
INSTALLATION AND
MAINTENANCE INSTRUCTIONS
PWC Series "Magic-Pak"
Self-Contained Heat Pump
[ WARNING
Improper installation, adjustment, alteration, service or maintenance can cause injury
or property damage. Refer to this manual. For assistance or additional information,
consult a qualified installer or service agency.
I _'WARNING I
For your safety, do not store or use gasoline or
other flammable vapors and liquids in the
vicinity of this or any other appliance. Such
actions could result in property damage, per-
sonal injury or death.
TABLE OF CONTENTS
INSTALLATION ....................................... 2
OPERATION .......................................... 5
MAINTENANCE ..................................... 6
Installation and servicing of air conditioning
equipment can be hazardous due to internal
refrigerant pressure and live electrical compo-
nents. Only trained and qualified service
personnel should install or service this equip-
ment. Installation and service performed by
unqualified persons can result in property
damage, personal injury or death.
] A CAUTION I
These units are not approved for mobile home
applications. Such use could result in prop-
erty damage, p_rsonal injury or death.
WIRING DIAGRAMS .............................. 7
WARRANTY ......................................... 10
ManufacturedBy
A.A.C.
A Lennox International Company
421 MonroeStreet
Bellevue,OH 44811
IIIIIIIIIIII)llllllllllllllllllllllllll}lilllllll
I A CAUTION [
The installation of this appliance must conform to the requirements of the National Fire Protection Associa-
tion; the National Electrical Code, ANSl/NFPA No. 70 (latest edition) in the United States; the Canadian
Electrical Code Part 1, CSA 22.1 (latest edition) in Canada; and any state or provincial laws or local ordi-
nances. Local authorities having jurisdiction should be consulted before installation is made. Such appli-
cable regulations or requirements take precedence over the general instructions in this manual.
Save these instructions for future reference
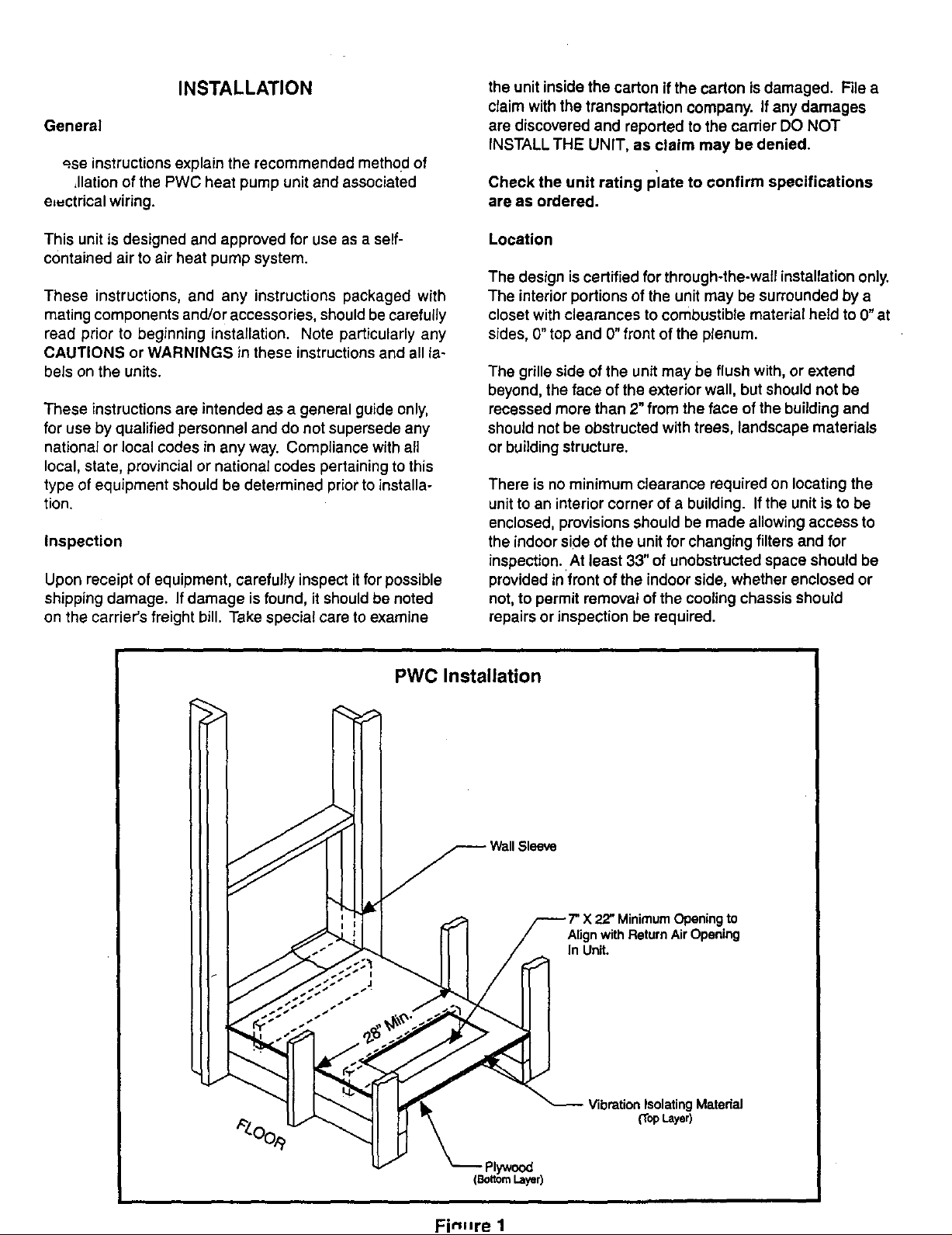
INSTALLATION
General
=.seinstructions explain the recommended method of
,llation of the PWC heat pump unit and associated
e_uctricalwiring.
the unit inside the carton ifthe carton isdamaged. File a
cfaimwith the transportation company. If any damages
are discovered and reported to the carrier DO NOT
INSTALL THE UNIT, as claim may be denied.
Check the unit rating p'late to confirm specifications
are as ordered.
This unit is designed and approved for use as a self-
contained air to air heat pump system.
These instructions, and any instructions packaged with
mating components and/or accessories, should be carefully
read prior to beginning installation. Note particularly any
CAUTIONS or WARNINGS in these instructions and all la-
bels on the units.
These instructions are intended as a general guide only,
for use by qualified personnel and do not supersede any
national or local codes in any way. Compliance with all
local, state, provincial or national codes pertaining to this
type of equipment should be determined priorto installa-
tion.
Inspection
Upon receipt of equipment, carefully inspect itfor possible
shipping damage. If damage is found, it should be noted
on the carrier's freight bill. Take special care to examine
PWCInstallation
Location
The design is certified for through-the-wall installation only.
The interior portions of the unit may be surrounded by a
closet with clearances to combustible material held to 0" at
sides, 0" top and 0" front ofthe plenum.
The grille side of the unit may be flush with, or extend
beyond, the face of the exterior wall, but should not be
recessed more than 2" from the face of the building and
should not be obstructed with trees, landscape materials
or building structure.
There is no minimum clearance required on locating the
unit to an interior corner of a building. If the unit is to be
enclosed, provisions should be made allowing access to
the indoor side of the unit for changing filters and for
inspection. At least 33" of unobstructed space should be
provided infront of the indoor side, whether enclosed or
not, to permit removal of the cooling chassis should
repairs or inspection be required.
Fin-re 1
Sleeve
F MinimumOpening to
Align with Return Air Opening
In Unit.
VibrationIsolating Matedal
{TopLayer)
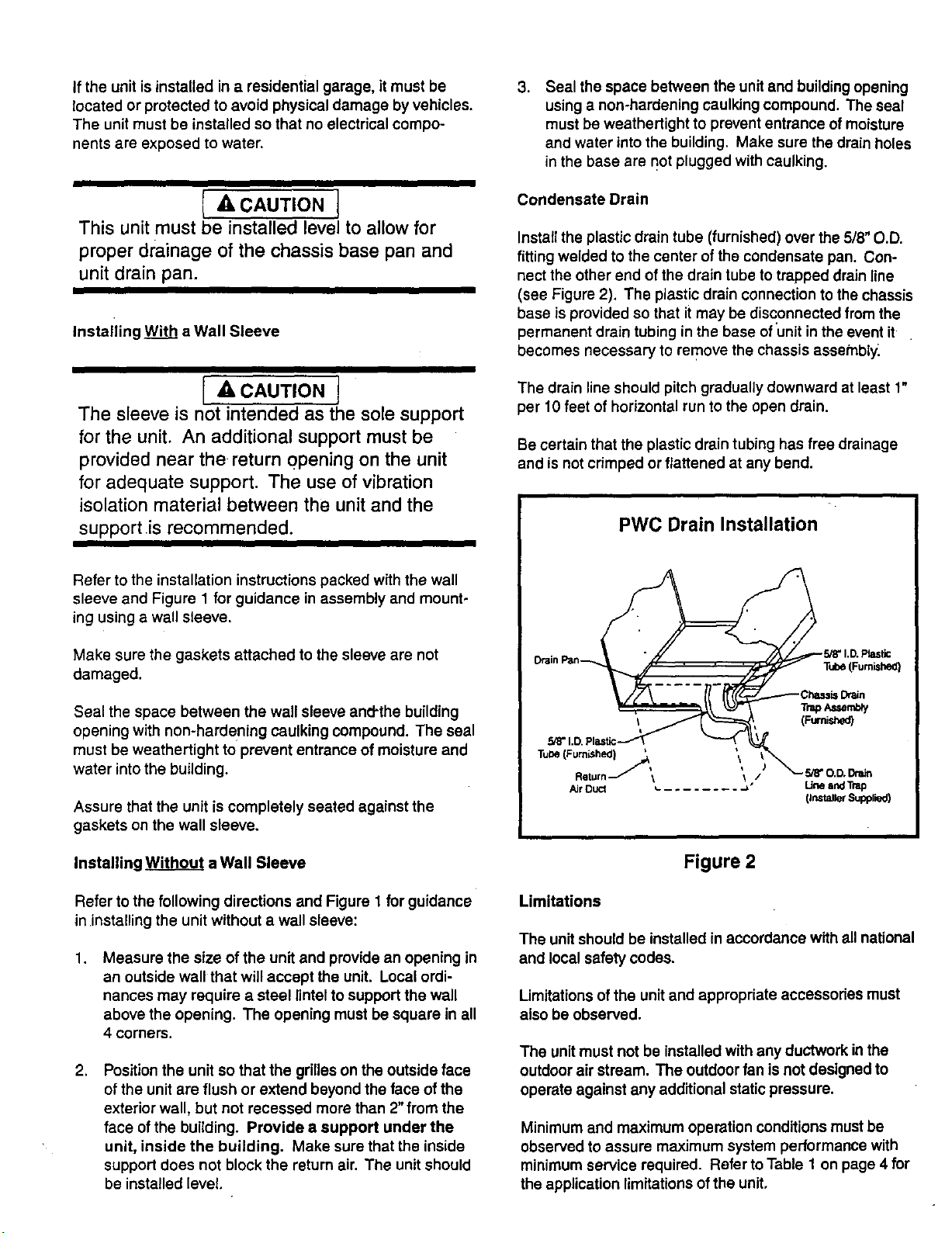
If the unitis installed in a residential garage, it must be
located or protected to avoid physical damage by vehicles.
The unit must be installed so that no electrical compo-
nents are exposed to water.
I
[A CAUT,ON]
This unit must be installed level to allow for
proper drainage of the chassis base pan and
unit drain pan.
Installing With a Wall Sleeve
.
Seal the space between the unit and building opening
using a non-hardening caulking compound. The seal
mustbe weathertight to prevent entrance of moisture
and water into the building. Make sure the drain holes
in the base are not plugged withcaulking,
Condensate Drain
Install the plastic drain tube (furnished) over the 5/8" O.D.
fitting welded to the center ofthe condensate pan. Con-
nect the other end of the drain tube to trapped drain line
(see Figure 2). The plastic drain connection to the chassis
base is provided so that it may be disconnected from the
permanent drain tubing in the base of unitin the event it
becomes necessary to remove the chassis assetnbly.
[ _, CAUTION l
The sleeve is not intended as the sole support
for the unit. An additional support must be
provided near the return opening on the unit
for adequate support. The use of vibration
isolation material between the unit and the
support is recommended.
Refer to the installation instructions packed with the wall
sleeve and Figure 1 for guidance in assembly and mount-
ing using a wall sleeve.
Make sure the gaskets attached to the sleeve are not
damaged.
Seal the space between the wall sleeve and-the building
opening with non-hardening caulking compound. The seal
must be weathertight to prevent entrance of moisture and
water into the building.
Assure that the unit is completely seated against the
gaskets on the wall sleeve.
The drain line should pitch gradually downward at least 1"
per 10feet of horizontal run to the open drain.
Be certain that the plastic drain tubing has free drainage
and is not crimped or flattened at any bend.
PWC Drain Installation
Drain Pan_
Installing Without a Wall Sleeve
Refer to the following directions and Figure I for guidance
in installing the unit without a wall sleeve:
.
Measure the size of the unit and provide an opening in
an outside wall that will accept the unit. Local ordi-
nances may require a steel lintel to support the wall
above the opening. The opening must be square in all
4 corners.
,
Position the unit so that the grilles on the outside face
of the unit are flush or extend beyond the face of the
exterior wall, but not recessed more than 2" from the
face of the building. Provide a support under the
unit, inside the building. Make sure that the inside
support does not block the return air. The unit should
be installed level
Figure 2
Limitations
The unit should be installed in accordance with all national
and local safety codes.
Limitations of the unit and appropriate accessories must
also be observed.
The unit must not be installed with any ductwork in the
outdoor air stream. The outdoor fan is not designed to
operate against any additional static pressure.
Minimum and maximum operation conditions must be
observed to assure maximum system performance with
minimum service required. Refer to Table 1 onpage 4 for
the application limitations of the unit.
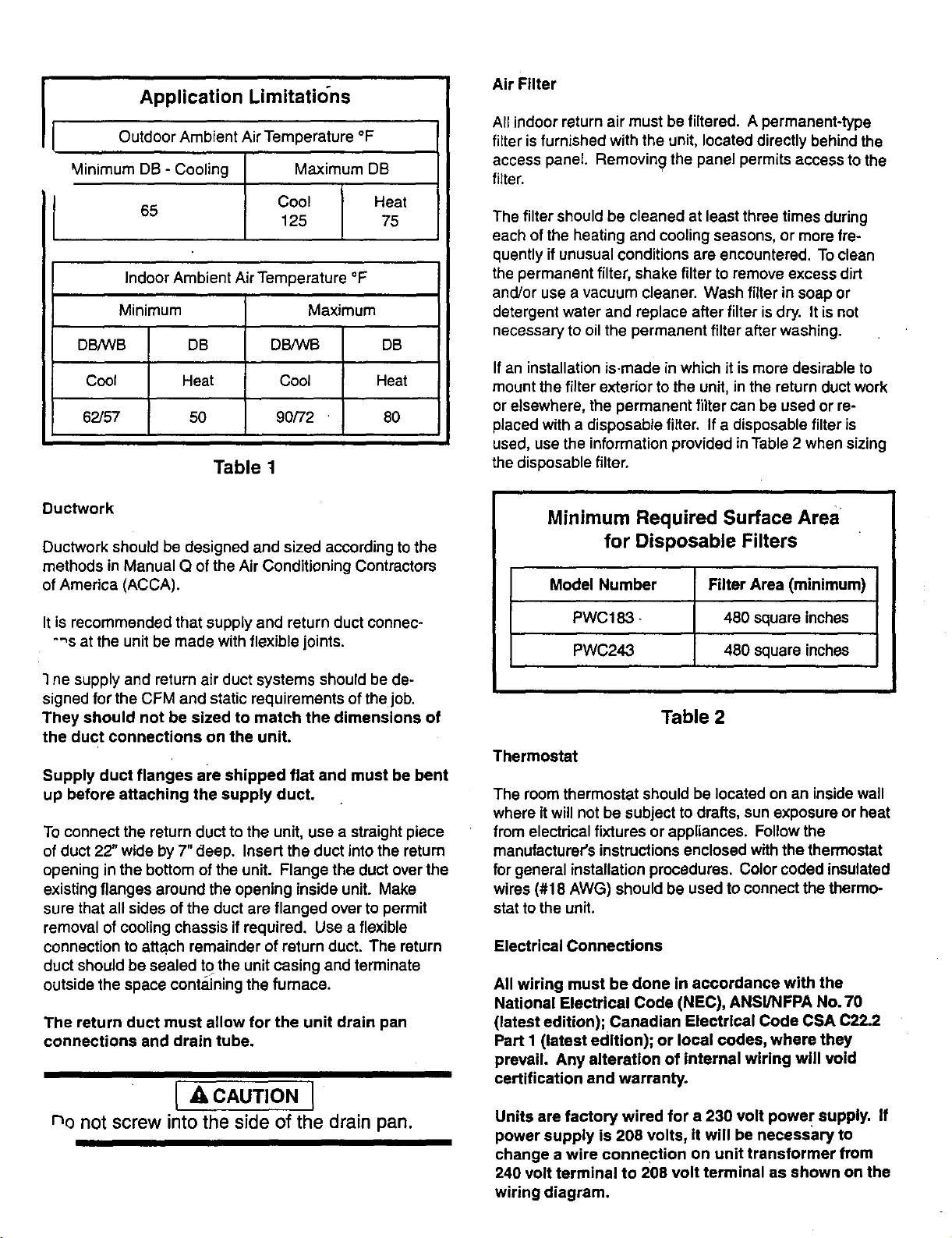
Application Limitations AirFilter
Outdoor Ambient Air Temperature °F
Minimum DB - Cooling Maximum DB
65
Indoor Ambient Air Temperature °F I
Minimum Maximum
DB/WB DB DB,_VB DB
Cool Heat Cool Heat
62/57 50 90/72 80
Table t
Cool Heat
125 75
All indoor return air must be filtered. A permanent-type
filter is furnished with the unit, located directly behind the
access panel. Removing the panel permits access to the
filter.
The filter should be cleaned at least three times during
each of the heating and cooling seasons, or more fre-
quently if unusual conditions are encountered. To clean
the permanent filter, shake filter to remove excess dirt
and/or use a vacuum cleaner. Wash filter in soap or
detergent water and replace after filter is dry. It is not
necessary to oil the permanent filter after washing.
If an installation is.made in which it is more desirable to
mount the filter exterior to the unit, in the return duct work
or elsewhere, the permanent filter can be used or re-
placed with a disposable filter. If a disposable filter is
used, use the information provided in Table 2 when sizing
the disposable filter.
Ductwork
Ductwork should be designed and sized according to the
methods in Manual Q of the Air Conditioning Contractors
of America (ACCA).
It is recommended that supply and return duct connec-
-'_s at the unit be made with flexible joints.
1ne supply and return air duct systems should be de-
signed for the CFM and static requirements of the job.
They should not be sized to match the dimensions of
the duct connections on the unit.
Supply duct flanges are shipped flat and must be bent
up before attaching the supply duct.
To connect the return duct to the unit, use a straight piece
of duct 22" wide by 7" deep. Insert the duct into the return
opening in the bottom of the unit. Flange the duct over the
existing flanges around the opening inside unit. Make
sure that all sides of the duct are flanged over to permit
removal of cooling chassis if required. Use a flexible
connection to attach remainder of return duct. The return
duct should be sealed to the unit casing and terminate
outside the space contai_ningthe furnace.
The return duct must allow for the unit drain pan
connections and drain tube.
[ ACAUTION J
no not screw intothe side of the drain pan.
Minimum Required Surface Area
for Disposable Filters
Model Number Filter Area (minimum)
PWC183 - 480 square inches
PWC24,3 480 square inches
Table 2
Thermostat
The room thermostat should be located on an inside wall
where it will not be subject to drafts, sun exposure or heat
from electrical fixtures or appliances. Follow the
manufacturer's instructions enclosed withthe thermostat
for general installation procedures. Color coded insulated
wires (#18 AWG) should be used to connect the thermo-
stat to the unit.
Electrical Connections
All wiring must be done In accordance with the
National Electrical Code (NEC), ANSl/NFPA No. 70
(latest edition); Canadian Electrical Code CSA C22.2
Part I (latest edition); or local codes, where they
prevail. Any alteration of internal wiring will void
certification and warranty.
Units are factory wired for a 230 volt power supply. If
power supply is 208 volts, it will be necessary to
change a wire connection on unit transformer from
240 volt terminal to 208 volt terminal as shown on the
wiring diagram.
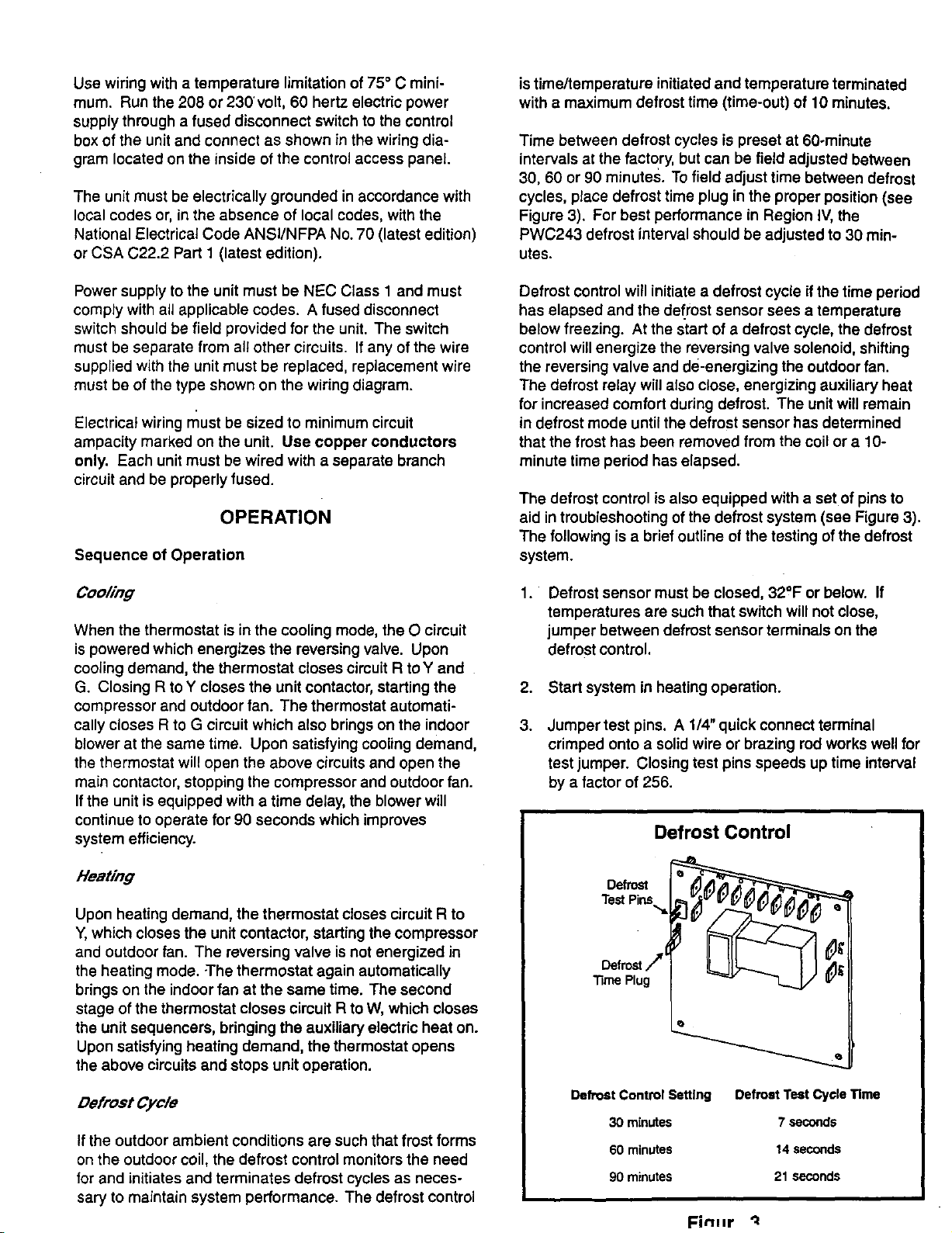
Usewiringwithatemperaturelimitation of 75 =C mini-
mum. Run the 208 or 230 volt, 60 hertz electric power
supply through a fused disconnect switch to the control
box of the unit and connect as shown in the wiring dia-
gram located onthe inside of the control access panel.
The unit must be electrically grounded in accordance with
local codes or, in the absence of local codes, with the
National Electrical Code ANSI/NFPA No. 70 (latest edition)
or CSA C22.2 Part 1 (latest edition).
is time/temperature initiated and temperature terminated
with a maximum defrost time (time-out) of 10 minutes.
Time between defrost cycles is preset at 60ominute
intervals at the factory, but can be field adjusted between
30, 60 or 90 minutes. To field adjust time between defrost
cycles, place defrost time plug in the proper position (see
Figure 3). For best performance in Region IV, the
PWC243 defrost interval should be adjusted to 30 min-
utes.
Power supply to the unit must be NEC Class 1 and must
comply with all applicable codes. A fused disconnect
switch should be field provided for the unit. The switch
must be separate from all other circuits. If any of the wire
supplied with the unit must be replaced, replacement wire
must be of the type shown on the wiring diagram.
Electrical wiring must be sized to minimum circuit
ampacity marked on the unit. Use copper conductors
only. Each unitmust be wired with a separate branch
circuit and be properly fused.
OPERATION
Sequence of Operation
Cooling
When the thermostat is in the cooling mode, the O circuit
is powered which energizes the reversing valve. Upon
cooling demand, the thermostat closes circuit R toY and
G. Closing R to Y closes the unit contactor, starting the
compressor and outdoor fan. The thermostat automati-
cally closes R to G circuit which also brings on the indoor
blower at the same time. Upon satisfying cooling demand,
the thermostat will open the above circuits and open the
main contactor, stopping the compressor and outdoor fan.
If the unit is equipped with a time delay, the blower will
continue to operate for 90 seconds which improves
system efficiency.
Defrost controlwill initiate a defrost cycle ifthe time period
has elapsed and the defrost sensor sees a temperature
below freezing. At the start of a defrost cycle, the defrost
control will energize the reversing valve solenoid, shifting
the reversing valve and de-energizing the outdoor fan.
The defrost relay will also close, energizing auxiliary heat
for increased comfort during defrost. The unit will remain
in defrost mode until the defrost sensor has determined
that the frost has been removed from the coil or a 10-
minute time period has elapsed.
The defrost control is also equipped with a setof pins to
aid in troubleshooting of the defrost system (see Figure 3).
The following is a brief outline of the testing of the defrost
system.
. Defrost sensor must be closed, 32°F or below. If
temperatures are such that switch will not close,
jumper between defrost sensor terminals on the
defrost control,
2. Start system in heating operation.
.
Jumper test pins, A 1/4" quick connect terminal
crimped onto a solid wire orbrazing rod works well for
test jumper. Closing test pins speeds up time interval
by a factor of 256.
Defrost Control
Heating
Upon heating demand, the thermostat closes circuit R to
Y, which closes the unit contactor, starting the compressor
and outdoor fan. The reversing valve is not energized in
the heating mode. -The thermostat again automatically
brings on the indoor fan at the same time. The second
stage of the thermostat closes circuit R to W, which closes
the unit sequencers, bringing the auxiliary electric heat on.
Upon satisfying heating demand, the thermostat opens
the above circuits and stops unit operation.
Defrost Cycle
Ifthe outdoor ambient conditions are such that frost forms
on the outdoor coil, the defrost control monitors the need
for and initiates and terminates defrost cycles as neces-
sary to maintain system performance. The defrost control
Defrost
TestPins.,,,=i
Defro=/
TimePlug
Defrost Control Setting Defrost Test Cycle Time
30 minutes 7 seconds
60 minutes 14 seconds
90 minutes 21 seconds
FinHr
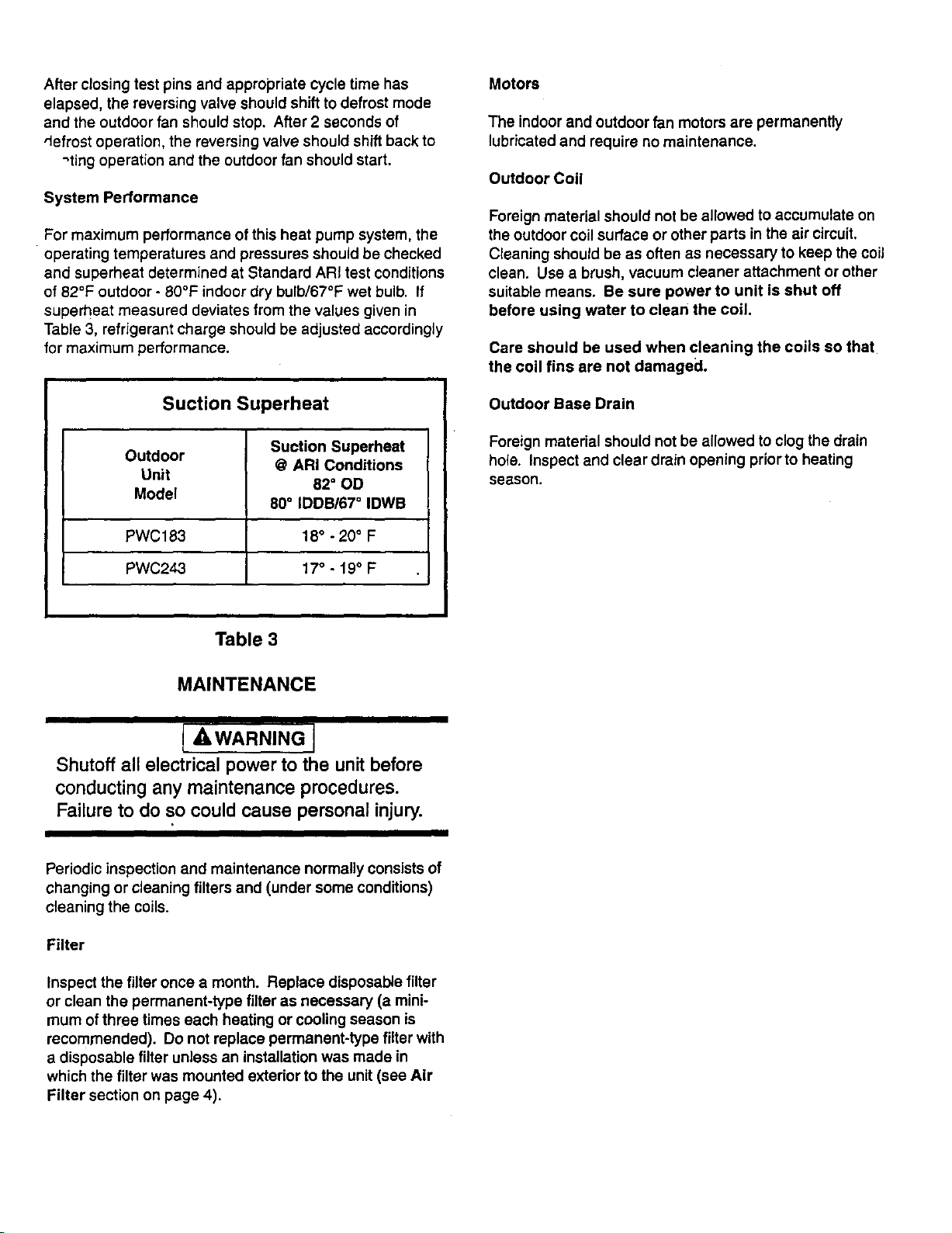
After closing test pins and appropriate cycle time has
elapsed, the reversing valve should shiftto defrost mode
and the outdoor fan should stop. After 2 seconds of
defrost operation, the reversing valve should shift back to
",tingoperation and the outdoor fan should start.
System Performance
For maximum performance of this heat pump system, the
operating temperatures and pressures should be checked
and superheat determined at Standard ARI test conditions
of 82°F outdoor - 80°F indoor dry bulb/67°F wet bulb. If
superheat measured deviates from the values given in
Table 3, refrigerant charge should be adjusted accordingly
for maximum performance.
Motors
The indoor and outdoor fan motors are permanently
lubricated and require no maintenance.
Outdoor Coil
Foreign material should notbe allowed to accumulate on
the outdoor coil surface or other parts in the air circuit.
Cleaning should be as often as necessary to keep the coil
clean. Use a brush, vacuum cleaner attachment or other
suitable means. Be sure power to unit is shut off
before using water to clean the coil.
Care should be used when cleaning the coils so that
the coil fins are not damaged.
Suction Superheat
Outdoor
Unit
Model
PWC183 18° - 20° F
PWC243 17° - 19° F
Suction Superheat
@ ARI Conditions
82 ° OD
80° IDDB/67 ° IDWB
Table 3
MAINTENANCE
Shutoff all electrical power to the unit before
conducting any maintenance procedures.
Failure to do so could cause personal injury.
Outdoor Base Drain
Foreign material should not be allowed to clogthe drain
hole. inspect and clear drain opening priorto heating
season.
Periodic inspection and maintenance normally consists of
changing or cleaning filters and (under some conditions)
cleaning the coils.
Filter
Inspect the filter once a month. Replace disposable filter
or clean the permanent-type filter as necessary (a mini-
mum ofthree times each heating or cooling season is
recommended). Do not replace permanent-type filter with
a disposable filter unless an installation was made in
which the filter was mounted exterior to the unit (see Air
Filter section on page 4).
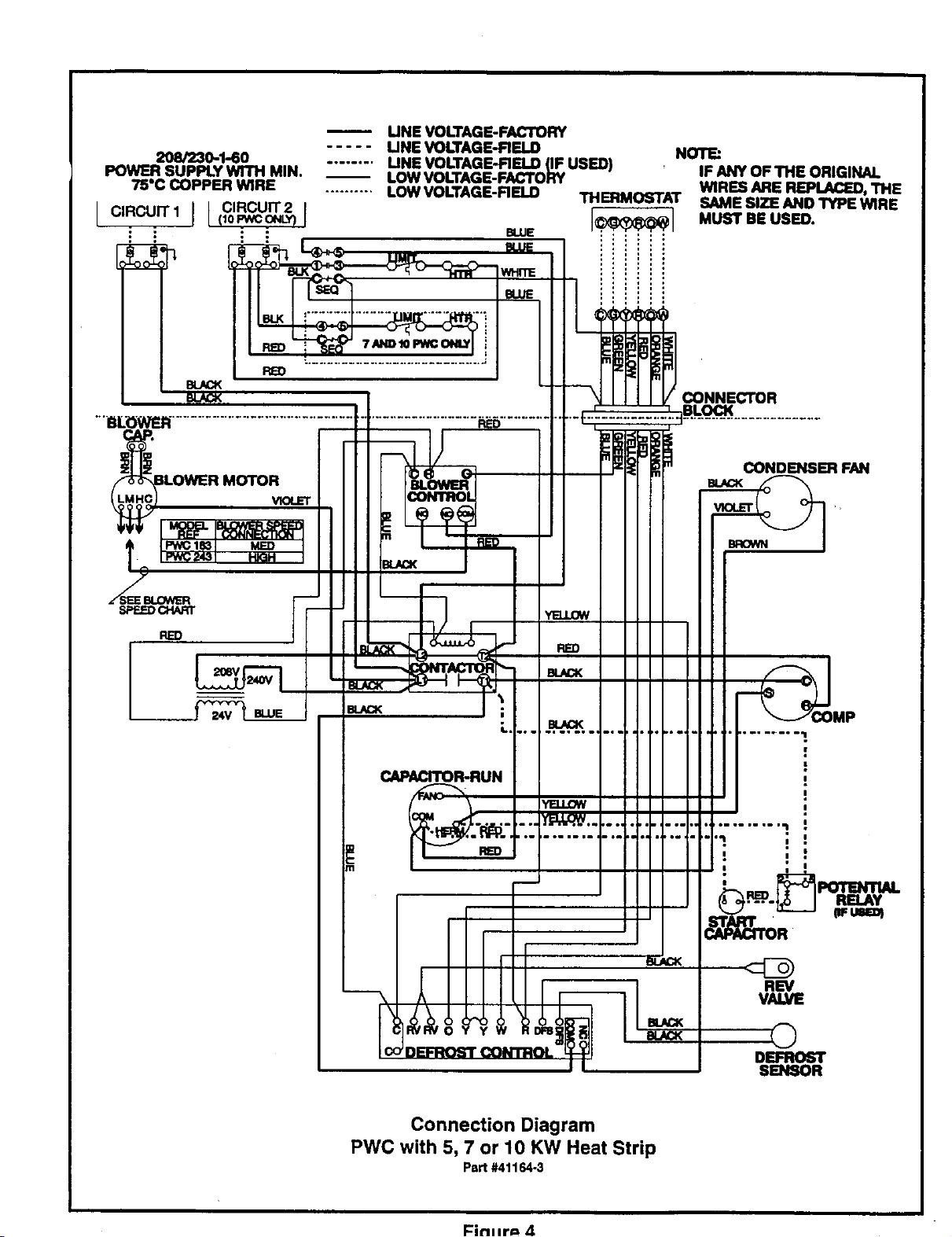
POWERSUPPLYWITHMIN.
208/230-1-60
75"CCOPPERWIRE
I CIRCUIT1I I (lo_cO_L'qCIRCUIT2I
•; ..; : :
P_D
BLACK
LOWER MOTORvloI_rr
UNE VOLTAGE-FACTORY
UNE VOLTAGE-RELD
........ UNE VOLTAGE-RELD (IF USED)
LOW VOLTAGE-FACTORY
.......... LOWVOLTAGE-FIELD
BLUE
7 AND 10 PWC ONLY
I
BLOWER
(
NOTE:
IF ANY OF THE ORIGINAL
WIRES ARE REP_, THE
SAME SIZE AND TYPE WIRE
MUST BE USED.
CONNECTOR
CONDENSER FAN
BLACK
BROWN
RED
M1
CAPACr_R-RUN
REV
VALVE
©
DEFROST
SENSOR
Connection Diagram
PWC with 5, 7 or 10 KW Heat Strip
Part #41164-3
Fin.r== 4
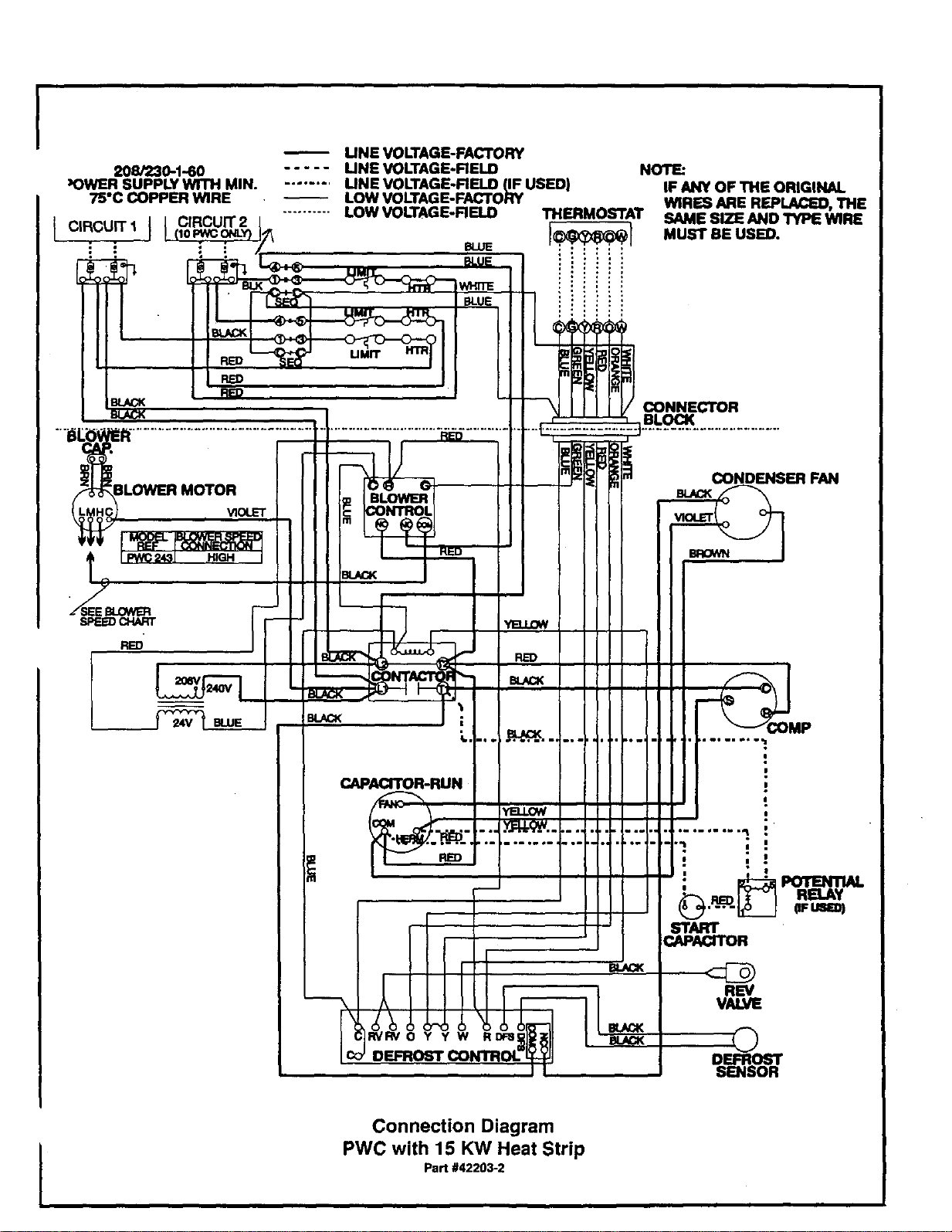
208/230-1-60
:OWER SUPPLY WITH MIN.
75"C COPPER WIRE
I CIRCUIT 1 I CIRCUIT 2
: i : :
: •
..... LINE VOLTAGE-RELD
UNE VOLTAGE-FACTORY
........ LINE VOLTAGE-FIELD (IF USED)
LOW VOLTAGE-FACTORY
.......... LOW VOLTAGE-R ELD
BLUE
NOTE:
IF ANY OF THE ORIGINAL
WIRES ARE REPLACED, THE
SAME SIZE AND TYPE WIRE
MUST BE USED.
RED
F_
UMrT
BLOWER
m
NT
CAPACITOR-RUN
CONNECTOR
BLOCK
CONDENSER FAN
E_CK
¥
I
I
RED
REV
VALVE
O
DEFROST
Connection Diagram
PWC with 15 KW Heat Strip
Part #42203-2
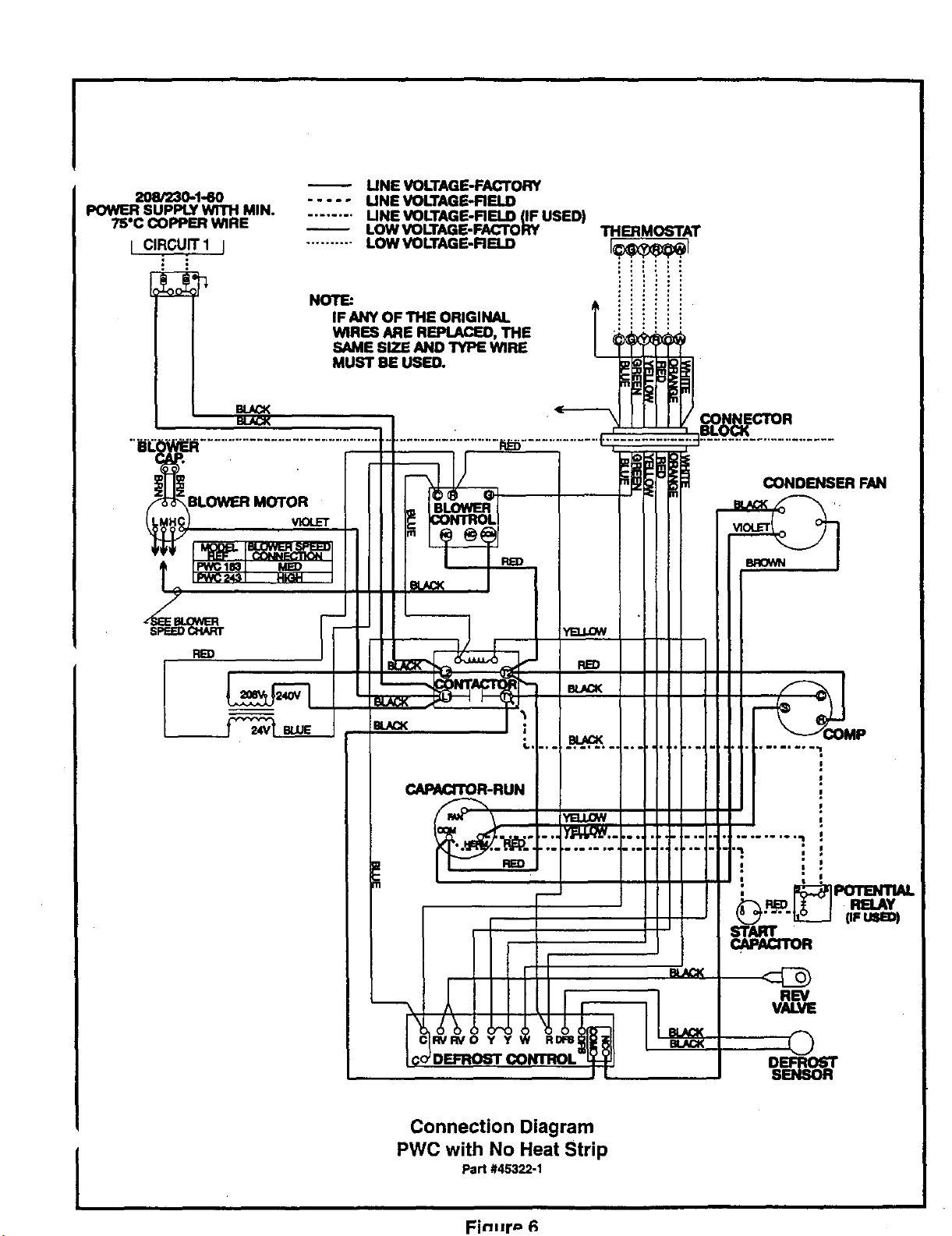
POWER SUPPLY WITH MIN.
208/230-1-60
75"C COPPER WIRE
BLOWER MOTOR
..... UNE VOLTAGE-FIELD
........ UNE VOLTAGE-FIELD (IF USED)
.......... LOWVOLTAGE-FIELD
NOTE:
LINE VOLTAGE-FACTORY
LOWVOLTAGE-FACTORY THERMOSTAT
IF ANY OF THE ORIGINAL
WIRES ARE REPLACED, THE
SAME SIZE AND TYPE WIRE
MUST BE USED.
BLOWER
CONDENSER FAN
_-RUN
I_)
RE)
RED
BROWN
: : °
!
, POTENTIAL
RELAY
pFUSe_
I
Connection Diagram
PWC with No Heat Strip
Part #45322-1
Fin-r== 6
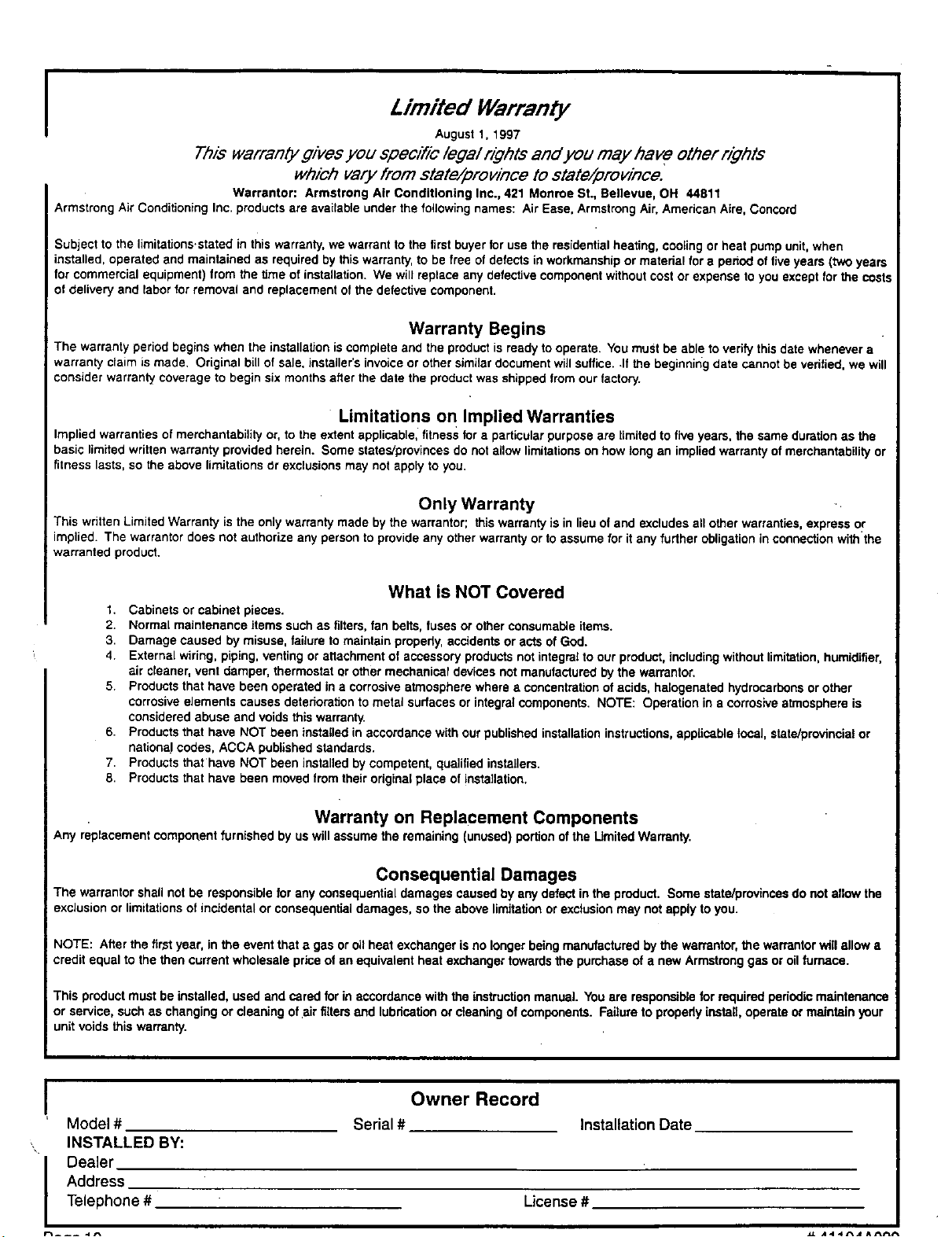
I
Limited Warranty
August 1, 1997
Thiswarran(ygivesyou specificlegalrightsand you may have otherrights
which vary from state/provincetostate/province.
Warrantor: Armstrong Air Conditioning Inc., 421 Monroe St., Bellevue, OH 44811
Armstrong Air Conditioning Inc products are available under the following names: Air Ease, Armstrong Air, American Airs, Concord
Subject to the limitafions.stated in this warranty, we warrant to the first buyer for use the residential heating, cooling or heat pump unit, when
installed, operated and maintained as required by this warranty, to be free of defects in workmanship or material for a pehod of five years (two years
for commercial equipment) from the time of installation. We will replace any defective component without cost or expense to you except for the costs
of delivery and labor for removal and replacement of the defective component.
Warranty Begins
The warranty period begins when the installafion is complete and the product is ready to operate. You must be able to verity this date whenever a
warranty claim is made. Original bill of sale, installer's invoice or other similar document will suffice..If the beginnir_g date cannot be Verified. we will
consider warranty coverage to begin six months after the date the product was shipped from our factory.
Limitations on Implied Warranties
Implied warranties of merchantability or, to the extent applicable, fitness for a particular purpose are timited to five years, the same duration as the
basic limited written warranty provided herein. Some states/provincas do not allow limitations on how tong an implied warranty of merchantability or
fitness lasts, so the above limitations dr exclusions may not apply to you.
Only Warranty
This written Limited Warranty is the only warranty made by the warrantor; this warranty is in lieu of and excludes all other warranties, express or
implied. The warrantor does not authorize any person to provide any other warranty or to assume for it any further obligation in connection withthe
warranted product.
What is NOT Covered
I. Cabinets or cabinet pieces.
2. Normal maintenance items such as filters, fan belts, fuses or other consumable items.
3 Damage caused by misuse, failure to maintain properly, accidents or acts of God.
4 External wiring, piping, venting or attachment of accessory products not integral to our product, including without limitation, humidifier,
air cleaner, vent damper, thermostat or other mechanical devices not manufactured by the warrantor.
5 Products that have been operated in a corrosive atmosphere where e concentration of acids, halogenated hydrocarbons or other
corrosive elements causes deterioratfon to metsi surfaces or integral components. NOTE: Operation in a corrosive atmosphere is
considered abuse and voids this warranty
6 Products that have NOT been installed in accordance with our published installation instructions, applicable focal, state/provincial or
national codes, ACCA published standards.
7 Products that have NOT been installed by competent, qualified installers.
8 Products that have been moved from their odginai place of installation.
Warranty on Replacement Components
Any replscement component furnished by us will assume the remaining (unused) portion of the Limited Warranty.
Consequential Damages
The warrantor shall not be responsible for any consequential damages caused by any defect in the product. Some state/provinces do not allow the
exclusion or limitations of incidental or consequential damages, so the above limitation or exclusion may not apply to you.
NOTE: After the first year, in the event that a gas or oil heat exchanger is no longer being manufactured by the warrantor, the warrantor will allow a
credit equal to the then current wholesale price of an equivalent heat exchanger towards the purchase of a new Armstrong gas or oil furnace.
This product must be installed, used and cared for in accordance with the instructiott manual You are responsible for required pedodic maintenance
or service, such as changing or cleaning of air filters and lubrication or cleaning of components. Failure to properly install, operate or maintain your
unit voids this warranty.
!
Model #
, INSTALLED BY:
Address
Telephone #
I ealer
Owner Record
Serial # Installation Date
License #
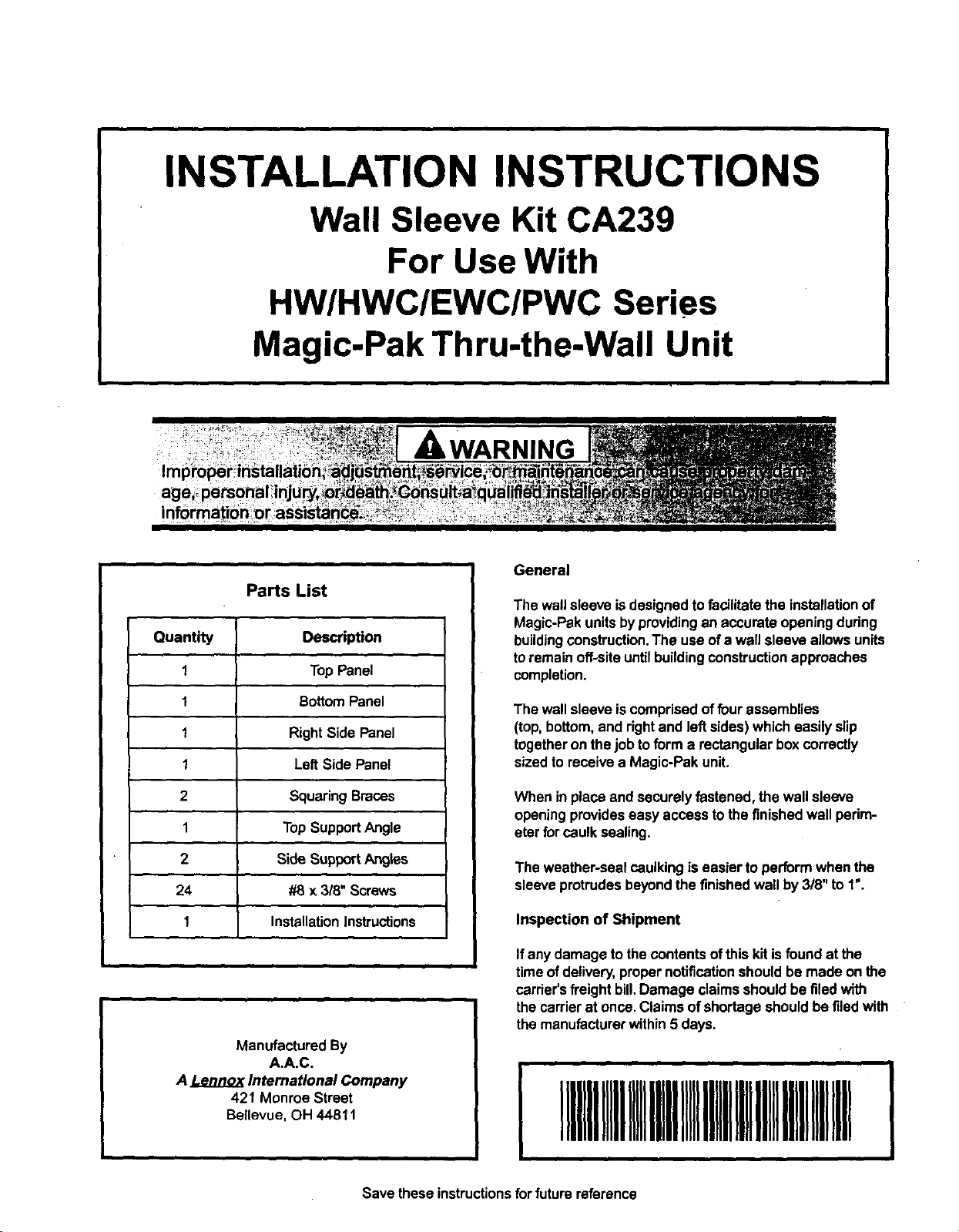
INSTALLATION INSTRUCTIONS
Wall Sleeve Kit CA239
For Use With
HW/HWC/EWC/PWC Series
Magic-Pak Thru-the-Wall Unit
_WARNING
age_
General
Parts List
The wall sleeve isdesignedto facilitatethe installationof
Quantity Description
1 TopPanel
1 BottomPanel
1 Right Side Panel
1 LeftSide Panel
Magic-Pakunits by providingan accurateopeningduring
buildingconstruction.The use ofa wall sleeveallowsunits
toremain off-siteuntilbuildingconstructionapproaches
completion.
The wall sleeve iscomprisedof four assemblies
(top,bottom,and rightand left sides) which easily slip
togetheron the job toform a rectangularbox correctly
sizedto receive a Magic-Pak unit.
2 Squaring Braces
1 TopSupportAngle
2 Side SupportAngles
24 #8 x 3/8" Screws
1 InstallationInstructions
Manufactured By
A.A.C.
A Lennox International Company
421 Monroe Street
Bellevue,OH 44811
Save these instructionsforfuture reference
When inplace and securely fastened, the wall sleeve
openingprovideseasy access to the finishedwall pedm-
efarfor caulksealing.
The weather-seal caulkingiseasier to performwhen the
sleeveprotrudesbeyondthe finishedwall by 3/8" to 1".
Inspection of Shipment
Ifany damage tothe contentsof this kitis found at the
timeof delivery,propernotificationshouldbe made onthe
carrier's freight bill.Damage claimsshouldbe filedwith
thecarrierat once. Claimsofshortage shouldbe filedwith
the manufacturerwithin 5 days.
1111111Ill1111111111IllIllIIIIIIIIIRillIIIIIIII
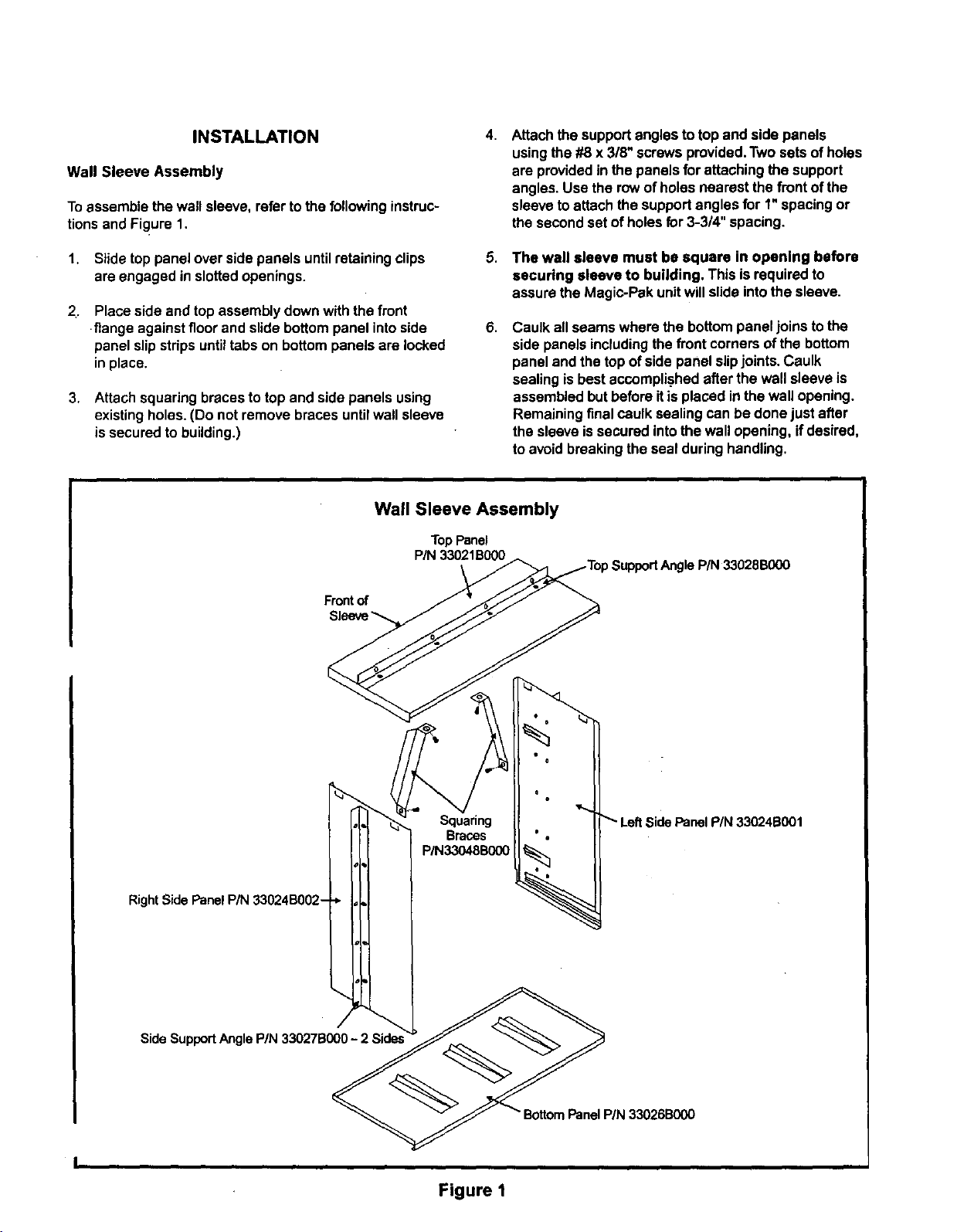
INSTALLATION
Wall Sleeve Assembly
Toassemble the wall sleeve, refer to the followinginstruc-
tionsand Figure 1.
4.
Attachthe supportanglesto top and side panels
usingthe #8 x 318"screwsprovided.Two sets of holes
are providedin the panels for attaching the support
angles. Use the rowof holes nearest thefront of the
sleeveto attach the support anglesfor 1"spacing or
the secondset of holesfor 3-3/4" spacing.
1. Slidetop panel over side panels untilretaining clips
are engaged in slottedopenings.
2_
Place side and top assemblydown withthe front
flange againstfloorand slide bottom panel intoside
panelslip strips untiltabs on bottom panels are locked
inplace.
3. Attach squaring bracesto top and side panels using
existingholes. (Do not remove braces untilwall sleeve
issecured to building.)
Wall Sleeve Assembly
P/N33021B000
Frontof
TopPanel
The wall sleeve must be square in opening before
securing sleeve to building. This is requiredto
assure the Magic-Pak unitwill slide intothe sleeve.
8.
Caulk all seams where the bottompaneljoins tothe
side panels includingthefront corners ofthe bottom
panel and the top of side panel slipjoints.Caulk
sealing is bestaccomplishedafterthe wall sleeve is
assembledbutbefore Risplaced inthe wall opening.
Remainingfinalcaulk sealing can be done just after
the sleeve issecured intothe wall opening, if desired,
to avoidbreakingthe seal duringhandling.
RightSide Panel P/N 33024B002-
Side SupportAngle PIN 33027BG00- 2 Side=
Squaring
Braces
P/N33048B000
Figure I
LeftSide Panel P/N 33024B001
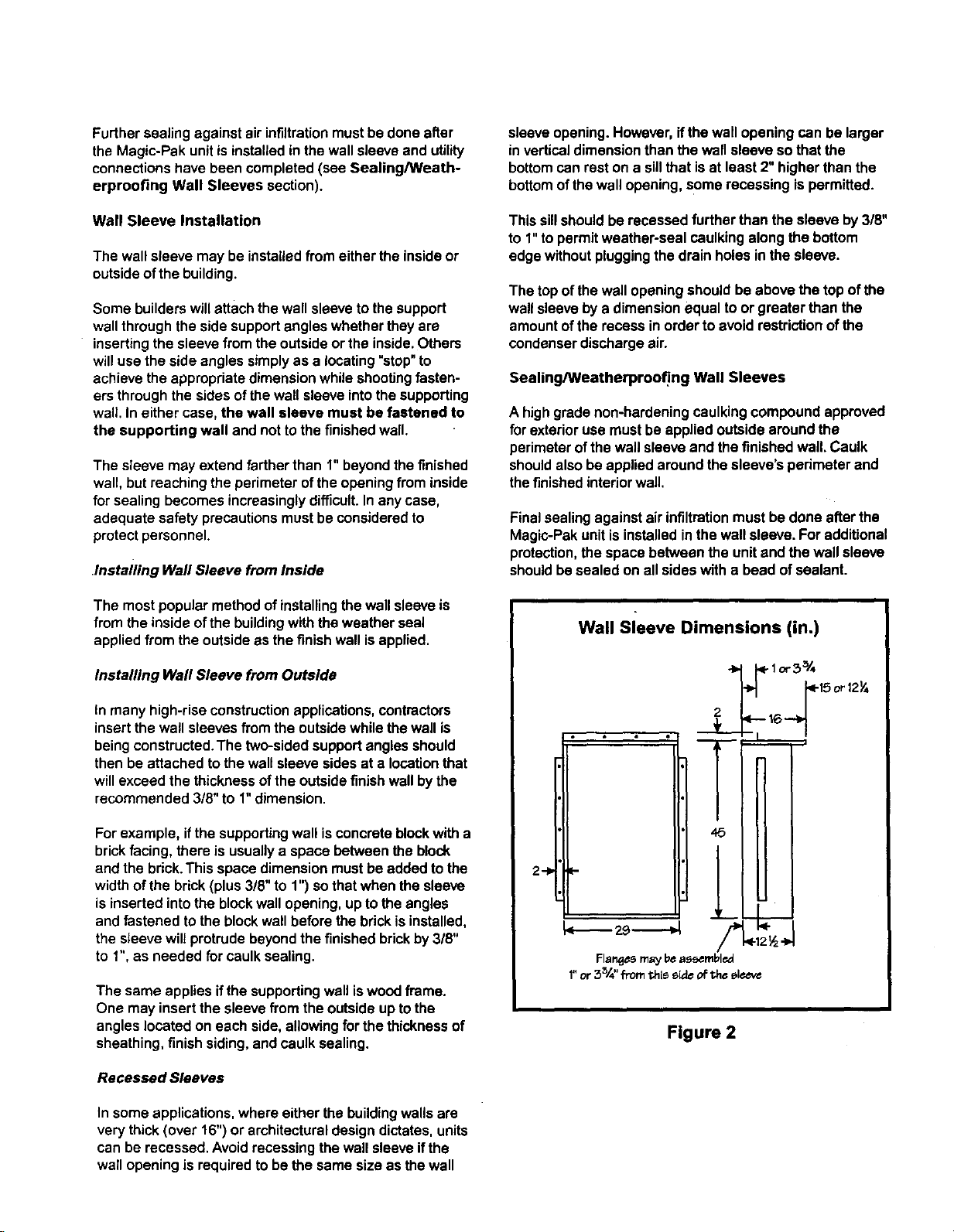
Furthersealing againstair infiltrationmustbe done alter
the Magic-Pak unitis installedin the wall sleeve and utility
connectionshavebeen completed (see Sealing/Weath-
erproofing Wall Sleeves section).
sleeveopening. However,if the wall openingcan be larger
inverticaldimensionthan the wall sleeve sothat the
bottomcan rest ona sill that isat least 2" higher thanthe
bottomof thewall opening,some recessing is permitted.
Wall Sleeve Installation
The wall sleeve may be installedfrom either the insideor
outsideofthe building.
Some builderswillattach the wall sleeve to the support
wallthroughthe side supportangleswhether they are
insertingthesleeve fromthe outsideor the inside.Othem
willuse the side angles simplyas a locating"stop"to
achievethe appropriatedimensionwhileshootingfasten-
ersthroughthe sides ofthe wallsleeve intothesupporting
wall.In either case,the wall sleeve must be fastened to
the supporting wall and notto thefinishedwall.
The sleeve may extend farther than 1"beyondthe finished
wall,but reachingtheperimeter ofthe openingfrom inside
for sealing becomes increasinglydifficult.In any case,
adequate safety precautionsmust beconsideredto
protectpersonnel.
Instailing Wall Sleeve from Inside
The most popular method of installingthe wallsleeve is
from the inside of the buildingwiththe weather seal
appliedfrom the outsideas the finishwall is applied.
Instalflng Wall Sleeve from Outside
Thissillshouldbe recessed further than the sleeve by3/8"
to 1"to permitweather-seal caulking along the bottom
edge withoutpluggingthe drain holes in the sleeve.
The topof the wall opening shouldbe above the topof the
wall sleevebya dimensionequal to or greater than the
amountof the recess in orderto avoid restrictionof the
condenserdischargeair.
Sealing/Weatherproofing Wall Sleeves
A highgrade non-hardeningcaulkingcompoundapproved
forexterioruse mustbe appliedoutsidearoundthe
perimeterofthe wall sleeveand the finishedwall. Caulk
shouldalso beapplied around the sleeve's perimeter and
thefinishedinteriorwall.
Final sealingagainst air infiltrationmust be donealter the
Magic-Pakunit is installedin thewall sleeve. For additional
protection,the space between the unit and the wall sleeve
shouldbe sealed on all sideswith a bead of sealant.
Wall Sleeve Dimensions (in.)
<.. 1or 3_/4
In manyhigh-rise constructionapplications,contractors
insertthe wall sleevesfrom the outsidewhilethewall is
beingconstructed.The two-sidedsupport anglesshould
then be attached to the wall sleeve sides at a locationthat
willexceed the thicknessofthe outsidefinish wall bythe
recommended3/8" to 1"dimension.
Forexample, ifthe supportingwall isconcreteblockwith a
brickfacing, there is usuallya space betweenthe block
and the brick.This space dimensionmust be addedto the
widthof the brick (plus3/8" to 1") so thatwhen the sleeve
is inserted intothe blockwall opening, up to the angles
and fastened to the blockwallbefore the brickisinstalled,
the sleevewilt protrudebeyondthe finishedbrickby 3/8"
to 1",as needed for caulk sealing.
The same applies if the supportingwall iswoodframe.
One may insertthe sleevefromthe outside upto the
angleslocated on each side,allowingforthe thicknessof
sheathing,finishsiding,and caulk sealing.
Recessed Sleeves
In someapplications,where either the buildingwallsare
verythick(over 16") or architecturaldesign dictates,units
can berecessed. Avoidrecessingthewall sleeve ifthe
wallopening is requiredto be the same size as the wall
2--I=
I.---- z9- -,4
Flar_es may b_ assembl_l
1"or 5_/4"from this e_e ofthe elc_v_
Figure 2
-$--
I
i
45
I
I
_t._
.16,.._15 or 12_
!