
IMPORTANT
INFORMATION
for
MS/SM/SMF SERIES
This cooler has passed the
QUALITY CONTROL INSPECTION
and meets the high standards at
Beverage-Air. This inspection includes
complete refrigeration system,
cabinet construction & finish.
809-022A
*
Quality Control Inspector, Beverage-Air
WARRANTY REGISTRATION CARD
Cabinet Serial No. _______________________
Original Purchaser _____________________________________________________________________
Address _____________________________________________________________________________
Installation Location ___________________________________________________________________
_____________________________________________________________________________________
Beverage-Air Model No. _________________________ Installation Date _______________________
This card must be mailed within 10 days after installation date to
You may also complete warranty registration at www.beverage-air.com
CITY STATE
NAME
ADDRESS

SCHOOL MILK, MIX AND BULK STORAGE COOLER SERIES
SM, SMF, MS MODELS
INSTALLATION AND OPERATING INSTRUCTIONS
• INSPECTION ON ARRIVAL
UPON ARRIVAL OF THE COOLER, THE CARTON SHOULD BE CAREFULLY INSPECTED FOR ANY OUTWARD SIGN OF
DAMAGE. IF ANY SIGN OF DAMAGE IS FOUND, IT SHOULD BE NOTED ON THE CARRIER’S FREIGHT BILL BEFORE SIGNING
FOR THE MERCHANDISE. IN ANY CASE, THE COOLER SHOULD BE IMMEDIATELY UNCRATED TO CHECK FOR APPARENT OR
CONCEALED DAMAGE WITHIN 48 HOURS AFTER DELIVERY AND THE CARRIER NOTIFIED FOR AN INSPECTION WITHIN THIS
PERIOD.
• UNCRATING - SM, SMF, MS MODELS
To uncrate cooler, remove staples around the bottom of carton with screwdriver. Care should be taken to remove the
staples completely so that they will not damage the cooler nish when the carton is removed. Lift the carton tube from
around the cooler. Remove cooler from skid.
• LOCATING COOLER
It is necessary to properly level cooler to provide adequate drainage and efcient functioning of the unit. Make sure there is
enough room around the cooler to assure good air circulation through the condenser.
• ELECTRICAL SUPPLY
Plug all standard models into a 110-115 volts A.C. 50- or 60-cycle outlet. Low line voltage is often the cause of service
complaints. Check to see that the live voltage is 110 volts or more with the unit running. Other motors or heavy appliances
should not be used on the same circuit with the cooler. When working on the inside of the cooler, disconnect from electrical
circuit for safety reasons.
• STARTING UP OF UNIT
Factory setting of temperature control is at No. 5 position (normal) on control dial which will maintain the temperature as
follows:
36°F —SM Models
40°F —MS Models
For colder temperature, turn control knob to higher number, one position at a time. Excessive tampering with the control
could lead to service difculties. Should it become necessary to replace temperature control, be sure it is ordered from an
authorized Beverage-Air distributor or direct from the factory.
• DRAINAGE — MS MODELS
The condensation drains into a condensate disposal pan located just below unit compartment grill. This pan is equipped
with vapor glass wicking to hasten the evaporation process so plumbing is not required. The drain lines and pan should be
thoroughly cleaned periodically as solids from spilled products may not evaporate, resulting in an unsanitary condition.
• CLEANING
The cooler should be thoroughly cleaned inside and out at regular intervals to preserve the nish and appearance. If
stainless steel becomes discolored or stained, it can be cleaned with standard cleaners such as Bon-Ami, but not with
steel wool. All dirt and lint should be removed from the condenser at regular intervals for efcient performance of the cooler.
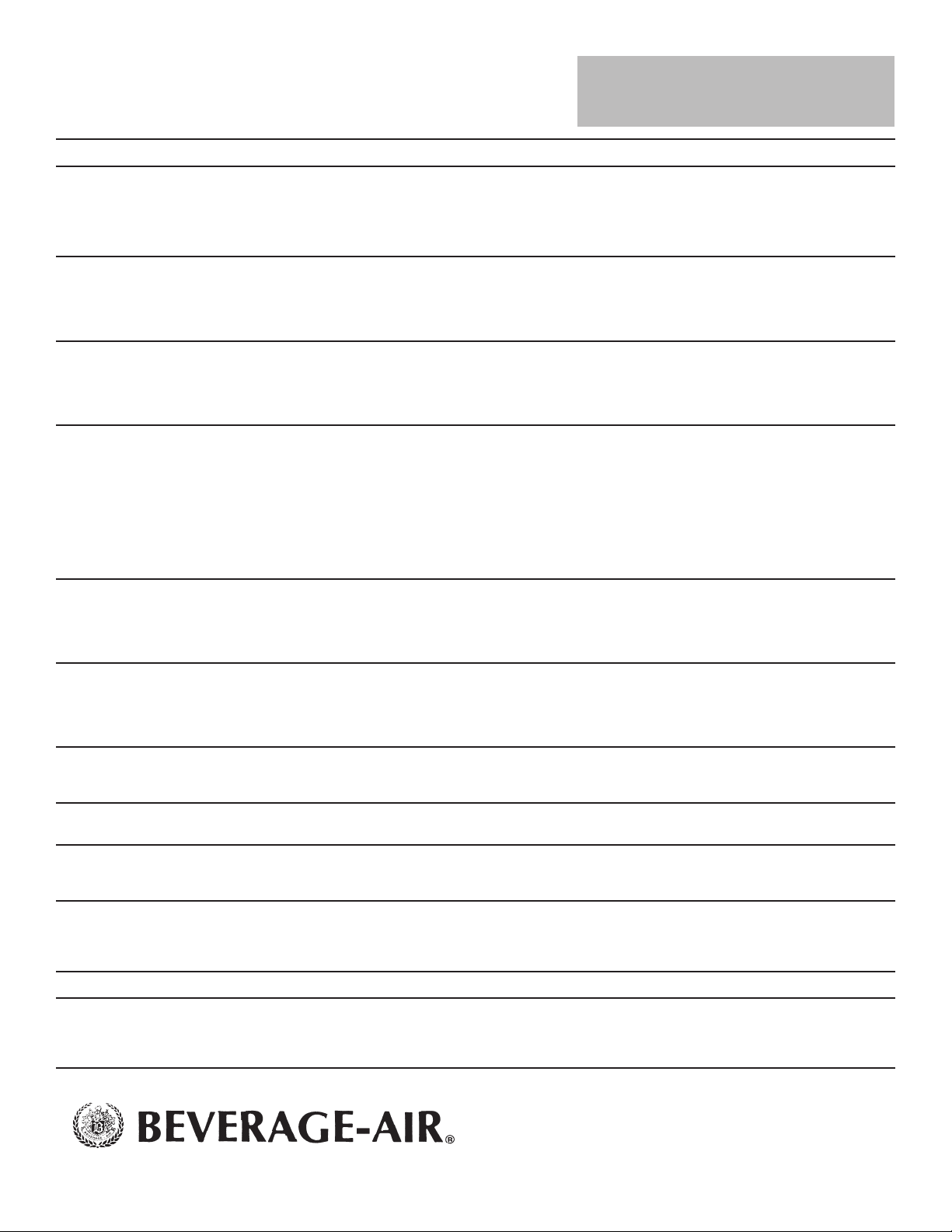
SERVICE AND
ANALYSIS CHART
REFRIGERATION
SYSTEM
MALFUNCTION POSSIBLE CAUSE SOLUTION
Compressor will not start — no hum. 1. Line cord not plugged in. 1. Plug in line cord.
2. Fuse removed or blown. 2. Replace fuse.
3. Overload protector tripped. 3. Refer to electrical section.
4. Control stuck in open position. 4. Repair or replace control.
5. Wiring improper or loose. 5. Check wiring against diagram.
Compressor will not start — hums but trips 1. Improperly wired. 1. Check wiring against diagram.
on overload protector. 2. Low voltage to unit. 2. Determine reason and correct.
3. Starting capacitor defective. 3. Determine reason and replace.
4. Relay failing to close. 4. Determine reason and correct.
Replace if necessary.
Compressor starts but does not switch off 1. Low voltage to unit. 1. Determine reason and correct.
of start winding. 2. Relay failing to open. 2. Determine reason and correct.
3. Run capacitor defective. Replace if necessary.
4. Compressor motor has a winding 3. Determine reason and replace.
open or shorted. 4. Replace compressor.
Compressor starts and runs, but short 1. Additional current passing through 1. Check wiring diagram. Check for added fan
cycles on overload protector. overload protector. motors, pumps, etc., connected to wrong
2. Low voltage to unit. side of protector.
3. Overload protector defective. 2. Determine reason and correct.
4. Run capacitor defective. 3. Check current, replace protector.
5. Excessive discharge pressure. 4. Determine reason and replace.
6. Compressor too hot — return hot gas. 5. Check ventilation, restrictions in cooling
medium, restrictions in refrigeration.
6. Check refrigerant charge (x leak).
Add if necessary.
Unit runs OK, but short cycles. 1. Overload protector. 1. Check wiring diagram.
2. Cold control. 2. Differential set too close — widen.
3. Overcharge. 3. Reduce refrigerant charge.
4. Air in system. 4. Recover and recharge.
5. Undercharge. 5. Fix leak. Add refrigerant.
Unit operates long or continuously. 1. Shortage of refrigerant. 1. Fix leak. Add charge.
2. Control contacts stuck or frozen closed. 2. Clean contacts or replace control.
3. Evaporator coil iced. 3. Defrost.
4. Restriction in refrigeration system. Determine location and remove.
5. Dirty condenser. 5. Clean condenser.
Start capacitor open, shorted or blown. 1. Relay contacts not opening properly. 1. Clean contacts or replace relay, if necessary.
2. Low voltage to unit. 2. Determine reason and correct.
3. Improper relay. 3. Replace.
Run capacitor open, shorted or blown. 1. Improper capacitor. 1. Determine correct size and replace.
2. Excessively high (line) voltage (11-% of rated max.) 2. Determine reason and correct.
Relay defective or burned out. 1. Incorrect relay. 1. Check and replace.
2. Line voltage too high or too low. 2. Determine reason and replace.
3. Relay being inuenced by loose vibrating mounting. 3. Remount rigidly.
Space temperature too high. 1. Control setting too high. 1. Reset control.
2. Improper overcharge. 2. Recover refrigerant and recharge with proper
3. Inadequate circulation. charge specied on data plate.
3. Improve air movement.
Cooler freezing beverage. 1. Control setting. 1. Reset control.
Unit noisy. 1. Loose parts or mountings. 1. Find and tighten.
2. Tubing rattle. 2. Reform to be free of contact.
3. Bent fan blade causing vibration. 3. Replace blade.
4. Fan motor bearings worn. 4. Replace motor.
ALL SERVICING MUST COMPLY WITH STATE AND FEDERAL REGULATIONS.
SALES OFFICE: 3779 Champion Blvd. • Winston-Salem, NC 27105
PLANT: BROOKVILLE, PENNSYLVANIA
PHONE: 336-245-6400 TOLL FREE: 800-845-9800
FEDERAL LAW REQUIRES THAT SOME REFRIGERANTS BE RECOVERED PRIOR TO SERVICING.