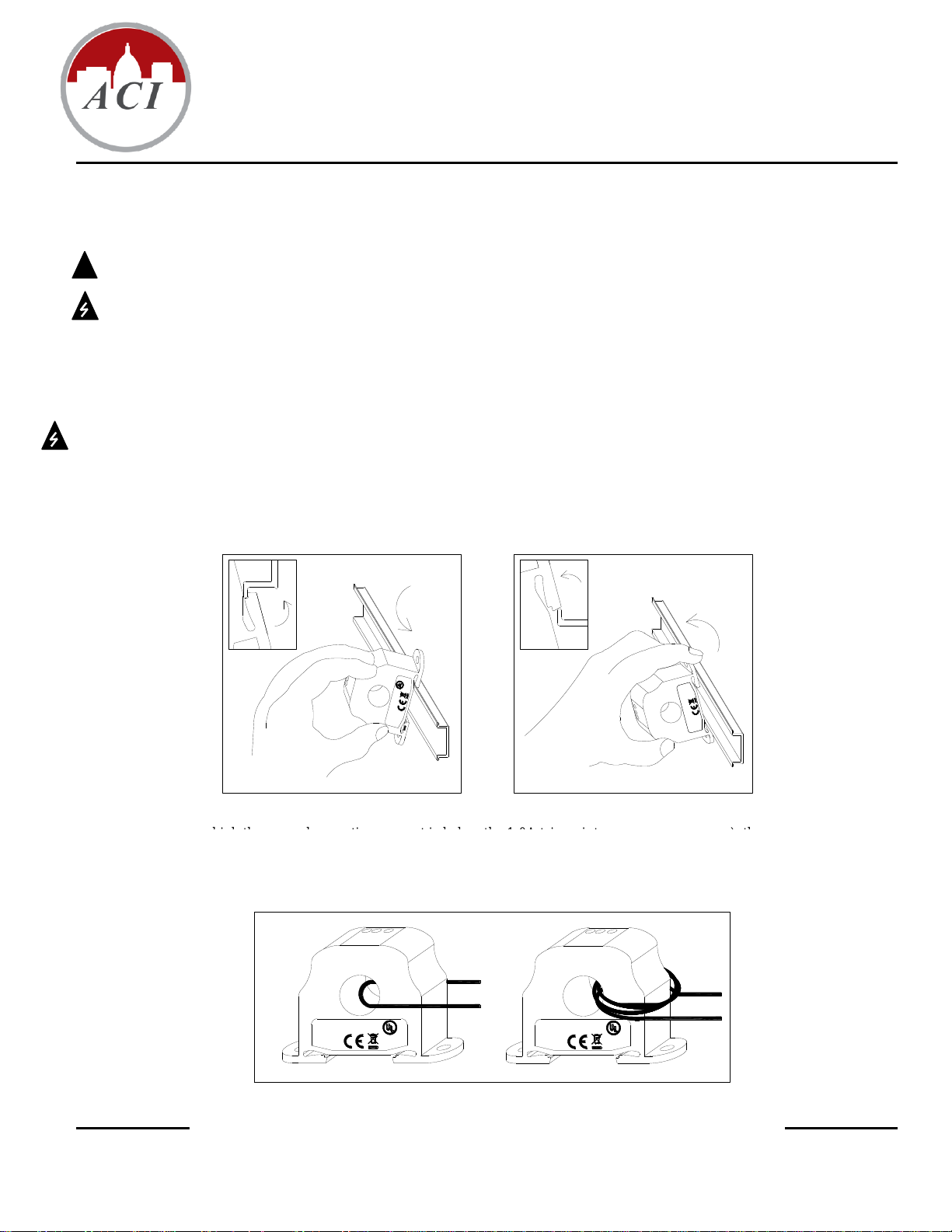
Installation and Operation Instructions
3X
ACI
Middleton, I
A/ACS
A I
C
IND.CONT.EQ.
LISTED
US
3JHX
A/ACS
I
3X
IND.CONT.EQ.
3JHX
LISTED
ACI
Middleton, WI
A/ACS
C US
ACI
Middleton, WI
A/ACS
IND.CONT.EQ.
C
3JHX
US
LISTED
Part #A/ACS, A/ACS-L, A/ACSX
Please Read Instructions Carefully Before Installation!
Safety
This product is not intended to be used for Life or Safety applications.
This product is not intended for use in any hazardous or classified locations.
Disconnect and lock out all power sources before installation as severe injury or death may result from electrical
shock due to contact with high voltage wires.
Installation
Make sure that all installations are in compliance with all national and local electrical codes. Only qualified individuals that are
familiar with codes, standards, and proper safety procedures for high-voltage installations should attempt installation. The current
switches will not require external power, since the power for the current switch is induced from the conductor being monitored.
Warning: Never rely on the LEDs to determine whether power is present at the current switch. The Red LED will
Indicate whether the current is above the adjustable trip point. The Green LED will indicate whether the
The A/ACS Series Current Switches should be used on Insulated Conductors Only! The current switch may be mounted in any
position using the (2) #8 x 3/4” Tek screws and the mounting holes in the base or snapped directly on to the 35mm DIN rail (See
Figures 1 & 2 below). Leave a minimum distance of 1” (3 cm) between the current switch and any other magnetic devices such
as contactors and transformers.
current is below the adjustable trip point.
Figure 1: Sensor Placed on Rail Figure 2: Sensor Removed From Rail
For applications in which the normal operating current is below the 1.0A trip point (See Figure 3 below), the conductor being
monitored may be looped through the sensor 6 times giving you a total operating current of 6X the original current.
Example: A small fan operating at 0.2A should be wrapped through the sensor 7 times to give you a total operating current of
1.4Amps flowing through the A/ACS or another option is to use the A/ACS-L.
Version : 1.0
Page 1 of 3 I0000136
Figure 3: Wires Through Sensors
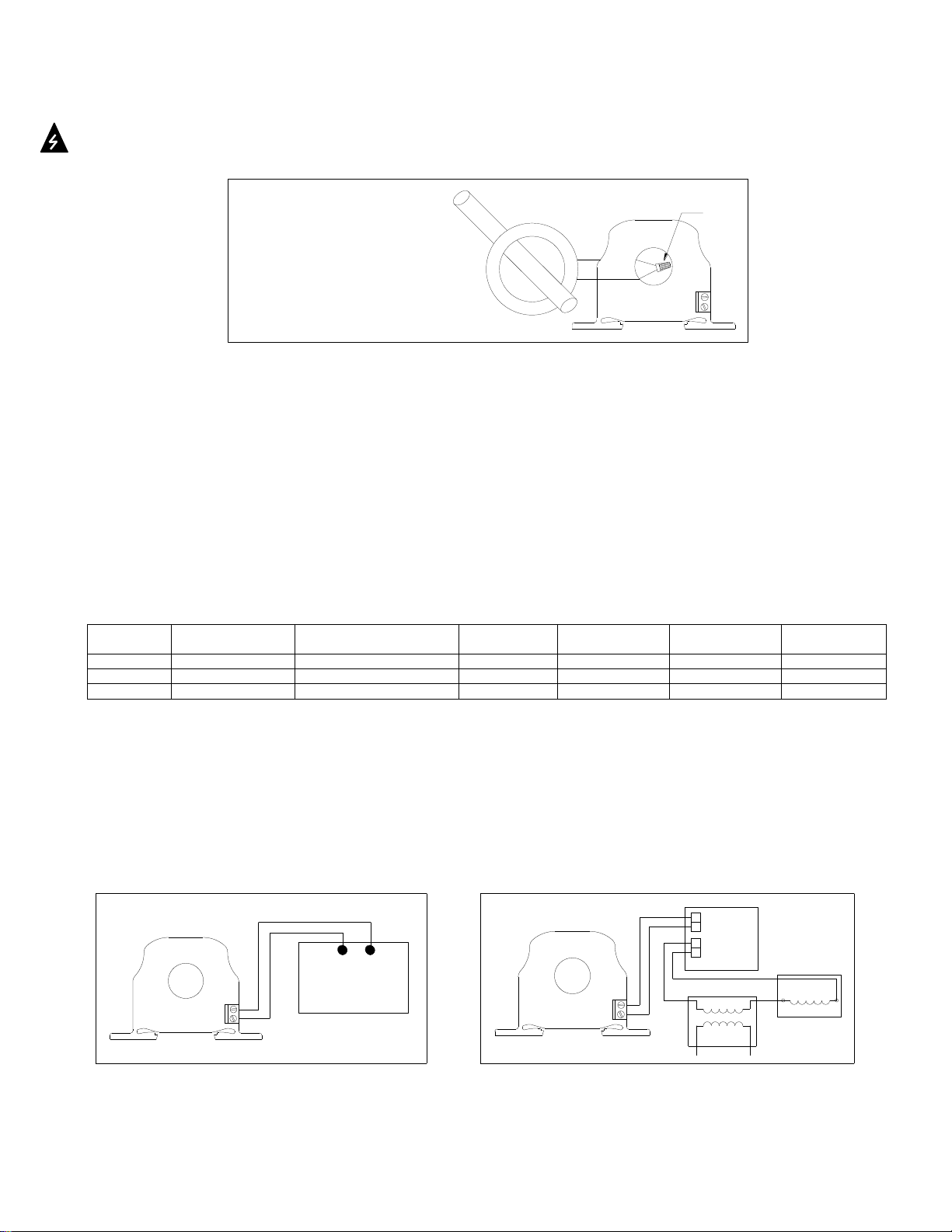
600:5 Ratio 5A C.T.
Example: For currents up to 600 Amps
(and not below 70 Amps, where
Current Transformer (C.T.)
secondary falls down to 1 Amp)
use a 600:5 ratio C.T. as shown:
Wire
Nut
Insulated
Conductor
Building Management
Digital Input #1
DI
(Status)
(Relay Coil or
DO
Contactor)
DDC Controller
Line
Transformer
Relay / Contactor
System
120 VAC
24 VAC Coil
24 VAC
Max. Sensing
Current Voltage
Max. Current for
6 seconds
Max. Current for
1 second
For applications in which the normal operating current is greater than 250 Amps or for conductor diameters larger than 0.750”
(1.90 cm) in diameter, an external 5 Amp Current Transformer must be used as shown in Figure 4 below.
Remember that the secondary of the 5A CT must be shorted together before the power may be turned onto the monitored
device.
Figure 4: Current Transformer
Wiring
ACI recommends the use of a 2 conductor 16 to 22 AWG shielded cable or twisted pair copper wire only for all current switch
applications. A maximum wire length of less than 30 meters (98.4 feet) should be used between the A/CS Series current switches
and the Building Management System or controller. Note: When using a shielded cable, be sure to connect only (1) end of the
shield to ground at the controller. Connecting both ends of the shield to ground may cause a ground loop. When removing the
shield from the sensor end, make sure to properly trim the shield so as to prevent any chance of shorting. The curr ent switch output
terminals represent a solid-state switch for controlling both AC and DC loads and is not polarity sensitive. The recommended
torque to be used on the terminal block connections is 0.67 Nm or 5.93 in-lbs.. The aperture (hole) size of the current switch is
0.75” (1.90 cm) and will accept a maximum cable diameter of 350 MCM’s.
Operating Specifications
See Figure 5 and Figure 6 for two different current switch applications using your Building Management System (DDC/PLC
Controller). Figure 5 is showing the use of the Adjustable Current Switch as a Digital Input to your DDC Controller, whereas
Figure 6 is showing you how to use the Adjustable Current Switch in conjunction with your building management system to
monitor belt loss on a motor.
Figure 5: Digital Circuit Figure 6: Analog Circuit
Page 2 of 3 I0000136
Version : 1.0
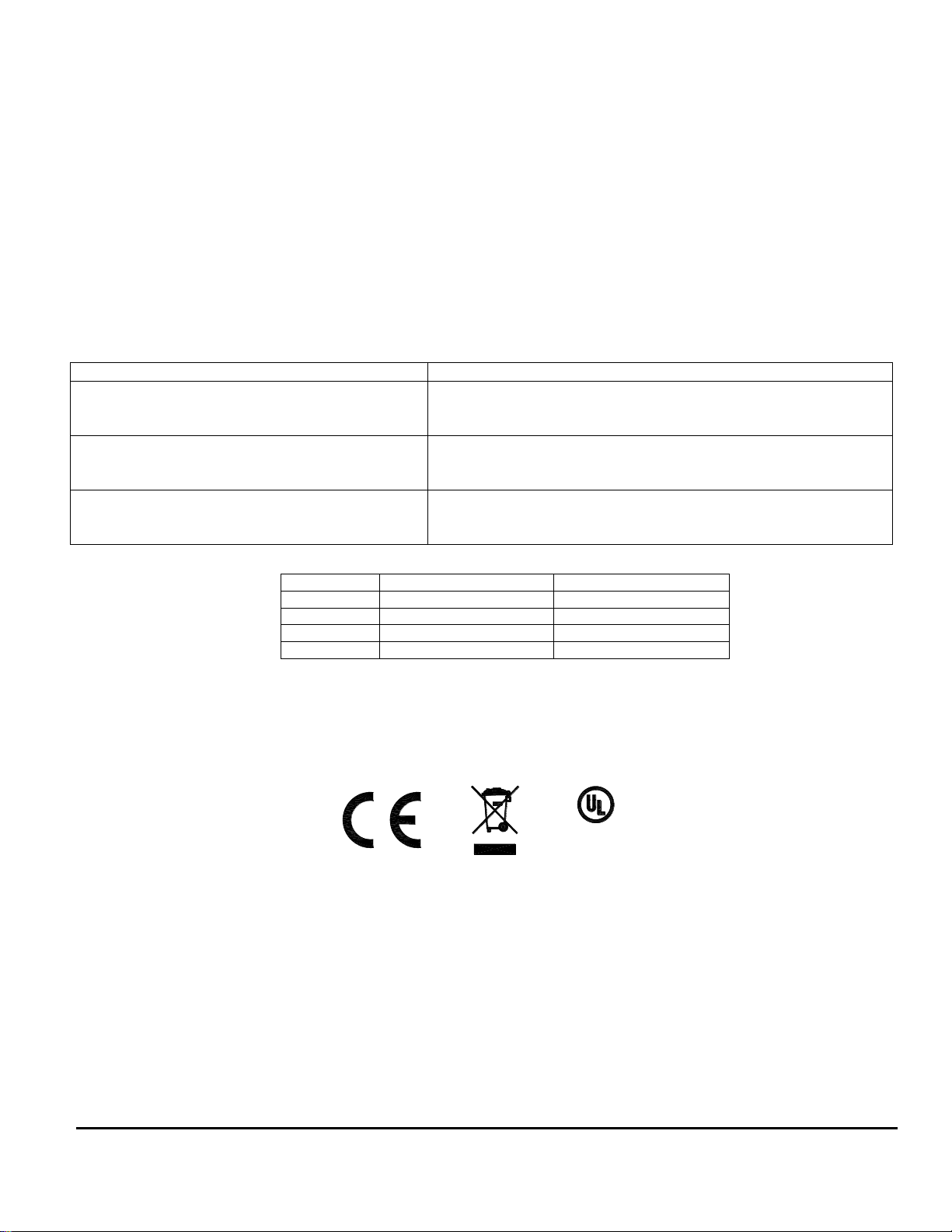
Red LED is on but the current switch didn’t activate
Disconnect the wires from the current switch output. Measure the
resistance across the contacts with an Ohmmeter. See Figure 7 below
for resistance readings for a good unit.
Red LED didn’t turn on and the current switch didn’t
activate
Verify that the conductor you are monitoring is above the adjustable
trip point. If the sensor is monitoring less than the adjustable trip point
See Figure 3 on Page 1.
Sensor doesn't switch at all, regardless of current
level.
Adjustment potentiometer is probably set to its maximum or minimum
position. Turn the Pot counter-clockwise all the way and verify if the
LED switches from Red to Green.
Resistance if switch open
Resistance if switch closed
LISTED
C US
IND.CONT.EQ.
3JHX
Calibration of Adjustable Trip Point
The adjustable current switch has an operating range of 0-250 Amps. Do not exceed! The adjustable current switch comes with
its fifteen-turn adjustment potentiometer set counter clockwise to the maximum (250A) trip point position. The adjustable current
switch can monitor Underload, Normal Load, and Overload conditions, depending on how it’s set. The procedure below is for the
Normal load condition for part numbers A/ACS & A/ACS-L.
Normal Loads
With power on, and the adjustable current switch on the proper range, turn the 15-turn adjustment potentiometer clockwise until
the Red LED turns on and stop immediately. The adjustable current switch is now tripped. The adjustable current switch
Hysteresis (Dead Band) is 10% of the trip point typically.
Troubleshooting
Figure 7
WEEE Directive
At the end of their useful life the packaging and product should be disposed of via a suitable recycling centre. Do not disp ose of
with household waste. Do not burn.
Page 3 of 3 I0000136
Version : 1.0