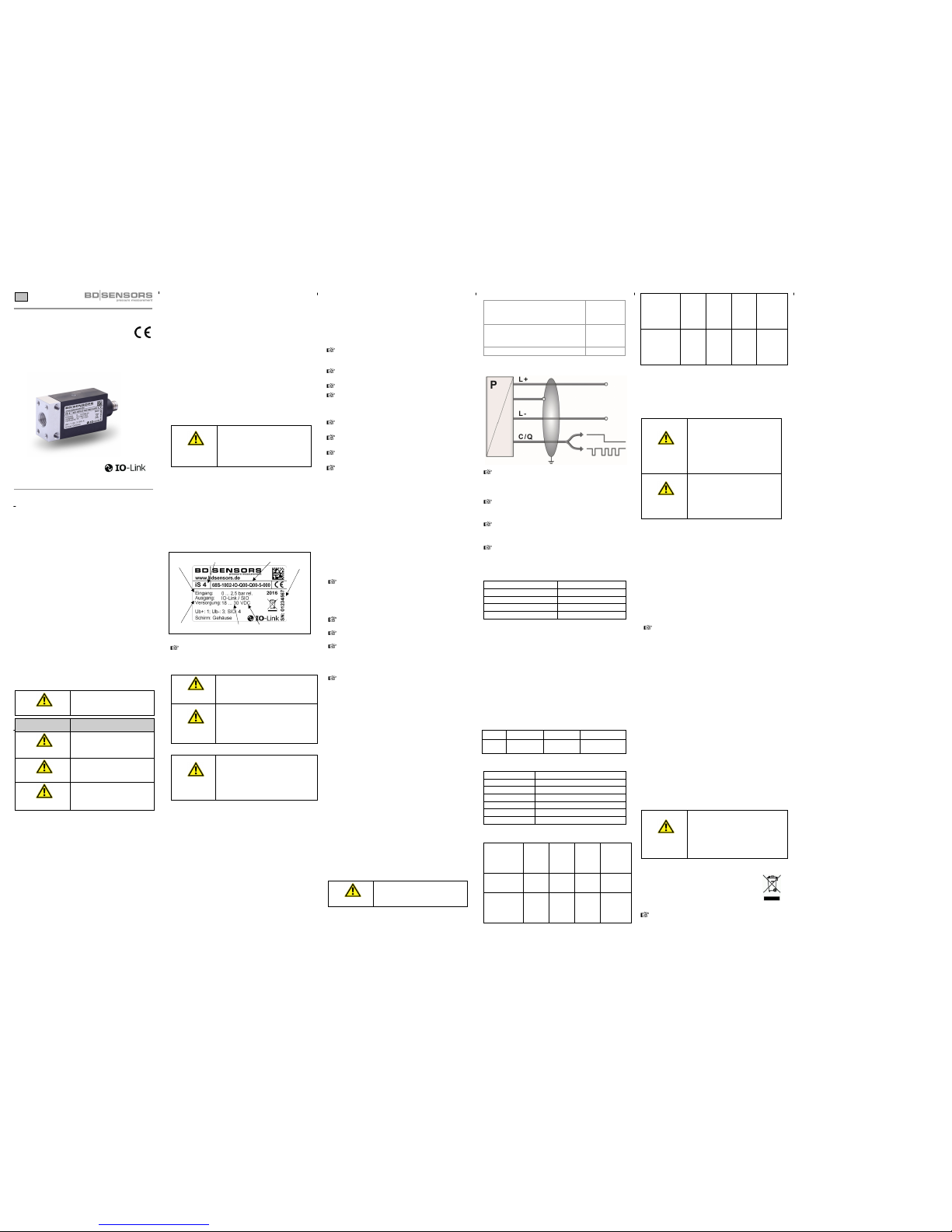
Operating Manual
Electronic OEM Pressure Switch Pneumatics with IO-Link
Interface
iS4
Headquarters
BD SENSORS GmbH
BD-Sensors-Str. 1
D - 95199 Thierstein
Deutschland
Tel.: +49 (0) 9235-9811-0
Fax: +49 (0) 9235-9811-11
Eastern Europe
BD SENSORS s.r.o.
Hradištská 817
CZ - 687 08 Buchlovice
Tschechische Republic
Tel.: +42 (0) 572-4110 11
Fax: +42 (0) 572-4114 97
The addresses of our overseas offices can be found at
www.bdsensors.de. Data sheets, user manuals, ordering
codes and certificates are al so available for you to download
from our website.
1. Generals
1.1 General and safety-related information on this
operating manual
This operating manual enables safe and proper handling of
the product, and forms part of the device. It should be kept in
close proximity to the place of use, accessible for staff
members at any time.
All persons entrusted with the mounting, installation, putting
into service, operation, mai ntenance, removal from service,
and disposal of the device must have read and understood
the operating manual and in particular the safety-rel ated
information.
– Technical modifications reserved –
1.2 Symbols Used
Warning word
- Type and source of danger
- Measures to avoid the
danger
Warning word Meaning
DANGER
- Imminent danger!
- Non-compliance will result in
death or serious injury.
- Possible danger!
- Non-compliance may result in
death or serious injury.
CAUTION
- Hazardous situation!
- Non-compliance may result in
minor or moderate injury.
NOTE – draws attention to a po ssibly hazardous situation
that may result in property damage i n case of noncompliance.
1.3 Staff Qualification
Qualified persons are persons that are familiar with the
mounting, installation, putting into service, operation,
maintenance, removal from service, and disposal of the
product a nd have the a ppropriate qualification for their
activity.
All work with this product must be carried out by qualified persons!
1.4 Limitation of Liability and Warranty
Failure to observe the instructions or technical regulations,
improper use and use not as intended, and alteration of or
damage to the device will result in the forfeiture of warranty
and liability claims.
1.5 Intended Use
- The Pressure switch iS4 with IO-Li nk interface has been
developed for pressure measuring applications depending
on the particular model. Depending on mechanical connection, they are suitabl e for a wide range of applications.
The press ure switch is intended for installation in a machine or system. It is the responsibility of the user to check
whether the device is suitable for the chosen application. If
in doubt, please contact our sales office. BD SENSORS
cannot, however, assume any liability for an incorrect
choice or any consequences arising from this!
- Media that can be measured compressed air and nonaggressive gases which are compatible with the materials
that contact the medium. These are described in the data
sheet. Furthermore, it must be ensured in each individual
case that the medium is compatible with the parts they
come in contact with it.
- The technical data listed in the current data sheet are
engaging. If the data sheet is not available, please order
or download it from our homepage.
WARNING
Danger of death through incorrect
use
- In order to avoid accidents, use the
device only in accordance with its
intended use.
1.6 Package contents
Check that all of the li sted parts are included in the delivered
package and have been supplied in accorda nce with your
order:
- Electronic OEM Pressure Switch iS4
- Operating Manual
2. Product Identification
The type plate serves to identify the device. The most
important data can be taken from this. The order code is
used for unique identification of your product.
.
Fig. 1 Type plate
The type plate must not be removed from the device!
3. Installation
3.1 Installation and safety instructions
DANGER
Danger of death from electric shock
-
Install the device only when the machine
is depressurized and the power supply
has been switched off!
WARNING
Danger of death from improper install
tion
- Installation must be performed only by
appropriately qualified specialist personnel
who have read and understood the user
manual.
General information for oxygen use
DANGER
Danger of death from explosion
through improper use of devices intended for use with oxygen
- The following points must be observed
in order to ensure safe handling:
- Make sure that a special version of yo ur device has
been ordered for use with oxygen and that the expected
device has been delivered. The easiest way for you to
verify this is by checking the type plate (see Fig. 1 regarding this). If your order code ends with the digits
"007", then your devi ce is suitable for oxygen applications.
- When it is delivered, the device is packaged in a plastic
bag to protect it from contamination. Take note of the
advice sticker with the text "Device for oxygen; unpack
immediately before installation"! Also note that contact
with skin should be avoided when unpacking and installing the device so as to a void leaving grease resi dues on the device.
- The relevant provisions concerning explosion protection
must be met during installation. Also check whether approval as intrinsically safe equipment is required in addition to suitability for oxygen. (This is not the case for the
device as supplied!)
- Please note that the entire system must comply with the
requirements of the BAM (German Federal Institute for
Materials Research and Testing, DIN 19247).
- Pressure transmitters designed for use wi thout seal s
are recommended for oxygen applications > 25 bar.
- Pressure transmitters with FKM (Vi 567) sealing rings:
Maximum permitted values: 25 bar / 150° C
(BAM approval).
Please treat this highly sensitive electronic measuring
instrument caref ully, both when packed and when unpacked!
No modifications or alterations may be made to the
device.
Do not throw or drop the device!
Only remove the packaging and, if applicable, the
protective cap from the device shortl y before its installation, so as to avoid damaging the diaphragm. Be sure to
retain the supplied protective cap!
Fit the protective cap back over the diaphragm immedi-
ately after dismounting the device.
Treat the unprotected diaphragm wi th extreme care; it
can be damaged very easily.
Do not apply any force to install the devi ce so as to
avoid damaging the device and the system!
When installing outdoors or in humid environments, the
following points should be noted:
- The device should be electrically connected immediately after installation to ensure that no moisture is able to
penetrate into the plug connector, if this is not possible,
the ingress of moisture must be prevented by using a
suitable protective cap. (T he protection class specified
in the data sheet applies to the connected device.)
- Select an installation position that allows spl ashed water
and condensation to drai n away. Ensure that sealing
surfaces are not exposed to standing liquid!
- Install the device such that it is protected from direct
sunlight. In the worst case, direct sunlight may result in
the maximum permissible operating temperature being
exceeded, which ca n then damage the device or affect
its ability to function correctly. If the internal pressure in
the device rises, this could also cause temporary measurement errors.
Take care that the pressure connector is not subjected
to any mechanical stresses higher than that permitted,
since this could cause the characteristic to shift or result
in damage. This applies especially to very small pressure ranges, as well as to devices wi th a pressure connector made of plastic.
In t he case of hydraulic systems, ori ent the device such
that the pressure connector faces upwards (for venting).
Provide a cooling section when using the device in
steam lines.
If there is a risk that a device installed outdoors mig ht
be damaged by lightning stri ke or overvol tage, we recommend the provisi on of overvoltage protection between the power supply unit or control cabinet and t he
device.
If the device is installed with the pressure connector
facing upwards, make sure that no liquid runs do wn the
housing. This could result i n moisture and dirt blocking
the gauge reference i n the housing and cause malfunctions. If necessary, remove any dust and dirt from the
edge of the screw joint of the electrical connector.
3.2 General installation instructions
- Carefully remove the device from i ts packaging and
dispose of the packaging properly.
- Then proceed as described in the following installation
instructions.
3.3 Installation steps for internal thread G1/8"
- Use a suitable seal for sealing, e. g. Teflon strip, flat
gasket or O-ring, on the screwed end of the counterpart.
- Ensure that the surface of the taking part is perfectly
smooth and clean.
- Tighten the counterpart with a wrench (max. torque
3 Nm).
3.4 Installation steps for internal thread M5
- For sealing use an O-ring that fits properl y into the
groove. (O-ring is not included in the scope of delivery)
- Ensure that the surface of the counterp art is perfectly
smooth and clean.
- Screw the counterpart (e.g. screw connection, quick
coupling) by hand into the pressure switch.
- Tighten the counterpart with a wrench (max. torque
1 Nm).
4. Electrical Installation
WARNING
Danger of death from electric shock
- Switch off the power supply before
installing the device.
Electrically connect the device in accordance with t he
specifications given on the type plate, the following pi n
assignment table and the connection diagram.
Pin configuration:
Electrical connection
M8x1
(4-pin)
(L+)
(L-)
C/Q
Supply +
Supply –
IO-Link (COMx) / SIO
1
3
4
Shield housing
Wiring diagram:
SIO / IO-Link (COMx)-System
If possi ble, use a shielded and twisted multicore cable
for the electrical connection.
5. Commissioning
Before using the device for the first time, check that it
has been properly installed, and make sure that it does
not show any visible defects.
The device may by commissioned only by appropriately
qualified specialist personnel who have read and understood the user manual.
The transmitter shall be supplied by Limited Energy
Source (per UL 61010) or NEC Class 2 Power Source.
6. IO-Link Interface
6.1 General device information
Baud rate COM2 (38,4 kbit/s)
Input process data length 2 byte
Minimum cycle time 5 ms
IO-Link version0000000000 V 1.1
SIO-Mode yes
6.2 SIO mode (standard IO mode)
In this mode the sensor operates like a normal pressure
sensor with standard output signals. The digital output is
always on Pin 4 of the connector plug or over green cable.
6.3 IO-Link mode (communication mode)
The pressure sensor switches to the IO-Link communication
mode, when it operates under an IO-Link master. IO-Link
communication is only possible over Pin 4 of the connector
plug or over green cable.
6.4 Process data
The process data length of the sensor is 16 bits. The switch
state (BCD1) as well as the current me asured values are
transmitted. The 14 bits of the measured val ue are scaled
according to the measuring range.
15 bit 14…2 1 0
Signed
Bit
Measured
value
0 BDC1 / Output 1
6.5 Error codes
0x8011 Index not available
0x8012 Subindex not available
0x8023 Access Denied
0x8030 Parameter Value out of Range
0x8033 Parameter length overrun
0x8034 Parameter length under run
6.6 Event codes
Event-
Codes
IO-Link
1.1
EventCodes
IO-Link
1.0
Device
status
Type
No malfunction
0x0000 0x0000 0 Noti fica-
tion
General
malfunction.
Unknown
error
0x1000 0x1000 4 Erro r
Process
variable range
over-run.
Process Data
uncertain
0x8C10 0x8C10 2 Warning
Process
variable range
under-run.
Process Data
uncertain
0x8C30 0x8C10 2 Warning
6.7 Parameter data
The parameter data of the pressure switch correspond to the
Smart Sensor Profile. The data can be found in the product
data sheet or parameter overview, see section 13.
7. Decommissioning
WARNUNG
Danger of injury from media escaping under pressure
- Dismount in an orderly fashion when
the machine is depressurized and the
power supply has been switched off.
-
Check whether the medium needs to
be drained before dismounting!
WARNUNG
Danger of injury from the measured
medium
- Depending on the measured medium, suitable precautions should be
taken, e.g. protective gloves, goggles.
8. Maintenance
The device is, in principle, maintenance free. If necessary,
the housing of the device may be cleaned with a damp cloth
and a non-aggressive cleaning solution while it is switched
off.
With certain media may, however, deposits or contamination
may accumulate on the diaphragm. The specification of
appropriate maintenance intervals for inspection is recommended in this case. Once the device has been properly
decommissioned, the diaphragm can normally be cleaned
with a non-aggressive cleaning solution and a soft brush or
sponge. Care should be taken while doing so. If the diaphragm is covered in lime scale, decalcification by BD
SENSORS is recommended. See the Servicing/Repair
section with regard to this.
Incorrect cl eaning can result in irreparable damage to
the measuri ng cell. For this reason, you should never
use sharp objects or compressed air to clean the diaphragm.
9. Servicing/Repair
9.1 Recalibration
It is possible that the offset value or the scaling value may
shift during the lifetime of the device. This is indicated by a
deviation in the output signal value with reference to the set
measurement range start or end values re spectively. If either
of these two phenomena should occur after a prolonged
period of use, recalibration is recommended in order to
ensure a continued high level of accuracy.
9.2 Return
Whenever the device i s returned, no matter whether for
recalibration, decalcification, modification or repair, it must be
carefully cleaned and packed such that there is no risk of
breakage. The device must be accompanied by a notice of
return giving a detailed description of the fault. If your device
has come i nto contact with pollutants, then a notice of
decontamination will also be needed. You can find the
relevant templates o n our website at www.bdsensors.de.
Should you send i n your device without a notice of decontamination and do ubts with regard to the medium used
should arise in our service department, repair work will
commence only once an appropriate notice has been received.
CAUTION
Danger of injury from pollutants
- If the device has come into contact with
pollutants, wear suitable protective clothing, e.g. gloves, goggles, when cleaning
it.
10. Disposal
The device must be di sposed of in accordance with European Directives 2002/96/EC
and 2003/108/EC (Waste Electrical and
Electronic Equipment). W aste electrical
products may not be disposed of with
household waste!
Depending on the medi um used, residues
on the devi ce may constitute a hazard to
the environment. You should therefore ta ke
appropriate precautions if necessary and
dispose of the device properly.
11. Guarantee Conditions
The guarantee conditions are subject to the statutory warranty period of 24 months, starting from t he date of dispatch. No
warranty claims will be accepted i f the device has been used
improperly, modified or damaged. The warranty does not
cover damaged diaphragms. Warranty cover also excludes
any claims for defects that have arisen as a result of normal
wear.
12. Declaration of conformity / CE
The suppl ied device fulfills the statutory requirements. The
relevant directives, harmonized standards and documents
are listed in the EU Declaration of Conformity applicable to
the product. This can be found at http:// www.bdsensors.de.
In addition, the operational safety of the device i s confirmed
by the CE mark on the type plate.
Order code
Pin configuration
Type designation
Supply
Measure range
ID: BA_IS4_E | Version: 08
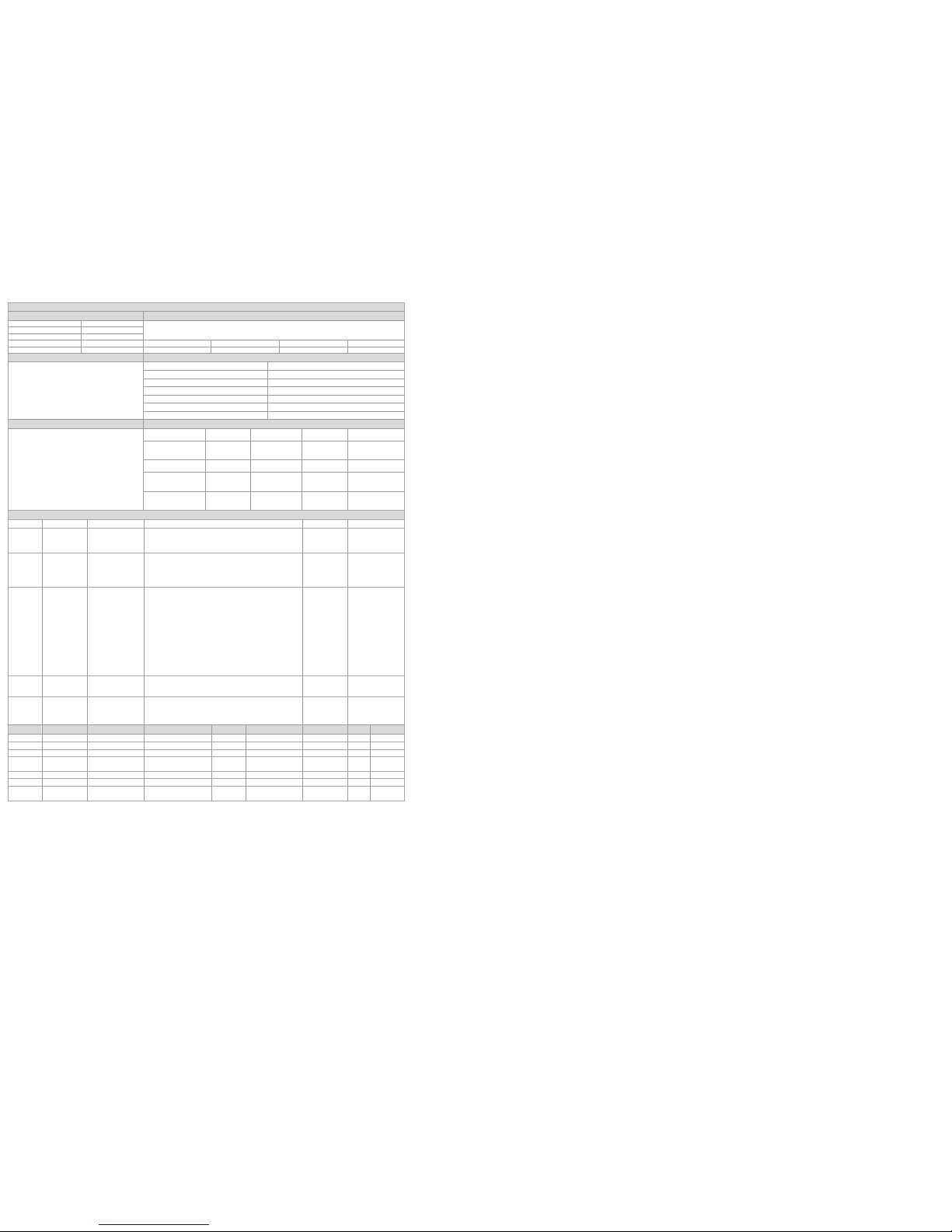
13. Parameter overview
IO-Link interface
1. General device information 4. Process data
Baud rate COM2 (38.4 kbit/s) The process data length of the sensor is 16 bits. The switch state (BCD1) as well as the current measured
values are transmitted. The 14 bits of the measured value are scaled according to the measuring range.
Input process data length 2 byte
Minimum cycle time 5 ms
IO-Link version V 1.1 15 bit 14 … 2 1 0
SIO mode yes Signed Bit measurement 0 BDC1 / output 1
2. SIO mode (standard IO mode) 5. Error message
In this mode the sensor operates like a normal pressure
sensor with standard output signals. The digital output is
always on Pin 4 of the connector plug.
Error Codes Description
0x8011 Index not available
0x8012 Subindex not available
0x8030 Parameter Value out of Range
0x8033 Parameter length overrun
0x8034 Parameter length underrun
3. IO-Link mode (communication mode) 6. Event codes
The pressure sensor switches into IO-Link communication mode when operating under an IO-Link master. IOLink communication is only possible via Pin connector.
IO-Link 1.0
Device status
Type
No malfunction
0x0000
0x0000
0 Notification
General malfunctionunknown error
0x1000 0x1000 4 Error
Process variable
range over-run -
Process Data uncertain
0x8C10 0x8C10
2
Warning
Process variable
range under-run.
Process Data uncertain
0x8C30
0x8C10
2
Warning
7. Parameter data (The parameter data for the pressure sensor correspon d to the Smart Sensor profile.)
Index hex Subindex hex Object name Single Value Default Comment
0x02 0x00 System Commands
0x81 = delete Min-/Max-Wert
0x82 = res
0xA0 = Set0
The action
is executed
by writing
in the subindex
0x03 0x00 Data Storage Index
0x01: Upload Start
0x02: Upload End
0x03: Download Start
0x04: Download End
0x05: Datastorage Break
0x0C 0x00 Device Access Lock
0x00: Unlocked
0x01: IO-Link Lock
0x02: Datastorage Lock
0x04: Parameterization Lock
0x08: User Interface Lock
0x03: IO-Link Lock + Datastorage Lock
0x05: IO-Link Lock + Parameterization Lock
0x09: IO-Link Lock + User Interface Lock
0x06: Datastorage Lock + Parameterization Lock
0x0A: Datastorage Lock + User Interface Lock
0x07: Datastorage Lock + IO-Link Lock + Parameterization Lock
0x0B: Datastorage Lock + IO-Link Lock + User
Interface Lock
0x00:
Unlocked
0x24 0x00 Device Status
0x00 Device is operating properly
0x02 Out-of-Specification
0x04 Failure
0x3D 0x02 Switch Point mode
0x80: Hysteresis NO
0x81: Hysteresis NC
0x82: Window NO
0x83: Window NC
0x80: HNo
Index hex Subindex hex Object name Access Length Value Range Gradient Unit Default
0x3C 0x01 SetPoint 1 = SP R/W 2 Byte Process Data 100%
0x3C 0x02 SetPoint 2 = rP R/W 2 Byte Process Data 0%
0xD0 0x00 Delay Switching Time R/W 2 Byte 0 ... 500 0.1 sec 0
0xD1 0x00 Delay Back Switching
Time
R/W 2 Byte 0 ... 500 0.1 sec 0
0xD5 0x00 Min Pressure Value R 2 Byte Process Data
0xD6 0x00 Max Pressure Value R 2 Byte Process Data
0xD7 0x00 Measure damping R/W 2 Byte 0…1000 in 10 ms
steps
1 ms 0