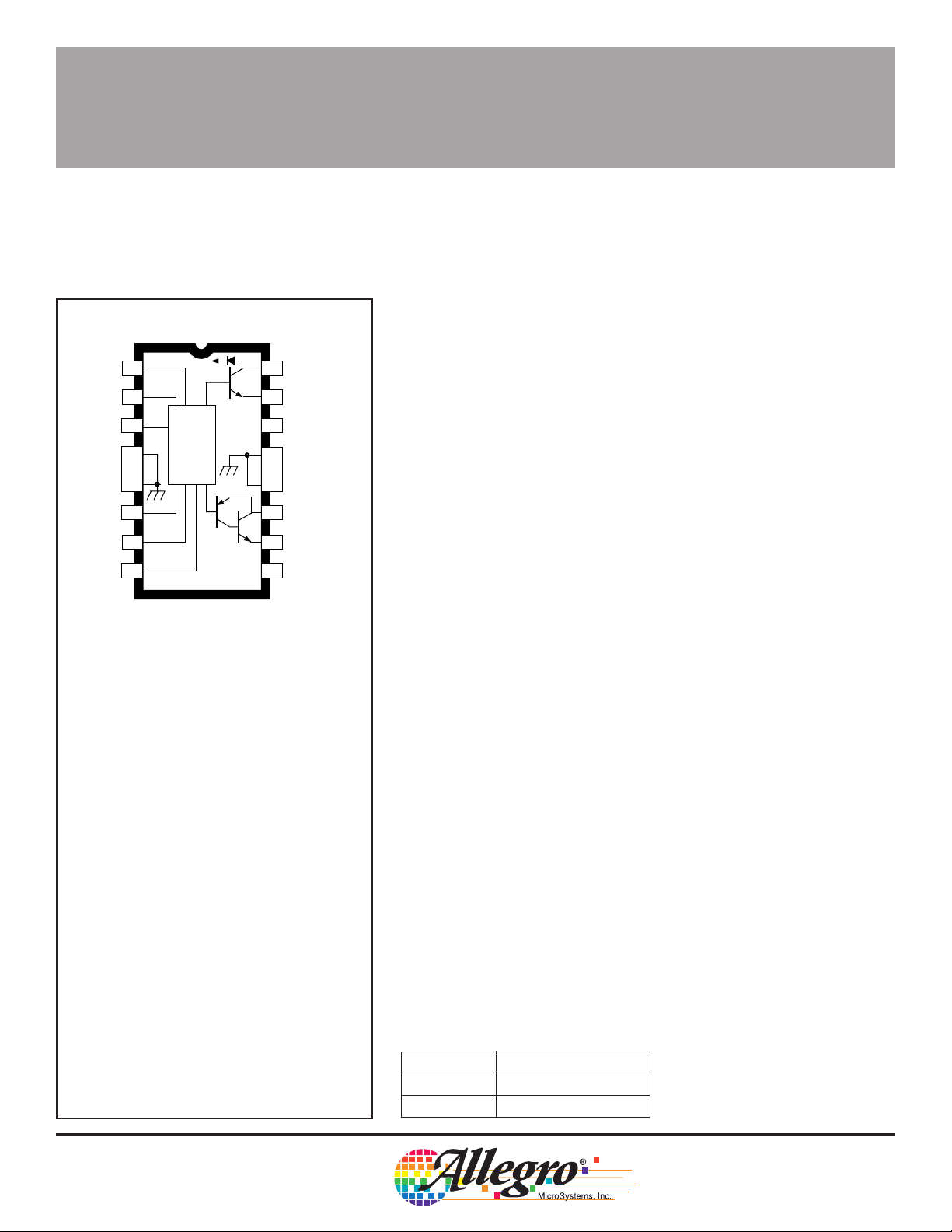
2961
HIGH-CURRENT
HALF-BRIDGE
PRINTHEAD/MOTOR DRIVER
PRINTHEAD/MOTOR DRIVER—WITH INTERNAL
CURRENT SENSING AND CONTROL
UDN2961B
V
1
REF
IN
2
3
INPUT
ENABLE
RC
MODE
4
5
6
7
8
GROUND
GROUND
ABSOLUTE MAXIMUM RATINGS
Supply Voltage, VBB. . . . . . . . . . . . . . 45 V
Output Current, I
(t
≤ 20 µs, 10% duty cycle) . . ±4.0 A
w
Logic Supply Voltage, V
Input Voltage Range,
V
. . . . . . . . . . . . . . . -0.3 V to +7.0 V
IN
Package Power Dissipation,
P
. . . . . . . . . . . . . . . . . . . See Graph
D
Operating Temperature Range,
T
. . . . . . . . . . . . . . . . -20°C to +85°C
A
Junction Temperature, T
Storage Temperature Range,
T
. . . . . . . . . . . . . . . -55°C to +150°C
S
Output current rating may be restricted to a value
determined by system concerns and factors.
These include: system duty cycle and timing,
ambient temperature, and use of any heatsinking
and/or forced cooling. For reliable operation, the
specified maximum junction temperature should
not be exceeded.
* Fault conditions that produce excessive junction
temperature will activate device thermal shutdown
circuitry. These conditions can be tolerated, but
should be avoided.
V
BB
CURRENTCONTROL
LOGIC
(continuous) . ±3.4 A
OUT
16
15
14
13
12
V
BB
11
10
9
V
CC
. . . . . . . . . 7.0 V
CC
. . . . . . . +150°C*
J
SINK OUT
EMITTER
NC
GROUND
GROUND
LOAD SUPPLY
SOURCE OUT
LOGIC SUPPLY
Dwg. PP-035
2961
HIGH-CURRENT HALF-BRIDGE
The UDN2961B and UDN2961W are 3.4 A half bridges designed
specifically for driving solenoid printheads, stepper motors, and dc
motors. The UDN2961B/W consists of a power source driver output,
a power sink driver output, a flyback recovery diode, internal current
sensing circuitry, and a user-selectable fixed off-time chopper circuit.
The output drivers are capable of sustaining 45 V with continuous
currents of ±3.4 A and peak transient currents of ±4 A permitted. The
outputs have been optimized for a low output saturation voltage
(typically 2.6 V total source plus sink drops at 3.4 A).
For output current control, load current is sensed internally and
limited by chopping the output driver(s) in a user-selectable fixed offtime PWM mode. The maximum output current is determined by the
user’s selection of a reference voltage. The MODE pin determines
whether the current control circuitry will chop in a slow current-decay
mode (only the source driver switching) or in a fast current-decay
mode (source and sink switching). A user-selectable blanking window
prevents false triggering of the current control circuitry during
chopping.
The UDN2961B is supplied in a 16-pin dual in-line plastic batwing
package with a copper lead-frame and heat sinkable tabs for improved
power dissipation capabilities. For higher power dissipation requirements, the UDN2961W is supplied in a 12-pin single in-line power tab
package.
FEATURES
■ 3.4 A, 45 V Source and Sink Drivers
■ Internal Current Sensing
■ User-Selectable Fixed Off-Time PWM Current Control
■ Internal Flyback Diode
■ Low Output Saturation Voltage
■ Chip Enable
■ Fast or Slow Current-Decay Modes
■ Programmable Blanking Window
■ Internal Thermal Shutdown Circuitry
Always order by complete part number:
Part Number Package
UDN2961B 16-Pin DIP
UDN2961W 12-Pin Power-Tab SIP
Data Sheet
29318.16*
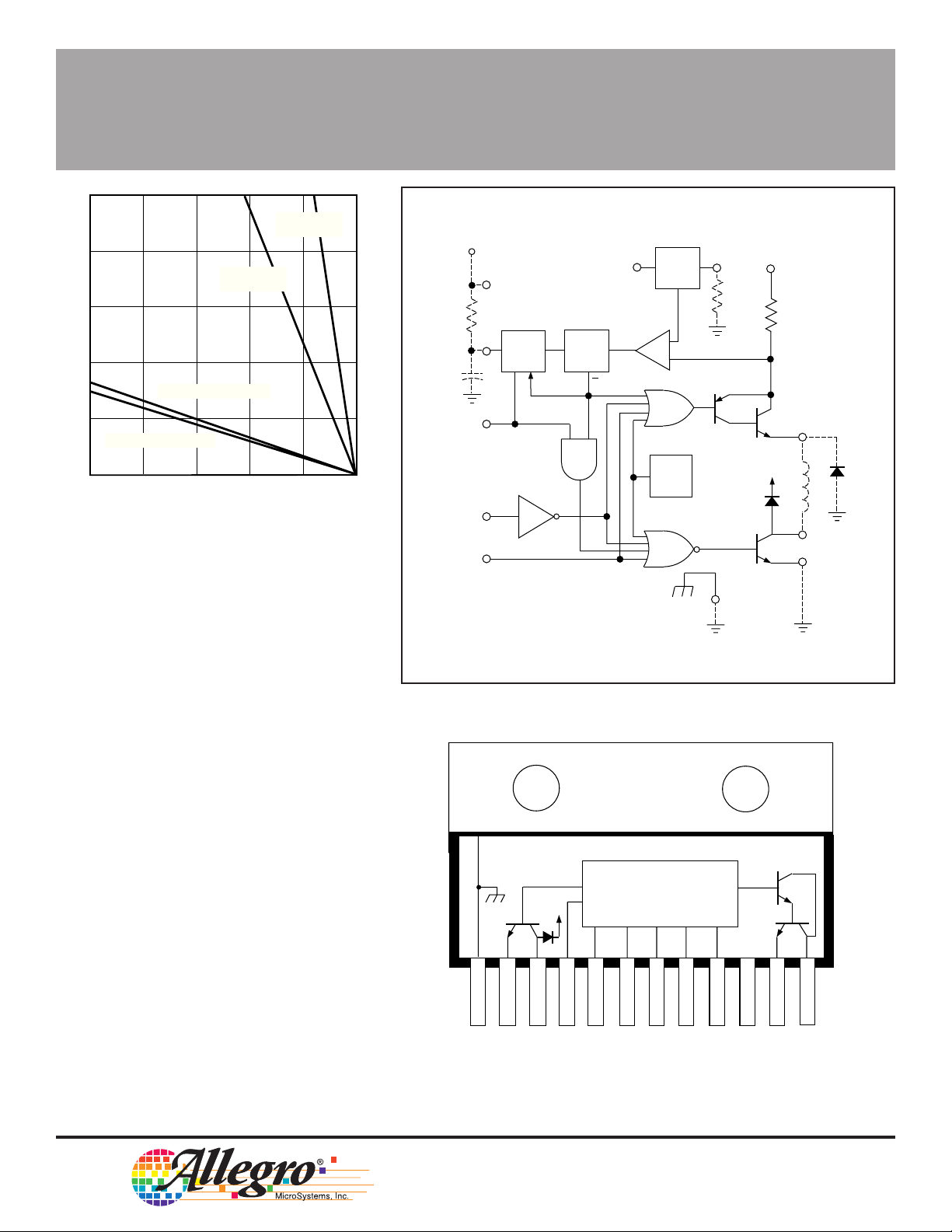
2961
HIGH-CURRENT
HALF-BRIDGE
PRINTHEAD/MOTOR DRIVER
10
SUFFIX 'W',
R = 2.0°C/W
θJT
8
SUFFIX 'B',
R = 6.0°C/W
θJT
6
4
SUFFIX 'W', R = 38°C/W
2
SUFFIX 'B', R = 43°C/W
0
ALLOWABLE PACKAGE POWER DISSIPATION IN WATTS
25
θJA
50 75 100 125 150
θJA
TEMPERATURE IN °C
Dwg. GP-032A
R
C
MODE
ENABLE
INPUT
FUNCTIONAL BLOCK DIAGRAM
+5 V
RC
V
LOW
TRIP
CC
ONE
SHOT
FLIPFLOP
V
REF
Q
CIRCUIT
RS
+
-
TSD
REF
V
R
CV
SENSE
2940 Ω
V
BB
SOURCE OUT
V
BB
SINK OUT
EMITTER
GROUND
UDN2961W
V
CURRENT-
V
BB
1 2 3 4 5 6 7 8 9 10 11 12
REF
V
EMITTER
GROUND
SINK OUT
CONTROL
LOGIC
V
CC
CV
R
INPUT
ENABLE
RC
MODE
SOURCE OUT
LOGIC SUPPLY
Dwg. PP-036
Dwg. FP-019A
BB
LOAD SUPPLY
115 Northeast Cutoff, Box 15036
W
Worcester, Massachusetts 01615-0036 (508) 853-5000
Copyright © 1995, 1996 Allegro MicroSystems, Inc.

2961
HIGH-CURRENT
HALF-BRIDGE
PRINTHEAD/MOTOR DRIVER
ELECTRICAL CHARACTERISTICS at T
V
= 4.75 V to 5.25 V, R
CC
= 2940 Ω (unless otherwise noted).
CV
= +25°C, V
A
= 45 V,
BB
Limits
Characteristic Symbol Test Conditions Min. Typ. Max. Units
Output Drivers
Output Leakage Current I
Output Saturation Voltage V
Output Sustaining Voltage V
CE(SAT)
CE(sus)
Recovery Diode Leakage Current I
Recovery Diode Forward Voltage V
Motor Supply Current I
BB(on)
I
BB(off)
Output Rise Time t
Output Fall Time t
CEX
R
VEN = 0.8 V, V
= 0.8 V, V
V
EN
Source Driver, I
Source Driver, I
Sink Driver, I
Sink Driver, I
I
= ±3.4 A, L = 3 mH 45 — — V
OUT
OUT
OUT
VR = 45 V — <1.0 100 µA
F
IF = 3.4 A — — 2.0 V
VEN = 2.0 V, VIN = 0.8 V, No Load — — 70 mA
VEN = 0.8 V — — 2.5 mA
r
f
Source Driver, I
Sink Driver, I
OUT
Source Driver, I
Sink Driver, I
OUT
= 0 V — <-1.0 -100 µA
SOURCE
= 45 V — <1.0 100 µA
SINK
= -3.4 A — 1.6 2.2 V
OUT
= -3.0 A — 1.5 — V
OUT
= 3.4 A — 1.0 1.4 V
= 3.0 A — 0.9 — V
= -3.4 A — — 600 ns
OUT
= 3.4 A — — 600 ns
= -3.4 A — — 600 ns
OUT
= 3.4 A — — 600 ns
Control Logic
Logic Input Voltage V
Logic Input Current I
Reference Input Current I
Transconductance I
TRIP/VREF
Logic Supply Current I
Turn On Delay t
IN(1)
V
IN(0)
IN(1)
I
IN(0)
REF
CC
pd(on)
VIN = 5.0 V — — 10 µA
VIN = 0 V — — -1.0 mA
V
= 5.0 V — — 50 µA
REF
V
= 1.0 V 0.9 1.0 1.1 A/V
REF
= 3.2 V 0.9 1.0 1.1 A/V
V
REF
VEN = 2.0 V, VIN = 0.8 V, No Load — — 160 mA
= 0.8 V — — 15 mA
V
EN
Source Driver — — 600 ns
2.0 — — V
— — 0.8 V
Sink Driver — — 600 ns
Turn Off Delay t
pd(off)
Source Driver — — 2.0 µs
Sink Driver — — 2.0 µs
Thermal Shutdown Temperature T
Negative current is defined as coming out of (sourcing) the specified device terminal.
J
— 165 — °C
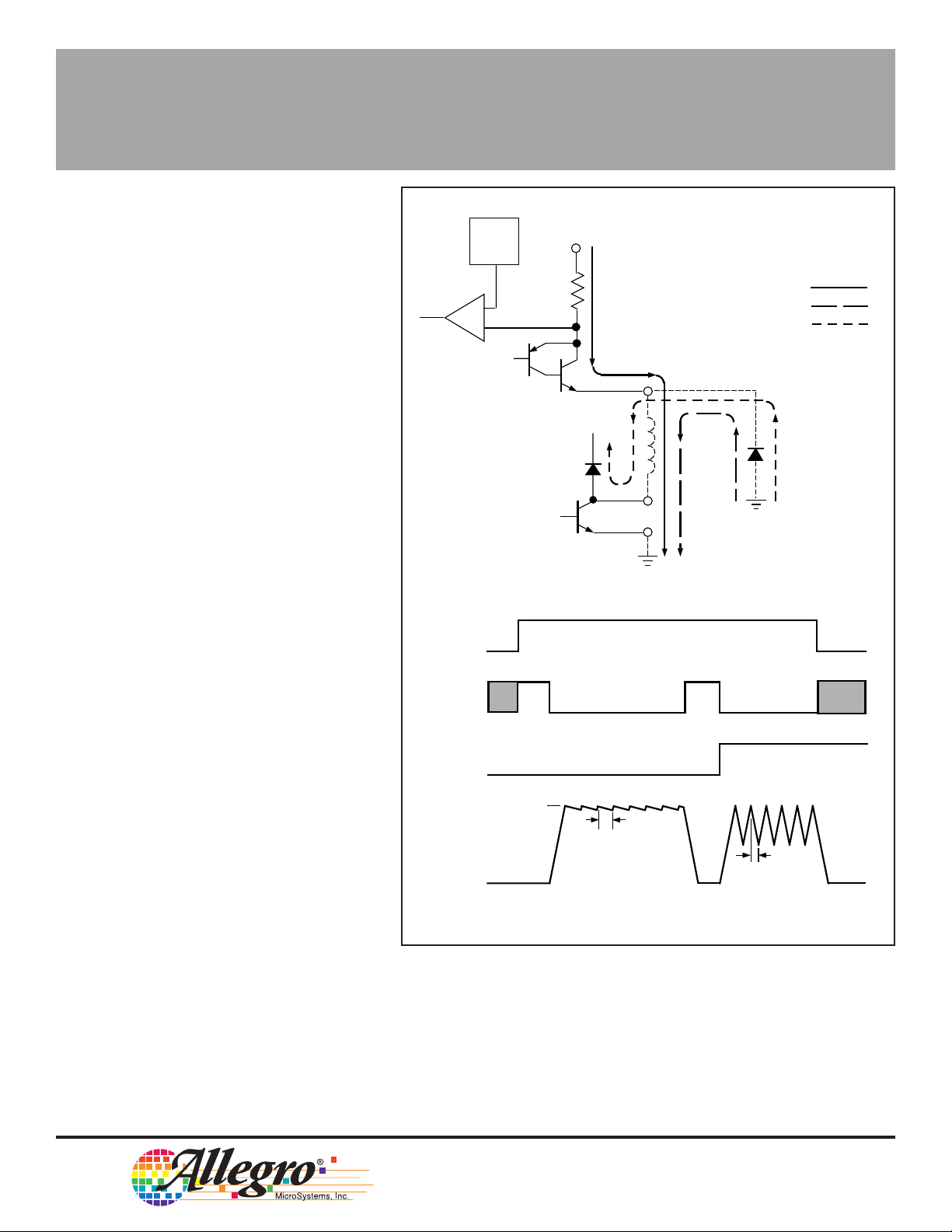
2961
HIGH-CURRENT
HALF-BRIDGE
PRINTHEAD/MOTOR DRIVER
APPLICATIONS INFORMATION
The UDN2961B/W is a high current
half-bridge designed to drive a number of
inductive loads such as printer solenoids,
stepper motors, and dc motors. Load current
is sensed internally and is controlled by
pulse-width modulating (PWM) the output
driver(s) in a fixed off-time, variablefrequency format. The peak current level is
set by the user’s selection of a reference
voltage. A slow current-decay mode
(chopping only the source driver) or a fast
current-decay mode (chopping both the
source and sink drivers) can be selected via
the MODE pin.
PWM CURRENT CONTROL
A logic low on the MODE pin sets the
current-control circuitry into the slow-decay
mode. The RS flip-flop is set initially, and
both the source driver and the sink driver are
turned ON when the INPUT pin is at a logic
low. As current in the load increases, it is
sensed by the internal sense resistor until the
sense voltage equals the trip voltage of the
comparator. At this time, the flip-flop is reset
and the source driver is turned OFF. Over the
range of V
current trip point transfer function is a direct
linear function of the reference voltage:
To ensure an accurate chop current level
(±10%), an external 2940 Ω ±1% resistor
(RCV) is used. The actual load current peak
will be slightly higher than the trip point
(especially for low-inductance loads) because
of the internal logic and switching delays
(typically 1.5 µs). After the source driver turns
OFF, the load current decays, circulating
through an external ground clamp diode, the
load, and the sink transistor. The source
driver’s OFF time (and therefore the magnitude of the current decrease) is determined
by the one-shot’s external RC timing components:
= 0.8 V to 3.4 V, the output
REF
I
= V
TRIP
t
OFF
REF
= RC
V
SENSE
BB
DRIVE CURRENT
RECIRCULATION (SLOW-DECAY MODE)
RECIRCULATION (FAST-DECAY MODE)
V
BB
RC
Dwg. EP-037
RC/2
Dwg. WP-015
ENABLE
INPUT
MODE
LOAD
CURRENT
REF
CIRCUIT
+
-
V
I
TRIP
within the range of 20 kΩ to 100 kΩ and 100 pF to 1000 pF. When the
one-shot times out, the flip-flop is set again, the source driver is reenabled, and the load current again is allowed to rise to the set peak
value and trip the comparator. This cycle repeats itself, maintaining the
average load current at the desired level.
115 Northeast Cutoff, Box 15036
Worcester, Massachusetts 01615-0036 (508) 853-5000