
About this manual
Some useful conversion factors:
Area: 1 in
Length: 1 in. (inch) = 25.4 mm
2
(square inch) = 645 mm2
1 ft (foot) = 304.8 mm
1 yard = 0.914 m
1 mile = 1.609 km
Mass:
Pressure: 1 psi (lb/in
Volume: 1 UK pint = 568.3 ml
1 oz. (ounce) = 28.35 g
1 lb (pound weight) = 0.454 kg
2
) = 68.95 mb
1 UK gallon = 4.546 litres
1 US gallon = 3.785 litres
Recycling information
At the end of this product’s life it should not be put in commercial or domestic refuse
but sent for recycling. Any batteries contained within the product or used during the
products life should be removed from the product and also be sent to an appropriate
recycling facility.
Campbell Scientific Ltd can advise on the recycling of the equipment and in some cases
arrange collection and the correct disposal of it, although charges may apply for some
items or territories.
For further advice or support, please contact Campbell Scientific Ltd, or your local agent.
Campbell Scientific Ltd, Campbell Park, 80 Hathern Road, Shepshed, Loughborough, LE12 9GX, UK
Tel: +44 (0) 1509 601141 Fax: +44 (0) 1509 270924
Email: support@campbellsci.co.uk
www.campbellsci.co.uk

Contents
PDF viewers note: These page numbers refer to the printed version of this document. Use
the Adobe Acrobat® bookmarks tab for links to specific sections.
1. Introduction ................................................................. 1
1.1 General Safety........................................................................................... 2
1.2 Sensor Unit Safety .................................................................................... 2
1.3 Principle of operation ................................................................................ 3
1.4 Recommended Tools ................................................................................ 6
1.5 Quickstart .................................................................................................. 6
2. Measurement specification ........................................ 6
3. Technical specification ................................ .............. 7
3.1 Electrical specification .............................................................................. 7
3.2 Optical specification ................................................................................. 7
4. Communications specification .................................. 8
4.1 Communications electrical specifications ................................................. 8
4.2 Supported data rates and formats .............................................................. 8
5. Environmental specifications .................................... 9
6. Mechanical specifications .......................................... 9
6.1 Dimensions ............................................................................................... 9
6.2 Weights ................................................................................................... 10
6.3 Mounting................................................................................................. 10
7. Installation procedure .............................................. 10
7.1 Equipment grounding ............................................................................. 11
7.2 Mounting the sensor ................................ ................................ ................ 12
7.3 Optional Campbell Scientific Mount ...................................................... 14
8. Sensor internal connectors’ description ................ 17
8.1 Sensor recommended wiring using Campbell Scientific cables ............. 19
9. HygroVUE 5, HygroVUE 10 or CS215 T/RH Sensor
(CS125 only) ................................................................... 21
10. Functions of the internal switches ........................ 23

ii
11. Message Formats: A breakdown of the different
default outputs of the sensor –
Basic/Partial/Full ............................................... 24
11.1 Visibility only messages ....................................................................... 25
11.2 Messages with SYNOP Present Weather Codes (CS125 only) .............. 26
11.3 Messages with METAR Present Weather Codes (CS125 only) ............. 27
11.4 Messages with Generic SYNOP Present Weather Codes (CS125 only) 28
11.5 Example sensor message outputs .......................................................... 33
11.6 Custom message format ........................................................................ 34
12. Interface methods – Device Configuration
Utility/Command line/Menu .................................. 36
12.1 Configuring a PC for talking to the sensor ........................................... 37
13. Definition of the variables that can be set by
the user on the sensor ........................................ 37
14. Command line mode............................................... 39
14.1 The SET Command .............................................................................. 40
14.1.1 Example of a SET Command ................................................... 40
14.2 The SETNC Command ......................................................................... 41
14.2.1 Example of a SETNC Command .............................................. 41
14.3 The MSGSET Command ...................................................................... 41
14.4 The GET Command .............................................................................. 43
14.5 The MSGGET Command ..................................................................... 45
14.6 The POLL Command – Polling the sensor ........................................... 46
14.7 The ACCRES Command – Resetting the accumulation value ............. 47
15. Entering the sensor menu system ........................ 47
16. Calibrating the sensor ............................................ 53
16.1 Visibility calibration ............................................................................. 53
16.2 Dirty window zero calibration .............................................................. 57
16.3 Internal temperature check (CS125) ..................................................... 57
17. Performing an operating system update .............. 58
18. Cleaning .................................................................. 60
19. Lubricating the enclosure screws ......................... 61
20. Desiccant ................................................................. 61
Addendum .................................................................Add-1

iii
Appendices
A. Sensor Block Diagram ........................................... A-1
B. Example C code of the checksum CRC-16 ........... B-1
C. Present Weather Codes ........................................ C-1
D. A comparison of the two alternative visibility
calibrations ........................................................... D-1
Figures
1-1 Particles in the sample volume scatter light in all directions, including
into the detector ....................................................................................... 3
1-2 Signals from large, slow falling snowflakes and smaller, faster,
raindrops .................................................................................................. 4
1-3 Defining possible precipitation types based on wet bulb and dry
bulb temperatures ..................................................................................... 5
1-4 A typical size/speed map used by the CS125 present weather
algorithm ................................................................................................... 5
7-1 Airflow ................................................................................................... 11
7-2 Grounding boss ....................................................................................... 12
7-3 Mounting arrangement ........................................................................... 13
7-4 Mounting to a flat surface ....................................................................... 13
7-5 Use of band clamps ................................................................................ 14
7-6 Optical sensor mast ................................................................ ................. 15
7-7 Mounting footprint ................................................................................. 16
8-1 Connections ............................................................................................ 17
8-2 Communications and power connections ............................................... 19
8-3 Communications and power connector .................................................. 20
8-4 Configuration cable ................................................................................ 20
8-5 USB configuration cable ........................................................................ 20
9-1 Connection for the optional HygroVUE 5, HygroVUE 10 &
CS215 T/RH sensors .......................................................................... 22
10-1 Internal switches ................................................................................... 23
16-1 Calibration disk .................................................................................... 55
16-2 Mounting calibration disk ..................................................................... 56
17-1 Sensor DevConfig download instructions ............................................ 58
17-2 Sensor DevConfig screen when OS update is complete ....................... 59
Tables
10-1 Internal switch functions ..................................................................... 24
11-1 Summary of message IDs and descriptions ......................................... 30
11-2 Summary of system alarms and descriptions ....................................... 31
13-1 User definable settings and descriptions .............................................. 37

CS120A and CS125 Visibility and Present Weather Sensors
4
This non-linear equation results in significantly higher visibility readings at lower
visibilities below 5000 metres. Further details of the calibration and graphs
comparing the two calibration options are given in Appendix D.
The TMOR calibration should be used for aviation applications as it is considered
to give more representative visibility values for a plane landing and viewing
landing lights. Use of the TMOR calibration is obligatory for use of this sensor on
German airfields.
The CS125 can be switched between outputting data using the original MOR or
the alternative TMOR calibration by using a configuration switch (See Section
10). Sensors made from early December 2020 leave the factory with this switch
set to ON to make the sensor output values according to the TMOR calibration.
The CS125 is capable of identifying weather type in addition to measuring
visibility. It does this by analysing the amplitude and width of spikes in the APD
signal corresponding to particles of precipitation passing through the sample
volume. The amplitude of the signal is a guide to the size of the particle and the
width, because it represents the time taken for the particle to fall through the
sample volume, is proportional to the fall speed, see Figure 1-2.
Figure 1-2. Signals from large, slow falling snowflakes and smaller, faster,
raindrops
The CS125 also has a temperature sensor. These three parameters, fall speed, size
and temperature are used to identify the type of particle. If an additional external
temperature and relative humidity probe is connected then a wet-bulb temperature
can be calculated. This provides useful additional information identifying particles
more accurately especially, between liquid and frozen around 0°C.
Figure 1-3 shows how these temperatures are used to define possible precipitation
types around 0°C.

CS120A and CS125 Visibility and Present Weather Sensors
6
1.4 Recommended Tools
The following installation tools are recommended:
10 mm open spanner/wrench (for grounding boss, must be open ended)
13 mm spanner/wrench
19 mm open spanner/wrench (for cable glands, must be open ended)
2 mm flat screwdriver
Number 2 cross head screwdriver
1.5 Quickstart
The sensor is shipped set to the following default communication RS-232, 8N1,
38400 baud, a sensor ID = 0 and set to transmit default messages, full format,
visibility only for the CS120A, SYNOP present weather full format for the
CS125, at 1 minute intervals (see Section 11).
To start using the CS120A or CS125, first connect a DC supply matching the
specification in Section 3.1 to the red and black wires on the ‘D-connector’ (see
Figure 8-3) and connect to a PC communications port with a terminal emulator set
to RS-232, 38400 baud, 8N1. After a couple of minutes, data messages will be
received. Typing ‘open 0’ will access the menu structure, see Section 15.
2. Measurement specification
Visibility characteristics
Reported visibility (metric)
Reported visibility (imperial)
Visibility accuracy calibration
against factory calibration disk**
Visibility accuracy up to 600 m
Visibility accuracy up to 10,000 m
Visibility accuracy up to 15,000 m
Visibility accuracy above 15,000 m
Precipitation characteristics, water equivalent (CS125 only)
Reported accumulation range
Reported intensity range (up to *)
*The maximum intensity reported is dependent on the mixture of precipitation falling.
**Please refer to Section 1.3 regarding the calibration options for the sensor.

Instruction Manual
7
3. Technical specification
3.1 Electrical specification
Main power supply for DSP and dew heaters
Current consumption sampling
continuously with dew heaters ON and
RS-232 communications active
(2, 3)
(at 12V DC)
248 mA
Current consumption sampling
continuously with dew heaters disabled
(at 12V DC)
Current consumption without any
sampling occurring and dew heaters
disabled (at 12V DC)
Hood heater voltage (AC or DC)
Hood heater wattage (at 24V AC or
DC)
User output high level (at 85ºC)
User output high level (at 25ºC )
User output low (All temperatures)
(1) If a CS215 or HygroVUE probe is being used with a CS125 the supply voltage should not exceed
28V.
(2) The RS-232 communications interface will automatically turn itself off when not transmitting.
(3) If hood heaters are not being used ensure ‘Hood heater override’ (details in Section 13) is set to
off.
(4) It is recommended that the hood heaters are run at 24V AC/DC. It is possible to run the heaters at
any voltage below 24V but the heaters will generate proportionally less heat reducing their ability
to prevent ice build-up.
(5) Each hood takes 30W, 60W is the total for both hoods on the sensor together.
If a CS215 or HygroVUE probe is being used the supply
voltage should not exceed 28V.
3.2 Optical specification

CS120A and CS125 Visibility and Present Weather Sensors
8
4. Communications specification
4.1 Communications electrical specifications
RS-232 Communications
(1)
RS-232 input threshold Low
RS-232 input threshold High
RS-232 input absolute maximum
RS-232 output voltage low
RS-232 output voltage high (into
3K)
RS-485 input threshold voltage
Maximum voltage at any terminal
(2)
(1) The RS-232 communications interface will automatically turn itself off when not transmitting.
(2) The ground of the sensor and the ground of any RS-485 equipment cannot be further apart than
this voltage. The sensor ground (pin 1) on connector B, see page 18, can be connected to the
ground of the host equipment. This will reduce any parasitic currents.
4.2 Supported data rates and formats
Serial setting 8N1
Supported data rates
• 1200 bps
• 2400 bps
• 9600 bps
• 19200 bps
• 38400 bps - default
• 57600 bps
• 115200 bps
Supported formats
• RS-232 (Full duplex only), default
• RS-485 (Half duplex)
• 8 bit data bytes
• 1 stop bit
• Parity checking is not supported as most communication protocols used by
the CS125 have built in checksums as well as checks that communications
have been understood.

CS120A and CS125 Visibility and Present Weather Sensors
10
6.2 Weights
Sensor weight: 3 Kg
Shipping weight: 6 Kg (including packing box)
6.3 Mounting
Sensor mounting: Bracket mounts on a vertical pole 32-52.5 mm diameter. The
mounting bracket has cut-outs for band clamps for larger
diameter masts.
7. Installation procedure
The sensor measures environmental variables and is designed to be located in
harsh weather conditions. However, there are a few considerations to take into
account if accurate and representative data from a site are to be obtained.
The descriptions in this section are not exhaustive. Please refer to
meteorological publications for further information on locating
weather instruments
The sensor should be sited in a position representative of local weather conditions
and not of a specific microclimate (unless the analysis of microclimate weather is
being sought).
The sensor has good resistance to background light but it is a good idea to avoid
locations where the transmitter is pointing at a light scattering or reflecting
surface. Ideally, the receiver should point north in the northern hemisphere or
south in the southern hemisphere but this is not critical. This is because it is more
important to make sure the receiver is not pointing towards any possible sources
or reflected light in its field of view, for instance nearby sensors or enclosures
mounted below it on a mast. Where those objects cannot be moved, pointing the
sensor away from North/South is acceptable. Failure to do this can result in the
sensor reporting a DC light saturation error when there is bright sunlight.
To give non-microclimatic measurements the sensor should be sited away from
possible physical obstructions that could affect the fall of precipitation. The sensor
should also be positioned away from sources of heat, electrical interference and in
such a position as to not have direct light on the sensor lenses. Whenever possible,
the sensor should be located away from windbreaks.
Several zones have been identified upwind and downwind of a windbreak in
which the airflow is unrepresentative of the general speed and direction. Eddies
are generated in the lee of the windbreak and air is displaced upwind of it. The
height and depth of these affected zones varies with the height and to some extent
the density of the obstacle.
Generally, a structure disturbs the airflow in an upwind direction for a distance of
about twice the height of the structure, and in a downwind direction for a distance
of about six times the height. The airflow is also affected to a vertical distance of
about twice the height of the structure. Ideally, therefore, the sensor should be
located outside this zone of influence in order to obtain representative values for
the region.

CS120A and CS125 Visibility and Present Weather Sensors
18
Connector A - Five way connector
Main electronics +ve supply input
Auxiliary Electronics 0V. Common with the main electronics 0V.
This is for the hood heater power supply. If the hood heater supply is
DC it should be the negative connection and if it is AC it should be
the ‘neutral’ or ‘ground’ connection if there is one.
Auxiliary Electronics 0V. Common with the main electronics 0V.
This is for the hood heater power supply. If the hood heater supply is
DC it should be the positive connection.
To avoid damage to noise filters on the hood heater inputs if
the heater voltage is DC the –ve connection should be made
to pin 3 and the +ve to pin 5. If the heater voltage is AC with a
ground or neutral wire then this should be connected to pin 3.
Pin 3 should not be more than 5 volts from the main
electronics 0V.
Connector B - Three way connector
0V connection for serial communications. This connection is
common with the main electronics 0V (Connector A, pin 2).
RS-232 receive line, RXD, B/D+ for RS-485 half duplex
RS-232 transmit line, TXD, A/D− for RS-485 half duplex
It may be necessary to use a 120 ohm termination resistor to reduce signal
distortion when using RS-485 for cable runs over about 500 m and baud rates
above 38400. It should be connected between pins 2 and 3.
Connector C - Four way connector
0V connection for user alarms. This connection is common with the
main electronics 0V (Connector A, Pin 2).
0V connection for user alarms. This connection is common with the
main electronics 0V (Connector A, Pin 2).
To use these connections it is necessary to either use the cable gland
taking the hood heater power or, if the hood heater is also required,
to use different cables to those supplied. Please contact Campbell
Scientific if you need any advice on choice of cable.

CS120A and CS125 Visibility and Present Weather Sensors
24
Table 10-1. Internal switch functions
When switched ON the sensor uses the TMOR
calibration and OFF it uses the MOR calibration.
Please refer to Section 1.3 for a description of
these two calibration options.
When switched to the ON position and the sensor
is power cycled this switch temporarily sets the
sensor communications port to a default RS-232
communication state at 38400 baud. This is useful
during field tests or maintenance when the sensor
has been remotely configured for RS-485 mode or
a baud rate your PC does not support. This change
is temporary and will not be stored to flash.
However, if the menu system is accessed and a
‘Save and exit’ command is performed these new
data rate settings will be committed to flash.
Once this switch is returned to its OFF position
and the sensor is power cycled the sensor will
return to its previous communications settings.
Reserved for future use, set to OFF.
When switched to the ON position this switch
will reset the sensor to its factory default values.
This reset will affect all communication settings.
This will take immediate effect upon power up.
NOTE: To use this the power supply must be
stable. Do not leave this switch set permanently.
If the lid is removed take care not to overtighten the screws when it
is replaced. A small gap should remain between the lid and box.
11. Message Formats: A breakdown of the different
default outputs of the sensor – Basic/Partial/Full
The sensor has twelve different message formats available to the user. All
parameters are space delimited with a unique start and end character allowing easy
storage into any logger (see Section 15 on how to set default outputs). The
SYNOP Full Format message is the default message for the CS125 and the Full
Format Visibility only message is the default for the CS120A. These can be
selected from the Message – Sub 3 menu.
CS125 MESSAGE - SUB 3
Set the message output format. Current format is: FULL SYNOP
- Basic = 0
- Partial = 1
- Full = 2
- Basic SYNOP = 3
- Partial SYNOP = 4
- Full SYNOP = 5
- Basic METAR = 6
- Partial METAR = 7
- Full METAR = 8
- Generic Basic SYNOP = 9
- Generic Partial SYNOP = 10
- Generic Full SYNOP = 11
- Custom output = 12
->

Instruction Manual
25
STX and ETX are hexadecimal command characters.
Refer to Appendix B for the checksum algorithm.
11.1 Visibility only messages
Basic Format, Visibility Only
Message ID Sensor ID System
status Visibility distance
Carriage return Line feed
0 0 0 19837 M FC92 (Example message, visibility units = metres)
In the following example messages the shown message intervals are
12 seconds and visibility units are in metres unless otherwise
indicated.
Partial Format, Visibility Only
Sensor ID System status Message interval Visibility distan
User alarms Checksum (CCITT) ETX
Carriage return Line feed
1 0 0 12 20405 M 0 0 EF07 (Example message)

CS120A and CS125 Visibility and Present Weather Sensors
26
Full Format, Visibility Only (Default message for CS120A)
System status Message interval Visibi
Visibility units Averaging duration User
System
alarms 10 charac
ters
Carriage return Line feed
2 0 0 12 68218 F 1 0 0 0 0 0 0 0 0 0 0 0 0 D378 (Example with Visibility Units = Feet)
2 0 0 12 21793 M 1 0 0 0 0 0 0 0 0 0 0 0 0 CB0F (Example with Visibility Units = Metres)
11.2 Messages with SYNOP Present Weather Codes (CS125 only)
SYNOP Present Weather Basic Format
Message ID Sensor ID System status Visibility distance
SYNOP Code Checksum (CCITT) ETX
Carriage return Line feed
3 0 0 20428 M 0 20B8 (Example message)
SYNOP Present Weather Partial Format
Message ID Sensor ID System status Message interval Visibility distance
Relative humidity* Checksum (CCITT) ETX
Carriage return Line feed
4 0 0 12 21157 M 0 0 0 0.00 0 24.1 -99 5A55 (Example message)

Instruction Manual
27
SYNOP Present Weather Full Format (Default message for CS125)
Message ID Sensor ID System status Message in
System alarms 12 characters
Particle count (minute) Intensity (mm/h) SYNO
Relative humidity* Checksum (CCIT
Carriage Return Line feed
5 0 0 12 20880 M 1 0 0 0 0 0 0 0 0 0 0 0 0 0 0 0 0.00 0 24.1 -99 CAFA (Example message)
11.3 Messages with METAR Present Weather Codes (CS125 only)
METAR Present Weather Basic Format
System status Visibility distance
METAR Code Checksum (CCITT) ETX
Carriage return Line feed
6 0 0 20573 M NSW 291A (Example message)
METAR Present Weather Partial Format
System status Message interval Visibility distance Visibility
METAR Code Temperature (deg C) Relative hu
7 0 0 12 20673 M 0 0 0 0.00 0 NSW 24.2 -99 BD78 (Example message)

CS120A and CS125 Visibility and Present Weather Sensors
28
METAR Present Weather Full format
Message ID Sensor ID System status Message inter
Visibility distance Visibility units
Averaging duration User alarms
System alarms 12 characters Particle count (minute) Intensity (mm/h) SYNOP Code METAR Code Temperature (
Carriage Return Line feed
8 0 0 12 20504 M 1 0 0 0 0 0 0 0 0 0 0 0 0 0 0 0 0.00 0 NSW 24.2 -99 40A2 (Example message)
Relative humidity is only available if a CS215 or HygroVUE probe
temperature and RH sensor is attached. If not this field is “-99”.
11.4 Messages with Generic SYNOP Present Weather Codes
(CS125 only)
These messages include simplified, generic present weather codes such as 70 for
snow which may be required for some data collection systems.
Generic SYNOP Present Weather Basic format
Message ID Sensor ID System status Visibility
SYNOP code METAR code Checksum
9 0 0 20481 M 0 0 NSW 73DF (Example message)

CS120A and CS125 Visibility and Present Weather Sensors
30
Table 11-1. Summary of message IDs and descriptions
Basic format. Contains only distance and system information
Partial format. Contains user alarm outputs
Full format. Contains all system alarms codes
Basic SYNOP present weather format
Partial SYNOP present weather format
Full SYNOP present weather format
Basic METAR present weather format
Partial METAR present weather format
Full METAR present weather format
Generic Basic SYNOP present weather format
Generic Partial SYNOP present weather format
Generic Full SYNOP present weather format
Unit number defined by the user to aid identification of data. Zero by default.
Useful for RS-485 networks. Operates as an address in RS-485 mode
System status break down
(1)
Possible degraded performance
(1) System status break down reflects the highest level of severity of any active alarm.
The amount of time, in seconds, between outputs in continuous mode
Visibility distance break down
Current visibility distance being detected by the sensor
Visibility units break down
Averaging duration break down (see note)

Instruction Manual
31
In accordance with WMO requirements the sensor produces
visibility measurement that are either one or ten minute rolling
averages that are updated at the chosen output interval or when the
sensor is polled. Those averages are not direct averages of MOR
measurements but are averages of extinction coefficient and that
average is then used to calculate the MOR for that period. As the
relationship between extinction coefficient and MOR is not linear it
is possible to see quite rapid changes in MOR that might not be
expected if the result was a rolling average of MOR. Please consider
this, especially when testing the sensor with artificial obscurants or
using the calibration disc.
Visibility either less or greater than a user specified threshold
Visibility either less or greater than a user specified threshold
Table 11-2. Summary of system alarms and descriptions
Emitter failure
(emitter hoods
main LED
output power
level)
0 = Everything is within normal parameters
1 = Light output level too low
2 = Light output level too high
0 = OK. The reported attenuation is below 10%
1 = Reported window signal value is out of range (>30%)
Possible sensor fault or hood could be blocked
2 = Slight dirt build up (10% signal attenuation or higher)
3 = High level of dirt build up (>20%)
0 = Temperature is within operating conditions
1 = Too low. Less than -40°C
2 = Too high. Over 80°C
3 = No sensor detected or below -54°C
0 = OK. The reported attenuation is below 10%
1 = Reported window signal value is out of range (>30%)
Possible sensor fault or hood could be blocked
2 = Slight dirt build up (10% signal attenuation or higher)
3 = High level of dirt build up (>20%)
0 = Temperature is within operating conditions
1 = Too low. Less than -40°C
2 = Too high. Over 80°C
3 = No sensor detected or below -54°C
Detector DC
saturation
level (amount
of background
light seen by
the detector
hood)
(1)
0 = Within limits
1 = Saturated. The sensor may not be able to perform visibility
readings in some circumstances. Possibly due to high level of
reflections into the detector.
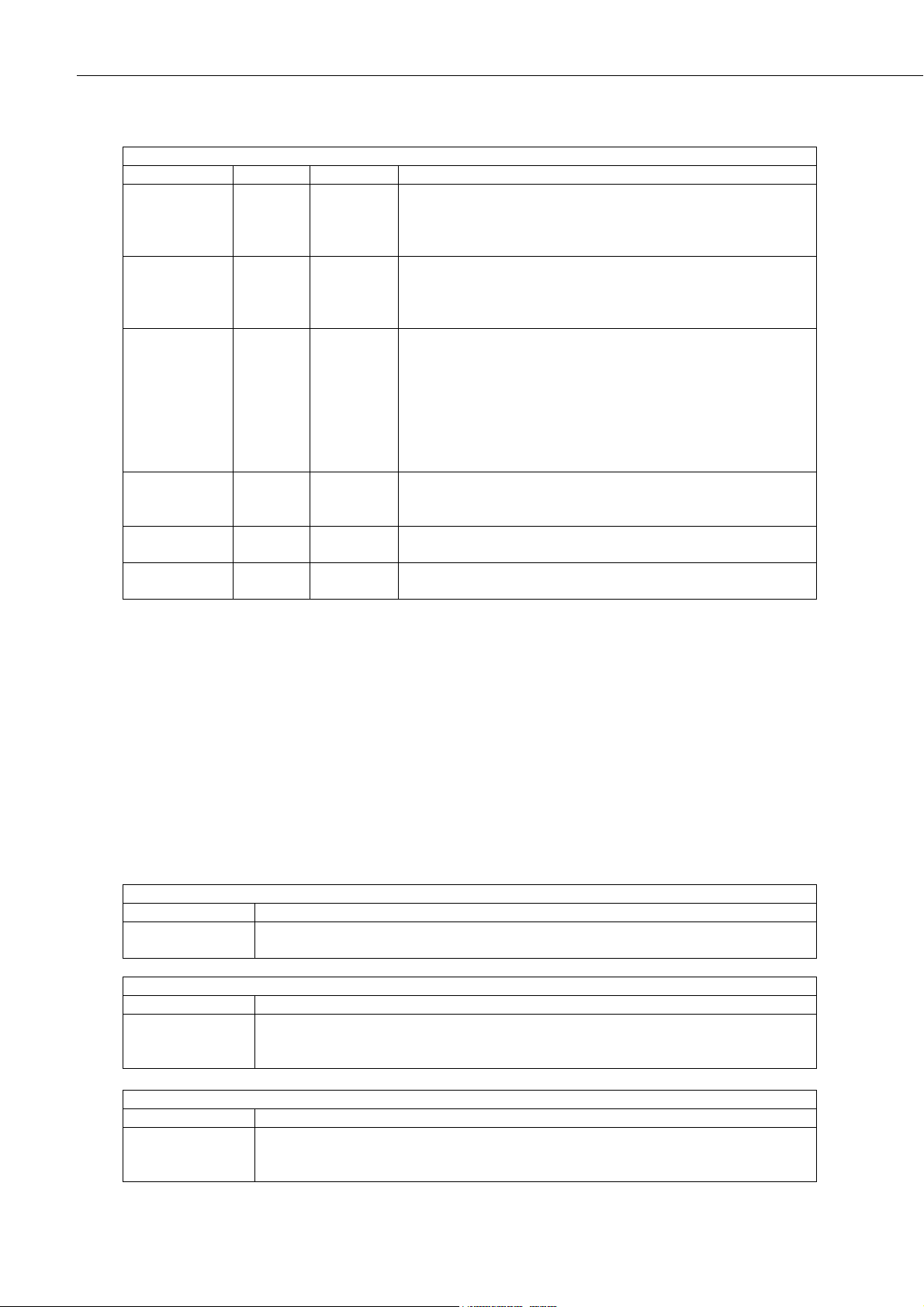
CS120A and CS125 Visibility and Present Weather Sensors
32
0 = Temperature is within operating conditions
1 = Too low. Less than -40°C
2 = Too high. Over 80°C
3 = No sensor detected or below -56°C
External
temperature
(CS125 only)
0 = Temperature is within operating conditions
1 = Too low. Less than -40°C
2 = Too high. Over 80°C
3 = No sensor detected or below -54°C
0 = No fault
1 = OS signature error at power up
2 = User memory signature did not match when last read
3 = User memory fault at power up. Secondary copy was
reinstated to correct error.
4 = User memory fault at power up. No secondary copy was
found to reinstate. Factory defaults have been reinstated.
System will need re-calibrating
0 = No errors
1 = One or more errors reading user variables from flash
occurred
0 = No errors
1 = One or more errors writing user variables to flash occurred
Particle limit
(CS125 only)
0 = No errors
1 = More particles detected than can be processed
(1)
With operating system 14 onwards, to avoid short term appearance of alarms caused by transient
events, such as insects or raindrops on the lens, the condition which triggers an increase in alarm level
must persist for 15 minutes before the alarm is set.
Errors are checked every 10 seconds and the next message output is updated with
the following exceptions:
Signature error is checked and reset at power up.
Flash read and write errors are checked when flash memory is updated, for
example when changes are made through the memory structure. They are also
reset on power up.
Particle limit is checked every minute and reset when read.
Value represented by an integer number of the current number of particle per minute.
(-99 indicates either an error or that the sensor has been powered less than one minute)
Value represented by a single precision value of the last minutes rainfall intensity in
mm/hr (-99 indicates either an error or that the sensor has been powered up less than
one minute)
SYNOP weather code for the last minute as defined by the WMO code table 4680.
(-1 indicates either an error or that the sensor has been powered up less than one
minute)

SYNOP weather code for the last three minutes as defined by the WMO code table
4680 simplified to give generic codes. (-1 indicates either an error or that the sensor
has been powered up for less than one minute)
METAR weather code for the last minute as defined by the WMO code table 4678.
External temperature in degrees Celsius
External relative humidity in %RH (-99 indicates either a fault or no CS215 or
HygroVUE T/RH sensor is connected)
*CS125 only, see Appendix C.
11.5 Example sensor message outputs
Full format, visibility only (CS120A default)
2 0 0 10 9622 M 1 0 0 0 0 0 0 0 0 0 0 0 0 46AA
SYNOP present weather full format (CS125 default)
5 0 0 10 112 M 1 0 0 0 0 0 0 0 0 0 0 0 0 0 0 6 0.14 52 24.0 -99 9190
METAR present weather full format
8 9 0 60 6682 M 1 0 0 0 0 0 0 0 0 0 0 0 0 0 0 54 4.5 63 +RA 20.2 91 ABCD
Where:
9 is the sensor id
60 is the message interval (60 seconds)
6682 is the visibility in metres
M is the visibility units (metres)
54 is particle count
4.5 is intensity (4.5 mm/hr)
63 is the SYNOP code (heavy rain)
+RA is the METAR code (heavy rain)
20.2 is the temperature (20.2 deg. C)
91 is the RH (91%)
ABCD is the checksum

CS120A and CS125 Visibility and Present Weather Sensors
34
11.6 Custom message format
Once a custom message has been formatted it can be output by selecting option 12
from the message - sub 3 menu.
The custom message format allows the CS120A/CS125 message to be modified to
meet particular requirements. The custom message contains a fixed basic set of
variables and up to 16 additional fields.
The custom message output is only available on OS7 and above.
The custom message is as follows:
Custom format
Message ID Unit ID System status
There are two ways to configure the custom message. The first is through the user
menu system. The second is through the use of logger commands. These logger
commands are MSGSET and MSGGET.
To configure the message using the user menu you will need to enter the sensor
menu system, see the following and Section 15. Entering the sensor menu system.
Return to the message menu 1 and select option 7. You will now be presented
with the list of options shown below:
CS125 MESSAGE - SUB 3
Set the message output format. Current format is: FULL SYNOP
- Basic = 0
- Partial = 1
- Full = 2
- Basic SYNOP = 3
- Partial SYNOP = 4
- Full SYNOP = 5
- Basic METAR = 6
- Partial METAR = 7
- Full METAR = 8
- Generic Basic SYNOP = 9
- Generic Partial SYNOP = 10
- Generic Full SYNOP = 11
- Custom output = 12
->

12 0 0 1 0 92 M1 000000000000 2 0 3 0 92 135 88EF
Menu 1: The message output menu
This will take you to message sub 4 so that the parameters required can be
selected from the available options to configure the message output format;
Enter the number of a custom message field you wish to use and type return. The
screen will update with a 1 next to the chosen field. Repeat for each field you
want then exit the menu. The changes take effect after selecting “Exit and Save”
from the main menu.
Example
In the following example selecting options 1, 3, 4, 10, 15 and 17 puts averaging
duration, system alarms, dirty windows values, SYNOP code, 10 minute average
visibility, and 1 sec visibility into the custom message.
This would give the following output:
Above the custom fields are “1 000000000000 2 0 30 92 135”. The averaging
duration is 1 minute, no system alarms are set, the emitter is reading 2%
contamination, the detector is reading 0% contamination, the SYNOP code is 30,
the 10 minute average visibility is 92 m and the 1 sec reading is 135 m.
CS125 MESSAGE - SUB 4
Configure the message output format:
1 - Averaging duration = 0
2 - User alarms = 0
3 - System alarms = 0
4 - Dirty windows values = 0
5 - Sensor serial number = 0
6 - Particle count = 0
7 - Intensity = 0
8 - Accumulation = 0
9 - Generic SYNOP = 0
10 - SYNOP code = 0
11 - METAR code = 0
12 - NWS code = 0
13 - Temperature (Degrees C) = 0
14 - Humidity (%) = 0
15 - 10 minute ave. vis. = 0
16 - Special 1 = 0
17 - One second vis = 0
18 - Past SYNOP = 0
19 - EXCO = 0
Or, choose 0 to exit when done.
->0
CS125 MESSAGE - MENU 1
ID 0
S/N E1007
(1) Set message format: FULL METAR
(2) Toggle units: METRES
(3) Toggle polled or continuous mode: CONTINUOUS
(4) Set continuous mode message-interval: 1 second(s)
(5) Toggle output averaging period: 1 minute(s)
(6) Sampling interval: 1 second(s)
(7) Configure custom message format
(9) Refresh
(0) Return to main menu

CS120A and CS125 Visibility and Present Weather Sensors
36
The following describes the number of values output.
List of custom output values
12 4 Dirty windows values, as percentages, emitter followed by detector
Particle count
(1)
, particles in the previous minute
Temperature (degrees C)
(1)
Visibility averaged over the last 10 minutes
One second visibility
(4)
(1) These options are only available with a CS125.
(2) This increments to 999.99 mm before resetting to zero. It may be reset to zero at any time with the ACCRES command.
(3) Only outputs a valid value when a CS215/HygroVUE temperature and humidity probe is connected.
(4) The 1 second visibility output is provided ffor special applicationsand research purposes only. This output will have increased noise
levels especially at high visibilities.
12. Interface methods – Device Configuration
Utility/Command line/Menu
The sensor can be set up and controlled in one of three ways.
The first method is by using Campbell Scientific’s Device Configuration Utility
Software (DevConfig) which is included with each delivery on the manuals/
resource disk. This software allows an easy menu driven interface for configuring
the sensor on any Microsoft™ based personal computer. All settings can be
accessed using this program.
The program includes online help instructions that describe its general use with
the sensor and also how to load an operating system.
The Device Configurator can also be used as a terminal emulator to use the builtin menu system of the sensor and to access its calibration menu.
The second method is by using the command line interface where discrete
commands are sent without response from the sensor. This would be the preferred

Instruction Manual
37
method of setting up a sensor if it was connected to a logger for instance. The
configuration setting commands can be sent via a logger to the sensor removing
the need for a local PC to set up the unit.
The third method is by using the simple menu interface built into the sensor
communicating via RS-232 or RS-485, using a terminal emulator program. This
menu system gives access to the more common settings.
All three of these methods use the sensor’s serial connector B to communicate
with the sensor. This can be via the normal communications cable or a
configuration cable as described in Section 8.1.
12.1 Configuring a PC for talking to the sensor
The following describes the procedure for setting up communications using a
terminal emulator program. The terminal emulators built into many Campbell
Scientific software products can also be used.
The following settings should then be used by default:
Bits per second: 38400
Data bits: 8
Parity: none
Stop bits: 1
Flow control: none
Ensure that if the baud rate of the unit has been adjusted and then the
corresponding bits per second value is entered in the port settings of the terminal
emulator. The sensor should now be ready to accept commands.
It is possible to set the sensor into the default communication state via one of the
internal switches on the sensor main board. See Section 9.
13. Definition of the variables that can be set by the
user on the sensor
Both DevConfig and the command line interface can access all the user
configurable variables within the sensor. The following lists the acceptable range
and the identification number for these variables along with a short description.
Table 13-1. User definable settings and descriptions
Separate ID used as an extra identifier for a
particular sensor on a network.
User alarm one activation state
0 = Alarm one disabled
1 = Alarm one enabled
0 = Check if distance is less than ‘User alarm 1
Distance’
1 = Check if distance is greater than ‘User alarm
1 Distance’

CS120A and CS125 Visibility and Present Weather Sensors
38
Table 13-1. User definable settings and descriptions
Distance value that alarm one will trigger against.
This value will correspond to metres or feet
depending upon which is selected in ‘Visibility
Unit’
User alarm two activation state
0 = Alarm two disabled
1 = Alarm two enabled
0 = Check if distance is less than ‘User alarm 2
Distance’
1 = Check if distance is greater than ‘User alarm 2
Distance’
Distance value that alarm one will trigger against.
This value will correspond to metres or feet
depending upon which is selected in ‘Visibility
Unit’
Baud rate for the main RS-232/RS-485 interface
0 = 115200 bps
1 = 57600 bps
2 = 38400 bps
3 = 19200 bps
4 = 9600 bps
5 = 2400 bps
6 = 1200 bps
Internal serial number for the sensor.
(Read only)
Unit the visibility value will be presented as
M = metres
F = feet
Interval in seconds between outputs in continuous
mode. This value has no effect if polled mode has
been selected in ‘Measurement mode’
Selects polled or continuous modes.
In continuous mode the sensor will output a string
in the format as set by ‘Message Format’ at
regular intervals as defined by ‘Continuous
Interval’.
0 = Continuous mode
1 = Polled mode
Output message
0, 1 and 2 = Basic, partial or full visibility
messages
3, 4 and 5 = Basic, partial or full SYNOP
messages
6, 7 and 8 = Basic, partial or full METAR
messages
9, 10 and 11 = Generic basic, partial or full
SYNOP messages
12 = Custom message
Selects the physical serial interface
0 = RS-232 mode
1 = RS-485 mode
The period of time that the visibility measurement
is averaged over. Either one minute or ten.

Used to define the time interval between sampling
the volume. It is recommended that this value is
left at one except when very low power demands
are needed. Note that 1s sample timing is needed
for present weather measurement. For example:
1 = Sample every second
2 = Sample one second in every two
3 = Sample one second in every three etc.
0 = Allow the sensor to automatically control the
dew heaters
1 = Turn the dew heaters off
0 = Allow the sensor to automatically control the
hood heaters
1 = Turn the hood heaters off
Dirty window
compensation
0 = No compensation applied
1 = Compensation for dirt on lenses applied.
The sensor will compensate for up to 10% signal
loss due to dirt per lens.
0 = Disable command line CRC-16 checking
(2)
1 = Enable command line CRC-16 checking
Note: this does not affect communications via
DevConfig or terminal emulator.
Sensor power down
voltage
PSU Input voltage level below which the sensor
will enter low power mode. This is usually used to
protect batteries.
Relative humidity
(3)
threshold
Threshold at which the sensor will define
obscuration as liquid or dry if a CS215 is fitted.
(1) Hood heater override needs to be set to ‘1’ (off) when either no hood heaters are installed or
the hood heaters have no power connected to them. This will save power as the relay is not
enabled at low temperatures in this mode.
(2) If disabled the sensor does not check the validity of received data against the checksum sent.
It is, however, recommended that checksum checking is enabled to remove any chance of the
sensor being configured incorrectly by accident.
(3) CS125 only.
14. Command line mode
The command line interface is broken down into three major commands. These
are GET, SET and POLL. The GET command is used to request all current user
settable values from the sensor. The SET commands sets user settable values and
the POLL command is used to request the current visibility and/or alarm
conditions from the sensor.
The sensor can be configured to expect any commands sent to it to include a valid
checksum. For simple commands, e.g. GET and POLL, fixed value checksums
can be used (see the downloadable example programs at:
www.campbellsci.com/downloads/cs125-example-programs or
www.campbellsci.com/downloads/cs120a-example-programs ).
For more complex SET commands the checksum needs to be calculated (see
Appendix B). The use of the checksum is disabled by default. It is recommended
that the checksum functionality is enabled where possible, especially when long
cable runs are used, or in electronically noisy environments.

CS120A and CS125 Visibility and Present Weather Sensors
40
14.1 The SET Command
The set command is used to configure the sensor via the command line. The SET
command is a single space delimited string that can be sent from any data logger
or PC equipped with serial communications. The SET command and the ‘Device
Configuration Utility’ software access identical settings within the sensor, please
refer to the ‘Device Configuration Utility’ section of this document for a more
detailed breakdown of the setting available here. This command is used to change
the default power up state of the sensor. See Section 14.2 if a setting is going to be
changed on a regular basis e.g. heater controls.
See Section 12 for more information on the values used by the ‘SET’ command.
Sensor ID (may be a new ID)
Sensor serial number (read only)
Polling or Continuous modes
RS-232 or RS-485 serial communications enabled
Dirty window compensation
CRC-16 checking on received commands
Sensor power down voltage
Relative humidity threshold
(3)
Checksum (use the valid CRC-16 checksum)
(1) These values are shown in hexadecimal format not ASCII.
(2) As entered on a keypad.
(3) CS125 only.
14.1.1 Example of a SET Command
SET:0:0 1 1 1000 1 0 15000 2 0 M 60 1 2 0 1 1 0 0 0 1 7 80 :68A3:

CS120A and CS125 Visibility and Present Weather Sensors
44
Data returned by the GET command
User Alarm 1 Active (0 = less than)
Sensor serial number (read only)
Polling or Continuous modes
RS-232 or RS-485 serial communications enabled
Dirty window compensation
CRC-16 checking on received commands
Sensor power down voltage
Relative humidity threshold
(1) These values are shown in hexadecimal format not ASCII.
Example of a GET returned data
0 0 0 10000 0 0 10000 2 1009 M 30 0 2 1 1 1 0 0 0 1 11.5 80 D4FD
Explanation:
Sensor ID = 0
User Alarm 1 not set
User Alarm 1 not active
User Alarm 1 distance = 10000 metres
User Alarm 2 not set
User Alarm 2 not active
User Alarm 2 distance = 10000 metres
Serial baud rate 2 (= 38400 Bd)
Serial number = 1009
Visibility Units = M

CS120A and CS125 Visibility and Present Weather Sensors
48
The ‘open 0’ command is not normally echoed.
The terminal menu only gives access to more common settings.
The following text should now be displayed:
The setup menu
The displayed options are accessed simply by typing the corresponding number
then pressing return. No changes will take effect until you ‘save and exit’. The
exception to this is the calibration menu, but you will be informed before any
changes are made.
The displayed options are accessed simply by typing the corresponding number
then pressing return. No changes will take effect until you ‘Exit and Save’. The
exception to this is the calibration menu, but you will be informed before any
changes are made.
Typing ‘1’ opens the message menu containing settings relating to the sensor’s
outputs.
Menu 1: The message output menu
CS125 MESSAGE - MENU 1
ID 0
S/N E1007
(1) Set message format: FULL METAR
(2) Toggle units: METRES
(3) Toggle polled or continuous mode: CONTINUOUS
(4) Set continuous mode message-interval: 1 second(s)
(5) Toggle output averaging period: 1 minute(s)
(6) Sampling interval: 1 second(s)
(7) Configure custom message format
(9) Refresh
(0) Return to main menu
->0
While in the message output menu, typing ‘1’ allows the message format to be set
(Section 11.6). The following lists options. Type the appropriate number to set the
required message format. The messages are described in more detail in Section 11.
Note that the CS120A Visibility Sensor can only output messages 0-2 and a
limited custom message.
WELCOME TO THE CAMPBELL SCIENTIFIC LTD CS125 SETUP
MENU
ID 0
S/N 2003
(1) Message output menu
(2) User alarm menu
(3) Calibrate sensor
(4) System information
(5) Communications setup
(6) System configuration
(9) Exit and save
(0) Exit and don't save

Instruction Manual
51
Menu 4: The system information menu
If either of the dirty window alarms are set it is recommended you follow the
cleaning section of this manual (Section 18).
If there is a flash error or signature error it is recommended that you contact
Campbell Scientific.
The sensor power down voltage shown before the supply voltage is not available
for CS120A sensors with serial numbers less than E1030.
CS125 INFORMATION - MENU 4
ID 0
S/N E1007
OS version: 007646v14
Alarm Value
- Last visibility reading: - 14899m
- Overall system status: 0 No faults
- Emitter dirty window alarm: 0 0%
- Emitter internal temperature: 0 27.6
- Detector dirty window alarm: 0 0%
- Detector internal temperature: 0 25.1
- Detector DC light saturation: 0 -
- Hood heater temperature: 0 20.3
- CS125 Calibrator Serial No: - 2000
- CS125 Calibrator EXCO: - 23.7
- Calibration value factory offset: - 0.031
- Calibration value factory scale: - 0.02493
- Calibration value cal offset: - 0.031
- Calibration value cal scale: - 0.02493
- Signature fault: 0 -
- Flash write errors: 0 0
- Flash read errors: 0 0
- Supply voltage: <7.0V 12.4V
- Aux supply voltages: +5V=5.0 -5V=-5.1 +6V=5.9
- External temperature: 0 22.2
- Present weather mode enabled
- TMOR mode disabled
(8) Get debug
(9) Refresh
(0) Return to main menu
->0

CS120A and CS125 Visibility and Present Weather Sensors
52
Menu 5: The communication menu
The communications menu is used to set baud rates and the mode of operation
(RS-232/RS-485).
No change will take effect until you ‘exit and save’.
Menu 6: Configuration
This menu sets dew and hood heaters to automatic or off, dirty window
compensation and CRC-16 checking.
In addition it allows the sensor power down voltage to be set. If set this will put
the sensor into a low power state (which will not make measurements) before the
battery voltage has fallen low enough to damage a back-up battery.
The RH threshold for a CS125 can also be set from this menu. This applies if a
CS215 sensor is attached and defines the level of RH below which obscuration is
deemed to be dry (that is haze, SYNOP 04 or 05, METAR HZ) rather than wet
(mist, SYNOP 10, METAR BR or fog, SYNOP 30 etc. METAR FG).
The default for Patchy Fog is ON in which case the message outputs will include
BCFG. If patchy fog is toggled to OFF the message output will not include BCFG.
It can be better sometimes to not output BCFG with some aviation systems.
CS125 COMMUNICATIONS - MENU 5
ID 0
S/N 1009
(1) Set sensor ID
(2) Set RS-232/RS-485 baud rate: 38400
(3) Toggle RS-232/RS-485 modes: RS-232
(9) Refresh
(0) Return to main menu
->
CS125 CONFIGURATION - MENU 6
ID 0
S/N E1007
(1) Dew heater: AUTOMATIC
(2) Hood heater: AUTOMATIC
(3) Dirty window compensation: COMPENSATED
(4) Command line CRC Checking: DO NOT CHECK
(5) Sensor power down voltage: 7.0V
(6) RH threshold: 80%
(7) Toggle patchy fog: ON
(8) Toggle status LED: AUTOMATIC
(10) Set hood heater ON above: 15
(11) Set hood heater OFF below: 25
(9) Refresh
(0) Return to main menu
->

Instruction Manual
53
Option (8) is reserved for future use.
Option (10) and (11) allows the user to manually set the temperatures at which the
hood heaters turn on and off. These values are not normally changed as they are
set to reduce the chances of icing in bad weather conditions and dew formation on
the lenses.
Menu 9 and 0: Exiting the menu system
Options ‘9’ and ‘0’ exit from the menu system. Note that typing ‘0’ will lose all
changes made including communications settings.
16. Calibrating the sensor
16.1 Visibility calibration
The sensor can be checked and adjusted using the optional sensor high grade
calibration kit. The calibration must be run using the onboard menu system. If you
have Campbell Scientific’s Device Configuration program a terminal emulation
screen is provided in the sensor screens to let you access this function. To perform
the calibration you will need a sensor calibrator disk and a computer with a
standard serial port compatible with the sensor. If your sensor is not currently
configured for RS-232 communications you can set the internal switch, switch
three, to temporarily set the sensor to RS-232 mode 38400 bps. If the sensor is
already set in RS-232 mode it should not be necessary to change any internal
switches. (See Section 10 for more information on the sensor internal switches.)
The test should ideally be performed in the following conditions:
• Ambient temperature should be between 0ºC and 50ºC
• The local visibility should be approximately 10,000 metres or higher.
The system is self-regulating. However, it is recommended that the sensor is
calibrated at least every two years.
The calibration is performed from menu item 3 on the main terminal screen.
Please refer to the menu section (Section 13) of this manual for further
information on how to access this menu.
Once you have selected menu item 3 you should be presented with the following
screen.
CAMPBELL SCIENTIFIC LTD sensor menu exited.

CS120A and CS125 Visibility and Present Weather Sensors
54
CS125 CALIBRATION - MENU 3
ID 0
S/N 1006
(1) Perform calibration
(2) Restore the factory calibration
(3) Perform dirty windows zero offset calibration
(4) Restore dirty windows factory calibration
(9) Refresh
(0) Return to main menu
Select option 1 to start the calibration. You will then be asked to confirm that you
would like to perform a calibration. Please note, once you have entered yes at this
point you will not be able to exit until the test is complete. However, power
cycling the unit at this point will have no adverse effect on the sensor.
At this stage it is advisable to clean the lenses. Refer to Section 18
‘Cleaning’ for more information. A simple visual check may be
enough to confirm the lenses are clean.
Once you have started the tests you will be asked for the sensor calibrator serial
number and extinction coefficient (EXCO) with a confirmation at each step giving
you the chance to correct typing mistakes.
You should not enter the “E” at the start of the calibration disk serial number.
When asked for confirmation you do not need to press return after
you type ‘y’.
Do you want to perform a calibration Y/N? Y
Starting calibration.
Input the calibration disk serial number ->2000
Is 2000 correct? (Y/N)? Y
Input the calibration disk EXCO ->23.7
Is 23.7 correct? (Y/N)? Y
Place one calibration bung into each hood, then
press any key.
Do you want to perform a calibration Y/N?

Instruction Manual
57
16.2 Dirty window zero calibration
Option 3 in the calibration menu allows the user to reset the zero contamination
level for dirty windows detection (option 4 allows a return to the factory value if
something goes wrong with the calibration process.)
This should be carried out every two years to correct for any slight drift in the
dirty window detection or changes caused by scratches or degradation of the
lenses some of which may not be visible to the naked eye.
To carry out the dirty window zero offset calibration make sure the windows are
very clean (see Section 18). Temperature should ideally be in the range 15-30°C
and the sensor should have been powered up for over 5 minutes. Before starting
this process make sure the lenses are dry and that neither the calibration bungs or
calibration disk are in place.
CS125 CALIBRATION - MENU 3
ID 0
S/N 1006
(1) Perform calibration
(2) Restore the factory calibration
(3) Perform dirty windows zero offset calibration
(4) Restore dirty windows factory calibration
(9) Refresh
(0) Return to main menu
Typing ‘3’ returns text similar to the following:
Current values EO=3200 DO=4649 DD=995
Cal DW offset? Y/N?
Then type ‘Y’. The sensor responds in a similar way to the following:
Calibrating dirty window system...Please wait
EO=3230 ES=371 DO=2251 DS=234 DD=1140
Press any key to exit (Not return)
The numbers reported are internal measurements reported for reporting to the
factory in case of a fault. Press any key and the dirty window zero offset
calibration is complete. As a final check of a successful calibration return to the
information screen and check the two dirty window alarm values which should not
report close to 0%.
16.3 Internal temperature check (CS125 only)
The CS125 has an internal temperature sensor in one of the cross arms. This is
used as part of the present weather identification if a CS215 temperature and RH
sensor is not connected. This does not need recalibration but can be checked if a
suitable nearby reference temperature measurement is available. The CS125
external temperature given in some standard messages (see Section 11) or in the
system information menu (see Section 15) should be within about 3°C of the
reference. The comparison should ideally be made in cloudy and windy conditions
and as near to 0°C as possible.

CS120A and CS125 Visibility and Present Weather Sensors
60
18. Cleaning
The sensor is a robust instrument that will provide years of uninterrupted weather
monitoring. Calibration is carried out at the factory and can be redone easily on
site with the optional sensor calibrator or carried out by Campbell Scientific if
required. Only general cleaning of the lenses is required to keep the sensor
working efficiently.
Cleaning of the sensor will be required from time to time to ensure that the lenses
are free from contaminants. The frequency of required cleaning depends on the
exposure of the instrument to such contaminants. This will vary depending on the
site location. The sensor is capable of self diagnosing dirty lenses and will indicate
in its output when the lenses are contaminated to such a degree that its visibility
measurements may be affected.
A lower level of contamination than is detected by the dirty window
alarms, can affect the visibility measurements. The sensor can be
configured to attempt to make a correction for contamination
although the accuracy of that correction depends on the ‘type of
dirt’.
We suggest 6 monthly intervals for locations not prone to contaminants and
monthly intervals for those prone to contamination (roadside or airport use). In
some cases more frequent cleaning may be required where there are high levels of
contaminants and high dependency on the instrument output.
If the lenses require cleaning, it is very important that only a
proper lens cloth or lens tissue be used. The use of
inappropriate materials to clean the lenses can permanently
damage or reduce the effectiveness of the lenses leading to
errors in measurement of precipitation and visibility.
It is advisable to use an air duster to blow any loose dust and dirt from the lenses
as a first step. Using a lint free lens cloth or lens tissue impregnated with a small
amount of isopropyl alcohol solvent clean the lens surface by dragging the cloth
across the lens surface being careful not to apply excessive pressure.
Excessive pressure may lead to some types of contaminant scratching the lens
surface. Over time such scratches can lead to reduced sensor accuracy.
Spiders webs and certain ‘fluffy ’ seeds which get lodged in the
optical path can lead to the sensor permanently giving low readings
and can lead to false reports of precipitation. Cleaning the visibility
contamination away with a duster will return the sensor to normal
operation.
If spiders are a persistent problem, using some carefully applied
insecticide can deter them.

Instruction Manual
61
19. Lubricating the enclosure screws
The sensor enclosure screws should be lubricated with a suitable anti-seize grease
to protect the threads from corrosion. This should be reapplied when resealing the
enclosure at regular intervals, normally after replacing the desiccant. This is of
particular importance if using the sensor in corrosive or salt laden atmospheres.
20. Desiccant
Two bags of desiccant are supplied. One is inside the enclosure, the other is
separate and sealed in a plastic bag. Desiccant use depends on your application but
for use in typical temperature conditions one bag is sufficient for a twelve month
period. The desiccant should be placed inside the enclosure taking care that it is
not trapped between the lid and the enclosure when the lid is replaced.
The second bag of desiccant should be kept in the plastic shipping bag as a
replacement for when the initial bag needs to be dried out. The bags can be rotated
in this way many times. Desiccant bags can be dried out by the following method:
1. Arrange the bags on a wire tray in a single layer to allow for adequate air flow
around the bags during the drying process. The oven’s inside temperature
should be room or ambient temperature (25°C - 30°C). A convection,
circulating, forced air type oven is recommended for this regeneration
process. Seal failures may occur if any other type of heating unit or appliance
is used.
2. When placed in a forced air, circulating air, or convection oven, allow a
minimum of 4 to 5 cm of air space between the top of the bags and the next
metal tray above the bags. If placed in a radiating exposed infra-red element
type oven, shield the bags from direct exposure to the heating element, giving
the closest bags a minimum of 40 cm clearance from the heat shield.
Excessive surface film temperature due to infra-red radiation will cause the
Tyvek material to melt and/or the seals to fail. Seal failure may also occur if
the temperature is allowed to increase rapidly. This is due to the fact that the
water vapour is not given sufficient time to diffuse through the Tyvek
material, thus creating internal pressure within the bag, resulting in a seal
rupture. Temperature should not increase faster than 0.1°C to 0.3°C per
minute.
3. Set the temperature of the oven to 118°C, and allow the bags of desiccant to
reach equilibrium temperature.
Tyvek has a melting temperature of 121°C - 127°C.
(NON MIL-D-3464E activation or reactivation of both silica gel and
Bentonite clay can be achieved at temperatures of 104°C).
4. Desiccant bags should be allowed to remain in the oven at the assigned
temperature for 24 hours. At the end of this period, the bags should be
immediately removed and placed in a desiccators jar or dry (0% relative
humidity) air tight container for cooling. If this procedure is not followed
precisely, any water vapour driven off during reactivation may be re-adsorbed
during cooling and/or handling.

Add-1
Addendum - Hail monitoring (CS125 only)
The CS125 can specifically report hail in its output messages by connecting to it a
WXT531 hail sensor via the internal SDI-12 port, which is otherwise used for
connecting the CS215 T/RH sensor to the CS125. The connections are shown in
Figure A1 overleaf.
When connected to a WXT531 the CS125 reads the number of hail particles that are
detected every minute. To ensure that hail is attributed accurately, the CS125 only
reports hail, sensed by the WXT531 if, during the same period, the CS125 has
detected one or more particle passing through its sensing volume. In this case it will
change the WMO code to the hail code.
If it is required that the CS125 monitor hail, RH and Temperature, the alternative
WXT535 hail sensor should be used. This is a combined sensor that connects to the
CS125 in the same manner as the WXT531.
Either WXT sensor can be mounted on the same mast as the CS125 but care should
be taken to ensure that it is placed to avoid the sampling zone for the CS125.
Operation of the CS125 with either the WXT531, or WXT535, requires the CS125
to be installed with Operating System 11 (OS11) or later. Free OS upgrades for
CS125 sensors are available from Campbell Scientific.
Note on connecting a hail sensor to a CS125
Summary
This describes the wiring and mechanical arrangement in connecting a WXT531, or
WXT535, hail sensor to a CS125.
This is applicable to CS125 sensors running OS11 or above.
Wiring
The hail sensor connects to the SDI-12 port inside the CS125 otherwise used for a
T/RH sensor as shown in Figure A1. It draws power over this connection in addition
to communicating to the CS125.
See also Sections 8 and 9 of this instruction manual.

C-1
Appendix C. Present Weather Codes
C1. SYNOP Codes produced by the CS125
56 codes are available.
No significant weather observed
Haze or smoke, or dust in suspension in the air, visibility ≥ 1 km*
Haze or smoke, or dust in suspension in the air, visibility < 1 km*
Fog (in the preceding hour)
Precipitation (in the preceding hour)
Drizzle (not freezing) or snow grains (in the preceding hour)
Rain (not freezing), (in the preceding hour)
Snow (in the preceding hour)
Freezing rain or freezing drizzle (in the preceding hour)
Fog or ice fog in patches
Fog or ice fog, has become thinner during the past hour
Fog or ice fog, no appreciable change during the past hour
Fog or ice fog has begun or become thicker during the past hour
Precipitation, slight or moderate
Solid precipitation, slight or moderate**
Freezing precipitation, slight or moderate**
Freezing precipitation, heavy**
Drizzle, not freezing, slight
Drizzle, not freezing, moderate
Drizzle, not freezing, heavy
Drizzle, freezing, slight
Drizzle, freezing, moderate
Drizzle and rain, moderate or heavy
Rain (or drizzle) and snow, slight
Rain (or drizzle) and snow, moderate or heavy
Snow, slight (snow includes graupel)
Snow, moderate (snow includes graupel)
Snow, heavy (snow includes graupel)
SHOWER(S) OR INTERMITTENT PRECIPITATION
Rain shower(s) or intermittent rain, slight
Rain shower(s) or intermittent rain, moderate

CS120A and CS125 Visibility and Present Weather Sensors
C-2
Rain shower(s) or intermittent rain, heavy
Rain shower(s) or intermittent rain, violent
Snow shower(s) or intermittent snow, slight
Snow shower(s) or intermittent snow, moderate
Snow shower(s) or intermittent snow, heavy
*Only reported if a CS215 is connected to provide relative humidity, otherwise they will default to mist (10) or fog (20, 30, 31,
32, 33, 34 or 35).
**Only reported in the generic SYNOP messages.
C2. METAR Codes produced by the CS125
The following METAR codes from WMO table 4678 can be output by the sensor.
UP Unidentified precipitation
HZ Haze
BR Mist
FG Fog
DZ Drizzle
RA Rain
SG Snow grains
SN Snow
PL Ice pellets
SMGR Hail*
Notes:
HZ will only be reported if a CS215 is connected to allow relative humidity
information to be available.
FZ (freezing) may be added as a descriptor in front of BR, FG, DZ and RA
Intensity qualifiers, ‘-‘ for light, ‘+’ for heavy, may be added in front of DZ, RA,
SN, and PL
Combinations, for example RASN for rain and snow can be reported.
*Only reported if an optional hail sensor is connected. Contact Campbell
Scientific for details.
C3. NWS Codes produced by the CS125
NWS codes produced by the CS125 available in a custom message
Z (freezing) may be added as a descriptor in front of L and R
Intensity qualifiers, ‘-‘ for light, ‘+’ for heavy, may be added after the NWS code.
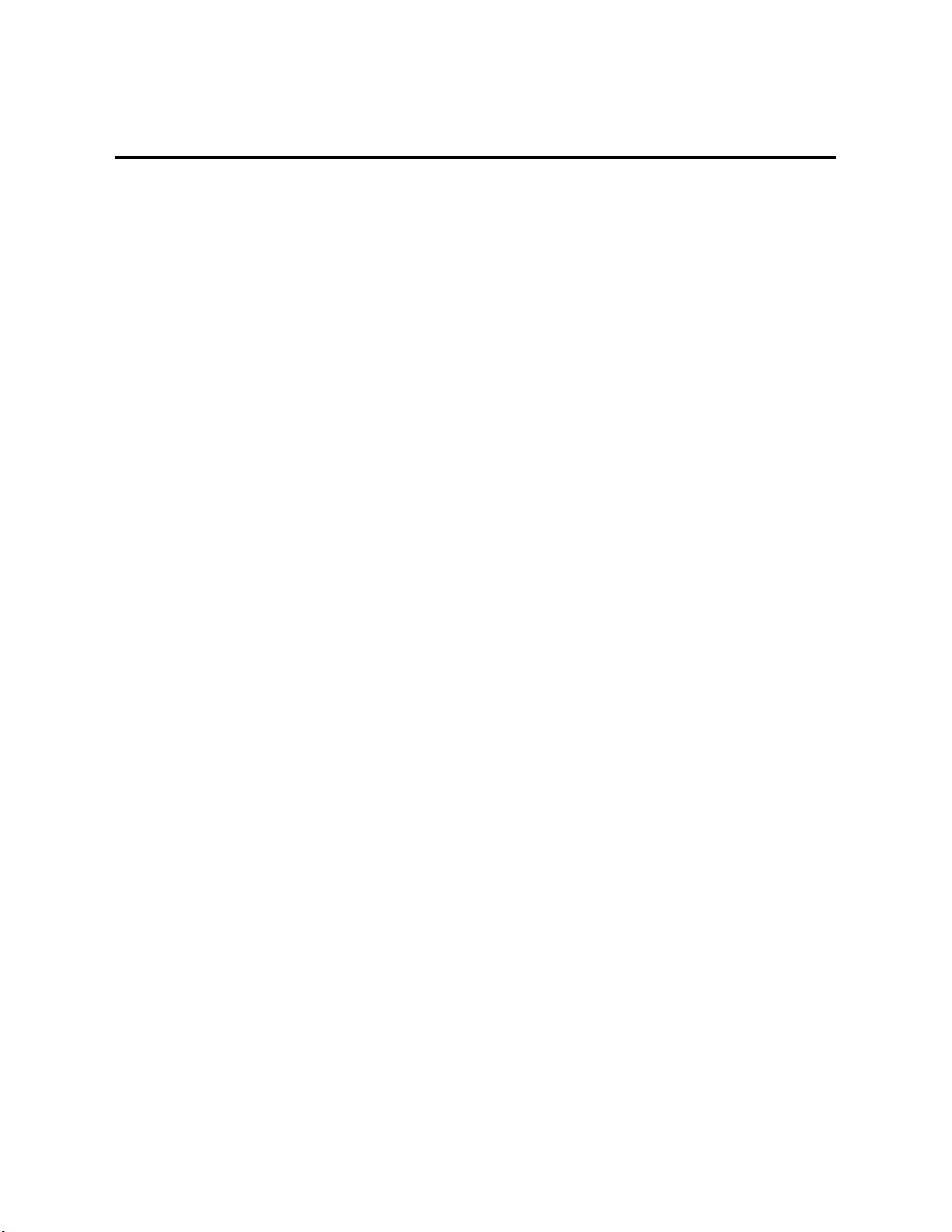
Limited warranty
Products manufactured by Campbell Scientific are warranted by Campbell
Scientific to be free from defects in materials and workmanship under normal
use and service for twelve months from the date of shipment unless otherwise
specified on the corresponding product webpage. See Product Details on the
Ordering Information pages at www.campbellsci.com. Other manufacturer's
products, that are resold by Campbell Scientific, are warranted only to the
limits extended by the original manufacturer.
Refer to www.campbellsc i.com/terms#warranty for more information.
CAMPBELL SCIENTIFIC EXPRESSLY DISCLAIMS AND
EXCLUDES ANY IMPLIED WARRANTIES OF MERCHANTABILITY
OR FITNESS FOR A PARTICULAR PURPOSE. Campbell Scientific
hereby disclaims, to the fullest extent allowed by applicable law, any and
all warranties and conditions with respect to the Products, whether
express, implied or statutory, other than those expressly provided herein.

Assistance
Products may not be returned without prior authorization.
Products shipped to Campbell Scientific require a Returned Materials
Authorization (RMA) or Repair Reference number and must be clean and
uncontaminated by harmful substances, such as hazardous materials,
chemicals, insects, and pests. Please complete the required forms prior to
shipping equipment.
Campbell Scientific regional offices handle repairs for customers within their
territories. Please see the back page for the Global Sales and Support Network
or visit www.campbellsci.com/contact to determine which Campbell Scientific
office serves your country.
To obtain a Returned Materials Authorization or Repair Reference number,
contact your CAMPBELL SCIENTIFIC regional office. Please write the
issued number clearly on the outside of the shipping container and ship as
directed.
For all returns, the customer must provide a “Statement of Product Cleanliness
and Decontamination” or “Declaration of Hazardous Material and
Decontamination” form and comply with the requirements specified in it. The
form is available from your CAMPBELL SCIENTIFIC regional office.
Campbell Scientific is unable to process any returns until we receive this
statement. If the statement is not received within three days of product receipt
or is incomplete, the product will be returned to the customer at the customer’s
expense. Campbell Scientific reserves the right to refuse service on products
that were exposed to contaminants that may cause health or safety concerns for
our employees.

Safety
DANGER — MANY HAZARDS ARE ASSOCIATED WITH INSTALLING, USING, MAINTAINING, AND WORKING ON OR AROUND
TRIPODS, TOWERS, AND ANY ATTACHMENTS TO TRIPODS AND TOWERS SUCH AS SENSORS, CROSSARMS, ENCLOSURES,
ANTENNAS, ETC. FAILURE TO PROPERLY AND COMPLETELY ASSEMBLE, INSTALL, OPERATE, USE, AND MAINTAIN TRIPODS,
TOWERS, AND ATTACHMENTS, AND FAILURE TO HEED WARNINGS, INCREASES THE RISK OF DEATH, ACCIDENT, SERIOUS
INJURY, PROPERTY DAMAGE, AND PRODUCT FAILURE. TAKE ALL REASONABLE PRECAUTIONS TO AVOID THESE HAZARDS.
CHECK WITH YOUR ORGANIZATION'S SAFETY COORDINATOR (OR POLICY) FOR PROCEDURES AND REQUIRED PROTECTIVE
EQUIPMENT PRIOR TO PERFORMING ANY WORK.
Use tripods, towers, and attachments to tripods and towers only for purposes for which they are designed. Do not exceed design limits. Be familiar and
comply with all instructions provided in product manuals. Manuals are available at www.campbellsci.com. You are responsible for conformance with
governing codes and regulations, including safety regulations, and the integrity and location of structures or land to which towers, tripods, and any
attachments are attached. Installation sites should be evaluated and approved by a qualified engineer. If questions or concerns arise regarding installation,
use, or maintenance of tripods, towers, attachments, or electrical connections, consult with a licensed and qualified engineer or electrician.
General
• Protect from over-voltage.
• Protect electrical equipment from water.
• Protect from electrostatic discharge (ESD).
• Protect from lightning.
• Prior to performing site or installation work, obtain required approvals and permits. Comply with all
governing structure-height regulations.
• Use only qualified personnel for installation, use, and maintenance of tripods and towers, and any
attachments to tripods and towers. The use of licensed and qualified contractors is highly recommended.
• Read all applicable instructions carefully and understand procedures thoroughly before beginning work.
• Wear a hardhat and eye protection, and take other appropriate safety precautions while working on or
around tripods and towers.
• Do not climb tripods or towers at any time, and prohibit climbing by other persons. Take reasonable
precautions to secure tripod and tower sites from trespassers.
• Use only manufacturer recommended parts, materials, and tools.
Utility and Electrical
• You can be killed or sustain serious bodily injury if the tripod, tower, or attachments you are installing,
constructing, using, or maintaining, or a tool, stake, or anchor, come in contact with overhead or
underground utility lines.
• Maintain a distance of at least one-and-one-half times structure height, 6 meters (20 feet), or the distance
required by applicable law, whichever is greater, between overhead utility lines and the structure (tripod,
tower, attachments, or tools).
• Prior to performing site or installation work, inform all utility companies and have all underground utilities
marked.
• Comply with all electrical codes. Electrical equipment and related grounding devices should be installed by a
licensed and qualified electrician.
• Only use power sources approved for use in the country of installation to power Campbell Scientific devices.
Elevated Work and Weather
• Exercise extreme caution when performing elevated work.
• Use appropriate equipment and safety practices.
• During installation and maintenance, keep tower and tripod sites clear of un-trained or non-essential
personnel. Take precautions to prevent elevated tools and objects from dropping.
• Do not perform any work in inclement weather, including wind, rain, snow, lightning, etc.
Maintenance
• Periodically (at least yearly) check for wear and damage, including corrosion, stress cracks, frayed cables,
loose cable clamps, cable tightness, etc. and take necessary corrective actions.
• Periodically (at least yearly) check electrical ground connections.
Internal Battery
• Be aware of fire, explosion, and severe-burn hazards.
• Misuse or improper installation of the internal lithium battery can cause severe injury.
• Do not recharge, disassemble, heat above 100 °C (212 °F), solder directly to the cell, incinerate, or expose
contents to water. Dispose of spent batteries properly.
WHILE EVERY ATTEMPT IS MADE TO EMBODY THE HIGHEST DEGREE OF SAFETY IN ALL CAMPBELL SCIENTIFIC PRODUCTS, THE
CUSTOMER ASSUMES ALL RISK FROM ANY INJURY RESULTING FROM IMPROPER INSTALLATION, USE, OR MAINTENANCE OF
TRIPODS, TOWERS, OR ATTACHMENTS TO TRIPODS AND TOWERS SUCH AS SENSORS, CROSSARMS, ENCLOSURES, ANTENNAS,
ETC.

Campbell Scientific regional offices
Australia
Location:
Phone:
Email:
Website:
Brazil
Location:
Phone:
Email:
Website:
Canada
Location:
Phone:
Email:
Website:
China
Location:
Phone:
Email:
Website:
Garbutt, QLD Australia
61.7.4401.7700
info@campbellsci.com.au
www.campbellsci.com.au
São Paulo, SP Brazil
11.3732.3399
vendas@campbellsci.com.br
www.campbellsci.com.br
Edmonton, AB Canada
780.454.2505
dataloggers@campbellsci.ca
www.campbellsci.ca
Beijing, P. R. China
86.10.6561.0080
info@campbellsci.com.cn
www.campbellsci.com.cn
France
Location:
Phone:
Email:
Website:
Vincennes, France
0033.0.1.56.45.15.20
info@campbellsci.fr
www.campbellsci.fr
Germany
Location:
Phone:
Email:
Website:
Bremen, Germany
49.0.421.460974.0
info@campbellsci.de
www.campbellsci.de
India
Location:
Phone:
Email:
Website:
New Delhi, DL India
91.11.46500481.482
info@campbellsci.in
www.campbellsci.in
South Africa
Location:
Phone:
Email:
Website:
Stellenbosch, South Africa
27.21.8809960
sales@campbellsci.co.za
www.campbellsci.co.za
Thailand
Location:
Phone:
Email:
Website:
UK
Location:
Phone:
Email:
Website:
USA
Location:
Phone:
Email:
Website:
Bangkok, Thailand
66.2.719.3399
info@campbellsci.asia
www.campbellsci.asia
Shepshed, Loughborough, UK
44.0.1509.601141
sales@campbellsci.co.uk
www.campbellsci.co.uk
Logan, UT USA
435.227.9120
info@campbellsci.com
www.campbellsci.com
Costa Rica
Location:
Phone:
Email:
Website:
San Pedro, Costa Rica
506.2280.1564
info@campbellsci.cc
www.campbellsci.cc
Spain
Location:
Phone:
Email:
Website:
Barcelona, Spain
34.93.2323938
info@campbellsci.es
www.campbellsci.es