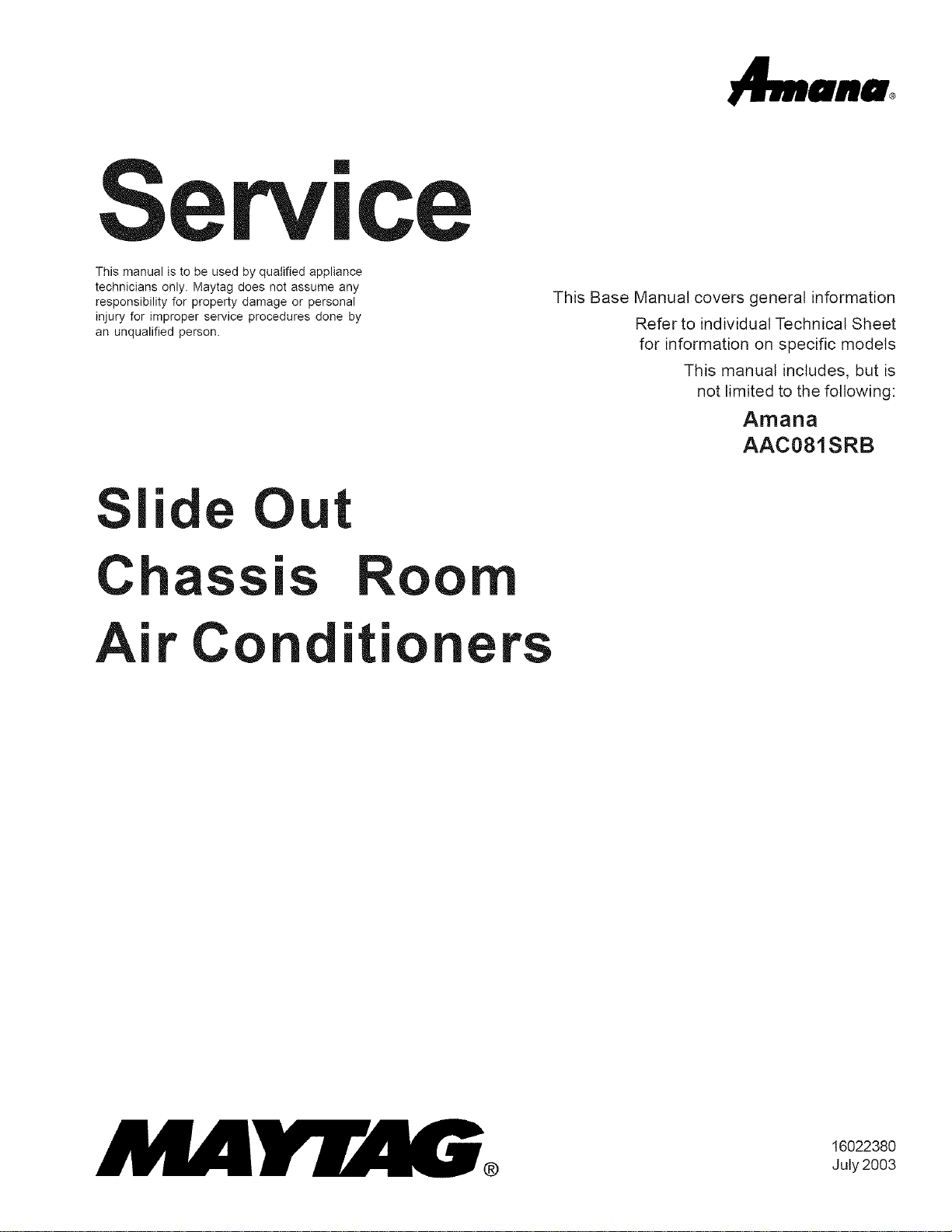
Servi
This manual is to be used by qualified appliance
technicians only. Maytag does not assume any
responsibility for property damage or personal
injury for improper service procedures done by
an unqualified person.
Sli e
This Base Manual covers general information
Refer to individual Technical Sheet
for information on specific models
This manual includes, but is
not limited to the following:
Amana
AAC081SRB
Chassis
Air C
RO
i io
e
16022380
July 2003
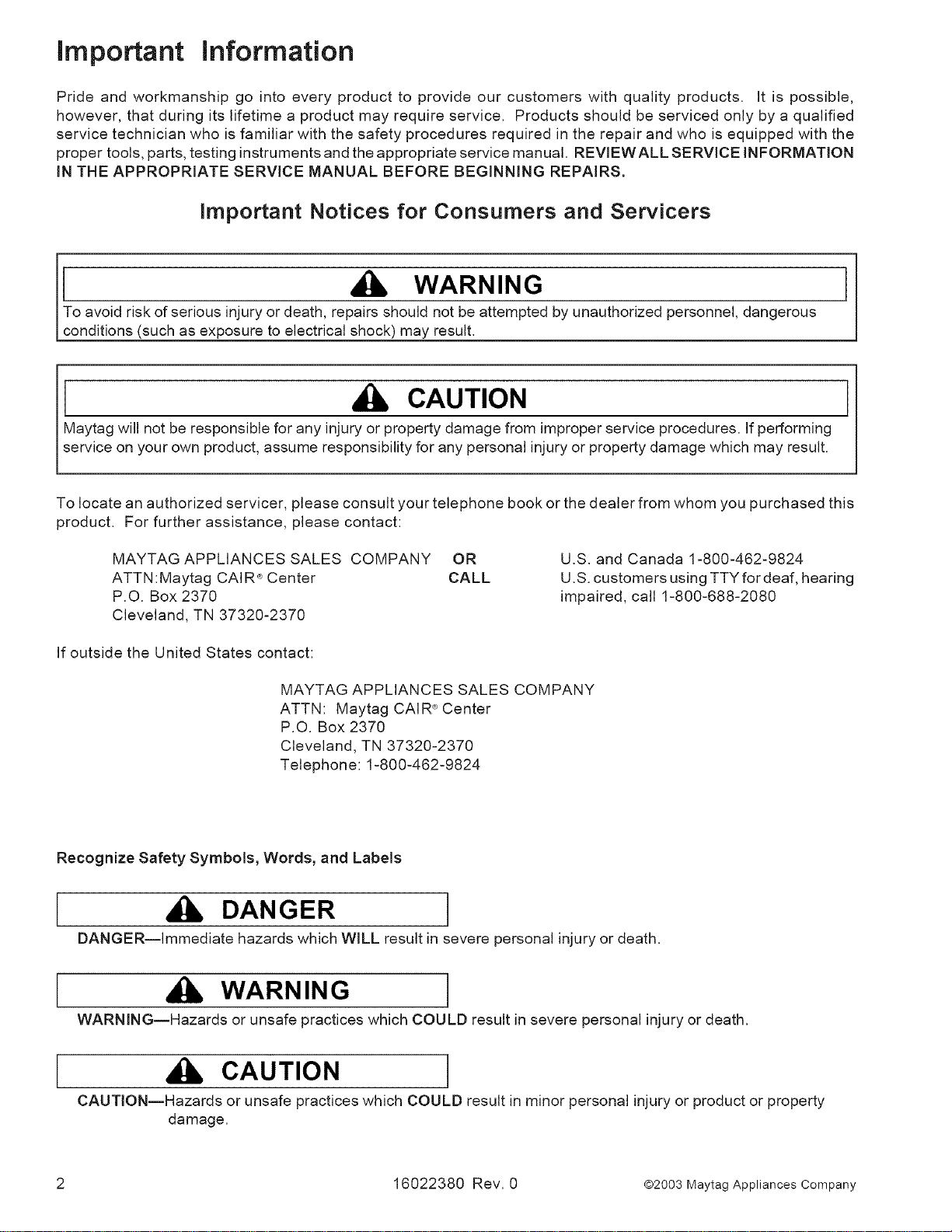
important information
Pride and workmanship go into every product to provide our customers with quality products. It is possible,
however, that during its lifetime a product may require service. Products should be serviced only by a qualified
service technician who is familiar with the safety procedures required in the repair and who is equipped with the
proper tools, parts, testing instruments and the appropriate service manual. REVlEWALL SERVICE INFORMATION
IN THE APPROPRIATE SERVICE MANUAL BEFORE BEGINNING REPAIRS.
important Notices for Consumers and Servicers
WARNING
To avoid risk of serious injury or death, repairs should not be attempted by unauthorized personnel, dangerous
conditions (such as exposure to electrical shock) may result.
[ CAUTION
Maytag will not be responsible for any injury or property damage from improper service procedures. If performing
serv ce on your own product, assume respons b ty for any persona njury or property damage wh ch may resu t.
To locate an authorized servicer, please consult your telephone book or the dealer from whom you purchased this
product. For further assistance, please contact:
MAYTAG APPLIANCES SALES COMPANY
ATTN:Maytag CAIR ®Center
P.O. Box 2370
Cleveland, TN 37320-2370
If outside the United States contact:
MAYTAG APPLIANCES SALES COMPANY
ATTN: Maytag CAIR ®Center
P.O. Box 2370
Cleveland, TN 37320-2370
Telephone: 1-800-462-9824
Recognize Safety Symbols, Words, and Labels
OR
CALL
U.S. and Canada 1-800-462-9824
U.S. customers using TTY for deaf, hearing
impaired, call 1-800-688-2080
DANGER
DANGER--Immediate hazards which WILL result in severe personal injury or death.
WARNING
WARNING--Hazards or unsafe practices which COULD result in severe personal injury or death.
CAUTION
CAUTION--Hazards or unsafe practices which COULD result in minor personal injury or product or property
damage.
2 16022380 Rev. 0 @2003 MaytagAppliancesCompany
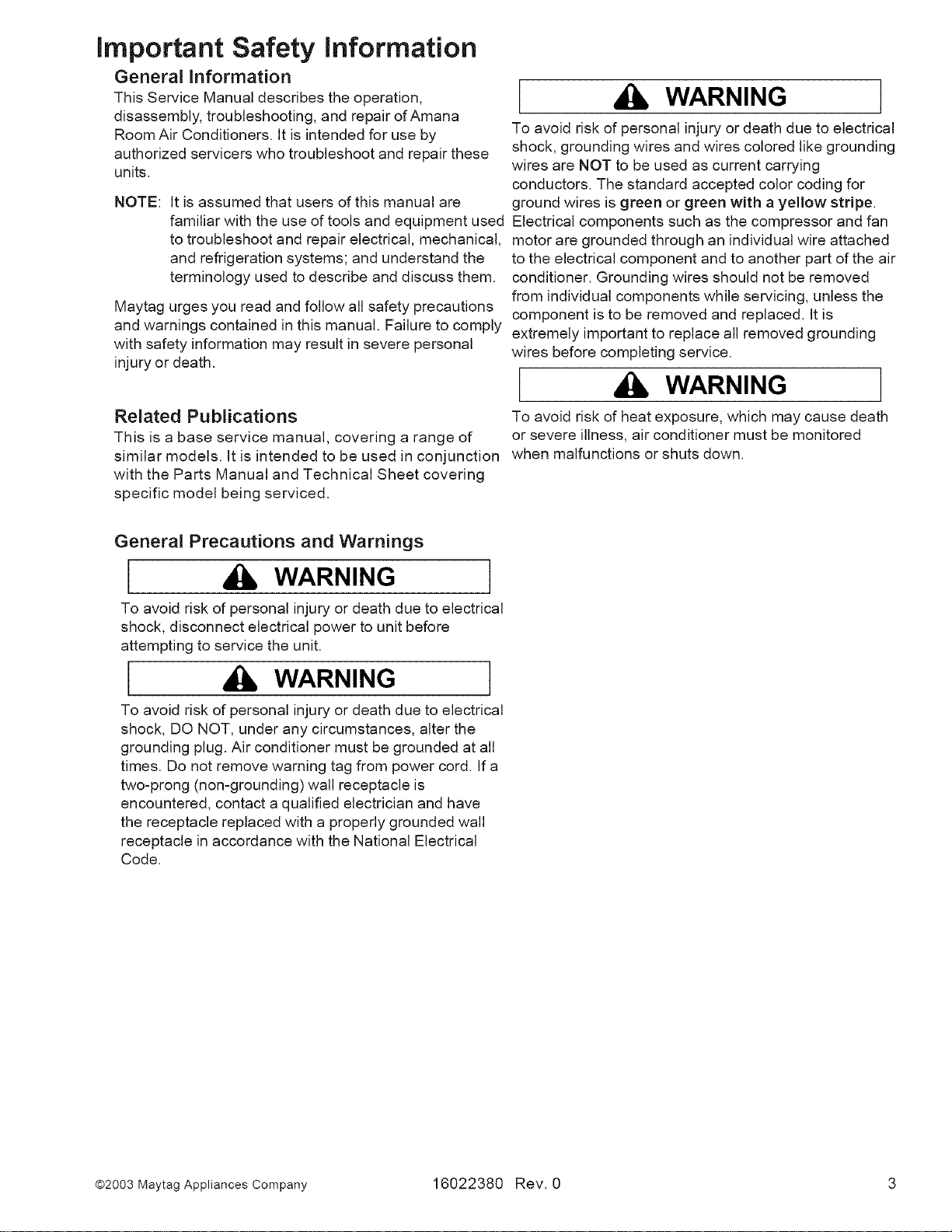
important Safety information
General information
This Service Manual describes the operation,
disassembly, troubleshooting, and repair of Amana
Room Air Conditioners. It is intended for use by
authorized servicers who troubleshoot and repair these
units.
NOTE: It is assumed that users of this manual are
familiar with the use of tools and equipment used
to troubleshoot and repair electrical, mechanical,
and refrigeration systems; and understand the
terminology used to describe and discuss them,
Maytag urges you read and follow all safety precautions
and warnings contained in this manual. Failure to comply
with safety information may result in severe personal
injury or death.
Related Publications
This is a base service manual, covering a range of
similar models. It is intended to be used in conjunction when malfunctions or shuts down.
with the Parts Manual and Technical Sheet covering
specific model being serviced.
[ WARNING J
To avoid risk of personal injury or death due to electrical
shock, grounding wires and wires colored like grounding
wires are NOT to be used as current carrying
conductors. The standard accepted color coding for
ground wires is green or green with a yellow stripe.
Electrical components such as the compressor and fan
motor are grounded through an individual wire attached
to the electrical component and to another part of the air
conditioner, Grounding wires should not be removed
from individual components while servicing, unless the
component is to be removed and replaced, It is
extremely important to replace all removed grounding
wires before completing service,
[ WARNING J
To avoid risk of heat exposure, which may cause death
or severe illness, air conditioner must be monitored
General Precautions and Warnings
WARNING ]
To avoid risk of personal injury or death due to electrical
shock, disconnect electrical power to unit before
attempting to service the unit,
WARNING ]
To avoid risk of personal injury or death due to electrical
shock, DO NOT, under any circumstances, alter the
grounding plug, Air conditioner must be grounded at all
times, Do not remove warning tag from power cord, If a
two-prong (non-grounding) wall receptacle is
encountered, contact a qualified electrician and have
the receptacle replaced with a properly grounded wall
receptacle in accordance with the National Electrical
Code,
@2003 Maytag Appliances Company 16022380 Rev. 0 3
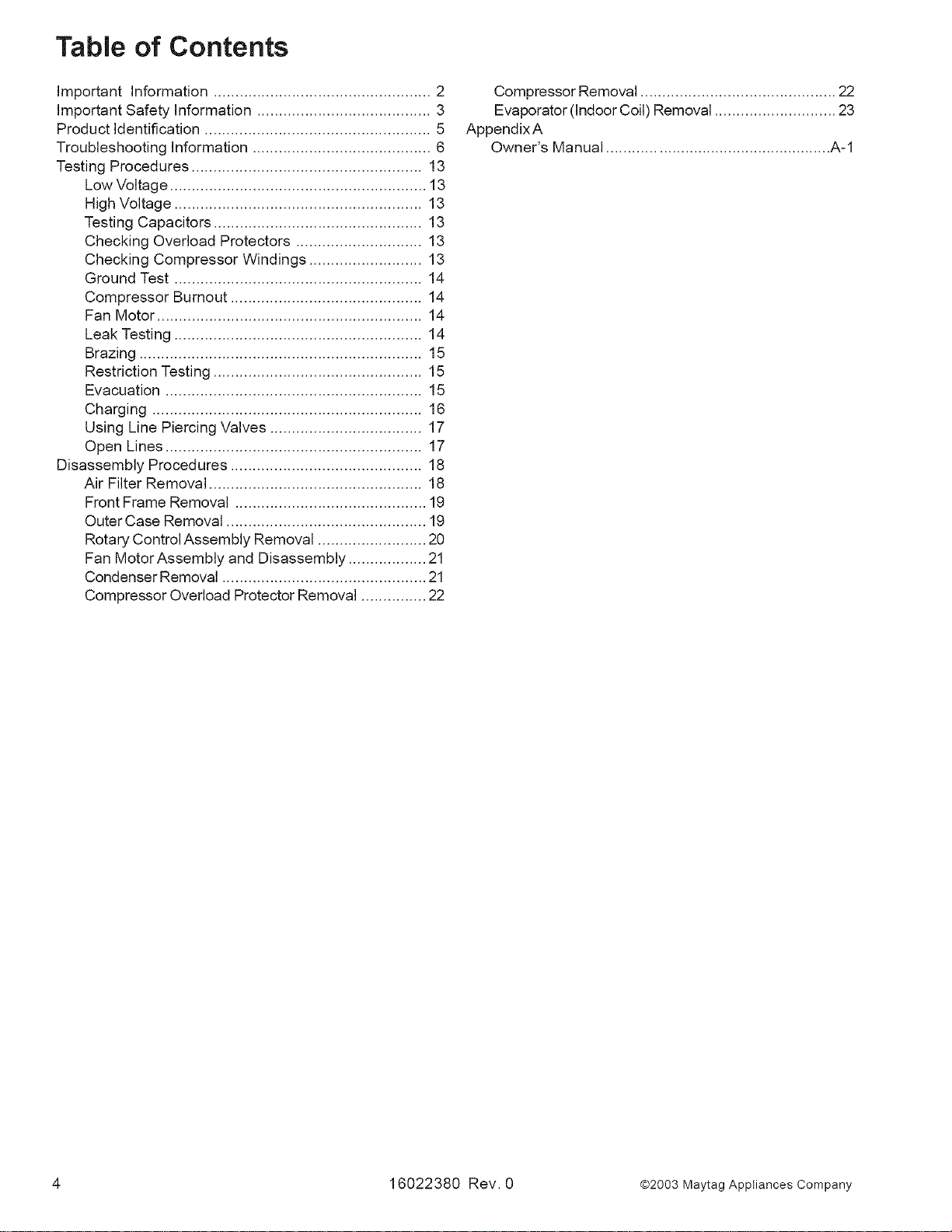
Table of Contents
Important Information .................................................. 2
Important Safety Information ........................................ 3
Product Identification .................................................... 5
Troubleshooting Information ......................................... 6
Testing Procedures ..................................................... 13
Low Voltage ........................................................... 13
High Voltage ......................................................... 13
Testing Capacitors ................................................ 13
Checking Overload Protectors ............................. 13
Checking Compressor Windings .......................... 13
Ground Test ......................................................... 14
Compressor Burnout ............................................ 14
Fan Motor ............................................................. 14
Leak Testing ......................................................... 14
Brazing ................................................................. 15
Restriction Testing ................................................ 15
Evacuation ........................................................... 15
Charging .............................................................. 16
Using Line Piercing Valves ................................... 17
Open Lines ........................................................... 17
Disassembly Procedures ............................................ 18
Air Filter Removal ................................................. 18
Front Frame Removal ............................................ 19
Outer Case Removal .............................................. 19
Rotary Control Assembly Removal ......................... 20
Fan MotorAssembly and Disassembly .................. 21
Condenser Removal ............................................... 21
Compressor Overload Protector Removal ............... 22
Compressor Removal ............................................. 22
Evaporator (Indoor Coil) Removal ............................ 23
AppendixA
Owner's Manual .................................................... A-1
4 16022380 Rev. 0 @2003 Maytag Appliances Company
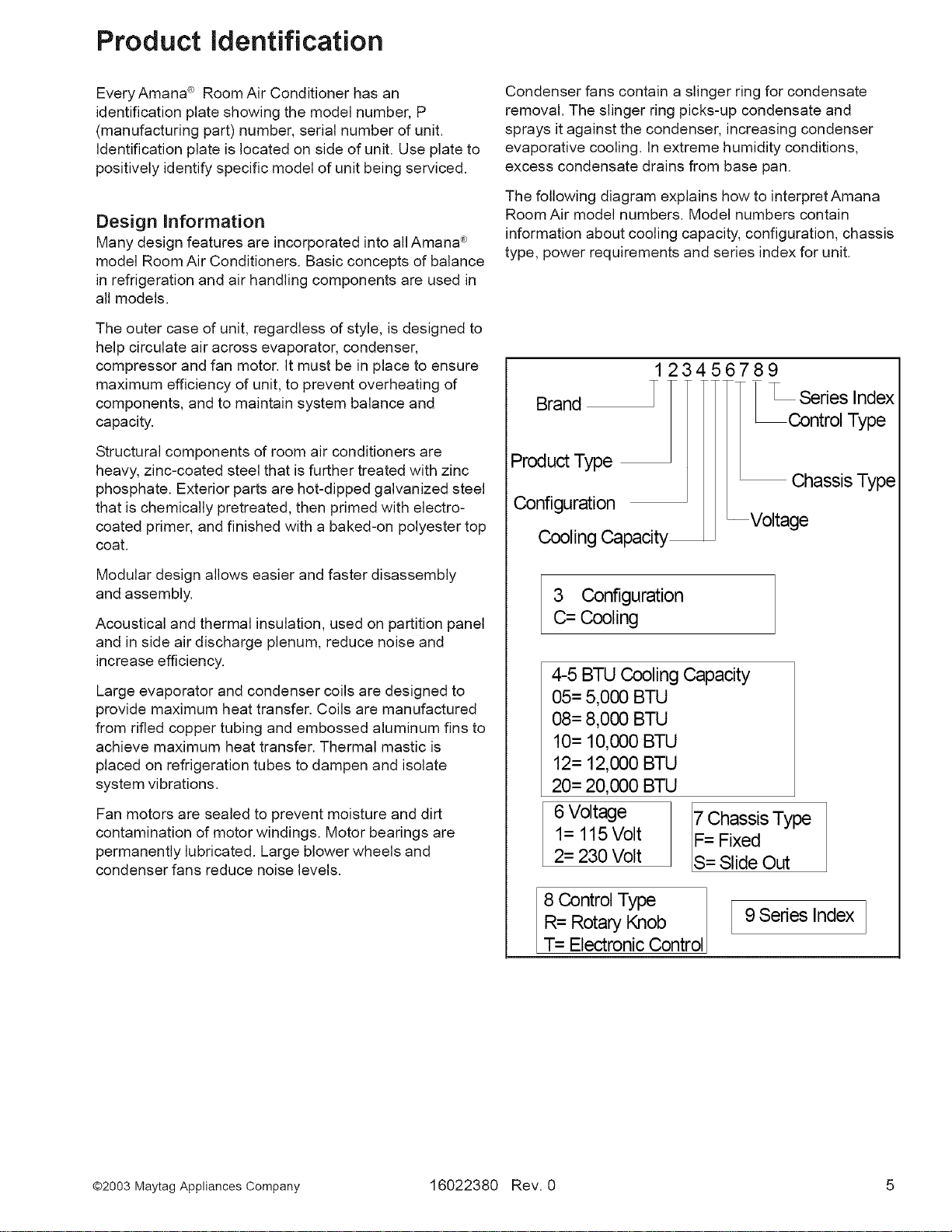
Product identification
EveryAmana ® Room Air Conditioner has an
identification plate showing the model number, P
(manufacturing part) number, serial number of unit.
Identification plate is located on side of unit. Use plate to
positively identify specific model of unit being serviced.
Design Information
Many design features are incorporated into all Amana ®
model Room Air Conditioners. Basic concepts of balance
in refrigeration and air handling components are used in
all models.
The outer case of unit, regardless of style, is designed to
help circulate air across evaporator, condenser,
compressor and fan motor. It must be in place to ensure
maximum efficiency of unit, to prevent overheating of
components, and to maintain system balance and
capacity.
Structural components of room air conditioners are
heavy, zinc-coated steel that is further treated with zinc
phosphate. Exterior parts are hot-dipped galvanized steel
that is chemically pretreated, then primed with electro-
coated primer, and finished with a baked-on polyester top
coat.
Condenser fans contain a slinger ring for condensate
removal. The slinger ring picks-up condensate and
sprays it against the condenser, increasing condenser
evaporative cooling. In extreme humidity conditions,
excess condensate drains from base pan.
The following diagram explains how to interpret Amana
Room Air model numbers. Model numbers contain
information about cooling capacity, configuration, chassis
type, power requirements and series index for unit.
123456789
Brand
_Controt Type
-_ Series Index
Product Type
Chassis Type
Configuration
--Voltage
Cooling Capacity
Modular design allows easier and faster disassembly
and assembly.
Acoustical and thermal insulation, used on partition panel
and in side air discharge plenum, reduce noise and
increase efficiency.
Large evaporator and condenser coils are designed to
provide maximum heat transfer. Coils are manufactured
from rifled copper tubing and embossed aluminum fins to
achieve maximum heat transfer. Thermal mastic is
placed on refrigeration tubes to dampen and isolate
system vibrations.
Fan motors are sealed to prevent moisture and dirt
contamination of motor windings. Motor bearings are
permanently lubricated. Large blower wheels and
condenser fans reduce noise levels.
3 Configuration
C= Cooling
4-5 BTU cooling Capacity
05= 5,000 BTU
08= 8,000 BTU
10= 10,000 BTU
12= 12,000 BTU
20= 20,000 BTU
6 Voltage
1= 115 Volt
2= 230 Volt
8 Control Type
R= Rotary Knob
T= Electronic control
7 Chassis Type
F= Fixed
S= Slide Out
9 Series Index
@2003 MaytagAppliancesCompany 16022380 Rev. 0 5
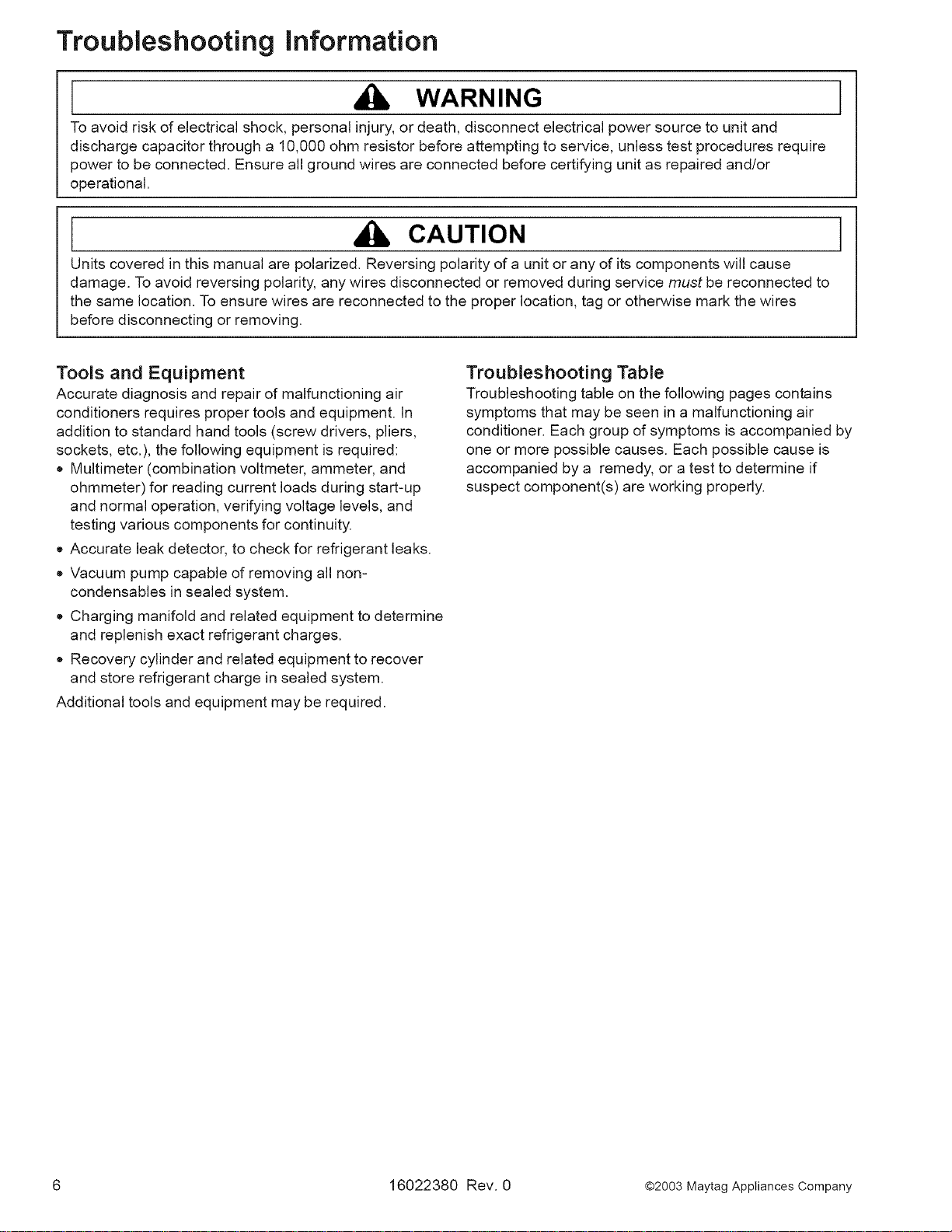
Troubleshooting information
WARNING
To avoid risk of electrical shock, personal injury, or death, disconnect electrical power source to unit and
discharge capacitor through a 10,000 ohm resistor before attempting to service, unless test procedures require
power to be connected. Ensure all ground wires are connected before certifying unit as repaired and/or
operational.
CAUTION
Units covered in this manual are polarized. Reversing polarity of a unit or any of its components will cause
damage. To avoid reversing polarity, any wires disconnected or removed during service must be reconnected to
the same location. To ensure wires are reconnected to the proper location, tag or otherwise mark the wires
before disconnecting or removing.
Tools and Equipment
Accurate diagnosis and repair of malfunctioning air
conditioners requires proper tools and equipment. In
addition to standard hand tools (screw drivers, pliers,
sockets, etc.), the following equipment is required:
, Multimeter (combination voltmeter, ammeter, and
ohmmeter) for reading current loads during start-up
and normal operation, verifying voltage levels, and
testing various components for continuity.
• Accurate leak detector, to check for refrigerant leaks.
• Vacuum pump capable of removing all non-
condensables in sealed system.
• Charging manifold and related equipment to determine
and replenish exact refrigerant charges.
, Recovery cylinder and related equipment to recover
and store refrigerant charge in sealed system.
Additional tools and equipment may be required.
Troubleshooting Table
Troubleshooting table on the following pages contains
symptoms that may be seen in a malfunctioning air
conditioner. Each group of symptoms is accompanied by
one or more possible causes. Each possible cause is
accompanied by a remedy, or a test to determine if
suspect component(s) are working properly.
6 16022380 Rev. 0 @2003 MaytagAppliancesCompany
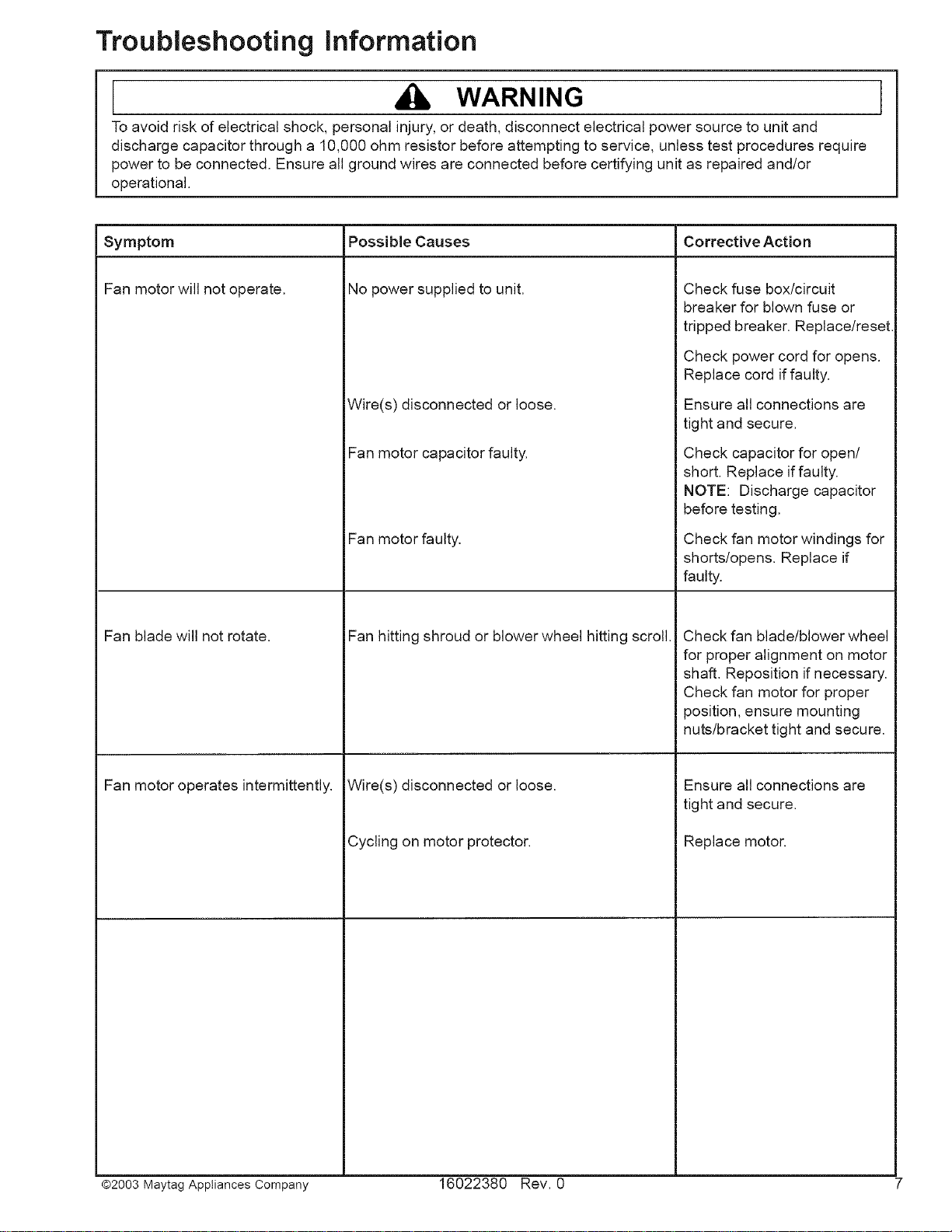
Troubleshooting information
WARNING
To avoid risk of electrical shock, personal injury, or death, disconnect electrical power source to unit and
discharge capacitor through a 10,000 ohm resistor before attempting to service, unless test procedures require
power to be connected. Ensure all ground wires are connected before certifying unit as repaired and/or
operational.
Symptom
Fan motor will not operate.
Fan blade will not rotate.
Possible Causes
No power supplied to unit.
Wire(s) disconnected or loose.
Fan motor capacitor faulty.
Fan motor faulty. Check fan motor windings for
Fan hitting shroud or blower wheel hitting scroll.
Corrective Action
Check fuse box/circuit
breaker for blown fuse or
tripped breaker. Replace/reset,
Check power cord for opens.
Replace cord if faulty.
Ensure all connections are
tight and secure.
Check capacitor for open/
short. Replace if faulty.
NOTE: Discharge capacitor
before testing.
shorts/opens. Replace if
faulty.
Check fan blade/blower wheel
for proper alignment on motor
shaft. Reposition if necessary.
Check fan motor for proper
position, ensure mounting
nuts/bracket tight and secure.
Fan motor operates intermittently. Wire(s) disconnected or loose.
Cycling on motor protector.
@2003 Maytag Appliances Company 16022380 Rev. 0 7
Ensure all connections are
tight and secure.
Replace motor.
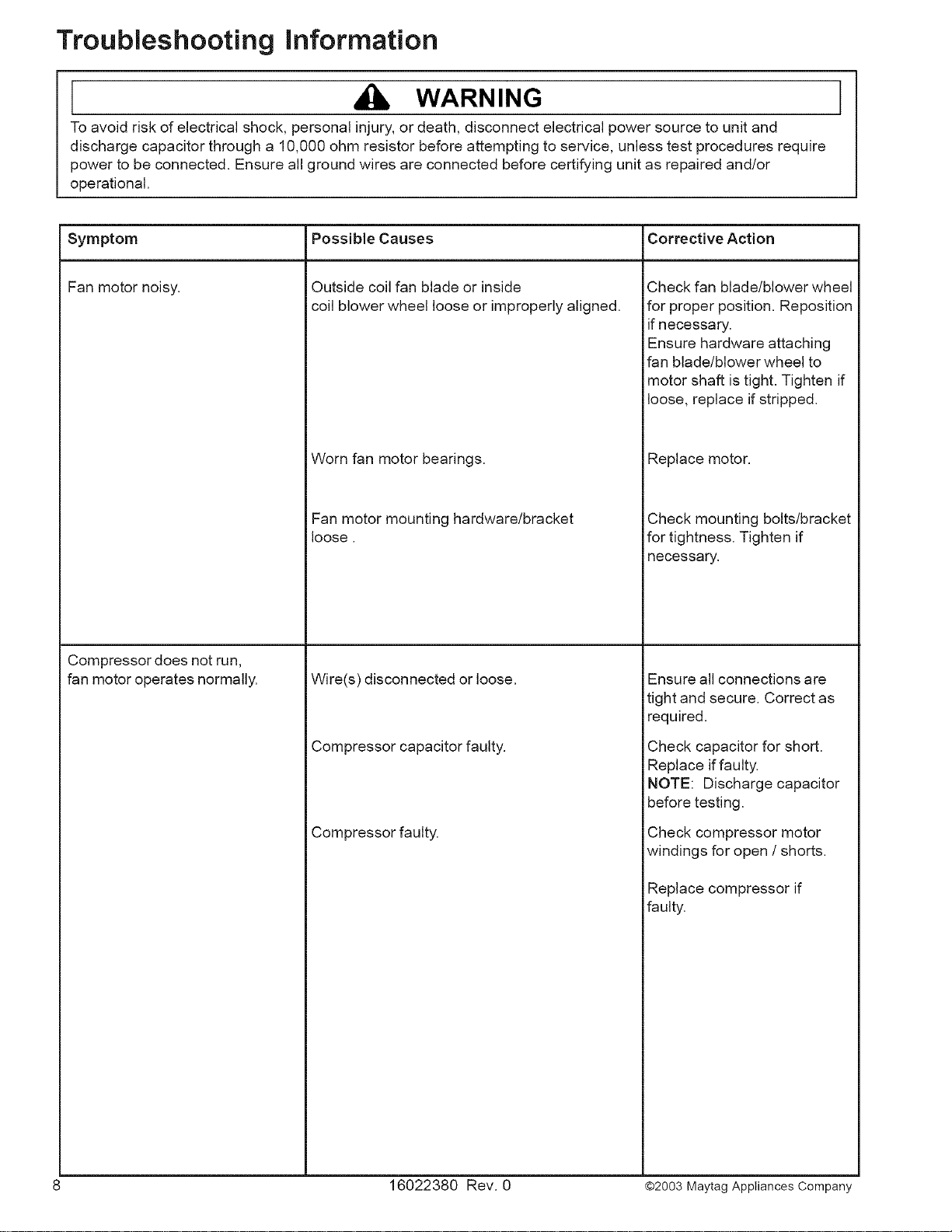
Troubleshooting information
WARNING
To avoid risk of electrical shock, personal injury, or death, disconnect electrical power source to unit and
discharge capacitor through a 10,000 ohm resistor before attempting to service, unless test procedures require
power to be connected. Ensure all ground wires are connected before certifying unit as repaired and/or
operational.
Symptom
Fan motor noisy.
Compressor does not run,
fan motor operates normally.
Possible Causes
Outside coil fan blade or inside
coil blower wheel loose or improperly aligned.
Worn fan motor bearings.
Fan motor mounting hardware/bracket
loose.
Wire(s) disconnected or loose.
Corrective Action
Check fan blade/blower wheel
for proper position. Reposition
if necessary.
Ensure hardware attaching
fan blade/blower wheel to
motor shaft is tight. Tighten if
loose, replace if stripped.
Replace motor.
Check mounting bolts/bracket
for tightness. Tighten if
necessary.
Ensure all connections are
tight and secure. Correct as
required.
Compressor capacitor faulty.
Compressor faulty.
8 16022380 Rev. 0 @2003 MaytagAppliancesCompany
Check capacitor for short.
Replace if faulty.
NOTE: Discharge capacitor
before testing,
Check compressor motor
windings for open / shorts.
Replace compressor if
faulty.
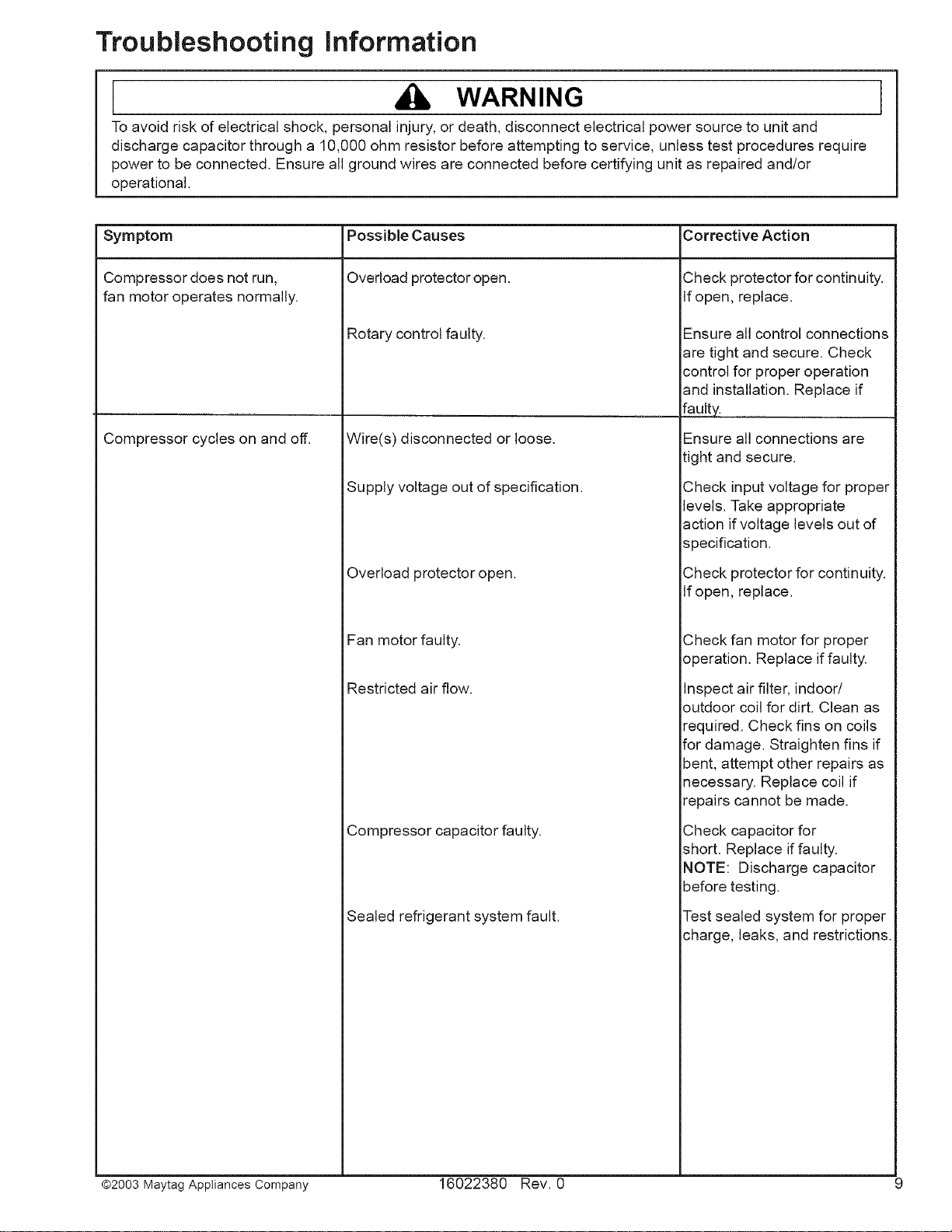
Troubleshooting information
WARNING
To avoid risk of electrical shock, personal injury, or death, disconnect electrical power source to unit and
discharge capacitor through a 10,000 ohm resistor before attempting to service, unless test procedures require
power to be connected. Ensure all ground wires are connected before certifying unit as repaired and/or
operational.
Symptom
Compressor does not run,
fan motor operates normally.
Compressor cycles on and off.
Overload protector open.
Rotary control faulty.
Wire(s) disconnected or loose.
Supply voltage out of specification.
Overload protector open.
Fan motor faulty.
Corrective ActionPossible Causes
Check protector for continuity.
If open, replace.
Ensure all control connections
are tight and secure. Check
control for proper operation
and installation. Replace if
faulty. ...
Ensure all connections are
tight and secure.
Check input voltage for proper
levels. Take appropriate
action if voltage levels out of
specification.
Check protector for continuity.
If open, replace.
Check fan motor for proper
operation. Replace iffaulty.
Restricted air flow.
Compressor capacitor faulty.
Sealed refrigerant system fault.
Inspect air filter, indoor/
outdoor coil for dirt. Clean as
required. Check fins on coils
for damage. Straighten fins if
bent, attempt other repairs as
necessary. Replace coil if
repairs cannot be made.
Check capacitor for
short. Replace iffaulty.
NOTE: Discharge capacitor
before testing.
Test sealed system for proper
charge, leaks, and restrictions.
@2003 Maytag Appliances Company 16022380 Rev. 0 9
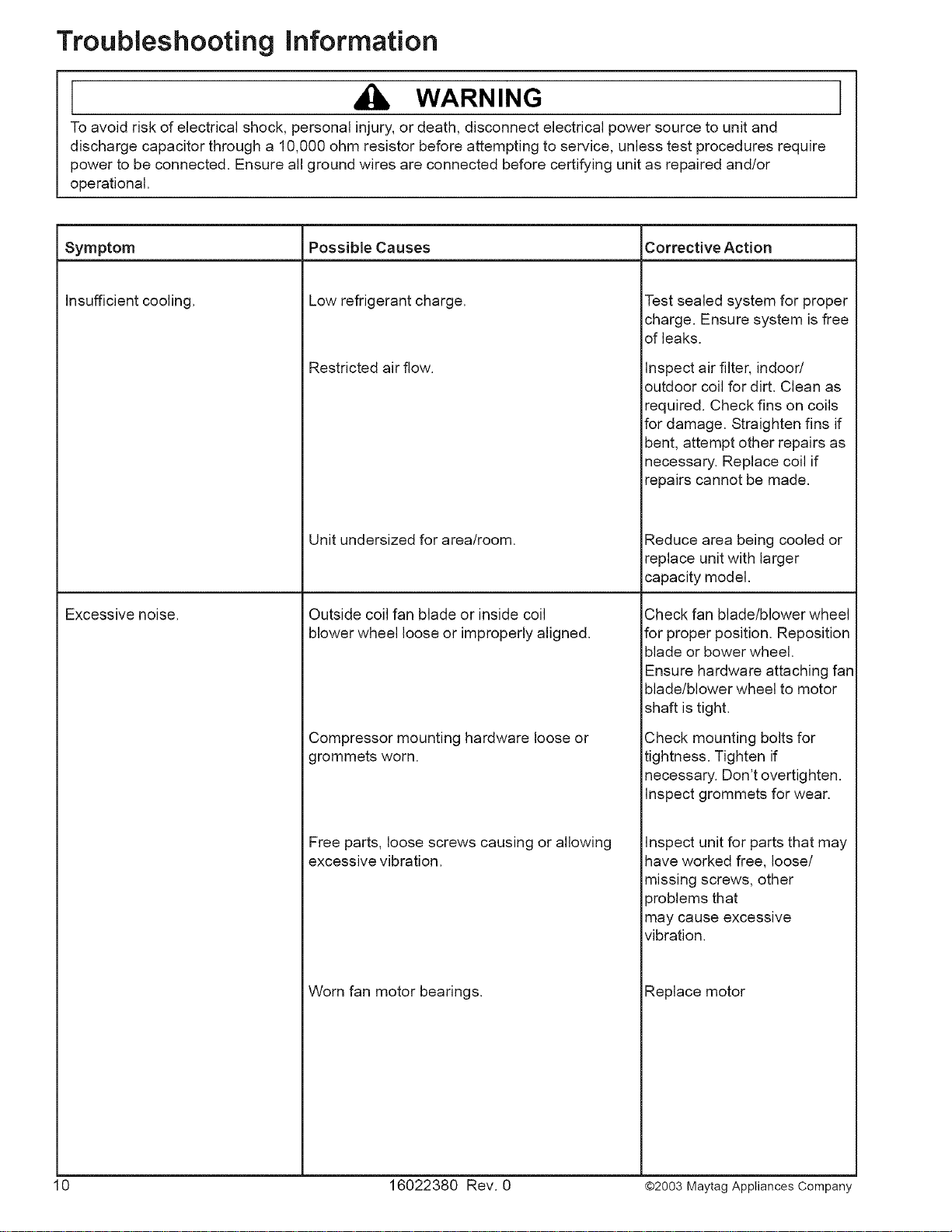
Troubleshooting information
WARNING
To avoid risk of electrical shock, personal injury, or death, disconnect electrical power source to unit and
discharge capacitor through a 10,000 ohm resistor before attempting to service, unless test procedures require
power to be connected. Ensure all ground wires are connected before certifying unit as repaired and/or
operational.
Symptom
Insufficient cooling.
Excessive noise.
Possible Causes Corrective Action
Low refrigerant charge.
Restricted air flow.
Unit undersized for area/room.
Outside coil fan blade or inside coil
blower wheel loose or improperly aligned.
Test sealed system for proper
charge. Ensure system is free
of leaks.
Inspect air filter, indoor/
outdoor coil for dirt. Clean as
required. Check fins on coils
for damage. Straighten fins if
bent, attempt other repairs as
necessary. Replace coil if
repairs cannot be made.
Reduce area being cooled or
replace unit with larger
capacity model.
Check fan blade/blower wheel
for proper position. Reposition
blade or bower wheel.
Ensure hardware attaching fan
blade/blower wheel to motor
shaft is tight.
Compressor mounting hardware loose or
grommets worn.
Free parts, loose screws causing or allowing
excessive vibration.
Worn fan motor bearings.
10 16022380 Rev. 0 @2003 MaytagAppliancesCompany
Check mounting bolts for
tightness. Tighten if
necessary. Don't overtighten.
Inspect grommets for wear.
Inspect unit for parts that may
have worked free, loose/
missing screws, other
)roblems that
may cause excessive
vibration.
Replace motor
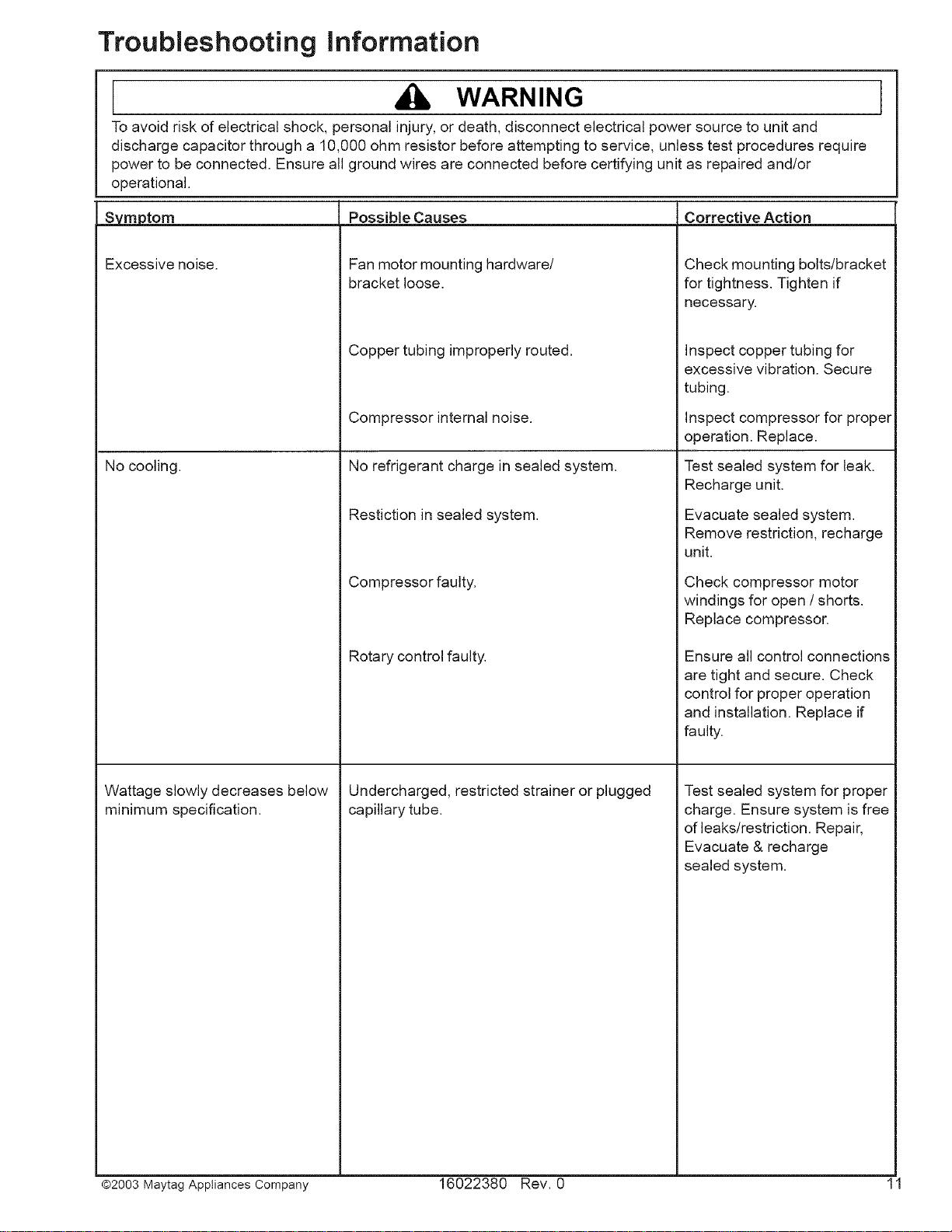
Troubleshooting information
WARNING
To avoid risk of electrical shock, personal injury, or death, disconnect electrical power source to unit and
discharge capacitor through a 10,000 ohm resistor before attempting to service, unless test procedures require
power to be connected. Ensure all ground wires are connected before certifying unit as repaired and/or
operational.
Symptom
Excessive noise,
No cooling.
Possible Causes
Fan motor mounting hardware/
bracket loose.
Copper tubing improperly routed.
Compressor internal noise.
No refrigerant charge in sealed system.
Restiction in sealed system.
Compressor faulty.
Rotary control faulty.
Corrective Action
Check mounting bolts/bracket
for tightness. Tighten if
necessary.
Inspect copper tubing for
excessive vibration. Secure
tubing.
Inspect compressor for proper
operation. Replace.
Test sealed system for leak.
Recharge unit.
Evacuate sealed system.
Remove restriction, recharge
unit.
Check compressor motor
windings for open / shorts.
Replace compressor.
Ensure all control connections
are tight and secure. Check
control for proper operation
and installation. Replace if
faulty.
Wattage slowly decreases below
minimum specification.
@2003 Maytag Appliances Company 16022380 Rev. 0 1
Undercharged, restricted strainer or plugged
capillary tube.
Test sealed system for proper
charge. Ensure system is free
of leaks/restriction. Repair,
Evacuate & recharge
sealed system.
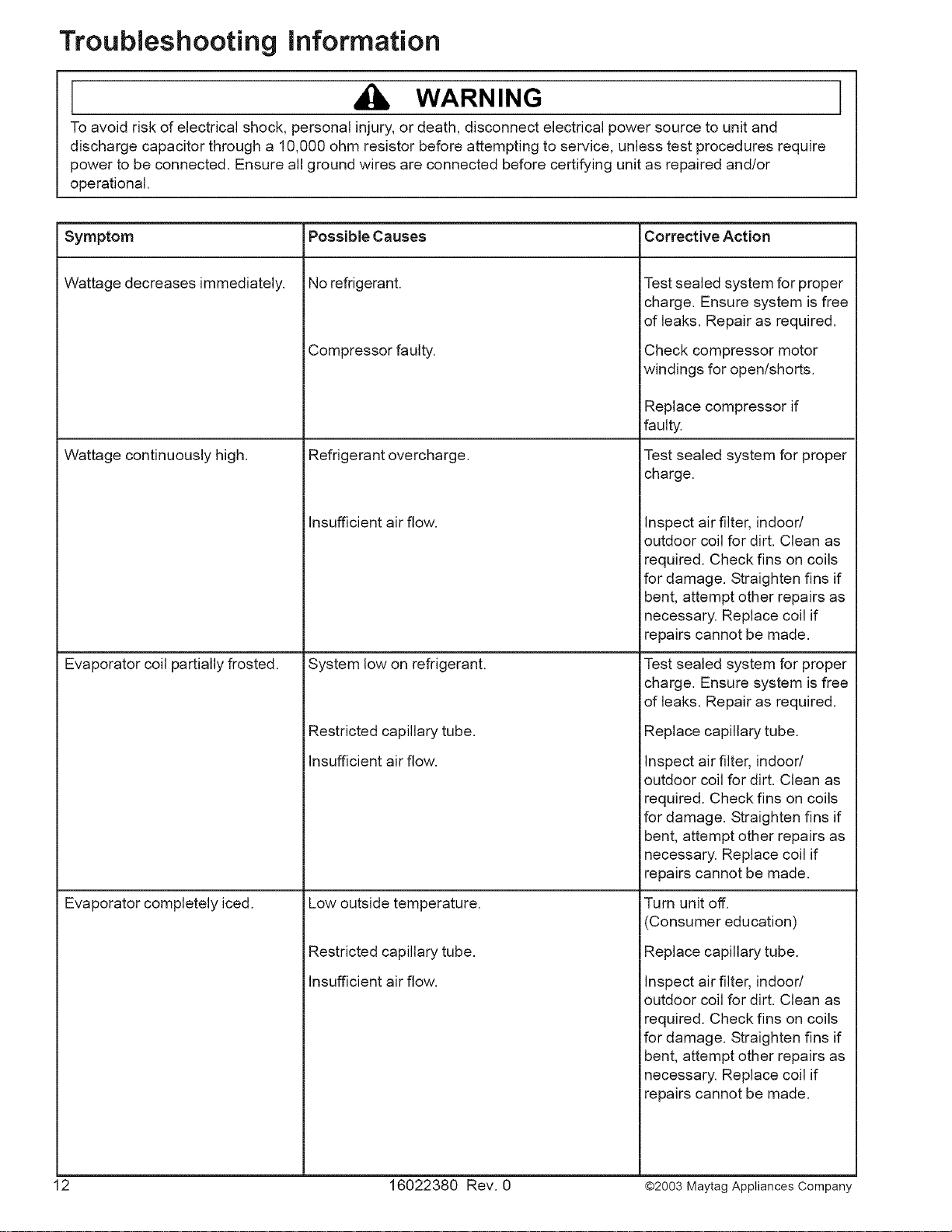
Troubleshooting information
WARNING
To avoid risk of electrical shock, personal injury, or death, disconnect electrical power source to unit and
discharge capacitor through a 10,000 ohm resistor before attempting to service, unless test procedures require
power to be connected. Ensure all ground wires are connected before certifying unit as repaired and/or
operational.
Symptom
Wattage decreases immediately.
Wattage continuously high.
Evaporator coil partially frosted.
Possible Causes
No refrigerant.
Compressor faulty.
Refrigerant overcharge.
Insufficient air flow.
System low on refrigerant.
Corrective Action
Test sealed system for proper
charge. Ensure system is free
of leaks. Repair as required.
Check compressor motor
windings for open/shorts.
Replace compressor if
faulty.
Test sealed system for proper
charge.
Inspect air filter, indoor/
outdoor coil for dirt. Clean as
required. Check fins on coils
for damage. Straighten fins if
bent, attempt other repairs as
necessary. Replace coil if
repairs cannot be made.
Test sealed system for proper
charge. Ensure system is free
of leaks. Repair as required.
Evaporator completely iced.
Restricted capillaw tube.
Insufficient air flow.
Low outside temperature.
Restricted capillaw tube.
Insufficient air flow.
Replace capillary tube.
Inspect air filter, indoor/
outdoor coil for dirt. Clean as
required. Check fins on coils
for damage. Straighten fins if
bent, attempt other repairs as
necessary. Replace coil if
repairs cannot be made.
Turn unit off.
(Consumer education)
Replace capillary tube.
Inspect air filter, indoor/
outdoor coil for dirt. Clean as
required. Check fins on coils
for damage. Straighten fins if
bent, attempt other repairs as
necessary. Replace coil if
repairs cannot be made.
12 16022380 Rev. 0 @2003 MaytagAppliancesCompany
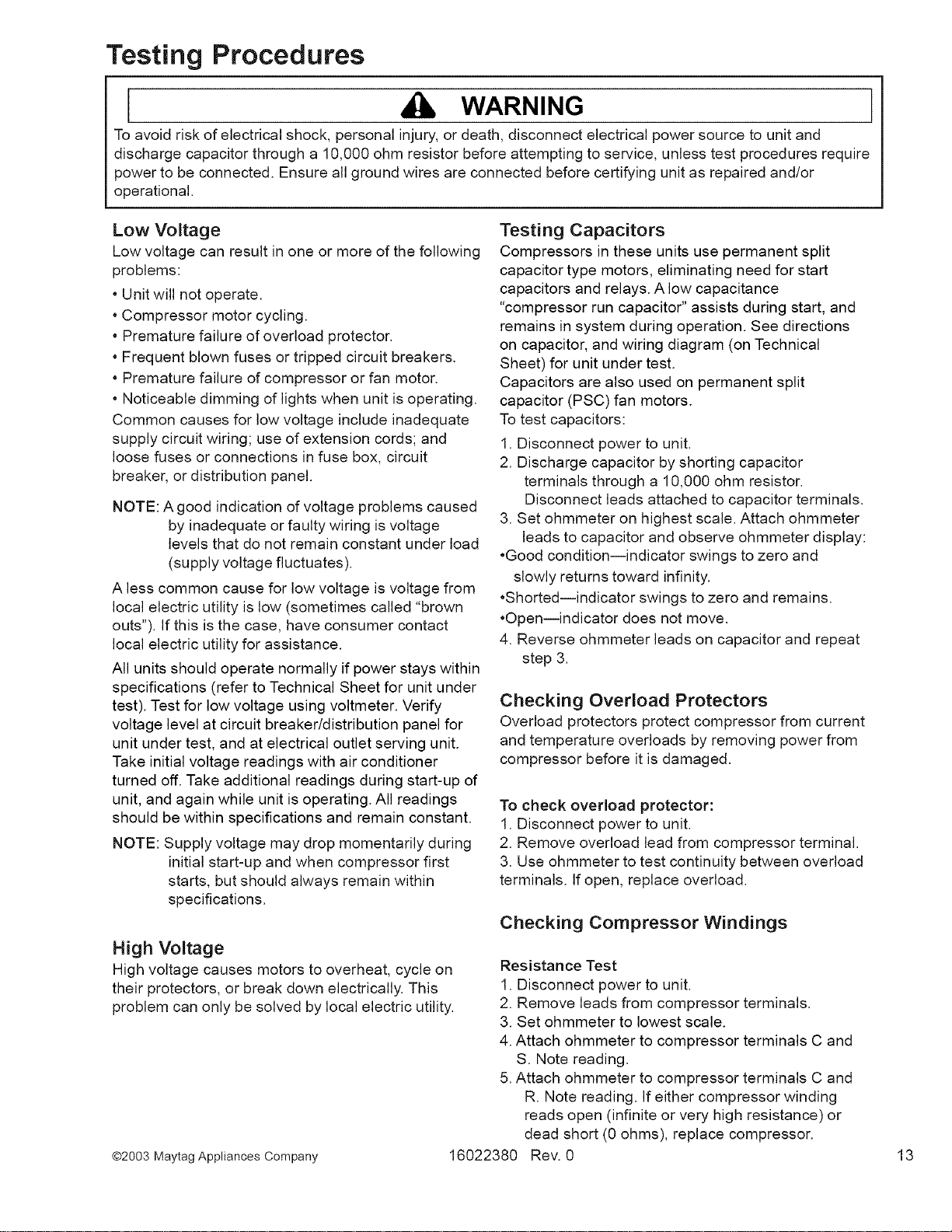
Testing Procedures
WARNING
To avoid risk of electrical shock, personal injury, or death, disconnect electrical power source to unit and
discharge capacitor through a 10,000 ohm resistor before attempting to service, unless test procedures require
power to be connected. Ensure all ground wires are connected before certifying unit as repaired and/or
operational.
Low Voltage
Low voltage can result in one or more of the following
problems:
Unit will not operate.
Compressor motor cycling.
Premature failure of overload protector.
Frequent blown fuses or tripped circuit breakers.
Premature failure of compressor or fan motor.
Noticeable dimming of lights when unit is operating.
Common causes for low voltage include inadequate
supply circuit wiring; use of extension cords; and
loose fuses or connections in fuse box, circuit
breaker, or distribution panel.
NOTE: A good indication of voltage problems caused
by inadequate or faulty wiring is voltage
levels that do not remain constant under load
(supply voltage fluctuates).
A less common cause for low voltage is voltage from
local electric utility is low (sometimes called "brown
outs"). If this is the case, have consumer contact
local electric utility for assistance.
All units should operate normally if power stays within
specifications (refer to Technical Sheet for unit under
test). Test for low voltage using voltmeter. Verify
voltage level at circuit breaker/distribution panel for
unit under test, and at electrical outlet serving unit.
Take initial voltage readings with air conditioner
turned off. Take additional readings during start-up of
unit, and again while unit is operating. All readings
should be within specifications and remain constant.
NOTE: Supply voltage may drop momentarily during
initial start-up and when compressor first
starts, but should always remain within
specifications.
High Voltage
High voltage causes motors to overheat, cycle on
their protectors, or break down electrically. This
problem can only be solved by local electric utility.
@2003 Maytag Appliances Company
16022380 Rev. 0 13
Testing Capacitors
Compressors in these units use permanent split
capacitor type motors, eliminating need for start
capacitors and relays. A low capacitance
"compressor run capacitor" assists during start, and
remains in system during operation. See directions
on capacitor, and wiring diagram (on Technical
Sheet) for unit under test.
Capacitors are also used on permanent split
capacitor (PSC) fan motors.
To test capacitors:
1. Disconnect power to unit.
2. Discharge capacitor by shorting capacitor
terminals through a 10,000 ohm resistor.
Disconnect leads attached to capacitor terminals.
3. Set ohmmeter on highest scale. Attach ohmmeter
leads to capacitor and observe ohmmeter display:
,Good condition--indicator swings to zero and
slowly returns toward infinity.
•Shorted--indicator swings to zero and remains.
•Open--indicator does not move.
4. Reverse ohmmeter leads on capacitor and repeat
step 3.
Checking Overload Protectors
Overload protectors protect compressor from current
and temperature overloads by removing power from
compressor before it is damaged.
To check overload protector:
1. Disconnect power to unit.
2. Remove overload lead from compressor terminal.
3. Use ohmmeter to test continuity between overload
terminals. If open, replace overload.
Checking Compressor Windings
Resistance Test
1. Disconnect power to unit.
2. Remove leads from compressor terminals.
3. Set ohmmeter to lowest scale.
4. Attach ohmmeter to compressor terminals C and
S. Note reading.
5. Attach ohmmeter to compressor terminals C and
R. Note reading. If either compressor winding
reads open (infinite or very high resistance) or
dead short (0 ohms), replace compressor.
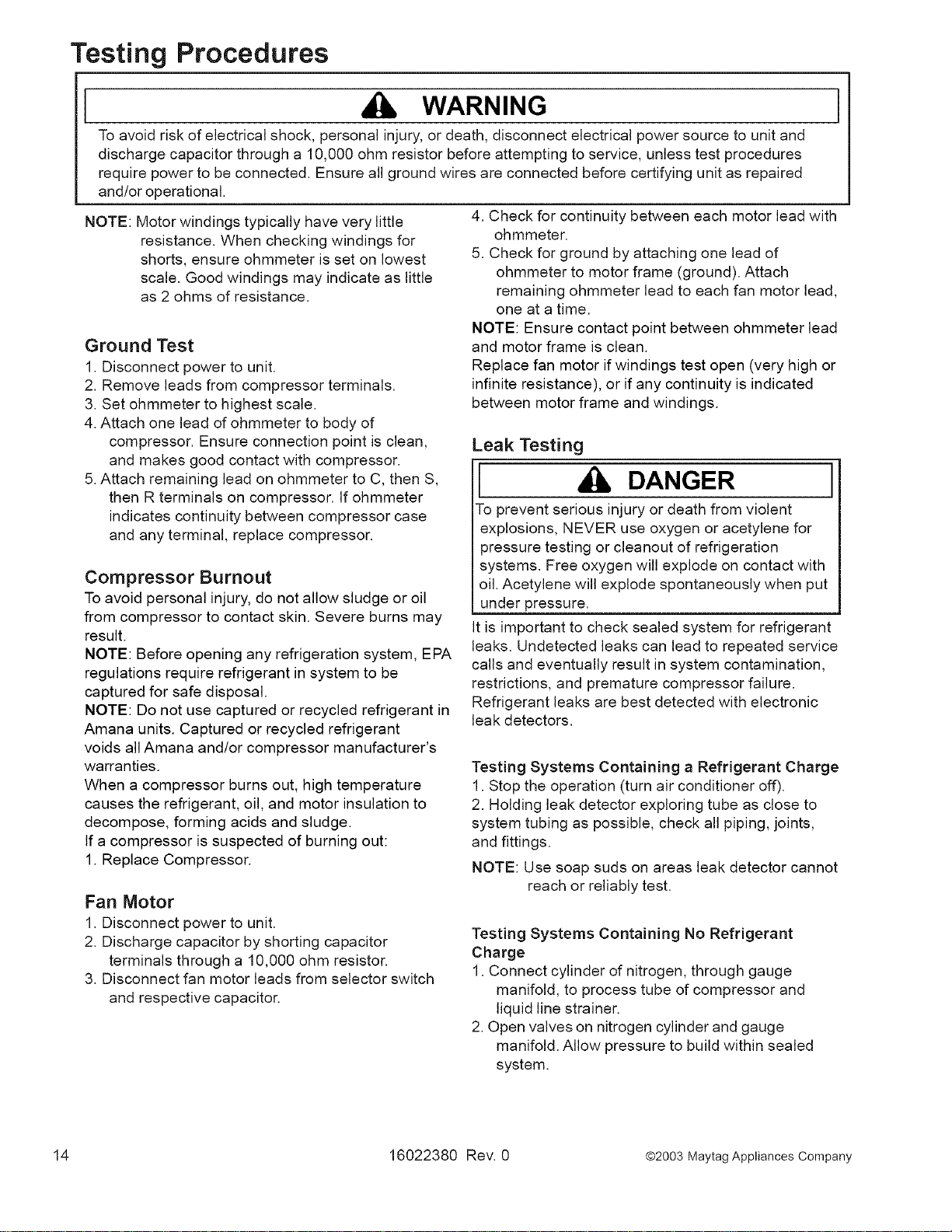
Testing Procedures
WARNING
To avoid risk of electrical shock, personal injury, or death, disconnect electrical power source to unit and
discharge capacitor through a 10,000 ohm resistor before attempting to service, unless test procedures
require power to be connected. Ensure all ground wires are connected before certifying unit as repaired
and/or operational.
NOTE: Motor windings typically have very little
resistance. When checking windings for
shorts, ensure ohmmeter is set on lowest
scale. Good windings may indicate as little
as 2 ohms of resistance.
Ground Test
1. Disconnect power to unit.
2. Remove leads from compressor terminals.
3. Set ohmmeter to highest scale.
4. Attach one lead of ohmmeter to body of
compressor. Ensure connection point is clean,
and makes good contact with compressor.
5. Attach remaining lead on ohmmeter to C, then S,
then R terminals on compressor. If ohmmeter
indicates continuity between compressor case
and any terminal, replace compressor.
Compressor Burnout
To avoid personal injury, do not allow sludge or oil
from compressor to contact skin. Severe burns may
result.
NOTE: Before opening any refrigeration system, EPA
regulations require refrigerant in system to be
captured for safe disposal.
NOTE: Do not use captured or recycled refrigerant in
Amana units. Captured or recycled refrigerant
voids all Amana and/or compressor manufacturer's
warranties.
When a compressor burns out, high temperature
causes the refrigerant, oil, and motor insulation to
decompose, forming acids and sludge.
If a compressor is suspected of burning out:
1. Replace Compressor.
Fan Motor
1. Disconnect power to unit.
2. Discharge capacitor by shorting capacitor
terminals through a 10,000 ohm resistor.
3. Disconnect fan motor leads from selector switch
and respective capacitor.
4. Check for continuity between each motor lead with
ohmmeter.
5. Check for ground by attaching one lead of
ohmmeter to motor frame (ground). Attach
remaining ohmmeter lead to each fan motor lead,
one at a time.
NOTE: Ensure contact point between ohmmeter lead
and motor frame is clean.
Replace fan motor if windings test open (very high or
infinite resistance), or if any continuity is indicated
between motor frame and windings.
Leak Testing
I DANGER
To prevent serious injury or death from violent
explosions, NEVER use oxygen or acetylene for
pressure testing or cleanout of refrigeration
systems. Free oxygen will explode on contact with
oil. Acetylene will explode spontaneously when put
under pressure.
It is important to check sealed system for refrigerant
leaks. Undetected leaks can lead to repeated service
calls and eventually result in system contamination,
restrictions, and premature compressor failure.
Refrigerant leaks are best detected with electronic
leak detectors.
Testing Systems Containing a Refrigerant Charge
1. Stop the operation (turn air conditioner off).
2. Holding leak detector exploring tube as close to
system tubing as possible, check all piping, joints,
and fittings.
NOTE: Use soap suds on areas leak detector cannot
reach or reliably test.
Testing Systems Containing No Refrigerant
Charge
1. Connect cylinder of nitrogen, through gauge
manifold, to process tube of compressor and
liquid line strainer.
2. Open valves on nitrogen cylinder and gauge
manifold. Allow pressure to build within sealed
system.
14 16022380 Rev. 0 @2003 MaytagAppliancesCompany