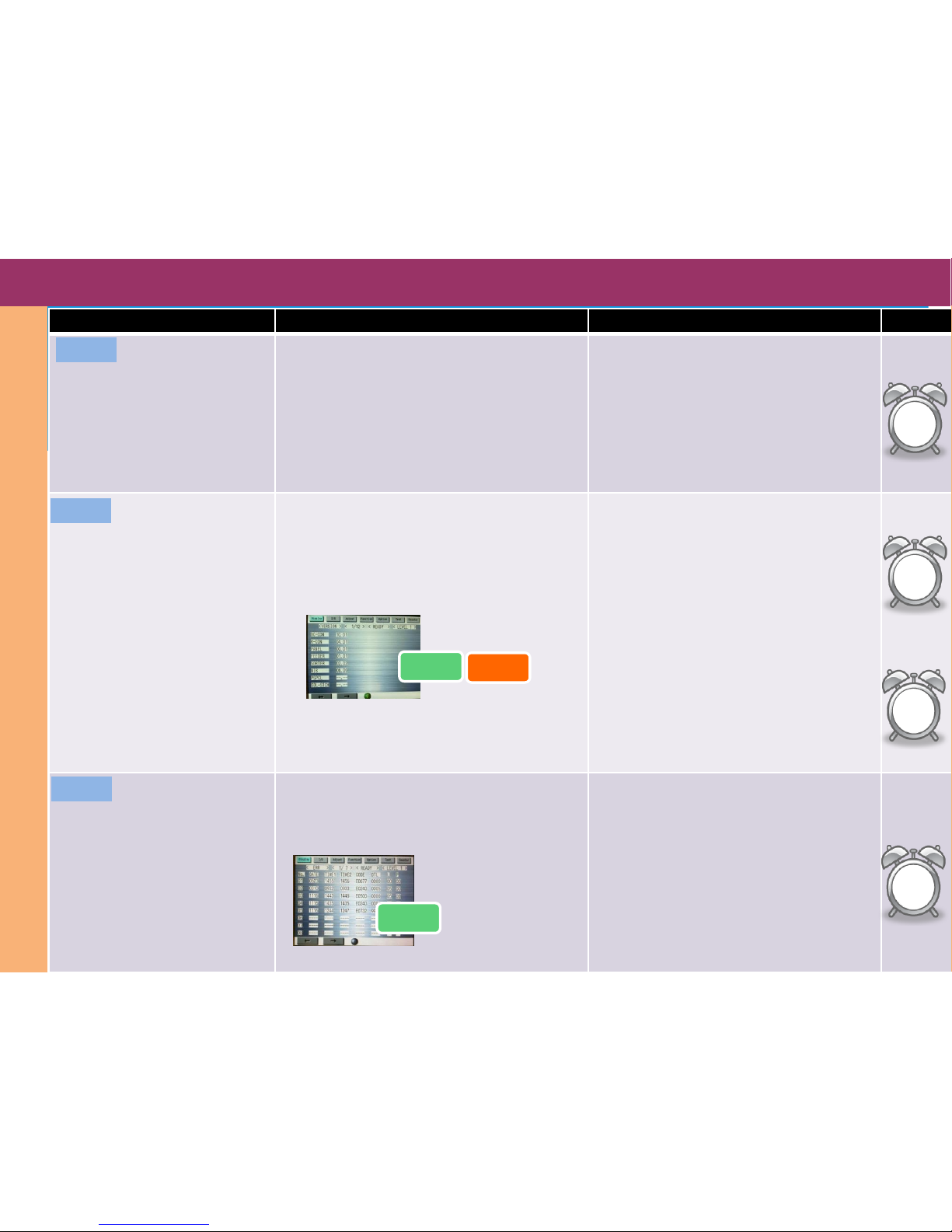
Procedure Detail Note Time
Check Service Log
1. Check Service Log Point:
1. Check the log to see if there is any reoccurring
issues. If you see the same issues listed on the
log, then the root cause hasn’t been fixed.
2. Check what parts were replaced recently.
These parts should not be replaced again for
the same issue.
3. If the problem seems to be related to the
previous call, check what the previous tech did.
1. Check System Software Version
Check for latest version on e-support and
recommend to update the system software to latest
version
Point:
The latest firm contains following major
countermeasure.
Check Service history
1. Check ERR/JAM history Address all Error and Jams.
Check
COPIER>DISPLAY>ERR
COPIER>DISPLAY>JAM
1
min
Visual Check
1
min
1
min
Check
COM TEST
1
min
Visual Check
If Snapshot tool was used
successfully, skip steps C5
through C8
Check System
Software Version
Check
Update
COPIER>DISPLAY>VERSION
1. As of 4/26/17 MN-CON is 19.06.01 (TP17-079)
If Snapshot tool was used
successfully, skip steps C5
through C8
Common Process (Before)
C4
C5
C6
iR ADV C255iF/ C355iF Advanced Maintenance Guide