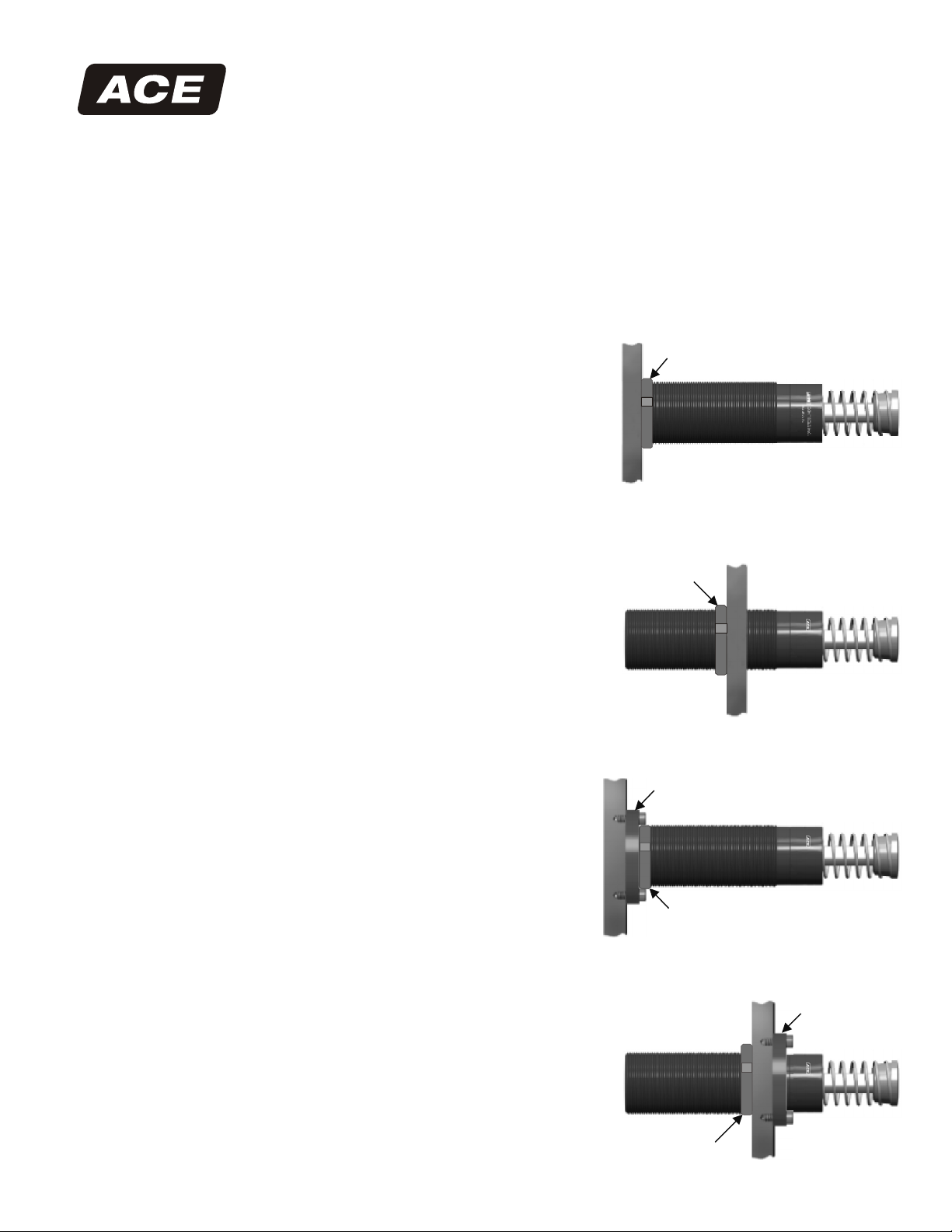
Installation Instructions
Magnum Group Shock Absorbers
ACE MC 33, 36, 45 and 64 Self-Compensating Series
ACE MA, ML 33, 36, 45 and 64 Adjustable Series
23435 Industrial Park Drive
Farmington Hills, Michigan 48335
tel: 248.476.0213
fax: 248.476.2470
www.acecontrols.com
Maximum efficiency of operation can be obtained by
carefully following these instructions:
GENERAL
Install the shock on a surface of sufficient strength.
Align the shock absorber rod end button with the load
striking surface.
Guard the shock absorber to protect it from foreign
materials such as acids, steam, weld flash, solvents,
cutting fluids, dust and debris.
Mount in an area consistent with the operating temperature
range of the shock absorber, not to exceed 75 F (24 C)
00
ambient at full energy capacity. To allow maximum heat
dissipation, do not paint the shock absorber.
Applications using two or more adjustable shock absorbers
should have the load balanced equally between them.
Note: Self-contained models MC, MCN, MA, MAN, ML and
MLN are pre-filled with ATF and are ready for use after proper
installation.
STANDARD MOUNTING INSTALLATION (Figures 1, 1A)
Fully screw the shock absorber into the threaded mounting
hole. Tighten the lock nut. Refer to the Torque Specifications
chart, Figure 8, for proper lock nut installation.
For adjustable models, orient the adjustment graduations
to the desired position by unscrewing the shock absorber no
more than a 3/4 turn and then tightening the lock nut.
CAUTION: Insufficient tightening of the lock nut may
result in the shock absorber working loose due to
structural vibration.
Figure 1...Standard Mounting
Lock Nut
(Lock Securely)
Figure 1A...Standard Mounting
Lock Nut
(Lock Securely)
MA 4550 2
CONTROLS INC.
Figure 2...Rear Flange Mounting
Flange
MA 4550-2
CONTROLS INC.
FLANGE MOUNTING INSTALLATION (Figures 2, 2A)
Bolt the flange to the mounting structure. Assure that the
bolts are securely tightened. Thread shock absorber into
flange.
For rear flange mounting (Figure 2), install lock nut securely
against flange. For front flange mounting (Figure 2A), install
lock nut securely against mounting structure.
Refer to Torque Specifications chart, Figure 8, for proper
lock nut installation.
ACE Controls Inc.
World leader in deceleration technology
ISO 9001:2000 Certified
Lock Nut
(Lock Securely)
Figure 2A...Front Flange Mounting
Flange
MA 4550-2
CONTROLS INC.
Lock Nut
(Lock Securely)
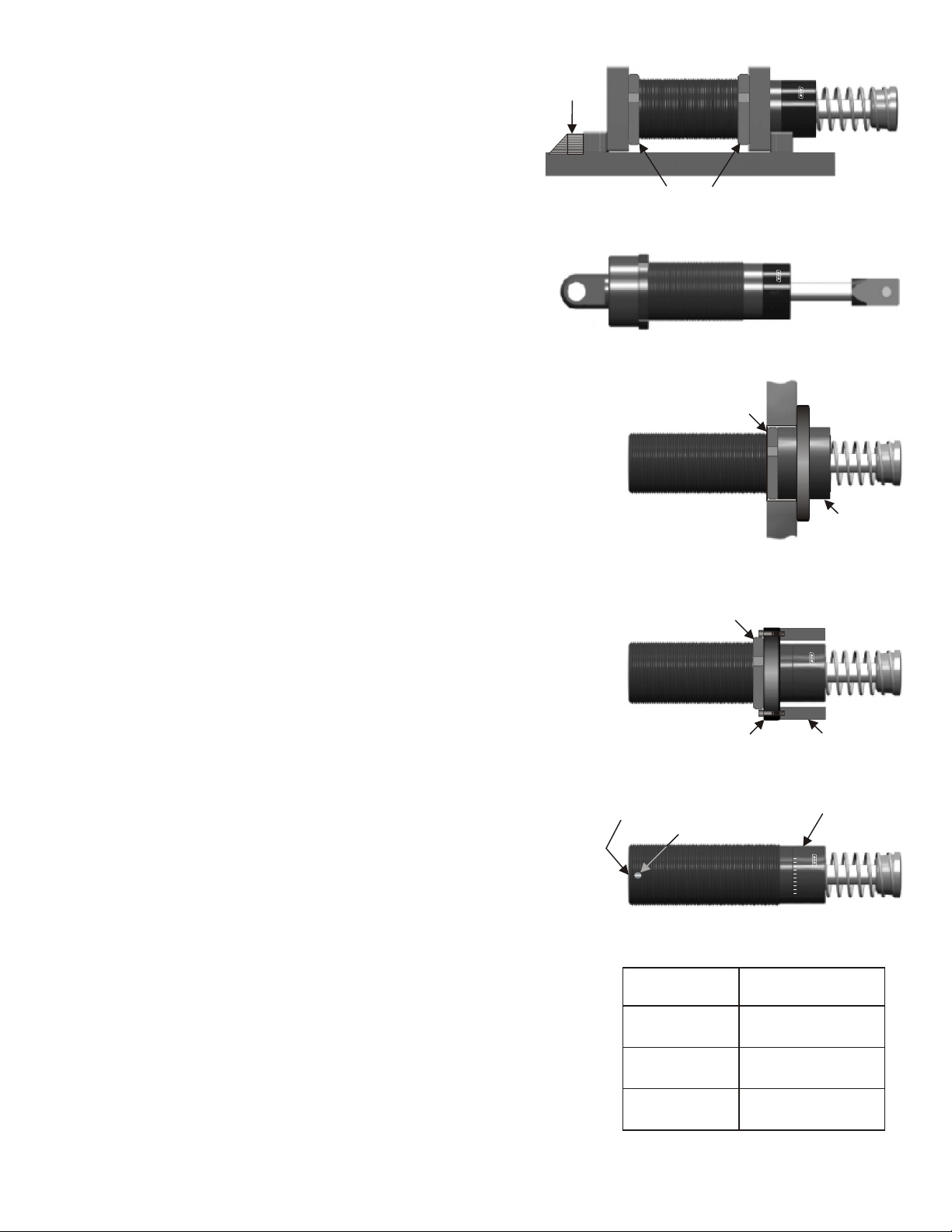
SIDE-FOOT MOUNT INSTALLATION (Figure 3)
Thread lock nuts onto shock absorber. Thread shock
absorber into side-foot mounts. Install lock nuts securely.
Bolt side-foot mount assembly to the mounting structure.
Assure that the bolts are securely tightened. In order to
prevent movement of the side foot-mount assembly,
weld a key into position behind the rear foot bar.
CLEVIS MOUNT INSTALLATION (Figure 4)
Fasten the rear clevis and the rod clevis to the mating clevis
members of the equipment. Assure that the equipment cannot
pull the rod out any farther than the shock absorber stroke will
allow.
Welded
Key
Figure 3..Side-Foot Mounting
MA 4550 -2
CONTROLS INC.
Lock Nut
(Lock Securely)
Figure 4...Clevis Mount
FLANGED STOP COLLAR INSTALLATION (Figure 5)
Thread shock absorber into flanged stop collar. Front edge
of flanged stop collar is opposite the internal threaded end of
flanged stop collar.
Front edge of integral shock absorber stop collar should be
directly aligned with front edge of flanged stop collar. Thread
lock nut onto shock absorber. Install lock nut securely against
rear surface of flanged stop collar. Bolt flanged stop collar to
mounting surface. Horizontal alignment of the bolts is preferred.
ADDING STOP BARS TO FRONT FLANGE MOUNT
APPLICATION (Figure 6)
Mount stop bars to flange. Thread shock absorber into flange.
Front edge of stop bars should be directly in line with front
edge of stop collar. Thread lock nut onto shock absorber.
Install lock nut securely against rear surface of flange. Refer to
the Torque Specifications chart, Figure 8.
ADJUSTMENT FOR MA, ML 33, 36, 45 AND 64 SERIES (Figure 7)
Proper adjustment is important to the efficient operation of the
ACE adjustable shock absorber. All units are preset at the factory
at 5.
After installation of the shock absorber, cycle the machine a
number of times. Turn the front stop collar or the rear adjuster
against the scale marked 0 to 9 until optimum deceleration is
achieved. (i.e. smooth deceleration throughout the stroke).
If hard impact is experienced at the start of the stroke, turn
the adjuster toward 9. If hard set-down is experienced at
the end of stroke, turn adjuster toward 0. If the final setting
is less than 2 or greater than 8, a different shock absorber
should be utilized.
Be sure to tighten the lock screw, (64 Series models only), on the
side of the shock absorber to secure the adjustment setting.
Torque the lock screw to 12 ft-lbs. (16 Nm). Failure to do this may
result in a shift in the adjustment setting during deceleration.
A 5/64 (2 mm) allen/hex bit wrench is required.
MA 4550 -2
CONTROLS INC.
Figure 5...Flanged Stop Collar
Lock Nut
(Lock Securely)
MA 4550 2
CONTROLS INC.
Figure 6...Stop Bars
Lock Nut
(Lock Securely)
MA 4550 2
CONTROLS INC.
Adjuster
(Front)
8 69
7
MA 4550-2
CONTROLS INC.
5
4
3
12
0
Stop Bar
Flange
Figure 7...Adjustment
Adjuster
(Rear)
Tighten lock screw to
secure adjustment
(64 Series only)
Flanged
Stop Collar
TORQUE SPECIFICATIONS CHART (Figure 8)
Refer to the Torque Specifications chart for the proper
Figure 8...Torque Specifications
torque when installing the shock absorber lock nut.
APPLYING APPROPRIATE TORQUE WITHOUT CALIBRATED TOOLING
The following procedure may be utilized if calibrated tooling is not available
to torque lock nut. Note: it is assumed that all necessary installation
instructions have been followed prior to this procedure.
1. After positioning the shock properly in relation to the accessory (i.e. flange,
collar, etc.) or mounting surface, with the proper adhesive (if applicable),
finger tighten the lock nut against the accessory or mounting surface until it
can no longer be turned.
2. Using appropriate equipment, tighten the lock nut until it rotates 1/8 to 1/4
of a full rotation (45 to 90 degrees) from the finger tight position. ACE has
Model
MC, MA, ML
33, 36 Series
MC, MA, ML
45 Series
MC, MA, ML
64 Series
Torque/Lock Nut
54-59 ft-lbs
(74-81 Nm)
167-183 ft-lbs
(225-250 Nm)
560-610 ft-lbs
(755-830 Nm)
determined that a lock nut secured in this manner meets the torque specifications
listed in the chart on the right.
Note: flanges, stop bars, flanged stop collars, side-foot mount and clevis mount assemblies are available from ACE Controls
directly or through distributors. See the ACE main catalog or visit the ACE web site for stocking distributors.
ACE Form16, MA, ML, MC Magnum