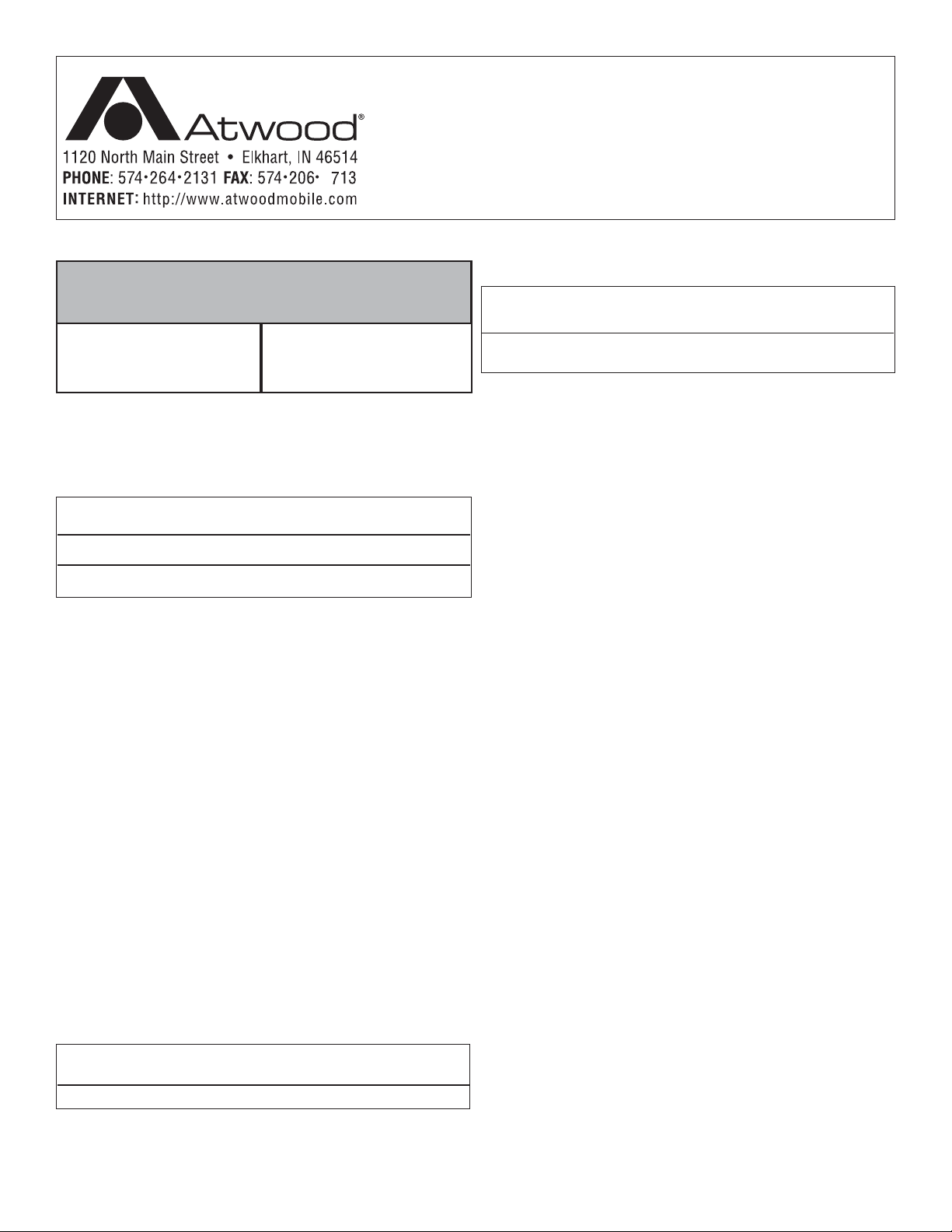
LITERATURE NUMBER MPD 87985
THUMB LATCH
9
ENGLISH, FRANÇAIS (et Canada) •Installation •Operation •Maintenance
SAFETY ALERT SYMBOLS
Safety Symbols alerting you to potential personal safety hazards. Obey all safety
messages following these symbols.
WARNING CAUTION
avoid possible avoid possible
injury or death injury and/or property damage
FOR YOUR SAFETY READ ALL INSTRUCTIONS
Installer: Provide these instructions to the consumer.
Consumer: Read and keep documents available for future reference.
• Adequate ventilation must be provided when welding.
Coupler latching mechanism must operate freely after welding installation.
•
• Do not clamp ground strap to latch during welding.
WELDING INSTRUCTIONS
• M.I.G. OR STICK-Attach couplers with 5/32˝ fillet weld minimum.
.I.G. WELDING
• M
eter of .035 - .045. The recommended shielding gas mixture is 75% 95% Argon & 25% - 5% CO2.
• STICK WELDING - Use E6011 A.W.S. welding rod or equivalent.
Recommended machine settings for specific electrode diameter are as
follows: 1/8” electrode set power between 115-130 Amps DC or 5/32”
electrode set power between 140-160 Amps DC.
UNDERSLUNG COUPLER
PART # 82680, 82681, 82682 13,000 lb. Capacity
Top Plate PA RT # 82740 or 22375
1. On I-beams remove approximately 9˝ of outside bottom flange of the
I-beams (
For an alternative to removing a length of the I-beam flange:
a. Make two plates 9ˇ long x .135˝ thick x height of I-beam (
b. Weld the plates to the outside of the I-beam flanges.
c. Weld both plates full length top and bottom following
2. With bottom of beam contacting inside bottom coupler, butt front edge
of beams against back of ball housing. Edges of beams must make full
contact with inside surface of coupler sides.
3. On beams with flanges wider than 1-15/16˝, trim front corners (
to allow beams to penetrate fully into coupler.
4. Following
with a continuous weld (FIG 5-B). Weld must run from rear edge of
coupler past front edge of beam, then onto inside of coupler (
Weld bottom rear edge of coupler to bottom of trailer frame.
• Top support plates must be used with all underslung couplers.
5. Align hole in top plate with hole in coupler (
INSTRUCTION
weld top support plate to frame full length both sides and around the
corner to inside edges of the trailer frame (
BEFORE INSTALLATION AND OPERATION
REFERENCE FIGURES FOUND ON PAGE 3
INSTALLATION
CAUTION
HAZARDOUS FUMES
PRODUCT DAMAGE
-Use A.W.S. ER 70S-3 or 6 wire or equivalent with a diam-
FIG 5-A) so coupler can be welded directly to the I-beam web.
FIG 2-B & 5-E).
WELDING INSTRUCTIONS.
FIG 2-C)
WELDING INSTRUCTIONS, weld full length, both sides of coupler,
FIG 5-D).
CAUTION
COUPLER OR FRAME DAMAGE
to assure structural integrity of coupler attachment system,
FIG 5-F). Following WELDING
FIG 5-C).
TOP MOUNT A-FRAME COUPLERS
CAUTION
COUPLER OR FRAME DAMAGE
• A bottom support plate MUST be used with A-Frame couplers.
• Weld completely around bottom plate following WELDING INSTRUCTIONS.
..............................................
Part # 81916 (Kit includes 81917 bottom plate) 15,000 lb. Capacity
Part # 81912 13,000 lb. Capacity
SAE/CSA Class 4 Part # 81911, 81915 10,000 lb. Capacity
Bottom Plate PART # 81917, 82672, 83400, 83470, 83511, 84150, 84160, 86081
1. Penetration of trailer frame into coupler must be 8˝ minimum measured along coupler sides (FIG 1-A).
2. Following
coupler under flange and past front edge of trailer frame to inside of
coupler (FIG 1-B).
3. A bottom support plate must be used to assure structural integrity of
coupler attachment system. Align hole in bottom support plate with
hole for jack in coupler (
support plate, align them with the mounting holes in the coupler.
Following
attachment system, weld bottom support plate to frame full length
both sides and around the corner to inside edges of the trailer frame.
..................................................
WELDING INSTRUCTIONS weld full length on both sides, from rear of
WELDING INSTRUCTIONS to assure structural integrity of coupler
Part # 81916 (Kit includes 81917 bottom plate) 15,000 lb. Capacity
Part # 81912 13,000 lb. Capacity
SAE/CSA Class 4 Part No. 81911, 81915 10,000 lb. Capacity
Bottom Plate PART # 81917, 82672, 83400, 83470, 83511, 84150, 84160, 86081
1. For I-beams, remove approximately 9˝ of outside top flange of the
I-beam (
For an alternative to removing a length of the I-beam flange:
a. Make two plates 9˝ long x .135˝ thick x height of I-beam (FIG 2-B).
b. Weld the plates to the outside of the I-beam flanges.
c. Weld both plates full length top and bottom following
2. With top of beams contacting inside top of coupler, butt front edge
of beams against back of welded plate on coupler. Edges of beams
must make full contact with inside surface of coupler sides.
3. On beams with flanges wider than 1-15/16˝, trim front inside corners
to allow beams to penetrate fully into coupler (
4. Penetration of frame into coupler must be 8˝ minimum measured
along sides (FIG 1-A.)
5. Following
coupler under flange and past front edge of trailer frame to inside of coupler (FIG 1-B).
6. A bottom support plate must be used to assure structural integrity of
coupler attachment system. Align hole for jack in bottom support
plate with hole for jack in coupler (
assure structural integrity of coupler attachment system weld bottom
support plate to trailer frame full length both sides and around the
corner to inside edges of the trailer frame.
1
FIG 2-A), welding coupler directly to web of beams.
WELDING INSTRUCTIONS
BOX BEAM APPLICATION
FIG 1-C). If there are mounting holes in the
I-BEAM APPLICATION
, weld full length on both sides, from rear of
COUPLERS
Effective 11/21/07
..........................................
..............................................
WELDING INSTRUCTIONS.
FIG 2-C).
FIG 1-C). Follow WELDING INSTRUCTIONS to
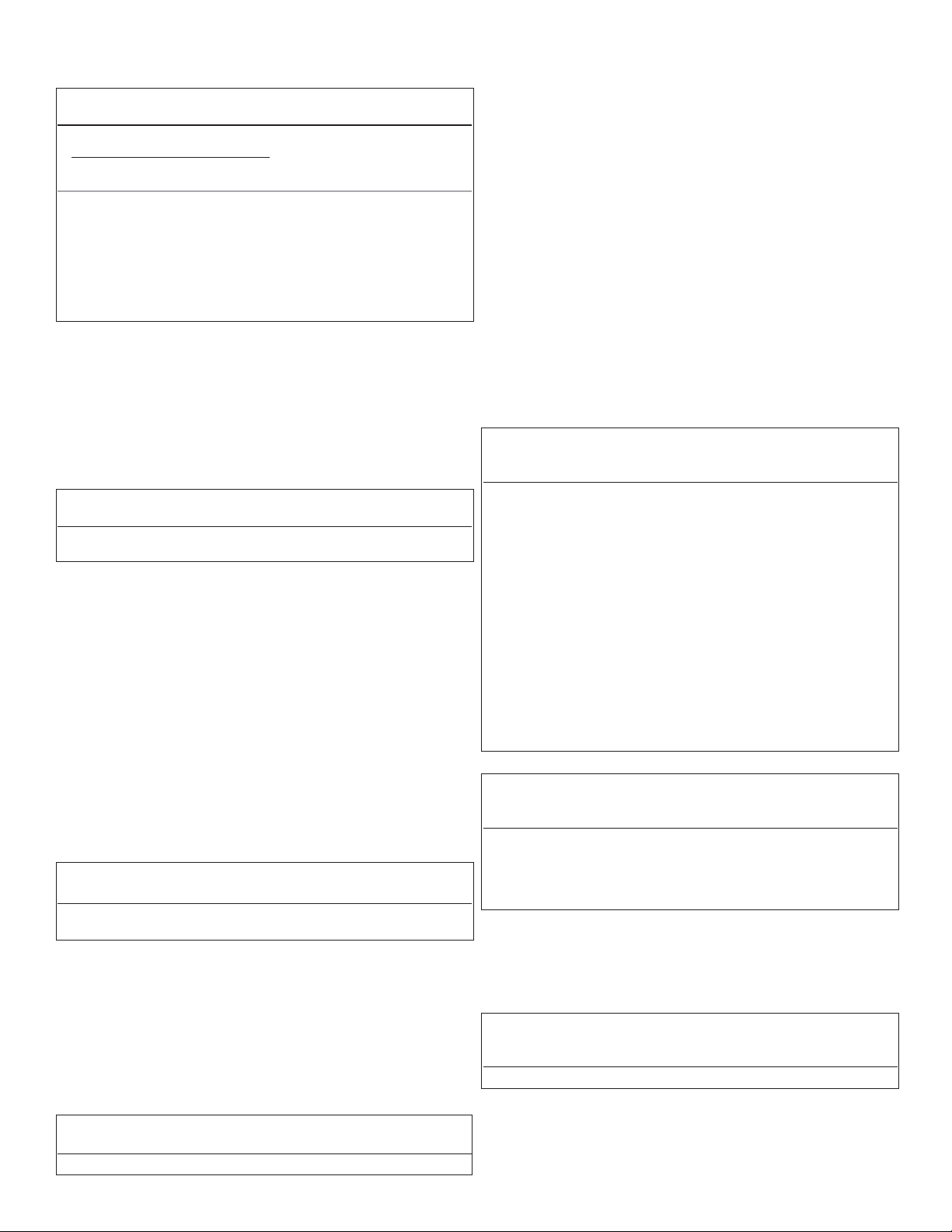
STRADDLE MOUNT COUPLERS
CAUTION
FIG 4).
CAUTION
CAUTION
CAUTION
FIG 3).
FIG 2-C) of the I-beam
FIG 2-C) of the I-beam
COUPLER OR FRAME DAMAGE
• MPD 83462 AND MPD 83549 - 44,000 LB. MOBILE HOME COUPLERS -
Use only on mobile home applications These couplers are for one time use
to tow a mobile home.
DO NOT RECYCLE/REUSE THE COUPLER - TOW BAR ASSEMBLY.
• Straddle mount couplers are to be used only on mobile homes.
• Top and bottom support plates MUST be used with all Straddle
Mount Couplers.
• Do not mount couplers directly onto corrugated type beams
• Must use 50˚ coupler with a 50˚ A-frame only.
• Must use 60˚ coupler with a 60˚ A-frame only.
• Larger beam reinforcements and improved attachments may be nec-
essary for adequate structural capacity.
PART # 83461, 84102 - 50˚ coupler 32,000 lb. Capacity
PART # 83462 - 50˚ coupler 44,000 lb. Capacity
PART # 83551, 83556 - 60˚ coupler 32,000 lb. Capacity
PART # 83549 - 60˚ coupler 44,000 lb. Capacity
Top Plate PA RT # 22375, 82740, or 83480 (50˚), or 83670 (60˚)
Bottom Plate 82672, 83400, 83470, 83511, 84150, 84151, 84160, 84161, 86081
1. Butt front edge of beam web against the end of slot in top of coupler
and back of plate at bottom of coupler (
2. If necessary, remove the front inside corners (
flange to allow beams to penetrate fully into both sides of the coupler.
COUPLER OR FRAME DAMAGE
• Following WELDING INSTRUCTIONS weld around front of beam and on inside
of beam.
3. Following WELDING INSTRUCTIONS weld along top, back and sides specifically
under flange and around slots in coupler (FIG 3-A).
4. When installing coupler at top of I-beam, provide for clearance between
latch and flanges of beams for proper operation. Weld coupler to front
edge of I-beam flange and top of coupler sides to underside of I-beam
FIG 3-B).
flange (
5. Align hole in top support plate with hole in bottom support plate (FIG 3-C,
4-B). Following
attachment system weld bottom support plate to trailer frame full length
both sides and around the corner to inside edges of the trailer frame.
WELDING INSTRUCTIONS to assure structural integrity of coupler
Part # 84140 - 50˚ coupler 40,000 lb. Capacity
Part # 84060 - 60˚ coupler 40,000 lb. Capacity
Top Plate PA RT # 83480 (50˚), or 83670 (60˚)
Bottom Plate
1. Butt front edge of beam web against the end of slot in top and bottom of coupler (
2. If necessary, remove the front inside corners (
flange to allow beams to penetrate fully into both sides of the coupler.
PAR T # 82672, 83511, 84150, 84160
COUPLER OR FRAME DAMAGE
• Following WELDING INSTRUCTIONS weld around front of beam and on inside
of beam.
3. Using WELDING INSTRUCTIONS weld along top, back and sides specifically under
flange and around slots in coupler completely to integrate coupler and Ibeams (FIG 4-A).
4. When installing coupler at top of I-beam provide for clearance between
latch and flanges of beams for proper operation. Weld coupler to front
edge of I-beam flange and top of coupler sides to underside of I-beam
FIG 4-B).
flange (
5. Align hole in top support plate with hole in bottom support plate (FIG 4-C).
Following
attachment system weld bottom support plate to trailer frame full length
both sides and around the corner to inside edges of the trailer frame.
WELDING INSTRUCTIONS to assure structural integrity of coupler
COUPLER OR FRAME DAMAGE
• Weld top and bottom of coupler, both sides.
ADJUSTABLE COUPLER
..................................
1. POSITIONING BRACKET - Center bracket side to side on trailer tongue with
bracket height adjusted to meet your towing needs (
ground clearance and provide position options for coupler. Trailer must
travel in a level, horizontal to ground position. This will provide optimal coupler axle loading and range of motion. Support mounting bracket sides
with C-clamps or bolts before welding to prevent distortion of brackets
during welding process. Inside dimension of bracket must be 3.00˝±.03˝
after welding (
2. Follow
3. Weld along top, bottom and sides of bracket where it meets trailer tongue.
Add gussets (5/16˝ thick steel plate) (FIG 9-B) equal in height to bracket (FIG
9-A) to fully support bracket. Weld along all joint edges of gusset using
welding instructions.
................................................
1. Fasten coupler to bracket with two 5/8˝ diameter bolts S.A.E. grade 8
and lock nuts or nuts and lock washers.
2. Torque bolts to 200-230 ft. lbs. (dry).
3. Retorque bolts after first two hours of service, then continue to follow
maintenance schedule.
WELD ON BRACKET APPLICATION
FIG 4-A).
WELDING INSTRUCTIONS.
BOLT ON APPLICATION
................................
FIG 9). Allow adequate
..............................................
OPERATION
WARNING
• Safe towing practice requires the proper use of safety chains used in
accordance with instructions provided by the trailer manufacturer.
• Check that the ball has been completely inserted into the coupler ball socket and the ball clamp (inside the coupler) is closed around the underside of
the tow ball and the handle is in the closed position.
• The loaded weight of the trailer must never exceed the maximum
capacity marked on the coupler, tow ball and hitch of the trailer or vehicle.
• Check coupler, hitch and ball for damage or wear before each use.
Assure all parts operate freely. Replace any component if worn or damaged.
• Failure to follow warnings and instructions could result in separation of
tow vehicle and trailer which can result in death, personal injury and
property damage.
• For proper tow vehicle and trailer hookup, towing performance and to
prevent damage to hitch and trailer coupling, the tow vehicle and trailer
are to be level with respect to flat ground after hitching up. If your trailer is not level, equipment is available to raise or lower the hitch ball.
PERSONAL INJURY
CAUTION
PRODUCT DAMAGE
• Use caution when backing or towing vehicle for hook-up.
• Do not set closed coupler on ball.
• Avoid sharp turns when towing or backing. Jack-knifing could bend
coupler or create extreme stress or fracture to coupler, coupler
attachment and trailer frame.
LATCHING INSTRUCTIONS
THUMB LATCH COUPLERS
PART # 80281, 81906, 81911, 81912, 81915, 81916, 82680, 82681, 82682,
83461, 83551, 83556, 84060, 84102, 84140, 86040
WARNING
• Always open latch handle before inserting ball.
1. With thumb, press down and back on latch (FIG 8-A). Latch will catch
at rear of slot and remain open (FIG 8-B).
Place coupler on 2-5/16˝ ball of same or greater capacity than trailer GVW.
2.
3. When ball is completely nested in ball socket, push down and forward on latch until rear of latch locks in slot
2
PERSONAL INJURY
FIG 9-C.