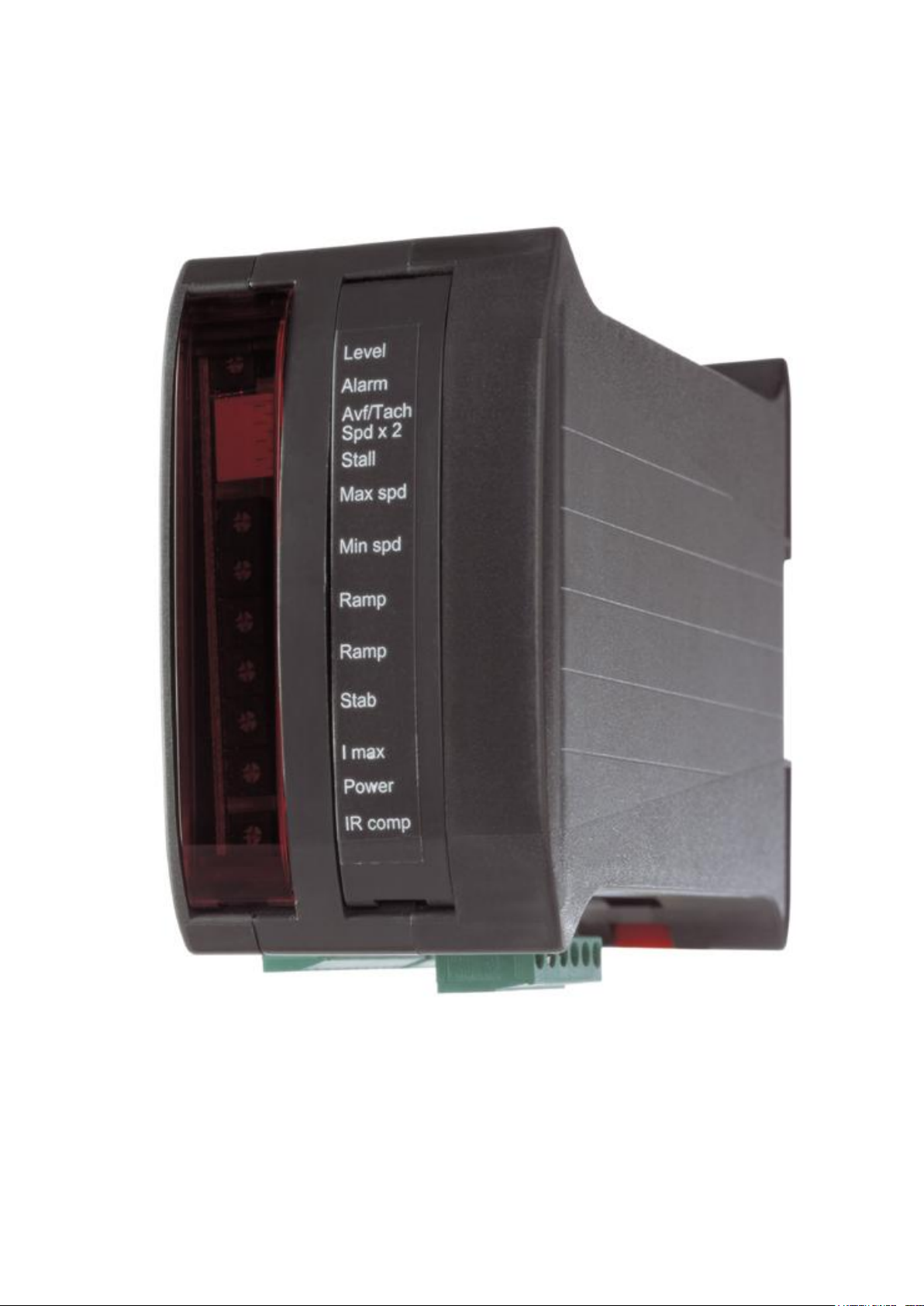
340i / 680i / 1220i Applications 1
- Data – Product manuals – Technical help – Drive glossary – FAQ – Brochures – Images – Data – Product manuals
K340i, K680i, K1220i Application manual.
w w w .barda c . c o m
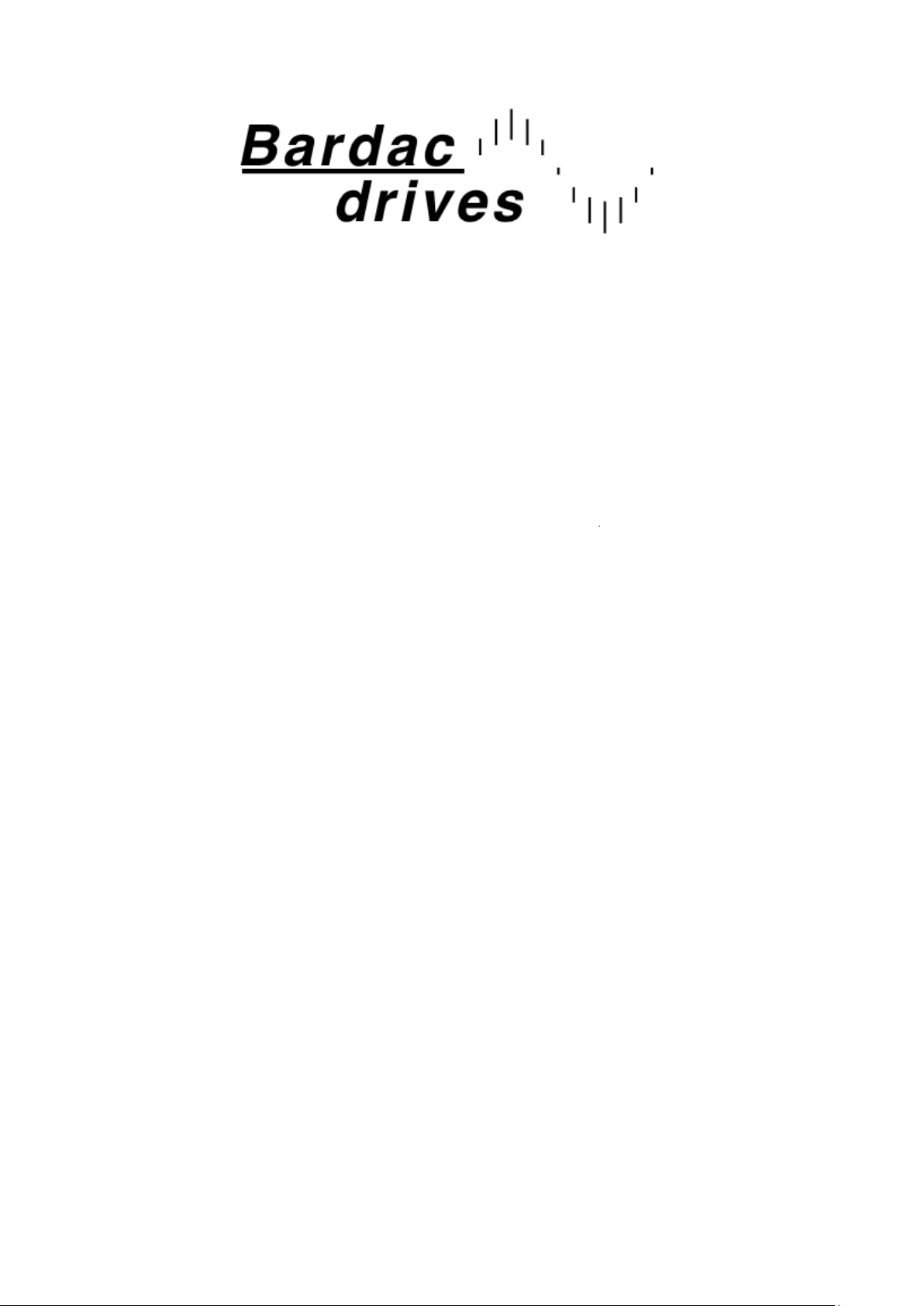
K340i / K680i / K1220i Applications 2
NOTE. These instructions do not purport to cover all details or variations in equipment, or to provide for every
possible contingency to be met in connection with installation, operation, or maintenance. Should further
information be desired or should particular problems arise which are not covered sufficiently for the purchaser's
purposes, the matter should be referred to the local Supplier sales office. The contents of this document shall
not become part of or modify any prior or existing agreement, commitment, or relationship. The sales contract
contains the entire obligation of Bardac Drives. The warranty contained in the contract between the parties
is the sole warranty of Bardac Drives. Any statements contained herein do not create new warranties or
modify the existing warranty.
HEALTH AND SAFETY AT WORK
Electrical devices can constitute a safety hazard. It is the responsibility of the user to ensure the compliance of
the installation with any acts or bylaws in force. Only skilled personnel should install and maintain this
equipment. If in doubt refer to the supplier.
Note. The contents of this document are believed to be accurate at the time of printing. The manufacturers,
however, reserve the right to change the content and product specification without notice. No liability is
accepted for omissions or errors. No liability is accepted for the installation or fitness for purpose or
application of the K340i / K680i / K1220i motor drive units.
1 Table of contents
1 Table of contents ....................................................................................... 2
2 340i Block Diagram and terminal listing. ............................................................ 3
3 Typical applications..................................................................................... 8
3.1 ON OFF switch with ramp to stop or coast to stop................................................................. 8
3.2 Zero reference interlock and Stop / Start pushbuttons. ......................................................... 9
3.3 Using an external 4-20mA speed signal ............................................................................ 10
3.4 Torque control ........................................................................................................... 11
3.5 Load sharing slave single direction. ................................................................................. 12
3.6 Low voltage speed feedback .......................................................................................... 12
Bardac Corporation
40 Log Canoe Circle
Stevensville, MD 21666 USA
Phone: (410)604-3400 Fax: (410)604-3500
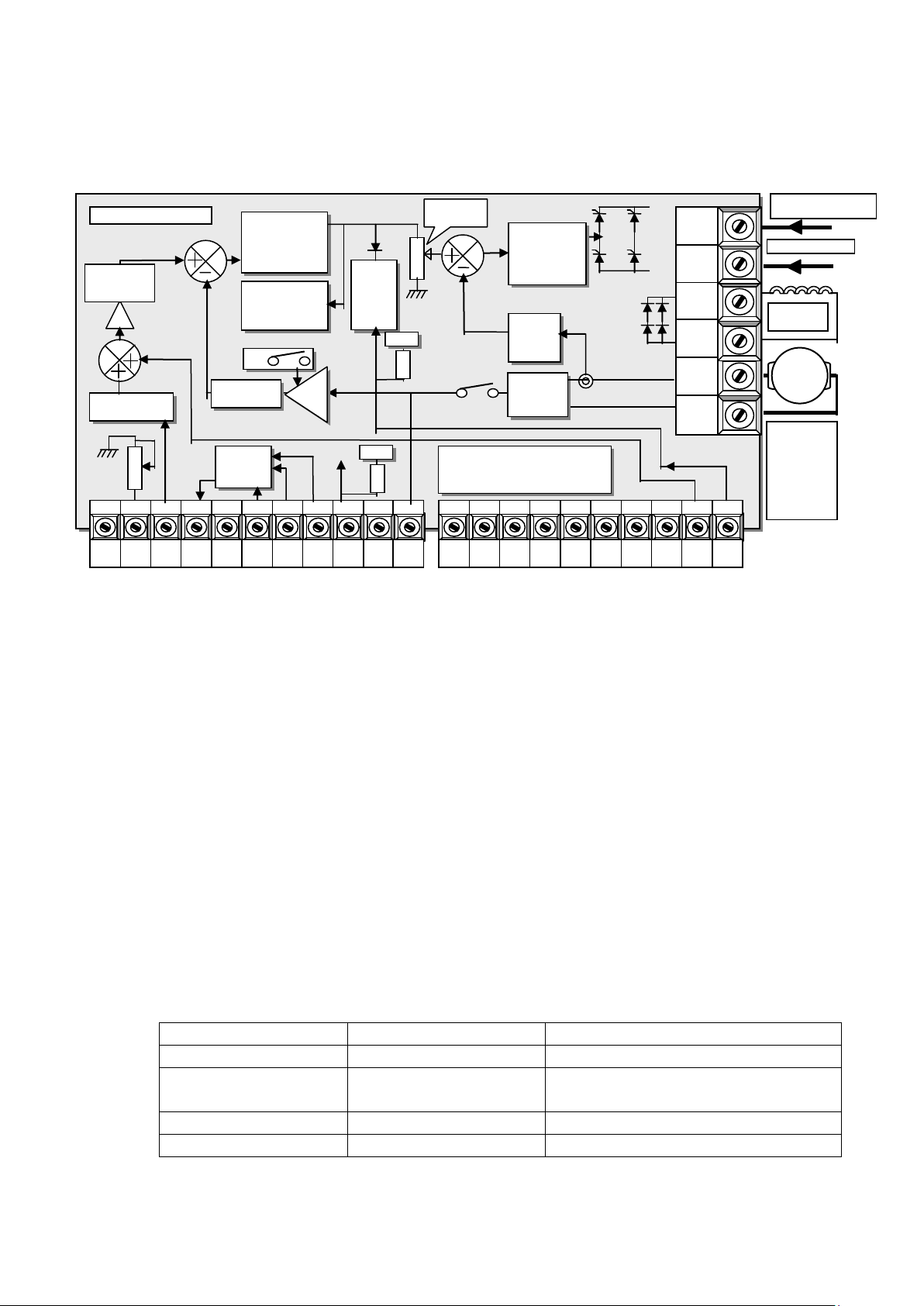
K340i / K680i / K1220i Applications 3
Input T6 to output T4 mode
Remains in prevailing mode.
Powers up in invert mode.
Non-invert (0 to +10.5V range)
Up / Down Ramp
OP on T16. ROP
Speed P+I error
amplifier with
stability preset.
Output provides
current demand.
Arm Amps
Isolation
Amplifier.
IOP on T19
Total speed
demand DEM
on T17 (-ve)
Arm Volts
Isolation
Amplifier
30 Sec Stall timer
with logic outputs
TRIP on T15 and
Overload on T14
Current
Demand
Clamp.
0 - 5V on
T21 =
0 -100%
Centre zero comparator with window
threshold from +/-50mV to +/-10.5V
Goes high on T12 (0-10V. 10mA) if
+/- signal input T13 exceeds window.
Current P+I error
amp with phase
angle controlled
anti-parallel
bridge.
Armature.
For armatures
with a time
constant of
less than 5mS
a DC choke
must be wired
in series.
AC supply must be
semi-conductor fused.
2 K340i Block Diagram and terminal listing.
K340i/680i/1220i
1 +10V output. 10mA max. (Use a 10K Ohm pot for external speed reference).
2 MIN SPEED. (Bottom end of external pot. 5K Ohms preset to common).
3 IP. Speed input. 0 to +/-10V speed input from pot wiper. 47K internal pull down.
4 OP+/-. +/-10.5V range. Input from T6. Invert with pushbutton input T8 open. Non-
invert with pushbutton input T7. 10mA max.
5 COM. Common. (0 Volts)
6 IP+/-. Input to pushbutton controlled +/- signal channel. OP on T4. 50K Ohms
impedance for invert mode, 10M input impedance in non-invert mode.
Note. This channel can invert input signals in the range +/-10.5V. It can also buffer
(i.e. non-invert) signals in the range 0V to +10.5V. (It cannot buffer negative signals.
If you try to buffer a negative signal the output will be positive).
Note. If using a high resistance external pot for positive signals e.g. greater than
20KOhms, then this channel can be used to buffer it using the non-invert mode.
7 PB+ Pushbutton input. 47K Ohm pull up to +12V. Connect to T5 COM. Latches T4 to
buffer (non-invert) positive T6 signals when opened, provided T8 PB- is connected to
T5 COM.
8 PB- Pushbutton input. 47K Ohm pull up to +12V. Connect to T5 COM. Latches T4 to
invert T6 when opened. T7 PB+ may be open or connected to T5 COM.
See truth table below for T7 and T8 operation. See terminal 6 IP+/- for notes.
a) Hence if PB+ Terminal 7 remains open then a switch on PB- Terminal 8 can be
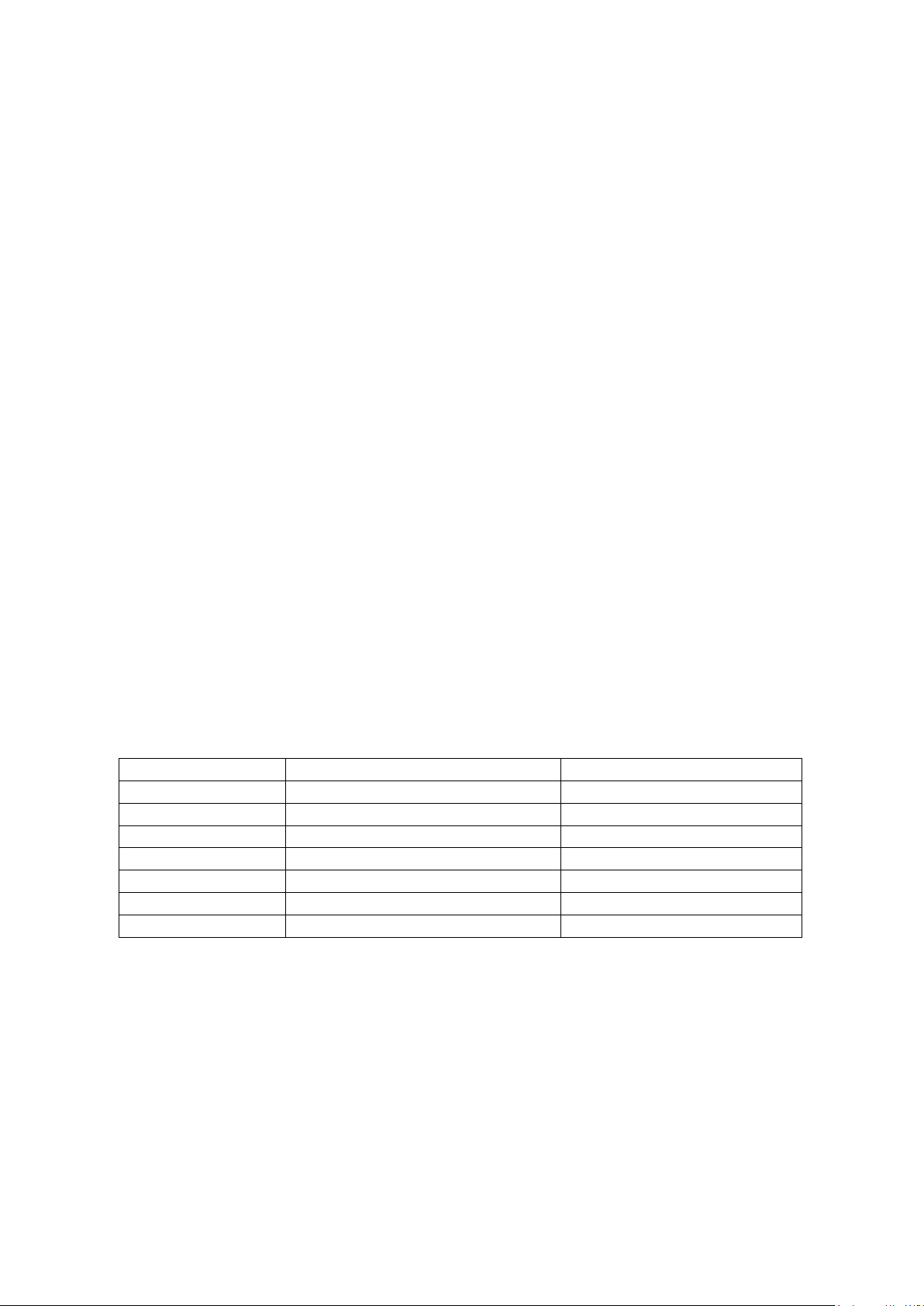
K340i / K680i / K1220i Applications 4
Typical current limit available
used to change modes.
b) If both PB+ Terminal 7 and PB- Terminal 8 remain open then the invert mode is
established.
c) If both PB+ Terminal 7 and PB- Terminal 8 are connected to common then the
desired mode can be established by momentarily opening PB+ Terminal 7 for noninvert, or PB- Terminal 8 for invert mode. The mode remains latched when the
common connection is re-established. This is useful for end of travel reversal. To
implement, connect T1 +10V to T6 IP+/- and use the T4 OP+/- as the reference to
the external max speed pot. Then connect the normally closed contacts from
microswitches on the track, to the pushbutton inputs T7 PB+ and T8 PB- such that
when the load reaches and opens the microswitch it toggles the reference in the
opposite direction.
9 RUN. Internal 12K pull up to +12V. Open to stop, close to COMMON to run. WARNING.
RUN is an electronic inhibit function. The field remains energised, and all power
terminals ‘live’. RUN must not be relied on to ensure the machine is stationary
during hazardous operations. Remove the power source to the system.
Opening T9 RUN will cause immediate drive inhibit and hence if the motor is
rotating at the time it will coast to zero speed.
10 COM. Common. (0 Volts)
11 TACH input. The tach must be opposite polarity to speed input. 1.5 MOhms.
12 RLOP. Relay driver. +10.5V active high. Flywheel diode to COM.
Note. The output is current limited. When in current limit, the output voltage
achieved, depends on the resistance of the load multiplied by the available current
limit at that voltage, according to the table below.
When driving relays, ensure the coil operating range is suitable. E. g. a 12V relay
with a coil operating range of 80-110% will energise at voltages of 9.6V and above
(80% of 12V). Hence it must have coil resistance greater than 633 Ohms for the
output to be capable of achieving the desired voltage. (See table above).
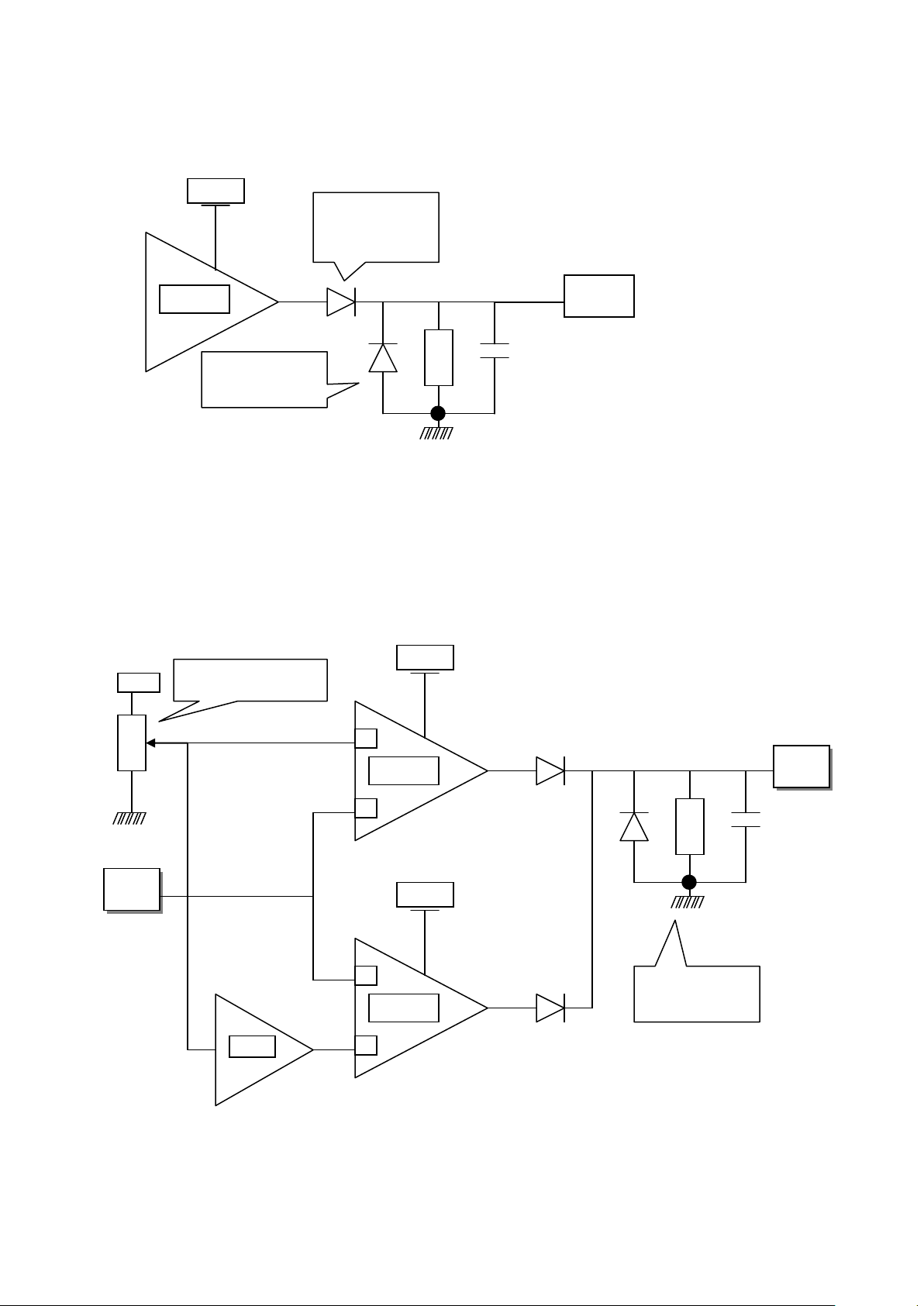
K340i / K680i / K1220i Applications 5
Flywheel diode,
47K resistor and
47nF capacitor
This diode allows
relay outputs to
be OR'd together
if desired,
Flywheel diode,
47K resistor and
47nF capacitor
Level preset range
0.5% to 105%
Diagram of relay driver output stage
terminal
13 RLIP. Relay driver input. Accepts 0 to +/- 10.5V signal inputs. The threshold to
activate the relay driver is symmetrical around zero, and set by the RELAY preset
between +/- 0.05V and +/-10.5V. When the T13 input exceeds the positive or
negative threshold, then the T12 RELAY DRIVER OUTPUT is turned ON. Typical uses
include zero speed detector, zero current detector, stall detector etc.. The
input will accept any output provided on other control terminals. 50K Ohm pull
down to common.