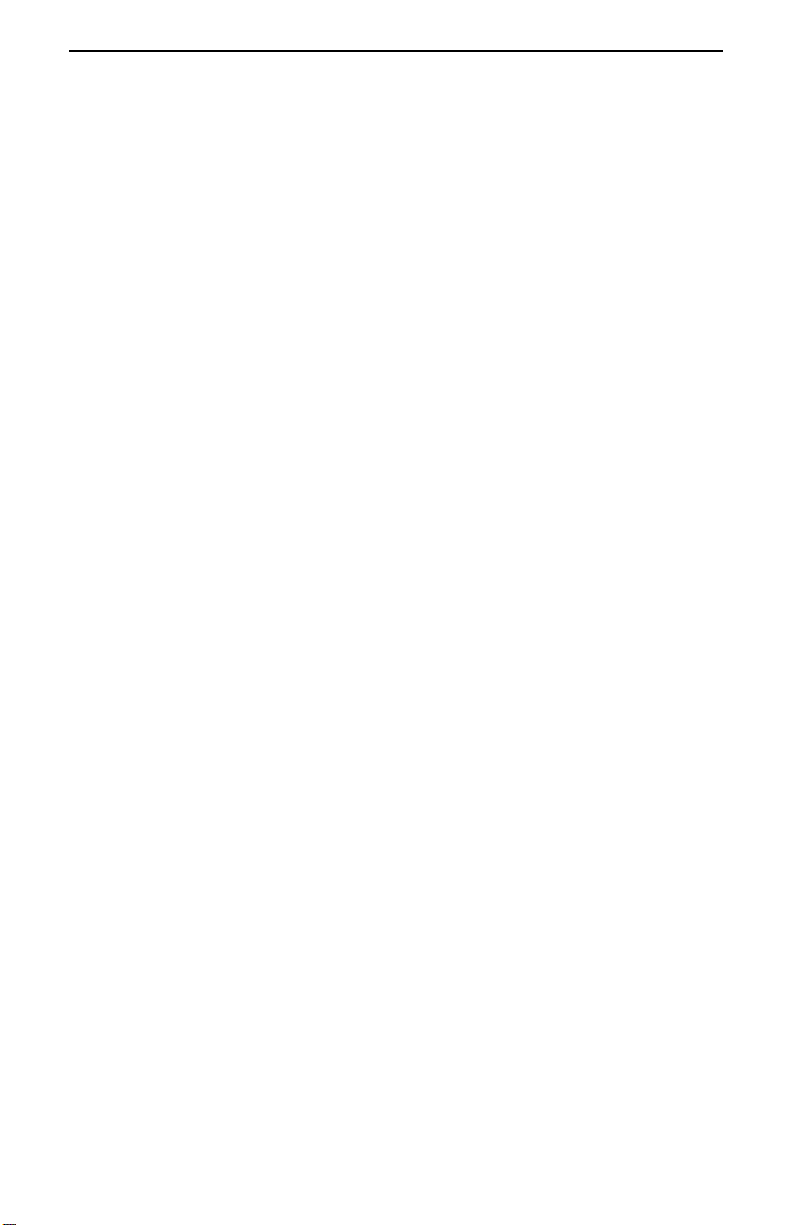
ATP-102 Instruction Manual Tuning Pulser II
Ameritron ATP-102 Tuning Pulser II
The Ameritron ATP-102 Tuning Pulser II relieves temperature related stress on
amplifiers, tuners, and dummy loads while allowing proper system adjustments.
It allows amplifiers to be properly adjusted without the use of long steady
carriers.
The Ameritron ATP-102 Tuning Pulser II allows tuning of an amplifier with full
required drive from the transceiver without over-heating the finals or anything
else in the RF line. It sends a series of pulses to the transceiver allowing the
peak power to be high enough to drive the amplifier to full power, but with the
average power being low enough not to over-heat the final(s).
The Ameritron ATP-102 Tuning Pulser II works with any solid state amateur
transceiver or transmitter, and all other equipment using positive keying line
voltages below 50 volts open circuit and 100 mA closed key current. It can also
be used with negative voltage key lines (commonly found in older tube type
radios) provided keying voltages are below 25 volts dc open circuit.
The Ameritron ATP-102 Tuning Pulser II is a valuable troubleshooting and
diagnostic aid. The Ameritron ATP-102 Tuning Pulser II can be used in
performance tests of QSK systems, wattmeters, and other equipment.
The Ameritron ATP-102 Tuning Pulser II uses a single 9-volt battery for power,
with battery life dependent on operating and storage time. To install the battery
remove the cover by removing the two screws (one on each side) that secure it.
A battery clip and holder, located on the left side of the enclosure, are provided
for installing the 9-volt battery.
Technical Description
The Ameritron ATP-102 Tuning Pulser II uses a 555 timer driving an FET open
drain switch. Two front panel controls allow independent adjustment of both
pulse repetition rate (PULSE RATE) and on-to-off time duty cycle (DUTY
CYCLE).
PULSE RATE is adjustable from about 17 to 40 pulses per second, while DUTY
CYCLE is adjustable from about 10 to 90 percent. The keying time intervals are
typically adjustable from 2- 40 mS "on" time, and a 24 to 60 mS pulse repetition
time interval.
Minimum duty cycle and the slowest PULSE RATE occur at the full
counterclockwise settings of both front panel controls.
1
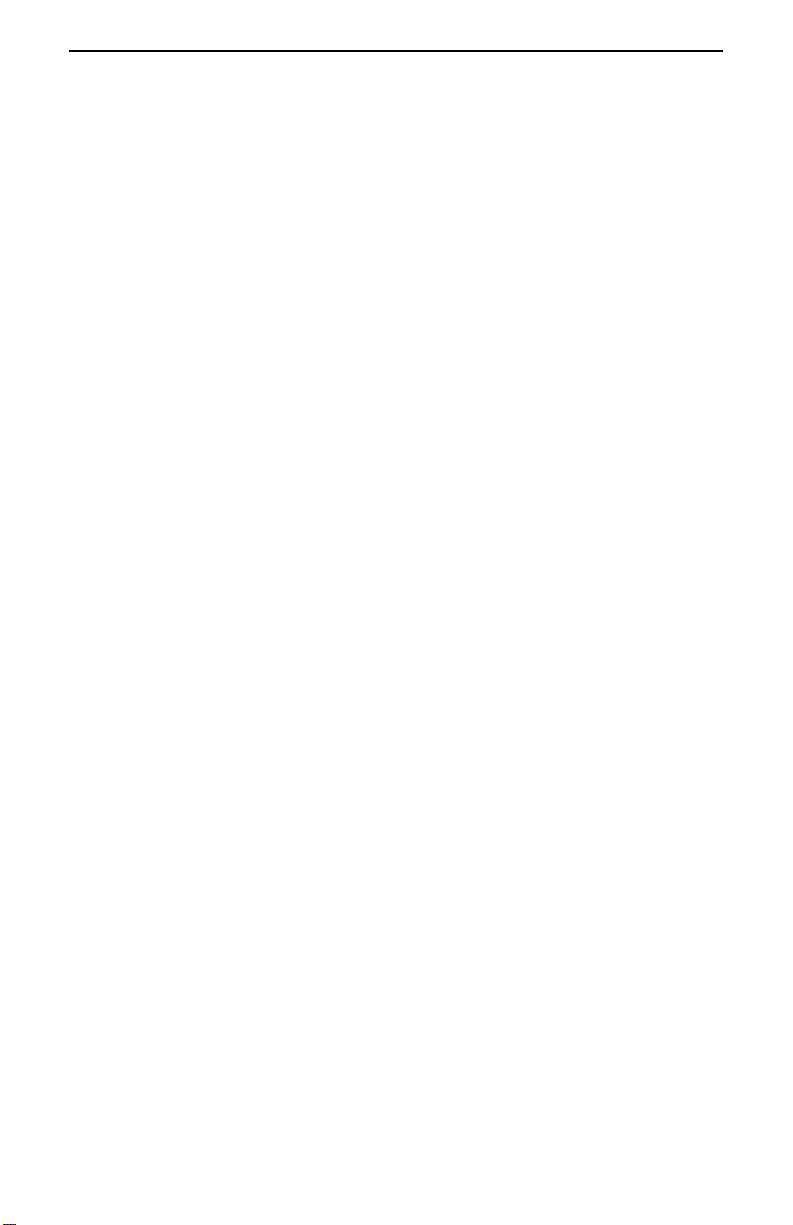
ATP-102 Instruction Manual Tuning Pulser II
The CARRIER button is a momentary contact switch that temporarily locks the
transmitter in a continuous carrier transmit mode.
The PULSE button is a latching switch that activates the pulse circuit when
pressed in and locked.
Speech Duty Cycle
The duty cycle of average power to peak envelope power varies widely in the
real world. Every voice and system varies, no universal duty cycle of peak to
average power applies to the many real-world combinations of voices and
equipment.
Unprocessed speech usually has an average power between one percent and ten
percent of peak envelope power. Sustained speech, such as a long "hello",
produces average power levels that typically range from 10 to 30% of PEP.
Heavy speech processing increases the average power, pushing the short term
average power of normal speech to 30% or more.
During normal voice operation, most equipment heat is generated by the
quiescent current required to make the transmitting system linear. Proper
amplifier or transmitter tuning require adjustments at maximum peak power,
generally with maximum available drive from the exciter. A continuous tone or
carrier is generally used during adjustment, and the amplifier is generally tuned
for maximum output.
The continuous single tone carrier, commonly used to adjust the PA or tuner,
will raise heat significantly. The Ameritron ATP-102 Tuning Pulser II allows
proper tuning while driving the PA with a low duty cycle waveform. It is NOT
necessary to use a peak reading meter when adjusting an amplifier or tuner with
the Ameritron ATP-102 Tuning Pulser II, although the lack of a true peak
reading meter will prevent you from knowing the amount of peak power
produced.
2
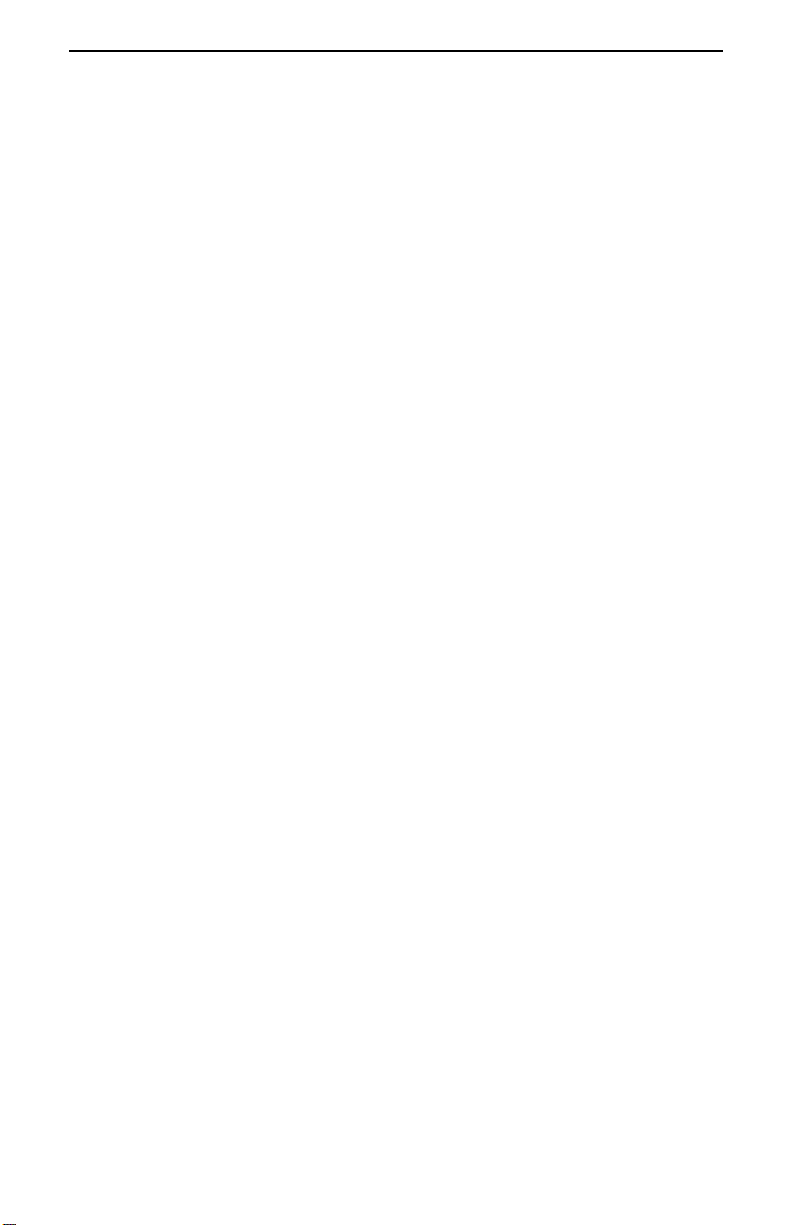
ATP-102 Instruction Manual Tuning Pulser II
PULSE RATE and DUTY CYCLE
The Ameritron ATP-102 has two front panel controls labeled Pulse rate and
duty cycle. As indicated by the names, these controls adjust the rate at which the
transmit keying pulses occur (pulse rate), and the ratio of on- to-off time (duty
cycle).
Some care must be used to insure PULSE RATE is slow enough, and the DUTY
CYCLE is long enough, to be within the keying response limits of the exciter
and meter. If the pulse rate is too fast and/or the duty cycle is too long, the
pulses will blur into one long steady signal.
The typical exciter has a leading edge rise time and tailing edge decay time of a
few milliseconds. This stretches the pulse duty cycle out, making the actual RF
envelope have a longer duty cycle than the actual keying waveform from the
Ameritron ATP-102 . Because of this effect, the Ameritron ATP-102 Tuning
Pulser II may actually produce a 100% duty cycle waveform at high (clockwise)
PULSE RATES with longer (clockwise) on-time DUTY CYCLE settings.
If the pulse rate is too slow and/or the duty cycle too slow, peak power will not
be reached. All exciters have a delayed response to the leading edge of the
keying waveform. This delay may prevent full peak power from being reached if
the duty cycle is too short. Most peak meters have limited response time, this
causes lower power readings with short duty cycle pulses.
Another problem is nearly all meters have limited storage time, causing the
meter to "fall-back" during the time interval between RF pulses. To obtain the
most accurate meter readings, both PULSE RATE and DUTY CYCLE should
be set far enough clockwise to allow maximum peak power to be indicated on a
scope or peak reading meter.
Some peak meters do not read true peak power at all, instead reading something
less than the true peak power. If your meter reads less power when the pulser is
used, compared to the power when a steady or near steady carrier is produced,
your meter is probably not a good peak reading meter. Nearly every radio and
amplifier produces more peak power than steady carrier power, because of ALC
response time and power supply voltage sag under load. Too much duty cycle
on-time can cause unwanted component heating.
3