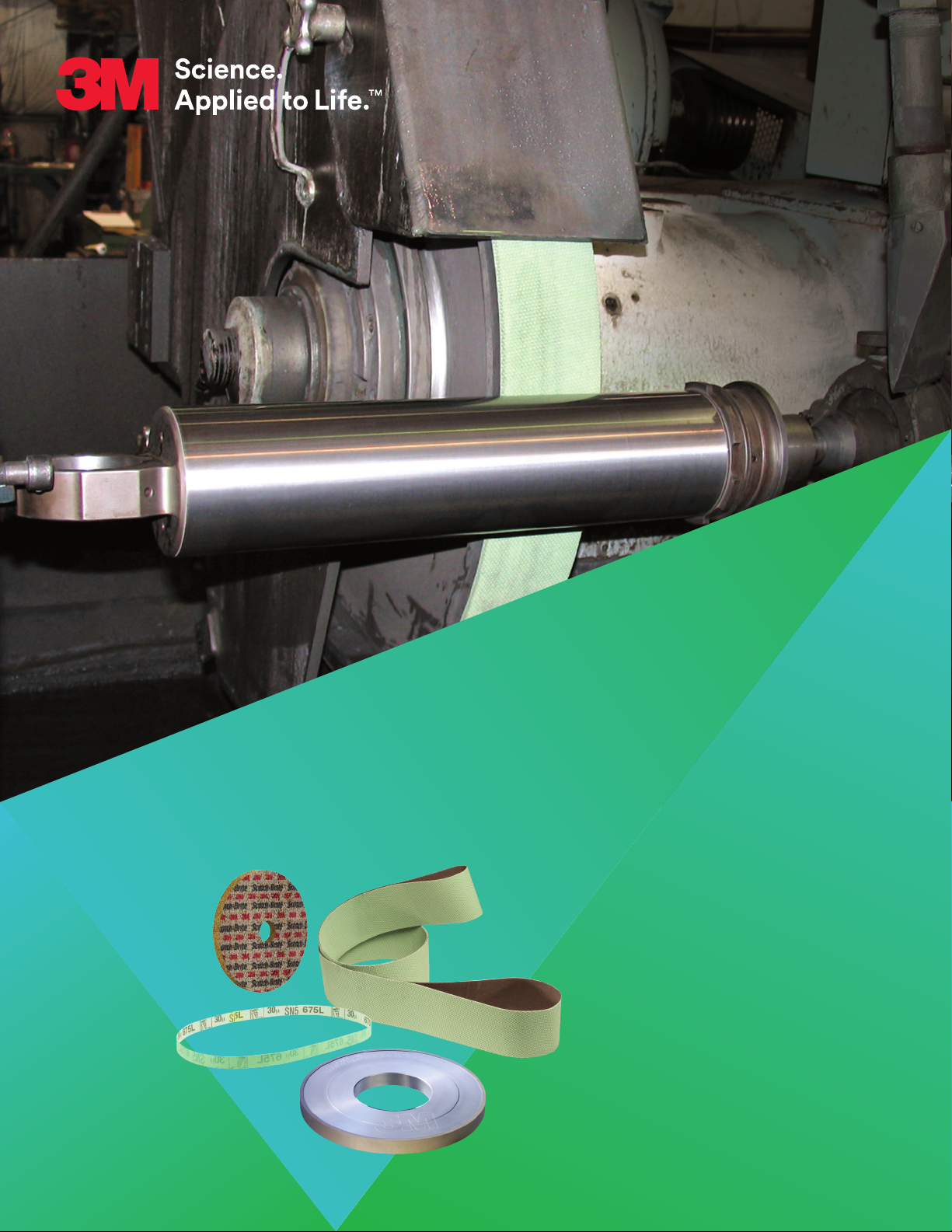
Hard-to-grind
materials cut
down to size.
Courtesy of
Abbott Machine Co.
From rough grinding to nal
nishing, 3M brings you a
complete range of abrasive
solutions designed to meet today’s
tough processing challenges.
3M.com/abrasives
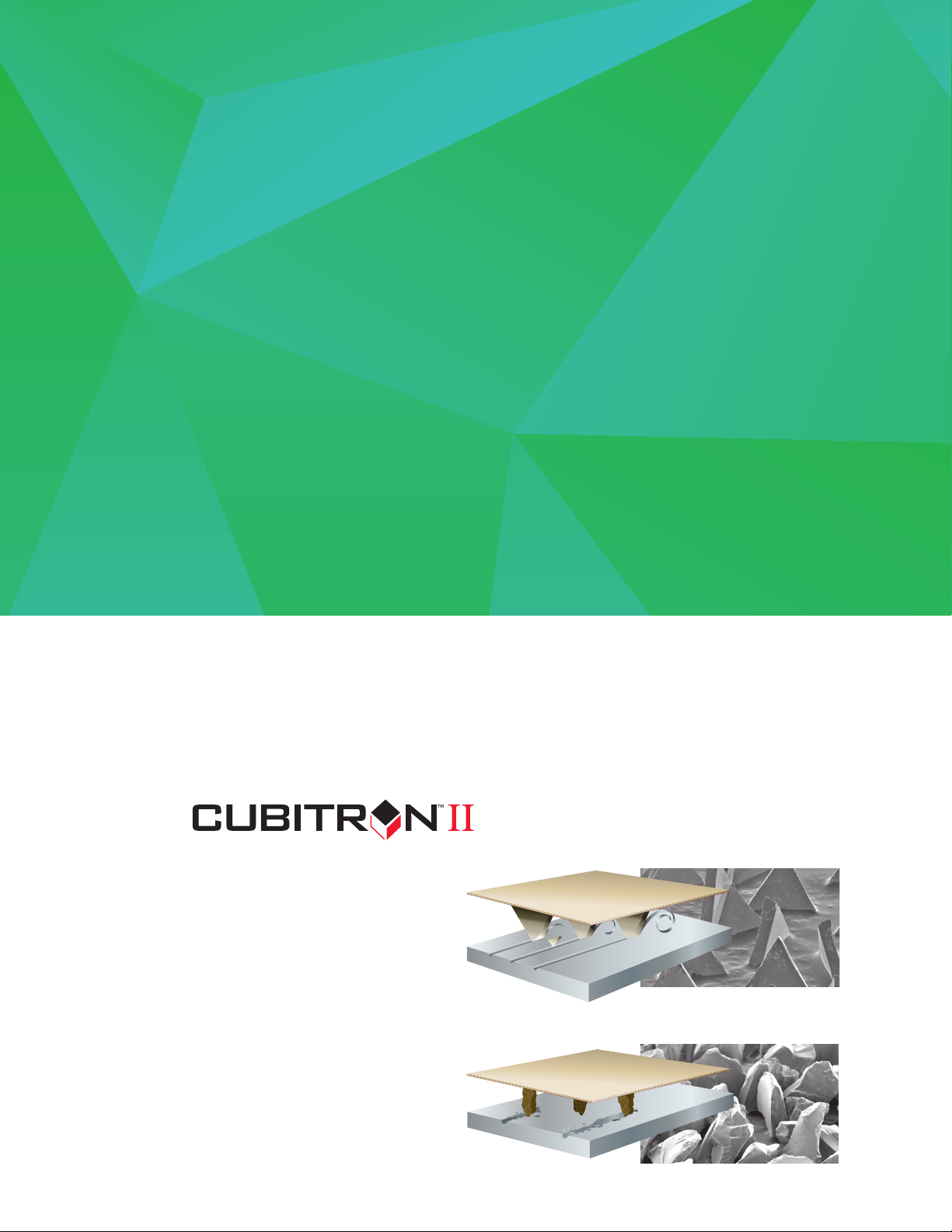
Cut to the
science of
the matter.
3M abrasive technologies.
The precision-shaped grain found in
3M™ Cubitron™ II Abrasives combines
the advanced material properties of our
original Cubitron grain with the precise
microreplicated structures pioneered in
3M™ Trizact™ Abrasives. As the triangular
shaped grain wears, it continuously
fractures to form sharp points and edges.
Conventional ceramic abrasive grain is
irregular and blocky in shape. Instead of a
clean, machining action, the grain tends to
“plow” through the metal, causing heat to
build up in the workpiece and the abrasive —
resulting in a slower cut, shorter belt life and
undesirable eects, such as burnishing.
Shaping a new era of
grinding performance.
Precision-shaped
Grain
Conventional
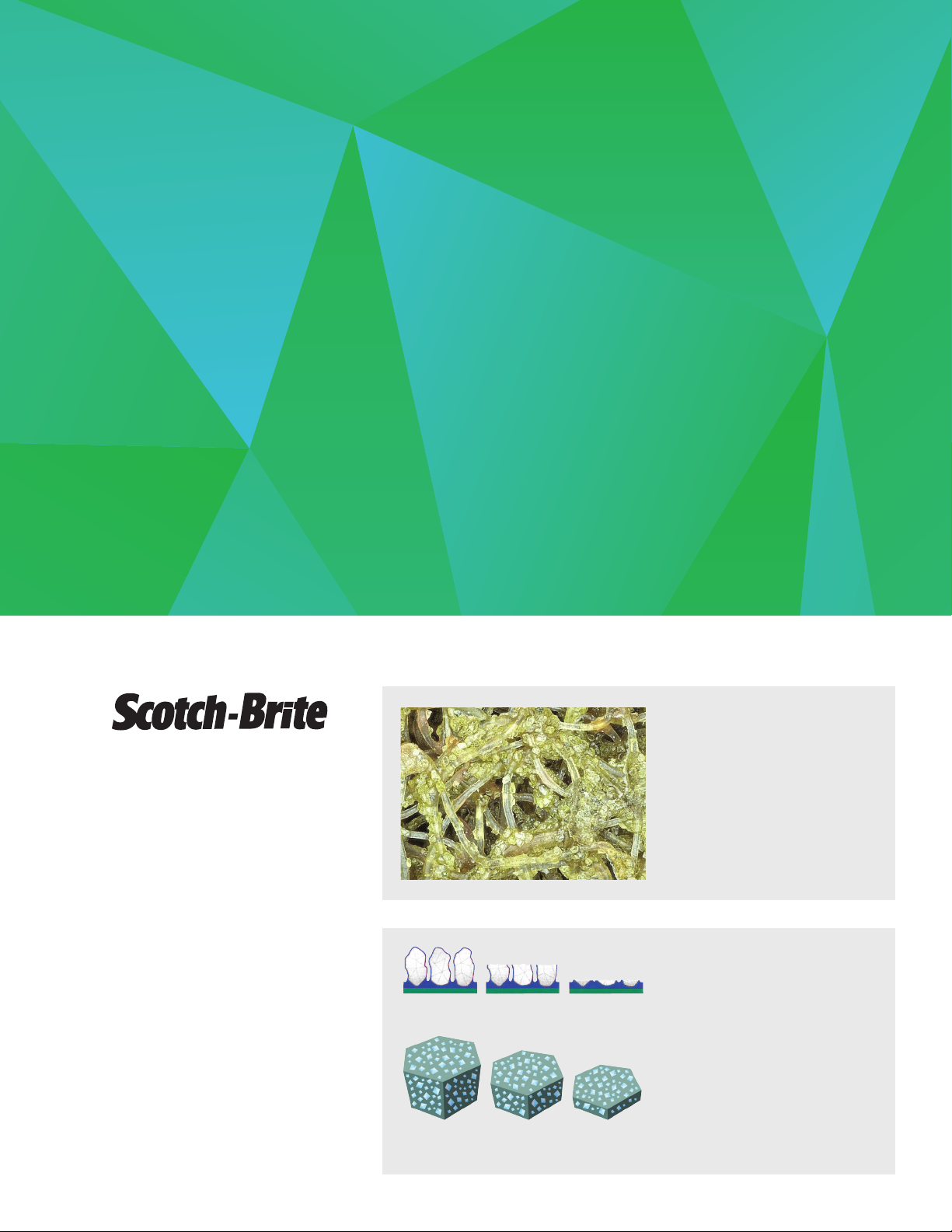
The fast yet forgiving cut and consistent
performance of Scotch-Brite™ Abrasives
allows you to improve surfaces without
signicantly changing the shape of
dimension or the workpiece —and helps
prevent undercutting and gouging.
Revolutionary 3M technologies
deliver required geometry
tolerances without sacricing cut
rates on hard-to-grind materials.
Consistently and easily achieve
nishing specs part after part.
Flexible, non-woven construction
with high concentration of active
mineral sites for fast, consistent
cutting without compromising
nal nish. Specially coated
to minimize loading. Produces
controlled, uniform scratch
throughout life of the abrasive.
Trizact
™
Derived from patented 3M microreplication
technology, 3M™ Trizact™ Abrasives consist
of precisely-shaped three-dimensional
structures distributed uniformly over the
substrate. Unlike conventional abrasives,
which are constructed from randomlyspaced and irregular-shaped minerals, the
uniform conguration of Trizact abrasives
helps deliver consistent performance.
Conventional abrasives start
out sharp, but dull quickly.
The three-dimensional structures
of 3M™ Trizact™ Abrasives contain
multiple layers of mineral. As
these structures wear, fresh, sharp
mineral is constantly exposed
to the workpiece, resulting in
faster, more consistent cutting
throughout the life of the belt.
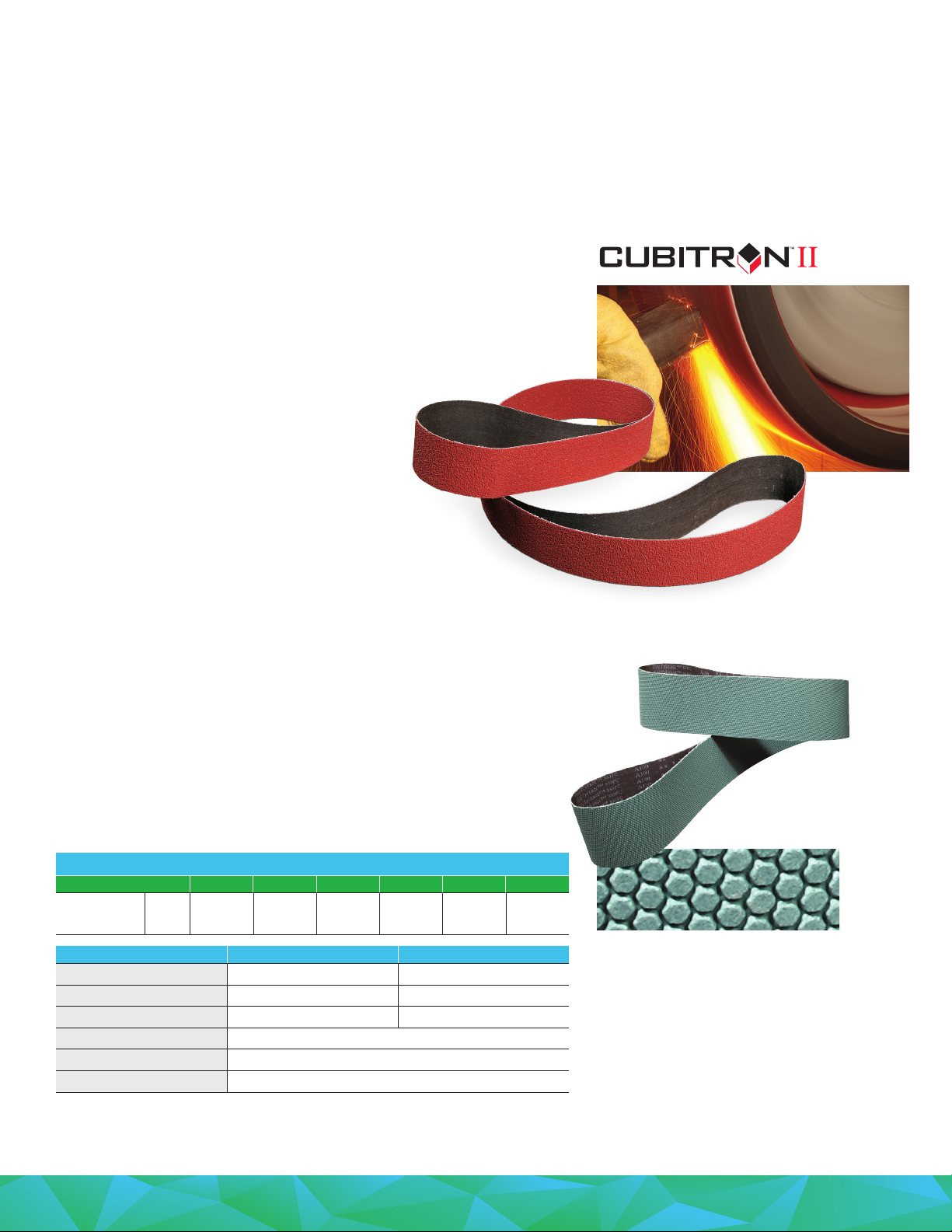
Base Steel Dimensioning
3M™ Cubitron™ II Abrasive Belt 984F
New 3M™ Cubitron™ II Abrasive Belts have raised the bar for
grinding performance and productivity — thanks to a breakthrough
3M technology that re-writes the rules for speed, consistency and
belt life.
• Cuts cooler —diverts heat from the workpiece
and belt to the swarf
• Helps eliminate burnishing and heat stress
• 3M’s highest performing belt in most metal
working applications
3M™ Trizact™ Cloth Belt 363FC
3M’s newest belt for cylindrical and centerless grinding provides outstanding performance
when dimensioning the base material prior to thermal spray coating of parts. Combine
the unmatched consistency of this Trizact abrasive with the ease and versatility of a belt
dimensioning process for fast, predictable results on stainless, mild and hardened steel.
Grade A300 provides quick cutting and accurate dimensioning of base metal prior to thermal
spray coating. Finer nishes can be quickly achieved through simple belt changes to the
appropriate abrasive grade.
Base Material Prep and Dimensioning with 3M™ Trizact™ Cloth Belt 363FC
Sequential Surface Finishes Obtained
Roll Material A300 A160 A100 A65 A45 A35
Mild Steel
Operating Conditions Recommended Acceptable Range
Belt Speed (SFPM) 6,000 4,000 –7,000
Workpiece Speed 75 50–150
Traverse Rate 1/4 inch/rev 1/10–1/2 inch/rev
Contact Wheel
Alternate Contact Wheel 90 Shore A, smooth or serrated
Coolant Water with 4–8% synthetic coolant
Ra 60–70 55–65 40–50 30–35 20–25 12–18
Target
Removal
0.010–
0.015
Ra (micro inch) Target Removal (inches o the diameter)
0.005–
0.0075
0.005 0.004 0.0025 0.001
Incompressible Aluminum, Steel, Polymer;
1/4" wider than abrasive belt
3M™ Trizact™ Cloth Belt 363FC
is available in A300 to A35 grades.
• Faster than conventional bonded wheels
• Up to 5 times extended belt life over
conventional coated abrasives
• Improved nish consistency
• Reduced taper on long parts
• Improved part-to-part size