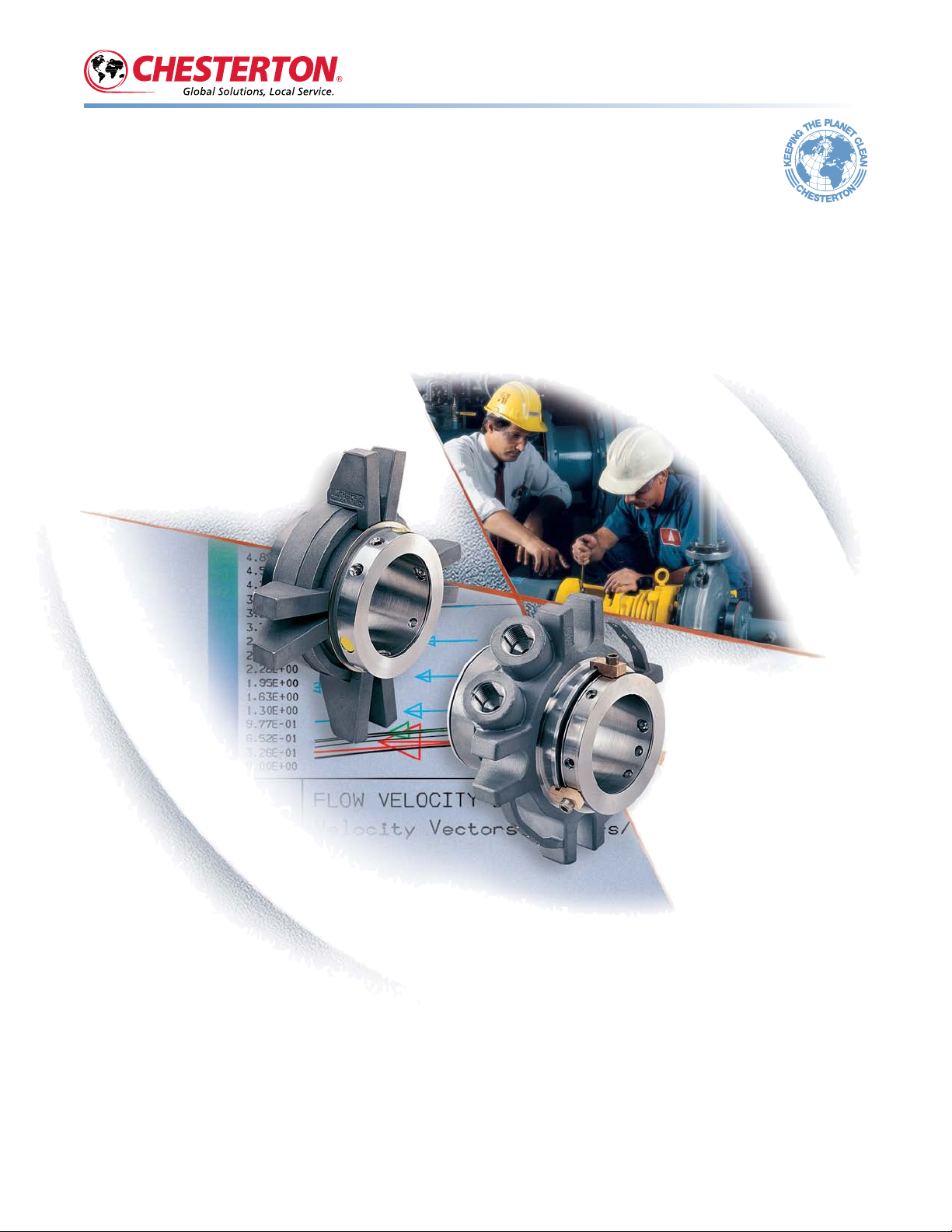
TM
155TM Single and 255
Dual
Cartridge Seals
Patented
n Global acceptance and satisfaction across a variety of industrial applications
n Exclusive face design for superior emissions control capability
n Stable, secure sealing under fluctuating conditions
n Patented features assure precision alignment from start-up
n Versatile and cost-effective
ISO 9001
CERTIFIED
Delivering the best value
in cartridge sealing today
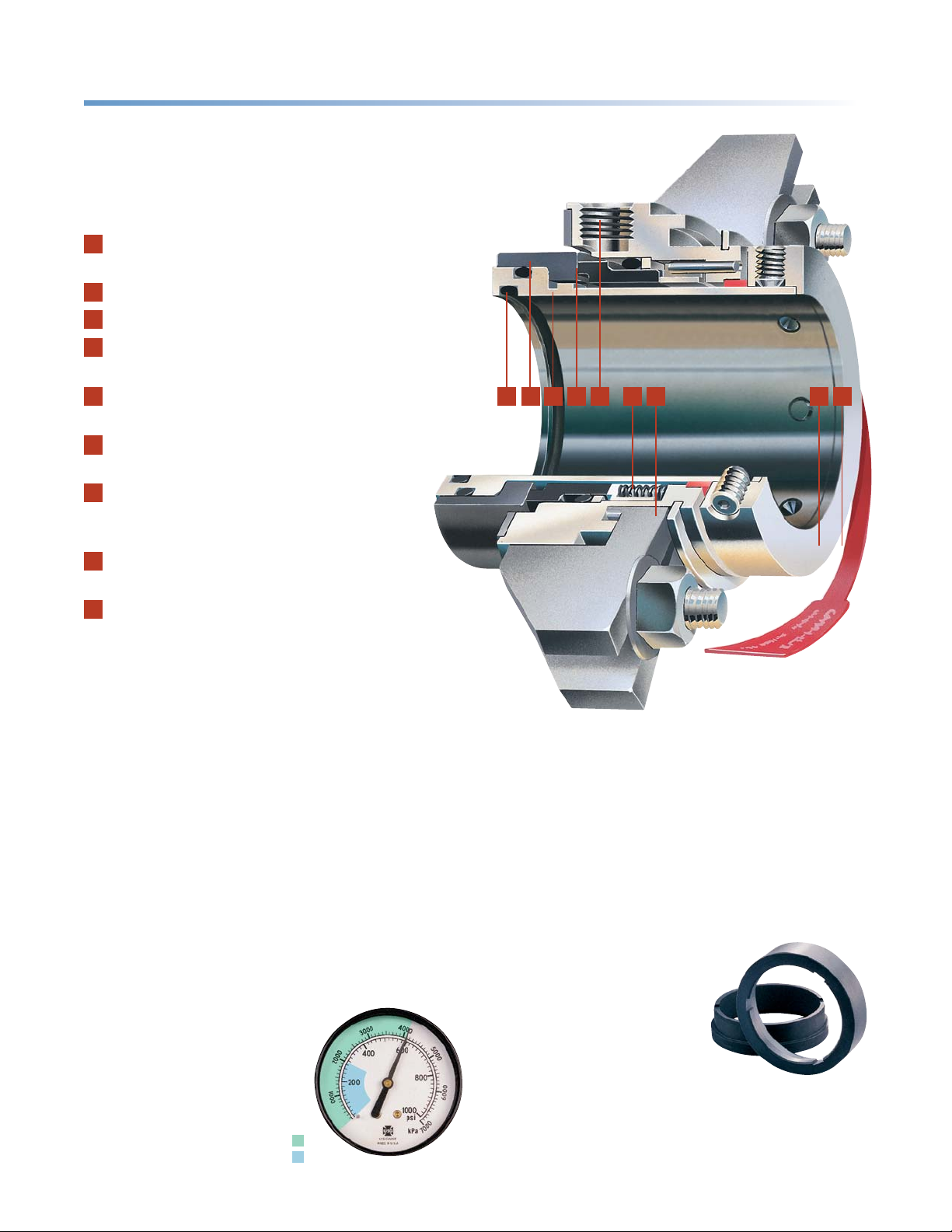
CHESTERTON
®
155TM
Cartridge Single Seal
Construction Details
1
All O-rings are either static or move on
non-metallic, non-fretting surfaces.
2
Seal face support shoulder is precisely square.
3
Integral drive pads cannot fall out.
4
Hydraulically balanced faces
for low frictional heat.
5
Flush port can be rotated 360° for ease
of piping as required.
6
Stationary springs, isolated from fluid
to prevent clogging.
7
Patented Adjustable Gland™
fits common bolt arrangements
without modification.
8
Self- Centering Lock Ring™
for superior concentricity.
9
Centering strap for simple installation.
1•2•3•4•5•6•7
8•9
•
•
Self-Centering Lock Ring™
ensures reliability
The patented Self-Centering Lock Ring
makes installation precise for correct face mating
and sustainable sealing. Cloverleaf 3- point
contact ensures concentricity to the shaft.
Faces start out square and stay square to prevent
the intrusion of contaminants or abrasives.
Also, constant face squareness reduces
opportunities for fluid leakage and uneven wear.
Superior reliability
during system variations
Pressure surges at start-up and
shut- down can create seal reliability
problems. The 155 seal can handle
50% to 100% greater transient
pressure than conventional seals
and provides a “margin of safety”
during normal surges.
CHESTERTON 155 Seal
Conventional Seal
Dynamic stress relief keeps faces closed
Variances in temperature or pressure, fluid phase changes,
or water hammer can create dynamically changing
stresses on the seal faces. Common face geometries
distort at the mating surface under such conditions
and create drastic wear. Chesterton face geometry
compensates for stresses in the body of the seal ring,
away from the critical face mating surfaces.
Face material
interchangeability
With the 155, the interchanging is
a fast and easy process, with seal
function and reliability assured.
Standard face materials are
silicon carbide or carbon.
The carbon can be swapped for
silicon carbide, tungsten carbide or
Duplex Carbide™, which provides the utility
of two hard faces but with lower frictional heat.
All faces are interchangeable with the
225 and 255 dual seals.
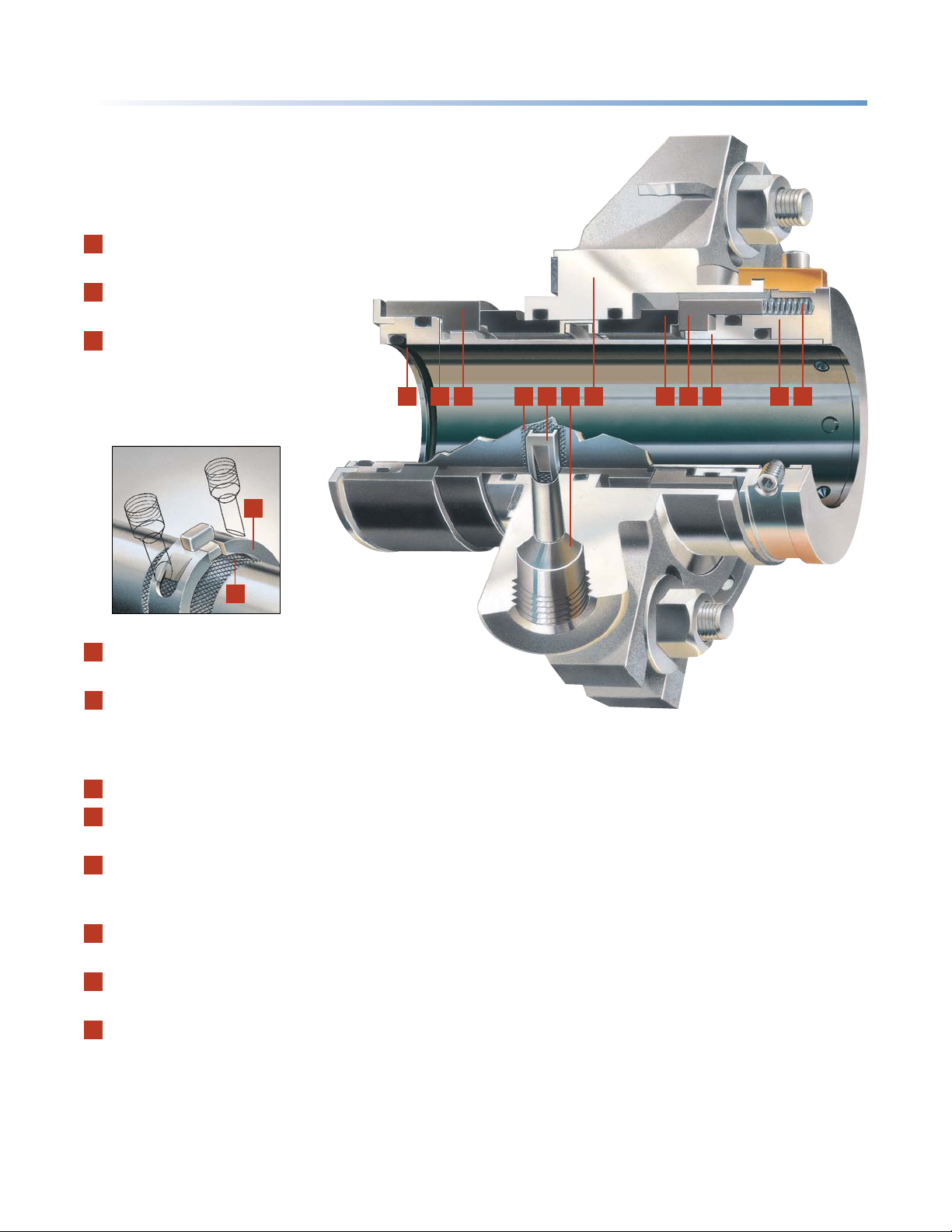
255TM
Cartridge Dual Seal
Construction Details
1
Every O-ring is either static or moves on
a non-fretting, non-metallic surface.
2
Precision seal ring support shoulder
maintains rotary alignment.
3
Inboard rotary and stationary faces.
Dynamic stress-relieving seal rings,
mated over a narrow cross-section
for low heat generation.
5
1•2•3
CHESTERTON
®
•
•
•
•
4•5•6
7
8•8• 9
10• 11
•
•
4
4
Profiled sleeve provides positive
pumping of barrier fluid.
5
Patented shuttle slides within gland to
decouple faces from gland misalignment,
channel barrier fluid, and provide anti-rotation
for stationary seal rings.
6
Barrier fluid ports provide high capacity cooling.
7
Universal gland fits majority of pumps.
ANSI oversize and API glands available.
8
Outboard stationary and rotary faces,
identical to inboard set for simple assembly,
low replacement inventory.
9
Inboard and outboard integral drive pads
cannot loosen or fall out.
10
Patented Self-Centering Lock Ring™
for superior concentricity.
11
Revolutionary Unified Seal Alignment™
requires only one set of springs to provide
constant loading of all four faces.
Springs are isolated from process and
barrier fluids.
•
Built for the future of emissions control
The Chesterton 255 seal is designed to meet
environmental regulations for emissions control.
Advanced technology for applications flexibility
The exclusive design of the 255 enables it to operate
in double-mode (barrier fluid pressure higher than
stuffing box pressure) or tandem-mode (barrier fluid
pressure lower than stuffing box pressure).
Staying cool in operation and under pressure
The 255 handles 50% to 100% more pressure than
typical seals, providing users with a “margin of safety”
at start-up and shut-down when transient surges
often occur. The 255 features an internal positive
barrier fluid pumping system with wide flow channels
for efficient removal of heat. To test the 255’s cool
running, the 255 and a widely used competitive double
seal were run under identical conditions with repeated
shutoffs. Test conditions: 1.875” (48 mm) shaft, water
barrier fluid room temperature, 1750 RPM, closed
convection system. Results: 255 ran cool and steady
while the conventional seal overheated and flashed.