
MODEL: KUDOS 6 DUAL FLOW
KUDOS 9 DUAL FLOW
INSTALLATION, OPERATION AND SERVICING INSTRUCTIONS
Calomax Limited
Lupton Avenue, Leeds LS9 7DD
Tel. 0113 249 6681 Fax. 0113 235 0358
e-mail: service@calomax.co.uk www.calomax.co.uk
Please read these
instructions carefully
before operating your
boiler for the first time
Issue 8
09/07/13
DCR 872

Page 3
INTRODUCTION
Thank you for purchasing a Calomax Kudos range boiler. All our
products are designed to give years of simple, reliable operation.
To ensure this, it is important that the installation and subsequent
servicing is carried out by a suitably qualified engineer in
accordance with these instructions.
For assistance in finding a suitable engineer in your area, visit our
website, contact our service department on 0113 249 6681 or
e-mail: service@calomax.co.uk
CHECK LIST
Before commencing installation, check that the following parts have
been supplied with the boiler:
1. WRAS approved flexible water inlet hose suitable for
potable water.
2. Status label
This product conforms to the CE marking directive 93/68/
EEC through compliance with the following standards:
Electromagnetic Compatibility Directive
Low Voltage Directive 73/23/EEC in accordance with:
BS EN 60335-2-63:1993
Compliance with these standards has been confirmed through
testing by an independent NAMAS approved body
Calomax products have been tested and found to comply with the
requirements of the Water Supply (Water Fittings) Regulations 1999
for England and Wales Water Bylaws 2000, Scotland and the Water
Regulations Ireland.
APPROVALS

Page 4
LOCATION
COLD WATER INLET
INSTALLATION
All metalic components of the machine, in direct contact with drinking
water are manufactured from high quality 304 grade stainless steel, or
non ferrous materials, providing maximum resistance to corrosion.
CONSTRUCTION
To comply with recommendations from the
health and safety executive it is important
that due consideration be given to safe
operation of the controls of the boiler.
The boiler should therefore be mounted
in such a manner that the operator can
stand directly facing the machine with the
controls at a recommended height from the
floor to the draw-off tap handle of 1200mm
+/- 100mm. Consideration should also
be given to the servicing requirements
of the machine. The maximum and
minimum ambient operating conditions
must be between 5 °C and 35 °C. The appliance is not suitable for
installation where a water jet could be used. Install the boiler on a
surface suitable for near boiling temperatures and the working weight
of the boiler. Allow adequate clearance for ventiation and for the easy
removal of the outer casing lid and left hand side panel panel. Calomax
ltd recommend a minimum clearance of 50mm on all sides of the boiler
except the left hand side which requires minimum fo 150 mm clearance
for maintenance. A suitably qualified engineer must install this unit.
Plumbing and electrical installation work is involved.
To comply with the U.K. Water Supply Regulation a single check-
valve
must be fitted to the supply.
The boiler must be installed in a location where access is restricted to
operators that are suitably trained, or where untrained operators of the
machine can be supervised by trained personnel.

Page 5
MODEL
A B C
DRY
WEIGHT
WORKING
WEIGHT
KUDOS 6
KUDOS 9
mm 745 380 275 21 Kg 48 Kg
ALL DIMENSIONS ARE APPROXIMATE
DIMENSIONS AND WEIGHTS
BEFORE CONNECTING, THE SUPPLY PIPE MUST BE
THOROUGHLY FLUSHED OUT TO ENSURE THAT FOREIGN
MATTER DOES NOT BLOCK OR ENTER THE SOLENOID VALVE
The boiler must be connected to a potable water supply using the
food grade hose provided, in a manner which complies with UK water
regulations. The hose should be connected to a ½” (15mm) drinking
water supply via an appropriate isolating valve. The supply must
provide a constant pressure of between 20 KPa and 1000 KPa (0.2 to
10 Bar).
If the water supply contains excessive solids in suspension it is
recommended that a fine mesh “in line” water filter is fitted in the pipe
VENT & OVERFLOW
The vent / overflow pipe must be extended and laid with a
continuous
fall,
discharging to a safe and visible point. The pipe should not be
directly connected to a closed waste, as taste problems may occur and
should never be allowed to become blocked or restricted.15mm copper
or ‘Speedfit’ pipe should be used. If the machine is operated without

Page 6
ELECTRICAL CONNECTIONS
Kudos6 Dual-flow boilers require fixed wiring to the rear terminal block.
A means of disconnection must be provided in which at least 3mm
seperation between the live and neutral poles of the supply exists.
Kudos9 Dual-flow boilers require fixed wiring to a 3 phase 4 wire supply in
which at least 3mm seperation exists in the three phases of the supply (but
not the neutral).
The installation of a residual current device (RCD) having a rated residual
operating current not exceeding 30 mA is advisable.
USER INSTRUCTIONS
During normal operation some external parts will become
very hot, particularly the tap body. Care must be taken to
avoid injury, a burn or scald.
Commissioning
Turn on the water supply and then switch on the electrical supply.
The Wait/Ready light will flash yellow and the unit will pulse with water
(8L/Min). When water reaches the normal operating level sensor, the
solenoid will be disabled and the element will be energised. When a
band of water around the draw off tap has reached the normal operating
temperature, the Wait/Ready light will show solid yellow colour (indicating
water available). The elements will remain energised until the full capacity
has reached normal operating temperature, indicated by the wait/ready
light turning to solid a orange colour.
Subsequent Use
After the boiler has finished the commissioning cycle and water is drawn
from the tap, water will be replaced in pulses automatically by the solenoid
the overfill pipe being extended as advised, any subsequent damage
incurred will be the responsibility of the installer.

Page 7
The element(s) may be also be energized at the same time. If water is
drawn from the machine but boiling water is still available, the Wait/Ready
light will be illuminated solid yellow. If full draw off capacity is removed the
boiler may cool, indicated by the Wait/Ready light flashing yellow.
Note:
When the green service indicator light on the front of the boiler is showing
solid colour, the header tank sensor has been starved of water for in
excess of 30 seconds and the bottom thermistor has been disabled. To
reinstate normal operation the water supply needs to be re-applied.
If the service indicator light flashes, this indicates that the water level has
reached the high level sensor and the likelihood is that the normal level
sensor requires de-scaling, or the machine has over-filled due to debris
trapped in the solenoid valve.The debris can be removed by drawing plenty
of water from the dispense tap, causing the solenoid valve to operate and
flush out the obstruction. The machine will reset itself once the problem has
cleared. If this does not rectify the problem, turn off the water supply and
remove the flexible hose to check for debris in the valve’s filter. When the
service light is flashing, the element is disabled and the boiler may cool.
For further assistance, contact our service department on 0113 249 6681,
or e-mail service@calomax.co.uk.
The production of scale is a natural phenomenon and commonly occurs
in hot water systems. The nature of the scale produced and its rate of
formation varies widely throughout the country.
To ensure continuous, reliable operation, the boiler should be regularly descaled by a suitably qualified engineer. Suitable chemical de-scalants must
only be used if the manufacturers recommendations are strictly adhered
to. This is to prevent health and safety issues, taste problems and potential
damage to the appliance. Misuse of such chemicals is not covered by the
product warranty.
The Kudos range of boilers benefit from an integral scale inhibitor. This
is not a scale eliminator and its effects will differ according to the water
quality in your area. To ensure trouble free operation, periodically check
for scale inside the boiling chamber. The production of scale is a natural
phenomenon and some de-scaling may be required within the first 12
months. This is not covered under the products warranty as it is not a fault.
SCALE

Page 8
CLEANING
GENERAL
NOTES
GENERAL OPERATION
• Hold a cup below the tap or place large vessels on the drip tray.
Care must be taken to avoid injury through splashing or over-filling.
• To begin filling, pull the handle forward or push it backward – hot
water begins to flow. If the tap is opened fully it can be locked open
(for filling large vessels) in this state the boiler must never be left
unattended.
• To stop filling, release the handle so it returns to the closed
position. AS STANDARD THIS BOILER IS FITTED WITH
AN EXTENDED NOZZLE DESIGNED FOR FILLING LARGE
VESSELS. DUE TO THIS, WATER WILL CONTINUE TO FLOW
FOR SEVERAL SECONDS AFTER THE TAP HAS BEEN
CLOSED NEVER PASS YOUR HAND BENEATH THE NOZZLE.
• Please retain these instructions for future reference
• Ensure that a suitable drip tray is positioned below the tap nozzle.
This will help keep the surrounding work surfaces and floor free
from drips or splashes. Various options are available and are
outlined on the Accessories page of this booklet (page 9).
• All de-scaling and servicing must be performed by a suitably
qualified engineer.
Avoid using any abrasive materials. Wiping the outer casing
with a damp cloth should be sufficient. Some stainless
steel cleaning products may not be suitable for plastic and
must not come in contact with the plastic fascia. Always
disconnect the electrical supply before cleaning.
NEVER USE A SPRAY JET OR ANY OTHER METHOD WHICH COULD
CAUSE WATER TO ENTER THE ELECTRICAL CHAMBER.

Accessories
Worktop-mounting Stainless
Steel drip tray
Ref. SSDTK
(freestanding)
Wall-mounting bracket
(for boiler)
Ref. KWMBK
Stainless Steel drip tray for
Wall-mounting bracket
(above)
Ref. KWMBDTK
(free standing)
KWMBDTWDK
(with drain outlet)
SSDTWDK
(with drain outlet)
Boiler securing clamp
(To fix boiler to a worktop)
Ref. KC14MM
(To suit all Kudos models unless stated otherwise)

Ingredient caddy
Ref. IC3 (3 bay) -
as shown
Shelf unit
(For storing cups / saucers etc.)
Ref. SHU
Back panels
(To conceal water & electrical connections)
REF. K9BAC
for Kudos6 Dual Flow &
Kudos9 Dual Flow)
IC4 (4 bay)

For more information visit our website at www.calomax.co.uk or call 0113 249 6681
Water filter kit
(To reduce taste & odour problems)
Ref. CWFK
Filter Cartridge
(Replacement filter for kit shown above)
Ref. CWFC1

Page 12
When the green service indicator light on the front of the boiler is
showing solid colour, the header tank sensor has been starved of
water for in excess of 30 seconds and the bottom thermistor & bottom
element(s) have been disabled. To reinstate normal operation the water
supply needs to be re-applied.
If the service indicator light flashes, this indicates that the water
level has reached the high level sensor and the likelihood is that the
normal level sensor requires de-scaling, or the machine has overfilled due to debris trapped in the solenoid valve.The debris can be
removed by drawing plenty of water from the dispense tap, causing
the solenoid valve to operate and flush out the obstruction. The
machine will reset itself once the problem has cleared. If this does not
rectify the problem, turn off the water supply and remove the flexible
hose to check for debris in the valve’s filter. When the service light is
flashing, the element is disabled and the boiler may cool. For further
assistance, contact our service department on 0113 249 6681, e-mail
service@calomax.co.uk. or find a local service engineer at
www.calomax.co.uk
Access to internal components can be gained by the removal
of the outer casing lid and left hand side panel. Once the outer
casing is removed, access to the Service Area has been gained.
This access must be restricted to persons having knowledge and
practical experience of the appliance, in particular as far as safety
and hygiene are concerned.
De-scale
To gain access to internal components, the body lid must be removed.
Break the lid gasket seal and lift it clear of the body.
Note: Whenever the body lid has been removed from the boiler a new
lid gasket may be required to ensure a steam-tight joint. Damage to the
unit caused by a poor lid seal is not covered by warranty.
SERVICE INSTRUCTIONS
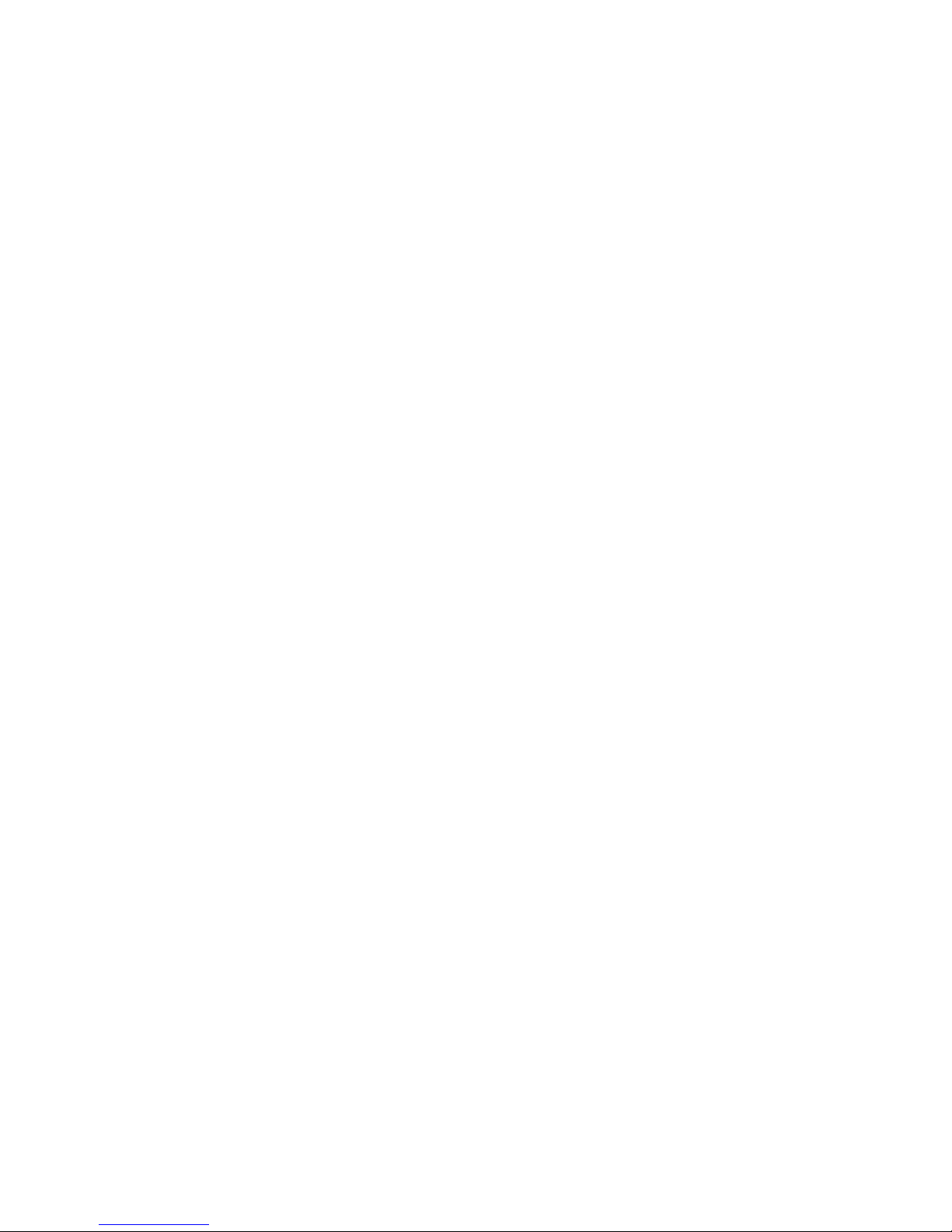
Page 13
Scale deposits should be removed from all internal surfaces,
particularly the heating element, thermistors and level sensors by
gently tapping or scraping. If the deposits are soft, use a nylon
pad and flush out. Abrasive cleaning materials containing scouring
powders and detergents must not be used, such materials can
cause taste problems.
Suitable chemical de-scalants must only be used in accordance
with the manufacturers recommendations. This will prevent health
and safety issues, taste problems and potential damage to the
appliance. All trace of these chemicals must be removed before recommissioning the unit. Misuse of such chemicals is not covered by
the product warranty.
IMPORTANT Bef
ore re-commissioning the boiler it is
important that all scale and moisture is removed from the level
sensors and insulating gaskets, to avoid a false signal being
transmitted through the scale to the boiler body. Failure to
remove this scale and/or moisture could cause the sensor to
indicate to the PCB that water is covering the element, whether
or not water is present. In this situation the PCB could energise
the element causing failure. If in doubt, protect the element by
hand filling with water to the level of the draw-off tap before
switching on the electrical supply to the boiler.
General function
The printed circuit board (PCB) controls the heating and filling
functions of the boiler by monitoring the thermistors and level
sensors. The PCB also controls the external light unit to indicate
the current state of the boiler. Red and yellow LED’S on the circuit
board indicate whether the PCB has energised the elements or
solenoid respectively.
Should an element fail and need to be replaced, it may be

Page 14
necessary to replace the lid gasket to ensure a reliable steam-tight
seal. Note: the elements have a permanent ‘Live’ feed, and the
‘Neutrals’ are switched.
Printed Circuit Board replacement (PCB)
In the event of a PCB failing and a replacement being required, full
instructions will be supplied. It is important to note however, that the
Triac PCB’s must be securely mounted against the copper heatsinks to ensure reliable heat dissipation. Heat transfer compound is
also supplied with all replacement circuit boards.
Adjusting the Water Temperature Set Point
The temperature potentiometer (Pot) is pre-set at Calomax and
will only require adjustment in exceptional circumstances. Contact
Calomax for advice.
Water boils at different temperatures depending on barometric
pressure. The temperature should not be tuned higher than 98
°C, or
over boiling may occur during low barometric pressure conditions,
causing the unit to trip the overheat cut-out device.

Exploded parts view
Kudos6
Dual Flow
(To be read in conjunction with the spare parts list)
1
2
5
*
Fitted as standard. Items 3, 4
or 5 available as alternatives
Houses item 23
Includes thermistor pocket, all
washers & nuts
6
7
9
8
11
13
15
17
19
20
24
21
22
**
*
**
12
18
3
*
11
†
†
†
If parts required
are not identified,
please contact
Calomax Limited
13
Part
10
10
16
Part
25

Exploded parts view
Kudos9
Dual Flow
(To be read in conjunction with the spare parts list)
1
2
5
*
Fitted as standard. Items 3, 4
or 5 available as alternatives
Houses item 23
Includes thermistor pocket, all
washers & nuts
6
7
9
8
11
14
15
17
19
20
24
21
22
**
*
**
12
18
3
*
11
†
†
†
If parts required
are not identified,
please contact
Calomax Limited
14
Part
10
10
16
10
Part
25

Page 17
Spare parts are usually available ex-stock.
Please quote Model & Serial Number.
TBT TN2CK TN3CK
CBTSCBTCWKTTKNK
KSVNBE3HKCBTSS
K6PCBT KUDTC
DRAW OFF TAP
BODY
TAP BODY HEAT
SHIELD
SLOW-FILL NOZZLE FAST-FILL NOZZLE
TAP TOP ASSEMBLYEXTENDED
FAST-FILL NOZZLE
TAP CUP WASHER TAP SPRING
TAP SLOTTED
STEM
3kW ELEMENT THERMISTOR
ASSEMBLY KIT
SOLENOID VALVE
PRINTED CIRCUIT
BOARD-6kW Inc.TRIACS
MANUAL RESET
THERMAL CUTOUT
1 2 3 4
8765
9 10 11 12
16151413
UTHS
KR
RELAY
K9PCBT
PRINTED CIRCUIT
BOARD-9kW Inc.TRIACS
X1
TAKE
X1

Page 18
NB: Not to scale.
Spare parts are usually available ex-stock.
Please quote Model & Serial Number.
17 18 19 20
24232221
NBPRG
KDFLPCBAKDFPMFK
BODY LID
GROMMET
WATER LEVEL
CONTROL PIPE
WATER INLET
HOSE
PLASTIC FASCIA FOR
DUAL FLOW BOILERS
LIGHT PCB FOR DUAL
FLOW BOILERS
KTSK
TANK SENSOR KIT
NB15BLG KWTLG
BODY LID GASKET WATER TANK
GASKET
KUDIHB
INTERNAL HOSE
ASSEMBLY
(K6/DF & K9/DF)
25
KWLCPK
FIH (1m)
IH2M (2m)
WATER INLET
HOSE
WIH (1m)
26
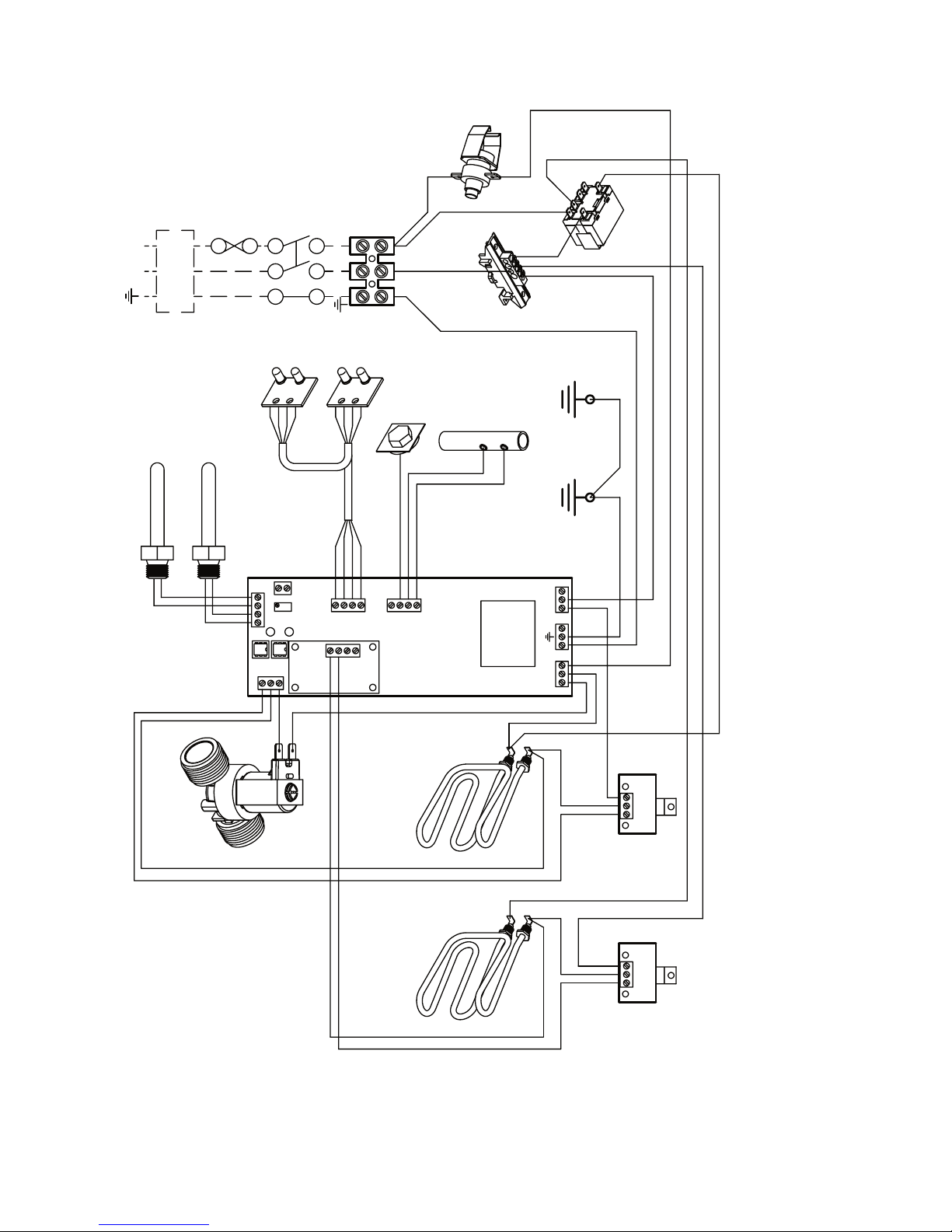
Page 19
NB: Not to scale.
Wiring Schematic for Kudos-6 Dual Flow Water Boiler
RED
YELLOW
BLACK
BLUE
PINK
BROWN
ORANGE
NO CONNECTION
BLACK
RED
YELLOW
WHITE
BLACK
BLACK
RED
N L
BLUE
L
N
BLACK
YELLOW / GREEN
YELLOW / GREEN
RED
RED
COLD WATER INLET
SOLENOID VALVE
TOP
ELEMENT
TRIAC PCB
HIGH
NORMAL
TANK
SENSOR
LEVEL
SENSING
PIPE
HEATER
LED
SOLENOID
LED
BOTTOM THERMISTOR
THERMAL
CUTOUT
EARTH ON
INTERNAL PANEL
EARTH
ON BODY
TOP THERMISTOR
NO
CONNECTION
BLUE
BLUE
BLUE
RED
BOTTOM
ELEMENT
TRIAC PCB
RELAY
NEUTRAL
BLOCK
RCD
INCOMING SINGLE
PHASE SUPPLY
THROUGH A
DOUBLE POLE
ISOLATING SWITCH,
FUSE AND
(RECOMMENDED)
RCD DEVICE
HAVING A RATED
OPERATING
CURRENT NOT
EXCEEDING 30mA
L
N
LIGHT PCBs
(TRANSPARENT
LIGHT
UPPER-MOST IN
FASCIAS)
WHITE SHEATHING
ORANGE
ORANGE
RED
RED
BLACK
YELLOW / GREEN
BLACK
BLACK
RED

Wiring Schematic for Kudos-9 Dual Flow Water Boiler
RED
YELLOW
BLACK
BLUE
PINK
BROWN
ORANGE
NO CONNECTION
BLACK
RED
YELLOW
WHITE
BLACK
BLACK
RED
N L
BLUE
N
BLACK
YELLOW / GREEN
YELLOW / GREEN
RED
RED
COLD WATER INLET
SOLENOID VALVE
TOP
ELEMENT
TRIAC PCB
HIGH
NORMAL
TANK
SENSOR
LEVEL
SENSING
PIPE
HEATER
LED
SOLENOID
LED
BOTTOM THERMISTOR
THERMAL
CUTOUT
EARTH ON
INTERNAL PANEL
EARTH
ON BODY
TOP THERMISTOR
NO
CONNECTION
BLUE
BLUE
BLUE
RED
MIDDLE
ELEMENT
TRIAC PCB
RELAY
NEUTRAL
BLOCK
RCD
INCOMING THREE
PHASE SUPPLY
THROUGH A TRIPLE
POLE ISOLATING
SWITCH, FUSES AND
(RECOMMENDED)
RCD DEVICE HAVING
A RATED
OPERATING
CURRENT NOT
EXCEEDING 30mA
L
3
N
BOTTOM
ELEMENT
TRIAC PCB
L
2
L
1
L
3
L
2
L
1
RED
RED
RED
2
4
6
8
YELLOW / GREEN
LIGHT PCBs
(TRANSPARENT
LIGHT
UPPER-MOST IN
FASCIAS)
WHITE SHEATHING
ORANGE
ORANGE
PINK
PINK
BLACK BLACK
BLACK
BLACK
BLACK

Page 21
BASIC TROUBLE SHOOTING
Symptoms Possible Cause Remedy
No boiling water
available
Broken tap top
Normal level sensor
holding signal
Thermal cut-out
tripped (no light)
Element failed
Replace tap top (or component)
De-scale
Reset and check for faults
Replace element
Thermal cut-out
trips regularly
Excessive internal scale. (See
‘De-Scale’ page 12)
Faulty wiring to thermistors /
faulty thermistors
Temperature controller needs
adjusting
Element failed to earth
Defective Printed Circuit Board
De-scale the boiler
(Particularly thermistors)
Repair / replace as required
Lower operating temperature
Replace element
Replace Circuit Board
Overflows
Dirt in solenoid valve.
Level sensors require descaling or replacing
Printed circuit board faulty
Clean solenoid filter / or replace
solenoid, “work the boiler” -see
Service Instructions (page 12).
De-scale / replace sensors
Replace P.C.B

Page 22
NB: Not to scale.
SERVICE HISTORY AND NOTES

Page 23
Calomax have manufactured water boilers in the UK for over 50
years. We are proud of our products and the back-up service we
provide
Properly maintained and serviced, a Calomax boiler should last
many years and we have no hesitation in providing a full 12
months (mainland U.K.) parts and labour warranty for all models.
Please complete and return the enclosed product registration form
as soon as possible to activate this, or register online at www.
calomax.co.uk .
In addition, the Clipper, Kudos and Quantum models carry an
additional 12 month back to base warranty.
Some factors are beyond our control and would invalidate the
warranty offered. These include:
Incorrect installation
High / Low water pressure
Incorrect voltage supply
Accidental damage
Limescale build-up
The last item can be a particular problem for water dispensing
equipment in hard-water areas. All hot water equipment should be
serviced and de-scaled by approved organisations on a regular
basis to avoid a damaging build-up of limescale.
Although our boilers incorporate scale-inhibitor technology, we
recommend that a taste, odour and scale filter should be fitted
where appropriate.
Please visit our website www.calomax.co.uk for details of our
Service Partner Network and the range of filters and accessories
available
WARRANTY GUARANTEE (UK Mainland customers only)

Page 24
Model
Serial Number
Draw off Capacity
22 Litres
Heat-up Time
(First fill to - K6/DF
full capacity) - K9/DF
31 Minutes
23 Minutes
Average Flow
rate from tap
Extended nozzle
Fast flow nozzle
Slow flow nozzle
8.5 Litres / Minute
6 Litres / Minute
3.5 Litres / Minute
Voltage - K6/DF
- K9/DF
220 - 240 V ac 50-60 Hz 1 PHASE
415 V ac 50-60 Hz 3 PHASE
Power rating - K6/DF
- K9/DF
6kW (MAX)
9kW (MAX)
Note: All measurements are approximate.
PLEASE ENTER MODEL AND SERIAL NUMBER FOR
FUTURE REFERENCE
PLEASE CONTACT OUR SERVICE DEPARTMENT FOR ASSISTANCE
Calomax Limited, Lupton Avenue, Leeds LS9 7DD
Tel: 0113 249 6681
Fax: 0113 235 0358
e-mail: service@calomax.co.uk