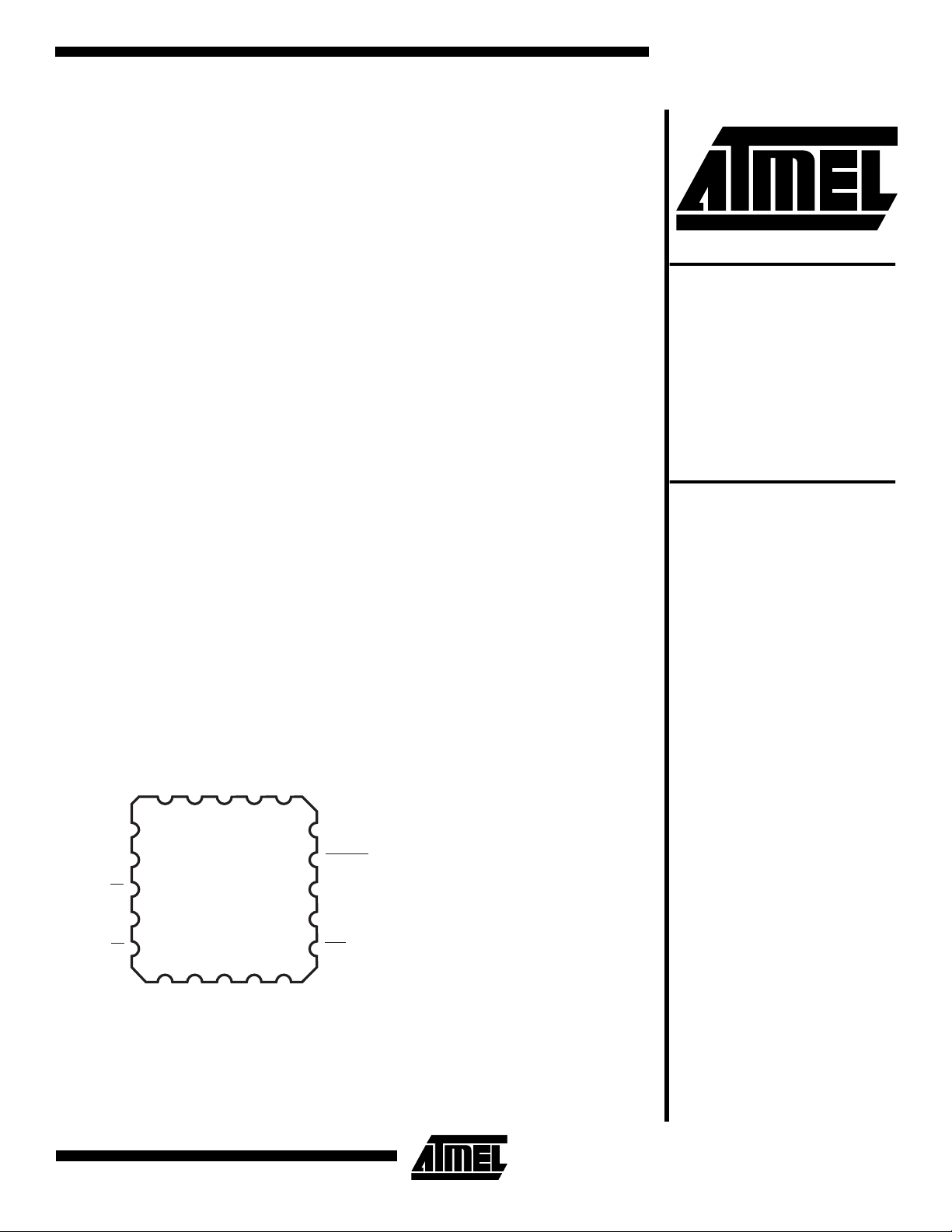
Features
•
E2 Programmable 524, 288 x 1 and 1,04 8,5 76 x 1 bit Serial Memories Designe d To Store
Configuration Programs For Field Programmable Gate Arrays (FPGA)
•
Simple Interface to SRAM FPGAs
•
Compatible With Atmel AT6000, AT40K FPGAs, Altera EPF8K, EPF10K,
EPF6K FPGAs, ORCA FPGAs, Xilinx XC3000, XC4000, XC5200 FPGAs, Motorola
MPA1000 FPGAs
•
Cascadable To Support Additional Configurations or Future Higher-density Arrays
•
Low-power CMOS EEPROM Process
•
Programmable Reset Polarity
•
Available In PLCC Package (Pin Compatable across Product Family)
•
In-System Programmable Via 2-Wire Bus
•
Emulation of 24CXX Serial EPROMs
•
Available in 3.3V ± 10% LV and 5V Versions
•
System Friendly READY Pin
FPGA
Configuration
2
E
PROM
Description
The AT17C512/010 and AT17LV512/010 (high-density AT17 Series) FPGA Configuration EEPROMs (Configurators) provide an easy-to-use, cost-effective configuration
memory for Field Program mable Gate Arrays. The high -densit y AT17 Series is packaged in the popular 20-pin PLCC. The hig h-densi ty AT17 S eries fam ily uses a simple
serial-access procedure to configure one or more FPGA devices. The high-density
AT17 Series organization supplies enou gh memory to configure one or multi ple
smaller FPGAs. The user can select the polarity of the reset function by programming
one EEPROM byte. The devices also support a write protection mode and a system
friendly READY pin, which signifies a “good” power level to the device and can be
used to ensure reliable system power-up.
The high-density AT17 Series can be program med with industry-standar d programmers, and the Atmel ATDH2200 Programming board.
Pin Configurations
20-Pin PLCC
CLK
WP1
D
A
T
N
A
C
3 2 1 20 19
4
V
C
N
C
N
C
C
NC
18
SER_EN
17
Memory
512K and 1M
AT17C512
AT17LV512
AT17C010
AT17LV010
RESET/OE
WP2
CE
9510611712813
N
G
N
C
N
D
NCN
C
C
16
15
14
NC
READY
CEO
Rev. 0944A-A–12/97
1
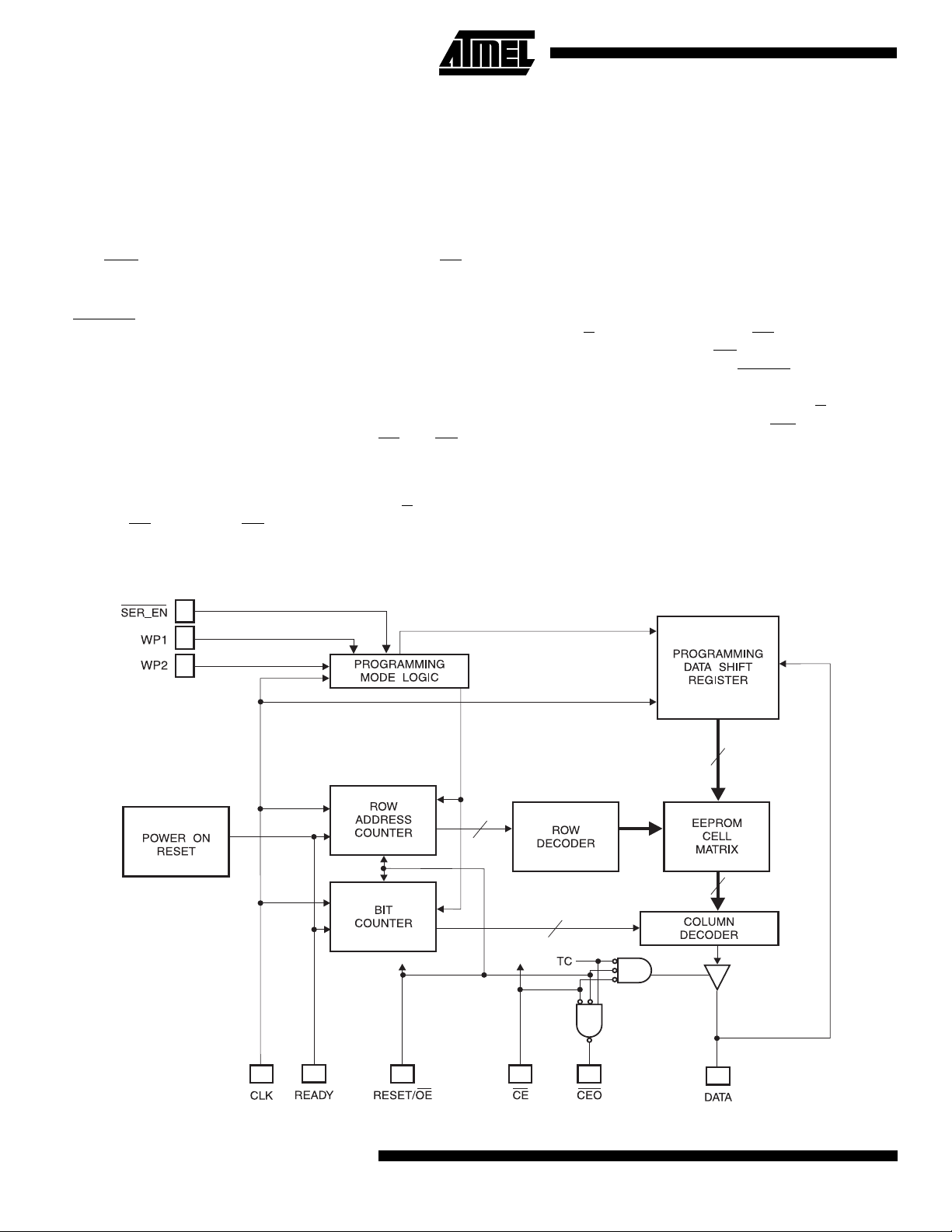
Controlling The High-Density AT17 Series Serial EEPROMs
Most connections between the FPGA device and the Serial
EEPROM are simple and self-explanatory:
• The DATA output of th e high-density AT17 Series dr ives
DIN of the FPGA devices.
• The master FPGA CCLK output dr ives the CLK input of
the high-density AT17 Series.
• The CEO
input of the next AT17C/LV512 /010 in a ca scad e chain of
PROMs.
•SER_EN
ISP).
READY is available as an open-collector indicator of the
device’s RESET s tatus; i t is driven L ow while the device is
in its POWER-ON RESET cycle and released (tri-stated)
when the cycle is complete.
There are two different wa ys to use the inp uts CE
as shown in the AC Characteristics waveforms.
output of any AT17C/LV5 12/010 drives the CE
must be connected to VCC, (except during
and OE,
Condition 1
The simplest connection is to have the FPGA D/P output
drive both CE
and RESET/OE in paral le l ( F ig ure 1) . Du e to
its simplicity, however, this method will fail if the FPGA
receives an external reset condi tion during the configuration cycle. If a sy stem rese t is ap plied to the FPGA, it will
abort the original configuration and then reset itself for a
new configuration, as in tend ed. O f cour s e, the hig h-density
AT17 Series does not see the ex ter nal r es et sig nal an d wi ll
not reset its internal address counters and, consequently,
will remain out of sync with the FPGA for the remainder of
the configuration cycle.
Condition 2
The FPGA D/P output drives only the CE in put of t he high density AT17 Series, while its OE
inversion of the input to the FPGA RESET
connection works under all normal circumstances, even
when the user aborts a configuration before D/P
High. A High level on the RESET/OE
AT17C/LVxxx – during FPGA reset – cl ears t he Conf igu rator’s internal address pointer, so that the reconfiguration
starts at the beginn ing . The high- de ns ity AT 17 Ser ies do es
not require an inverter since the RESET polarity is programmable.
input is driven by the
input pin. This
has gone
input to the
Block Diagram
2
AT17C/LV512/010
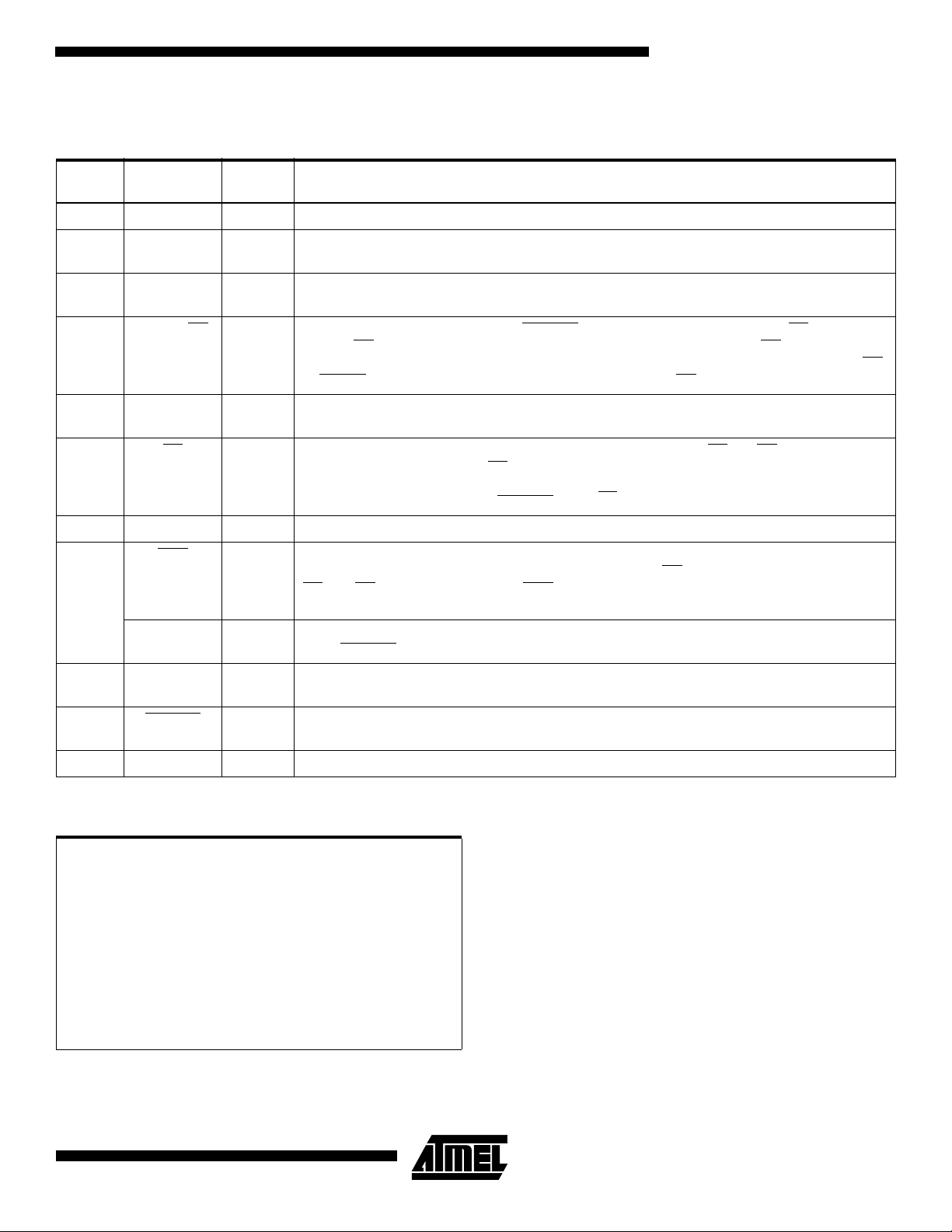
AT17C/LV512/010
Pin Configurations
20
PLCC Name I/O Description
2 DATA I/O Three-state DATA output for reading. Input/Output pin for programming.
4 CLK I Clock input. Used to increment the internal address and bit counter for reading and
programming.
5 WP1 I WRITE PROTECT (1). Used to protect portions of memory during programming. See
programming guide for details.
6 RESET/OE
7 WP2 I WRITE PROTECT (2). Used to protect portions of memory during programming. See
I RESET/Output Enable input (when SER_EN is High). A Low level on both the CE and
RESET/OE
address and bit counters . The l ogic p olarity of t his input i s prog ra mmab l e as eithe r RESET/ OE
or RESET
programming guide for details.
inputs enables the data output driver. A High level on RESET/OE resets both the
/OE. This document describes the pin as RESET/OE.
8CE
10 GND Ground pin.
14 CEO
A2 I Device selection input, A2. This is used to enable (or select) the device during programming,
15 READY O Open collector reset state indicator. Driven Low during power-up reset, released when power-
17 SER_EN I Serial enable is normally high during FPGA loading operations. Bringing SER_EN Low,
20 V
CC
I Chip Enable input. Used for device selection. A Low level on both CE and OE enables the data
output driver. A High level on CE
device into a low power mode. Note this pin will not
Programming mode (i.e., when SER_EN
O Chip Enable Out output. This signal is asserted Low on the clock cycle following the last bit
read from the memory. It will stay Low as long as CE and OE
CE
until OE goes Hig h. There after, CEO will stay Hig h until the ent ire PR OM is read again and
senses the status of RESET polarity.
when SER_EN
up is complete. (Recommend a 4.7KΩ Pull-up on this pin if used).
enables the two wire serial interface mode for programming.
+3.3V/+5V power supply pin.
is Low (see Programming Guide for more details)
disables both the address and bit counters and forces the
enable/disable the device in 2-wire Serial
is Low).
are both Low. It will then follow
Absolute Maximum Ratings*
Operating Temperature.................................. -55°C to +125°C
Storage Temperature.....................................-65°C to +150°C
Voltage on Any Pin
with Respect to Ground............................-0.1V to V
Supply Voltage (V
).........................................-0.5V to +7.0V
CC
+ 0.5V
CC
*NOTICE: Stresses beyond those listed under Absolute Maxi-
mum Ratings may cause permanent damage to the
device. These are stress ratings only, and functional
operation of the device at these or any other conditions beyond those listed under Operating Cond itions
is not implied. Exposure to Absolute Maximum Ratings conditions for extended periods of time may
affect device reliability.
Maximum Soldering Temp. (10 s @ 1/16 in.)..................260°C
ESD (R
= 1.5K, C
ZAP
= 100 pF)...............................2000V
ZAP
3