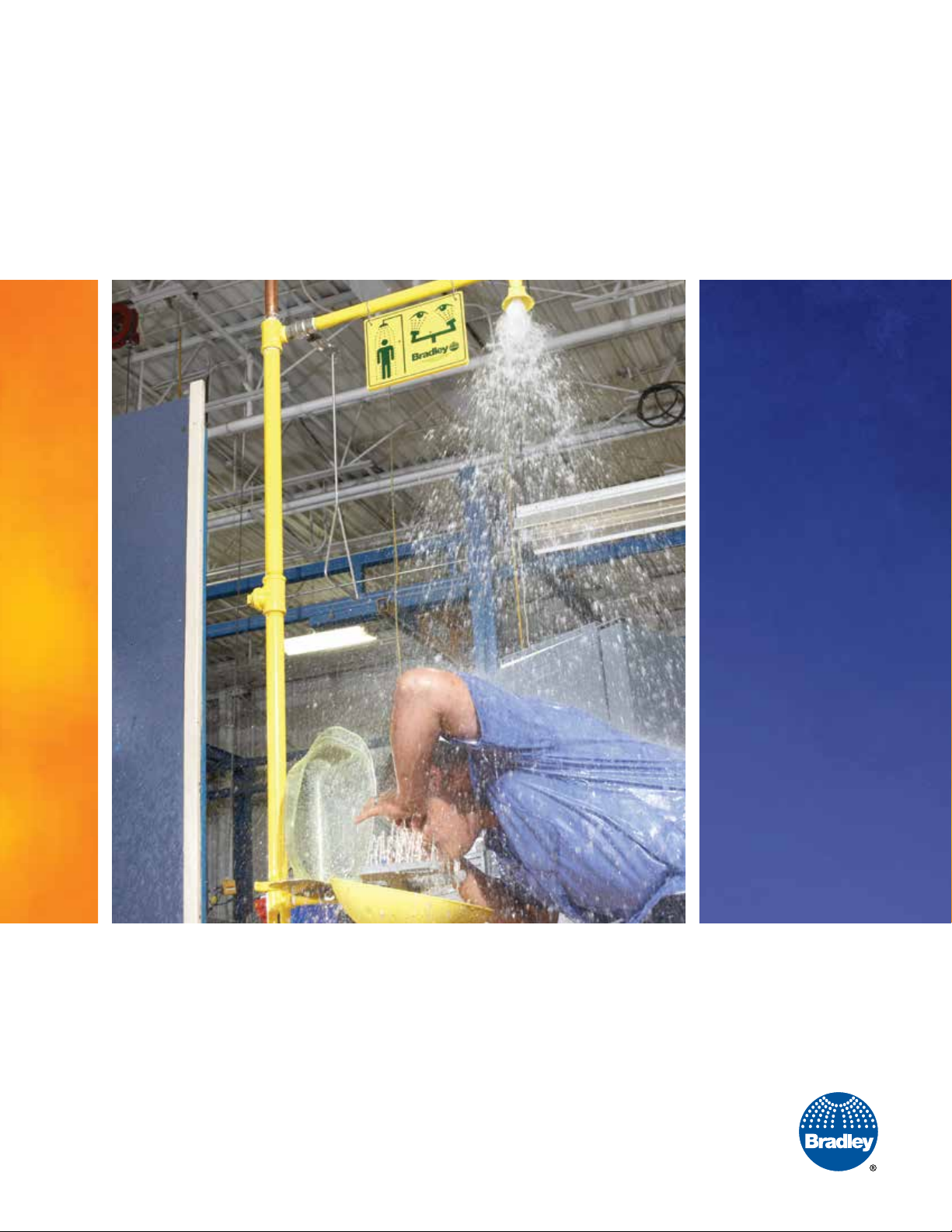
ANSI/ISEA Z358.1-2014
Quick Compliance Guide
BRADLEYCORP.COM
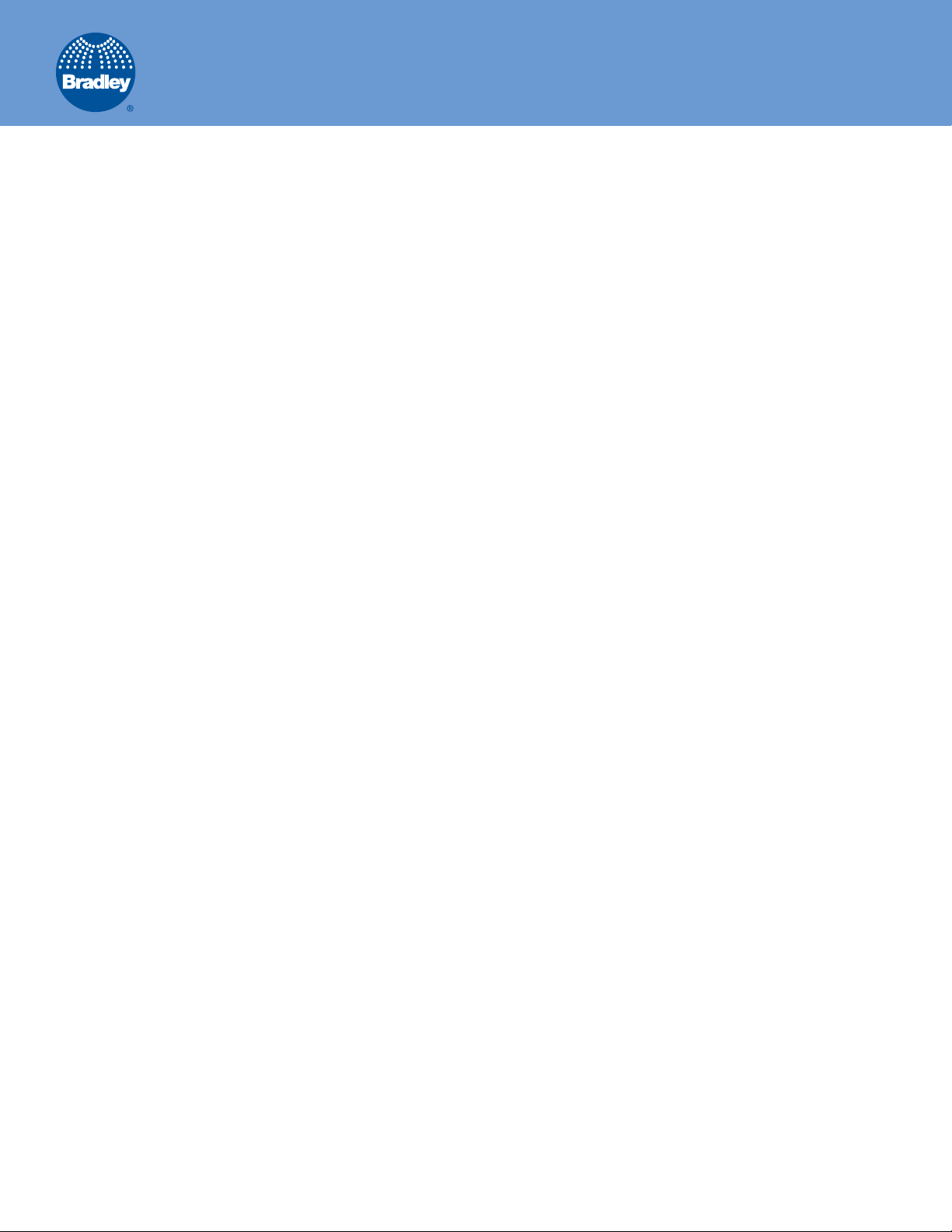
Quick Compliance Guide
This guide serves as a supplement to the ANSI/ISEA Z358.1-2014 standard.
Important Information
About Compliance
The U.S. Code of Federal Regulations 29CFR 1910.151 states:
“Where the eyes or body of any person may be exposed to
injurious or corrosive materials, suitable facilities for quick
drenching or ushing of the eyes and body shall be provided
within the work area for immediate emergency use.”
The American National Standards Institute (ANSI)
establishes standards for minimum performance and use
requirements for eyewash and shower equipment. The
ANSI/ISEA Z358.1-2014 for Emergency Eyewash and Shower
Equipment provides detailed guidelines to which the
Occupational Safety and Health Administration (OSHA),
State OSHA and other regulatory agencies commonly refer.
The Joint Commission 2009 EC Standard for Hospitals
requires: “The hospital takes action to minimize or
eliminate identified safety and security risks in the
physical environment.” Furthermore, hospitals are
required to “Minimize risk associated with selecting,
handling, storing, transporting, using, and disposing
hazardous chemicals.” Surveyors commonly refer to OSHA
requirements and the ANSI Standard for further guidance
on best demonstrated practices.
Canadian Provincial authorities also typically refer to
ANSI standards when auditing for or advising proper
requirements for emergency eyewash showers.
Safety Considerations
Personal Wash Unit
ANSI standards allow a personal wash unit (ie. Bottled
Eyewash) to be used as a supplement to the compliant
ANSI/ISEA Z358.1 xtures outlined in this guide. While
supplemental xtures (single head drench hoses, bottle
eyewash) serve an important function in highly toxic,
hazardous environments, it is important to remember they
do not provide the same protection as ANSI compliant
drench showers, eye or eye/face washes. (Appendix A1)
First Aid Practices
Prior to the occurrence of an accident, consult with a
physician or other professional for guidance in regards
to common and specic work place hazards that may be
present in your facility. Refer to Safety Data Sheets (SDS)
for specic type of ush required (eyewash, eye/face or
combination drench) given the hazards in the environment.
Provide access to a physician or other medical professional
immediately after an accident occurs. (Appendix A2)
Waste Disposal
Few consider the ramications of hundreds of gallons of
pooling ushing uid in the area surrounding drench showers
and eyewashes. It’s important to have a plan in place for
the disposal of the ushing uid, whether one opts for
the installation of drains in new construction facilities or
dedicated waste containment systems. Pooling uid creates
slip hazards, and presents a safety risk to an impaired worker.
When planning for the disposal of ushing uid, consult your
local ordinances and governing authorities. (Appendix A3)
Personal Protective Equipment
Providing employees with personal protective equipment
(safety glasses, protective suits, etc), in accordance with
OSHA 1910.132(a), is required. It can be challenging to
enforce the use of that protection equipment at all times.
ANSI explicitly states that personal protective equipment
does not replace the role of safety drench showers,
eyewashes, and other safety ushing equipment. These
xtures are intended to treat injuries should PPE prove to
be inadequate or fail. (Appendix A4)
2
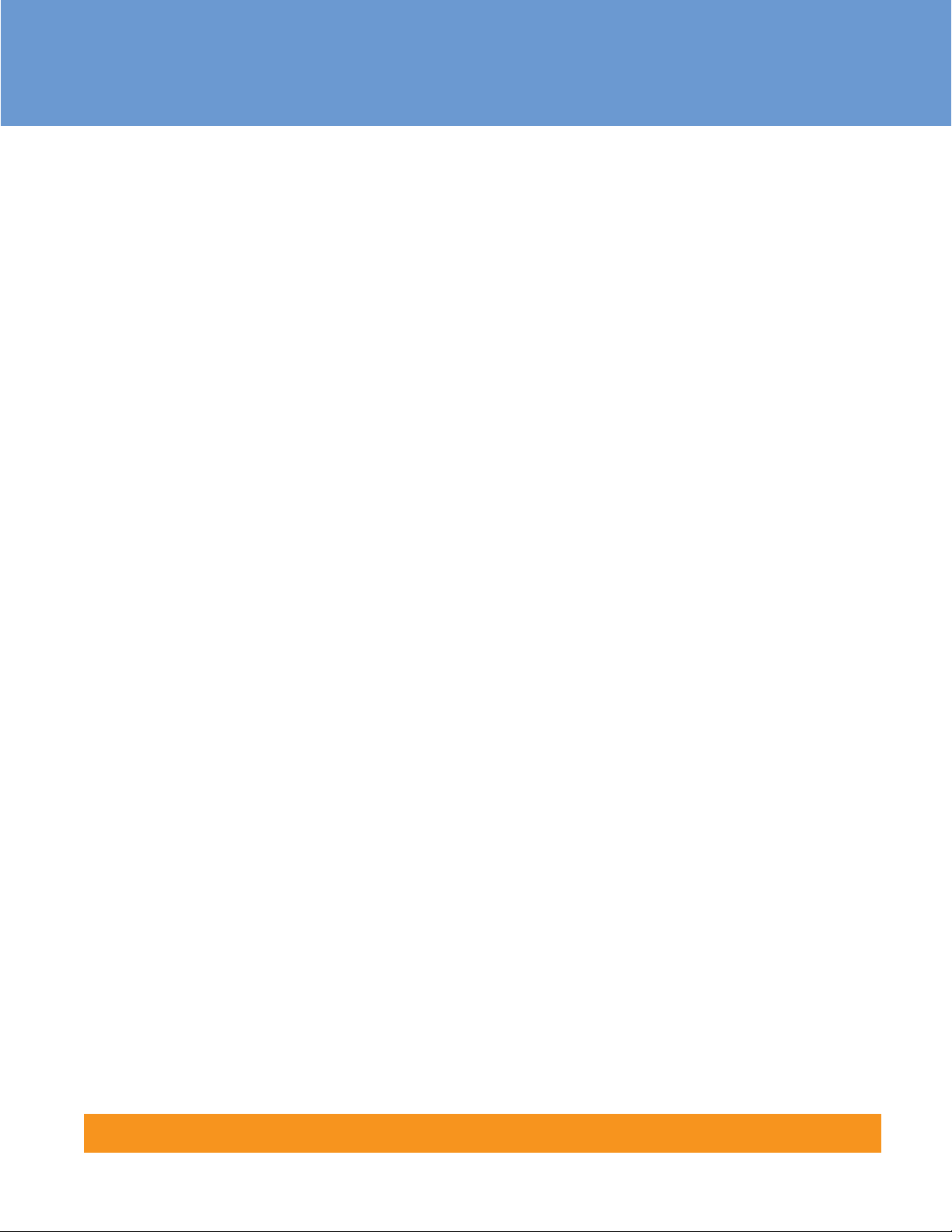
Installation
Supply lines
Each manufacturer provides its own recommendations in
regards to the supply size that’s adequate for each xture. It’s
important to note that by reducing the size of the supply, the
shower’s ability to deliver the ushing uid at the proper rate
with the intended pattern is directly aected. (Appendix B1)
Water Capacity
Compliant safety showers and eyewashes are supplied
with a minimum pressure of 30 psi (207 kPa). Typical
facilities supply their xtures with 45 psi (310 kPa) inlet
supply pressure. Extra care should be taken with any
pressure that exceeds 80 psi (552 kPa). Complicated
site conditions often require the installation of xtures
a signicant distance from the water supply. The owner
and designer are responsible for ensuring that adequate
pressure and ushing uid will be delivered through the
xture even at low points of pressure. (Appendix B2)
Valve Operation
Placement of Emergency Equipment
Safety drench showers, eye and eye/face washes must be
within 10 seconds or 55 feet (16.8 meters) of the hazard.
Fixtures may not be blocked. A door is considered an
obstruction. However, if the contaminant is not hazardous
or corrosive, a single door may be present provided it opens
in the same direction of travel. The door may not have a
locking mechanism, which may prevent the person access to
use the equipment during an emergency. (Appendix B5)
Delivered Flushing Fluid Temperature
Lukewarm (tepid) water is required for the full 15 minute
ush, for a drench shower, eye or eye/face wash. To
encourage injured personnel to continue to ush the entire
15 minutes or longer as needed, the ANSI/ISEA Z358.1-2014
standard indicates that tepid water is required. Tepid is
dened as 60-100ºF (15.6-37.8ºC). Prolonged exposure to
near freezing water has been proven to aect the body’s
ability to maintain body temperature, increasing the risk of
hypothermia. Whenever possible, consult a physician to
determine the recommended temperature based on specic
types hazardous chemicals or material. (Appendix B6)
Valves that remain open are required in order to allow the
injured individual to maximize the use of their hands to
disrobe and ush their eyes. In limited circumstances, an
inspector or other “enforcing authority” may allow a self-
closing ball valve, in school-related laboratory environments,
where the contaminant is “not a serious threat.” (Appendix B3)
Alarm Devices
Systems that provide visual, audible and an auxiliary
connection serve as a great asset that discourages false
activations, and allows medical personnel to locate where
the accident occurred and respond rapidly. (Appendix B4)
FREE Confidential Safety Evaluation • 800.BRADLEY • bradleysafety.com
Weekly Activation
Emergency Drench Showers, Eye and Eye/Face Washes
must be activated one time per week. This activation
ensures that nothing is blocking the flow of the flushing
fluid and eliminates any chance of contamination from
stagnant water. (Appendix B7)
3
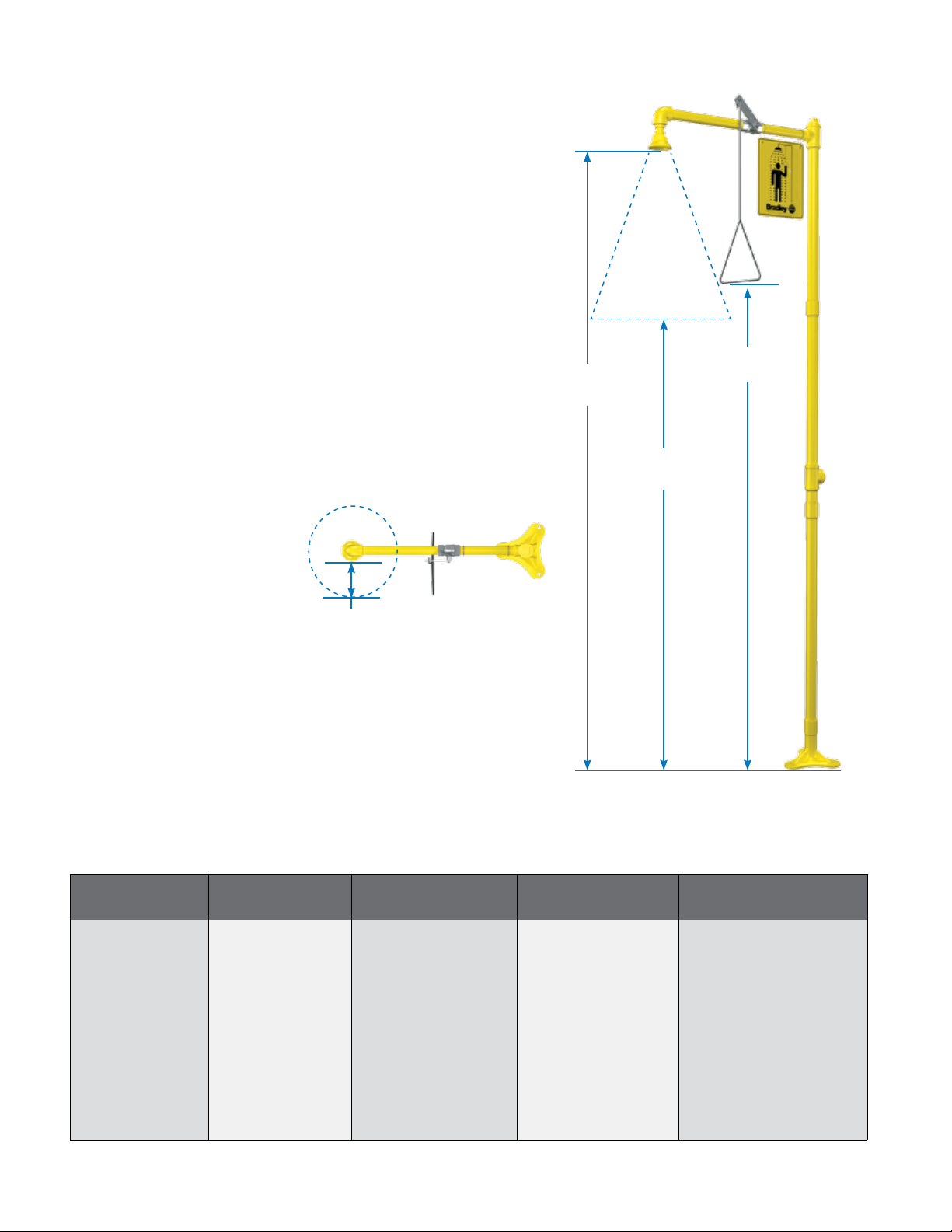
Safety Drench Showers
• Valve mechanism opens in one second or less; it stays open until
manually closed. (Section 4.2)
• Supply with flushing fluid ("potable water, preserved water,
preserved buffered saline solution or other medically acceptable
solution…"). (Definitions, Sections 4.1.1, 4.4.1)
• Locate 10 seconds or 55' (16.8 m) from contaminants or hazardous
materials. Locate on the same plane as hazard and free of
obstructions. (Section 4.5.2, Appendix B5)
• Doors are an obstruction. (Appendix B5)
• Must resist corrosion in the presence of flushing fluid. (Section 4.1.5)
• Audible, visual and central control alarm systems deter vandals and
notify personnel that an accident occurred. (Appendix B4)
• Environmental conditions often require freeze or scald protection
equipment. (Section 4.5.5)
Top down view
(Section 4.1.4, 7)
82–96" (2083–2438 mm)
(Sections 4.1.3, 7)
(Sections 4.1.4, 7)
Spray Pattern
Diameter
20" (508 mm)
69" (1752 mm)
(Sections 4.2, 7)
60" (1524 mm)
Requires a 16" (406 mm)
radius from the center of the
drench shower spray pattern
to be free of obstructions.
(Section 4.1.4)
15-minute Flush Tepid Water
Compliant showers
release a continuous
flow of at least 20
GPM (76 L-MIN) of
tepid flushing fluid
for a period of at
least 15 minutes.
(Sections 4.1.2, 4.4.1,
4.5.5, 4.5.6)
(lukewarm) 60–100°F
(15.6–37.8°C)
encourages full 15
minute flush or until
medical personnel
arrive. (Definitions,
Sections 4.5.6,
Appendix B6)
16" (406 mm)
(Sections
4.1.4, 7)
Manufacturers may
have their safety fixtures
independently evaluated
by a third-party testing
organization. Look
for certification when
selecting a compliant
fixture. (Definitions)
Third-Party
Certifications
Weekly Activations: Annual Inspections
Flush lines and test
by activating weekly.
Inspection tags are often
included with fixtures to
document testing and
to satisfy a safety audit.
(Section 4.6.2)
ANSI recommends a
comprehensive annual
inspection of the facility to
evaluate modified work space,
assess new hazards introduced
into the area, and to identify
fixtures needing replacement
or repair. (Section 4.6.5)
4

Combination Drench Shower, Eye and Eye/Face Washes
• Valve mechanism opens in one second or less; it stays open until
manually closed. (Sections 4.2, 5.2, 6.2, 7.1.1, 7.1.2, 7.1.3)
• Drench shower and eye or eye/face wash must operate simultaneously. (Section 7.4.4)
• Supply with flushing fluid ("potable water, preserved water, preserved buffered
saline solution or other medically acceptable solution…”).
(Definitions, Sections 4.1.1, 4.4.1, 5.1.1, 6.1.1, 7.1.2, 7.1.3)
• Locate 10 seconds or 55' (16.8 m) from contaminants or hazardous materials. Locate on
same plane as the hazard, free of obstructions.
(Sections 4.5.2, 5.4.2, 6.4.2, 7.1.1, 7.1.2, 7.1.3, 7.4.2, Appendix B5)
• Must resist corrosion in the presence of flushing fluid
(Sections 4.1.5, 5.1.5, 6.1.5, 7.1.1, 7.1.2, 7.1.3)
• Protect eye and eye/face wash heads from contaminants.
(Sections 5.1.3, 6.1.3, 7.1.2, 7.1.3)
• Flow Rates: Eyewash unit delivers a minimum of .4 GPM (1.5 L-MIN) for 15 minutes.
(Section 5.1.6) Eye/face wash unit delivers a minimum of 3.0 GPM (11 L-MIN) for 15
minutes. (Section 6.1.6)
• Use flow meter to check flow rate; use test gauge to test flow pattern.
(Sections 5.1.8, 5.3.1, 6.1.7, 6.3, 7.1.2, 7.1.3)
• Environmental conditions often require freeze or scald protection equipment.
(Sections 4.5.5, 5.4.5, 6.4.5, 7.1.1, 7.1.2, 7.1.3)
82–96"
(2083–2438 mm)
(Sections 4.1.3, 7)
Spray Pattern
Diameter
20" (508 mm)
(Section 4.1.4, 7)
69" (1752 mm)
(Sections 4.2, 7)
60" (1524 mm)
(Sections 4.1.4, 7)
Top down view
Requires a 16" (406 mm) radius from the
center of the drench shower spray pattern to
be free of obstructions. (Sections 4.1.4, 7.1.1)
Required to be free of obstructions a
minimum of 6" (152 mm) from the outside
of the eye or eye/face wash sprayheads.
(Sections 5.4.4, 6.4.4, 7.1.2, 7.1.3)
Use a Bradley test gauge (Model 269-1444) to
check flow pattern.
Compliant showers release a
continuous flow of at least 20 GPM
(76 L-MIN) of tepid flushing fluid for a
period of at least 15 minutes. (Sections
4.1.4, 4.4.1, 4.5.5, 4.5.6, 7.1.1)
Compliant eye or eye/face wash fixture
releases a continuous flow of flushing
fluid for a minimum of 15 minutes.
(Sections 5.1.6, 5.4.5, 5.4.6, 6.1.6, 6.4.5,
6.4.6, 7.1.2, 7.1.3)
15-minute Flush Tepid Water
16"
(406 mm)
(Sections
4.1.4, 7)
(lukewarm)
60–100°F
(15.6–37.8°C)
encourages full
15-minute flush
or until medical
personnel arrive.
(Definitions,
Sections 4.5.6,
5.4.6, 6.4.6,
Appendix B6)
6" (152 mm)
(Sections
5.4.4, 6.4.4)
Third-Party
Certifications
Manufacturers
may have their
safety fixtures
independently
evaluated by a
third-party testing
organization. Look
for certification when
selecting a compliant
fixture. (Definitions)
(838–1346 mm)
(Sections 5.4.4,
Weekly
Activations:
Flush lines and test
by activating weekly.
Inspection tags are
often included with
fixtures to document
testing and to satisfy
a safety audit.
(Sections 4.6.2, 5.5.2,
6.5.2, 7.5.2)
33–53"
6.4.4)
Annual Inspections
ANSI recommends a
comprehensive annual
inspection of the facility
to evaluate modified work
space, assess new hazards
introduced into the area,
and to identify fixtures
needing replacement or
repair. (Section 7.5.5)
(Section 4.6.5)
5

Eye and Eye/Face Wash Fixtures
• Valve mechanism opens in one second or less; it stays open until
manually closed. (Sections 5.2, 6.2)
• Supply with flushing fluid, ("potable water, preserved water, preserved
buffered saline solution or other medically acceptable solution…”)
Definitions, Sections 5.1.1, 6.1.1)
• Locate 10 seconds or 55' (16.8 m) from contaminants or hazardous
materials. Locate on the same plane as hazard and free of obstructions.
(Sections 5.4.2, 6.4.2, Appendix B5)
• Must resist corrosion in the presence of flushing fluid.
(Sections 5.1.5, 6.1.5)
• Protect eye and eye/face wash heads from contaminants.
(Sections 5.1.3, 6.1.3)
• Flow Rates: Eyewash unit delivers a minimum of .4 GPM (1.5 L-MIN) for
15 minutes. (Section 5.1.6) Eye/face wash unit delivers a minimum of 3.0
GPM (11 L-MIN) for 15 minutes. (Section 6.1.6)
• Use a flow meter to test flow rate; use a test gauge to test flow pattern.
(Sections 5.1.8, 5.3.1, 6.1.7, 6.1.8, 6.3, 6.3.1)
• Audible, visual and central control alarm systems deter vandalism and
alert safety personnel. (Appendix B4)
• Environmental conditions often require freeze or scald protection
equipment. (Sections 5.4.5, 6.4.5)
33–53”
(838–1346 mm)
(Sections 5.4.4, 6.4.4)
Top down view
Required to be free of obstructions
a minimum of 6" (152 mm) from the
outside of the eye or eye/face wash
sprayheads. (Sections 5.4.4, 6.4.4)
Use a Bradley test gauge (Model
269-1444) to check flow pattern.
15-minute Flush Tepid Water
Compliant fixtures
release a continuous
flow of tepid flushing
fluid for a minimum
of 15 minutes.
(Sections 5.1.6, 5.4.5,
5.4.6, 6.1.6, 6.4.5,
6.4.6)
(lukewarm) 60–100°F
(15.6–37.8°C) encourages
full 15 minute flush or
until medical personnel
arrive. (Definitions,
Sections 5.4.6, 6.4.6,
Appendix B6)
Third-Party
Certifications
Manufacturers may
have their safety fixtures
independently evaluated
by a third-party testing
organization. Look
for certification when
selecting a compliant
fixture. (Definitions)
6" (152 mm)
(Sections 5.4.4, 6.4.4)
Weekly Activations: Annual Inspections
Flush lines and test
by activating weekly.
Inspection tags are often
included with fixtures to
document testing and
to satisfy a safety audit.
(Sections 5.5.2, 6.5.2)
ANSI recommends a
comprehensive annual
inspection of the facility to
evaluate modified work space,
assess new hazards introduced
into the area, and to identify
fixtures needing replacement
or repair. (Sections 5.5.2, 5.5.5,
6.5.2, 6.5.5)
6

Dual Head Eye/Face Wash & Drench Hose
• Considered an eye/face wash if it complies with the installation and performance
requirements of the eye/face wash standard. (Sections 6, 8.2.1)
• Single-head drench hoses complement the 15-minute flush provided by a
primary ANSI/ISEA Z358.1 compliant eyewash fixture. (Section 8)
• Valve mechanism opens in one second or less; it stays open until manually closed.
(Sections 6.2, 8.2.1)
• Fixtures compliant as an eye/face wash must remain "on" once activated
(Sections 6.2, 8.2.1)
• Supply with flushing fluid ("potable water, preserved water, preserved
buffered saline solution or other medically acceptable solution…”) (Definitions,
Sections 6.1.1, 8.2.1)
• Locate 10 seconds or 55' (16.8 m) from contaminants or hazardous materials.
Locate on same plane as the hazard, free of obstructions.
(Section 6.4.2, Appendix B5)
• Protect unit heads from contaminants. (Sections 6.1.3, 8.2.1)
• Flow Rates: Eye/face wash unit delivers a minimum of 3.0 GPM
(11 L-MIN) for 15 minutes. (Section 6.1.6, 8.2.1)
• Use a flow meter to test flow rate; use a test gauge to test flow pattern.
(Sections 6.1.7, 6.3, 8.2.1)
Top down view
Required to be free of obstructions
a minimum of 6" (152 mm) from the
outside of the eye or eye/face wash
sprayheads. (Sections 6.4.4, 8.2.1)
Use a Bradley test gauge (Model 269-1444)
to check flow pattern.
15-minute Flush Tepid Water
Compliant fixtures
release a continuous
flow of tepid flushing
fluid for a minimum
of 15 minutes.
(Sections 6.1.6, 6.4.5,
6.4.6, 8.2.1)
(lukewarm) 60–100°F
(15.6–37.8°C) encourages
full 15 minute flush or
until medical personnel
arrive. (Definitions,
Sections 6.4.6, 8.2.1,
Appendix B6)
(Sections 6.4.4, 8.2.1)
Third-Party
Certifications
Manufacturers may
have their safety fixtures
independently evaluated
by a third-party testing
organization. Look
for certification when
selecting a compliant
fixture. (Definitions)
6" (152 mm)
Weekly Activations: Annual Inspections
Flush lines and test
by activating weekly.
Inspection tags are often
included with fixtures to
document testing and
to satisfy a safety audit.
(Sections 6.5.2, 8.2.1,
8.2.4.2)
Distance to oor
33–53” (838–1346 mm)
(Sections 5.4.4, 6.4.4)
ANSI recommends a
comprehensive annual
inspection of the facility to
evaluate modified work space,
assess new hazards introduced
into the area, and to identify
fixtures needing replacement
or repair. (Sections 6.5.5,
8.2.4.5)
7

Laboratory Eye & Eye/Face Wash Fixtures
• Valve mechanism opens in one second or less; it stays open
until manually closed. (Sections 5.2, 6.2)
• Supply with flushing fluid, ("potable water, preserved
water, preserved buffered saline solution or other medically
acceptable solution…”) (Definitions, Sections 5.1.1, 6.1.1)
• Locate 10 seconds or 55' (16.8 m) from contaminants
or hazardous materials.
• Locate on same plane as the hazard, free of obstructions.
(Sections 5.4.2, 6.4.2, Appendix B5)
• Protect unit heads from contaminants. (Sections 5.1.3, 6.1.3)
• Flow Rates: Eyewash unit delivers a minimum of .4 GPM for 15
minutes. (Section 5.1.6) Eye/face wash unit delivers a minimum
of 3.0 GPM (11 L-MIN) for 15 minutes. (Section 6.1.6)
• Use a flow meter to test flow rate; use a test gauge to test flow
pattern. (Sections 5.1.8, 5.3.1, 6.1.7, 6.3)
The Joint Commission 2009 EC Standard for Hospitals requires: “The
hospital takes action to minimize or eliminate identified safety and
security risks in the physical environment.” Furthermore, hospitals are
required to “Minimize risk associated with selecting, handling, storing,
transporting, using, and disposing hazardous chemicals.” Surveyors
commonly refer to OSHA requirements and the ANSI Standard for further
guidance on best demonstrated practices.
Distance to oor
33–53” (838–1346 mm)
(Sections 5.4.4, 6.4.4)
Top down view
Required to be free of obstructions
a minimum of 6" (152 mm) from the
outside of the eye or eye/face wash
sprayheads. (Sections 5.4.4,6.4.4)
Use a Bradley test gauge (Model 269-
1444) to check flow pattern.
15-minute Flush Tepid Water
Compliant fixtures
release a continuous
flow of tepid flushing
fluid for a minimum of
15 minutes. (Sections
5.1.6, 5.4.5, 5.4.6, 6.1.6,
6.4.5, 6.4.6)
(lukewarm) 60–100°F
(15.6–37.8°C) encourages
full 15 minute flush or
until medical personnel
arrive. (Definitions,
Sections 5.4.6, 6.4.6,
Appendix B6)
6" (152 mm)
(Sections 6.4.4, 8.2.1)
Third-Party
Certifications
Manufacturers may
have their safety fixtures
independently evaluated
by a third-party testing
organization. Look
for certification when
selecting a compliant
fixture. (Definitions)
Weekly Activations: Annual Inspections
Flush lines and test
by activating weekly.
Inspection tags are often
included with fixtures to
document testing and
to satisfy a safety audit.
(Sections 5.5.2, 6.5.2)
ANSI recommends a
comprehensive annual
inspection of the facility to
evaluate modified work space,
assess new hazards introduced
into the area, and to identify
fixtures needing replacement
or repair. (Sections 5.5.5, 6.5.5)
8

Self-Contained Eyewash Fixtures
• Eyewash unit delivers a minimum of .4 GPM for 15 minutes.
(Section 5.3.2)
• Valve mechanism opens in one second or less; it stays open
until manually closed. (Section 5.3.2)
• Supply with flushing fluid, ("potable water, preserved
water, preserved buffered saline solution or other medically
acceptable solution…”) (Definitions, Section 5.1.1)
• Locate 10 seconds or 55' (16.8 m) from contaminants or
hazardous materials. Locate on same plane as the hazard, free
of obstructions. (Sections 5.4.2, Appendix B5)
• Use a flow meter to test flow rate; use a test gauge to test
flow pattern. (Section 5.4.7)
• Frigid conditions require the installation of freeze
protection equipment. (Section 5.4.5)
Front View
Top down view
Required to be free of obstructions a minimum
of 6" (152 mm) from the outside of the eyewash
sprayheads. (Sections 5.4.4)
Use a Bradley test gauge (Model
269-1444) to check flow pattern.
6" (15.2 cm)
(Sections 6.4.4, 8.2.1)
15-minute Flush Tepid Water
Third-Party
Certifications
Distance to oor
33–53” (838–1346 mm)
(Sections 5.4.4, 6.4.4)
Weekly Activations: Annual Inspections
Compliant fixtures
release a continuous
flow of tepid flushing
fluid for a minimum of
15 minutes. (Sections
5.1.6, 5.4.5, 5.4.6)
(lukewarm) 60–100°F
(15.6–37.8°C)
encourages full 15
minute flush or until
medical personnel
arrive. (Definitions,
Sections 5.4.6,
Appendix B6)
Manufacturers may
have their safety fixtures
independently evaluated
by a third-party testing
organization. Look
for certification when
selecting a compliant
fixture. (Definitions)
Flush lines and test
by activating weekly.
Inspection tags are often
included with fixtures to
document testing and to
satisfy a safety audit.
(Sections 5.5.2)
ANSI recommends a
comprehensive annual
inspection of the facility to
evaluate modified work space,
assess new hazards introduced
into the area, and to identify
fixtures needing replacement
or repair. (Sections 5.5.5)
9

Enclosed Safety Showers
• Colder ambient temperature may require an enclosure for added
protection. (Section B6)
• Valve mechanism opens in one second or less; it stays open until
manually closed. (Sections 4.2, 5.2, 6.2, 7.1.1, 7.1.2, 7.1.3)
• Drench shower and eye or eye/face wash must operate
simultaneously. (Section 7.4.4)
• Supply with flushing fluid ("potable water, preserved water,
preserved buffered saline solution or other medically acceptable
solution…”). (Definitions, Sections 4.1.1, 4.4.1, 5.1.1, 6.1.1, 7.1.2, 7.1.3)
• Locate 10 seconds or 55' (16.8 m) from contaminants or hazardous
materials. Locate on same plane as the hazard, free of obstructions.
(Sections 4.5.2, 5.4.2, 6.4.2, 7.1.1, 7.1.2, 7.1.3, 7.4.2, Appendix B5)
• Must resist corrosion in the presence of flushing fluid
(Sections 4.1.5, 5.1.5, 6.1.5, 7.1.1, 7.1.2, 7.1.3)
• Protect eye and eye/face wash heads from contaminants.
(Sections 5.1.3, 6.1.3, 7.1.2, 7.1.3)
• Requires a 16" (406 mm) radius from the center of the drench
shower spray pattern to be free of obstructions. (Sections 4.1.4, 7.1.1)
• Required to be free of obstructions a minimum of 6" (152 mm)
from the outside of the eye or eye/face wash sprayheads.
(Sections 5.4.4, 6.4.4, 7.1.2, 7.1.3)
• Flushing fluid height 33–53" (838-1346 mm)
from standing surface. (Sections 5.4.4, 6.4.4, 7)
• Flow Rates: An eyewash delivers a minimum of .4 GPM for 15
minutes (Sections 5.1.6, 7.1.2). An eye/face wash delivers a minimum
of 3.0 GPM (11 L-MIN) for 15 minutes. (Sections 6.1.6, 7.1.3)
• Use flow meter to check flow rate; use test gauge to test flow
pattern. (Sections 5.1.8, 5.3.1, 6.1.7, 6.3, 7.1.2, 7.1.3)
• Use a Bradley test gauge (Model 269-1444) to check flow pattern.
• Environmental conditions often require freeze or scald
protection equipment. (Sections 4.5.5, 5.4.5, 6.4.5, 7.1.1, 7.1.2, 7.1.3)
Top down view
16" (406 mm)
(Sections 4.1.4, 7)
6" (152 mm)
(Sections
5.4.4, 6.4.4)
(Section 4.1.4, 7)
(Sections 4.1.4, 7)
82–96"
(2083–2438 mm)
(Sections 4.1.3, 7)
Spray
Pattern
Diameter
20" (508 mm)
60"
(1524 mm)
69"
(1752 mm)
(Sections 4.2, 7)
15-minute Flush Tepid Water
Compliant showers release a
continuous flow of at least 20 GPM
(76 L-MIN) of tepid flushing fluid
for a period of at least 15 minutes.
(Sections 4.1.4, 4.4.1, 4.5.5, 4.5.6, 7.1.1)
Compliant eye or eye/face wash
fixture releases a continuous flow
of flushing fluid for a minimum of 15
minutes. (Sections 5.1.6, 5.4.5, 5.4.6,
6.1.6, 6.4.5, 6.4.6, 7.1.2, 7.1.3)
10
(lukewarm)
60–100°F
(15.6–37.8°C)
encourages full
15-minute flush
or until medical
personnel arrive.
(Definitions,
Sections 4.5.6,
5.4.6, 6.4.6,
Appendix B6)
Third-Party
Certifications
Manufacturers
may have their
safety fixtures
independently
evaluated by a
third-party testing
organization. Look
for certification when
selecting a compliant
fixture. (Definitions)
Weekly
Activations:
Flush lines and test
by activating weekly.
Inspection tags are
often included with
fixtures to document
testing and to satisfy
a safety audit.
(Sections 4.6.2, 5.5.2,
6.5.2, 7.5.2)
Annual Inspections
ANSI recommends a
comprehensive annual
inspection of the facility
to evaluate modified work
space, assess new hazards
introduced into the area, and
to identify fixtures needing
replacement or repair.
(Section 7.5.5)
(Section 4.6.5)

11

FREE Confidential Safety Evaluation • 800.BRADLEY • bradleysafety.com
262 251 6000
800 BRADLEY bradleycorp.com
W142 N9101 Fountain Boulevard
Menomonee Falls, WI 53051
4055-2.5-0815