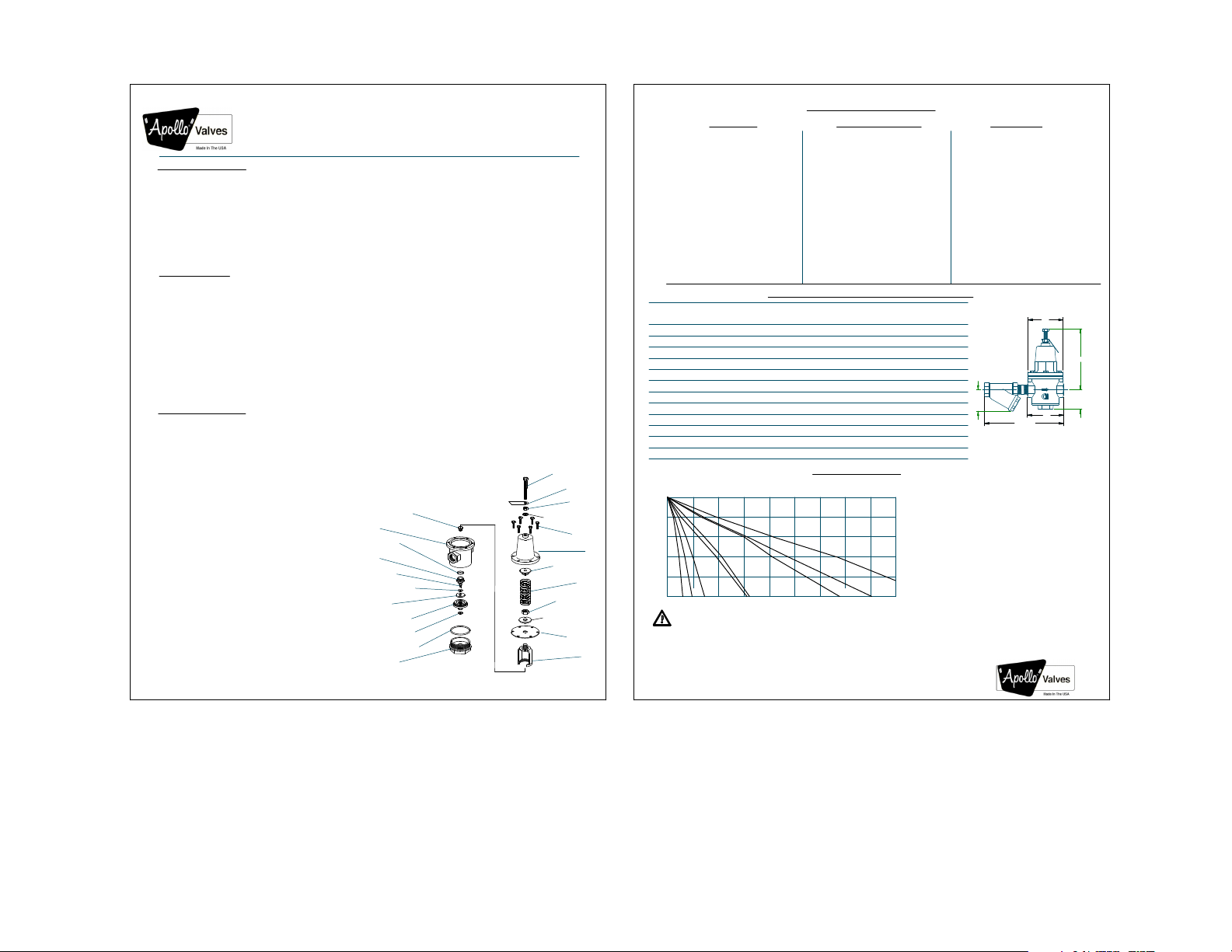
MODEL PRH
(36H & LEAD FREE 36H SERIES)
Water Pressure Reducing Valve
INSTALLATION
The APOLLO PRH must be installed in a conveniently accessible location to facilitate testing, repair and
maitenance. Flush upstream piping thoroughly to remove any foreign matter prior to installing the device. It
is important that this unit be installed between shut-off valves in order to isolate the unit during repair and
service. INSTALL THE DEVICE WITH THE ARROW ON THE VALVE POINTING IN THE DIRECTION OF
FLOW. Do not install this unit in areas subject to freezing temperatures. Provide sufficient support on the
piping system upon installation of this unit.
CAUTION: Anytime a reducing valve is adjusted, a pressure gauge must be used downstream to verify
a correct pressure setting. Maximum pressure will be obtained prior to bottoming out adjustment
screw. DO NOT BOTTOM ADJUSTMENT BOLT ON BELL HOUSING.
OPERATION
Do not install the unit in areas subject to freezing temperatures.
The PRH are designed to reduce high supply pressure (up to 400 psig) to a lower outlet pressure within
it's adjustment range. The standard unit is factory set at 50 psig outlet pressure (static condition), and is adjustable from 25 to 75 psig (low and high pressure setting option available).
During static (no-flow) conditions, the valve is closed because the magnitude of the diaphragm force exposed to
the downstream pressure is greater than the valve spring force. The balance of the forces on the supply and
spring pressure (which tends to open the valve) against the diaphragm pressure, determines the outlet or reduced pressure downstream of the valve.
the set pressure. By decreasing the spring load (turning the adjusting screw counterclockwise), the set
pressure decreases.
Under flow conditions, the pressure under the diaphragm will start to fall below the set pressure causing the
spring and the supply pressure to open the valve and allowing more water to flow.
The amount of water that will pass through the valve depends on the difference between the inlet and the outlet
pressure. As the pressure differential increases, the volume of water increases.
MAINTENANCE
Regular inspection, testing and cleaning of water pressure reducing valve and other components in a piping system assures maximum life and proper function.
The PRH is designed so that it can be serviced through the bottom plug without removing the cap and
disturbing the pressure setting. Both the seat and seat disc assembly can be accessed through the bottom plug.
NOTE: PRIOR TO DISASSEMBLING THE UNIT, SHUT-OFF WATER SERVICE AND RELIEVE PRESSURE DOWNSTREAM.
a) DISASSEMBLY OF SEAT
1. Unscrew bottom plug.
2. Unscrew seat disc holder.
3. Remove seat.
b) DISASSEMBLY OF SEAT DISC
1. Remove bottom plug and seat disc holder.
2. In the seat disc holder, remove seat disc by
unscrewing the seat screw.
c) DISASSEMBLY OF DIAPHRAGM
CAUTION:
CAP IS SPRING LOADED.
RELIEVE SPRING PRESSURE BY
UNSCREWING THE ADJUSTING SCREW
BEFORE ATTEMPTING TO REMOVE CAP!
1. Remove cap bolts.
2. Remove cap, spring retainer, and spring.
3. Unscrew diaphragm nut.
4. Remove diaphragm washer and diaphragm.
d) DISASSEMBLY OF BY-PASS ASSEMBLY
1. Unscrew bottom plug and remove seat disc holder.
2. Relieve spring pressure on the cap and remove
cap bolts. Dismantle the spring retainer and spring.
3. Remove yoke with diaphragm attached.
Do not unscrew diaphragm nut.
4. Unscrew the by-pass assembly.
High Capacity
Increasing the spring load through the adjusting screw will increase
By-Pass Assembly
Body
Seat O-Ring
Seat
Seat Screw
Seat Disc Washer
Seat Disc
Seat Disc Holder
Disc Holder O-Ring
Bottom Plug O-Ring
Bottom Plug
Adjusting Screw
Self Sealing Washer
Spring Retainer
Diaphragm Washer
I-5957-00
Rev. M
Nameplate
Lock Nut
Cap Bolt
Spring
Diaphram Nut
Diaphragm
Yoke
TROUBLE-SHOOTING
PROBLEM POSSIBLE CAUSE SOLUTION
1. Inlet pressure equalizes outlet
pressure at no flow conditions.
2. Outlet pressure rises above inlet
pressure.
3. Excessive noise within the pipe line at the PRH.
Leakage within the valve may be due
to the following:
(a) Seat disc not sealing tight
against seat
(b) Seat O-ring may be cut or damaged
(c) Damaged or cut diaphragm
(d) By-pass leaking
By-pass assembly not opening or
clogged
Thermal expansion downstream
High water velocity at the pipeline
can sometimes cause a whistling
noise or hum.
-Inspect and replace if defective.
-Inspect and replace if defective.
-Replace
-Inspect by-pass washer and rubber
ball.Rubber ball should move freely inside
the housing. If defective replace the
by-pass assembly.
-Disassemble the unit, clean and replace
the by-pass assembly, if defective.
-Rubber ball should move freely inside the
housing.
-Slight adjustment on the PRH may
eliminate the noise. If not, the line or the
PRH may be too small for the application.
DIMENSIONS (in.) & WEIGHTS (lbs.)
Size
(NPT)
A B C D
1/2" 4-1/8 2-1/4 7 1-7/8 8-3/8 4 7 6
3/4" 4-1/8 2-1/4 7 2-7/16 9 4 7 6
1"
1-1/4"
1-1/2"
2-1/2"
Flanged
2-1/2"
Flow curves are based on static conditions of: Inlet pressure = 100 psig.
Outlet pressure = 50 psig
0
5
Cap
10
15
20
PRESSURE FALL-OFF (PSI)
¾
½"
25
500 100 150 200 250 300 350 450400
10103-3/8
3-15/16
"
1" 1½" 2" 2½" 3"
1-1/4"
CALIFORNIA PROP 65: WARNING:
FOR NON-LEAD FREE VALVES:
for potable water services (water intended for human consumption).
FOR LEAD FREE VALVES:
Act (SDWA). Suitable for potable water applications intended for human consumption.
E F
3-7/8
4-5/8
16
5-15/16
16-11/16
6-15/16
6-1/4
20
7-1/8
21-11/16
8-1/8
FLOW CURVES
FLOWRATE (GPM)
Cancer and Reproductive Harm - www.P65Warnings.ca.gov
It is illegal to use this product in the United States
This product complies with U.S. Safe Drinking Water
WGT. WGT.
W/STRAINER W/OUT STRAINER
6-1/2
6-1/2
7-5/8
7-5/8
9-3/4
7-5/8
105
7-5/8
1363-15/16
9-3/4
F
8124-11/1610-1/447-1/22-5/164-1/8
242912-1/23-3/166-3/4
232913-1/83-3/166-3/4
384712-1/23-1/28-1/82"
374912-1/23-1/28-1/8
708720-1/215-1/810-3/83"
497912-1/23-1/210-3/82"
5512-1/23-1/210-3/8
9224-1/215-1/812-1/23"
At static (no flow) conditions, inlet
EXAMPLE:
pressure of 100 psig and outlet set pressure of 50 psig
(standard), a PRH-3/4" unit will deliver 23 gpm
of water with a 10 psi fall-off (40 psi reduced flow
pressure). If outlet set pressure at static condition is
less than 50 psig, deduct 20% from capacity shown.
NOTES:
D
E (REF.)
1) Repair kits contact factory
(C)
USA
B
A
FRONT
BACK