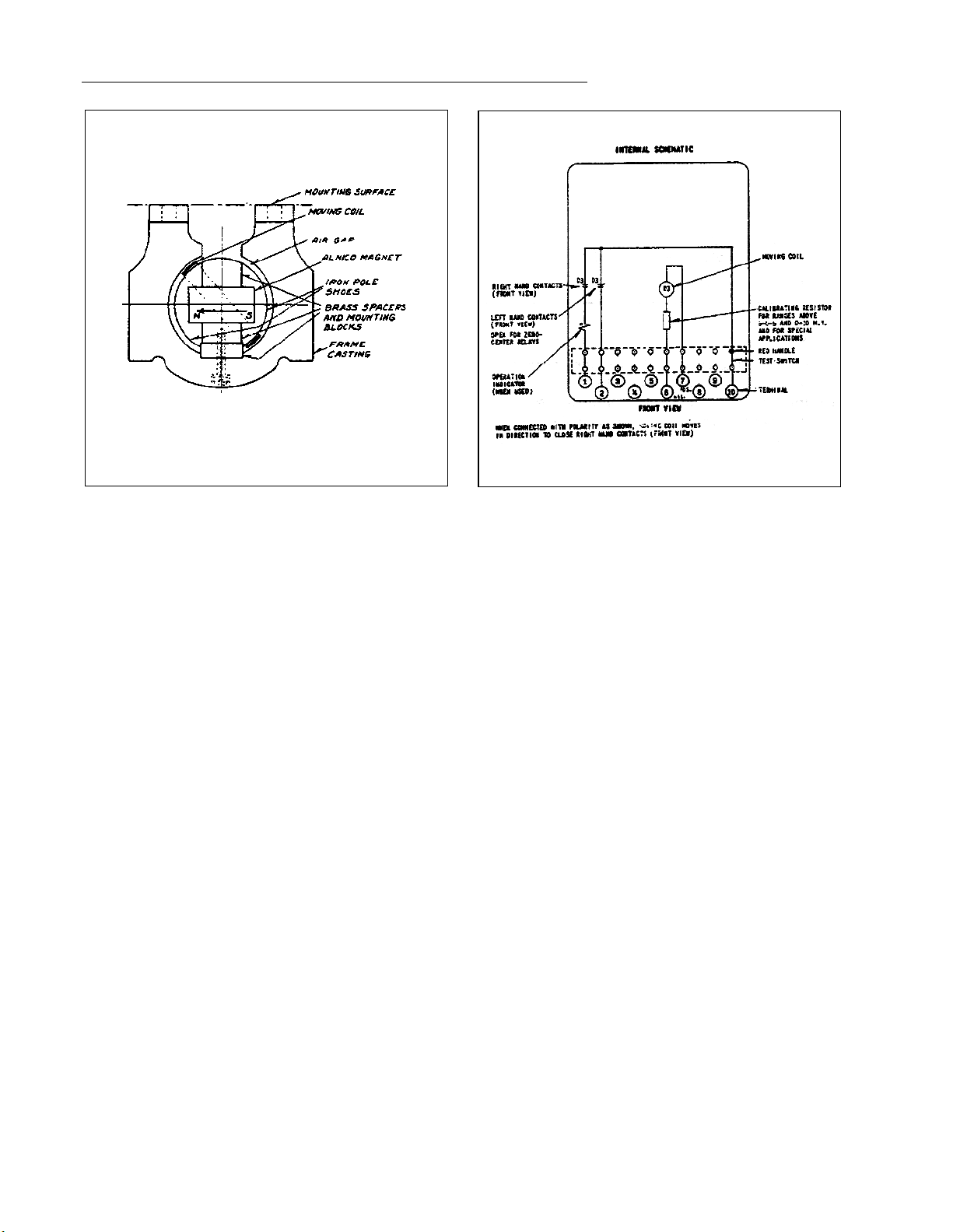
41-151.1H Type D-3 Direct Current Relay
Sketch
205342
182A787
Figure 1: Schematic Drawing of Magnetic Circuit of Type
D-3 Relay (Top View). Moving Coil Bearing Supports, Springs and Contacts Omitted.
2.2 MOVING COIL
The moving coil rotates in the air gap between the
core and the iron frame. Electrical connections are
made to the coil through two springs located at the
top of the element. One end of each spring is connected through a lever am to a head of the coil.
cache other end of each spring is fastened to posts
mounted in a circular insulation plate. This plate can
be rotated to permit adjustment of the zero position
of the moving element.
A third spiral spring located at the bottom of the element provides a current path to the moving contact.
2.3 AUXILIARY SWITCH (CS-1) (WHEN USED)
The auxiliary switch is a small solenoid type switch. A
cylindrical plunger with a silver disc mounted on its
lower end moves in the core of the solenoid. As the
plunger travels upward the disc bridges three silver
stationary contacts.
2.4 OPERATION INDICATOR (WHEN USED)
The operation indicator consists of a small solenoid
coil mounted in a steel frame, a spring restrained
armature and a white flag. The indicator is reset by a
push rod in the cover.
Figure 2: Internal Schematic of the Type D-3 Relay in the
Type FT-21 Case.
3.0 OPERATION
The D-3 relay operates on the principle of a current
carrying conductor (moving coil) located in a magnetic field (permanent magnet). When a current is
applied to the coil of the relay, a torque is produced
that rotates the moving coil until the electrical torque
is equal to the torque of the restraining spring. The
moving contact will assume a position in its travel
that is proportional to the current applied to the moving coil.
The direction of movement of the moving coil is
determined by the polarity of the current applied to
the roil. In the “left zero” and “suppressed zero” D-3
relays, the contacts will move to the right when a current of the proper magnitude and polarity is applied
to the relay. On the other hand, the contact of the
“center zero” relay will move either left or right
depending on the polarity and magnitude of the
applied current.
4.0 CHARACTERISTICS
The type D-3 relay is supplied in the standard ranges
listed in the table below. The numbers on the scale
indicate in millivolts the potential required at the relay
base terminals to operate the moving element to the
indicated scale position.
2
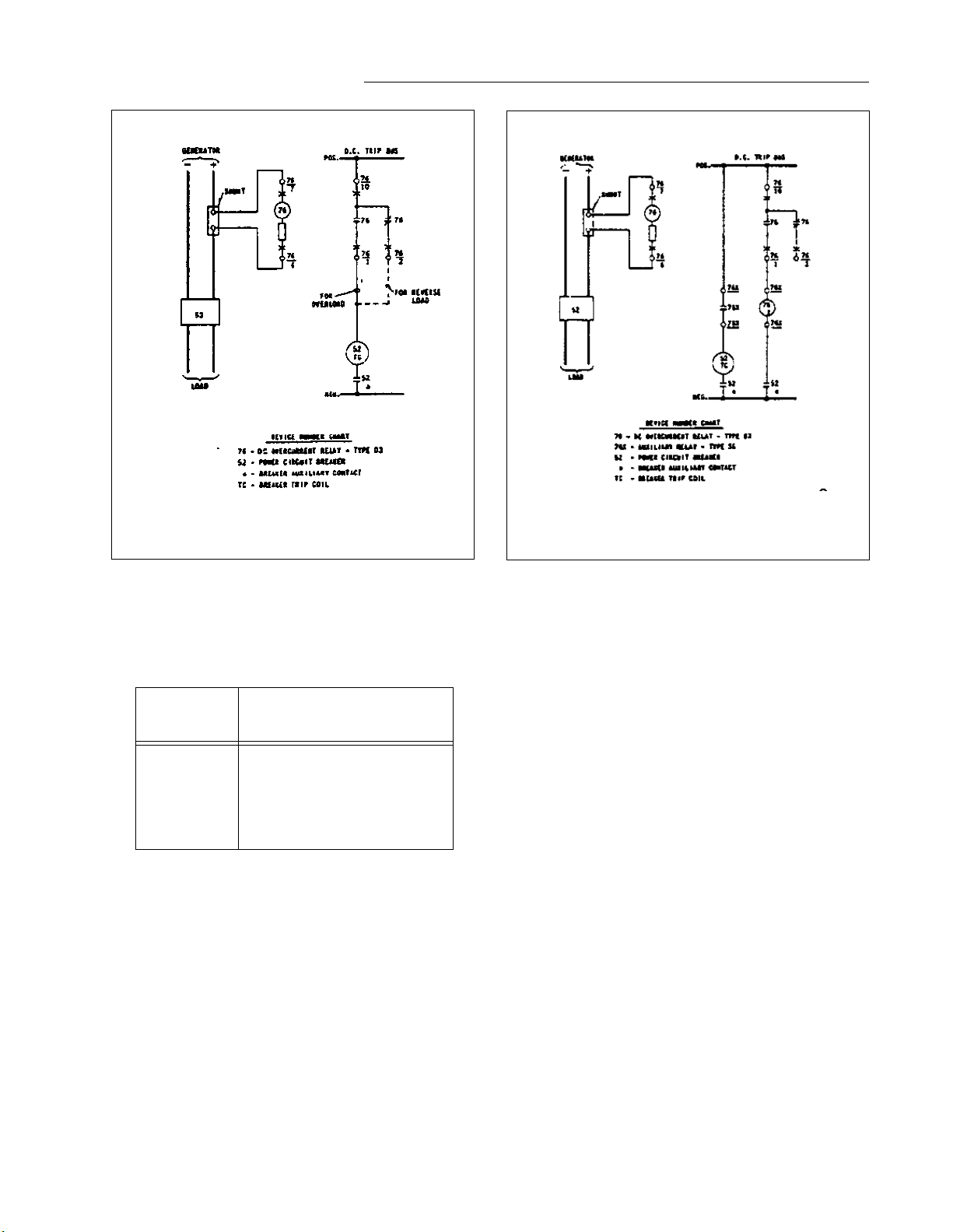
Type D-3 Direct Current Relay 41-151.1H
183A342
Figure 3: External Schematic Diagram for Overload or Re-
verse Current Protection, using the Type D-3 Relay.
MOVING COIL CIRCUIT
Ranges in
Millivolts, dc
Resistance in Ohms at 25°C
0-10
5-0-5
40-80
100-0-100
0-200
* Other ranges can also be supplied.
Average
0.3
0.3
1.2
6.0
6.0
As shown in the above Table, the D-3 relay is available with a “left zero,” “suppressed zero” and “center
zero” scale. In the “left zero” and the “suppressed
zero” relays the moving contact is located in the
extreme left hand position of the scale when the
relays are deenergized. The “suppressed zero” relay
is held in this position with considerable more force
than the “left zero” relay. When the relays are energized with voltages of the proper magnitude and
polarity, the moving contact moves to the right.
183A343
Figure 4: External Schematic Diagram for Overload Protec-
tion where Trip Currents in Excess of One Ampere
Rating Require Use of an Auxiliary Relay.
In the “center zero” relay, the moving contact is
located in the center of the scale when the relay is
deenergized. When the relay is energized, the contact will move either to the right or left depending
upon the polarity of the applied voltage.
A modification of the D-3 relay, in which a rectifier is
mounted internally, makes it suitable for ac operation. Full scale deflection can be obtained with 6 milliamperes ac Relays modified for AC volts can also be
supplied.
The relay has a slight time-delay, with inverse characteristics. In the usual application the moving coil
terminals are connected across a shunt, and this
results in longer delay for both operating and reset
times. When a shunt is used the operating time for
full scale travel at 125% of the full scale operating
current is about 4 seconds, while at 1000% it is about
.25 second. In applications where no shunt is used,
the operating times for the same conditions are about
1.25 and .15 second respectively. When the relay is
deenergized, the time required for it to reset from the
full scale position to the 10% position is approxi-
3