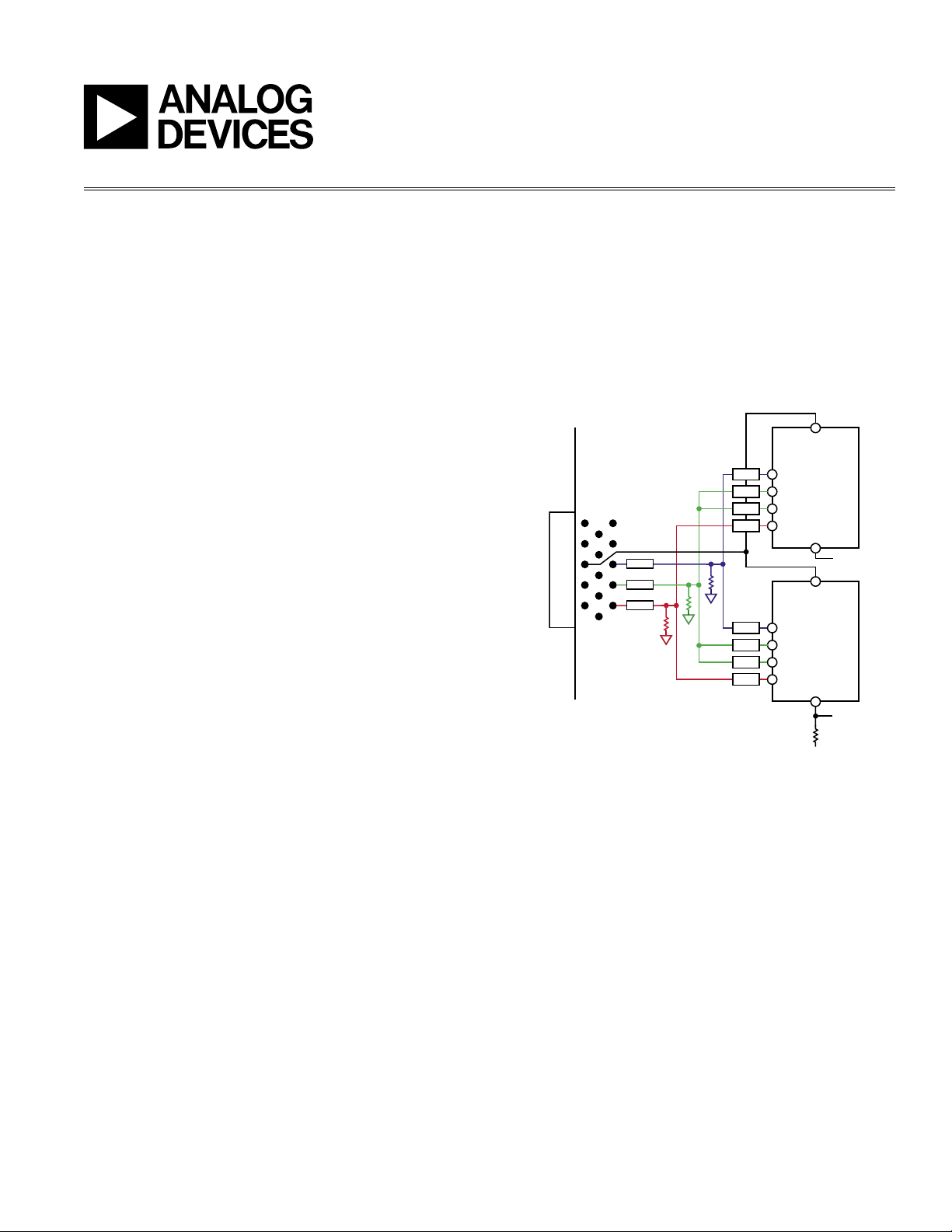
AN-776
HSYNC
BAIN
C
A0
GAIN
C
SOGIN
C
RAIN
C
AD9981
BAIN
C
HSYNC
A0
GAIN
C
SOGIN
C
RAIN
C
AD9981
VDD
VSOUT
VSOUT
10k
L
L
L
APPLICATION NOTE
One Technology Way • P.O. Box 9106 • Norwood, MA 02062-9106 • Tel: 781/329-4700 • Fax: 781/461-3113 • www.analog.com
Dual AD9981 Design Guideline to Achieve UXGA Resolutions
by Del Jones
INTRODUCTION
Pixel clock speeds in excess of 110 MHz can be achieved
with the AD9981 by using a dual chip “ping - pong”
conguration. A dual chip solution is different from an
alternate pixel sampling solution in that full refresh rates
can be maintained.
There are many ways to implement a dual AD 9981
design. This application notes serves to make the user
aware of the considerations that should be weighed
when implementing this conguration. Among the variables are layout and routing constraints, clock selection,
graphics controller requirements, and maximum speed
requirements.
Analog Input Layout and Routing
When laying out and routing the analog inputs (R, G, B,
and HSYNC), several factors should be considered. The
trace lengths of the R, G, and B inputs should be kept
as equal as possible, while also keeping the routes
direct (no zigzagging) to maintain equal propagation
delays. The branches to each of the AD9981’s analog
inputs should be kept as short as possible. The 75
terminators on the RGB inputs should be placed as close
to the branch junctions as possible. Lastly, each R, G,
and B branch requires its own coupling capacitor. These
considerations are illustrated in Figure 1.
Clock Source Selection
There are three methods that can be used for clocking
data. An external clock source can be used to clock
both AD9981s as well as the data latching device(s)
(graphics controller). This method requires external PLL
circuitry and special high speed clock layout and routing
considerations.
A second option is to use the PLL in chip 1 to drive chip 2.
This method would require chip 2 to be congured for
external clock operation, using the negative edge of
chip 1’s DATACK to sample the RGB data. This method
employs the most direct routing of HSYNC. The HSYNC
could be routed directly to chip 1, and then routed to
the second device. (Although the second device does
not use HSYNC to generate a clock, it is still needed
to provide a timing reference for other functions, such
as clamping.) The problem with this option is that it
causes difculty in setting the correct clock phase of
chip 2 because of the added propagation delay between
REV. 0
HSYNC and chip 1’s data clock output. It will also cause
ongoing clock phase difculty in chip 2 because of the
variability of chip 1’s data clock propagation delay over
time and temperature.
Figure 1. Analog Input Routing
The recommended method for clocking is to use the
PLLs in both chips . This method requires special at ten -
tion to HSYNC input layout, as shown in Figure 1. If very
careful attention is paid to keeping the branch lengths
identical (avoiding zigzagging), then the skew between
the two chips’ sampling clock and digital outputs will be
negligible.
Sampling Clock Inversion
All three clocking methods described earlier require
chip 2 to sa mpl e RGB dat a 180 out of ph ase with
chip 1. This can be achieved by using the phase adjustment control. The initial phase setting of chip 2 would
be offset 180 (nominally, 16 steps) from chip 1’s initial
phase setting. Using this method, the data output from
chip 2 will be shif ted by 1/2 pixel clock. This method
allows both chips to run their clocks at half of the
ef fective data rate. Chip 1 would capture odd data on
its sampling edge, while chip 2 captures even data on
its sampling edge (180 out of phase from chip 1).
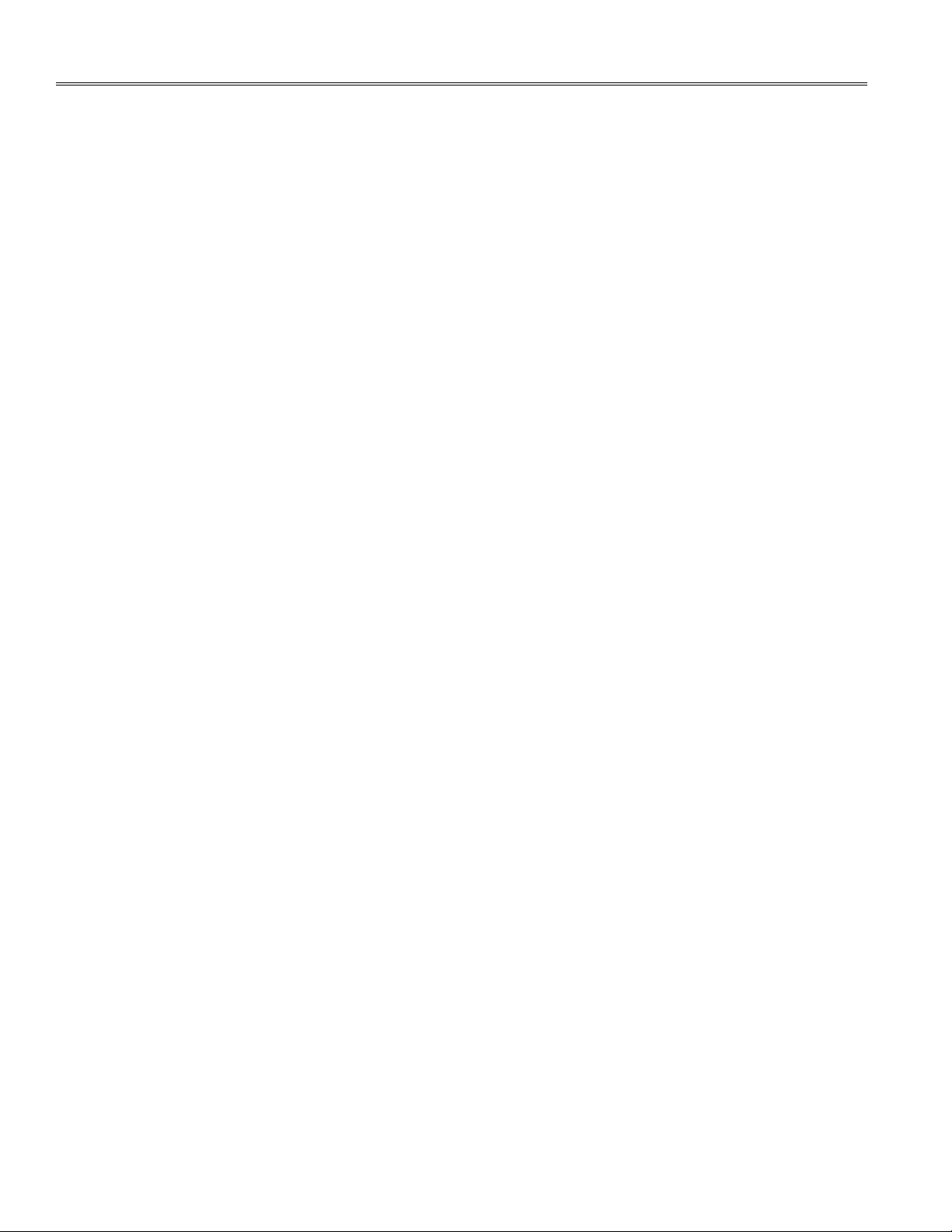
AN-776
The timing issues associated with data capture are
negligible if the capture device has separate capture
clocks for each data port (odd and even data). If only
one clock pin is available on the latching device (graphics
controller, ASIC, and so on) for both ports, it will be necessar y to invert the clock internal to the latching device.
This would be true unless the latching device has the
ability to capture data on either edge of the data clock.
Figure 2 illustrates the basic timing relation between the
incoming data pixels and the digitized output data for
both devices.
Clock Phase Adjustment
Although the internal clock delays should be the same,
each chip’s phase will need to be adjusted separately.
Phase differences between the two chips can come from
layout trace length variations in HSYNC or RGB inputs,
and from normal internal chip variations.
Since each chip is running at half speed, the phase
adjustment step sizes are doubled with respect to the
full speed clock. This results in 1/2 the number of useable
phase adjustment steps (16 instead of 32) since the
phase adjustment range will now cover two full speed
pixels rather than one.
It is recommended that the phase adjustment for the
two devices be performed independently since the
optimal phase setting for each device may not differ by
exactly 16 phase steps (for various reasons). To speed
the phase selection algorithm, a limited phase selection
process could be used on device 2 after the full process
is performed on device 1. If the optimal phase setting
(OPS1) is less than 16 on device 1, then it is reasonable to
expect that the optimal phase setting for device 2 (OPS2)
is OPS1 + 16 4 (wrap around if result is > 31). If OPS1
is ≥ 16 then OPS2 = OPS1 – 16 4 (wrap around if result
is < 0). Therefore, the second step of the phase selection
algorithm (for device 2) can be limited to those steps that
are expected to be the optimal setting.
Interpart Difference Adjustments
Dual ADC applications are sensitive to the differences
bet ween the t wo ADCs. These differences can come
from gain, offset, and linearity.
Gain and Offset
Dual ADC applications are highly sensitive to gain and
offset errors between the two chips. Any dif ference
between odd and even pixels is highly visible. Therefore,
accurate gain and offset adjustment is required for each
chip. Fortunately, the AD9981 has the automatic clamp
feedback feature. When enabled, the clamp feedback
automatically eliminates the channel -to - channel differences in offset for all channels.
While the dif ferences in channel -to - channel gain will
not affect the image as much as differences in of fset,
it is still recommended that any channel-to -channel
gain mismatch be minimized using a one -time factory
calibration scheme.
Linearity/Dithering
Dual ADC applications are also sensitive to differences
in linearity between the two devices. The use of 10 - bit
ADCs greatly improves the linearity performance of
a dual ADC application so that dithering may not be
necessary. However, if the application’s requirements
prove to be stringent, dithering can be used to enhance
the linearity even further. The dithering method requires
that on every other data frame the even and odd device
be swapped. For example, during frame one, device
1 processes odd pixels and device 2 processes even
pixels. During frame two, device 1 processes even pixels
while device 2 processes odd pixels. Dithering allows
the eye to essentially “average” the effect of the linearity
differences as well as differences in offset and gain.
Device Addressing
Each AD9981 requires a different serial bus address.
This is achieved using the A0 / VSOUT pin, shown in
Figure 1.
–2–
REV. 0