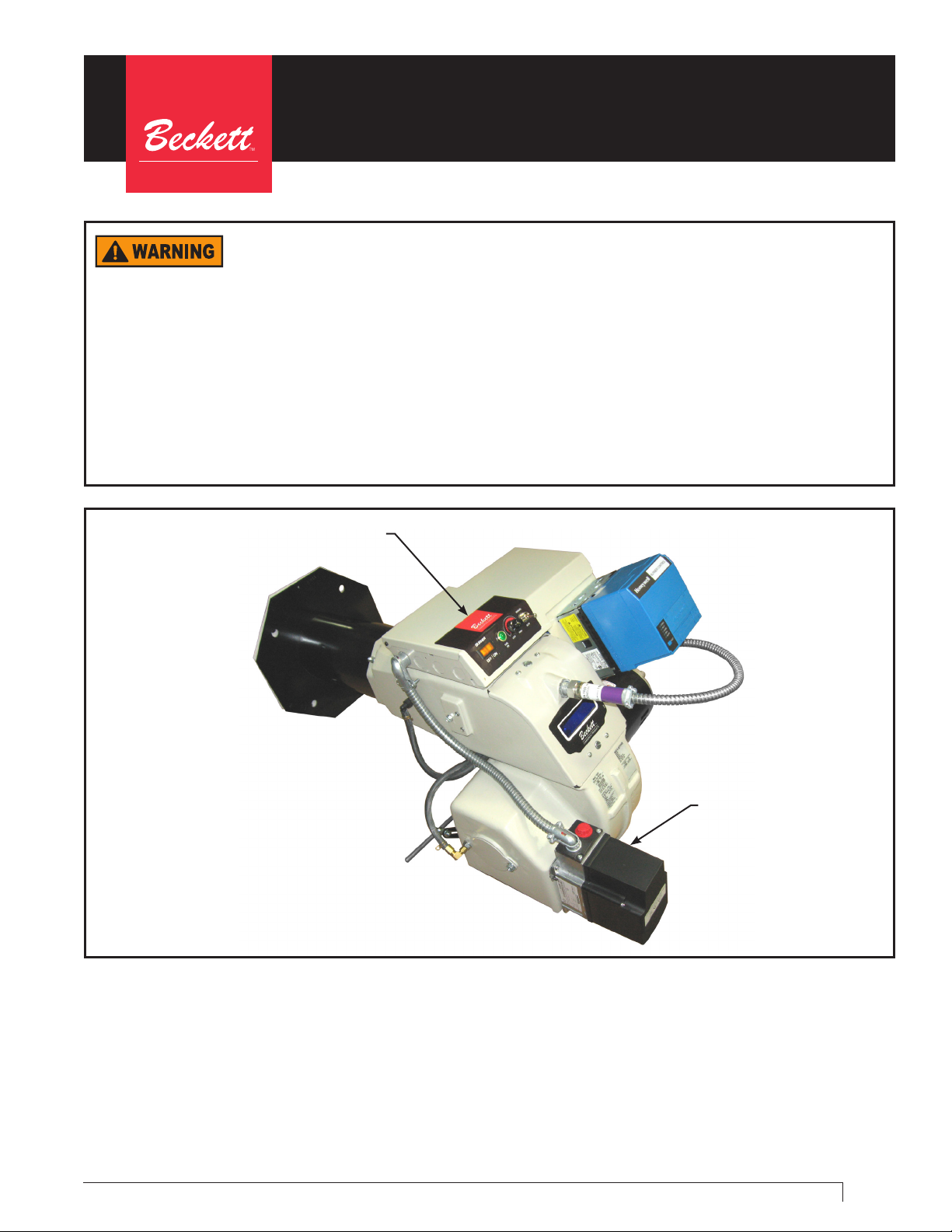
Gas Burner Manual Supplement
CG15 / CG25 / CG50 Optional Modulation Control Systems
COMMERCIAL PRODUCTS
Professional Installation and Service Required
Incorrect installation and mishandling of startup could lead to equipment malfunction
and result in asphyxiation, explosion, or re.
y This Gas Burner Supplement shall be used in conjunction with the Beckett 6104 BCG50 Installation Manual.
y This burner shall only be installed and prepared for startup by a qualied service technician who is trained and
experienced in commercial gas burner system installation and operation.
y Carefully follow the wiring diagrams, control instruction sheets, ame safeguard sequence of operation, test procedures
and all appliance manufacturer’s directions that pertain to this installation.
y Perform all wiring in accordance with the National Electric Code ANSI/NFPA 70, Canada CSA C22.1 and all authorities
having jurisdiction.
y If any of these items are not clear or are unavailable, call Beckett at 1-800-645-2876 for assistance.
Figure 1
Operator controls are the
same for all 3 signal types.
I. Introduction
The CG15, CG25, and CG50 gas burners are available
in three optional congurations that can be controlled
by the three most popular modulation control signals:
135 Ohm, 4 – 20 mA, or 2 – 10 VDC. All three of these
options use the Siemens SQM40 actuator for damper
control. The SQM40 accepts any of those signals, so the
difference between burners using any of those control
signals is internal wiring of the burner, the control signal
Siemens SQM40 actuator
connections you make, and trim adjustments. When
operating with any of these signals, the burner’s ring
rate responds in a direct proportional control manner,
making them well suited for use with lead/lag or building
automation system controls. The standard burner
conguration for these modulation systems is with the
junction box (shown in Figure 1), but a panel enclosure
is optionally available.
1

II. Wiring
III. Damper Motor Components
Electric Shock Hazard
Turn off all electric power to the burner before
servicing.
y If power is required for adjustments, use extreme
care while working near live conductors.
Figure 2
Color Coded Label
Terminal Strip
The damper motor positions for high re and for low re
are set by adjustment of individual cams in a cam stack
(Shown in
Figure 3). Only three of the cams in this
motor are active, the red, black and green cams.
○ The red cam limits the maximum position of the
motor to the burner’s high re setting.
○ The black cam limits the minimum position of the
motor to the burner’s low re setting.
○ The green cam could be used to set a third position,
for example an off position for the damper. We do
not use the green cam, but we recommend that it be
set to the same position as the black cam.
Figure 3
Red High Fire Cam
(Example:Red Pointer set at 90)
Black Low Fire Modulation Limit Cam
(Example: Black Pointer set at 25)
For standard construction burners the junction
box contains a color coded terminal strip showing
connections for control system power (and blower
motor power for 120 VAC blower motors), limit string
connections, gas valve connections, and rate control
connections. The terminal strip markings match the
wiring diagram speci c to your burner. All of your
control connections are to be made to this terminal
strip. For burners with blower motors operating at a
voltage greater than 120 VAC the junction box will have
a separate motor contactor section with its own power
connections. Refer to the wiring diagram supplied with
your burner for connection details.
Figure 4
Adjusting
Screws
Indicating Notch for
Damper Position
Green Low Fire Limit Cam
(Example: Green Pointer set at 25)
Damper Position Scale
2