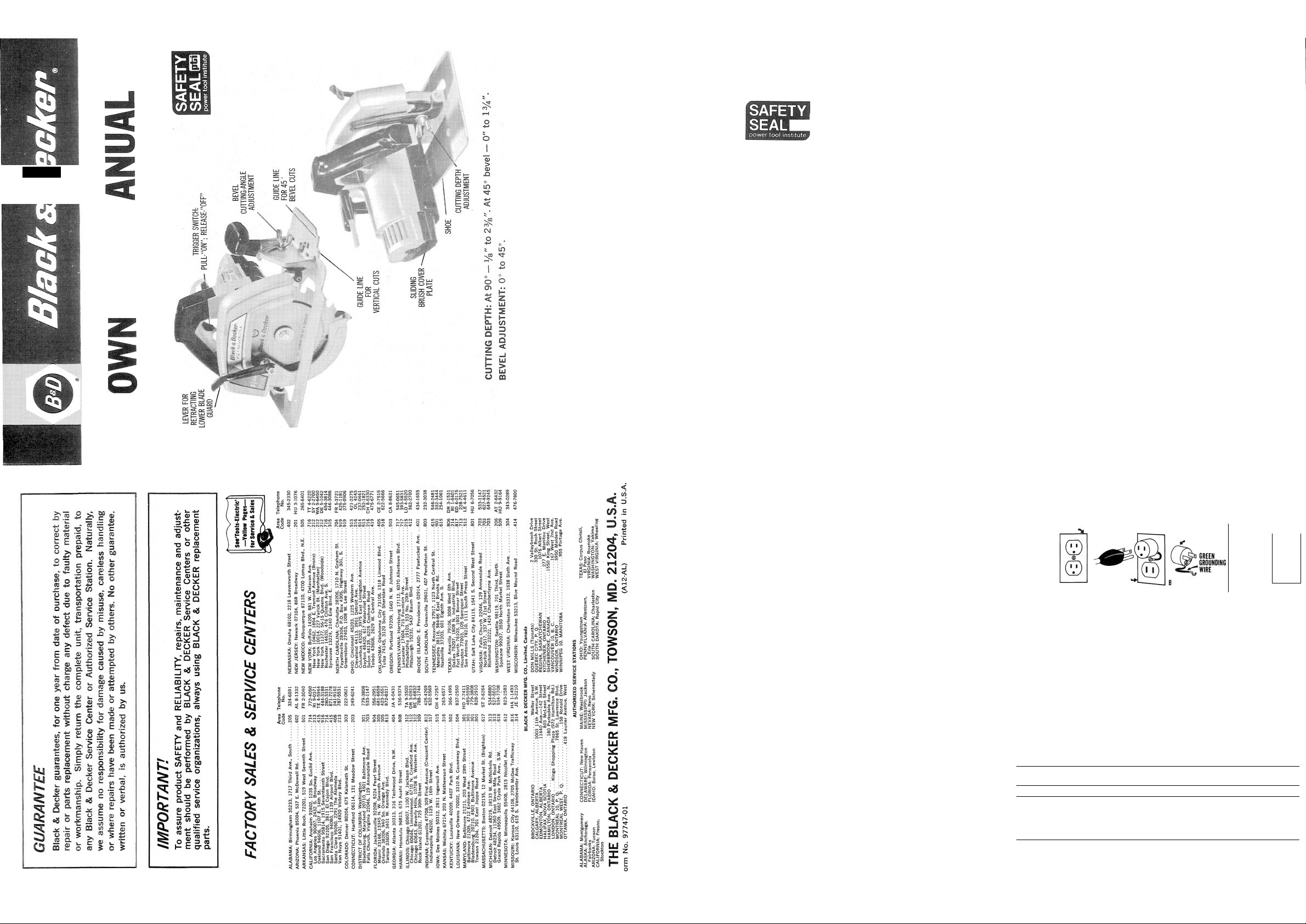
Decker, jvd' sawcat
s
ûl
8
IX
û-
X
m
m
Z
O
ci
<
m
Ü
O
>
O
CM
PJJ. SAFETY RULES
+
^ FOR POWER TOOLS
MOTOR
Your Black and Decker tool is powered by a B&D-built motor.
Be sure your power supply agrees with voltage marked on name
plate. Volts AC means Alternating Current (25 to 60 cycles) only.
1. KNOW YOUR POWER TOOL - Read owner's manual care
fully. Learn its applications and limitations as well as the
specific potential hazards peculiar to this tool.
GROUND ALL TOOLS - UNLESS DOUBLE-INSULATED. If
2.
tool is equipped with three-prong plug, it should be plugged
Volts AC/DC means it will also operate on Direct Current (single
speed unit only). Voltage variation of more than 10% will cause
loss of power and over-heating. All B&D tools are factory-tested.
If this tool does not operate, check the power supply line for
blown fuses and the plug and receptacle for proper contact.
into a three-hole electrical receptable. If adapter is used to
accommodate two-prong receptacle, the adapter wire must
be attached to a known ground. Never remove third prong.
3. KEEP GUARDS IN PLACE and in working order.
4. KEEP WORK AREA CLEAN. Cluttered areas and benches
invite accidents.
5. AVOID DANGEROUS ENVIRONMENT. Don't use power tool
in damp or wet locations. And keep work area well lit.
6. KEEP CHILDREN AWAY. All visitors should be kept safe dis
tance from work area.
7. STORE IDLE TOOLS. When not in use, tools should be
stored in dry, high or locked-up place — out of reach of
children.
8. DON'T FORCE TOOL. It will do the job better and safer at
the rate for which it was designed.
9. USE RIGHT TOOL. Don't force small tool or attachment to
do the job of a heavy duty tool.
10. WEAR PROPER APPAREL. No loose clothing or jewelry to
get caught in moving parts. Rubber gloves and footwear are
recommended when working outdoors.
11. USE SAFETY GLASSES with most tools. Also face or dust
mask if cutting operation is dusty.
12. DON'T ABUSE CORD. Never carry tool by cord or yank it to
disconnect from receptacle. Keep cord from heat, oil and
sharp edges.
13. SECURE WORK. Use clamps or a vise to hold work. It's
safer than using your hand and it frees both hands to
operate tool.
14. DON'T OVERREACH. Keep proper footing and balance at all
GROUNDING
These units are equipped with approved 3-conductor power cord
and 3-prong grounding type attachment plug to be used with the
proper grounding type receptacle, in accordance with the National
Electrical Code, Canadian Electrical Code, and Underwriters'
Laboratories specifications. The green colored conductor in the
cord is the grounding wire. It is connected to the metal frame
of the unit inside the housing and to the longest prong of the
attachment plug.
terminal.
If your unit requires less than 150 volts it has a plug that looks
like Fig. "A". It will fit directly into the proper type of 3-wire
grounding receptacle. The unit is then grounded automatically
each time it is plugged in.
Shown In Fig. "B” is a special grounding adapter (not allowed
in Canada by the Canadian Electrical Code) which is available
from your dealer and will permit using a 2-wire receptacle. The
green grounding wire extending from the side of the adapter
must be connected to a Permanent Ground.
If the unit requires from 150 to 250 volts, it has a plug like Fig.
“C”. No adapter is available and the plug must be used in the
proper 3-wire grounding receptacle.
If you use an extension cord, be sure that it is a 3-conductor,
grounding type cord. Grounding must be continuous from the
tool plug to the grounded receptacle.
Never connect the green wire to a 'live”
times.
15. MAINTAIN TOOLS WITH CARE. Keep tools sharp at all
times, and clean for best and safest performance. Follow
instructions for lubricating and changing accessories.
16. DISCONNECT TOOLS. When not in use, before servicing,
when changing accessories such as blades, bits, cutters, etc.
17. REMOVE ADJUSTING KEYS AND WRENCHES. Form habit
of checking to see that keys and adjusting wrenches are
GROUNDED OUTLET BOX
/
GROUNDING
PRONG IS
LONGEST OF
THE 3 PRONGS A
OUTLET BOX
ADAPTER
GROUNDED
GROUNDED OUTLET BOX^
o
GROUNDING
PRONG IS
LONGEST OF
THE 3 PRONGS c
®
©
removed from tool before turning it on.
18. AVOID ACCIDENTAL STARTING. Don't carry plugged-in tool
with finger on switch.
EXTENSION CORD
When using the tool at a considerable distance from power
ADDITIONAL SAFETY RULES
FOR SAWS
DISCONNECT PLUG from power supply before changing
1.
blades, making cutting depth or cutting angle adjustments,
lubricating, inspecting, or when saw is not being used.
WHEN RETRACTING the lower blade guard, always use the
2.
retracting lever on the guard.
NEVER TIE BACK the lower blade guard or its retracting knob.
3.
WHEN SAWING never reach underneath the material.
4.
KEEP BLADE SHARP. Dull blades may cause the saw to
5.
swerve or stall under pressure.
IF YOU DROP or damage the saw, unplug it first; then check
6.
+
to see if the blade and lower blade guard operate freely be
fore resuming operations.
IF SAW STALLS, release the trigger and disconnect plug from
7.
power supply before attempting to loosen the unit.
source, a 3-conductor, grounding-type extension cord of ade
quate size must be used for safety, and to prevent loss of power
and over-heating. Use the table below for 120-volt tools. For
220-volt tools, see same chart but use a wire size corresponding
to an extension cord length shown which is % the length of
extension to be used.
P.T.I. Safety Rule #12 applies to Extension Cords as well as the
Tool Power Cord. Before using cords, inspect them for loose or
exposed wires and damaged insulation. Make any needed repairs
or replacement before using your power tool.
Ampere rating
(on nameplate)
Ext. Cable length
25 ft. 18
50 ft. 18
75 ft.
100 ft. 18
150 ft.
200 ft.
0 to
2.0
18
16
16
2.10 to 3.5 to
3.4
18
18 18
18
16
14 12
14 12 10
5.0
Wire Size (A.W.G.)
18
16 14
14
5.10 to
7.0
18
16
12
12
7.10 to
12.1 to
12.0 16.0
16
14
12
10
_
____
_
—
14
12
10
_
____
_
____
_
.—
Form No. 97717.m
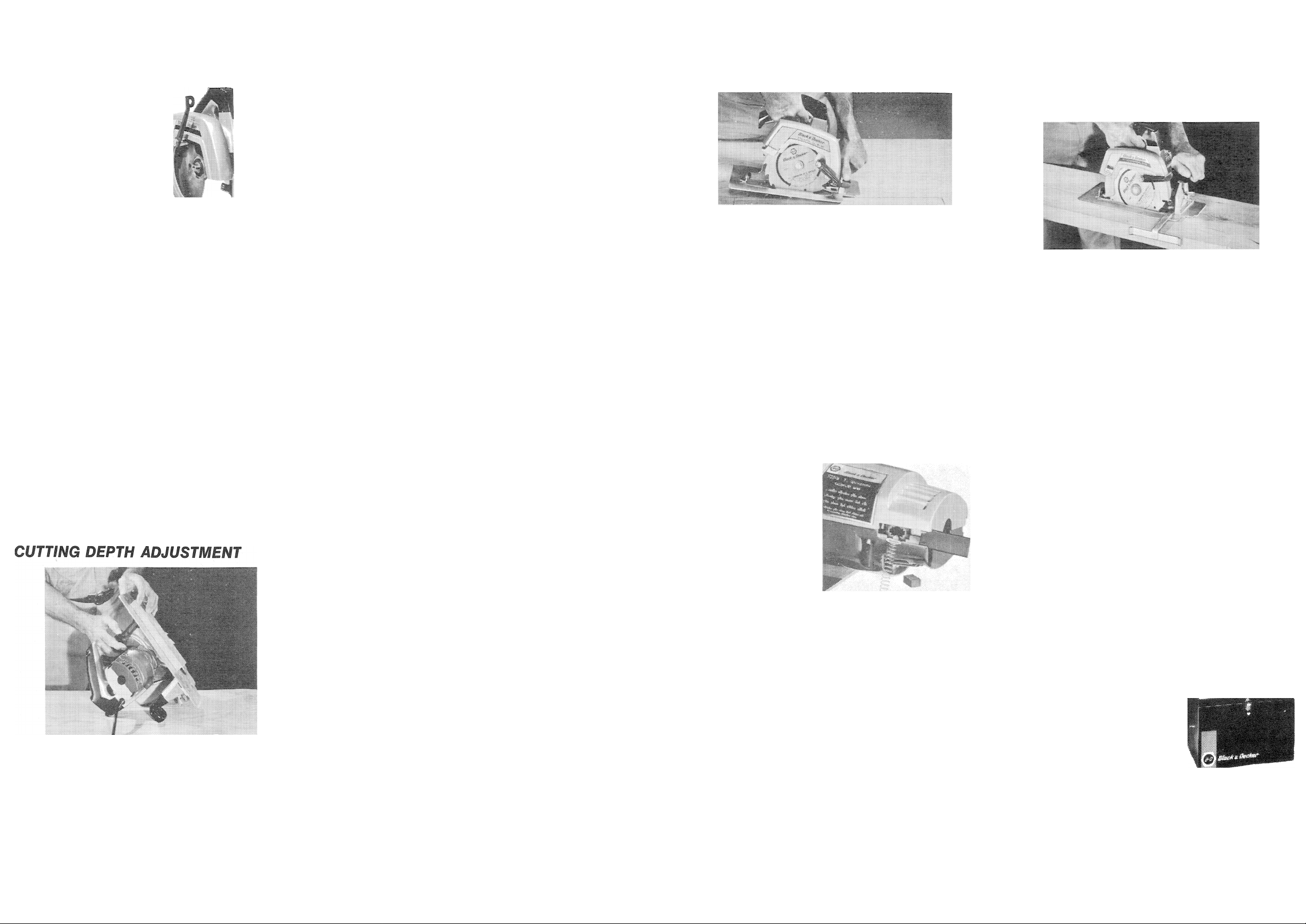
MOUNTING SAW BLADES
BEVEL ANGLE ADJUSTMENT
POCKET CUTTING
SAW ACCESSORIES:
%
1. BE SURE THE SAW IS DISCONNECTED FROM THE POWER
SUPPLY!
2. To remove blade clamping screw;
— a. ON NEW SAWS (without blade attached), turn screw
counter-clockwise with blade wrench provided. If screw does
not loosen easily from spindle, tap the outer end of the
wrench sharply in a counter-clockwise direction with a piece
of wood to "free" the screw threads. Remove screw and outer
clamp washer.
- b. ON SAWS WITH BLADE ATTACHED, turn the blade so
that the single hole In the rim is exposed at the front of the
saw. Put a nail through this hole and turn the blade counter
clockwise until the nail is against the housing and stops the
blade from turning. Turn the blade clamping screw counter
clockwise with the blade wrench and remove the screw and
outer clamp washer.
3. To attach the blade, retract the lower blade guard and slip
the blade over the saw spindle against the inner clamp washer
with printed side of blade out (teeth at bottom of blade
pointing forward). Place outer clamp washer or spindle so
that "flats" in washer fit "flats" on spindle. Thread on clamp
ing screw to hold washer in position. Place a nail through
hole in blade rim so that nail rests on front of saw base and
keeps blade from turning. Tighten clamping screw (clock
wise) securely with the blade wrench.
BE SURE SAW IS UNPLUGGED. When cutting any material with
steel blades, the most efficient depth adjustment is one that
permits the blade tooth depth only to project below the bottom
of the material (except when using Carbide Tipped Blades, where
only 1/2 oi the tooth tip should project below the material). This
keeps blade friction at a minimum, removes sawdust from the
cut and results In cooler, faster sawing. Correct cutting depth is
obtained by: (1) Place the saw in the position shown above and
loosen the wing nut on the inside of the blade guard. (2) Raise
or lower the base until the blade projects from the base the de
sired distance. Retighten wing nut securely.
DISCONNECT PLUG FROM POWER SUPPLY BEFORE MAKING
THIS OR ANY OTHER ADJUSTMENT. The adjustable base (shoe)
permits bevel cutting at any angle between 45° and 90°, The
quadrant on the front of the saw is calibrated for accurate
adjustment. To set saw for bevel angle cut, loosen wing nut and
tilt base to angle desired. Retighten wing nut securely.
SWITCH
Pull the trigger switch to turn the motor "ON". Releasing the
trigger instantly turns the motor "OFF," but the blade will
continue to rotate for a short time. For safer operation, this tool
has no provision to lock the switch in the "ON" position.
OPERATION
ALWAYS DISCONNECT THE SAW BEFORE MAKING ANY AD-
JUSTMENTS. Place the work with its "good” side — the one on
which appearance is msore important — down. The saw cuts
upward, so any splintering will be on the face that is up when
you saw it. Support the stock so that the cut will be on your
right, with the wider base portion of the saw base on that part
of the work piece which is solidly supported, not on the section
that will fall off when the cut is made. If the stock is short or
small, clamp it down. Don’t try to hold short pieces by hand.
Draw the required guide lines then rest the front of the saw base
(shoe) fiat on top of the work, with the guide notch correctly
aligned. Run the stationary blade lightly against the edge of the
work, back it off a little, and only then start the motor. Advance
the saw into the wood. The telescoping blade guard will swing
back by itself. Feed the tool at the speed at which the blade
cuts easily. Remember that hardness and toughness can vary
even in the same piece. A knotty or damp section can put a
heavy load on the saw; when this happens feed more slowly.
Feed the saw hard enough to keep it working without much
decrease in speed. Forcing it beyond this makes for rough cuts,
inaccuracy, and overheating of the motor.
Should your cut begin to go off the line, don’t try to force it
back on. It's best, of course to make errors on the waste side
of the line. Then you can withdraw the saw, sight anew, and
start a new cut a trifle inside the wrong one. In any event,
withdraw the saw if you must shift the cut. Forcing a correction
inside the cut can stall the saw and perhaps spoil the work. IF
SAW STALLS, RELEASE THE TRIGGER, DISCONNECT PLUG
FROM POWER SUPPLY AND THEN BACK THE SAW UNTIL IT
IS LOOSE. BE SURE BLADE CLEARS THE WORK BEFORE RE
STARTING CUTTING.
As you finish a cut, release the trigger and allow the blade to
stop before lifting the saw from the work. As you lift the saw
the spring-tensioned telescoping guard will automatically close
under the saw. Remember the blade is exposed until this occurs;
never reach under the work for any reason whatsoever. When
you have to retract the telescoping guard manually (as is neces
sary for starting pocket cuts) always use the retracting lever.
Adjust saw base (shoe) so blade cuts at desired depth. Tilt saw
forward and rest front of base on materia! to be cut. Using
lever, retract blade guard to an upward position. Lower rear of
base until blade teeth almost touch cutting line. Now release
the blade guard and its contact with the work will keep it in
position to open freely as you start the cut. Start the motor and
gradually iov^/er the saw until its base rests fiat on the material
to be cut. Advance saw along cutting line until cut is completed.
Release trigger and allow blade to stop completely before with
drawing the blade from the material. \Yhen starting each new
cut, repeat as above. Never tie the blade guard In a raised
position.
MOTOR
BRUSHES
Carbon motor brushes
should be inspected fre
quently for wear. To in
spect brushes, FIRST, UN
PLUG SAW FROM POWER
SUPPLY. Then, with a
screwdriver, slide the
brush cover plates out
ward and the brush spring
will pop out Put the /
spring, with attached wire
extended out of the open
ing into the position
shown at right and tilt the
saw so that the carbon brush will drop out of the opening. If the
brush is worn down to the grooved line on its side, a new brush
is needed and can be obtained from any B&D Service Center
see "TOOLS, ELECTRIC" in Yellow Pages.
To reassemble, insert brush with worn end toward motor, or a
new brush with longest distance from end to grooved line toward
motor. Next, insert the
small brass plate behind the brush, and
then feed in the spring until the round spring cap fits flush with
the opening. This allows the cover plate to be pushed back into
the closed position.
LUBRICATION
Your tool was properly lubricated before leaving the factory. It is
recommended that, at least once a year, you take or send the
tool to a B&D Service Center for a thorough cleaning, inspec
tion and lubrication of the gear case.
RIP FENCE
The Rip Fence permits fast, smooth
rip-cuts without penciled lines. To
install, insert Rip Fence in front
slots, set Fence at desired dis
tance from blade and tighten
screw. The Rip Fence may also be
inserted from the opposite side of
the base slots. Cat. No. 55584
SAW PROTRACTOR
Guides accurate cross cuts at any
angle from 0° to 90°. Calibrated
in degrees. Has adjustable pointer.
Cat, No. 49531
t:
CUT-OFF GUIDES
One-piece guide for making accu
rate 90° or 45° cuts. Cat. No. 55582
CARRYING CASE
Gives easy portability and protec
tion for your saw. Has room for
extra blades, accessories and ex
tension cord. Cat. No. 55580
SMW BLMDES
Black & Decker manufacturers a complete line of blades which
are available from your Distributor. These include: COMBINATION
(crosscut & rip), CROSSCUT, PLYWOOD, PLANER, FLOORING,
CARBIDE-TIPPED, METAL CUTTING, PLYWOOD, FRICTION,
FRAMING, and RIPPING Blades.