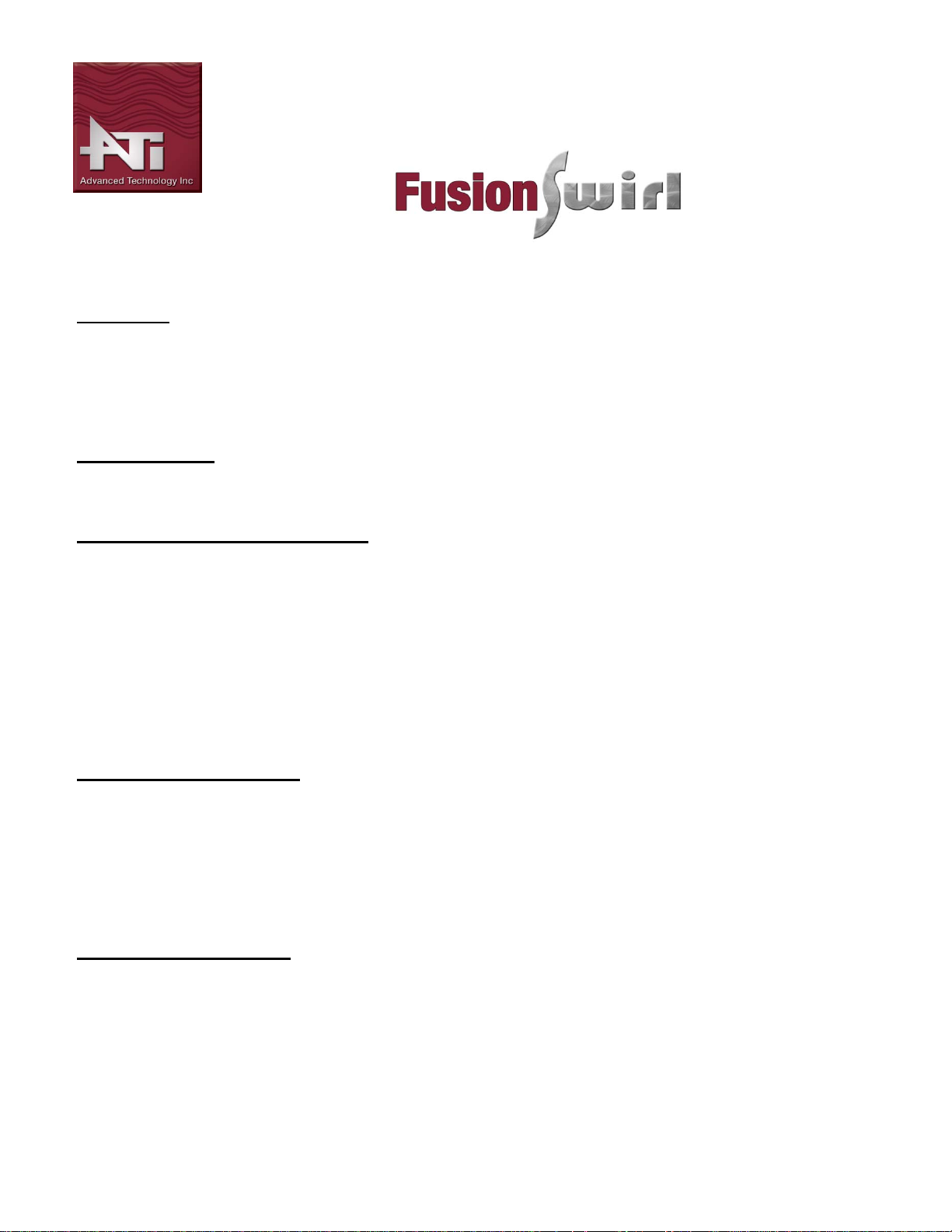
ATI‐FSII Revision0 EffectiveDate:10/26/2011
Installation Instructions for
FusionSwirl™ is a decorated aluminum sheet that can be installed easily to various substrates, including
drywall.
STORAGE
Sheets should be stored indoors on a solid, flat, dry surface. Do not stack on concrete floor or
any other surface that emits moisture. Lay sheets flat with proper support on the ends of sheets.
Do not stand sheets on edge. Sheets should be stored in a cool, well-ventilated, dry area. Prior
to installation, allow sheets to acclimate to the room temperature and humidity for 24-48 hours in
the installation location.
MAINTENANCE
Clean surfaces with a soft cloth using a household cleaner – waxes, Windex type solutions, or
ordinary soap and water. Good furniture or automobile waxes can provide additional protection.
ALUMINUM SHEET LAMINATION
If adhering the sheet to a substrate first (good quality hardwood plywood, high density
particleboard, or MDF should be used as the substrate) - clean the substrate with a clean brush.
Inspect the sheet for quality prior to fabrication.
Laminate to substrate using techniques similar to working with HPL’s. Cut the sheet to size with
shears or a saw, and be sure that the blades are sharp. Leave the protective masking on the
product during machining/installation. Cut into the sheet so that rough edges are on the back of
the sheet. Sand down cut edges with 220 grit sandpaper. Files may also be used to de-bur
sharp edges, and always file down on the decorative surface. It is always best to test cut first to
confirm results.
ROUTING INFORMATION
Sharp multi-fluted carbide cutters are necessary; the larger the diameter the cutter the better the
results. It is important that the cutter travel direction is against the cutter rotation. ALWAYS CUT
DECORATIVE SIDE UP (into the decorative face). When routing, the less material removed, the
better. It is also important that the face of the material be protected from the base plate of the
router. For edge trimming, high speed trimmers should be used (approximately 22,000 RPM)
and will produce smooth burr-free edges. If using a CNC router refer to your CNC manual for
optimal settings for cutting aluminum.
SAWING INFORMATION
Table and/or panel saw: always use sharp carbide tipped blades with 80 to 100 teeth. Blade
should be 8” to 12” in diameter, and at 0 degree rake for best results. It is always best to cut into
the decorative face with the blade to minimize burring and edge distortion. Do not force material
through saw. A constant feed rate will produce smoother cuts. Blade wax will promote better
cuts.
AdvancedTechnology,Inc 800‐849‐1320 www.advtechnology.com
Page1of3
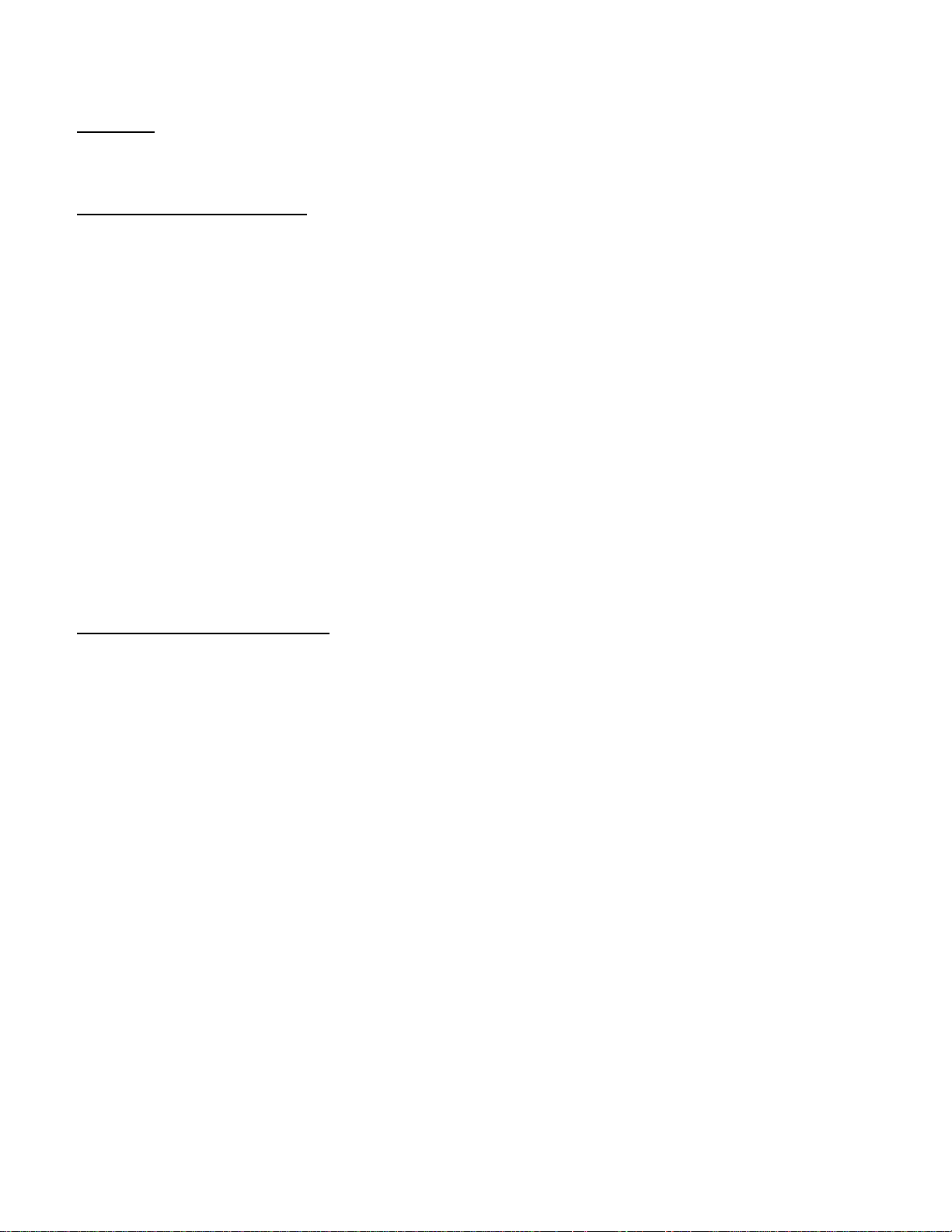
ATI‐FSII Revision0 EffectiveDate:10/26/2011
SHEARS
Blades must be clean, sharp, and properly maintained. Shears that are normally used to cut
stainless may be dull and unreliable for precision cutting. Always sample cut first.
LAMINATION/ADHESIVES
Always check with your adhesive supplier first to make sure that the adhesive that you select is
suitable for your application (common types are: contact adhesives, cements – trowel on types
such as FRP adhesives, panel adhesives, or double sided tapes, but specs do vary from specific
item to item and from manufacturer to manufacturer – not all are compatible). In all cases, the
adhesive manufacturer’s instructions should be followed as to the use of the adhesive and
substrate preparation.
A) It is helpful to prep sheets prior to lamination by scuffing the backside with 80 grit sandpaper.
B) When applying FRP adhesive, follow the adhesive manufacturer’s recommendations for
trowel style (e.g. appropriate height of adhesive bead left by trowel). It is important to apply
adhesive carefully and follow all directions to prevent problems that may result from using too
little or too much adhesive. 100% adhesive coverage applied to the entire back of the panel
is recommended by using a “crosshatch” pattern. Adhesive should extend to all edges of the
panel and should be applied directly to the back of each individual panel.
C) Use only oil-based naptha, or mineral spirits for adhesive clean up. Do not use ammonia,
abrasive cleaners/pads, or harsh solvents like lacquer thinner. It is recommended that you
test your adhesive system and/or cleaning agents with a sample piece of aluminum.
LAMINATION TO DRY-WALL
1) If applying to painted drywall, aluminum sheets can be applied directly with drywall screws,
drilled and countersunk or drilled with finish washers, and FRP adhesive. Pre-drilled holes
should be slightly larger than the fastener to account for expansion and contraction of the sheet.
2) Prior to applying FRP adhesive, prep sheets by scuffing the backside with 80 grit sandpaper.
When applying FRP adhesive, follow the adhesive manufacturer’s recommendations for trowel
style (e.g. appropriate height of adhesive bead left by trowel). It is important to apply adhesive
carefully and follow all directions to prevent problems that may result from using too little or too
much adhesive. 100% adhesive coverage applied to the entire back of the sheet is
recommended by using a “crosshatch” pattern. Adhesive should extend to all edges of the sheet
and should be applied directly to the back of each individual sheet.
3) Use only oil-based naptha, or mineral spirits for adhesive clean up. Do not use ammonia,
abrasive cleaners/pads, or harsh solvents like lacquer thinner. It is recommended that you test
your adhesive system and/or cleaning agents with a sample piece of aluminum.
AdvancedTechnology,Inc 800‐849‐1320 www.advtechnology.com
Page2of3

ATI‐FSII Revision0 EffectiveDate:10/26/2011
CONDITIONS & WARRANTY
Advanced Technology, Inc. believes all information contained herein to be correct. It is the responsibility
of the fabricator/customer to completely test the adhesives and methods of fabrication to ensure that the
results are satisfactory. ATI is not responsible for any fabrication or ancillary costs involved with using
FusionSwirl products.
All shipments are to be inspected within 10 working days after delivery. We are to be informed in writing
of any potential adjustment necessary. The seller’s only obligation will be to replace defective sheets on
a one to one basis. Neither the manufacturer nor the seller shall be liable for any additional damage or
loss, directly or indirectly, arising as a result of using FusionSwirl products.
Slight imperfections and color variations from sheet to sheet are possible and considered normal.
Please inspect each sheet carefully before fabrication to ensure it meets your needs.
CAUTION
FusionSwirl and other metal laminates will conduct electricity. To avoid electrical shock and
damage to equipment, please make sure that all electrical circuits, tools, and devices used with
FusionSwirl are properly grounded.
AdvancedTechnology,Inc 800‐849‐1320 www.advtechnology.com
Page3of3