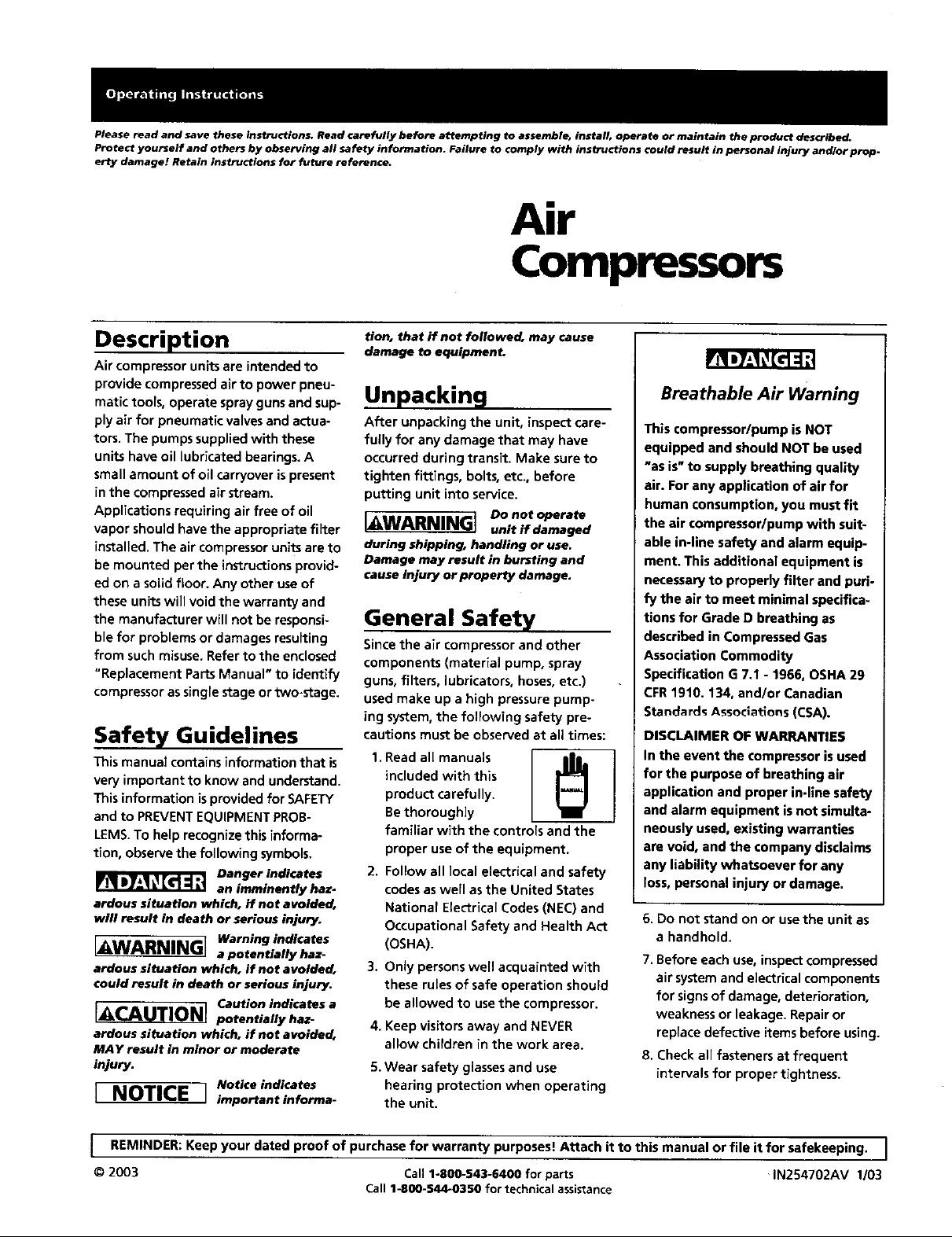
Please read and save these instructions. Read carefully before attempting to assemble, install, operate or maintain the product described.
Protect yourself and others by observing all safety information. Failure to comply with instructions could result in personal injury and/or prop.
erty damage! Retain instructions for future reference.
Air
Compressors
Description
Air compressorunits are intended to
provide compressedair to power pneu-
matic tools, operate sprayguns and sup-
plyair for pneumatic valves and actua-
tors. The pumps supplied with these
units have oil lubricated bearings. A
small amount of oil carryover ispresent
in the compressed air stream.
Applications requiring air free of oil
vapor should have the appropriate filter
installed. The air compressorunits are to
be mounted per the instructionsprovid-
ed on a solid floor. Any other useof
these units will void the warranty and
the manufacturer will not be responsi-
ble for problems or damages resulting
from suchmisuse.Refer to the enclosed
"Replacement PartsManual" to identify
compressoras single stage or two-stage.
Safety Guidelines
This manual contains information that is
very important to know and understand.
This information isprovided for SAFETY
and to PREVENTEQUIPMENTPROB-
LEMS.To help recognize this informa-
tion, observe the following symbols.
Danger indicates
ardous situation which, ff not avoided,
will result in death or serious injury.
I_WARNINGI Warningindicates
ardous situation which, if not avoided,
could result in death or serious injury.
an imminently haz.
a potentially haz-
Caution indicates a
[_CAUTIONI potentiallyhaz-
ardous situation which, if not avoided,
MAY result in minor or moderate
injury.
Notice indicates
I NOTICE l importantinforma-
tion, that if not followed, may cause
damage to equipment.
Unpacking
After unpacking the unit, inspect care-
fully for any damage that may have
occurred during transit. Make sureto
tighten fittings, bolts, etc., before
putting unit into service.
I WARNINGI Donotoperete
during shipping, handling or use.
Damage may result in bursting and
causeinjury or property damage.
General Safety
Since the air compressorand other
components (material pump, spray
guns, filters, lubricators, hoses, etc.)
used make up a high pressure pump-
ing system, the following safety pre-
cautions must be observed at all times:
included with this
product carefully.
la amnu1
Bethoroughly
familiar with the controls and the
proper use of the equipment.
2. Follow all local electrical and safety
codes as well as the United States
National Electrical Codes (NEC) and
Occupational Safety and Health Act
(OSHA).
3.Only personswellacquaintedwith
theserulesofsafeoperationshould
be allowedto usethe compressor.
4.Keep visitorsaway and NEVER
allowchildreninthe work area.
5.Wear safetyglassesand use
hearingprotectionwhen operating
the unit.
unit if damaged
Breathable Air Warning
This compressor/pump isNOT
equipped and should NOT be used
"as is" to supply breathing quality
air. For any application of air for
human consumption, you must fit
the air compressor/pump with suit-
able in-line safety and alarm equip-
ment. This additional equipment is
necessary to properly filter and puri-
fy the air to meet minimal specifica-
tions for Grade D breathing as
described in Compressed Gas
Association Commodity
Specification G 7.1 - 1966, OSHA 29
CFR1910. 134, and/or Canadian
Standards Associations (CSA).
DISCLAIMER OF WARRANTIES
In the event the compressor is used
for the purpose of breathing air
application and proper in-line safety
and alarm equipment is not simulta-
neously used, existing warranties
are void, and the company disclaims
any liability whatsoever for any
loss, personal injury or damage.
6. DO not stand on or usethe unit as
a handhold.
7. Before each use, inspect compressed
air system and electrical components
for signs of damage, deterioration,
weakness or leakage. Repair or
replace defective itemsbefore using.
8. Check all fasteners at frequent
intervals for proper tightness.
I REMINDER: Keep your dated proof of purchase for purposes! Attach it to this manual file it for I
© 2003 Call 1-B00-543-6400 for parts IN254702AV 1/03
Call 1-800-54Z_-0350 for technical assistance
warranty
or
safekeeping.
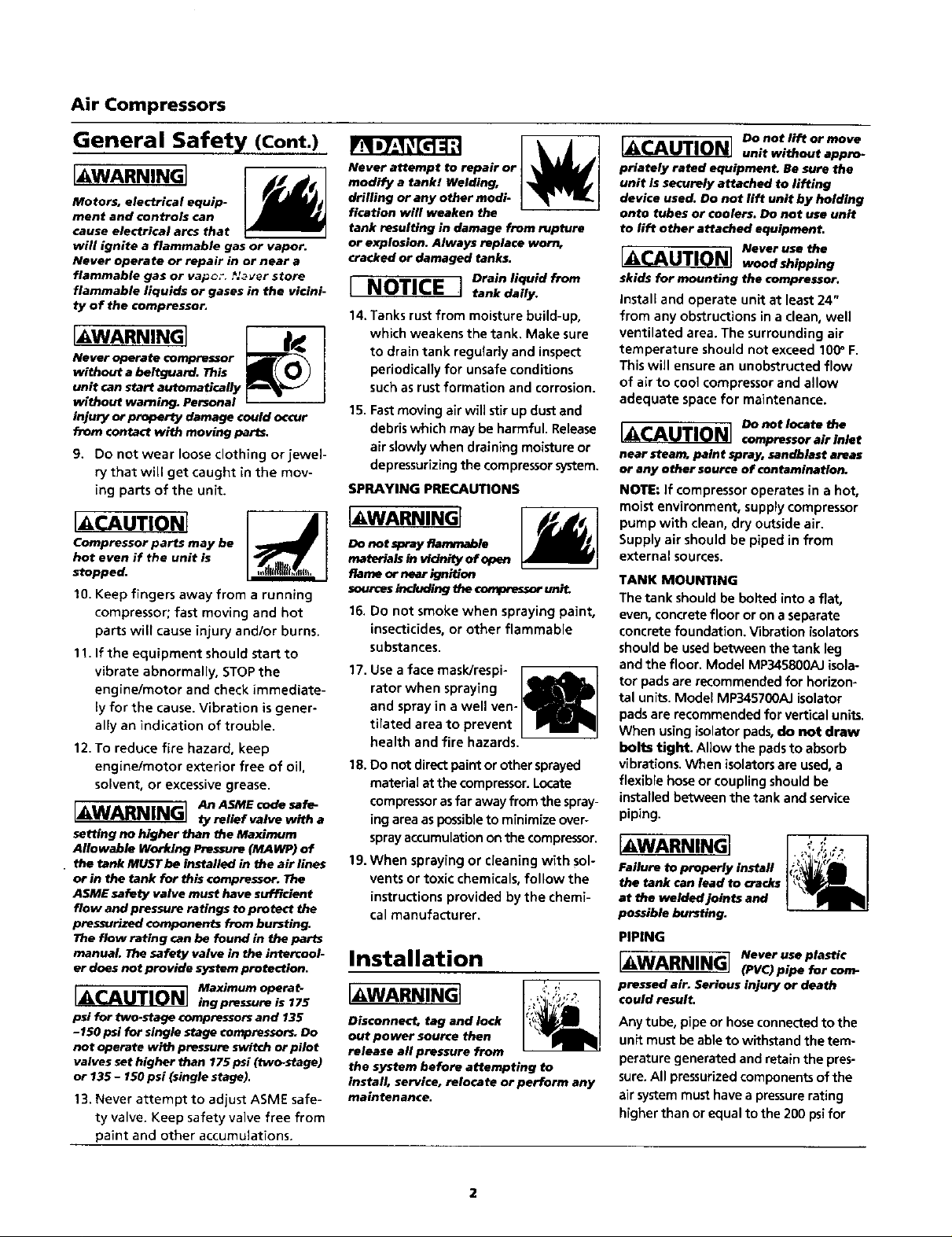
Air Compressors
General Safety (Cont.)
IAWARNINGI
Motors, electrical equip-
ment and controls can
cause electrical arcs that
will ignite a flammable gas or vapor.
Never operate or repair in or near a
flammable gas or yaps;, .AJ_verstore
flammable liquids or gases in the vicini-
ty of the compressor.
I WARNINGI
Never operate compressor
without a beltguard. This m_ Q j
unit can start automatically _Jh._
without warning. Personal
injury or property damage could occur
from contact with moving parts.
9. Do not wear loose clothing or jewel-
ry that will get caught in the mov-
ing parts of the unit.
Compressor parts may be
hot even if the unit is
AI - --0-TI 0 N I
stopped.
10. Keep fingers away from a running
compressor; fast moving and hot
parts will cause injury and/or burns.
11. If the equipment should start to
vibrate abnormally, STOPthe
engine/motor and check immediate-
ly for the cause. Vibration isgener-
ally an indication of trouble.
12. To reduce fire hazard, keep
engine/motor exterior free of oil,
solvent, or excessive grease.
IAWARNINGI AnASME Sa -
setting no higher than the Maximum
Allowable Working Pressure (MAWP) of
the tank MUST be installed in the air lines
or in the tank for this compressor. The
ASME safety valve must have sufficient
flow and pressure ratings to protect the
pressurized components from bursting.
The flow rating can be found in the parts
manual. 7he safety valve in the intercool-
er does not provide system protection.
ty relief valve with a
Maximum operat.
IACAUTIONI ingpre ureis,75
psi for two-stage compressors and 135
-150 psi for single stage compressors. DO
not Operate with pressure switch or pilot
valves set higher than 175 psi (two-stage)
or 135- 150 psi (single stage).
13. Never attempt to adjust ASME safe-
ty valve. Keep safety valve free from
paint and other accumulations.
Never attempt to repair or
modify a tank! Welding,
drilling or any other modi.
fication will weaken the
tank resulting in damage from rupture
or explosion. Always replace worn,
cracked or damaged tanks.
[ NOTICE ] Drainliquidfrom
tank daily.
14, Tanks rust from moisture build-up,
which weakens the tank, Make sure
to drain tank regularly and inspect
periodically for unsafe conditions
such as rust formation and corrosion.
15. Fastmoving air will stir up dust and
debris which may be harmful. Release
air slowly when draining moisture or
depressufizing the compressor system.
SPRAYING PRECAUTIONS
IAWARNINGI
Do not spray flammable
materials in vidnity of open
flame or near ignition
sources including the compressor unil_
16. Do not smoke when spraying paint,
insecticides, or other flammable
substances.
17. Use a face mask/respi-
rator when spraying
and spray in a well ven-
tilated area to prevent
health and fire hazards.
18. Do not direct paint or other sprayed
material at the compressor. Locate
compressor as far away from the spray-
ing area as possible to minimize over-
spray accumulation on the compressor.
19. When spraying or cleaning with sol-
vents or toxic chemicals, follow the
instructions provided by the chemi-
cal manufacturer.
Installation
I_WARNING]
Disconnect. tag and lock
out power source then
release all pressure from
the system before attempting to
install, service, relocate or perform any
maintenance.
[ACAUTION1 _ not lift or move
priately rated equipment. Be sure the
unit is securely attached to lifting
device used. Do not lift unit by holding
onto tubes or coolers. Do not use unit
to lift other attached equipment.
unit without appro.
Never use the
IACAUTIONI .oodshlpplng
skids for mounting the compressor.
install and operate unit at least 24"
from any obstructions in a clean, well
ventilated area. The surrounding air
temperature should not exceed 100 ° F.
This will ensure an unobstructed flow
of air to cool compressor and allow
adequate space for maintenance.
Do not locata the
near steam, paint spray, sandblast areas
or any other source of contamination.
NOTE: If compressor operates in a hot,
moist environment, supply compressor
pump with clean, dry outside air.
Supply air should be piped in from
external sources.
TANK MOUNTING
The tank should be bolted into a flat,
even, concrete floor or on a separate
concrete foundation, Vibration isolators
should be used between the tank leg
and the floor. Model MP345800AJ isola-
tor padsare recommendedfor horizon*
tal units. Model MP345700AJ isolator
padsare recommended for vertical units.
When usingisolatorpads,do not draw
bolts tight. Allow the padsto absorb
vibrations.When isolatorsare used, a
flexible hoseor coupling should be
installed between the tank and service
piping.
[AWARNINGI
Failure to properly install
the tank can lead to cracks
at the welded joints and
possible bursting.
PIPING
IAWARNINGI Neveruseplastic
pressed air. Serious injury or death
could result.
Any tube, pipe or hoseconnected to the
unit must be able to withstand the tem-
perature generated and retain the pres-
sure. All pressurized components of the
air system must have a pressure rating
higher than or equal to the 200 psi for
compressor air inlet
(PVC) pipe for corn-
2
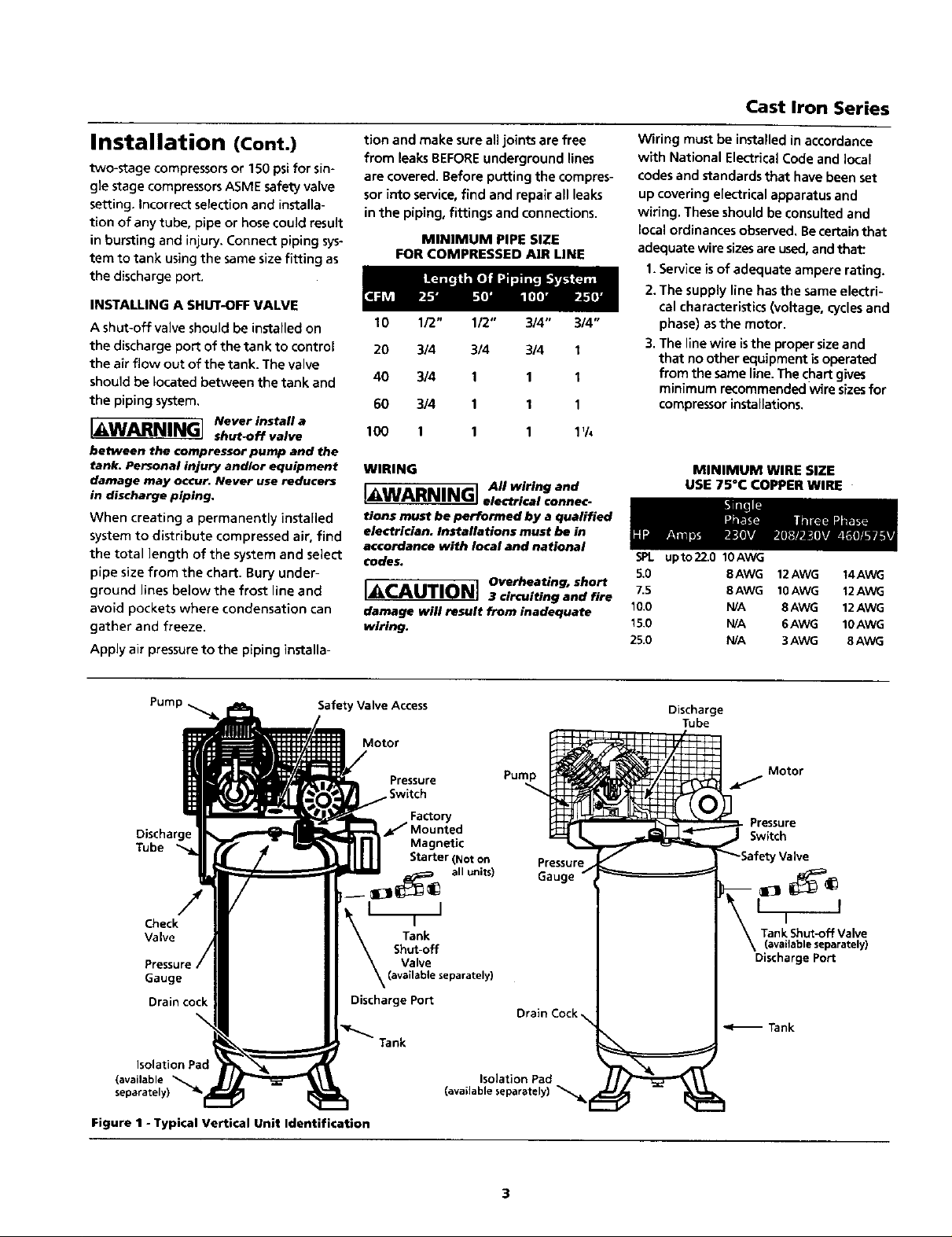
Cast Iron Series
Installation (Cont.)
t_vo-stage compressors or 150 psi for sin-
g]e stage compressors ASME safety valve
setting. Incorrect selection and installa-
tion of any tube, pipe or hose could result
in bursting and injury. Connect piping sys-
tem to tank using the same size fitting as
the discharge port.
INSTALLING A SHUT-OFF VALVE
A shut-off valve should be installed on
the discharge port of the tank to control
the air flow out of the tank. The valve
should be located between the tank and
the piping system.
IAWARNINGI Neverinstalla
between the compressor pump and the
tank. Personal injury andlor equipment
damage may occur. Never use reducers
in discharge piping.
When creating a permanently installed
system to distribute compressed air, find
the total length of the system and select
pipe size from the chart. Bury under-
ground lines below the frost line and
avoid pockets where condensation can
gather and freeze.
Apply air pressure to the piping installa-
shut-off valve
tion and make sure all joints are free
from leaksBEFOREunderground lines
are covered. Before putting the compres-
sorinto service, find and repair all leaks
in the piping, fittings and connections.
MINIMUM PIPE SIZE
FOR COMPRESSED AIR LINE
10 1/2" 1/2" 3/4" 3/4"
20 314 3/4 3/4 1
40 314 1 1 I
60 3/4 1 1 1
100 1 1 1 1'/4
WIRING
[AWADPj,mjr. I All wiring and
tions must be performed by a qualified
electrician. Installations must be in
accordance with local and national
codes.
IACAUTIO- Overheating. short
damage will result from inadequate
wiring.
a_'alaal'_'Wl electrical connec-
3 circuiting and fire
Wiring must be installedin accordance
with National Electrical Code and local
codes and standards that have been set
up covering e[ectrical apparatus and
wiring. These should be consulted and
Eocalordinancesobserved. Becertainthat
adequate wire sizesare used,and that:
1.Serviceisof adequate ampere rating.
2. The supply line has the same electri-
cal characteristics(voltage, cyclesand
phase) asthe motor.
3. The line wire isthe proper sizeand
that noother equipment isoperated
from the sameline.The chartgives
minimum recommended wire sizesfor
compressorinstallations.
MINIMUM WIRE SIZE
USE 75°C COPPER WIRE
5PL upto22.0 10AWG
S.0 8AWG 12AWG t4AWG
7.5 8AWG 10AWG 12AWG
10.0 HA 8AWG 12AWG
15.0 HA 6AWG 10AWG
25.0 HA 3AWG 8AWG
Pump
Discharge
Tube
Safety Valve Access
/
Check
Valve
Gauge
Drain cock
Isolation Pad
(available
separate
Figure 1 - Typical Vertical Unit Identification
Motor
Pressure
,Switch
Factory
_" Mounted
Magnetic
Starter (Not on
_ all units)
__eparately)
Discharge Port
Pump
Pressure Valve
Gauge _
Drain Cock
o__,a, olat o2Pad
Discharge
Tube
Motor
Pressure
Switch
Discharge Port
_<_ Tank
3