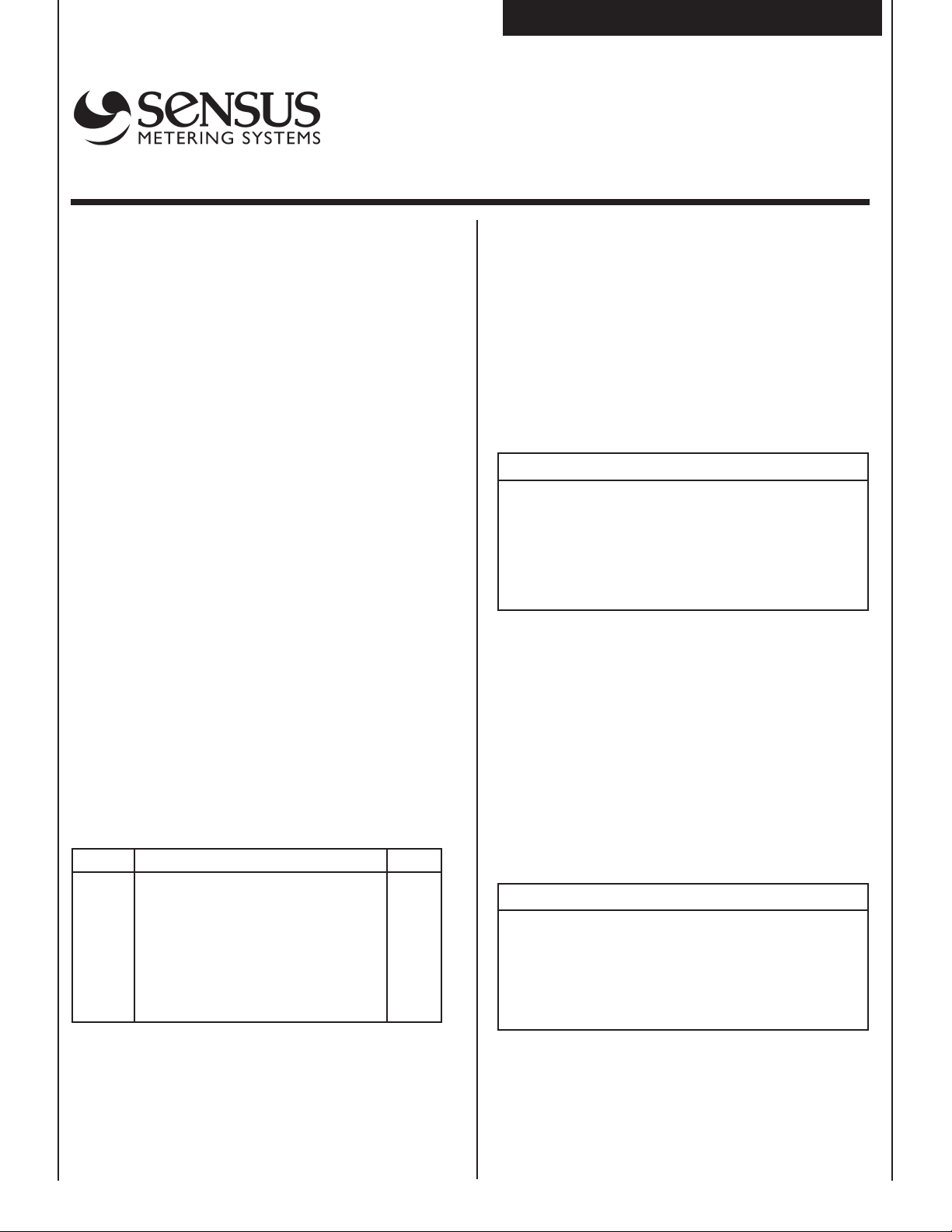
M-1306-1 Rev. 11
R
Regulator Installation and
Maintenance Instructions
243 Service
Regulators
Introduction
The 243 is a large capacity general-purpose gas pressure
regulator.
ts outstanding performance and versatility make it an excellent
I
hoice for use on industrial meter sets, combustion equipment,
c
oilers, burners, unit heaters, furnaces, ovens and other appli-
b
cations.
Use it for natural gas, air, dry CO
nitrogen, and others. Special materials are available for cer-
, propane, butane, L.P.G.,
2
tain corrosive gases.
In addition to the standard models and internal relief models
covered in this bulletin, the 243 is also available with low pressure cut-off, with built-in monitor, and as a pilot operated regulator (outlet pressures to 35 psig), a back pressure valve, a
relief valve, a vacuum regulator and a vacuum breaker. For
information, please contact your Sensus Sales Office or
authorized industrial distributor. The 243 is manufactured in
conformance with Code B31.8.
Note: The term standard refers to Non-IRV configurations.
Model Specifications
243-12-1 and 243-12-2
Maximum Inlet Pressure.........................................125 psi
Outlet Pressures......................................3 1⁄2” w.c. to 3 psi
Pipe Sizes................................................ 1 1⁄4”, 1 1⁄2” and 2”
Diaphragm..................................... 12” (nominal diameter)
243-8-1 and 243-8-2
Maximum Inlet Pressure.........................................125 psi
Outlet Pressures..................................3 1⁄2” w.c. to 4 1⁄4” psi
Pipe Sizes................................................ 1 1⁄4”, 1 1⁄2” and 2”
Diaphragm....................................... 8” (nominal diameter)
243-8HP
Maximum Inlet Pressure.........................................125 psi
Outlet Pressures................................................3 to 10 psi
Pipe Sizes................................................ 1 1⁄4”, 1 1⁄2” and 2”
Diaphragm....................................... 8” (nominal diameter)
Maximum Inlet Pressures
243-12
15 psi
*
25 psi
25 psi
*
40 psi
40 psi
60 psi
t
100 psi
125 psi
125 psi
•••
Applies only to 243-12 with external control line.
*
80 psi for 243-12 with external control line
t
ORIFICE SIZE - VALVE
1” - 30
1” - 10
3
⁄4” - 30
3
⁄4” - 10
⁄2” - 10
3
⁄8” - 10
1
⁄4” - 10
O
O
O
O
O
O
O
O
O
O
11⁄4” - 30
11⁄4” - 10
1
.207” - 10
243-8
•••
•••
25 psi
25 psi
40 psi
40 psi
80 psi
100 psi
125 psi
125 psi
Temperature Limits
The Model 243 Service Regulators can be used for flowing
temperatures from -20 F to 150 F
O
O
.
Buried Service
The Model 243 Service Regulators are
buried service.
not
recommended for
Installation and Start Up
(See Illustrations on Page 3.)
1. Make certain that regulator and piping are free of dirt,
moisture, foreign matter and other debris.
2. Be sure all shipping screens or covers are removed and
regulator is installed with flow in correct direction.
3. Regulator may be installed in any position; right-side-up, up-
side down, vertical pipe, horizontal pipe, diagonal pipe, etc.
By loosening union bolts
(16), the diaphragm case assembly
may be rotated to various positions in relation to the body.
Make certain
(16) are re-tightened to hold diaphragm case
assembly in new position and to reseal.
CAUTION
The diaphragm case vent must be positioned
to protect against flooding, drain water, ice
formation, traffic, tampering, etc. The vent
must be protected against nest building
animals, bees, insects, etc. to prevent vent
blockage and minimize the chances for
foreign material from collecting in the vent
side of the regulator diaphragm.
4. Make sure there are no leaks and all connections are firm
and tight. Tighten flange bolts evenly and firmly. On screwed
connections apply pipe dope to male threads only.
5. On regulators arranged for External Control Line, run pipe
or tubing from
trol connection in the outlet piping. This control piping
should not be less than
1
⁄2” NPT connection in lower case to the con-
1
⁄2” in size and should be adequately
protected against breakage (regulators go wide open if the
control line is broken). In general, the control connection
should be at least 8 pipe diameters from the regulator and in
as straight a run of pipe as possible.
The connection itself
must be smooth on the inside of the pipe. Pitch the control
line away from the regulator and avoid moisture pockets.
Keep inside of control line clean. Never install any type of
automatic shut-off device, which closes completely, between
the regulator outlet and the control line connection.
CAUTION
It is the user’s responsibility to assure that all
regulator vents and/or vent lines exhaust to a
non-hazar
used,
that eac
dous location a
ces of ignition.
sour
it is the user’
vice regulator is individuall
h ser
and that common vent lines
6. Adjust outlet pressure (set point) by removing cap (1) or
(1e) and turning adjustment spring button (3). On 243-8 HP
remove cap
(1b).
(1a), loosen locknut and turn adjustment screw
urn clockwise to increase and counter-clockwise to
T
decrease outlet pressure. Only adjust when gas is flowing
through regulator. When adjustment is completed, seal cap
(1) or (1e) must be securely screwed into place.
absence of this seal cap can result in unstable operation.
y from
wa
any potential
Where vent line are
s responsibility to assure
y vented
are not used.
The
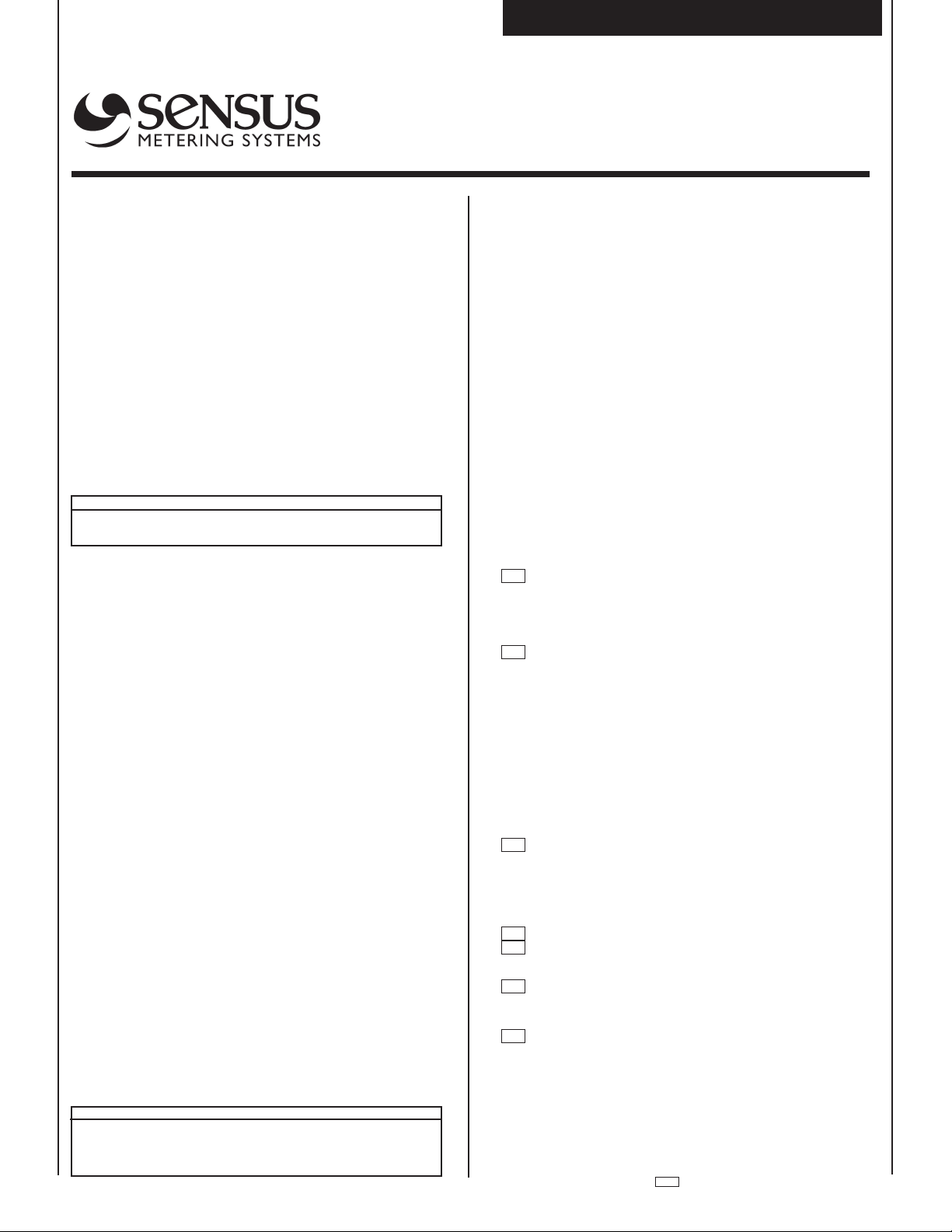
Installation and Start Up (Continued)
. On regulators with Internal Relief Valve, there is no
7
adjustment for the internal relief. It is fixed, with relief beginning at approximately 9” w.c. to 20” w.c., above regulator set
oint, depending on relief spring (11k)used.
p
Internal Relief Valves must be carefully sized. For informa-
ion, contact your Sensus Representative.
t
6. Regulators installed indoors must be vented outside. Run
vent pipe from regulator vent connection to safe place outside. Vent piping should be as short and direct as possible.
ent piping for regulators with internal relief valve (Models
V
243-12-2 or 243-8-2) must be large enough to vent all relief
valve discharge to atmosphere without excessive back pressure and resulting excessive pressure in regulator.
Vent pipe outlet must be protected against nest building animals, bees, insects, etc., and positioned to protect against
flooding, drain water, ice formation, etc. but must allow free
and unobstructed passage of air or gas.
AUTION
T
urn gas on very slowly. If an outlet stop valve is used, it should be opened first.
Do not overload the diaphragm with a sudden surge of inlet pressure. Monitor
the outlet pressure during start-up to prevent an outlet pressure overload.
vicing
Ser
1. Make sure the regulator is entirely depressured before
disassembling.
2. Carefully note location and position of all disassembled
parts to be certain reassembly is correct. Inspect each part
and replace those that are worn or damaged or otherwise
unsatisfactory.
3. For access to valve
(16) and remove diaphragm case assembly from body.
bolts
To remove valve
Orifice
(24) unscrews from body. Use 1-5/8” hex socket
(21), first remove hair pin cotter (20b).
“thinwall” type. When replacing orifice use moderate
amount of pipe dope on orifice threads.
4. Before reassembling and tightening union bolts
make certain Tetraseal
5. To replace diaphragm; remove spring
(8) and nuts (9), and disassemble diaphragm assem-
bolts
bly. Remove old diaphragm
(11b). Remove old adhesive from the diaphragm pan using
a solvent such as methyl ethyl ketone (MEK).
To reassemble, apply a thin, even layer of a rubber based
adhesive such as 3M Industrial
cleaned, prepared side of the diaphragm pan.
Attach the diaphragm to the adhesive side of the diaphragm
pan, being careful to align the center hole of the diaphragm
with the corresponsing center hole in the diaphragm pan.
Make certain all parts are reassembled in their correct order
and bolts
(8) are tightened to a torque of 150 in-lbs. Bolts
must be tight enough to prevent leakage but not too tight
that the diaphragm material is crushed or damaged.
Diaphragm must not be twisted or pinched.
6. Upon completion of servicing, make certain that regulator
installation is entirely free of leaks.
s are pressure contr
Regulator
wear that is dependent upon particular operating conditions. To assure continuous
satisfactor
the frequency of inspection determined by the severity of service and applicable
y operation,
a periodic inspection schedule must be adhered to with
C
(21) and orifice (24) loosen union
(17) is in position.
(4), remove flange
(11a) from diaphragm pan
Adhesive #EC-847 to the
CAUTION
vices with numerous moving parts subject to
ol de
laws and regulations.
(16),
Condensed Parts List
The following are the parts generally required in maintenance and servicing. For a listing of all parts refer to Parts
List RP-1306
LL. Part
I
o. Description Number
N
1
Cover Cap (IRV)
1e
Cover Cap (STD)
1d
Tetraseal 1 1⁄2 x 15⁄8”
2
O-Ring #2-140
2a
O-Ring #2-142
3
Adjustment Spring Button
4
Spring (See Table, 1st page)
5
243-12 Cover Assembly IRV (includes
vent valve and spring)
243-12 Cover Assembly STD (includes
vent valve and spring)
243-8 Cover
valve and spring)
8
Flange Bolt, 5⁄16 x 1” Hex Hd
9
Flange Nut, 5⁄16 - 18 Hex S.F.
10
243-12 Lower Case
243-12 Lower Case (tapped for external control line)
243-08 Lower Case
243-08 Lower Case (tapped for external control line)
11a
243-12 Diaphragm
243-8 Diaphragm
243-8 HP Diaphragm
11b
243-12 Diaphragm Pan
243-8 Diaphragm Pan
243-8 HP Diaphragm Pan
11d
Seal Washer
11e
Emery Cloth Washer (faces against
top side of 243-8 HP diaphragm)
11f
Spring guide
Spring guide (243-8 HP)
11k
Internal Relief Valve Spring,
for 243-8-2 only.
(relief begins at approx. 9” w.c.
11k
11s
13
16
17
18
20b
21
24
25
26
27
28
above regulator set point)
Internal Relief Valve Spring
(relief begins at approx. 9”w
for 243-12-2, and approx.
20” w.c. for 243-8-2
above regulator set point)
243-8 HP
243-12 Coupling-Lever-
Stem
243-8 Coupling-Lever-
Stem Assembly
243-8 (HP) Coupling-Lever-
Stem Assembly
Union Bolts,
etraseal (or O-Ring) 2
T
243-8 Throat Block with O-Ring Seal
243-12 Throat Block with O-Ring Seal
Hair Pin Cotter
Valve Assembly - 10 - Buna N
Valve Assembly - 10 - Viton
alve
V
Valve Assembly - 30 - Viton
1
1
⁄4” Orifice, Brass
1” Orifice, Brass
3
⁄4” Orifice, Brass
1
⁄2” Orifice, Brass
3
⁄8” Orifice, Brass
1
⁄4” Orifice, Brass
.207” Orifice, Brass
ravel Stop Stem
T
Warning Tag-Travel Stop
Warning Tag-Body Interchangeability
Clamping Plate
2
Assembly (includes vent
Diaphragm Plate
Assembly
3
⁄16” x 11⁄4” Hex
Assembly - 30 - Buna N
1
⁄4 x 21⁄2”
o
o
o
o
Denotes recommended spare par
.c.
143-16-005-00
143-16-005-08
906534
951357
951376
143-16-009-00
143-16-503-03
143-16-503-19
143-82-503-04
910030
921002
143-16-002-00
143-16-002-01
143-82-002-00
143-82-002-01
143-16-150-00
143-82-150-00
121-10-150-50
143-16-017-00
143-82-017-00
121-10-017-50
143-16-115-00
143-82-178-00
143-16-018-00
121-10-022-53
143-82-021-03
143-16-021-02
121-10-022-52
143-16-530-00
143-82-530-00
143-82-530-02
910056
904075
143-16-508-00
143-16-508-04
143-62-118-00
143-16-511-09
143-16-511-11
143-16-511-10
143-16-511-12
143-16-023-03
143-16-023-02
143-16-023-01
143-16-023-00
143-16-023-04
143-16-023-10
143-16-023-11
143-16-060-02
143-16-136-05
143-16-136-06
143-16-102-01
ts