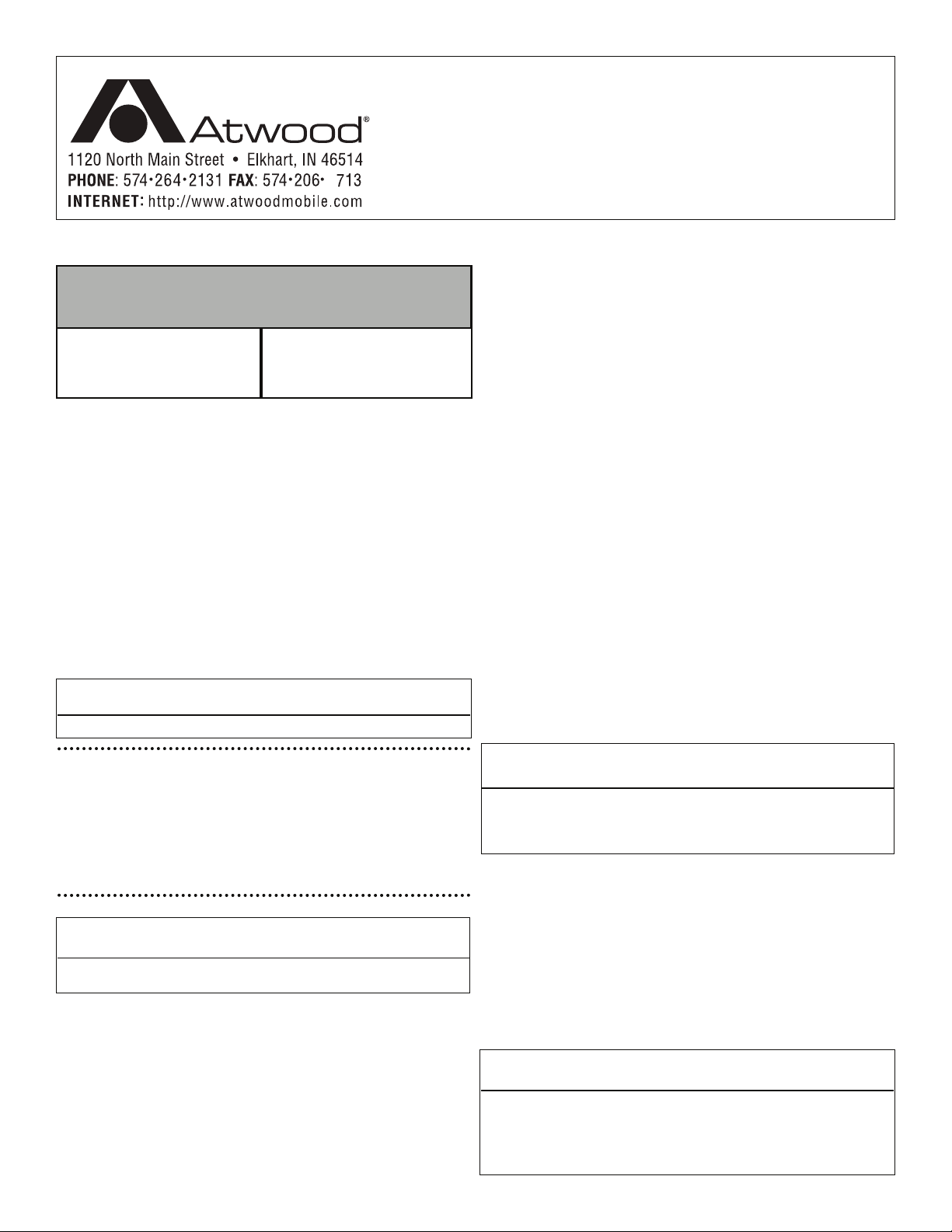
LITERATURE NUMBER MPD 87984
YOKE STYLE &
9
FLIP LATCH
COUPLERS
ENGLISH, FRANÇAIS (et Canada) •Installation •Operation •Maintenance
Effective 1/22/08
SAFETY ALERT SYMBOLS
Safety Symbols alerting you to potential personal safety hazards. Obey all safety
messages following these symbols.
WARNING CAUTION
avoid possible avoid possible
injury or death injury and/or property damage
FOR YOUR SAFETY READ ALL INSTRUCTIONS
BEFORE INSTALLATION AND OPERATION
Installer: Provide these instructions to the consumer.
Consumer: Read and keep documents available for future reference.
TRAILER & COUPLER CLASSIFICATION
TRAILERS WITH A TRAILERS WITH A GVWR
GVWR OVER NOT TO EXCEED
(MINIMUM)(MAXIMUM)
Class 1 0 2000 lb. (910 kg)
Class 2 2000 lb. - (910 kg) 3500 lb. (1590 kg)
Class 3 3500 lb. - (1590 kg) 5000 lb. (2270 kg)
Class 4 5000 lb. - (2270 kg) 10,000 lb. (4540 kg)
Trailer GROSS VEHICLE WEIGHT RATING (GVWR) = Maximum trailer weight with load
INSTALLATION
WELD APPLICATION
1. Coupler must overlap frame 4-7/8˝ minimum (FIG 1-A.)
2. Follow
3. Weld along top, back and sides specifically under flange where
WELDING INSTRUCTION.
coupler meets the trailer frame (
FIG 1-B.)
STRAIGHT TONGUE COUPLERS
SAE/CSA Class 3 Part # 80060, 80082, 80083
WELD ONLY:
1. Front edge of frame must contact internal frame stop on coupler
FIG 2-D.)
(
2. Coupler must overlap frame (FIG 2-A.)
80082, 80083 . . . . . . . . . . . . . . . . . . . . . . . . . . . . . . . . . . . . . .5-1/16˝ minimum
80060 . . . . . . . . . . . . . . . . . . . . . . . . . . . . . . . . . . . . . . . . . . . . . . . . .4-7/8˝ minimum
3. Follow
4. Weld along top, back and sides specifically under flange where
SAE/CSA Class 4 (8500 lbs. cap.) Part # 80131
WELD ONLY:
1. Frame to penetrate coupler 7-5/8˝ minimum (
2. Follow
3. Weld along top, back and sides specifically under flange where
WELDING INSTRUCTION.
coupler meets the trailer frame (
80082, 80083
80060 . . . . . . . . . . . . . . . . . . . .4-7/8˝ minimum horizontal weld length
WELDING INSTRUCTION.
coupler meets the trailer frame
80131
. . . . . . . . . . .5-1/6˝ minimum horizontal weld length
. . . . . . . . . . . . . . . . . . . .7-5/8˝ minimum horizontal weld length
FIG 2-B.)
FIG 3-A.)
FIG (3-B.)
CAUTION
HAZARDOUS FUMES
• Adequate ventilation must be provided when welding.
WELDING INSTRUCTION
• M.I.G. OR STICK - Class 2 & 3 coupler-Attach with 1/8˝ fillet weld min.
• M.I.G. WELDING - Use A.W.S. ER 70S-3 or 6 wire or equivalent with a
diameter of .035 - .045. The recommended shielding gas mixture is
75% - 95% Argon & 25% - 5% CO
• STICK WELDING - Use E6011 A.W.S. welding rod or equivalent with a
diameter are as follows: 1/8” electrode set power between 115-130
Amps DC or 5/32” electrode set power between 140-160 Amps DC.
Class 4 coupler-Attach with 5/32˝ fillet weld minimum.
2
.
CAUTION
PRODUCT DAMAGE
• Coupler latching mechanism must operate freely after welding installation.
• Do not attach ground strap to latch during welding.
STRAIGHT TONGUE COUPLERS
SAE/CSA Class 2 Part # 80051, 80055, 80056
BOLT APPLICATION
1. Coupler must overlap frame 4-7/8˝ minimum (
2. Fasten with two 1/2˝ diameter bolts S.A.E. grade 5 and lock nuts or
nuts and lock washers (FIG 1-D) (hardware not included).
3. To prevent collapse of coupler sides during bolt tightening, use
spacers (1/2˝ pipe or equivalent) placed between the inside surface
of coupler frame (
4. Torque bolts to 74-78 ft. lbs. (dry).
5. Retorque bolts after first two hours of service, then continue to follow maintenance schedule.
FIG 1-E) (hardware not included).
FIG 1-A.)
WELD BETWEEN COUPLERS
SAE/CSA Class 2 Part # 82311, 82315
SAE/CSA Class 3 Part # 80082, 80083
CAUTION
COUPLER OR FRAME DAMAGE
• A bottom support plate must be used with all Atwood Weld Between
Couplers.
• Do not attach ground strap to latch during welding.
• Weld completely around bottom plate using
WELD ONLY:
1. Front edge of frame must butt against side flanges of coupler
FIG 4-A. Weld full length both sides as indicated in
FIG 4-B. Weld around coupler and frame as shown.
2. Follow
3. Bottom rear of coupler and frame must be enclosed by a plate
WELDING INSTRUCTION.
welded to the frame to prevent flexing of frame and coupler.
FIG 4-E)
(
WELDING INSTRUCTION.
A-FRAME COUPLERS
SAE/CSA Class 3 Part # 80072, 80075, 84035, 84176
SAE/CSA Class 4 Part # 80101, 88007, 88555, 88010, 88600
CAUTION
COUPLER OR FRAME DAMAGE
• Atwood Class 3 & 4 couplers are designed for use on 50° A-Frames only.
• A bottom support plate must be used with all Atwood A-Frame couplers (
FIG 5/6/7-D.)
• Weld completely around bottom plate follow
• Do not attach ground strap to latch during welding.
1
WELDING INSTRUCTION.
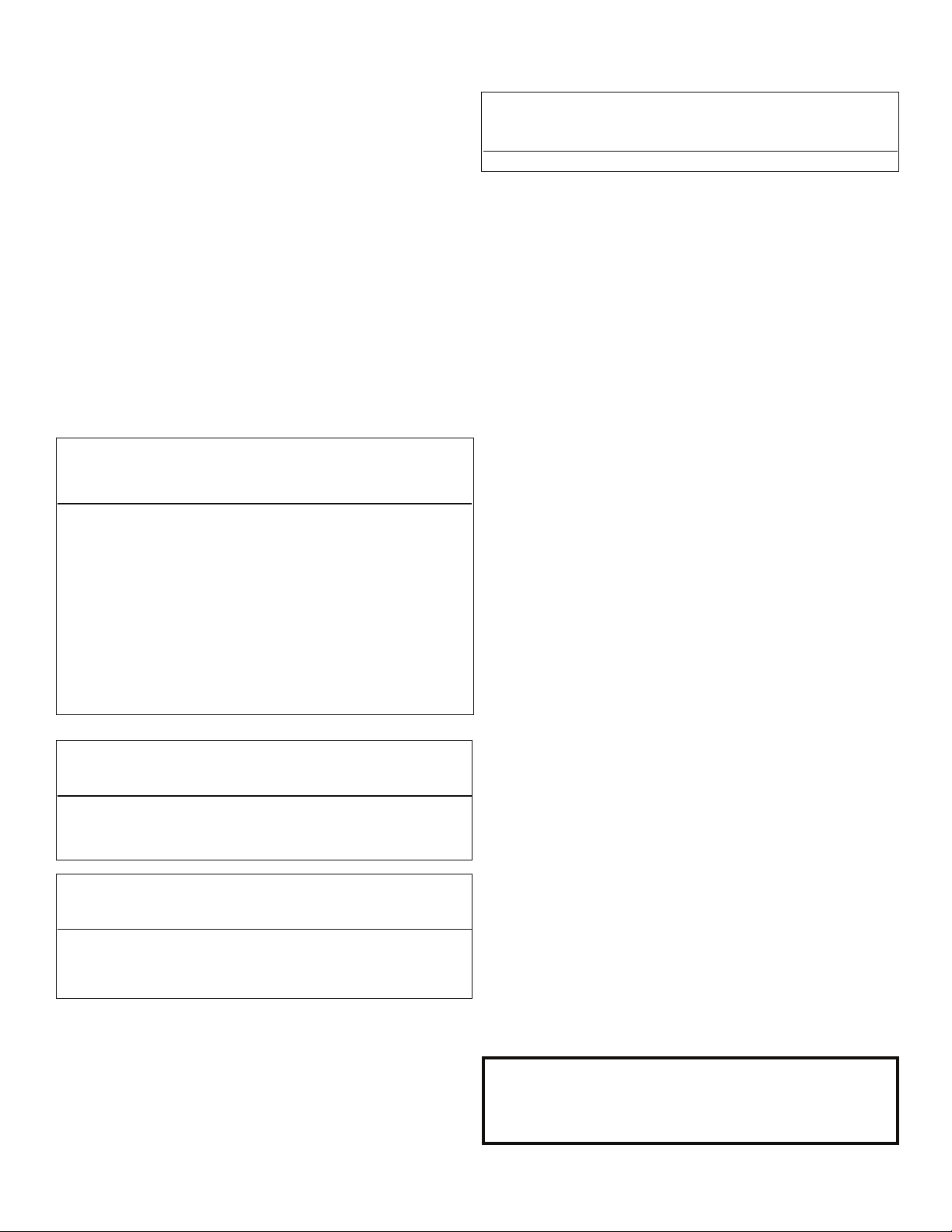
WELD ONLY:
1. Measuring along sides, penetration of frame into coupler must be :
Class 3 Couplers: 7˝ minimum
Class 4 Couplers: 8˝ minimum FIG
2. Follow
WELDING INSTRUCTION. Weld full length on both sides, from rear of
coupler past front edge of frame to inside of coupler under flange
FIG 5/6/7-B.)
(
FIG 6-A
5-A & 7-A
SAE/CSA Class 3 Part No. 80073
BOLT APPLICATION ONLY
1. Coupler must overlap frame 7˝ minimum (FIG 8-A.)
2. Bottom rear of coupler and frame must be enclosed by a plate
(MPD #87286) bolted to the frame to prevent flexing of frame and
coupler (
3. Fasten with four (4) 1/2˝ diameter bolts S.A.E. grade 5 and lock nuts
with flatwashers, or nuts and lock washers with flatwashers
(
4. To prevent collapse of frame during bolt tightening, use spacers
(1/2˝ tubing or equivalent) placed between the inside surface of
coupler frame (FIG 8-F) (not supplied).
5. Torque bolts to 74-78 ft. lbs. (dry).
6. Retorque bolts after first two hours of service, then continue to follow maintenance schedule.
FIG 8-D.)
FIG 8-E) (not supplied).
OPERATION
WARNING
• Safe towing practice requires the proper use of safety chains used in
accordance with instructions provided by the trailer manufacturer.
• BEFORE TOWING: The ball must be completely inserted into the coupler ball
socket. The ball clamp (inside the coupler) must be closed around the
underside of the tow ball. The handle must be in the closed position.
• The loaded weight of the trailer must never exceed the maximum
capacity marked for each component (coupler, tow ball, hitch) of the
trailer or vehicle.
• Check coupler, hitch and ball for damage or wear before each use.
Assure all parts operate freely. Replace any component if worn or damaged.
• Failure to follow warnings and instructions could result in separation of
tow vehicle and trailer which can result in death, personal injury and
property damage.
PERSONAL INJURY
WARNING
• For proper tow vehicle and trailer hookup, towing performance and to
prevent damage to hitch and trailer coupling, the tow vehicle and trailer
are to be level with respect to flat ground after hitching up. If your trailer
is not level, equipment is available to raise or lower the hitch ball.
PERSONAL INJURY
LATCHING INSTRUCTIONS
WARNING
• Always open latch handle before inserting ball.
YOKE STYLE COUPLERS
PART # 70643, 80051, 80055, 80060, 80072, 80073, 80075, 80082, 80101,
82311, 82315, 84035, 84176
1. To open, lift the latch and pull backward, raising the yoke and resting it on the nose of the coupler (
2. Place coupler on ball of same diameter as coupler and of same or
greater capacity.
3. When ball is completely nested in ball socket, push latch handle
forward until yoke drops over nose of coupler and the latch handle
locking tips freely enter slots on top of coupler (
4. Extend jack to ground and lift car/trailer combination 2˝-4˝ to insure
coupler is securely attached to tow ball. Retract jack completely
before towing.
Note: These are non-locking couplers.
Note: These couplers are not adjustable for ball size.
FLIP LATCH COUPLERS
PART # 88555, 88600 8,000 lb. Capacity
PART # 88007, 88010 10,000 lb. Capacity
1. To open, slide forward and pull up open latch before inserting ball
FIG 10-A.)
(
2. Place coupler on ball of same diameter as coupler ball socket size
and of same or greater capacity than trailer GVW.
88555/88600 ............2˝ 88007/88010 ............2-5/16˝
3. When ball is completely nested in socket, push top of latch handle
rearward until handle snaps into closed position.(
4. Extend jack to ground and lift car/trailer combination 2˝-4˝ to insure
coupler is securely attached to tow ball. Retract jack completely
before towing.
5. Insert padlock through hole in handle (
Note: These couplers are not adjustable for ball size.
STRAIGHT TONGUE COUPLERS
PART # 80131
1. Insert finger in latch hole. Pull out and up on latch (
latch 90° from original position. (FIG 11-B.)
2. Place coupler on 2-5/16˝ ball of same or greater capacity than trailer GVW.
3. When ball is completely nested in ball socket, push forward on
4. Extend jack to ground and lift car/trailer combination 2˝-4˝ to insure
5. Insert padlock or bolt through lock hole (
Note: These couplers are not adjustable for ball size.
FIG 11-B.) Be sure that the nib (FIG 11-A1) on the latch is
latch (
secured in slot (FIG 11-A2.)
coupler is securely attached to tow ball. Retract jack completely
before towing.
PERSONAL INJURY
FIG 9-A.)
FIG 9-B.)
FIG 10-B.)
FIG 7-C) .
FIG 11-A.) Rotate
FIG 3-C) in latch.
CAUTION
PRODUCT DAMAGE
• Use caution when backing or towing vehicle for hook-up, damage to
coupler may result.
• Avoid sharp turns when towing or backing. Jack-knifing could bend
coupler or create extreme stress or fracture.
MAINTENANCE
1. Lubricate ball socket and ball clamp with wheel bearing grease.
Clean and lubricate monthly.
2. Check towing hitch, ball and coupler for signs of wear before each
trip. Replace coupler if damaged or worn.
3. Lubricate moving or sliding parts monthly with S.A.E. 30 weight oil.
4. Should problems or questions arise, contact your dealer, the trailer
manufacturer or Atwood Service Department 574-264-2131.
5. For Warranty information contact Atwood before having any work
done 574-264-2131.
FIG 1-11 are located following page
A = minimum/maximum coupler/tongue overlap
B = weld areas (XXXXXXXXXX )
C = lock hole
2