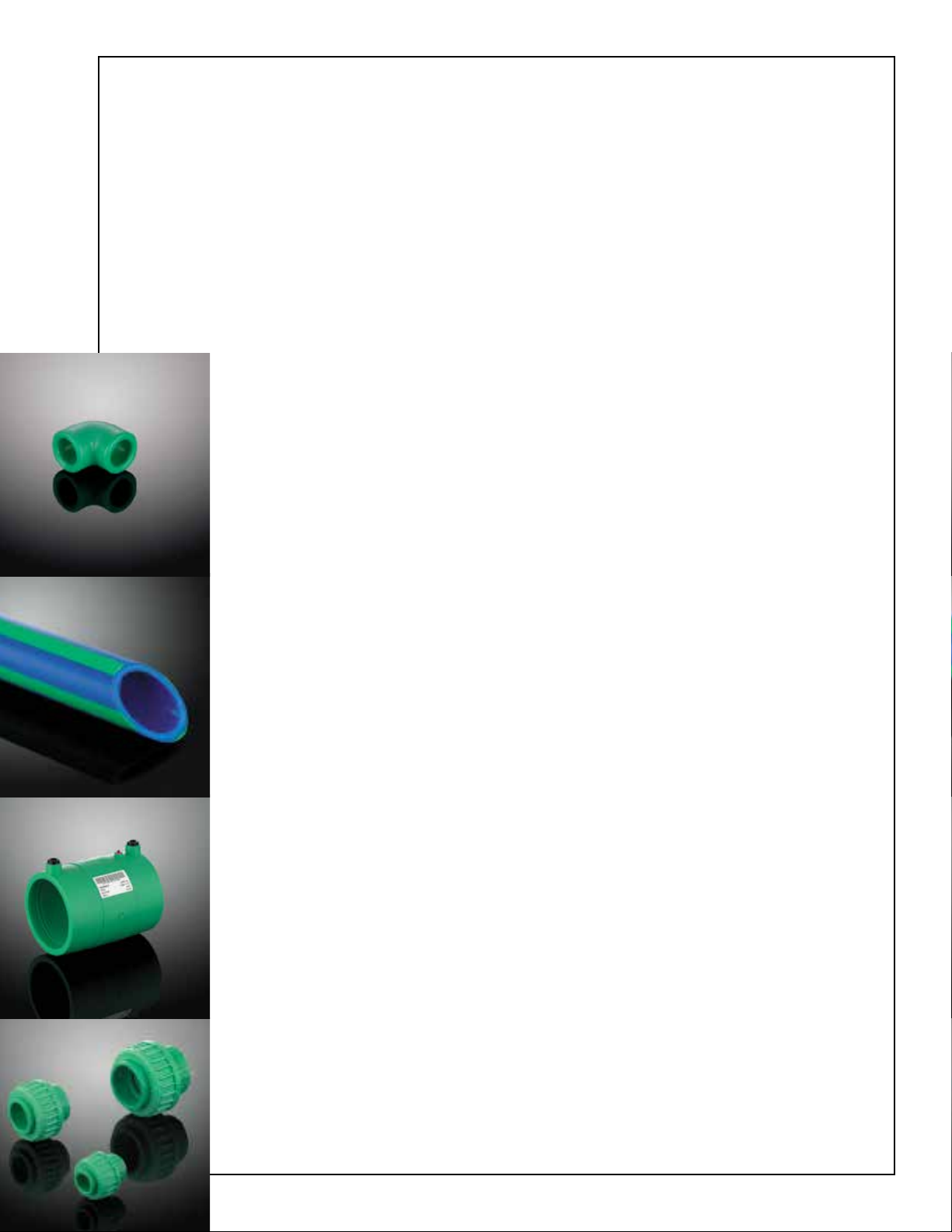
Technical Information for
aquatherm greenpipe
pressure pipe system for potable water,
food processing, and hygienically sensitive applications
®
climatherm
pressure pipe system for hydronic, compressed air,
chemical and industrial applications
aquatherm lilac
®
pressure pipe system for
recycled and reclaimed water systems
Table of Contents
Features
Quality Assurance
Planning
Installation Principles
Heat Fusion
Product Range
© 2012 aquatherm GmbH, aquatherm NA, L.c., and Aquatherm CA. All rights reserved.
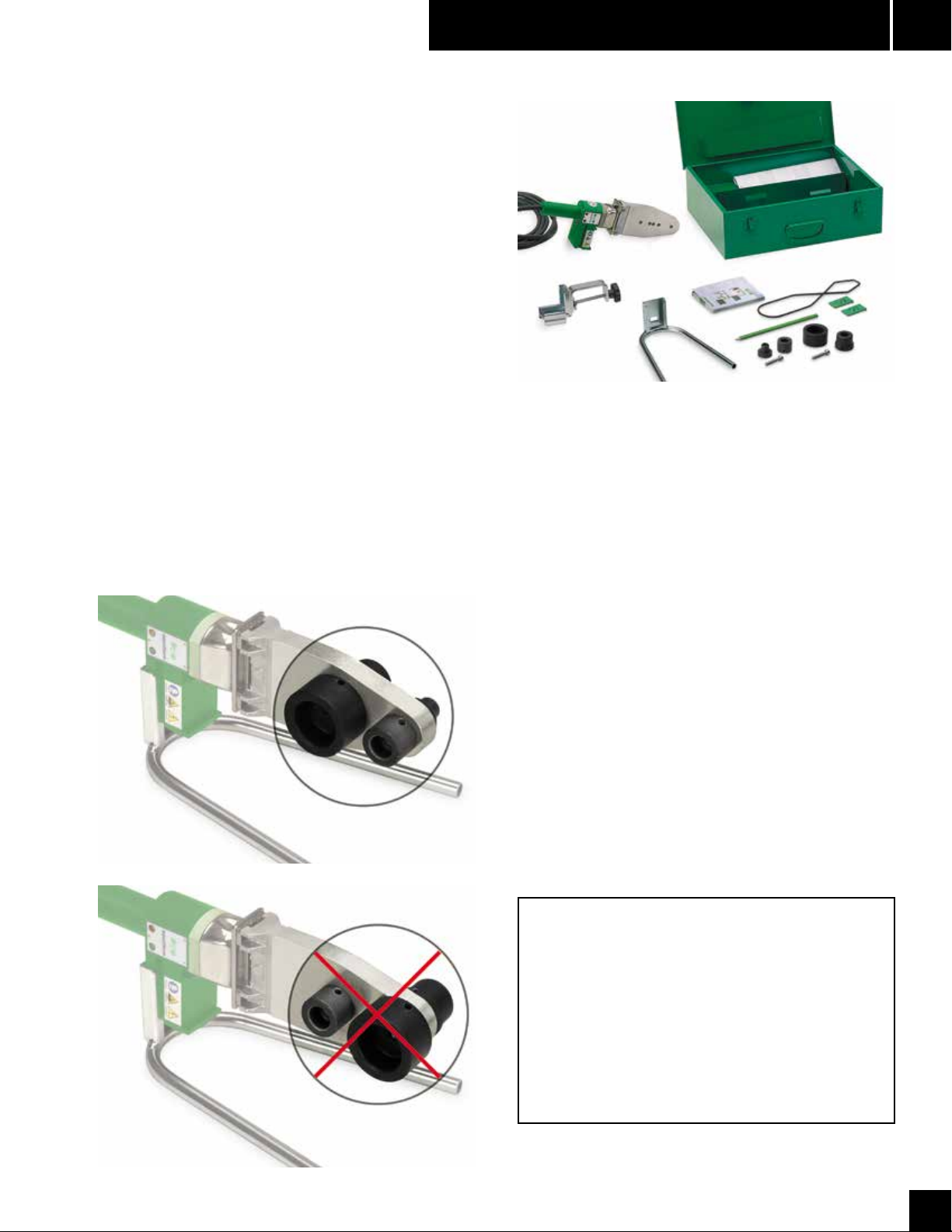
Installation training
Installers need to be trained by Aquatherm in heat fusion
techniques in order have their installation covered under
warranty. Training is available from local Aquatherm
trainers and instructors. Failure to follow proper installation
procedures will also invalidate the warranty.
Welding tools: Assembly
1. Use only Aquatherm approved tools and welding irons.
They are designed with the proper temperatures
and dimensions for working with Aquatherm
products. Information on approved tools is available
on Aquatherm’s website or from local Aquatherm
instructors and trainers.
2. Both the welding iron and the welding heads must be
free of residue, dirt, oils, and other impurities before
beginning fusion. Make sure they are clean before
assembly. If necessary, clean the welding tools with
a non-abrasive cleaning wipe. Use rubbing alcohol
or a similar agent. Avoid using corrosive cleaners or
cleaners that will leave a hazardous residue.
Heat Fusion
The assemblies and fusions shown in this chapter are done using the
Aquatherm branded tools. Assembly and operation instructions may vary
for other approved tools. Follow any additional instructions or variations
given by the tool’s manufacturer.
3. Before plugging in the iron, place the welding heads
on the welding iron so that there will be full surface
contact between the welding head and the heating
plate. Welding heads over 1 ¼” (40 mm) must always
be fitted to the rear position of the heating plate. Outlet
welding heads should always be fitted in the rear
position unless there is not enough available space
around the connection.
5
Right
4. Tighten the welding heads until they are almost
touching the heating plate. Do not finish tightening the
welding heads until the heating plate is hot. Tightening
the heads completely before the iron is hot will leave
impressions on the heating plate and reduce its
performance over time.
5. Plug in the welding tool. Depending on the ambient
temperature, it will take 10 - 30 minutes to heat up the
heating plate. The tool gives a signal when it is plugged
in, and gives another signal when it reaches its target
temperature.
Electrical supply:
Make sure that the electrical supply used is fully
compatible with the welding iron being used.
Improper use of any electrical device can cause
harm to both the tool and the operator. Make
sure any extension cords used are compatible
with the power input of the welding tools. Note that
fluctuations in the power supply can cause the tool
to go through longer heating cycles.
Wrong
5.1
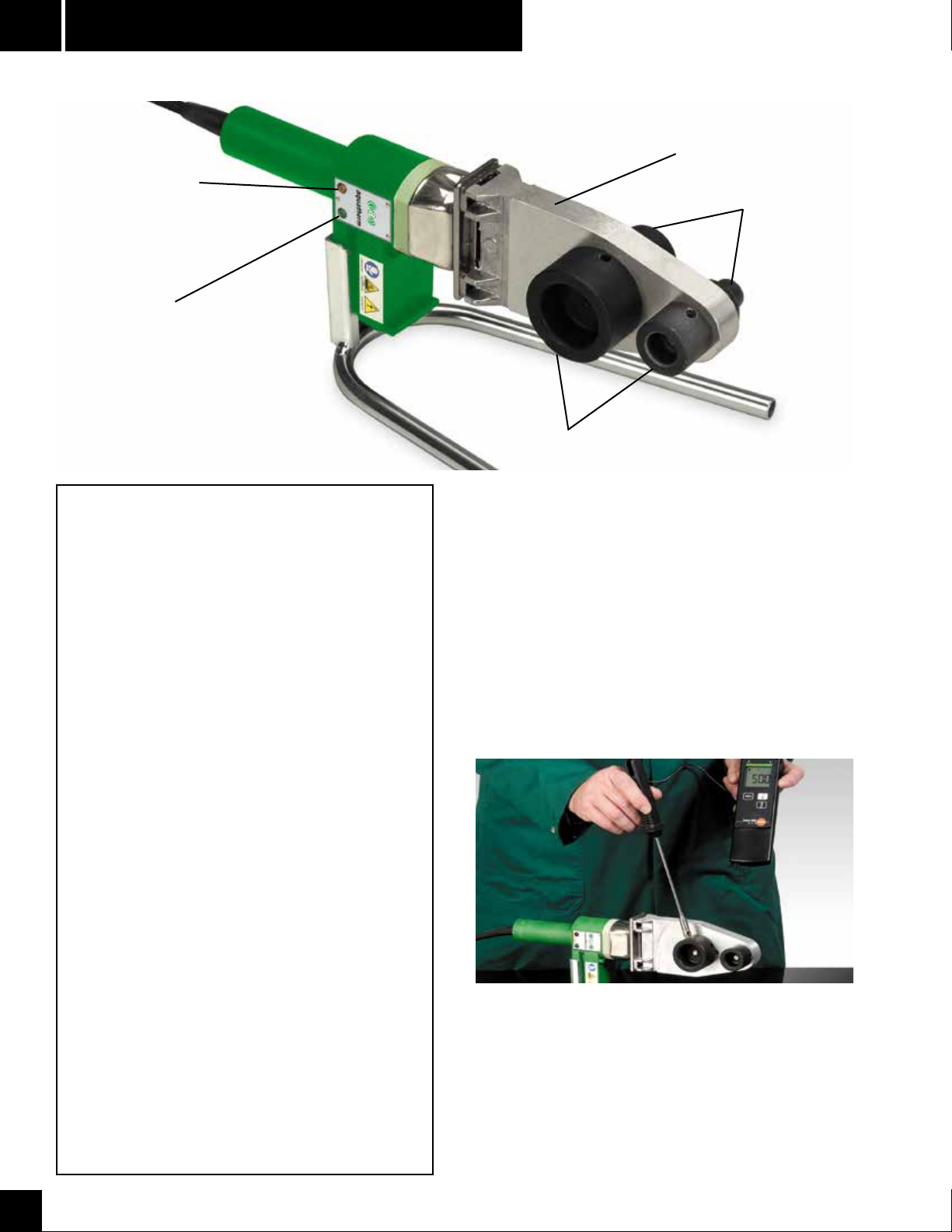
5
Heat Fusion
Temperature light
(yellow)
- Cycles on while the iron is heating
- Cycles off when the iron reaches 500 °F
Operating light
(green)
- On whenever the tool is plugged in
Heating plate
Welding head
Welding head
Safety precautions
By using a non-hazardous material and an emissionfree joining process, Aquatherm has eliminated
many of the hazards of installing a piping system.
However, there will always be a certain level of risk
involved in pipe installation, so it is imperative to
always follow the appropriate safety precautions.
The irons are the primary concern. The surface
temperature of the welding iron and heads will
normally be between 450 °F (240 °C) and 500 °F
(260 °C) during operation and may remain at these
temperatures for as long 30 minutes after being
unplugged.
When working with the welding irons, always
wear the appropriate hand and arm protection to
avoid the risk of burns. Protective eyewear is also
recommended.
During operation, always be aware of the location
of the iron. Do not leave the iron hanging loosely or
allow it to brush up against flammable materials.
Make sure to keep the iron clear of other people.
Always post a sign to inform those working nearby
that the iron is hot and could pose a safety risk to
them.
Do not leave the iron unattended while it is plugged
in. After unplugging the iron, protect it with a heatresistant covering or place the iron back in its
container. Do not allow the cord to contact the
welding surfaces.
Welding tools: Heating phase
6. After the iron is hot, tighten the welding heads carefully
with the hex wrench. Do not grab the welding heads with
pliers or other tools that could damage the coatings.
Make sure the welding heads are in complete contact
with the heating plate.
7. The temperature of 500 °F (260 °C) is required for
welding with the Aquatherm piping systems. The
temperature of the welding head must be checked
before starting the welding process. This can be done
with a digital thermometer capable of measuring
temperatures up to 650 °F (340 °C).
Important: If the pipe or the air around it is below 40 °F
(5 °C), heating times are increased by 50%. Remember
to take greater care with the pipe as it can become
brittle in cold temperatures. Using power cutters on cold
pipe can cause cracking and is not recommended. Use
standard ratchet or wheel cutters instead. Never preheat the pipe beyond 100 °F (38 °C).
5.2
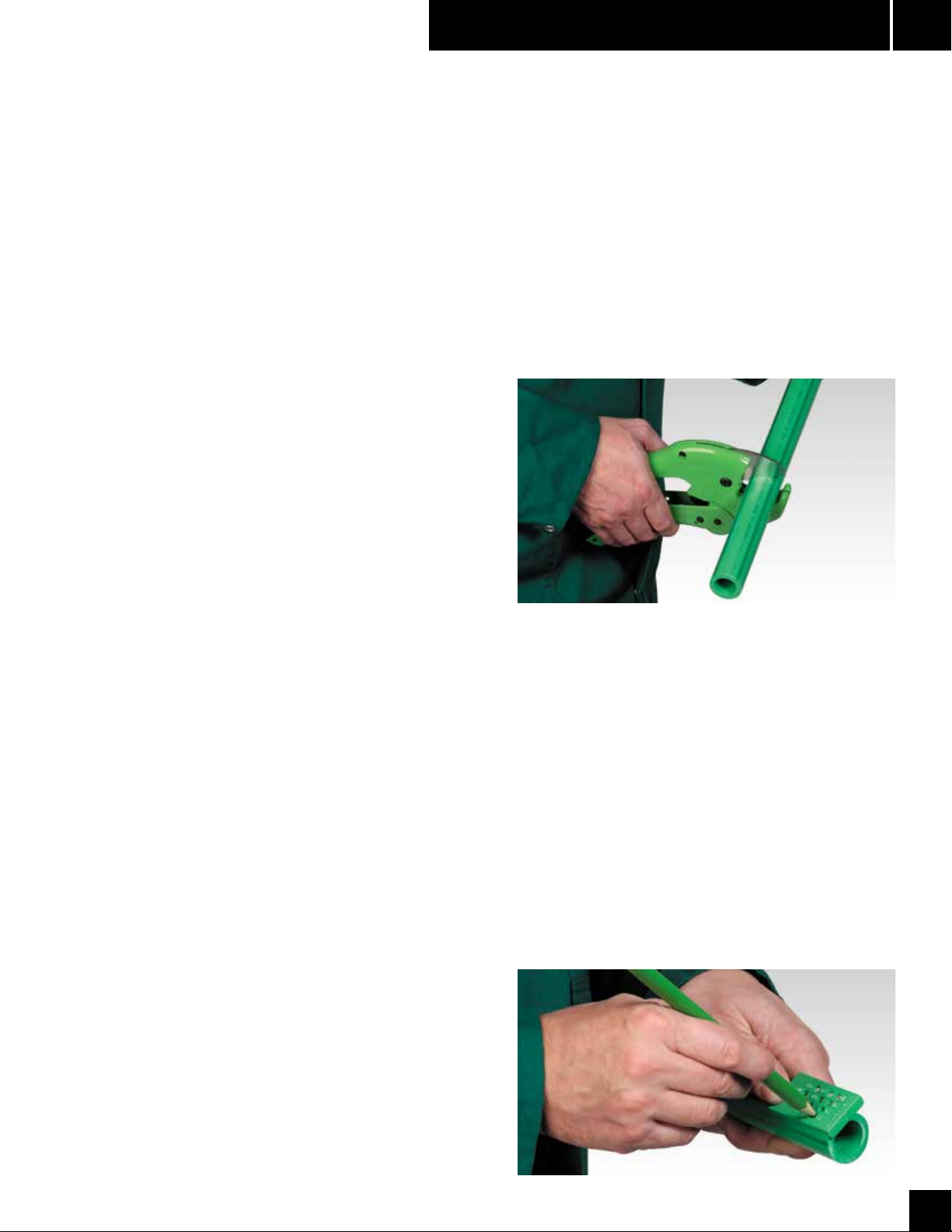
Heat Fusion
5
Welding tools: Handling
8. Changing welding heads on a heated iron requires the
installer to check the temperature on the new head
once it heats up.
9. If the tool has been unplugged (e.g. during longer
breaks), the heating process must be restarted (see
item 5).
10. After use, unplug the welding tool and let it cool down.
Never use water to cool the welding device, as this
will destroy the temper of the metal. Always keep the
welding heads dry.
11. Protect Aquatherm welding tools and heads against
impurities. Residue from previous fusions may lead to
an incorrect connection. After cooling, the heads can
be cleaned with a non-abrasive cloth.
12. For a proper fusion, damaged or scratched welding
heads must be replaced, as only undamaged heads
guarantee a perfect connection.
13. Never attempt to open or repair a defective tool. Return
the defective iron to the supplier for repair.
Socket fusion: Preparation
1. Make sure the Aquatherm welding devices and tools
comply with the guidelines in “Welding tools.”
2. All devices and tools must have reached the necessary
operating temperature of 500 °F (260 °C). This should
be checked on the welding head, not the heating plate.
This should be verified with a handheld contact or
digital thermometer.
3. Cut the pipe at right angles to the pipe axis. Only use
Aquatherm cutters or other suitable cutting tools.
Inspect the pipe thoroughly for any cracks.
14. Check the operating temperature of the Aquatherm
welding irons regularly by means of a suitable
measuring device.
Welding tools: Guidelines
15. Fusion welding of joints in Aquatherm piping systems
must be done in accordance with the instructions in
this manual. Additional information is available, and
should be followed where applicable and not in conflict
with these instructions:
• ASTM D 2657 - Standard practice for heat fusion
joining of polyolefin pipe and fittings.
• ASTM F 1290 - Standard practice for electrofusion
joining polyolefin pipe and fittings.
16. Remember to use gloves when handling the iron
while it is plugged in and for at least 30 minutes after
unplugging it. Avoid leaving the iron exposed and
unguarded, as passers-by might accidentally injure
themselves. Always post a sign to inform those working
nearby that the iron is hot and could pose a safety risk
to them.
Always ensure that cutters are sharp. Cutting pipes
with dull or damaged ratchet cutters can cause the
pipe to crack.
Only use the cutters to cut fusiolen® PP-R material.
It is also acceptable to use power saws with plasticappropriate blades. Take care that the pipe surface is
free from burrs or cutting debris and remove where
necessary.
4. Mark the welding depth at the end of the pipe with a
pencil using the Aquatherm marking guide.
5. Mark the desired position of the fitting on the pipe
and/or fitting. The markings on the fitting and the
uninterrupted line on the pipe may be used as a guide
over short distances.
5.3