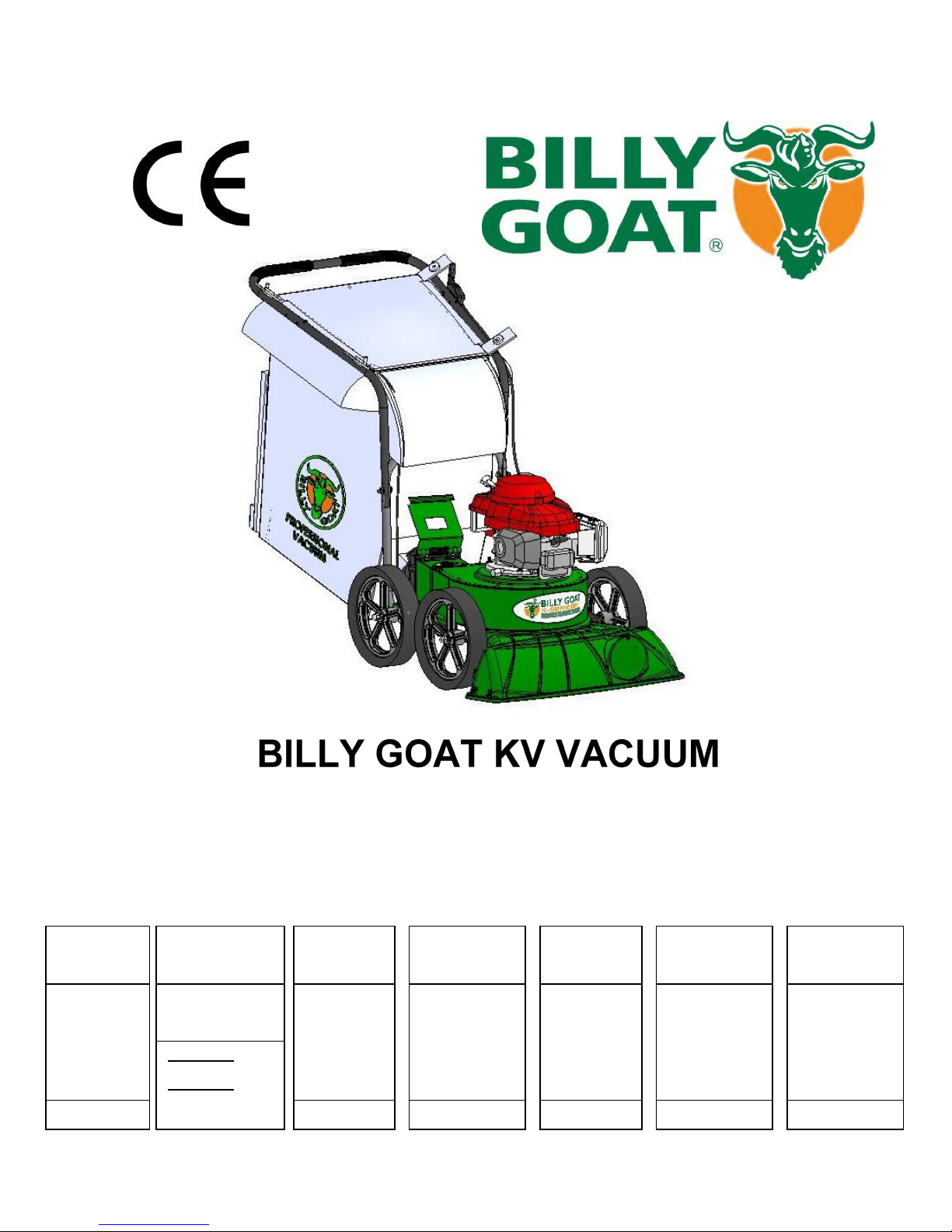
4"(102mm) x
7.5' (2.13m)
For
vacuuming in
hard to reach
areas.
OPTIONAL
FELT/MESH
DEBRIS BAG
For use in leaves
and grass in dusty
conditions.
P/N 891126 FELT
BAG
P/N 891132
MESH BAG
For use in
increasing the
life of your
nozzle by
protecting it
from damage
To allow for
easy rolling and
maneuverability
on smooth
surfaces.
Shreds
leaves,
reducing total
volume.
Increases the
life of the
housing by
protecting it from
damage.
Protects the
machine from
the environment
when not in use.
KV600, KV650H, KV600FB, KV650HFB
Accessories
Part No 891203 Form No F081612B
Owner's Manual

SPECIFICATIONS AND SOUND/ VIBRATION ___ 3
INSTRUCTION LABELS 4
PACKING CHECKLIST & ASSEMBLY 5
OPERATION _6
MAINTENANCE AND TROUBLESHOOTING 7
ILLUSTRATED PARTS & PARTS LISTS 8-9
Go to http://www.billygoat.com for French-Canadian translations of the product manuals.
Visitez http://www.billygoat.com pour la version canadienne-française des manuels de produits
CONTENTS
Part No 891203 Form No F081612B
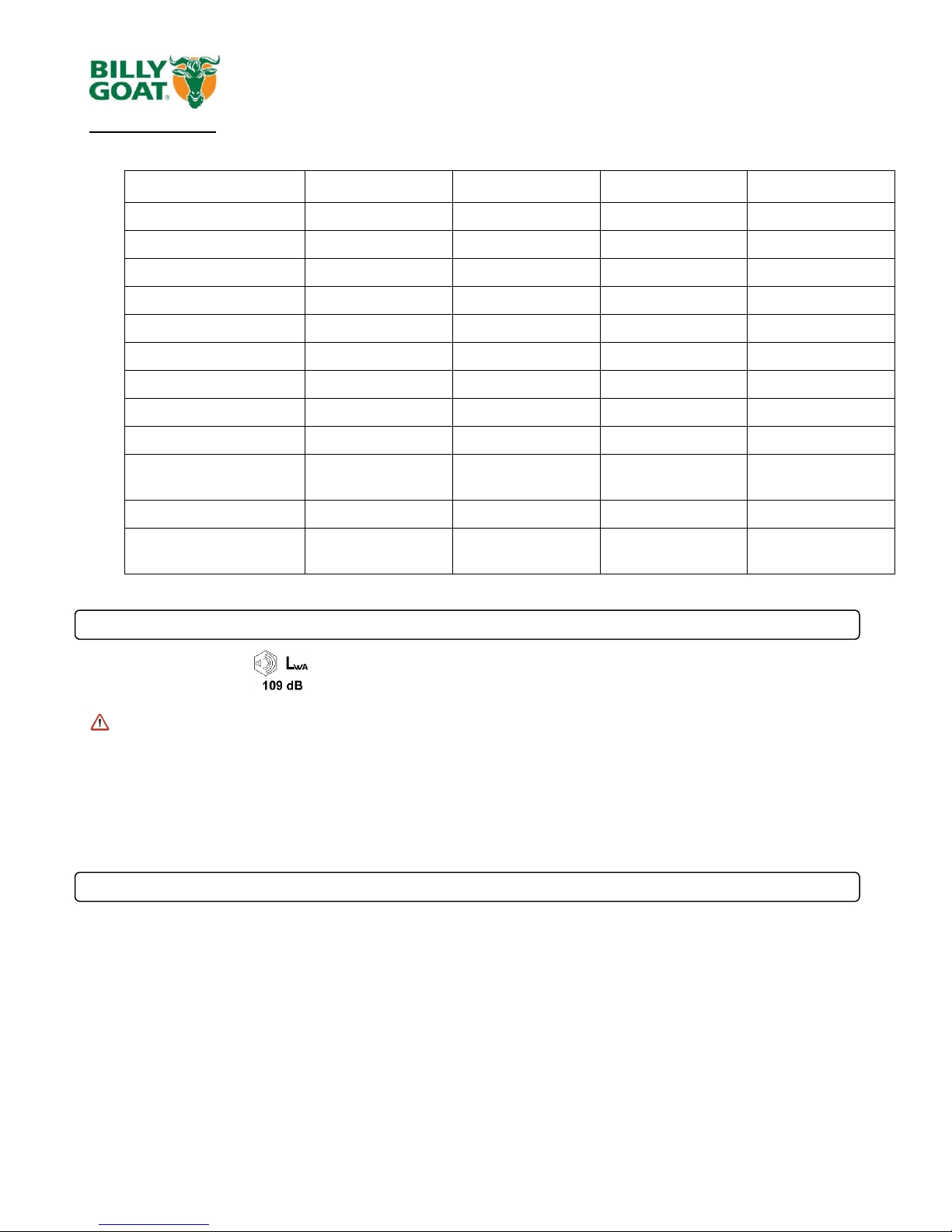
Sound in accordance with
2000/14/EEC standards
Vibration at operator
position
General Conditions: Sunny
Temperature: 88oF (31.1oC)
Wind Speed: 2 mph (3.8 kmh)
Wind Direction: South South East
Humidity: 44%
Barometric Pressure: 30.07”Hg (764 mm Hg)
General Conditions: Sunny
Temperature: 47.5oF (8.6oC)
Wind Speed: 3 mph (4.8kph)
Wind Direction: West
Humidity: 87%
Barometric Pressure: 29.98 Hg (101.5kpa)
Specifications
KV600 KV650H KV600FB KV650HFB
SOUND
Sound tests were conducted in accordance with 2000/14/EEC, and were performed on 7-25-07 under the conditions listed below.
Sound power level listed is the highest value for any model covered in this manual. Please refer to serial plate on the unit for the sound
power level for your model.
SOUND LEVEL 97 dB(a) at Operator Position
VIBRATION DATA
VIBRATION LEVEL 0.5g (4.95m/s2)
Vibration levels at the operator’s handles were measured in the vertical, lateral and longitudinal directions using calibrated vibration test
equipment. Tests were performed on 12-20-2007 under the conditions listed below.
Part No 891203 Form No F081612B
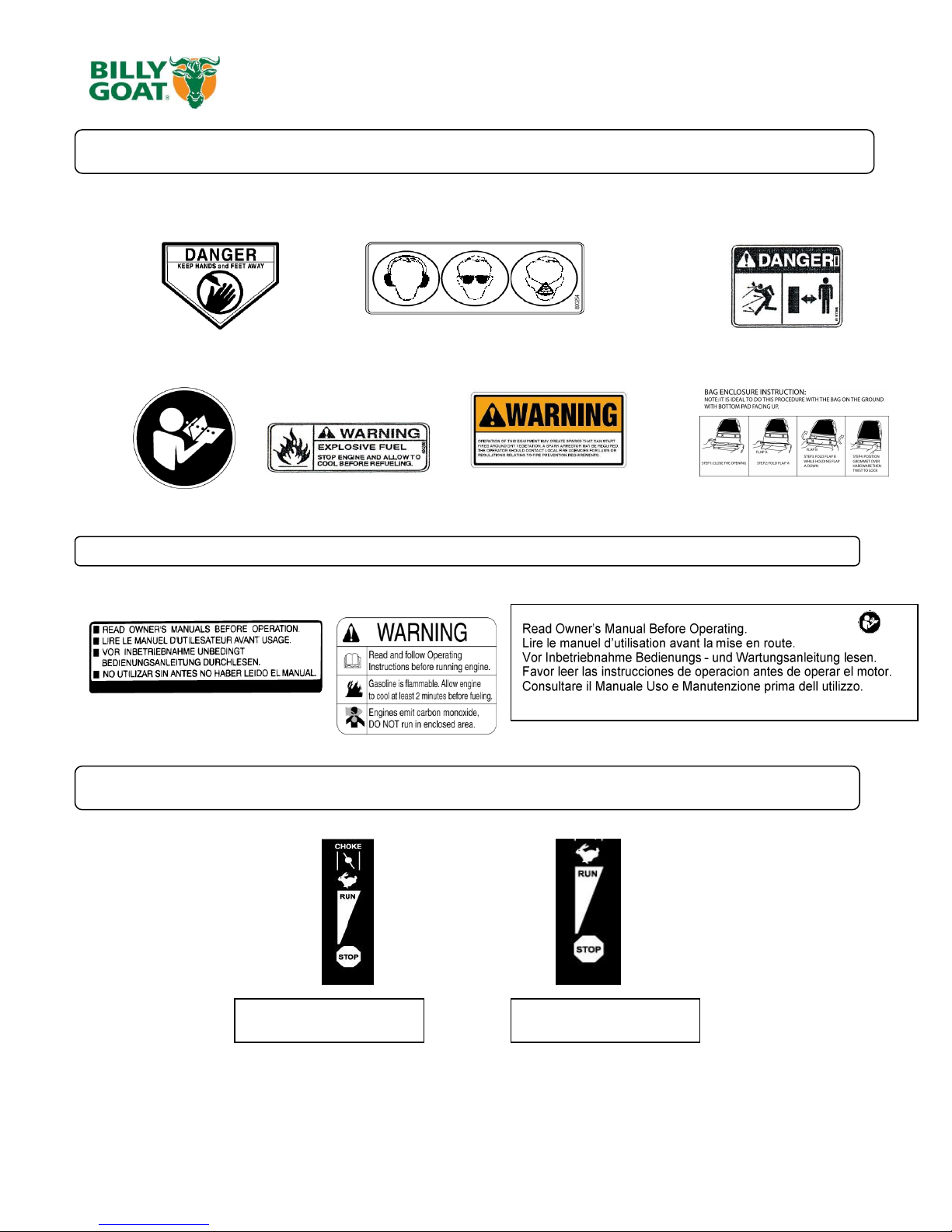
Las Skotselinstruktionen Innan Start.
INSTRUCTION LABELS
The labels shown below were installed on your BILLY GOAT ® KV Vacuum. If any labels are damaged or missing, replace them before operating
this equipment. Item numbers from the Illustrated Parts List and part numbers are provided for convenience in ordering replacement labels. The
correct position for each label may be determined by referring to the Figure and Item numbers shown.
LABEL DANGER KEEP HANDS LABEL EAR EYE BREATHING ITEM #20 DANGER FLYING DEBRIS
AND FEET AWAY P/N 890254 ITEM # 19 P/N 810736
ITEM #18 P/N 400424
LABEL READ MANUAL LABEL EXPLOSIVE FUEL LABEL SPARK ARRESTOR DEBRIS BAG FOLDING LABEL
ITEM #17 P/N 890301 ITEM # 16 P/N 400268 P/N 100252 LOCATED ON BAG
ENGINE LABELS
ENGINE CONTROLS
Part No 891203 Form No F081612B
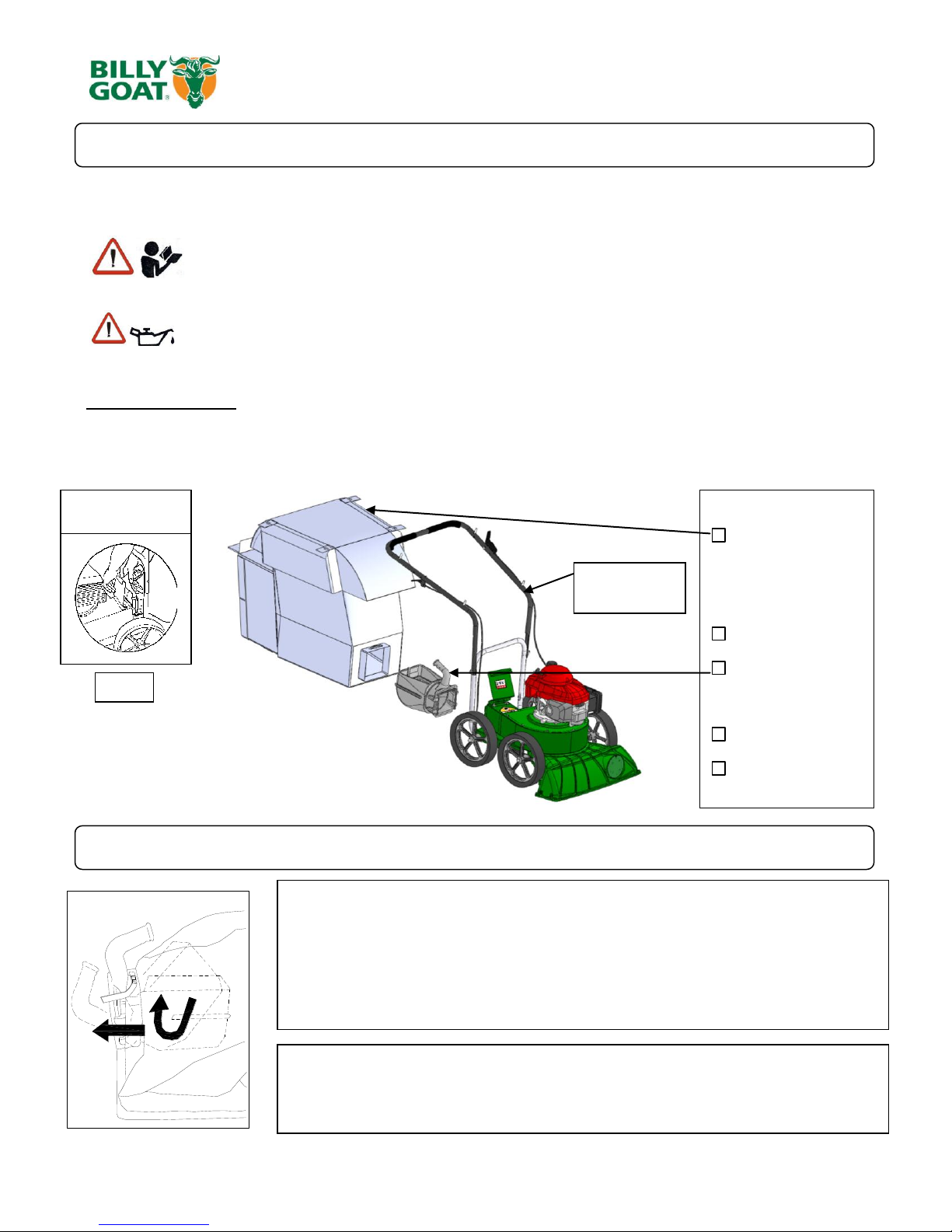
READ all safety instructions before assembling unit.
TAKE CAUTION when removing the unit from the box the Handle Assembly is attached by
cables and folded over
1. ASSEMBLE Lift upper handle (item 11), remove items 34, 32, and 33 from lower
handle (item 10). Attach and secure upper handle as shown using same hardware.
2. UNFOLD the debris bag (item 21) and fasten bag neck to bag quick disconnect
(item 12). Attach firmly to housing exhaust (item 1) see fig. 2.
3. ATTACH bag hanger strap to bag supports (item 13), preassembled to upper
handle.
4. CONNECT spark plug wire.
Debris Bag
P/N-891132
OR
Felt Bag
P/N-891126
Literature Assy
P/N-891123
Connector Quick
Disconnect
P/N-890630
Briggs & Stratton
6.0 HP Quantum
PARTS BAG &
LITERATURE ASSY
Warranty card P/N- 400972, Owner’s Manual P/N-891203, General Safety and Warnings Manual- 100294,
Declaration of Conformity P/N-891057, Ty-Wraps 900407 (qty2).
Insert the quick disconnect from the inside of the bag, tilt the handle so it can
be fed through first. Then slide the connecting end through and tighten the
strap
PACKING CHECKLIST
Your Billy Goat KV Vacuum is shipped from the factory in one carton, completely assembled except for the
upper handle, debris bag, and bag quick disconnect.
PUT OIL IN ENGINE BEFORE STARTING
ASSEMBLY
Part No 891203 Form No F081612B
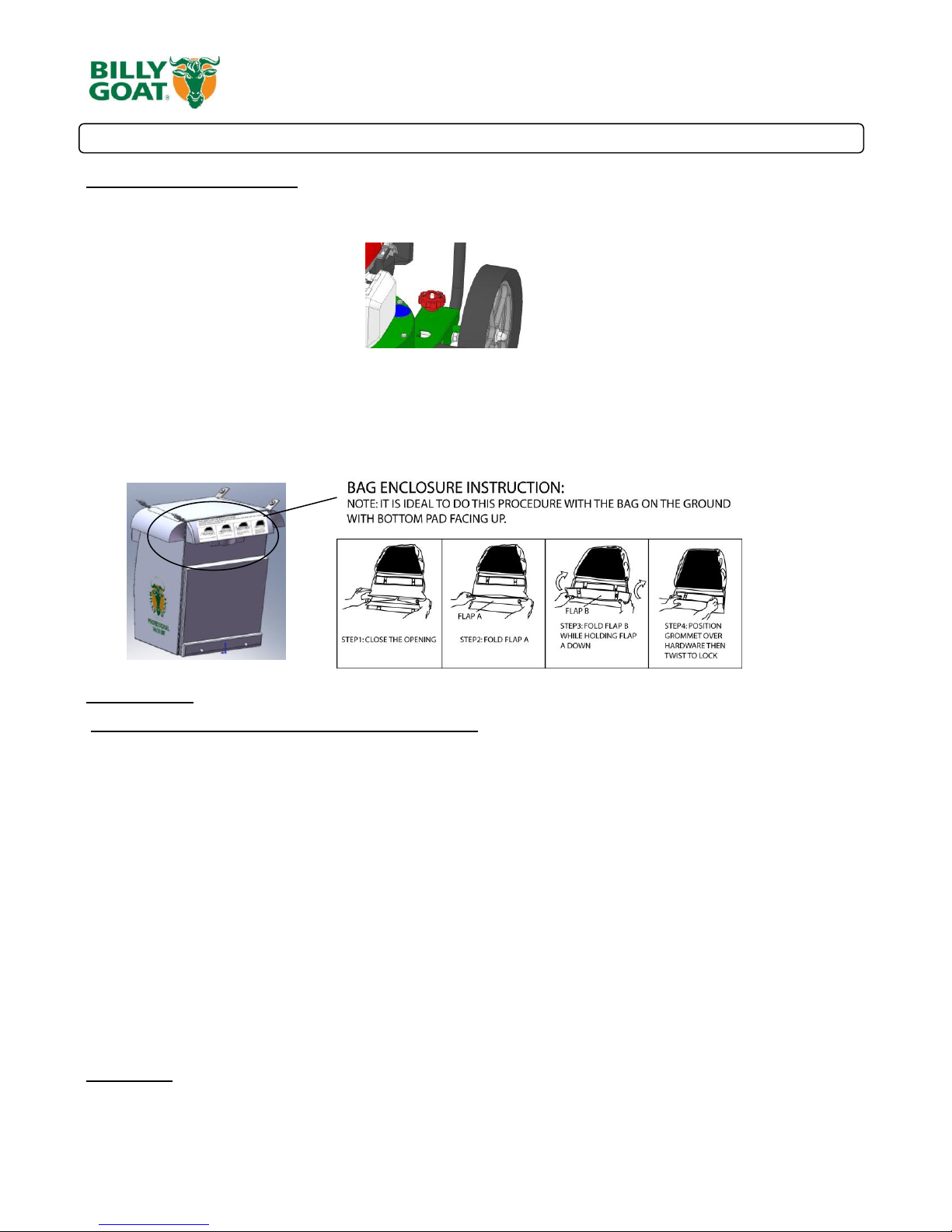
VACUUMING OPERATION
VACUUM NOZZLE HEIGHT ADJUSTMENT: Nozzle height is raised and lowered by rotating the red knob near
the left rear wheel. Nozzle height should be adjusted based on the task being performed.
FOR MAXIMUM PICKUP: Adjust nozzle close to debris, but without blocking airflow into the nozzle. NOTE:
Never bury nozzle into debris.
CLEARING A CLOGGED NOZZLE & EXHAUST: Turn engine off and wait for impeller to stop completely
and disconnect spark plug wire. Wearing durable gloves, remove clog. DANGER the clog may contain sharp
materials. Reconnect spark plug wire.
DEBRIS BAG
Debris bags are normal replaceable wear items.
Note: Frequently empty debris to prevent bag overloading with more weight than you can lift.
An optional felt bag is available for use where debris will be vacuumed in dusty conditions (see Optional Accessories
shown on page 1).
DO NOT place bag on or near hot surface, such as engine. Be sure engine has come to a complete stop before removing or
emptying bag.
This vacuum is designed for picking up trash, organic material and other similar debris (see Safety and General
Operation manual).
However, many vacuums are used where dust is mixed with trash. Your unit can intermittently vacuum in dusty areas.
Dust is the greatest cause of lost vacuum performance. However, following these rules will help maintain your
machine's ability to vacuum in dusty conditions:
• Run machine at idle to quarter throttle.
• The debris bag must be cleaned frequently. A vacuum with a clean, pillow soft bag will have good pickup
performance. One with a dirty, tight bag will have poor pickup performance. If dirty, empty debris and vigorously shake
bag free of dust.
• Pressure-wash debris bag if normal cleaning does not fully clean bag. Bag should be thoroughly dry before use.
NOTE: Having one or more spare debris bags is a good way to reduce down time while dirty bags are being cleaned.
DO NOT leave debris in bag while in storage.
COMPOST
Vacuumed leaves, grass and other organic material from your own yard can be emptied into a pile or composter to
provide enriched soil for later use as fertilizer in gardens and flower beds
NOTE: Allow green chips to dry before spreading around living plants.
OPERATION
Part No 891203 Form No F081612B
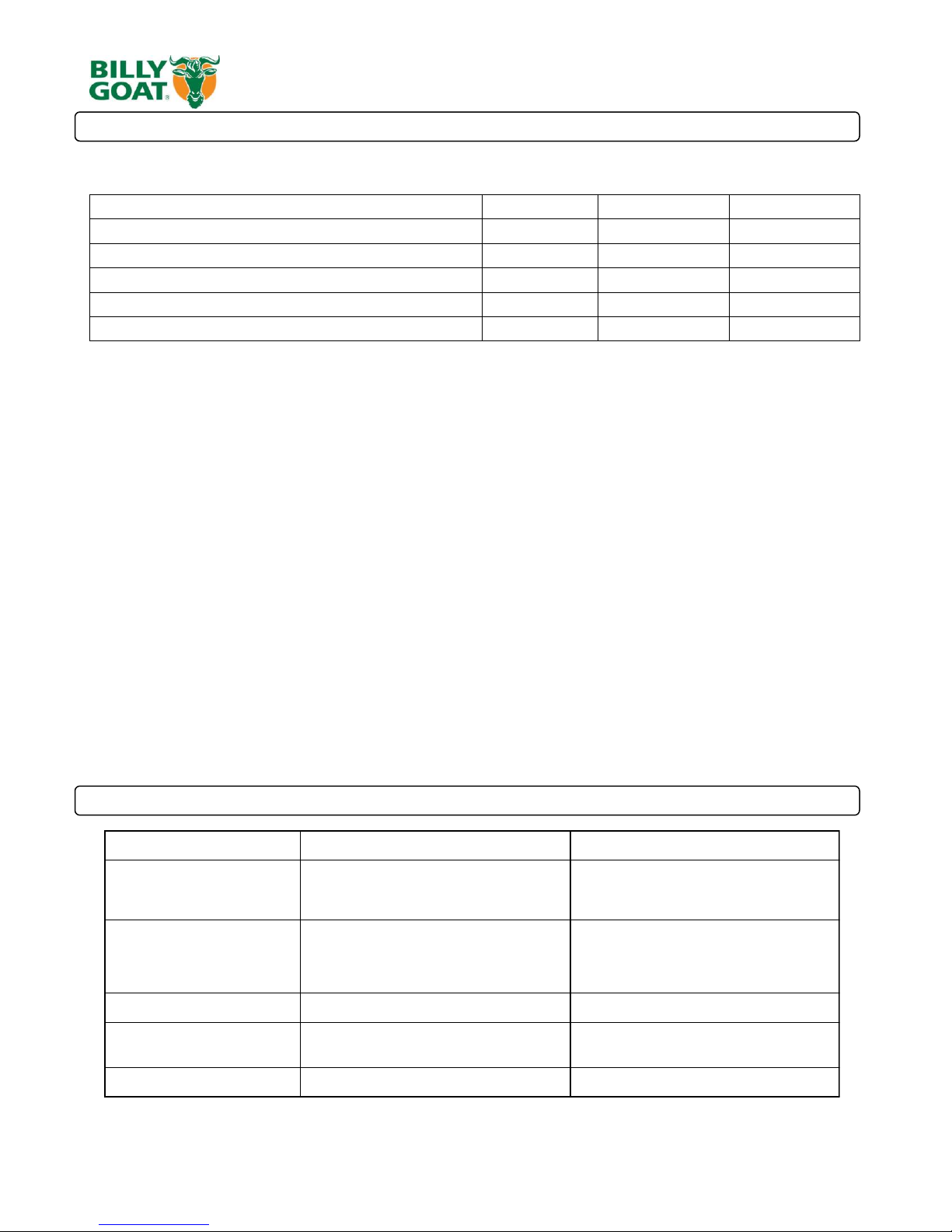
Inspect for loose, worn or damaged parts.
Check bag strap tightness
Engine (See Engine Manual)
Check for excessive vibration
Problem Possible Cause Solution
· Loose or out of balance impeller or
loose engine
· Check impeller and replace if required.
Check engine
Will not vacuum or has poor
vacuum performance
· dirty debris bag. Hose kit cap missing.
·Clogged nozzle or exhaust. Excessive
quantity of debris.
· Improper nozzle height
· Clean debris bag. Shake bag clean or
wash. Check for hose kit cap. Unclog
nozzle or exhaust. Allow air to feed with
debris
· Stop switch off. Throttle in off position.
Engine not in full choke position. Out of
gasoline. Bad or old gasoline.
Sparkplug wire disconnected. Dirty air
cleaner
· Check stop switches, throttle, choke
position and gasoline. Connect spark
plug wire. Clean or replace air filter. Or
contact a qualified service person.
Engine is locked, will not
pull over.
· Debris locked in impeller. Engine
problem.
· See page 5. Contact a engine service
dealer for engine problems
Nozzle scrapes ground in
lowest height setting.
Nozzle height out of adjustment
Adjust nozzle height (See Nozzle
height fine adjustment for hard surfaces
on page 5
Too much dust coming from
bag.
· Vacuuming very dry, brittle or small
debris
· Switch to felt bag (see page 1
accessories)
IMPELLER REMOVAL
1. Wait for engine to cool and disconnect spark plug.
2. Drain fuel and oil from the engine.
3. Remove bag, quick release, and upper handle. Do not kink, stretch, or break control cables, control
housings, or end fittings while removing handles.
4. Remove housing top plate by removing bolts around outside of housing.
5. Leaving engine fastened to top plate, turn it upside down so the impeller is on top.
6. Remove impeller bolt and lock washer and washer.
7. Lift impeller upward. If impeller slides freely, proceed to (step 10).
8. Place two crowbars between impeller and housing on opposite sides. Pry impeller away from engine until it
loosens. Using a penetrating oil can help loosen a stuck impeller.
9. If the impeller does not loosen, use two pry bars and pull the impeller near the hub away from the engine,
this should loosen it and allow you to remove the impeller from shaft. Using a penetrating oil can help loosen a
stuck impeller.
10. Using a new impeller bolt and lockwasher and washer, reinstall new impeller in reverse order.
11. Tighten impeller bolt. Torque impeller bolt to 33-38 Ft. Lbs. (44-51 N.m) (see item 30 on page 15).
12. Reinstall engine onto housing in reverse order of removal.
13. Gas and oil.
14. Reinstall spark plug wire.
MAINTENANCE
PERIODIC MAINTENANCE
Periodic maintenance should be performed at the following intervals:
Troubleshooting
Part No 891203 Form No F081612B