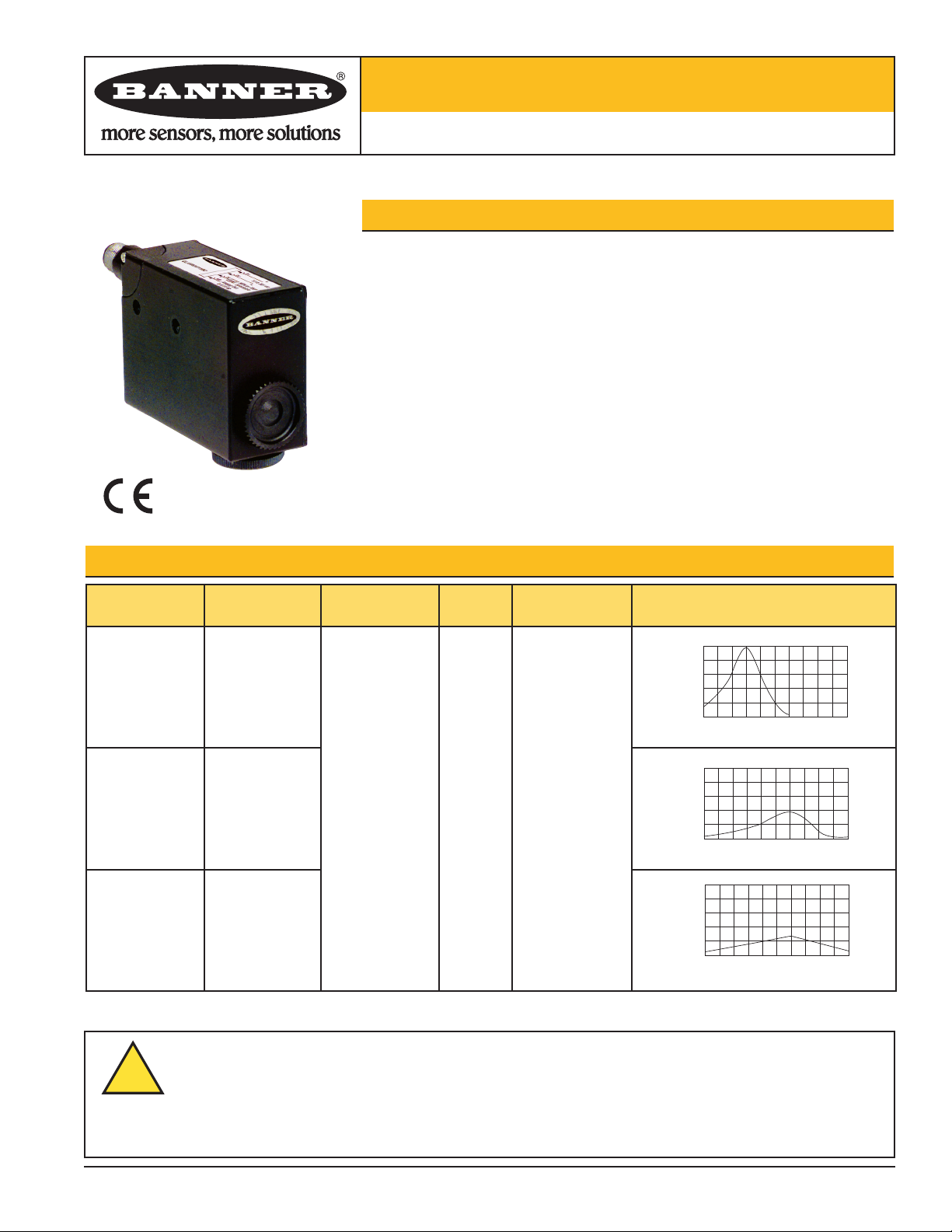
QL55 Series Luminescence Sensor
Relative Received Signal
Sensing Distance
0
0
10 mm
(0.4")
20 mm
(0.8")
30 mm
(1.2")
40 mm
(1.6")
50 mm
(2.0")
20%
40%
60%
80%
100%
Relative Received Signal
Sensing Distance
0
0
10 mm
(0.4")
20 mm
(0.8")
30 mm
(1.2")
40 mm
(1.6")
50 mm
(2.0")
20%
40%
60%
80%
100%
Relative Received Signal
Sensing Distance
0
40 mm
(1.6")
30 mm
(1.2")
50mm
(2.0")
60 mm
(2.4")
70 mm
(2.8")
80 mm
(3.2")
20%
40%
60%
80%
100%
Self-contained, microprocessor-based luminescence sensor
Features
• Self-contained design in a robust, compact metal housing
• High sensitivity
• Microprocessor-controlled
• Senses luminescent marks, even on luminescent backgrounds
• Senses luminescence on reflective surfaces, such as ceramic, metal, or mirrored
glass
• Easy-to-set sensing threshold
• Fast 250-microsecond sensing response time; high 2 kHz switching frequency
• Switch-selectable NPN or PNP discrete output, plus 0 to 5.5V dc analog output
• Switch-selectable output OFF-delay
• 3-position swivel QD connector
Models
QL55M6XD15BQ
Sensing
Range
9 to 18 mm
(0.35" to 0.71")
Cable/
Connector*
4-pin Euro-style
(M12)
QD connector
with 3-position
swivel
QL55M6XD30BQ
20 to 40 mm
(0.79" to 1.57")
(locking
screw-secured)
QL55M6XD50BQ
40 to 75 mm
(1.57" to 2.95")
* Mating cable required; see back cover for cable options.
Models
Supply
Voltage
10 to
30V dc
Outputs Sensor Performance
One selectable
NPN or PNP
discrete plus
one
0 to 5.5V dc
analog
WARNING . . .
Not To Be Used for Personnel Protection
Never use these products as sensing devices for personnel protection. Doing so could lead to serious injury or death.
These sensors do NOT include the self-checking redundant circuitry necessary to allow their use in personnel safety
applications. A sensor failure or malfunction can cause either an energized or de-energized sensor output condition. Consult your current
Banner Safety Products catalog for safety products which meet OSHA, ANSI and IEC standards for personnel protection.
Printed in USA 02/05 P/N 112153 rev. C
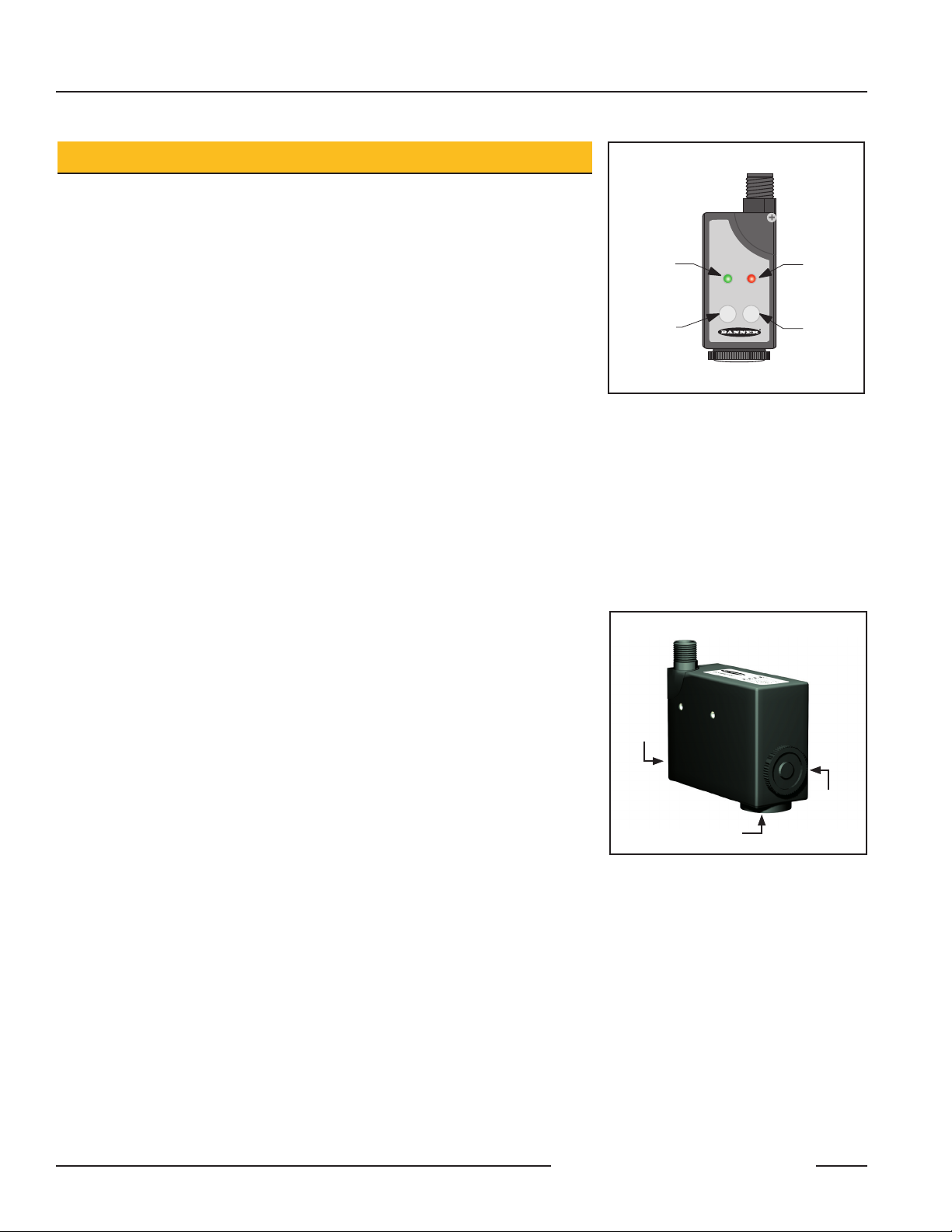
QL55 Series Luminescence Sensor
READY OUT
MARK
BKGD
Red
Output LED
Green Ready/
Overload LED
(Power ON
Indicator)
Mark
Push Button
Background
Push Button
Overview
The QL55 Series Sensor is an easy-to-use, extremely sensitive microprocessor-based
luminescence sensor that emits ultraviolet light from a high-power LED and scans for
luminescence in materials. The QL55 senses the luminescence inherent in a material,
or it can sense luminophores added to a material in process to make it luminescent.
The sensor can be set to accurately sense a wide range of luminescence intensities
and background conditions. The two-step QL55 Sensor programming procedure
sets the threshold for target luminescence and background. The Luminescent Target
condition is taught first, followed by the Luminescent Target Absent (background)
condition. During operation, the sensor outputs will be ON when the luminescent
target object is present, and OFF for the background condition. (The sensor may
instead be taught to respond to the Background condition; see page 3.)
Located within the QL55 Sensor, two selector switches may be used to enable an
output OFF-delay option and for setting the discrete output to NPN or PNP (see Figure
5). The QL55 is available with one of three operating ranges, to a maximum of 75 mm
(2.95"), depending on the model.
The sensor housing has two push buttons, Mark and Background, for easy
programming; it has two LEDs, Ready/Overload and Output, for easy monitoring
during operation. See Figure 1.
Figure 1. QL55 Luminescence Sensor
features (sensor back)
For easier understanding, the sensor faces are described in this data sheet as labeled
in Figure 2. The key pad is considered the sensor back, and the lens is on the bottom.
Luminescence Sensing
Luminescence sensing detects a form of electromagnetic radiation, caused by the
shining of UV light (“black” light, invisible to the human eye) on a luminescent
substrate material, such as a petroleum-based adhesive. When the UV light shines
on the adhesive, the light “excites” electrons in the material (effecting a change of
state), causing it to reflect visible light. Thus an invisible light source can produce a
visible reflection. Because it emits UV light but detects visible waves, the sensor can
distinguish between the fluorescent material and other highly reflective materials.
Cost Factors
When comparing luminescence sensors to make a selection, it is important to
consider whether luminophores must be added to the product sensed, in order for
the sensor to detect luminescence. Generally speaking, the more sensitive the sensor,
the lower the level of luminescence required for detection. Less sensitive (and usually
less expensive) sensors may require an additional step in the production process, and
a substantial cost over time, to add luminophores. For information on less expensive,
less sensitive luminescence sensor models, refer to data sheet p/n 112151, Model
QL50 Luminescence Sensor, or contact a Banner applications engineer for more
information (see back page for addresses).
Top
Back
Key
Pad
Bottom
Lens
Figure 2. QL55 orientation of features
Front
Blanking
Plug
2 P/N 112153 rev. C
Banner Engineering Corp. • Minneapolis, MN U.S.A.
www.bannerengineering.com • Tel: 763.544.3164
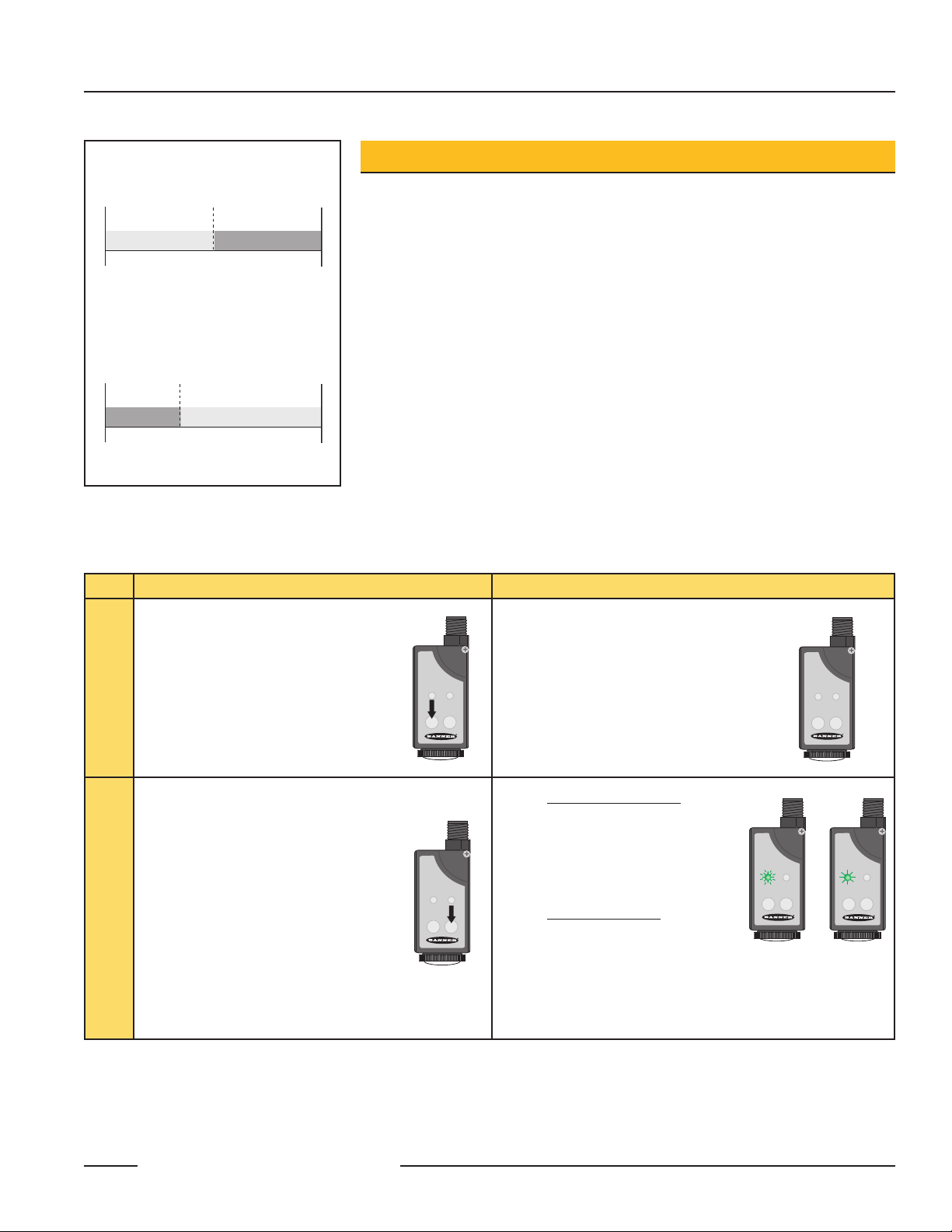
Output OFF Output ON
Less Luminescent
Condition
More Luminescent
Condition
Less Luminescent
Condition
More Luminescent
Condition
Least
Luminescent
Most
Luminescent
Output OFFOutput ON
Least
Luminescent
Most
Luminescent
Light Operate
Dark Operate
Figure 3. Sensor automatically selects light
READY OUT
MARK
BKGD
OUTREADY
MARK
BKGD
then
operate or dark operate, when
configured as described below
QL55 Series Luminescence Sensor
Sensor Configuration
In this simple two-step procedure, the sensor samples the luminescence levels of
both the target (Mark) and the background (Background) conditions. The sensor
automatically selects light operate or dark operate (see Figure 3) based on the relative
luminescence of the two conditions. Using the procedure described below, sensing
the more luminescent condition (in this case the target to be sensed) will close the
normally open output, turn on the red Output LED, and cause the output to conduct
current (light operate).
If the application requires the output to conduct for a less luminescent condition,
reverse the procedure (dark operate):
• Present the less luminescent condition first (Mark push button) and then
• Present the more luminescent condition (Background push button).
Condition
SET Output ON
Condition
SET Output OFF
Procedure Result
• Position luminescent target in front of
sensing lens.
• Press Mark push button (approx. 4 sec.)
until green Ready LED turns OFF.
• Remove luminescent target from
sensor’s field of view.
• Press and hold Background push button
(approx. 4 sec.) until green blinks.
Green Ready LED: turns OFF
Red Output LED: OFF
Green Ready LED stays OFF, and
sensor stores the Output ON condition.
Programming Accepted
Green Ready LED: Flashes 1x, then ON
Red Output LED: OFF
Green Ready LED stays ON, and
sensor stores the Output OFF
(background) condition.
Programming Error
(Due to insufficient contrast between
target and background luminescence)
Green Ready LED: flashes slowly (approx. 2 Hz)
Repeat programming procedure from the beginning.
If programming fails again, increase the target luminescence or
subdue the background.
P/N 112153 rev. C 3
Banner Engineering Corp. • Minneapolis, MN U.S.A.
www.bannerengineering.com • Tel: 763.544.3164