
Installation Instructions
2
3
5
6
01
23
45
67
CH 0 CH 1
CH 2
CC
VV
4
1
CH 3
Original Instructions
POINT I/O Wiring Base Assembly
Catalog Numbers 1734-TB, 1734-TBS
Environment and Enclosure
ATTENTION: This equipment is intended for use in a Pollution Degree 2 industrial
environment, in overvoltage Category II applications (as defined in EN/IEC 60664-1), at
altitudes up to 2000 m (6562 ft) without derating.
This equipment is not intended for use in residential environments and may not provide
adequate protection to radio communication services in such environments.
This equipment is supplied as open-type equipment for indoor use. It must be mounted within
an enclosure that is suitably designed for those specific environmental conditions that will be
present and appropriately designed to prevent personal injury resulting from accessibility to
live parts. The enclosure must have suitable flame-retardant properties to prevent or
minimize the spread of flame, complying with a flame spread rating of 5VA or be approved for
the application if nonmetallic. The interior of the enclosure must be accessible only by the
use of a tool. Subsequent sections of this publication may contain more information
regarding specific enclosure type ratings that are required to comply with certain product
safety certifications.
In addition to this publication, see the following:
• Industrial Automation Wiring and Grounding Guidelines, publication 1770-4.1, for more
installation requirements.
• NEMA Standard 250 and EN/IEC 60529, as applicable, for explanations o f the degrees of
protection provided by different types of enclosure.
Prevent Electrostatic Discharge
ATTENTION: This equipment is sensitive to electrostatic discharge, which can cause internal
damage and affect normal operat ion. Follow these guidelines when you handle this
equipment.
• Touch a grounded object to discharge potential static.
• Wear an approved grounding wriststrap.
• Do not touch connectors or pins on com ponent boards.
• Do not touch circuit components inside the equipment.
• Use a static-safe workstation if available.
• Store the equipment in appropriate static-safe packaging when not in use.
European Hazardous Location Approval
The following applies to products marked , II 3 G:
• Are intended for use in potentially explosive atmospheres as defined by European Union
Directive 2014/34/EU and has been found to comply with the Essential Health and Safety
Requirements relating to the design and construction of Category 3 equipment intended for
use in Zone 2 potentially explosive atmospheres, given in Annex II to this Directive.
• Compliance with the Essential Health and Safety Requirements has been assured by
compliance with EN 60079-15 and EN 60079-0.
• Are Equipment Group II, Equipment Category 3, and comply with the Essential Health and
Safety Requirements relating to the design and construction of such equipment given in Annex
II to Directive 2014/34/EU. See the EC Declaration of Conformity at rok.auto/certifications for
details.
• The type of protection is “Ex nA IIC T4 Gc” according to EN 60079-15.
• Comply to Standards EN 60079-0:2012+A11:2013, EN 60079-15:2010, refe rence certificate
number DEMKO 04 ATEX 0330347X.
• Are intended for use in areas in which explosive atmospheres caused by gases, vapors, mists,
or air are unlikely to occur, or are likely to occur only infrequently and for short periods. Such
locations correspond to Zone 2 classification according to ATEX directive 2014/34/EU.
WARNING: Special Conditions for Safe Use:
• This equipment is not resistant to sun light or other sources of UV radiation.
• This equipment shall be mounted in an ATEX/IECEx Zone 2 certified enclosure with a minimum
ingress protection rating of at least IP54 (in accordance with EN/IEC 60079-15) and used in an
environment of not more than Pollution Degree 2 (as defined in EN/IEC 60664-1) when applied
in Zone 2 environments. The enclosure must be accessible only by the use of a tool.
• This equipment shall be used within it s specified ratings defined by Rockwell Automation.
• Provision shall be made to prevent the rated voltage from being exceeded by transient
disturbances of more than 140% of the peak rated voltage w hen applied in Zone 2
environments.
• The instructions in the user manual shall be observed.
• This equipment must be used only with ATEX certified Rockwell Automation backplanes.
• Earthing is accomplished through mounting of modules on rail.
• Devices shall be used in an environment of not m ore than Pollution Degree 2.
ATTENTION: If this equipment is used in a manner not specified by the manufacturer, the
protection provided by the equipment may be impaired.
ATTENTION: Read this document and the documents listed in the Additional Resources
section about installation, configuration, and operation of this equipment before you install,
configure, operate, or maintain this product. Users are required to familiarize themselves
with installation and wiring instructions i n addition to requirements of all applicable codes,
laws, and standards.
ATTENTION: Installation, adjustments, putting into service, use, assembly, disassembly, and
maintenance are required to be carried out by suitably trained personnel in acco rdance with
applicable code of practice.
In case of malfunction or damage, no attempts at repair sh ould be made. The module should
be returned to the manufacturer for repair. Do not dismantle the module.
ATTENTION: This equipment is certified for use only within the surrounding air temperature
range of -20…+55 °C (-4…+131 °F). The equipment must not be used outside of this range.
ATTENTION: Use only a soft dry anti-static cloth to wipe down equipment. Do not use any
cleaning agents.
About the Assembly
The POINT I/O™ wiring base assembly consists of a mounting base (4) a nd a removable terminal block (RTB)(3). 1734-TB3
uses screw-clamp termination; 1734-TB3S uses spring-clamp terminations.
Description Description
1 DIN rail locking screw (orange) 4 Mounting base
2 Removable Terminal Block (RTB) handle 5 Interlocking side pieces
3 Removable Terminal Block 6 Mechanical keying (orange)
Prepare the Wires
Wiring Without Wire End Ferrule
Wire Size Range Number of Wires
0.25…2.5 mm²
(22...14 AWG)
1 16±1 mm (0.63±0.03 in) 14±1 mm (0.55±0.03 in)
2 18±1 mm (0.71±0.03 in) 16±1 mm (0.63±0.03 in)
Wiring With Wire End Ferrule
Wire Size
Number of
Range
Wires
0.75 mm²
1
(18 AWG)
(1) TWIN wire end ferrules are not recommended for wiring.
Strip Length
8-position RTB 12-position RTB
16±1 mm (0.63±0.03 in) 14±1 mm (0.55±0.03 in) Ferrule with insulating collar, in
18±1 mm (0.71±0.03 in) 16±1 mm (0.63±0.03 in)
ATTENTION: Do not wire more than 2 conductors on any single terminal.
Strip Length
8-position RTB 12-position RTB
Recommended Wire End
(1)
Ferr ule
accordance with DIN 46228-4 and
UL 486F.
Sleeve length: 12 mm (0.47 in)
Install the Mounting Base
To install the mounting base on the DIN rail (Allen-Bradley part number 199-DR1; 4 6277-3; EN50022), proceed as follows.
ATTENTION: This product is grounded through the DIN rail to chassis ground. Use zinc-plated
chromate-passivated steel DIN rail to assure proper grounding. The use of other DIN rail
materials (for example, aluminum or plastic) that can corrode, oxidize, or are poor
conductors, can result in impropTer or intermittent grounding. Secure DIN rail to mounting
surface approximately every 200 mm (7.8 in.) and use end-anchors appropriately. Be sure to
ground the DIN rail properly. See Industrial Automation Wiring and Grounding Guidelines,
Rockwell Automation publication 1770-4.1, for more information.
1. Position the mounting base vertically above the installed units (adapter, power supply or existing module).
2. Slide the mounting base down allowing the interlocking side pieces to engage the adjacent module or adapter.
3. Press firmly to seat the mounting base on t he DIN rail.
The mounting base snaps into place.
Install the Module
The module can be installed before or after base installation. Make sure that the mounting base is correctly keyed before
installing the module into the mounting base. In addition, make sure that the mounting base locking screw is positioned
horizontal referenced to the base.
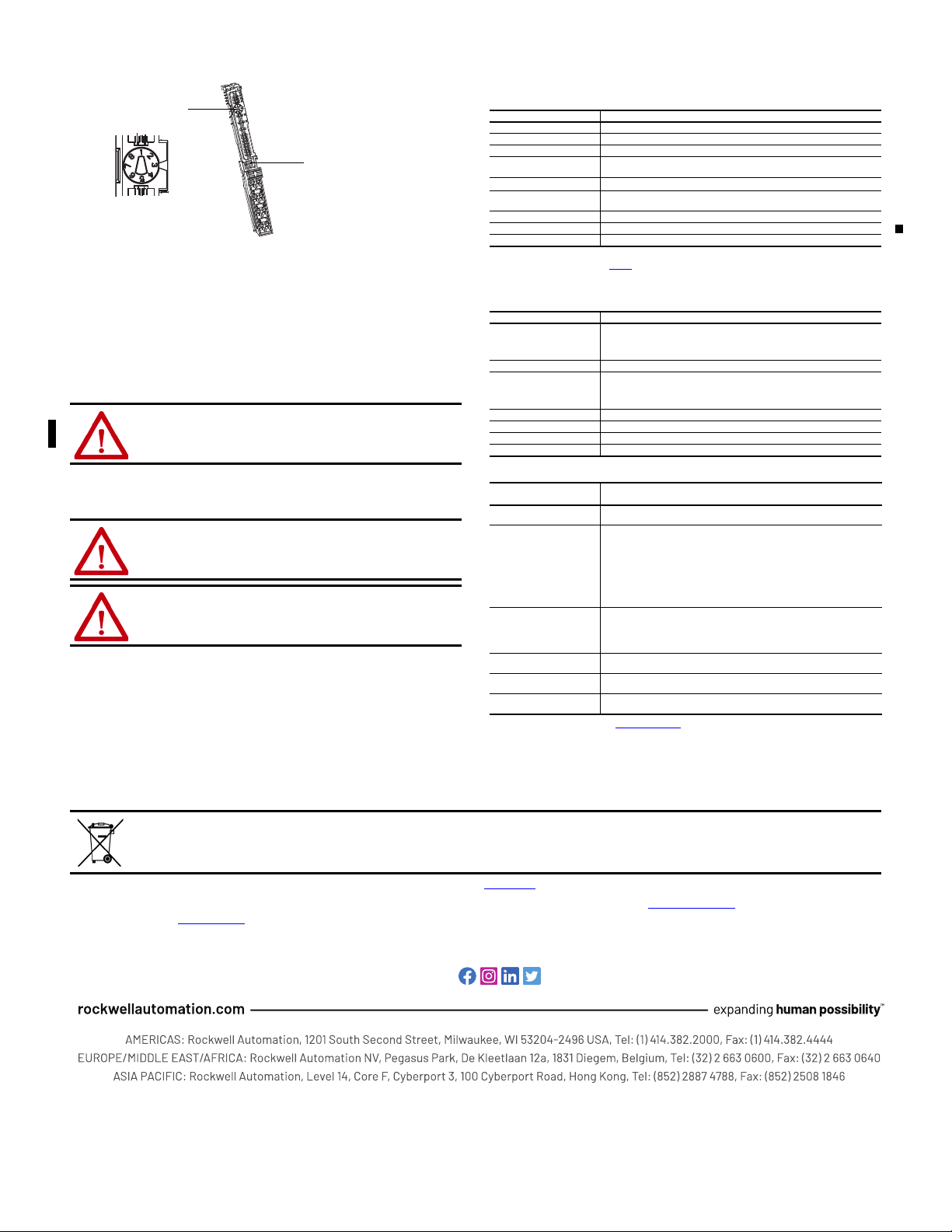
1734-MB
44229
Turn the keyswitch to align
the number with the notch.
Notch position 3 is shown.
Be sure the DIN rail
locking screw is in the
horizontal position.
1. Use a bladed screwdriver to rotate the keyswitch on the mounting base clockwise until the number required for
the type of module you are installing aligns with the notch in the base.
2. Verify the DIN rail locking screw is in the horizontal position.
You cannot insert the module if the locking mechanism is unlocked.
3. Insert the module straight down in to the mounting base and press to secure.
The module locks into place.
Install the Removable Terminal Block
A Removable Terminal Block (RTB) is supplied with your wiring base assembly. To remove, pull up on the RTB handle. This
allows the mounting base to be removed and replaced as necessary without removing any wiring. To reinsert the removable
terminal block, proceed as follows.
1. Insert the end opposite the handle into the base unit.
This end has a curved section that engages with the wiring base.
2. Rotate the terminal block into the wiring base until it locks itself in place.
3. If an I/O module is installed, snap the RTB handle into place on the module.
WARNING: For 1734-RTBS and 1734-RTB3S, to latch and unlatch the wire, insert a bladed
screwdriver (catalog number 1492-N90 – 3 mm diameter blade) into the opening at approximately
73° (blade surface is parallel with top surface o f the opening) and push up gently.
Remove a Mounting Base
To remove a mounting base, you must remove any installed module, and the module installed in the base to the right.
Remove the removable terminal block, if wired.
ATTENTION: Do not remove or replace a Terminal Base unit while power is applied.
Interruption of the backplane can result in unintentional operation or machine motion.
WARNING: Do not disconnect or replace component unless power is switched off or area is known
to be nonhazardous. Do not pull on the installed wiring to remove a terminal base. A shock hazard
exists if power is applied to the terminal base.
1. Unlatch the RTB handle on the I/O module.
2. Pull on the RTB handle to remove the removable terminal block.
3. Press the module lock on the top of the module and pull on the I/O module to remove from the base.
4. Repeat steps 1…3 for the module to the right.
5. Use a small bladed screwdriver to rotate the orange base locking screw t o a vertical position.
This releases the locking mechanism.
6. Lift the mounting base straight up to remove.
Specifications
General
Attribute Value
Field power bus supply voltage 28.8V DC, 120/240V AC
Field power bus supply current max 10 A
Dimensions (HxWxD) approx. 65 x 12 x 133.4 mm (2.56 x 0.47 x 5.25 in.)
Weight, approx.
(1) (2)
Wire category
Wire size
Enclosure type rating None (open-style)
Terminal base screw torque 0.8 N•m (7 lb•in) — 1734-TB only
ATEX temp code T4 — 1734-TB only
(1) Use this conductor category information for planning conductor routing as described in Industrial Automation Wiring and
Grounding Guidelines, publication 1770-4.1
(2) Use this Conductor Category information for planning conductor routing as described in the appropriate System Level
Installation Manual.
Environmental Specifications
Attribute Value
Temperature, operating
Temperature, surrounding air max 55 °C (131 °F)
Temperature, nonoperating
Relative humidity IEC 60068-2-30 (Test Db, Unpackaged Damp Heat): 5…95% noncondensing
Vibration IEC 60068-2-6 (Test Fc, Operating): 5 g @ 10…500 Hz
Shock, operating IEC 60068-2-27 (Test Ea, Unpackaged Shock): 30 g
Shock, nonoperating IEC 60068-2-27 (Test Ea, Unpackaged Shock): 50 g
Certifications
Certification (when the product is
(1)
marked)
c-UL-us
CE
Ex
RCM
KC
EAC
(1) See the Product Certification link at rok.auto/certifications for Declarations of Conformity, Certificates, and other certification
details.
(2) Low Voltage (LV) certification applies to 1734-TB only.
83.8 g (2.94 oz) — 1734-TB
73.3g (2.57 oz) — 1734-TBS
2
0.25…2.5 mm² (22…14 AWG) solid or stranded copper wire that is rated at 75 °C (167 °F), or
greater, 1.2 mm (3/64 in.) insulation max
.
IEC 60068-2-1 (Test Ad, Operating Cold),
IEC 60068-2-2 (Test Bd, Operating Dry Heat),
IEC 60068-2-14 (Test Nb, Operating Thermal Shock):
-20…+55 °C (-4…+131 °F)
IEC 60068-2-1 (Test Ab, Unpackaged Nonoperating Cold),
IEC 60068-2-2 (Test Bb, Unpackaged Nonoperating Dry Heat),
IEC 60068-2-14 (Test Na, Unpackaged Nonoperating Thermal Shock):
-40…+85 °C (-40…+185 °F)
Value
UL Recognized Component Industrial Control Equipment, certified for US and Canada.
See UL File E195367.
European Union 2014/30/EU EMC Directive, compliant with:
EN 61131-2; Programmable Controllers (Clause 8, Zone A & B)
EN 61326-1; Meas./Control/Lab., Industrial Requirements
EN 61000-6-2; Industrial Immunity
EN 61000-6-4; Industrial Emissions
European Union 2014/35/EU LVD, compliant with:
EN 61131-2; Programmable Controllers (Clause 11)
European Union 2011/65/EU RoHS, compliant with:
EN 50581; Technical Documentation
European Union 2014/30/EU ATEX Directive, compliant with:
EN 60079-0:2012 + A11:2013; General Requirements
EN 60079-15”2010: Potenti ally Explosive Atmospheres, Protection “n”
II 3G Ex nA IIC T4 Gc
DEMKO 04 ATEX 0330347X
Australian Radiocommunications Act, compliant with:
AS/NZS CISPR 11; Industrial Emissions
Korean Registration of Broadcasting and Communications Equipment, compliant with:
Article 58-2 of Radio Waves Act, Clause 3
Russian Customs Union TR CU 020/2011 EMC Technical Regulation
Russian Customs Union TR CU 004/2011 LV Technical Regulation
(2)
Waste Electrical and Electronic Equipment (WEEE)
At the end of life, this equipment should be collected separately from any unsorted municipal waste.
Rockwell Automation maintains current product environmental compliance information on its website at rok.auto/pec.
Your comments help us serve your documentation needs better. If you have any suggestions on how to improve our content, complete the form at rok.auto/docfeedback.
For technical support, visit
Rockwell Otomasyon Ticaret A.Ş. Kar Plaza İş Merkezi E Blok Kat:6 34752, İçerenköy, İstanbul, Tel: +90 (216) 5698400 EEE Yönetmeliğine Uygundur
Allen-Bradley, expanding human possibility, FactoryTalk, POINT I/O, Rockwell Automation, and TechConnect are trademarks of Rockwell Automation, Inc.
Trademarks not belonging to Rockwell Automation are property of their respective companies.
Publication 1734-IN511C-EN-P - January 2021 | Supersedes Publication 1734-IN511B-EN-P- March 2001
Copyright © 2021 Rockwell Automation, Inc. All rights reserved. Printed in China.
rok.auto/support.
PN-612938