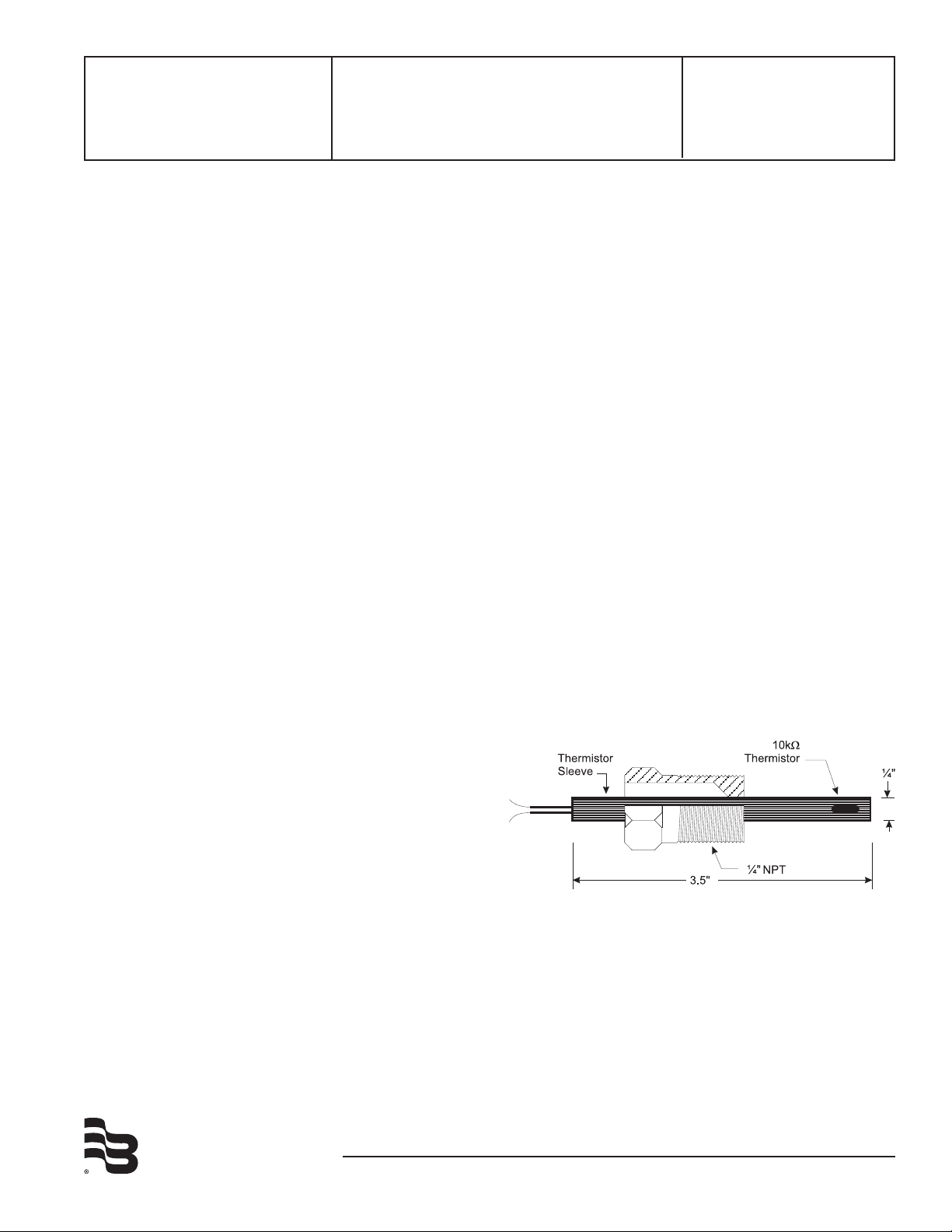
Badger® T-Series
Series 340, 1550 &
2300
2-Wire 10K Thermistors Btu Monitor
Temperature Sensors
Technical
Brief
Badger Meter's Series 340 Btu T ransmitter , 1550 Energy Monitor,
and 2300 Btu Energy Monitor each require two temperature
sensors, as well as a flow sensor , to operate. The proper selection
and placement of the temperature sensors is extremely important
to the operation of these Btu monitors. There are a number of
options available to help maximiz e the efficiency of Btu monitoring.
The following are a f e w hints to help fully take advantage of the
Badger Meter monitoring capabilities.
The temperature sensor is based on a 10kΩ thermistor. A
thermistor is actually a resistor made of specific semiconductor
material whose resistance decreases as the temperature around
it increases. Thermistors should NO T be confused with thermocouples, which are fabricated from two dissimilar conductors
joined at the ends, as where the junction is heated, the voltage
across it becomes proportional to the rise in temperature.
The actual resistance values for Badger Meter thermistors are
based on all temperature sensors being 10kΩ resistance at
25° C. 25° C is the industrial standard used as the main point
of reference for most thermistor calibration. The following chart
references the change in resistance values relative to changes
in temperature. Note that at 25° C (77° F) the resistance value
is 10,000 ohms.
°C °F Resistance
0 32 32,654 Ω
10 50 19,903 Ω
20 68 12,493 Ω
25 77 10,000 Ω
30 86 8,056 Ω
40 104 5,325 Ω
50 122 3,602 Ω
60 140 2,488 Ω
70 158 1,753 Ω
80 176 1,257 Ω
90 194 917 Ω
100 212 679 Ω
The simplest temperature sensor option is a 1/4 inch tube, 3 ½
inch long with ½ inch NPT pipe connections. The thermistor is
potted solid inside the tube fixture. The potting is used to eliminate
any air pockets from forming around the temperature sensitive
areas of the 10kΩ thermistor. If air is present, it will act as an
insulation barrier to the thermistor, adversely affecting the heat
transfer coefficients of the tubing wall, the potting material, and
the semiconductor material itself. The quality built into the Badger
Meter temperature sensors allows minimum variation from sensor
to sensor. Each temperature sensor can be replaced without
affecting either the other temperature sensor or the accuracy
of the Btu calculations. Individual circuit adjustments are NOT
required when changing temperature sensors.
PROTECTING TUBE CONFIGURATION
Badger Meter temperature sensors are available as a thermistor potted in protecting tube for direct insertion or for use with a
thermowell. The T106 has an adjustable length and a ¼” process
connection so it can be used in line sizes from ½” and up. The
sensing portion of the probe is at the tip and must be mounted
so that the tip is completely immersed in the direct fl ow stream.
All sensors measure not only the fl uid they are in, but also the
mass and effect of their own body to the fl uid stream.
For higher velocity or pressure systems or for industrial applications in larger pipe sizes, we suggest that thermowells be used.
A thermowell is a sleeve assembly that protects the temperature
sensing device from direct damage by higher velocities, and also
allows ease in service or replacement of the thermistor elements
without draining or shutting down of the fl uid system.
Badger Meter thermistors' accuracy is ±0.2° C. They can
operate accurately from 0° C (32° F) to 70° C (158° F) with
maximum temperature of 110° C (230° F), and are designed
for use with liquid heating and cooling media. The maximum
distance between a temperature sensor and any Badger Meter
Btu monitor is 500 feet.
BadgerMeter, Inc.
DTB-030-01
4-09
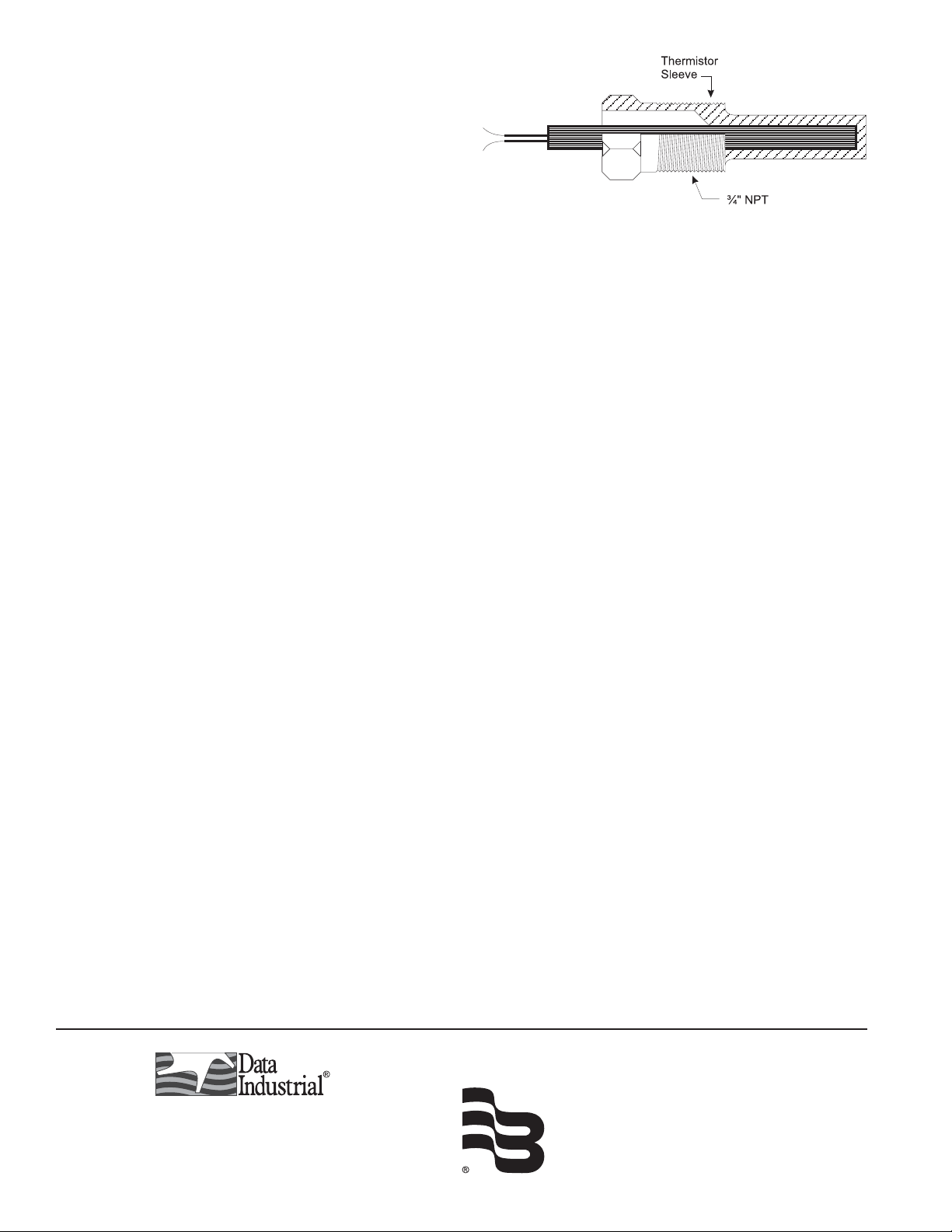
THERMOWELL STYLE
Thermowells also allow deeper sensor penetration into larger
piping systems. A general rule is to allow the sensing area of the
thermowell to be as close to the actual center of the pipe I.D. as
practical. This helps make the response time of the thermistor
faster and more representative of the actual fluid temperature.
Badger Meter offers a number of optional thermowells. When
the actual thermistor sleeve is mounted at the bottom of the thermowell, make sure some type of heat transf er material (silicone
grease) is used to fill the area between the I.D . of the thermowell
and the O.D. of the thermistor tubes. This mater ial serves the
same purpose as potting the actual thermistor element in the
tube assembly previously discussed. The thermistor sleeve is
held in the thermowell by a threaded retainer.
Badger® and Data Industrial® is a registered trademark of Badger Meter, Inc.
Due to continuous research, product improvements and enhancements, Badger
Meter reserves the right to change product or system specifications without notice,
except to the extent an outstanding contractual obligation exists.
Please see our website at www.badgermeter.com
for specific contacts.
Copyright © Badger Meter, Inc. 2009. All rights reserved.
BadgerMeter, Inc.
P.O. Box 581390, Tulsa, Oklahoma 74158
(918) 836-8411 / Fax: (918) 832-9962
www.badgermeter.com