
See Warranty on page 8 for important information about commercial use of this product.
Operating Instructions and Replacement Parts List
Please read and save these instructions. Read carefully before attempting to assemble, install, operate or maintain
the product described. Protect yourself and others by observing all safety information. Failure to comply with
instructions could result in personal injury and/or property damage! Retain instructions for future reference.
sional’s Line
fes
The Pro
Engine Driven
Centrifugal Pump
Description
The Blue Angel pumps are general use
centrifugal water pumps. The pump is
equipped with a Viton® seal assembly
that is also compatible with many
agricultural chemicals.
Safety Guidelines
This manual contains information that is
very important to know and understand.
This information is provided for SAFETY
and to PREVENT EQUIPMENT PROBLEMS.
To help recognize this information,
observe the following symbols.
Danger
indicates
an imminently hazardous situation which,
if not avoided, WILL result in death or
serious injury.
Warning
indicates
a potentially hazardous situation which,
if not avoided, COULD result in death or
serious injury.
Caution
indicates a
potentially minor or moderate injury.
Notic
indicates
important information, that if not
followed, may cause damage to
equipment.
General Safety
Information
CALIFORNIA PROPOSITION 65
This
product
or its power cord may contain chemicals
known to the State of California to
cause cancer and birth defects or other
reproductive harm. Wash hands after
handling.
REMINDER: Keep your dated proof of purchase for warranty purposes!
1. Know the pump application,
limitations, and potential hazards.
Read these rules and the instructions
carefully. Failure to follow them could
cause serious bodily injury and/or
property damage.
Never run engine in an
enclosed area. Exhaust gases
contain deadly poisonous
carbon monoxide, which has
no odor or taste.
Do not use to pump flammable
or explosive fluids such as
gasoline, fuel oil, kerosene, etc.
Do not use in flammable and/or
explosive atmospheres. Pump should only
be used with liquids compatible with pump
component materials. Failure to follow
this warning can result in personal injury
and/or property damage.
2. Observe all safety precautions for the
handling of the fuel.
Do not refuel a hot engine. Fuel
spilled on a hot engine could
result in a fire or explosion. Do
not refuel a running engine.
3. Pump should be located and should
rest on a level solid foundation. Do
not suspend pump by means of the
discharge pipe.
Be sure
secure footing so it doesn’t fall over.
4. Do not use torches or apply excessive
heat, fire or flames to this pump as an
explosion may result.
Attach it to this manual or fi le it for safekeeping.
pump is on
BGPS400
A
N
R
C
U
E
S
S
P
A
R
Need
O
G
R
A
M
Y
T
I
L
A
U
Assistance?
Q
Call Us First!
1-888-636-6628
5. Before working on the unit, insulate
the wire from the spark plug, by
disconnecting the spark plug wire from
the spark plug.
Complete
pump and
piping system MUST be protected against
below freezing temperature. Failure to do
so could cause serious damage and voids
the warranty.
6. Do not run pump dry. Water is
required to lubricate the shaft seal.
7. Pumping chemicals or corrosive liquids
with this pump may shorten the life of
the pump and may be hazardous to the
operator.
8. Personal Safety:
a. Wear safety glasses at all times when
working with pumps.
b. Keep work area clean, uncluttered
and properly lighted; replace all
unused tools and equipment.
c. Keep visitors at a safe distance from
the work area.
d. Make workshop child-proof with
padlocks, master switches, and by
removing starter keys.
9. This pump is designed for non-abrasive
fluid transfer; do not use as a trash
pump. Always use a suction strainer
with this pump to filter abrasive
material. Abrasive materials such as
sand and gravel will shorten the life of
the pump.
© 2007 Blue Angel™ Pumps
For parts, product & service information
visit www. blueangelpumps.com
320601-002 7/07
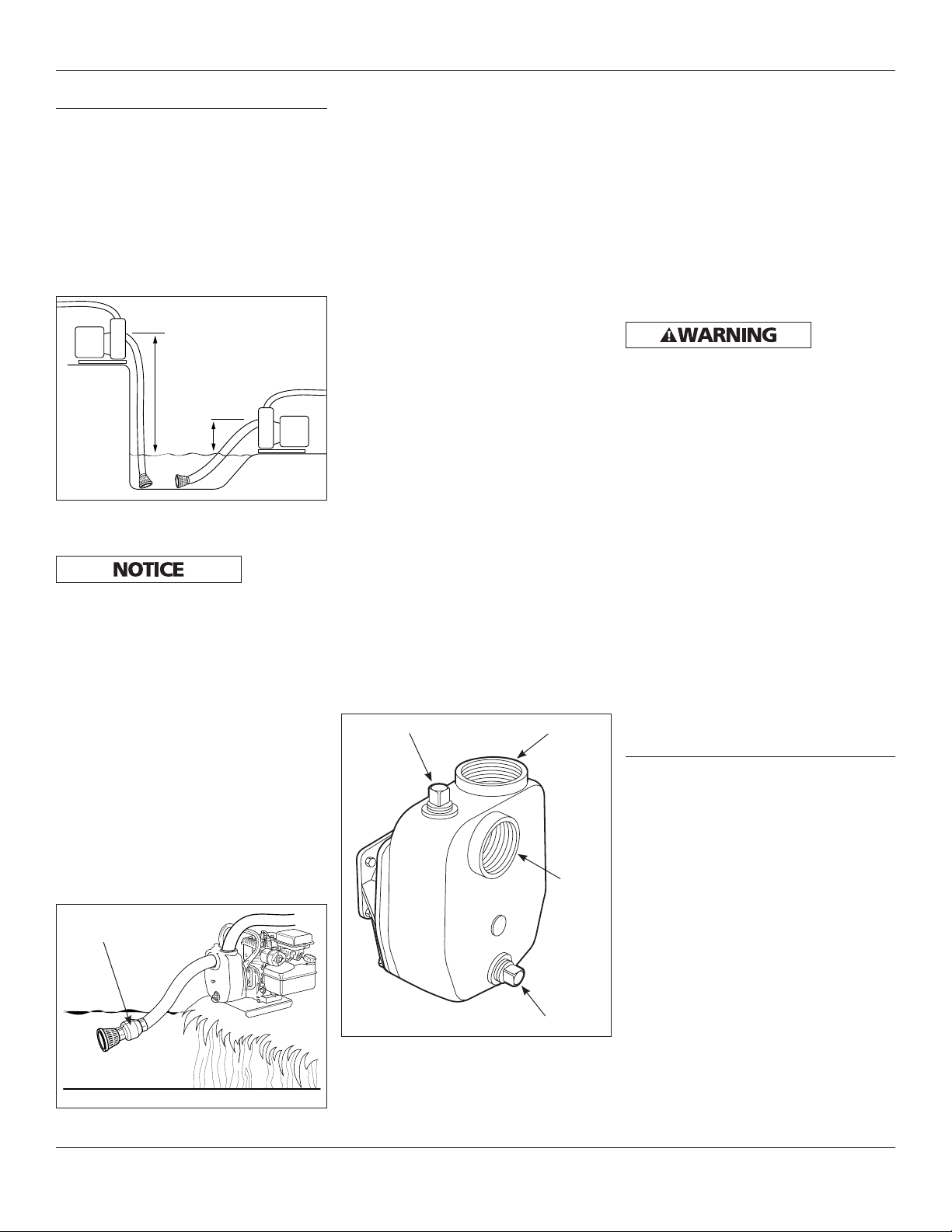
Operating Instructions and Replacement Parts List
Installation
This pump is designed to be self-priming
when installed and operated as specified
below.
1. The pump should be placed as close as
possible to the liquid being pumped.
A pump with 20 foot suction lift will
not remove water as quickly as a
pump with 5 foot suction lift
(Figure 1).
20 Ft. Suction Lift
5 Ft.
Suction
Lift
Figure 1
2. Suction hose and fitting must be
airtight.
An air
leak in
the suction line may prevent priming
of the pump. Use of thread sealant is
recommended.
Suction lines must be reinforced hose
or rigid pipe. Non-reinforced hose will
collapse due to the suction created
by the pump and prevent pump from
operating.
3. A check valve must be used in the
suction line to maintain the selfpriming capability. If no check valve is
used the pump will need to be primed
at the start of each operation. For best
operation, the check valve should be
installed at the intake of the suction
line.(Figure 2).
Check valve
4. A suction strainer is required to filter
abrasive material. Abrasive material,
such as gravel, will destroy the pump
and void the warranty. This pump
is not designed to handle abrasive
materials.
5. The discharge hose and fitting should
be leak-tight. A leak in the discharge
hose will allow water to spray
around the work site, making the site
hazardous.
6. Keep all pipes and hose lines as short
and straight as possible. Long lengths
and curves in the pipes and hose lines
will reduce the pressure the pump
develops.
7. Fill the engine crankcase with oil.
Refer to the engine operating manual
for the specific grade of oil and
amount required.
8. Fill the engine fuel tank with
gasoline. Refer to the engine
operating manual for specific gasoline
type that is most efficient for this
engine.
9. Add water to the priming port on
the pump (See Figure 3). Continue
adding water until the water level is
approximately 3 inches from the top.
Install the priming plug. The water in
the pump will create the suction that
primes the pump.
Priming port
Discharge
Suction
12. Move the engine switch to ‘ON’
position.
13. Pull engine crank until engine starts.
Once engine starts, move choke lever
to ‘RUN’ position.
14. The pump will take several minutes to
prime.
PIPING
Always place the pump as close as possible
to the liquid being pumped. Keep all pipe
and hose lines as short and straight as
possible.
Support
pump
and piping when assembling and after
installation. Failure to do so may cause
piping to break, pump to fail, etc; all of
which can result in property damage and/or
personal injury.
All suction connections must be airtight.
If the pump won’t prime, check for leaks
in the suction piping or fittings. If flexible
suction hose is used instead of pipe, use
reinforced hose with a two inch inner
diameter. Non-reinforced flexible hose may
collapse from the vacuum created as the
pump primes.
Always use a strainer at the end of the
suction pipe or hose. Position strainer so
it doesn’t become clogged with stones
or debris. A suction line check valve is
recommended.
Do not use this pump for suction lifts over
twenty-five feet.
Maintenance
Always shut off the engine, allow the
engine to cool, and remove the spark plug
before performing any maintenance.
During freezing weather, open the drain
port and allow all the water in the pump
to drain. This will prevent damage to the
pump when the water freezes. If the pump
will be stored for a month or more, drain
the water from the pump and follow the
engine manufacturer’s recommendations
for long-term storage.
Figure 2
www.blueangelpumps.com
Figure 3
Drain port
10. Turn fuel valve to ‘ON’ position
11. Move choke level to ‘CHOKE’ position.
2
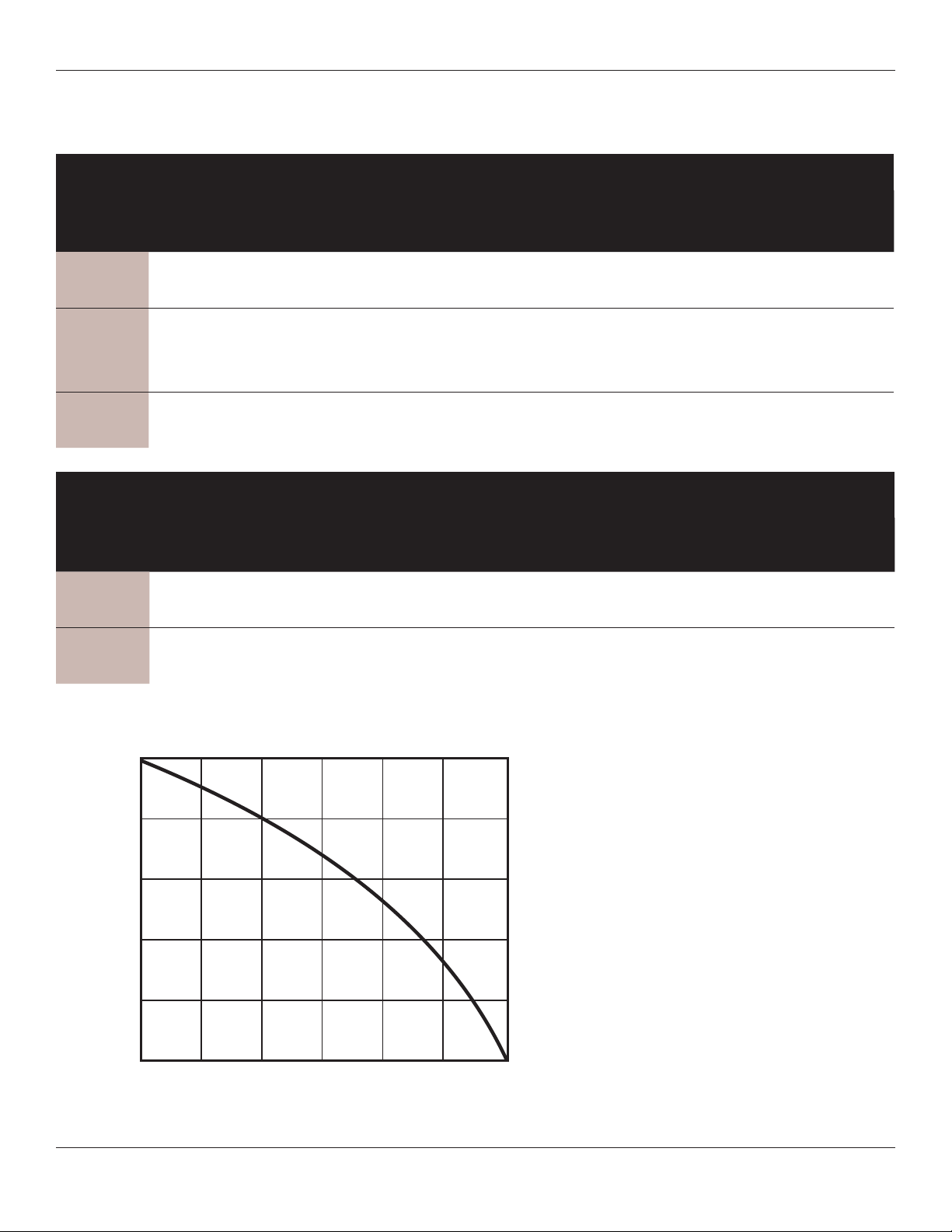
Performance Information
2” Cast Iron Pump Performance
CAPACITIES IN GALLONS PER MINUTE
BGPS400
Discharge
Head Feet
20 110 107 103 100 94 87
30 103 100 94 87 80 73
40 94 87 80 73 68 61
50 80 73 68 61 55 47
60 68 61 55 47 40 30
70 55 47 40 30 21 12
80 40 30 21 12 0 0
0 5 10 15 20 25
Dynamic Suction Lift - Feet
FEET FRICTION LOSS IN 100 FEET OF PLASTIC PIPE
Pipe
Size
1 1/
4
1 1/
2
2 1.2 1.6 2.8 4.2 5.8 9.9 15.0 21.2
20 25 30 40 50 60 80 100 120
5.6 8.5 11.9 20.2 30.5
2.6 4.0 5.5 9.4 14.3 19.9 34.2
Gallons Per Minute
2 1/
2
PERFORMANCE CURVE
100
80
60
40
20
Total Dynamic Head - FEET
0
20 40 60 80 100 120
Capacit
1.2 1.8 2.5 4.2 6.3 8.8
- GPM
www.blueangelpumps.com
3