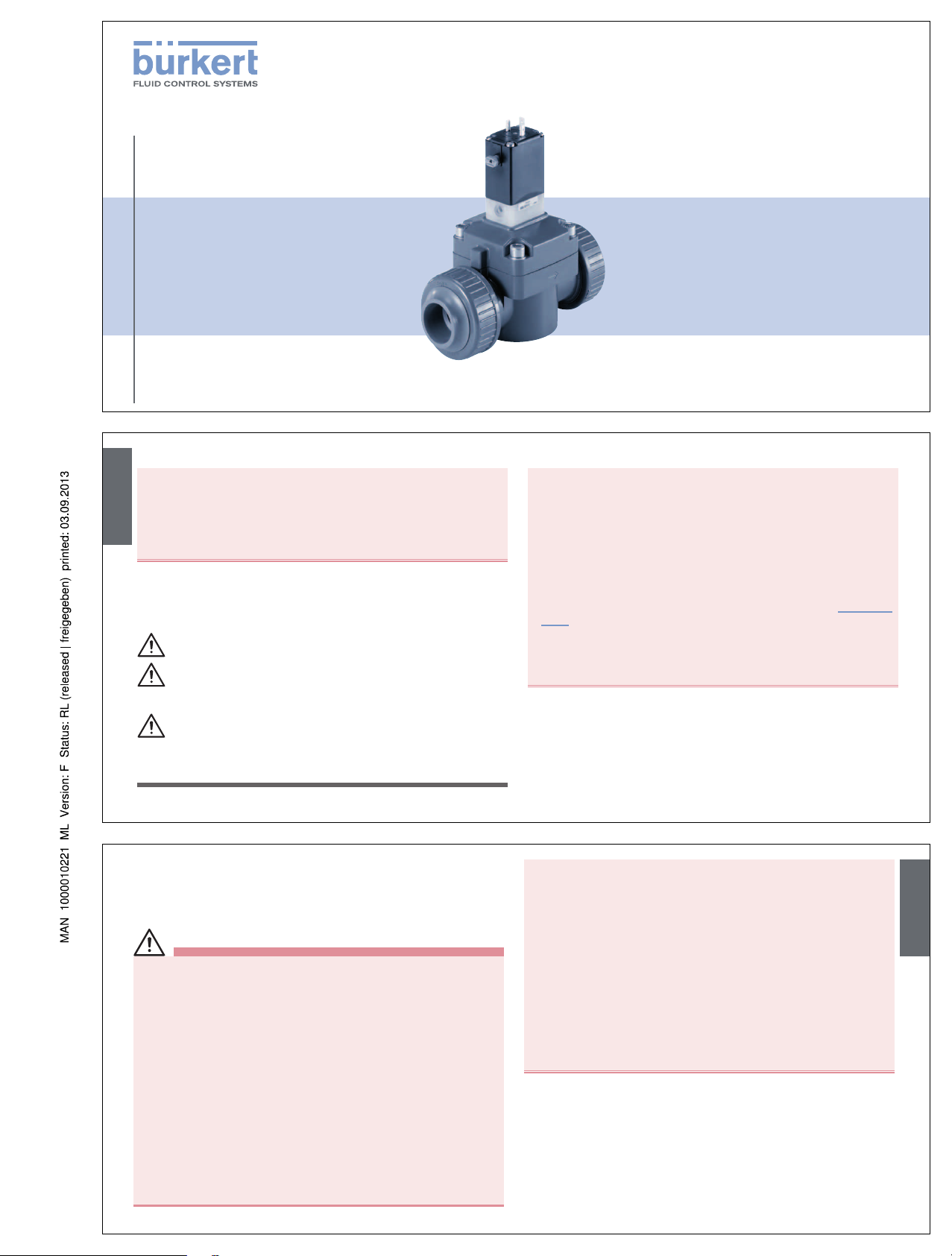
Bedienungsanleitung
Manuel d‘utilisation
Operating Instructions
Type 0142
Magnetventil
2/2-Way Solenoid Valve
2/2-Wege-Magnetventil
Électrovanne à 2/2 voies
Address / Adresse
Germany / Deutschland / Allemagne
Bürkert Fluid Control Systems
Sales Center
Christian-Bürkert-Str. 13-17
D-74653 Ingelfingen
Tel. + 49 (0) 7940 - 10 91 111
Fax + 49 (0) 7940 - 10 91 448
E-mail: info@de.buerkert.com
International
www.burkert.com → Bürkert → Company → Locations
Manuals and data sheets on the Internet:
www.burkert.com
Bedienungsanleitungen und Datenblätter im Internet:
www.buerkert.de
Manuel d'utilisation et fiches techniques sur Internet :
www.buerkert.fr
© 2013 Bürkert Werke GmbH
Operating Instr uctions 1307/04_EU-ml_00893140 / Original
DE
1. OPERATING INSTRUCTIONS
The operating instructions contain important information.
• Read the instructions carefully and follow the safety instructions in
particular, and also observe the operating conditions.
• Instructions must be available to each user.
• The liability and warranty for Type 0142 are void if the operating
instructions are not followed.
2. SYMBOLS
→ designates a procedure which you must carry out.
Warning of serious or fatal injuries:
Danger!
In case of imminent danger.
Warning!
In case of potential danger.
Warning of minor or moderately severe injuries:
Caution!
Warns of damage to property:
note!
3. INTENDED USE
Non-authorized use of the solenoid valve type 0142 may be a
hazard to people, nearby equipment and the environment.
• The device is designed to control, shut off and meter neutral and
aggressive media up to a viscosity of 21 mm
2
/s.
• Provided the cable plug is connected and installed correctly, e.g.
Bürkert type 2508, the device satisfies protection class IP65 in
accordance with DIN EN 60528 / IEC 60529.
• Use according to the permitted data, operating conditions and conditions of use specified in the contract documents and operating
instructions. These are described in the chapter entitled “Technical
data”.
• Correct transportation, correct storage and installation and careful
use and maintenance are essential for reliable and problem-free
operation.
• Use the device only as intended.
3.1. Restrictions
If exporting the system/device, observe any existing restrictions.
english
Risk of short-circuit/escape of media through leaking screw
joints.
• Ensure seals are seated correctly.
• Carefully screw valve and connection lines together.
To prevent injury, ensure that:
• Do not make any external modifications to the device bodies. The
system cannot be activated unintentionally.
• Installation and repair work may be carried out by authorized technicians only and with the appropriate tools.
• After an interruption in the power supply or pneumatic supply, ensure
that the process is restarted in a defined or controlled manner.
• Do not put any loads on the body.
• The device may be operated only when in perfect condition and in
consideration of the operating instructions.
4. BASIC SAFETY INSTRUCTIONS
These safety instructions do not make allowance for any contingencies and events which may arise during installation, operation and
maintenance.
Danger – high pressure!
• Before loosening the lines and valves, turn off the pressure and
vent the lines.
Risk of electric shock!
• Before reaching into the system, switch off the power supply and
secure to prevent reactivation!
• Observe applicable accident prevention and safety regulations for
electrical equipment.
Risk of burns/Risk of fire if used continuously through hot
device surface!
• Keep the device away from highly flammable substances and media
and do not touch with bare hands.
Risk of injury due to malfunction of valves with alternating
current (AC).
Sticking core causes coil to overheat, resulting in a malfunction.
• Monitor process to ensure function is in perfect working order.
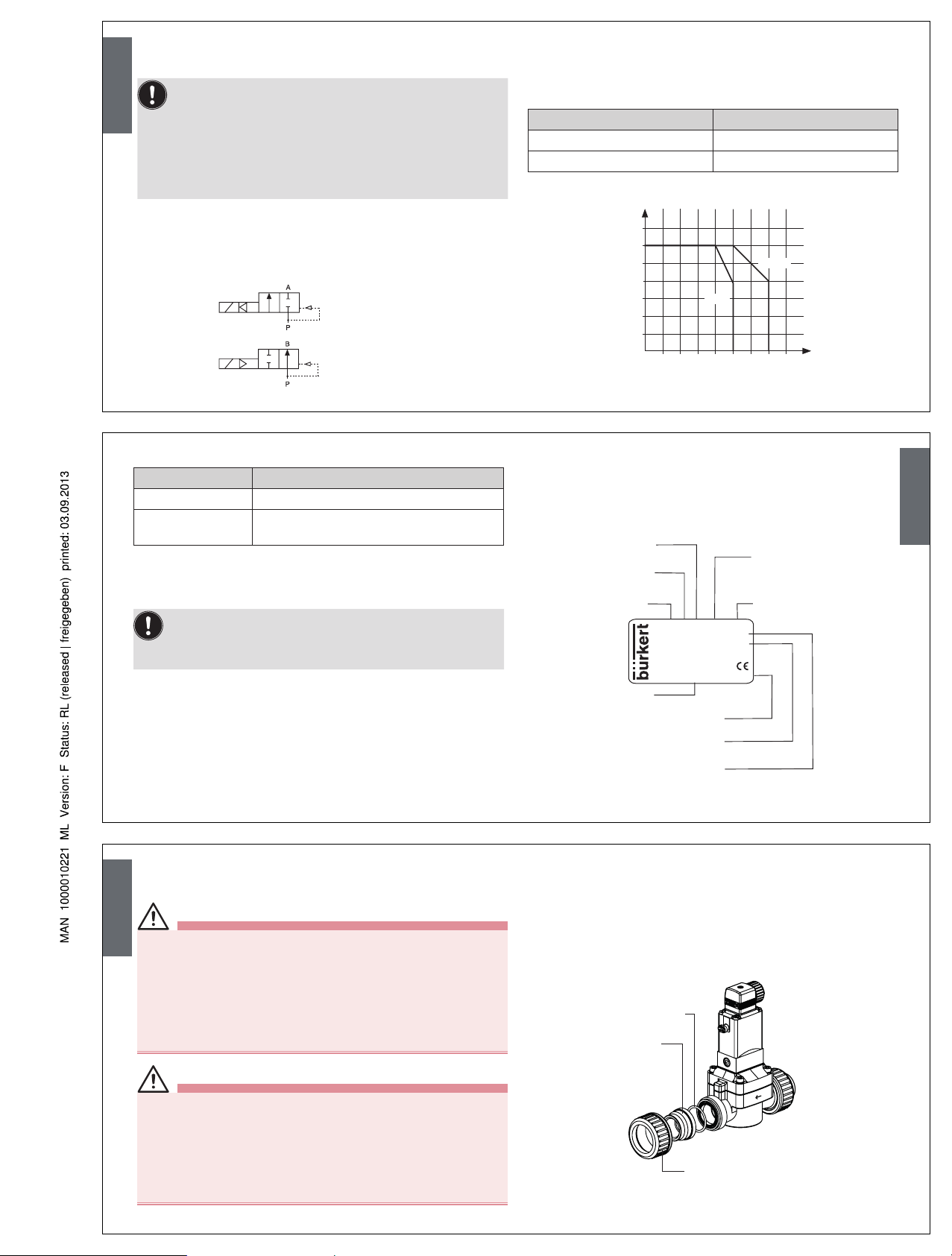
5. TECHNICAL DATA
5.1. Operating conditions
The following values are indicated on the type label:
• Voltage (Tolerance ± 10 %) / Current type
• Coil power consumption (active power in W - at operating temp.)
• Pressure range
• Body material
PVC (PV) or PVDF (PD)
• Seal material
FKM, EPDM
Protection class: IP65 with accordance with DIN EN 60529 /
IEC 60529 with cable plug, e. g. Bürkert Type
2508
Operating principle:
A (NC)
2/2-way valve, normally
closed
B (NO)
2/2-way valve, normally
opened
5.2. Application conditions
Ambient temperature: PVC 0 - +40 °C
PVDF 0 - +55 °C
Permitted medium temperature depending on body material:
Body material Medium temperature
PVC 0 °C ... +50 °C
PVDF 0 °C ... +70 °C
Pressure - Temperature Diaphragm for PVC and PVDF:
10 20 30 4050607080
1
2
3
4
5
6
7
PVC
PVDF
Temperature [°C]
Pressure [bar]
english
Permitted media depending on seal material:
Seal material Permitted media
FKM Oxidizing acids and substances, water
EPDM Alkalis, alkaline washing and bleaching lyes,
water, oil- and grease-free media
Operating duration
Unless otherwise indicated on the type label, the solenoid system is
suitable for continuous operation.
Important information for functional reliability during continuous
operation!
If standstill for a long period at least 1-2 activations per day
are recommended.
Service life
High switching frequency and high pressures reduce the service life.
5.3. Conformity
In accordance with the EC Declaration of conformity, the solenoid valve
Type 0142 is compliant with the EC Directives.
5.4. Standards
The applied standards, which verify conformity with the EC Directives,
can be found on the EC Type Examination Certificate and / or the EC
Declaration of Conformity.
5.5. Type label
Typ e
Operating
principle
Orifice
Seal material
Body material
Id. Number
Manufacture-Code
Voltage, Frequency, Power
consumption
Connection thread, Nominal
pressure
0142 A 20,0 FKM PV
Made in Germany
00042005
W17MG
230V 50-60Hz 5W
025 P
N 0,5 - 6 bar
6. INSTALLATION
6.1. Safety instructions
Danger!
Risk of injury from high pressure in the equipment!
• Before loosening the lines and valves, turn off the pressure and
vent the lines.
Risk of injury due to electrical shock!
• Before reaching into the system, switch off the power supply and
secure to prevent reactivation!
• Observe applicable accident prevention and safety regulations for
electrical equipment!
Warning!
Risk of injury from improper installation!
• Installation may be carried out by authorized technicians only and
with the appropriate tools!
Risk of injury from unintentional activation of the system and
an uncontrolled restart!
• Secure system from unintentional activation.
• Following installation, ensure a controlled restart.
6.2. Before installation
Installation position: any, actuator preferably upwards.
Procedure:
→ Check pipelines for dirt and clean.
→ Install a dirt filter before the valve inlet (≤ 500 µm).
6.3. Installation
Insert O-ring
Insert
Tighten union nut - evenly by
hand only
english
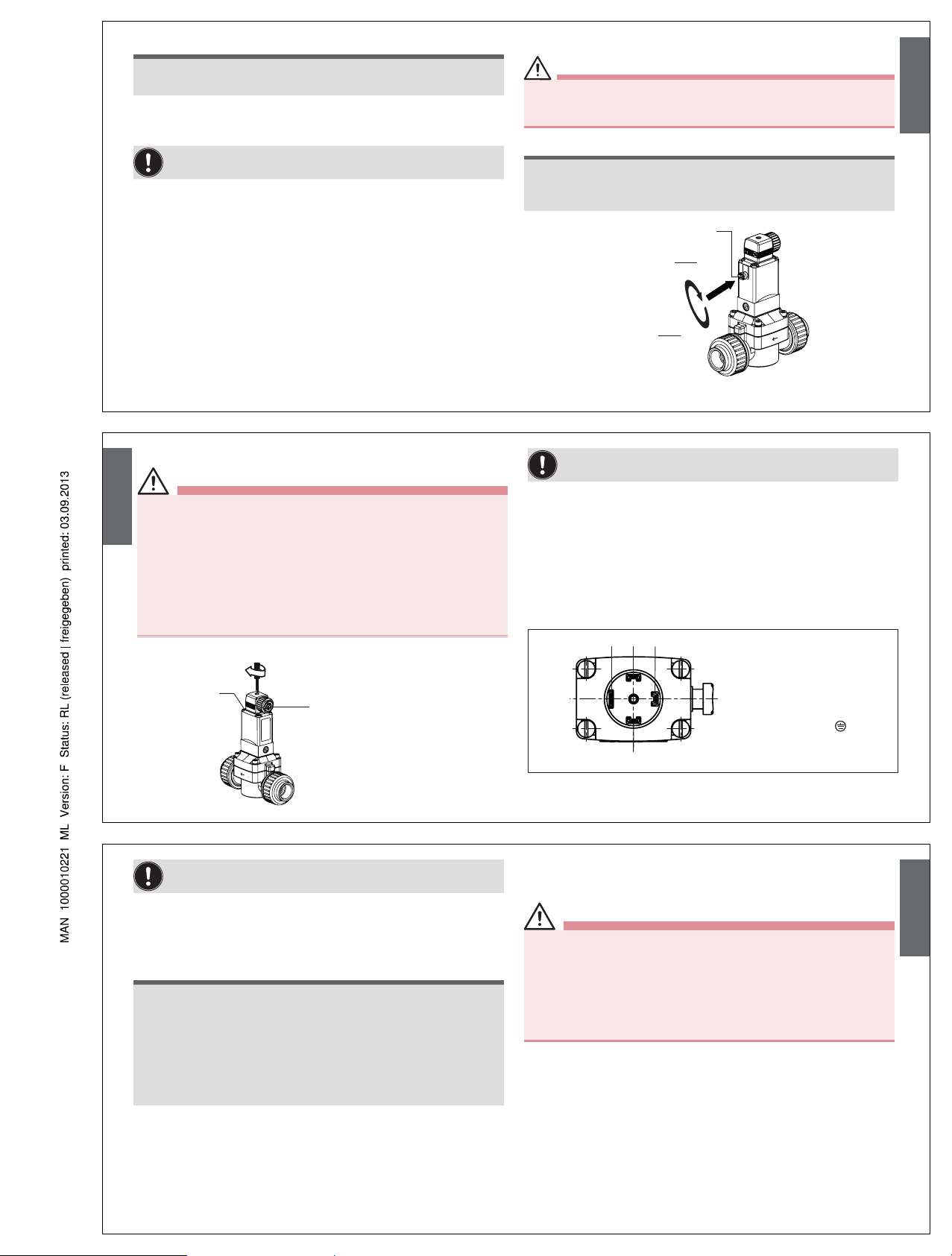
note!
Caution risk of breakage!
• Do not use the coil as a lifting arm.
→ Body with welded sleeve: Use PVDF.
→ Body with bonded sleeves: Use Tangit special adhesive.
Valve body must not be installed under tension.
→ Observe direction of flow:
The arrow on the body indicates the direction of flow (no function
in opposite flow direction).
6.4. Manual emergency actuation
Caution!
Discharge of medium due to loss of the O-rings!
• If the O-rings are lost, the valve will leak. Medium may be
discharged.
note!
Caution!
• When the manual emergency actuation is locked, the valve can no
longer be actuated electrically.
Manual emergency
actuation
Press
Turn
1
2
6.5. Electrical connection of the cable plug
Warning!
Risk of injury due to electrical shock!
• Before reaching into the device / equipment switch off the power
supply and secure to prevent reactivation!
• Observe applicable accident prevention and safety regulations for
electrical equipment!
If the protective conductor contact between the coil and body is
missing, there is danger of electrical shock!
• Always connect protective conductor.
• Check electrical continuity between coil and body.
Authorized cable plug e.g.
Type 2508 or other suitable
cable plug in accordance with
DIN EN 175301-803 Form A
Seal
max. 1 Nm
Note the voltage and current type as specified on the type
label.
Procedure:
→ Tighten cable plug (for permitted types see data sheet), observing
max. torque 1 Nm.
→ Check that seal is fitted correctly.
→ Connect protective conductor and check electrical continuity
between coil and body.
6.5.1. Electrical connection - Pulse
DC connections:
Terminal 1 = closed +
Terminal 2 = open +
Terminal 3 = GND Protective conductor
connection
24 3
1
english
The connection terminals in the cable plug are identified with
the numbers 1 to 3 according to the terminals on the valve.
Procedure:
→ Connect the pulse valves (variable code CF 02).
→ For direct current versions connect negative terminal to terminal 3.
note!
Important information:
• Avoid emitting pulses simultaneously to both coil windings.
• Do not switch any other consumers (relays, etc.) at the same time
as the terminals.
• The coil connection, to which voltage is not applied, must be galvanically isolated (open).
• If two or more valves are switched in parallel, ensure that this
requirement is met by using 2-pole or multi-pole switches.
7. MAINTENANCE, TROUBLESHOOTING
7.1. Safety instructions
Warning!
Risk of injury from improper maintenance!
• Maintenance may be carried out by authorized technicians only
and with the appropriate tools!
Risk of injury from unintentional activation of the system and
an uncontrolled restart!
• Secure system from unintentional activation.
• Following maintenance, ensure a controlled restart.
7.2. Malfunctions
If malfunctions occur, check:
→ the device has been installed according to the instructions,
→ the electrical and fluid connections are correct,
→ the device is not damaged,
→ all screws have been tightened,
→ the voltage and pressure have been switched on,
→ the pipelines are clean.
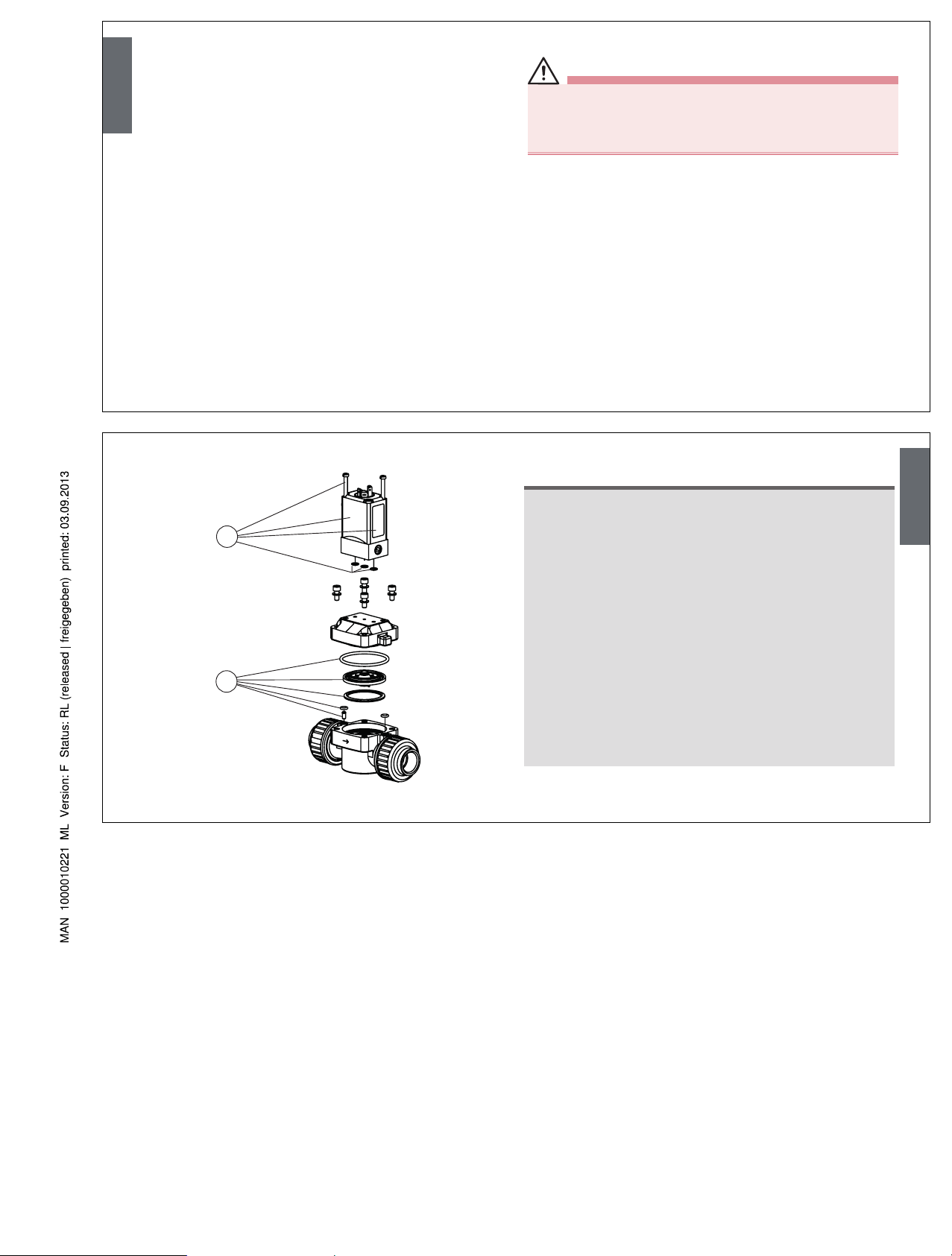
Valve does not switch
Possible cause:
• Short-circuit or coil interrupted.
• Medium pressure outside the permitted pressure range.
• Manual emergency actuation locked.
Valve does not close
Possible cause:
• Internal space of the valve is dirty.
• Manual emergency actuation locked.
• Flow restrictor (valve inlet) or pilot holes (valve inlet / outlet) dirty.
8. SPARE PARTS
Caution!
Risk of injury and/or damage by the use of incorrect parts!
Incorrect accessories and unsuitable spare parts may cause injuries
and damage the device and the surrounding area.
• Use only original accessories and original spare parts from Bürkert.
8.1. Ordering spare parts
Order the spare-part sets specifying the positions (Pos. 1: Pilot
control set, Pos. 2: Wearing part set) and the identification number of
the device.
english
8.2. Overview of spare parts
1
2
9. TRANSPORT, STORAGE, DISPOSAL
note!
Transport damages!
Inadequately protected equipment may be damaged during
transport.
• During transportation protect the device against wet and dirt in
shock-resistant packaging.
• Avoid exceeding or dropping below the allowable storage
temperature.
• Protect
electrical interfaces of the coil and the pneumatic connec
-
tions from damage with protective caps.
Incorrect storage may damage the device.
• Store the device in a dry and dust-free location!
• Storage temperature: -10 °C ... +50 °C (PVC)
-10 °C ... +70 °C (PVDF).
Damage to the environment caused by device components
contaminated with media.
• Observe applicable regulations on disposal and the environment.