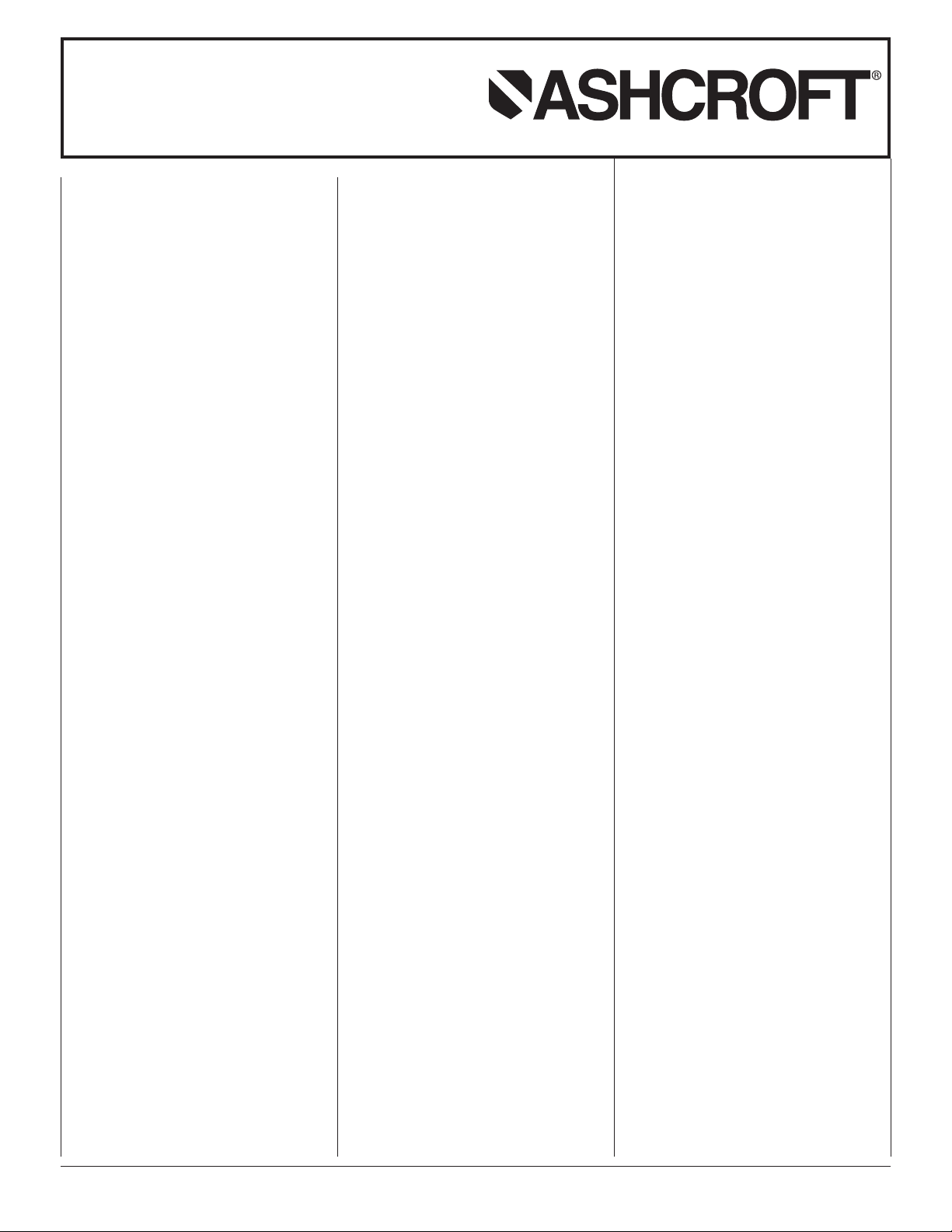
INSTRUCTIONS FOR THE INSTALLATION, OPERATION
AND MAINTENANCE OF TYPES 1125A/1128 &
1125/1127 DIFFERENTIAL PRESSURE GAUGES
1. Type 1125A/1128 – Gauge has a
dial with zero at top center. When the
pointer is to the right of the zero it indicates that the pressure at the right
hand socket connection is greater than
that exerted at the left and vice-versa.
The gauge will not be damaged if the
highest pressure should shift from left
to right or vice-versa.
2. Type 1125/1127 – Gauge has the
usual type dial, such as 0/30, 0/100,
etc., with the zero at the bottom left.
Pressure must be applied to the high
pressure connection before the low
pressure is applied. It is important that
the high pressure line be connected to
the right hand socket, (marked “H”).
3. General Information – The pressure gauge contains two bourdon
tubes, the free ends of which move
when subjected to pressure. A gear
movement transmits the motion of the
bourdon tubes to the pointer. A pressure gauge must not be subjected to a
pressure higher than the maximum
working pressure shown on the dial. If
higher pressures are applied, permanent distortion of the bourdon tube and
inaccurate readings may result. For
best service the gauge should operate
at approximately one half of the maximum working pressure.
(Example: A gauge with a dial range of
0-200 psi should operate at a working
pressure of about 150 lbs. or less.)
4. Installation – Pressure gauges
should be mounted in a vertical position and free from vibration. The gauge
socket is equipped with standard size
wrench flats. These wrench flats
should be used exclusively when
installing the gauge. Under no circumstances should any force be applied to
the gauge case directly. Twisting of the
case may result in disturbing the calibration of the gauge.
5. Applications – For steam pressure
applications use a siphon. If the gauge
is installed above the point of measurement, install the siphon in the pressure
line to the gauge. Install a shut-off cock
between the siphon and the gauge.
The siphon should be filled with water
to prevent steam from entering the
gauge, otherwise the high steam tem-
perature may damage the instrument.
If the gauge is located below the point
of measurement, the bourdon tube will
be filled with condensate and no
siphon is required. If the gauge is
installed on a liquid pressure line, lay
the piping so as to avoid vapor entrapment, otherwise readings may be
incorrect. If possible, arrange for vents
at high points in the line to bleed off
entrapped vapors.
6. Gauge Protectors and Dampeners
– On installations which are subject to
severe pressure fluctuation, pulsations
and/or line shock, the use of snubbers
or orifice pulsation dampeners is recommended. The snubber is placed in
the line just before the pressure gauge.
The pointer moves across the gauge
scale at a rate which is proportional to
the pressure differential across the element. A moderate but smooth action is
obtained, free from shock and pulsation. Gauge failure due to pressure
shock is eliminated. A simpler but less
effective protective dampening device
consists of a restrictive orifice screw.
The screw is available as an accessory
when ordering the gauge.
7. Zero Adjustment – First remove the
bezel or retaining ring and glass face in
order to reset the pointer. There are
two types of adjustable pointers. The
micrometer type is adjusted by holding
the pointer firmly with one hand and
rotating the adjustment screw with a
small screw driver. The friction type
adjustable pointer is reset by holding
the pointer firmly and rotating the slotted hub with a screw driver. Plain pointers must be removed with a hand jack.
On gauges equipped with plain pointers, minor adjustments can be made
by rotating the slotted scale. When
resetting pointers to zero, it is important that there be no pressure in both
inlets.
© 2007 Ashcroft, Inc., 250 East. Main Street., Stratford, CT 06614-5145, USA, Tel: 203-378-8281 • www.ashcroft.com
All sales subject to standard terms and conditions of sale. I&M008-10158 (84A493-01) 11/99 06/10