
1391
AC
Servo
Document
Controller
Update
un
Introduction
Page
1-5
Page
2-1
Instruction
publication
This
Manual
your
The
-
-
The
Speed
(1391-5.1,
manual
following
Anti-Backlash
Provisions
available.
Linear
Linear
This
for
be
Accel/Decel
accel/decel
module
to
up
set
for
following
Regulation
provides
for
future
is
updated
to
use
provides
four
preset
all
speeds.
specification
Manual
updated
October,
dated
reference.
Option/Modification
the
can
0.05%
Anti-Backlash
1388
be
set
a
manually
speeds.
has
(max.)
A
information
1992).
using
the
generated
single
been
added.
of
maximum
for
the
1391
Instruction
Please
information.
module
CR-APG-001
trapezoidal
acceleration/deceleration
speed
motor
place
(1388-XA)
with
this
publication
Control
velocity
95%
load
change
with
are
Module.
profile
can
rate
Page
Page
Page
Page
3-3
5-4
5-8
7-4
Planetary
The
addition,
External
The
Bus
Scaling
Table
Typical
Motor
Number2
1326AB-A1G
The
several
Shunt
following
voltage
information
5.C
Scaling
Catalog
following
Following
Gearbox
descriptions
Regulator
sentence
can
be
for
1326
(A)
lc
4.5
error
Error
=
catalog
supplements
monitoredonterminals
for
the
AC
example
Velocity
Gain
number
have
Resistor
1326AB-A1G
Servomotors
1391B-AA15
4
should be
1
00
1
been
(TB5,
the
S1
ipm
ipm/ml
description
clarified.
current
Switch
added
=
is
Refer
Terminals
material.
(+)
9
and
has
motor
Setting1
1391B-AA22
3
to
step
ml
100
being
to
pages
8,
9,
(-)
7
of
been
added.
1391B-AA45
15.
added.
10)
TB5.
In
and
2
3.

Document
1391
Instruction
Update
Manual
External
Shunt
Regulator
Resistor
Page
7-6
1391
Bulletin
Number
-
Type
Code
MOD
MOD
Description
Modifica¬
tion
Kit
Linear
The
with
provides
controller.
The
profiles
Accel/Decel
following
the
1391
when
Description
Code
SR22A
SR45A
information
Linear
Accel/Decel
adjustable
to
Up
can
be
the
SR22A
Description
Regulator
Shunt
Regulator
Shunt
Control
Module
new
is
Control
acceleration/deceleration
four
remote
manually
moduleisinstalled
or
operated
Resistor
Resistor
and
Module
local
preset
with
as
for
for
explains
Controller
22.5A
Controller
45A
manual
(CR-APG-001).
control
speeds
controlled
follows:
controller
the
for
are
1391
available.
trapezoidal
operation
This
motion
module
1
.
Perform
2.
Remove
3.
Install
shown
4.
Set
maximum
Accel
(minimum
Important:
bi-directional.
counterclockwise
rotation
Accel/Decel
increase
4
all
the
Start-Up
all
system
interconnect
and
in
Figure
of
the
clockwise
and
Decel
accel/decel
All
will
decrease
pots
time.
Procedure
power.
7.3.
Refer
Speed
pots
position
to
pots
time).
potentiometers
The
Local
rotation
output.
will
decrease
presented
the
Linear
to
(SPD
the
Speed
will
Accel/Decel
Figure
1-SPD
(speed
maximum
the
on
pots
increase
Counterclockwise
time,
earlierinthis
Control
7.4
minimum).
are
while
dimension
for
4
or
remote
pots)
Set
counterclockwise
setup
are
15
such
clockwise
and
rotationofthe
module
output
clockwise
chapter.
Module
information.
the
to
front
the
position
turn,
that
rotation
as
panel
will

TB2/3
TB2/3
5
;14-
m
20-
_B_
MAX/CONTROL1
m
TB2/3
m
Command
yx.
Feedback
(NOT)
A
(NOT)
B
z
(NOT)
Z
+5V
COMMON
CR-LPS-455
+5VDC
COMMON
+12VDC
DC
-12V
COMMON
COMMC
I
ZJ
Figure
Typical
Axis
Overtravel
Cables
Cable
5/12V
Power
+24V
r-
B.5
MAX/CONTROL
115V
AC
Remote
Stop
dwired
£
Har
I
2
3
A
H
A-B
845H/N
.
Encoder7
4
DC
Supply
DC
jjfc®
n
-
*
y
—
1
-
y
Jiol—
ifj-j
Interconnect
1391B
TB4
CONTACTOR
TB2
-VELOCITY
VELOCITY
2_
+
3
COMMON6
SOURCE,
ENABLE
ENABLE
TB4
DROK,
(CLOSED
COM.
COM.
115V
=
Servo
6
6
+23V
AC,
1
OK)
Document
1391
Diagram
Controller
DC
A
Update
Instruction
(when
Manual
Brake
supplied)
1326
<4
<4
/-
<4
AC
Servomotor
—
—
0ÿ5-1
-f)
-
-
j
-
CKyO—
Motor
Resolver
1
1
1
Refer
2
Use
3
Use
4
Use
5
X-axis
6
If
the
7
Maximum
8-1
Example:
Maximum
Assuming
maximum
meters),
to
the
MAX/CONTROL
Belden
brand
Belden
brand
Belden
brand
connections
drive
istobe
allowable
power
5V
DC
Encoder
Allowable
the
allowable
or
1/2
#8760
#9504
#9533
supply
cable
the
or
or
or
are
shown
operated
cable
distance
larger
or
requires
Cable
Resistance
AWG
is
22
resistance
calculated
Installation
equivalent
equivalent
equivalent
-
Y-axis
torque
as
a
using
cable.
regulated
a
(0.283
.25
1
of
length.
Setup
and
cable.
shielded
pair,
twisted
shielded
cable.
connections
block,
command
22
AWG
supply
between
V/l
=R=
mm2)
ohms.
=
with
Both
Manual
shielded
(TB3)
(0.283
4.75
(5-4.75)
resistance
a
supply
the
(999-051)
are
wires
mm2)
/
and
cable,
and
feet
40
identical.
shouldbeconnected
cable
and
V
5.25
0.20
1
.25
=
rating
of
return
and
1391
the
(12.2
5V
a
DC
and
ohms
ohms/1000
16
leads
Interconnect
meters)
to
supply
DC
will
draw
must
be
maximum.
TB2-15,
1391
is
39
200mA
(300
feet
considered,
Drawing
Shields
(11.9
feet
(max.).
meters),
so
16
the
for
grounded
&
17.
meters).
V
A
5
78
feet
actual
further
supply
DC
(23.8
length
details.
greater
If
controller
at
being
is
meters)
of
the
cable
of
cable
only.
distance
used.
cable
is
39
will
is
feet
needed,
have
(1
1
the
.9
use
a
17
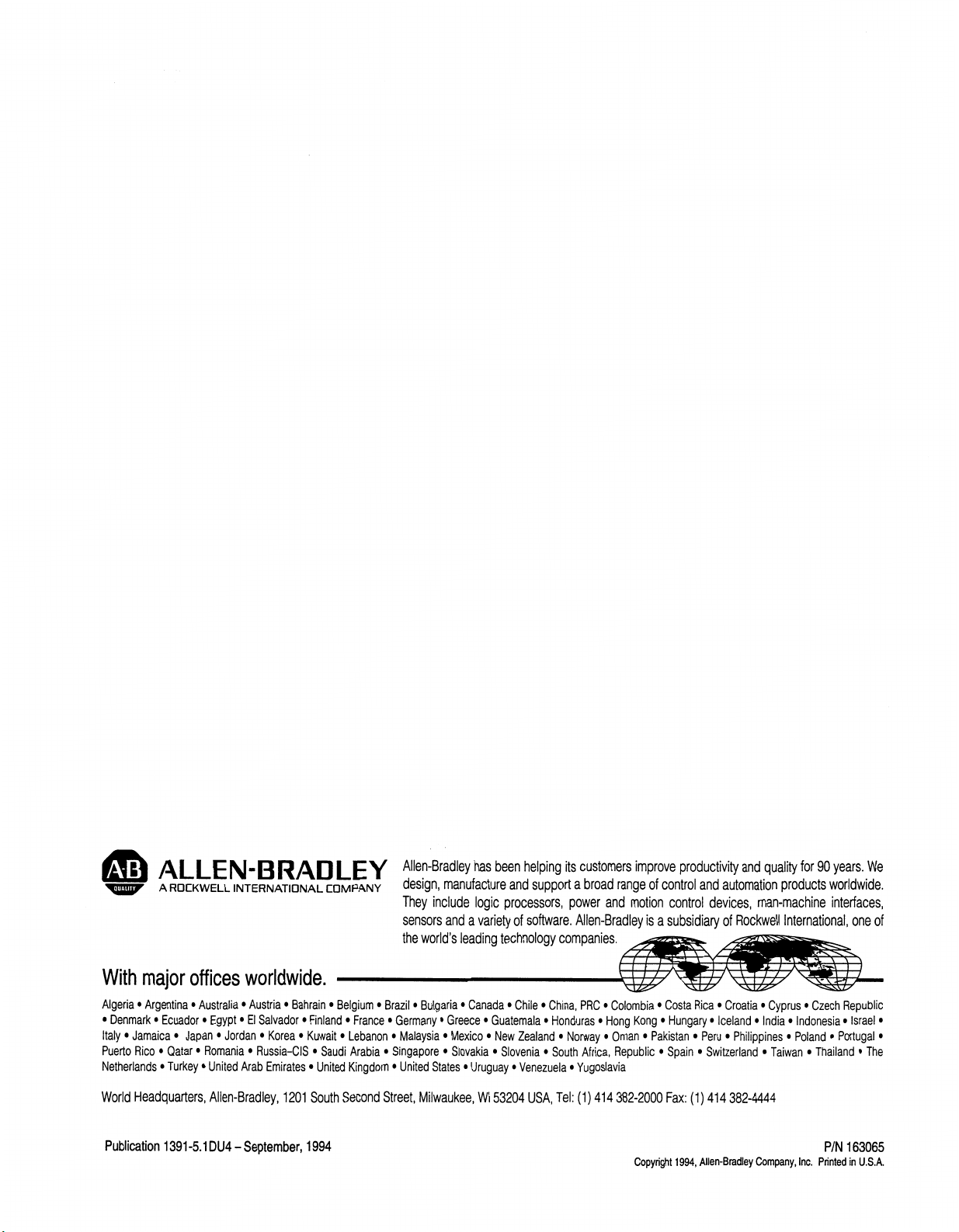
E3
With
Algeria•Argentina
Denmark•Ecuador
•
Italy
Puerto
Netherlands
ALLEN-BRADLEY
ROCKWELL
A
major
Jamaica
•
Rico
•
Qatar
•
Turkey
•
INTERNATIONAL
offices
•
Japan
•
worldwide.
Australia•Austria
Egypt
El
•
•
Jordan
•
Romania
•
United
Arab
•
COMPANY
Belgium
Bahrain
•
•
Salvador
•
Russia-CIS•Saudi
•
Korea
•
Emirates
Finland
Kuwait
United
•
•
•
France
•
Lebanon
Arabia
Kingdom
Allen-Bradley
design,
They
include
sensors
the
world’s
Bulgaria
Brazil
•
Germany
•
•
•
Malaysia
Singapore
United
States
•
•
has
been
manufacture
and
leading
•
Greece
Mexico
•
Slovakia•Slovenia
•
•
and
processors,
logic
variety
of
a
technology
Canada•Chile
Guatemala
•
New
Zealand
•
Uruguay
Venezuela
•
helping
its
support
software.
companies.
China,
•
Honduras
•
Norway
•
South
•
•
range
and
Colombia
•
Hong
•
Oman
•
Republic
motion
improve
Kong•Hungary
customers
broad
a
power
Allen-Bradley
PRC
Africa,
Yugoslavia
of
control
control
subsidiary
is
a
Costa
•
Pakistan
•
Spain
•
productivity
and
devices,
Rica
•
Iceland•India•Indonesia•Israel
•
Peru
•
Switzerland
•
quality
and
automation
man-machine
of
Rockwell
Cyprus
Croatia
•
Philippines
•
Taiwan•Thailand
•
products
International,
•
for
90
Czech
•
Poland
years.
We
worldwide.
interfaces,
one
of
Republic
•
Portugal
•
•
•
The
Headquarters,
World
Publication
1
391
-5.
1DU4
Allen-Bradley,
-September,
1201
South
1994
Second
Street,
Milwaukee,
Wl
53204
USA,
Tel:
(1)
414
382-2000
Fax:
Copyright
(1)
1994,
Allen-Bradley
414
382-4444
Company,
Inc.
P/N
Printed
163065
in
U.S.A.