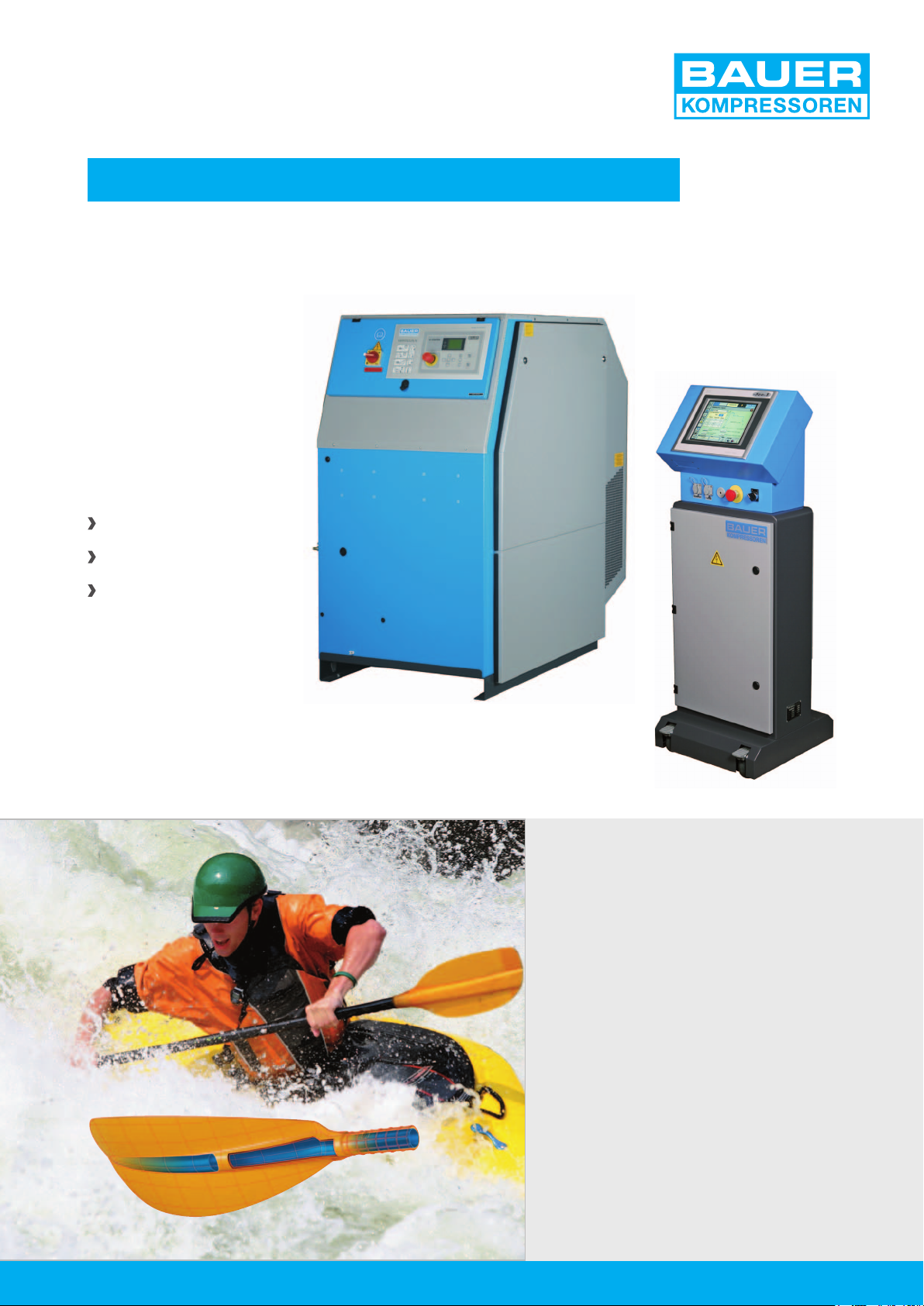
GAS INJECTION TECHNOLOGY – GIT
Innovative and complete solutions
ECONOMICAL
MODULAR
RELIABLE
www.bauer-kompressoren.de
BAUER KOMPRESSOREN
offer Gas Injection Technology
as a solution to the problems
of plastic part production.
The end user will benefit from
BAUER’s years of manufacturing
experience in the field of GIT and
compressor technology with tailormade systems from one source.
Bauer offer starter packs to complex
large-scale systems.
For a perfect system design, the
BAUER team is available and willing
to provide on site advice.
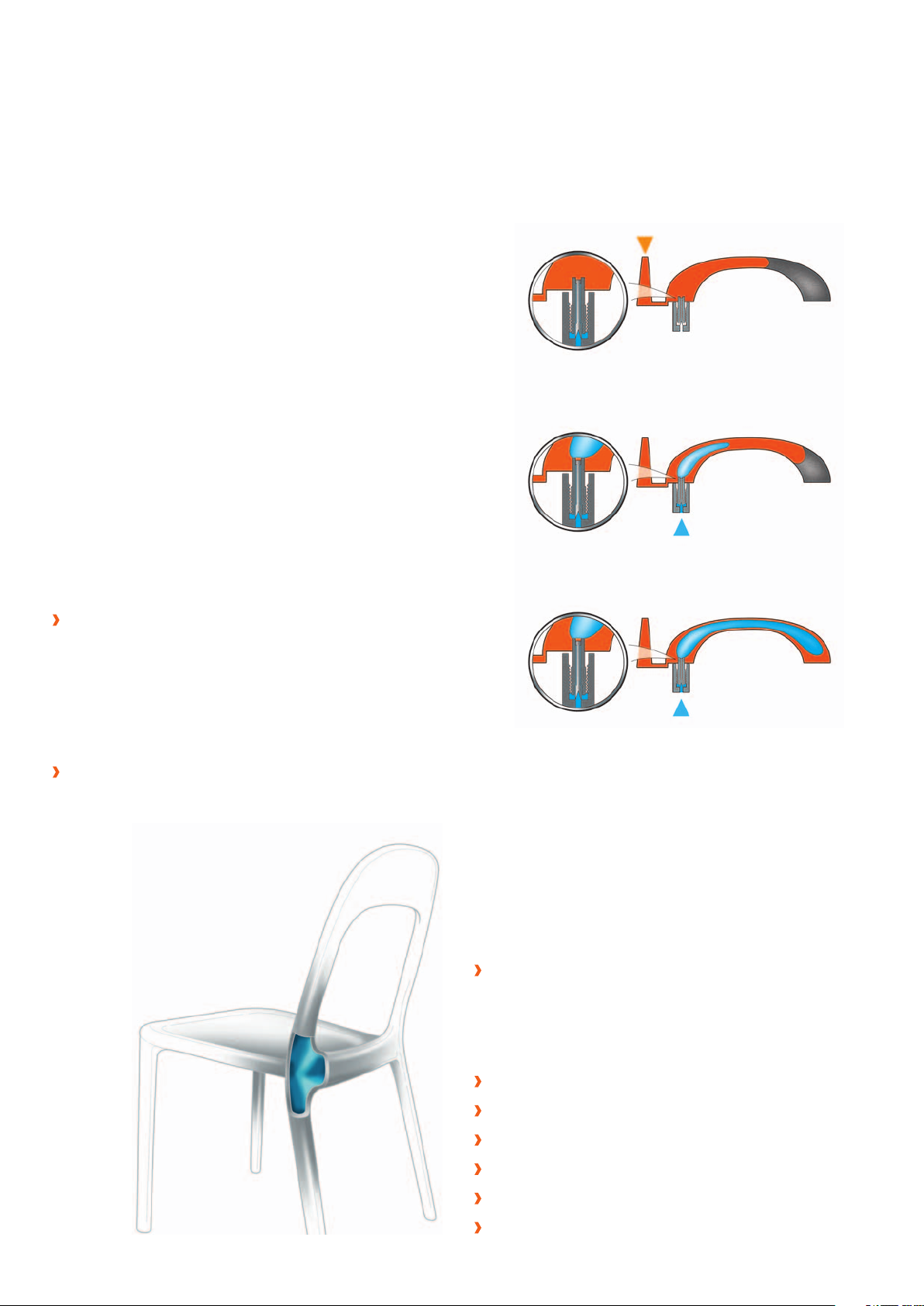
GIT-SYSTEMSBAUER KOMPRESSOREN
GIT technology from BAUER - solutions from one source
BRIEF OVERVIEW OF GIT TECHNOLOGY
A procedure similar to GIT was described for the
first time in 1972. This technology has a proven
reliability and market growth from the 1980’s.
We denote by GIT, the method of blowing gas,
especially nitrogen in the plastic, so that a hollow
tubular channel is created.
Previously, the plastic had been melted and injected
into a mould, which for thick pieces of plate, it was not
possible to produce a flattened bubble.
THE DIFFERENT TECHNIQUES
There are at least 10 variants of GIT, based on
the type of piece produced and its needs. The
two most commonly used techniques are briefly
explained as follows:
The partial original method, which is to fill 50-90%
of the cavity with plastic. By moving the mass of hot
plastic, the gas can finish filling 100% while creating
a hollow tubular channel. The holding phase under
pressure during the cooling phase is carried by the
gas, whose pressure drop just before opening
the mould.
Plastic
1
2
Gas
3
Gas
The over flow cavity, which requires the addition of
an annex cavity in the tool. After filling the part
cavity at 100% with polymer, the gas is injected
under pressure and the overflow cavity is
open to collect the superfluous plastic.
The gas ensures the holding phase
pressure during cooling and is
purged immediately
before opening
the mould.
BENEFITS OF GIT
The use of gas assisted injection technology
allows production of technical parts with
the appearance of superior quality. The
manufacturing process is also more efficient,
improving productivity and thus significantly
increasing profitability.
A better quality of injected part:
- High strength and rigidity
- Dimensional stability, no warpage
- Elimination of sink marks
- No assembly, single parts
Simplification of tools
Freedom in design
Lower clamping force (in partial)
Reduced cycle time
Material saving
Realization of hollow (pipe)
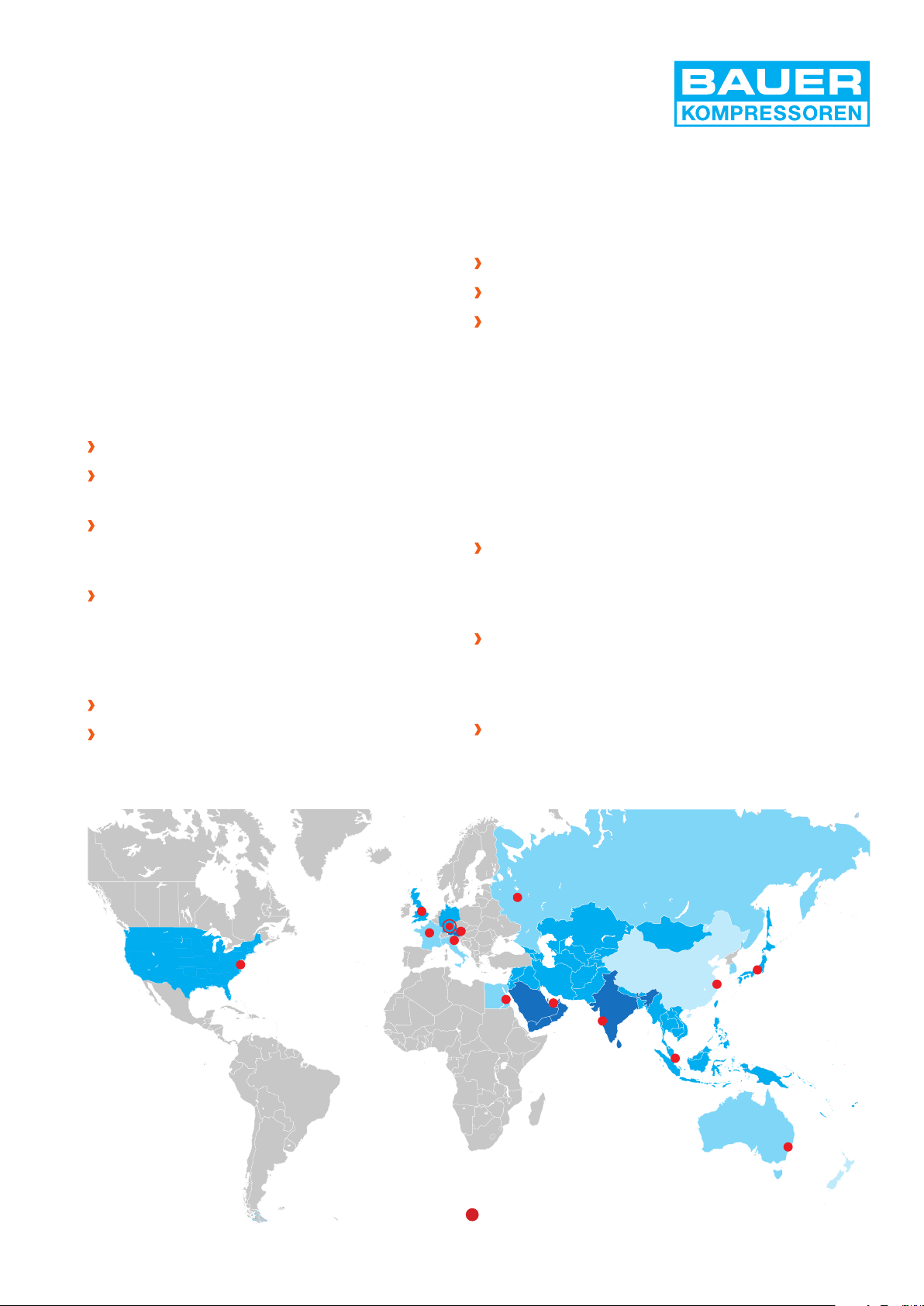
GIT-SYSTEMS
BAUER EXPERIENCE
Our outstanding expertise in purifying gases
coupled with software-based control technology developed by our BAUER specialists
guarantee you outstanding product quality
which will improve profitability.
HIGH PRESSURE COMPRESSOR
AND BOOSTER UNITS
Ready for use; compact and autonomous.
A compression of high quality nitrogen thanks
to our P-filter system.
Booster units with low power consumption by
using the inlet pressure of a nitrogen generator
or evaporator.
A security operation through an integrated
controller (B-CONTROL).
FCC CONTROL UNIT
A mobile and compact panel.
An adaptive control and therefore very precise
(reactivity adjustable).
Easy and intuitive programming.
A full connectivity to transfer files (USB and Ethernet).
Continuous process monitoring with quality data
storage.
EXCELLENT SERVICE GUARANTEED
For BAUER, „quality“ does not end with the production and delivery of the system. Independent
of the location of the installation, the customer
benefits from the excellent and comprehensive
after sales service support:
All major spare parts, including wearing parts, for all
models are permanently in stock, and available for
immediate dispatch. Parts are guaranteed to be
available for up to 25 years after delivery.
An integrated distribution network comprising of
over 50 overseas agencies, plus 360 support
distributors are continually available to support
our customers.
Maintenance kits for all systems are available
worldwide.
BAUER daughter companies worldwide
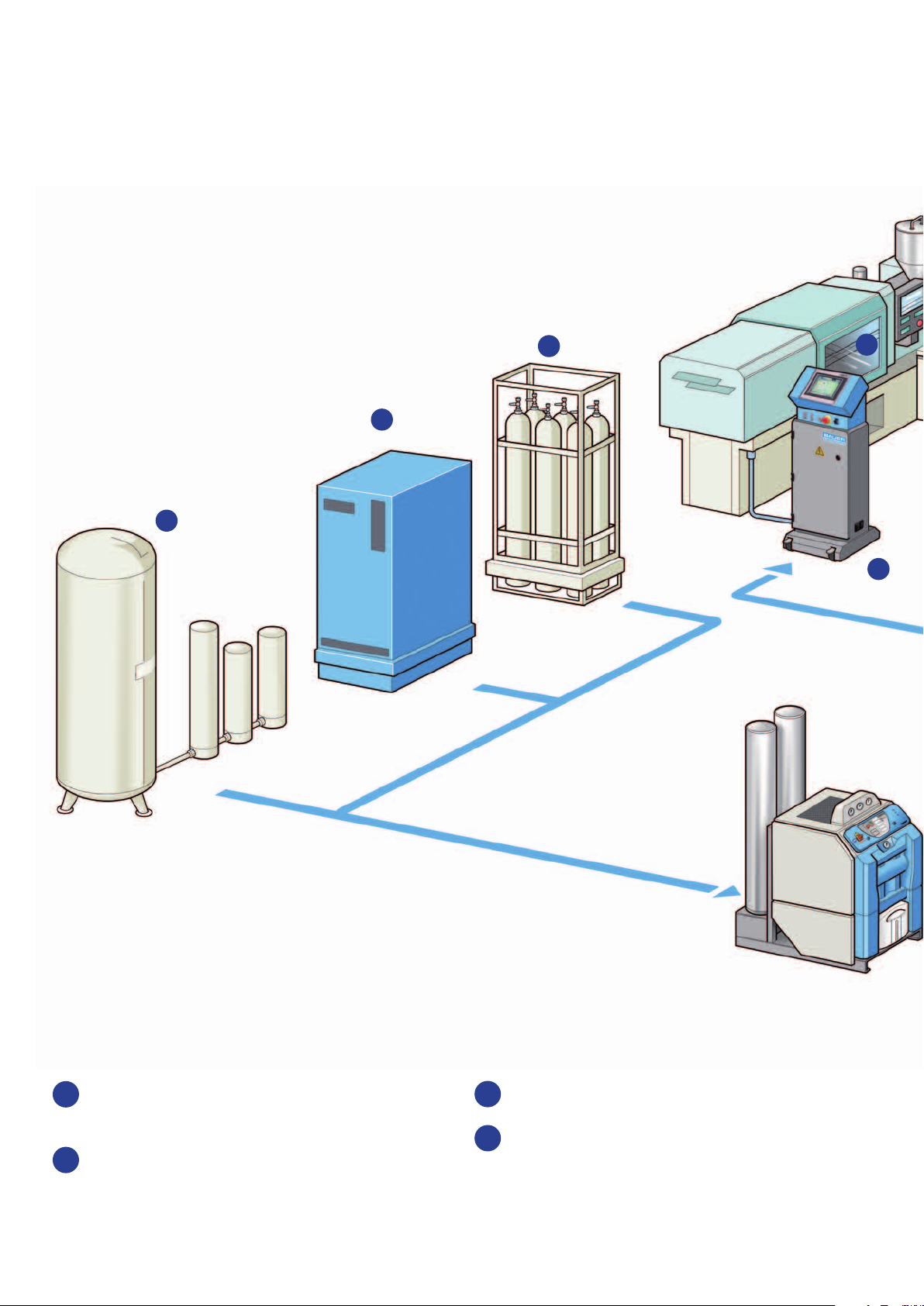
GIT-SYSTEMSBAUER KOMPRESSOREN
Structure of the system
System requirements: The following equipment is required to employ gas injection technology
in your process.
1
1
1
1
1
1
1
1
5
5
5
5
1
1
1
1
4
4
4
4
1
Source of nitrogen: Liquid tank, nitrogen
bottles or nitrogen generator.
2
A high pressure compressor with a suitably
sized gas receiver facility for the compression
and safe storage of nitrogen at high pressures.
3
High pressure lines to transport the nitrogen.
4
Distribution panel that generates a pressure- /
time profile to dispense the nitrogen.